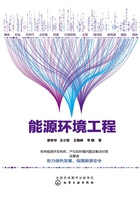
2.5.3 煤炭气化方法的分类
迄今为止,已开发及处于研究发展中的煤气化方法不下百种,由于许多因素互相掺杂,对气化过程进行通用的系统分类是比较困难的。有效的煤气化方法是根据不同的过程参数或所用的不同燃料种类进行分类的,依气固接触形式、传热方式、进料方式、排渣方式而不同,并因此对气化原料煤的要求也不同。
根据入炉煤在炉内的过程,煤炭气化可分为移动床气化、流化床气化、气流床气化、熔融床气化和地下气化。前三种气化方法对原料煤的粒度和黏结性、操作条件等有不同的要求,同时热效率、碳转化效率、处理能力及煤气组成也有明显的区别。表2-5列出了这三类气化炉的重要特点。
表2-5 三种典型气化方法的比较

2.5.3.1 移动床气化法
煤炭在移动床气化炉中的气化,也称为块煤气化,是最早出现的煤炭气化方法。从炉型上可概括为常压气化炉和加压气化炉两种,在运行方式上有连续式和间歇式的区分。
(1)常压移动床气化法
常压移动床气化法是在常压条件下运行,采用自供热和干法排灰的方式进行移动床气化。在气化炉内,固体原料煤从炉顶加入,在向下移动的过程中与从炉底通入的气化剂逆流接触,进行充分的热交换并发生气化反应,使得沿床层高度方向上有一明显变化的温度分布,一般自上而下可分为预热层、干馏层、气化层(还原层)、燃烧层(氧化层)以及灰渣层,如图2-14所示。
生产时,气化剂通过气化炉的布风装置自下而上均匀送入炉内,首先进入灰渣层,与灰渣进行热交换而被预热,灰渣则被冷却后经由旋转炉篦离开气化炉。由于灰渣层温度较低,且残炭含量较小,因此灰渣层基本不发生化学反应。

图2-14 移动床气化炉
预热后的气化剂在氧化层与炽热的焦炭发生剧烈的氧化反应,主要生成CO2和CO,并放出大量的热,因此氧化层是炉内温度最高的区域,并为其他气化反应提供热量,是维持气化炉正常运行的动力带,其发生的主要反应有:
C+O2CO2+393.8kJ/mol (2-17)
2C+O22CO+115.7kJ/mol (2-18)
在氧化层中,残留的极少量未燃尽炭和不可燃的灰分进入灰渣层冷却,高温的未反应气化剂以及生成的气体产物则继续上升,遇到上方区域的焦炭。在这里二氧化碳和水蒸气分别与焦炭发生还原反应,因此称为还原层。还原层是煤气中可燃气体(CO和H2)的主要生成区域,也称气化层。其主要反应均为吸热反应,因此其温度与氧化层相比有所降低。
CO2+C2CO-164.2kJ/mol (2-19)
C+H2OCO+H2-131.5kJ/mol (2-20)
还原层上升的气流中主要成分是可燃性气体产物(CO和H2等)和未反应尽的气体(CO2、H2O、N2)等,在上部区域与刚进入炉内的原料煤相遇,进行热交换,原料煤在温度超过350℃时,发生热解并析出挥发分(可燃气体或焦油)生成焦炭,由于此时上升气流中已几乎不含氧气,所以煤实际处于无氧热解的干馏状态,因此称为干馏层,其反应过程可表示为:
煤CH4+H2+CO2+H2O+CmHn+焦油+半焦
由上面的表达式可以看出,干馏层生成的煤气中含有许多气体杂质,这些气体杂质与还原层生成的煤气混合即为发生炉煤气,经过炉顶附近的干燥层将原料煤预热干燥后离开发生炉。事实上,在发生炉中的气化反应并非有如上面的分层面,但通过分析不同炉层内主要气体组成的变化(见图2-15),可见其变化趋势与分层的描述基本一致。

