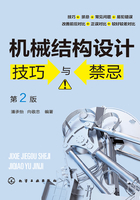
1.1 螺纹连接结构设计技巧与禁忌
1.1.1 螺纹类型选择技巧与禁忌
(1)螺纹主要类型、特点及应用
通过螺纹轴线剖切时,螺纹断面的轮廓形状称为螺纹的牙型。常用的螺纹牙型有三角形、矩形、梯形和锯齿形,其牙型图、特点及应用见表1⁃1。
表1⁃1 常用螺纹的类型、牙型图、特点及应用

(2)几种常用螺纹性能对比
表1⁃1所列4种牙型螺纹连接的自锁性、效率、强度、工艺性等性能对比见表1⁃2。
表1⁃2 常用螺纹性能对比

(3)螺纹类型选择技巧与禁忌
① 矩形螺纹不能用于连接 矩形螺纹因自锁性差,不能用于连接,且相同尺寸的矩形螺纹比三角形螺纹根部面积小,其强度也比三角形螺纹低。三角形螺纹由于自锁性好,一般主要用于连接中。
② 梯形螺纹不能用于连接 梯形螺纹自锁性不如三角形螺纹,其效率比三角形螺纹高,但比矩形螺纹低。由于梯形螺纹比矩形螺纹根部面积大,因此其强度比矩形螺纹高。综合考虑,梯形螺纹是工程上用得最多的一种传力螺纹。
③ 在薄壁容器或设备上不宜采用粗牙螺纹 在薄壁容器或设备上一般不用粗牙螺纹,避免对薄壁件损伤太大。因为细牙螺纹牙高小,因此对薄壁件损伤小,并且可以提高连接强度(细牙螺纹比粗牙螺纹根径大,根部面积大)和自锁性。
④ 在一般机械设备上不宜采用细牙螺纹 由于细牙螺纹的螺纹牙强度低,所以一般机械设备上用于连接的螺纹不宜采用细牙螺纹,尤其是受拉螺栓。
⑤ 承受双向轴向力时不能用锯齿形螺纹 锯齿形螺纹牙型剖面为锯齿形,一侧牙型角α=3°,为工作面;另一侧牙型角α=30°,为非工作面,因此锯齿形螺纹只能承受单向轴向力,不能用于双向轴向力的场合。
⑥ 锯齿形螺纹不能用于连接 锯齿形螺纹不能用于连接,因为自锁性不好。
⑦ 普通用途的螺纹一般不选用左旋 普通用途的螺纹一般默认为右旋,只有在特殊情况下,例如设计螺旋起重器时,为了和一般拧自来水龙头的规律相同才选用左旋螺纹;煤气罐的减压阀也选用了左旋螺纹。
⑧ 用于连接的螺纹不能选用双头螺纹和多头螺纹 由于双头螺纹和多头螺纹的自锁性不好,连接性能差,所以不能选用双头螺纹和多头螺纹用于连接。
1.1.2 螺纹连接主要类型设计技巧与禁忌
(1)螺纹连接的主要类型、特点及应用
螺纹连接的主要类型有螺栓连接、双头螺柱连接、螺钉连接、紧定螺钉连接,其特点及应用见表1⁃3。
表1⁃3 螺纹连接的主要类型、特点及应用


(2)螺纹连接类型选用技巧与禁忌
① 被连接件较薄时,不宜采用螺钉连接,而宜采用螺栓连接。
② 被连接件较厚、不宜钻透时,不宜采用螺栓连接,宜采用螺钉连接或双头螺柱连接。两者的区别在于:经常拆卸时采用双头螺柱连接,不经常拆卸时采用螺钉连接。
③ 紧定螺钉连接主要用来固定零件相互位置,不适于用来传递较大的力。
(3)普通螺栓连接结构设计技巧与禁忌
普通螺栓连接也称受拉螺栓连接,是工程中应用最广泛的一种螺纹连接方式。如图1⁃3(a)所示为普通螺栓连接常见错误示例,该螺栓连接有以下错误:
① 整个螺栓装不进去,应该掉过头来安装。
② 不应当用扁螺母,应选用一般螺母,根据GB/T 6175—2000,M12的螺母,厚度m=12mm。
③ 弹簧垫圈的尺寸不对,按标准查出其直径和厚度,如图1⁃13(b)所示。
④ 弹簧垫圈的缺口方向不对。
⑤ 螺栓长度不对,根据被连接件的厚度,按GB/T 5782—2000,应取标准长度60mm。
⑥ 铸造表面应加沉孔。
⑦ 螺栓距离机体侧面太近,扳手空间不足,应向左移一些。
⑧ 两被连接件的孔直径应相同,均大于螺栓大径。
改正后的结构如图1⁃3(b)所示。