图2-15 气体组成沿料层高度变化图
常压移动床气化法通常包括煤气发生炉气化法、水煤气气化法和相应的两段炉气化法。
(2)加压移动床气化法
加压移动床气化法是一种在高于大气压力(1.0~2.0MPa或更高压力)的条件下进行煤的气化操作,通常以氧气和水蒸气作为气化介质,以褐煤、长焰煤或不黏煤为原料的气化技术,其突出优点是煤气热值高,煤种适应性强,耗氧量较低,气化强度高,生产能力增大,粉尘带出量少等。加压气化技术的主要缺点是粗煤气中含有较多的酚类、焦油和轻油蒸气,煤气净化处理工艺较复杂,易造成二次污染,投资高,设备的维护和运行费用较高。
加压气化除了一般常压气化发生的煤燃烧、二氧化碳还原、水煤气反应和水煤气平衡反应外,主要是发生了一系列甲烷生成的反应,而这些反应在常压下是需要催化剂参与才能发生的。
C+2H2CH4+Q (2-21)
CO+3H2CH4+H2O+Q (2-22)
2C+2H2OCH4+CO2+Q (2-23)
CO2+4H2CH4+2H2O+Q (2-24)
加压移动床气化与常压移动床气化类似,气化炉内也可按反应区域来进行分层,各层的主要反应及产物如图2-16所示。其主要特点是在还原层上方,由于H2、CO2和C进行了大

图2-16 加压气化炉中各层的主要反应及产物
量反应,不断生成H2和CO,同时因吸热使环境温度降低,为甲烷的生成创造了条件。随着碳加氢反应及CO和H2合成反应的进行,甲烷的量不断增加,形成了所谓的甲烷层。由于生成甲烷的反应速率较慢,因此与氧化层和还原层相比,甲烷层较厚,占整个料层的近1/3。
与此同时,在加压条件下,其他反应也受到了不同程度的影响。由于主要的氧化反应C+O2CO2和水煤气平衡反应CO+H2O
CO2+H2的反应前后体积不变,因此压力提高不影响化学平衡,但加快了反应速率。而水煤气生成反应C+H2O
CO+H2和二氧化碳还原反应C+CO2
2CO则是体积增大的反应,压力提高化学平衡向左移动,因此在加压气化生成的煤气中CO2含量高,CO和H2含量降低,水蒸气消耗大,废水多。
鲁奇(Lurgi)炉是加压移动床气化炉中应用最广、最为成熟的炉型,一般分为两类:固态排灰的鲁奇炉和液态排渣的BGL-Lurgi炉。图2-17(a)是第四代的干式排灰鲁奇炉的结构。整个气化炉大体可分为加煤、搅拌、炉体、炉栅和排渣五大部分。由于气化炉处于高压操作条件,因此加煤装置采用双阀钟罩形式以保证原料煤可以连续不断地进入气化炉。布煤器和搅拌器同时由电机带动,如果气化没有黏结性的煤种,可以不设搅拌器。气化炉炉体由双层钢板焊制,形成水夹套,在其中形成的蒸汽汇集到上部蒸汽包通过汽水分离引出。其他结构如旋转炉篦等与常压移动床气化炉类似。

图2-17 加压鲁奇炉
保持炉内压力稳定对加压移动床气化十分重要,它直接影响到气化过程工况条件与产物气体的组成。鲁奇炉采用与太空舱缓冲门相似的煤锁与灰锁装置实现这一功能。煤锁加煤过程与灰锁排灰过程同为间歇性的操作,通过操作阀门,使煤锁或灰锁充压、泄压来实现加煤或排灰这一过程。
干式排灰鲁奇炉的操作压力通常为3MPa,在炉内氧化区域最高温度约为1000℃,粗煤气离开炉顶的温度为260~538℃,这取决于气化煤种,同样粗煤气的组成也随着煤种的不同而不同。