图1⁃3 螺栓连接的结构
(4)螺钉连接结构设计技巧与禁忌
如图1⁃4(a)所示的螺钉连接的结构有如下错误:
① 此结构不应当用螺钉连接,因为被连接件的两块板都比较薄,只有当被连件有一个很厚、钻不透时才采用螺钉连接。本结构应改为螺栓连接,具体结构和尺寸如图1⁃4(b)所示。
② 如果为螺钉连接,上边的板应该开通孔,螺钉的螺纹应与下边的板相拧紧[图1⁃4(c)]。
③ 铸造表面应加沉孔。
④ 一般可不必采用全螺纹。
改正后的结构如图1⁃4(b)、(c)所示。

图1⁃4 螺钉连接的结构
(5)双头螺柱连接结构设计技巧与禁忌
当被连件有一个很厚、钻不透时,采用双头螺柱连接,与螺钉连接的区别就在于:经常拆卸时采用双头螺柱连接,以保护较厚的被连接件的内螺纹不受破坏。如图1⁃5(a)所示的双头螺柱连接的结构有如下错误:
① 双头螺柱的光杆部分不能拧进被连接件的内螺纹。
② 锥孔角度应为120°,且画到了内螺纹的外径,应该画到钻孔的直径处。
③ 被连接件为铸造表面,安装双头螺柱连接时必须将表面加工平整,故采用沉孔。
④ 螺母的厚度不够,正确尺寸为12mm。
⑤ 弹簧垫圈的厚度不对,正确尺寸为3.1mm。
改正后的结构如图1⁃5(b)所示。

图1⁃5 双头螺柱连接的结构
(6)紧定螺钉连接结构设计技巧与禁忌
固定零件位置时经常采用紧定螺钉连接。如图1⁃6(a)所示的紧定螺钉连接的结构有如下错误:
① 螺钉掉在孔里,无法拧进。因为轴套上为光孔,没加工出螺纹,因此螺钉拧不进。应当在轴套上加工出内螺纹,才能使螺钉拧入。
② 螺钉不应拧进轴。
可以改为如图1⁃6(b)所示的结构,即轴套上加工成螺纹孔,与紧定螺钉的螺纹相旋合,螺钉末端抵紧在轴上进行定位。

图1⁃6 紧定螺钉连接的结构
1.1.3 螺纹连接结构设计技巧与禁忌
(1)螺纹连接结构应符合力学要求
① 受剪切力较大的连接不宜采用摩擦传力 剪切力较大时,靠摩擦传力的连接结构零件受力大,尺寸大,且传力不可靠,宜采用靠零件形状传力的结构。如图1⁃7(a)所示受剪切力较大的螺栓连接,用普通受拉螺栓连接两板,靠摩擦传力,不如图1⁃7(b)所示的用铰制孔受剪螺栓连接效果更好。

图1⁃7 受剪切力较大的连接不宜采用摩擦传力
② 利用工作载荷改善螺栓受力 有些场合可以利用工作载荷改善结构受力。如图1⁃8所示压力容器的盖,可以利用容器中介质的压力帮助压紧,以减少螺栓的受力。

图1⁃8 利用工作载荷改善螺栓受力
如图1⁃8(a)所示结构较差,如图1⁃8(b)所示结构较好。
③ 紧定螺钉不宜放在承受载荷方向上 设计紧定螺钉的位置时,在承受载荷的方向上放置紧定螺钉是不合适的,不能采取如图3⁃3(a)所示的结构,将紧定螺钉放在承受载荷的方向上,这样螺钉会被压坏,不起紧定作用。改进后的结构如图1⁃9(b)所示。

图1⁃9 紧定螺钉的位置
④ 避免螺纹孔轴线相交 如图1⁃10(a)所示,轴线相交的螺孔交在一起,能削弱机体的强度和螺钉的连接强度。正确的结构如图1⁃10(b)所示,应避免相交的螺孔。

图1⁃10 避免相交的螺孔
⑤ 避免产生附加弯矩
a.铸造表面不宜直接安装螺栓等连接件 铸造表面不应直接安装螺栓、螺钉或双头螺柱,因为铸造表面不平整,如果直接安装螺栓、螺钉或双头螺柱,则螺栓、螺钉或双头螺柱的轴线就会与连接表面不垂直,从而产生附加弯矩,如图1⁃11(a)所示,使螺栓受到附加弯曲应力而降低寿命。正确的设计应该是在安装螺栓、螺钉或双头螺柱的表面进行机械加工,例如铸造表面采用如图1⁃11(b)所示的凸台,或采用如图1⁃11(c)所示的沉头座等方式,避免附加弯矩的产生。