与常压移动床气化法相比,鲁奇炉的CH4和CO2的含量都有很大的提高,粗煤气经脱CO2和变换精制处理后,可作为合成氨、合成甲醇以及合成油品的原料气,也可以用于生产高热值的替代煤气。尤其重要的是,任何合成工艺都需在高压下进行,这就显示了鲁奇炉在加压条件下运行的优势。同时,新型鲁奇炉的粗煤气产量已达156m3/d以上,这是常压气化难以相比的。
图2-17(b)为液态排渣BGL-Lurgi炉的结构图。它与干式排灰气化炉最主要的区别是水蒸气和氧气的比,在干法排灰中该比例一般为4∶1至5∶1,而在液态排渣炉中则为0.5∶1。降低水蒸气和氧气的比,可使炉膛氧化区的温度上升,以超过煤灰的软化温度,使其以液态灰渣的形式排出炉外。
液态排渣炉通过提高炉温来加快气化反应的速率,炉内最高温度一般在1300℃以上,出口粗煤气的温度为550℃左右,使得气化强度和生产能力有了显著的提高,约为干法排灰式的3倍多。同时灰渣中含碳量有所下降,碳利用率一般在92%以上。此外,水蒸气利用率高是其另外一个显著的优点。但由于液态排渣的高温特点,使得气化煤气的组成也发生了变化,高温条件削弱了放热的甲烷生成反应,同时水蒸气量的减少使CO2还原成CO的反应加强,因此同干法排灰相比,其粗煤气中CH4含量下降,CO和H2组分之和约提高25%,同时CO/H2上升,而CO2则由30%降到5%~6%。
2.5.3.2 流化床气化法
流化床煤气化技术是气化碎煤的主要方法。流化床气化法的原理与流化床燃烧具有相同之处,都是利用煤的流态化实现煤的化学反应,只是流化床煤气化用气化剂代替了燃烧用的空气,使煤和气化剂在流态化状态下发生气化。
(1)流化床气化的原理与特点
图2-18所示为典型的温克勒气化炉示意图,煤料经过破碎处理后,通过螺旋给料机或气流输送系统进入气化炉,具有一定压力的气化剂从床层下部经过布风板吹入,将床上的碎煤托起,当气流速度上升到某一定值时,煤粒互相分开上下翻滚,同时床层膨胀且具有了流体的许多特性,即形成了流化床。根据流态化原理,影响流态化过程的主要因素是气流速度,即通过床层界面的平均流速,如果气流速度小于某一定值,则煤粒将不能流化,床层有结渣的危险。通常根据试验来选择确定最佳流化速度,并作为气化炉的操作气速。另外流化效果还受煤粒粒径的影响,如果煤粒太小,则将随煤气夹带出炉外,如果煤粒太大,则很难流化。工业中粒度要求较移动床要小,一般在0.1~6mm左右。
在流化床中,通常将气化温度控制在950℃,以免在流化不均引起局部过热时,产生局部结渣从而使流化状态破坏。因此,与移动床相比,其氧化反应进行得比较缓慢,而且只能用于气化反应性较好的煤种,如褐煤等。但在流化床内部由于燃料颗粒与气化剂混合良好,其温度沿床层高度的变化比固定床平稳。图2-19为流化床和移动床的温度分布比较。
与固定床类似,在流化床气化区仍分为氧化层和还原层,但其还原层温度较高且一直可以延伸到整个床层。流化床气化煤气中CO2的含量较高,这是由于床层燃料量较固定床少,所以还原反应进行得不完全,使得煤气中CO2含量较高,同时由于床内温度分布均匀,粗煤气出口温度较高。同时在流化床内由于具有良好的传质传热性能,因此进入气化炉的燃料可以迅速地分布在炽热颗粒之间而迅速加热,其干燥和热解过程在反应区同时进行,使得挥发分的分解完全,煤气中热解产物的含量很少,几乎不含焦油。
总的来说,由于流化床温度均匀,气固混合良好,同时煤的粒度小,比表面积大,因此能获得较高的气化强度和生产能力。但其缺点也同样突出,在流化状态下,很难将灰渣和料层进行分离,70%的灰及部分未燃尽炭被煤气夹带出气化炉,既增加了煤气净化的难度,也造成很大程度的热损失。同时,另外的灰分通过黏结落入灰斗,灰渣和飞灰的含碳量均较高,这是流化床气化最大的问题。