图1⁃11 铸造表面的螺纹连接
b.避免使用钩头螺栓产生附加弯矩 采用钩头螺栓时,如图1⁃12(a)所示,会使螺栓产生偏心载荷,这时螺栓除受拉力外还受由偏载引起的附加弯曲应力,从而使螺栓的工作应力大大增加,所以应尽量避免使用。

图1⁃12 避免使用钩头螺栓产生附加弯矩
c.避免连接件表面倾斜使螺栓产生附加弯矩 如图1⁃12(b)所示的结构因被连接件表面倾斜,与螺栓轴心线不垂直,从而使螺栓产生附加弯矩。这种情况下可以采用斜垫圈,如图1⁃12(c)所示。
d.避免被连接件因刚度不足产生附加弯矩 如图1⁃13(a)所示为被连接件刚度太小造成的螺栓附加弯矩,应当避免。应当使被连接件有足够的刚度,如图1⁃13(b)所示,加厚被连接件可增大被连接件刚度,结构合理。

图1⁃13 被连接件应有足够的刚度
⑥ 有利于夹紧力的螺钉连接 如图1⁃14所示为经常遇到的把某一机件牢固地安装在轴、杆或管子上的情况,要求能调整位置并便于装卸,此种情况可采用螺钉连接。如图1⁃14(a)所示的结构,无论怎样夹紧,总是固定不住,常易发生滑移和转动,原因是螺钉固定时,对轴的夹紧力仅限于有切槽的一侧,另一侧未开槽,刚性大,所以无论怎样锁紧螺钉,也总不能紧固,使用时就产生转动和滑移。改进后的结构如图1⁃14(b)所示,将切槽延伸至孔的另一侧,拧紧螺钉时,夹紧力使之发生弹性变形,并传递到轴的四周,将轴牢固地夹住。

图1⁃14 有利于夹紧力的螺钉连接
⑦ 螺母螺纹旋合高度禁忌 螺母的保证载荷是以螺母高度内的螺纹全部旋合而设计的,因此在使用螺母时必须让螺母的螺纹全部旋合。图1⁃15(a)、(b)所示结构不合理,它们减少了旋合的螺纹扣数,不能保证足够的螺纹连接强度,在重要的地方尤其应注意,否则容易引发事故。正确结构如图1⁃15(c)所示。

图1⁃15 螺母螺纹旋合高度
⑧ 提高螺栓疲劳强度的结构
a.采用柔性螺栓可以提高螺栓的疲劳强度 理论分析表明,降低应力幅σa可提高螺栓连接的疲劳强度。在一定的工作载荷F作用下,螺栓总拉力F0一定时,减小螺栓刚度C1或增大被连接件刚度C2,都能使应力幅σa减小,从而提高提高螺栓的疲劳强度。如图1⁃16(a)所示,采用加粗螺栓直径的方法,对提高螺栓疲劳强度并无裨益,这样只增加了螺栓的整体强度,而并未降低螺栓的刚度。一般情况下,减小螺栓的刚度可采用如下措施:采用细长杆的螺栓、柔性螺栓(即部分减小螺杆直径或中空螺栓),如图1⁃16(b)所示。

图1⁃16 采用柔性螺栓可以提高螺栓的疲劳强度
b.压力容器密封设计与螺栓的疲劳强度 如上所述,减小连接件刚度或增大被连接件刚度,均可提高螺栓连接疲劳强度。如图1⁃17(a)所示为压力容器,用刚度小的普通密封垫,就相当于减小了被连接件的刚度,因此降低了螺栓的疲劳强度。如果改为如图1⁃17(b)所示的结构,即被连接件之间无垫片,开密封槽并放入橡胶密封环进行密封,就增大了被连接件的刚度,因此比前一种大大提高了螺栓的疲劳强度。

图1⁃17 压力容器两种密封方案比较
c.特殊结构螺母可提高螺栓疲劳强度 悬置螺母[图1⁃18(a)]的旋合部分全部受拉,其变形性质与螺栓相同,栓杆与螺母的变形一致,减小螺距变化差,螺纹牙受力较均匀,可提高螺栓疲劳强度达40%。

图1⁃18 提高疲劳强度的特殊结构螺母
内斜螺母[图1⁃18(b)]可减小原受力大的螺纹牙的刚度,而把力分移到原受力小的牙上,可提高螺栓疲劳强度达20%。
环槽螺母[图1⁃18(c)]利用螺母下部受拉且富于弹性的特性,可提高螺栓疲劳强度达30%。
以上这些结构特殊的螺母制造费工,只在重要的或大型的连接中使用。
d.增大螺栓头根部圆角可提高螺栓疲劳强度 如图1⁃19(a)所示的螺栓头根部圆角太小,因此应力集中太大。如图1⁃19(b)所示的结构,螺栓头根部圆角增大,因此减小了应力集中,提高了螺栓的疲劳强度。如图1⁃19(c)所示的结构,螺栓头根部圆角更大,因此更加显著地减小了应力集中,提高螺栓疲劳强度效果好。

图1⁃19 螺栓头根部圆角对疲劳强度的影响
e.变载荷条件下容器不宜用短螺栓连接 如图1⁃20上半部分所示容器,缸体与缸盖的连接,在常温、动载荷条件下采用了短螺栓连接,不如图1⁃20下半部分所示采用等截面长螺栓连接,因为后者较前者的螺栓刚度小,可提高螺栓疲劳强度,且前者还增加了螺栓的数量和装卸的工作量,结构设计不如后者合理。

图1⁃20 变载荷条件下容器不宜用短螺栓连接
(2)螺纹连接结构应满足工艺性要求
① 螺纹孔边结构应易于装拆 如图1⁃21(a)所示,螺纹孔边没倒角,拧入螺纹时容易损伤孔边的螺纹。如图1⁃21(b)所示的螺纹孔边加工成倒角,较为合理。

图1⁃21 螺纹孔边结构应易于装拆
② 螺纹连接装拆时要有足够的操作空间 螺栓、螺钉和双头螺柱连接必须考虑安装及拆卸要有足够的操作空间。如图1⁃22(a)所示的结构,安放螺钉的空间太小,无法装入和拆卸螺钉。如图1⁃22(b)所示,L应大于螺钉的长度,才能装拆螺钉。

图1⁃22 螺纹连接装拆时要有足够操作空间
③ 螺纹连接装拆时要留扳手空间 设计螺栓、螺钉和双头螺柱连接的位置时还必须考虑留有足够的扳手空间。如图1⁃23(a)所示扳手空间不足,不利于操作。如图1⁃23(b)所示为考虑了标准扳手活动空间的结构。

图1⁃23 螺纹连接装拆时要留扳手空间
④ 经常拆装的外露螺纹的处理 在经常拆卸的地方,螺栓的外露部分容易受到扳手、锤子等碰伤而使螺纹破坏,给拆装带来麻烦,因此在经常拆装的地方(如夹具上的螺栓等),禁止采用图1⁃24(a)、(b)的结构,即仅保持螺栓原来的倒角平头,而应将外露部分的螺纹切去,如图1⁃24(c)所示,避免螺纹的破坏,尤其是大直径的螺栓更应该如此。

图1⁃24 经常拆装的外露螺纹的处理
⑤ 避免螺栓在机架下方装入 零件的结构要考虑到装、拆要求,保证零件能够正确安装,还要便于拆卸。如图1⁃25(a)所示,要想拆卸螺栓,必须先拆卸地脚螺栓,卸下底座是不合理结构。合理结构如图1⁃25(b)所示,改用双头螺柱连接较好。

图1⁃25 避免螺栓在机架下方装入
⑥ 避免错误安装 有些螺栓零件仅有细微的差别,安装时很容易弄错,应在结构上突显其差异,以便于安装。如图1⁃26(a)所示双头螺柱,两端螺纹都是M16,但长度不同,安装时容易弄错,如将其中一端改用细牙螺纹M16×1.5(另一端仍用标准螺纹M16,螺距为2mm),则不容易弄错;若将另一端改为M18,如图1⁃26(b)所示,则更不容易弄错,但加工困难些。

图1⁃26 避免错误安装的双头螺柱
⑦ 螺栓连接外露部分不宜过长 螺栓连接外露部分不宜过长,如图1⁃27(a)所示,螺栓的外露部分a太长,结构不紧凑,占空间大,也浪费材料、增加重量,且容易受到扳手、锤子等碰伤而使螺纹破坏,给拆卸带来麻烦。所以,如图1⁃27(b)所示,螺栓在螺母外的伸出长度一般取a=(0.2~0.3)d为宜。
⑧ 螺纹连接部分结构尺寸设计应规范 图1⁃28(a)中,螺钉的钻孔深度L2、攻螺纹深度L1都没按标准设计,正确的应如图1⁃28(b)所示,钻孔、攻螺纹、旋入深度必须按标准进行设计。