(2)灰团聚流化床煤气化技术
为了保持床层中的高炭灰比和稳定的不结渣操作,流化床内部物料必须良好混合,这样其排料组成与床内物料相同,排出的固体灰渣以及煤气带出物的含碳量就比较高(15%~20%)。为此提出了灰团聚(或称灰熔聚、灰黏聚)技术,具体措施是在流化床层形成局部高温区,使煤中的灰分在软化而未熔融的状态下,相互团聚而黏结成含碳量较低的灰渣,结球长大到一定程度时靠其重量与煤粒分离下落到炉底灰渣斗,从而有选择性地将灰球排出炉外,降低了灰渣的含碳量(5%~10%)。这一技术在一定程度上既克服了固态排渣碳损失高,又避免了液态排渣高显热损失和对床层的影响,提高了气化过程的碳转化率,是煤气化排渣技术的重要突破。
目前采用灰团聚排渣技术的有美国的U-gas气化炉、KRW气化炉和中国科学院山西煤炭化学研究所的ICC煤气化炉。美国开发的U-gas和KRW灰团聚气化工艺还同时进行了炉内脱硫试验,取得了脱硫效率达80%~90%的好结果。采用这一工艺生产的煤气可供联合循环发电(IGCC)作为燃料使用。
(3)循环流化床煤气化技术
循环流化床(CFB)气化炉的流化速度范围大于传统流化床速度而小于气动提升管速度,根据气化原料的种类,以气/固速度差异最大为特征,在两者之间选择合适的速度。物料循环量比传统流化床高,可达40倍以上。
循环流化床气化过程可克服鼓泡流化床中存在大量气泡造成气固接触不良的缺点,同时可避免气流床所需过高的气化温度,克服大量煤转化为热能而不是化学能的缺点,综合了气流床和鼓泡床的优点。CFB的操作气速介于鼓泡床和气流床之间,煤颗粒与气体之间有很高的滑移速度,使气固两相之间具有更高的传热传质速率。整个反应器系统和产品气的温度均一,不会出现鼓泡床中局部高温造成结渣。CFB可在高温(接近灰软化温度)下操作,使整个床层都具有很高的反应能力。CFB除外循环还存在内循环,床中心区颗粒向上运动,而靠近炉壁的物料向下运动,形成内循环。新加入的物料和气化剂能与高温循环颗粒迅速而完全混合,加上良好的传质传热,可使新加入的低温原料迅速升温,并在反应器底部就开始气化反应,使整个反应器生产强度增加。另外,由于循环比率高达几十倍,使颗粒在床内停留时间增加,碳转化率也得到提高。
2.5.3.3 气流床气化法
气流床气化法用极细的粉煤为原料,被氧气和水蒸气组成的气化剂高速气流携带进入并在气化炉内进行充分的混合、燃烧和气化反应。气流床气化是气固并流,气体与固体在炉内的停留时间几乎相同,都比较短,一般在1~10s。煤粉气化的目的是通过增大煤的比表面积来提高气化反应速率,从而提高气化炉的生产能力和碳的转化率。
气流床气化法属于高温气化技术,从操作压力上可分为常压气化与加压气化,除K-T炉为常压气化外,其他炉型均采用加压气化的方式。在气流床气化时,一般很少用空气做气化剂,基本都直接用氧气和过热蒸汽作为气化剂,因此,在炉内气化反应区温度可高达2000℃。由于煤被磨得很细,具有很大的比表面积,又处于加压条件下,因此气化反应速率极快,气化强度和单炉气化能力比前两类气化技术都高。气流床气化的主要特点表现为煤种适应性强,煤粉在气化炉中的停留时间极短,煤气中夹带有大量未反应的碳,不利于CH4的生成,煤气中CO含量高、热值低,粗煤气中不含焦油、酚及烃类液体等污染物,煤气温度高(一般都在1400℃左右)等。