图1⁃27 螺栓连接外露部分不宜过长

图1⁃28 螺钉连接结构
1.1.4 螺栓组连接的结构设计技巧与禁忌
(1)螺栓组连接结构应符合力学要求
① 螺栓组的布置应使各螺栓受力合理 对承受旋转力矩或翻转力矩的螺栓组连接,应使螺栓的位置适当靠近结合面的边缘,以减小螺栓的受力。如图1⁃29(a)所示螺栓受力较大,不合理。如图1⁃29(b)所示螺栓受力合理。

图1⁃29 受旋转力矩或翻转力矩时螺栓组的布置
② 在平行力的方向螺栓排列设计禁忌 如图1⁃30(a)所示,如果在平行外力的方向并排地布置9个螺栓,此时各螺栓受力不均,且间距太小。建议改为图1⁃30(b)所示的9个螺栓的布置,使螺栓受力均匀,设计时还要注意螺栓排列应有合理的间距、边距和留有扳手空间。

图1⁃30 在平行力的方向螺栓的排列
③ 受斜向拉力的吊环螺钉固定禁忌 如图1⁃31(a)所示的吊环螺钉是不合理的结构,因为吊环螺钉没有紧固座面,受斜向拉力,极容易在a处发生断裂而造成事故。合理的结构如图1⁃31(b)所示,应当采用带座的吊环螺钉。

图1⁃31 吊环螺钉的固定
④ 两个焊接件间螺纹孔设计禁忌 两个焊接件间不要有穿透的螺纹孔,如图1⁃32(a)所示,螺纹连接受力情况不好。对焊接构件,螺纹孔既不要开在搭接处,更不要设计成穿通的结构,以防止泄漏和降低螺钉连接强度。改进后的结构如图1⁃32(b)所示。

图1⁃32 两个焊接件间的螺纹孔
⑤ 高强度连接螺栓设计禁忌 高强度螺栓连接是继铆接、焊接之后采用的一种新型钢结构连接形式。靠高强度螺栓以巨大的夹紧压力所产生的摩接力来传递载荷,强度又取决于高强度螺栓的预紧力、钢板表面摩擦因数、摩擦面数及高强度螺栓的数量。它具有施工安装迅速、连接安全可靠等优点,特别适用于承受动力载荷的重型机械上。目前国外已广泛用于桥梁、起重机、飞机等的主要受力构件的连接。
对于高强度连接螺栓结构,在装配图中应注意以下问题:
a.标明预紧力要求。为使连接性能达到预期效果,应在图纸中标明预紧力及需用力矩扳手(或专用扳手)拧紧等。
b.注明特殊要求。为防止连接面滑移,应在图样中注明喷丸(砂)等处理,以及不得有灰尘、油漆、油迹和锈蚀等要求。
高强度连接螺栓结构还应注意对承压面的保护。如图1⁃33(a)所示的高强度连接螺栓只有一个垫圈,易造成连接体表面挤压损坏,应由两个高强垫圈组成,如图1⁃33(b)所示。

图1⁃33 高强度连接螺栓应注意保护承压面
1—螺栓头;2—螺母;3—垫圈
⑥ 往复载荷作用下防止被连接件窜动设计禁忌 滑动件的螺钉固定,例如滑动导轨,最好不用如图1⁃34(a)所示的结构,即只用沉头螺钉固定。因为这样固定只有一个螺钉能保证头部紧密结合,另外几个螺钉则由于必然存在加工误差而不能紧密结合,在往复载荷作用下,必然造成导轨的窜动。正确的结构是:如图1⁃34(b)所示,采用在端部能防止导轨窜动的结构。

图1⁃34 滑动件的螺钉固定结构
⑦ 螺钉位置与被连接件刚度设计禁忌 螺钉在被连接件的位置不要随意布置,应该布置在被连接件刚度最大的部位。如图1⁃35(a)所示,将螺钉布置在被连接件刚度较小的凸耳上不能可靠地压紧被连接件,为较差结构。图1⁃35(b)所示结构较好,加大边缘部分的宽度,提高刚度,可使结合面贴合得好一些。还可以在被连接件上加十字或交叉对角线的肋以提高刚度,对提高螺钉连接的紧密性效果更好,如图1⁃35(c)所示。

图1⁃35 螺钉在被连接件的位置
⑧ 换热器的螺栓连接 由于结构的需要,换热器的螺栓用于换热器的壳体、管板和管箱之间,用于将它们三者连接起来。连接时禁止简单地采用如图1⁃36(a)所示的普通螺栓连接的方法。因为换热器管程和壳程的压力一般差别较大,采用同一个穿通的螺栓不能同时满足两边压力的需要,另外,也给维修带来不便,即:要拆一起拆、要装一起装,不能或不便于分别维修。应该采用如图1⁃36(b)所示的结构,螺栓为带凸肩的螺栓,这样,可以根据两边不同的压力要求,选择不同尺寸的螺栓,也可以分别进行维修。

图1⁃36 换热器的螺栓连接
⑨ 磁选机盖板与隔块的螺栓连接

图1⁃37 磁选机盖板与铜隔块的螺栓连接
如图1⁃37所示为磁选机盖板与铜隔块的连接,螺栓是用碳钢制作的。禁止采用如图1⁃35(a)所示的连接结构。因为螺栓在运行中受到磁拉力脉动循环外载荷作用,易早期疲劳,出现螺栓卡磁头,造成螺栓折断,且折断的螺栓不便于取出。应采用如图1⁃37(b)所示的结构,成倒挂式连接,一旦出现螺栓折断,更换方便,昂贵的隔块也不会报废。
(2)螺栓组连接结构应满足工艺性要求
① 圆形布置螺栓组连接螺栓个数禁忌 如图1⁃38(a)所示,一组螺栓连接做圆形布置时设计成7个螺栓,即设计成了奇数,不便于加工时分度。应该设计成如图1⁃38(b)所示的8个螺栓,才便于分度及加工。所以得出结论:分布在同一圆周上的螺栓数目应取4、6、8、12等易于分度的偶数,以利于划线钻孔。

图1⁃38 圆形布置螺栓组连接螺栓的个数
② 螺纹孔钻孔时要留有加工余量 如图1⁃39(a)、(c)所示箱体的螺纹孔是不合理的结构,因为此结构没有留出足够的凸台厚度,尤其在要求密封的箱体、缸体上开螺纹孔时,无法保证在加工足够深度的螺纹孔时,不会将螺纹孔钻透而造成泄漏。在设计铸造件时,应考虑预留足够厚度的凸台,更应该考虑到铸造工艺有非常大的误差,必须留出相当大的加工余量。应采用如图1⁃39(b)、(d)所示的结构。

图1⁃39 箱体的螺纹孔结构
③ 高速旋转部件注意安全防护 高速旋转部件上的螺栓头部不允许外露,如图1⁃40(a)所示的结构是错误的,在高速旋转的旋转体上的螺栓,例如工业上广泛使用的联轴器,禁止将螺栓的头部外露,应将其埋入罩内,如图1⁃40(b)所示。如果能采用如图1⁃38(c)所示的结构,即用安全罩保护起来就更好了。

图1⁃40 高速旋转部件的螺栓连接结构
④ 用多个沉头螺钉固定零件禁忌 如图1⁃41(a)所示,用多个锥端沉头螺钉固定一个零件时,如有一个钉头的圆锥部分与钉头锥面贴紧,则由于加工孔间距误差,其它钉头不能正好贴紧。如改用圆柱头沉头螺钉固定,如图1⁃41(b)所示,则可以使每个螺钉都压紧,而使固定比较紧。

图1⁃41 用多个沉头螺钉固定零件的结构
⑤ 管道螺纹连接便于拆卸禁忌 如图1⁃42(a)所示,用双头螺柱连接安装的插入配合式管道,如不使连接的一个或两个机座在轴向移动就不能拆卸,即使不是用插入式管道,拆下螺母后双头螺柱也仍然妨碍管道沿垂直于轴线的方向拆卸,所以这种连接结构不合理。应改为如图1⁃42(b)所示结构,管道不是插入式的,且采用螺钉连接。

图1⁃42 管道螺纹连接
(3)紧密性要求较高的螺栓组连接结构设计技巧与禁忌
① 汽缸盖螺栓连接间距设计禁忌 气密性要求高的连接中,螺栓间距t不宜取得过大。如图1⁃43(a)所示,设计成2个螺栓是不合理的,因为一组螺栓做结构设计时,如相邻两螺栓的距离取得太大,则不能满足连接紧密性的要求,容易漏气等。因此,像汽缸盖等气密性要求高的螺栓组连接,应采用如图1⁃43(b)所示的形式,允许的螺栓最大间距t为:当p≤1.6MPa时,t≤7d;当p=1.6~10MPa时,t≤4.5d;当p=10~30MPa时,t≤(4~3)d。d为螺栓公称直径,t=πD0/z,D0为螺栓分布圆直径,z为螺栓个数。确定螺栓个数z时,应使其满足上述条件。