2.5.3.4 熔融床气化法
熔融床气化法的特点是在温度较高(1600~1700℃)且高度稳定的熔融金属或金属盐熔池内,完成气化反应的全部过程,生成以CO和H2为主的煤气,煤的转化率高达99%。熔融床气化反应过程是一种属于气、液、固三相反应的气化方法,其间不只是煤与气化剂发生反应,熔融介质也直接或间接地参与了反应过程。其最大的特点是能够改善气固接触状况,并具有一定的催化作用,使得煤种适应性较广,然而熔融物对于炉膛的腐蚀以及熔融物再生等问题阻碍了这类气化炉的进一步发展。
熔融物的作用是:作为煤和气化剂的分散剂,蓄热和提供气化反应热。依据熔融介质的种类不同可分为熔渣床气化法、熔铁床气化法和熔盐床气化法三类,如表2-6所示。
表2-6 熔渣床、熔铁床及熔盐床气化法的特点比较

2.5.3.5 煤炭地下气化
煤炭地下气化(underground coal gasification,UCG)是对地下煤层就地进行气化产生煤气的一种气化方法。在某些场合,如煤层埋藏很深、甲烷含量很高,或煤层较薄、灰分含量高、顶板状况险恶,进行开采既不经济又不安全时,如能采用地下气化方法则可以解决这些问题。因此,地下气化不仅是一种造气的工艺,也是一种有效利用煤炭的方法,提高了煤炭的实际可采储量。此外,地下气化可从根本上消除煤炭开采的地下作业,将煤层所含的能量以清洁的方式输出地面,而残渣和废液则留于地下,从而大大减轻采煤和制气对环境造成的污染。
煤炭地下气化的原理与一般气化原理相同,即将煤与气化剂作用转化为可燃气体。其基本过程如图2-20所示,从地表沿着煤层开掘两个钻孔1和2。两钻孔底有一水平通道3相连接,图中1、2、3所包围的整体煤堆,即为进行气化的盘区4。在水平通道的一端(如靠近钻孔1处)点火,并由钻孔1鼓入空气,此时即在气化通道的一端形成一燃烧区,其燃烧面称为火焰工作面。生成的高温气体沿气化通道向前渗透,同时把其携带的热量传给周围的煤层,在气化通道中形成由燃烧区(Ⅰ)、还原区(Ⅱ)、干馏区(Ⅲ)和干燥区(Ⅳ)组成的气化反应带。

图2-20 煤炭地下气化反应带示意
1,2—钻孔;3—水平通道;4—气化盘区;5—火焰工作面;6—崩落的岩石;Ⅰ—燃烧区;Ⅱ—还原区;Ⅲ—干馏区;Ⅳ—干燥区
随着煤层的燃烧,火焰工作面不断地向前、向上推进,火焰工作面下方的折空区不断被烧剩的灰渣和顶板垮落的岩石所充填,同时煤块也可下落到折空区,形成一反应性高的块煤区。随着系统的扩大,气化区逐渐扩及整个气化盘区的范围,并以很宽的气化前沿向出口推进。
由钻孔2到达地面的是焦油和煤气,燃气热值约为4000kJ/m3左右,煤气的组成大致为CO2:9%~11%;CO:15%~19%;H2:14%~17%;O2:0.2%~0.3%;CH4:1.4%~15%;N2:53%~55%。
煤炭地下气化集建井、采煤、气化三大工艺于一体,抛弃了庞大笨重的采煤设备和地面气化设备,变传统的物理采煤为化学采煤,是多学科开发清洁能源和化工原料的高新技术,大大减少了煤炭生产和使用过程中所造成的环境破坏,并可大大提高煤炭资源的利用率,被誉为第二代采煤方法和煤炭加工及综合利用的最佳途径,深受世界各国重视,也是中国洁净煤发展的重要方向之一。但由于地下煤层的构成及其走向变化多端,虽经多年的研究试验,但至今尚未形成一种工艺成熟、技术可靠、经济合理的地下气化方法,有待今后的努力探索。