图1⁃43 汽缸盖螺栓连接的间距
② 法兰螺栓连接的位置禁忌 法兰螺栓连接的设计必须考虑螺栓的位置问题,因为如果采用如图1⁃44(a)所示的结构,将螺栓置于正下方,则该螺栓容易受到管子内部泄漏流体的腐蚀,以致过早破坏或锈死,无法拆卸和维修。应该改变螺栓的位置,安排在如图1⁃44(b)所示的位置。

图1⁃44 法兰螺栓连接的位置
③ 高温环境气、液缸及容器的螺栓组连接方式 高温环境下气、液缸及容器的螺栓连接时,缸体与缸盖的连接不宜采用图1⁃45上半部分所示结构。因为螺栓长,热膨胀伸长量大,会使端盖与缸体的连接松弛,气密性降低。高温条件下,如冶金炉前的液压缸(工作温度有时达200~300°C),应改用图1⁃45下半部分的结构,使用效果良好。

图1⁃45 高温环境气、液缸及容器的螺栓组连接方式
④ 侧盖的螺栓间距要考虑密封性能 侧面的观察窗等的盖子,即使内部没有压力,也会有油的飞溅等情况,从而产生泄漏,特别是在下半部分容易产生泄漏。如图1⁃46(a)所示上、下部分的螺栓等距,不合理。为了避免泄漏,要把下半部分的螺栓间距缩小,一般上半部分的螺栓间距是下半部分的间距的两倍,如图1⁃46(b)所示,较为合理。

图1⁃46 侧盖的螺栓间距要考虑密封性能
⑤ 高压容器上盖与容器的螺栓连接禁忌
a.高压容器密封的接触面宽度宜小 有些容器中有高压的介质,为了密封,要用螺栓扭紧上盖和容器。为了有效地密封,不应该增加接触面的宽度b,如图1⁃47(a)所示。因为接触面愈大,接触面上的压强愈小,愈容易泄漏。有效的方法见图1⁃47(b),在盖上做出一圈凸起的窄边,压紧时可以产生很高的压强。但是应该注意这一圈凸起必须连续不断,凸起的最高点处(刃口)不得有缺口,而且必须有足够的强度和硬度,避免在安装时碰伤或产生过大的塑性变形。

图1⁃47 高压容器密封的接触面宽度宜小
b.用刃口密封时应加垫片 采用凸起的刃口作为高压容器的密封时,若不加垫片[图1⁃48(a)],则由于接触点压力很大,必然使下面的容器口部产生一圈凹槽。经过几次拆装,就会因为永久变形而使密封失效。因此在接触处应加用铜或软钢制造的垫片[图1⁃48(b)],一方面可以使盖上的一圈凸起(刃口)不致损伤,另一方面又可以在装拆时便于更换,以保证密封的可靠性。

图1⁃48 用刃口密封时应加垫片
⑥ 椭圆形法兰螺栓连接与受力方向禁忌 在用两个螺栓的法兰安装的管道上,如果在箭头方向施加弯曲载荷,如图1⁃49(a)所示,则非常容易泄漏。在设计这种形式的法兰时,要考虑不在上述方向加力。改成如图1⁃47(b)或图1⁃49(c)所示的结构,较为合理。

图1⁃49 椭圆形法兰螺栓连接与受力方向
(4)螺钉组连接可靠性优化设计
螺钉组连接除满足强度要求外,还必须满足结构要求、可靠性要求及其它有关工作性能要求等。这使设计时约束条件比较多,常规设计方法很难同时满足多方面条件的要求,即便满足,设计结果也很难达到最优,常常是顾此失彼,尤其是对被连接件材料强度比较弱的螺钉连接,安全可靠性显得尤为重要,容易造成设计不可靠或产品安全裕度过大,使产品尺寸大、笨重,形成材料浪费。而采用现代设计方法,

图1⁃50 木制品螺钉组连接
对其进行可靠性优化设计,则可解决上述问题。通过计算机编程运算,可大大提高设计速度与设计质量。现以木制品螺钉组连接可靠性优化设计为例说明如下。
如图1⁃50所示,一环形木制把手用螺钉组与钢板连接,设把手的拉力为F=1000N,木把手的螺纹牙材料的静曲强度为μs=39MPa,强度储备系数n=1.25。根据结构要求,取安装螺钉中心分布圆直径ϕ为100~160mm,螺钉旋合圈数z为5~10圈,螺纹孔公称直径D为10~20mm,螺钉个数m为2~12个(周向均布),要求木螺纹牙强度可靠度不小于95%,设计确定螺钉组连接的最佳结构参数。
木螺纹牙所受应力及强度均为正态分布,其强度可靠度的确定按正态分布进行计算。为了求得最佳结构参数,采用强度可靠性优化设计。
显然,螺纹孔直径D越细且螺钉旋合圈数z越少,相应的螺钉尺寸越小,价格越低;螺纹孔个数m越少且螺钉中心圆直径ϕ越小,木把手越小,加工成本越低。为使体积最小且成本最低,取设计变量
X=[x1,x2,x3,x4]T=[m,D,z,ϕ]T
(1)建立目标函数
minF(X)=mDzϕ=x1x2x3x4
(2)建立约束条件
由文献[28]可得强度可靠度约束条件为
c
式中,ZR为可靠度系数。ZR与F、μs、n、ϕ、D、z、m等参数有关,具体计算式详见参考文献[28,29]。[R]为要求的可靠度,由已知条件,[R]=0.95。
由参考文献[28]可得扳手空间约束条件为
紧密性约束条件为
结构参数边界条件由已知条件确定如下:
螺钉个数:mmin=2,mmax=12;
螺纹孔直径:Dmin=10mm,Dmax=20mm;
螺钉旋合圈数:zmin=5,zmax=10;
螺钉中心分布圆直径:ϕmin=100mm,ϕmax=160mm。
由以上得出结构参数约束条件为
g4(x)=x1-2≥0 g5(x)=12-x1≥0
g6(x)=x2-10≥0 g7(x)=20-x2≥0
g8(x)=x3-5≥0 g9(x)=10-x3≥0
g10(x)=x4-100≥0 g11(x)=160-x4≥0
(3)计算结果
将已知数据代入相关计算式,并将数值积分程序一并装入随机法优化程序,在计算机上编程序运算,计算结果圆整后为
即螺钉个数m=4,螺钉规格为M12,旋合圈数z=5圈,螺钉分布圆直径ϕ=150mm,连接强度可靠度为99.99%。
本例将强度可靠度作为约束条件进行了结构参数的优化设计,既可满足任一规定可靠度的要求,又可实现结构参数最佳,运算速度快、精度高。
以上设计结果可实现体积最小、成本最低、可靠度高达99.99%的最佳结构,为产品的开发与设计提供了较为先进的设计手段。
1.1.5 螺纹连接防松结构设计技巧与禁忌
(1)螺纹连接防松结构类型、特点及应用
螺纹连接的防松按防松原理可分为摩擦防松、机械防松及破坏螺纹副关系三种方法。摩擦防松工程上常用的有对顶螺母、弹簧垫圈、锁紧螺母等,简单方便,但不可靠。机械防松工程上常用的有开口销与槽形螺母、止动垫片、串联金属丝等,比摩擦防松可靠。以上两种方法用于可拆连接的防松,在工程上广泛应用。用于不可拆连接的防松,工程上可用焊、粘、铆的方法,破坏了螺纹副之间的运动关系。螺纹连接常用的防松方法、结构、特点及应用见表1⁃4。
表1⁃4 螺纹连接常用防松方法、结构、特点及应用


(2)螺纹连接防松结构设计技巧与禁忌
① 对顶螺母防松结构设计禁忌 如图1⁃51(a)所示对顶螺母的设置不合理,下面螺母应该薄一些,因为其受力较小,起到一个弹簧防松垫圈的作用。但是在实际安装过程中,这样安装实现不了,因为扳手的厚度比螺母厚,不容易拧紧,因此,通常为了避免装错,设计时采用两个螺母的厚度相同的办法解决,如图1⁃51(b)所示的结构。

图1⁃51 对顶螺母的设置
② 串联钢丝结构设计禁忌 螺钉组连接采用串联钢丝防松时,必须注意钢丝的穿绕方向,要促使螺钉旋紧。如果串联钢丝的穿绕方向采用如图1⁃52(a)所示的方法,则串联钢丝不仅不会起到防松作用,还将把已拧紧的螺钉拉松,因为连接螺钉一般都是右旋,正确的安装方法为如图1⁃52(b)所示的穿绕方向,才可以拉紧。

图1⁃52 串联钢丝的穿绕方向
③ 圆螺母止动垫圈防松结构设计禁忌 采用圆螺母止动垫圈时要注意,如果垫圈的舌头没有完全插入轴的槽中则不能止动,因为止动垫圈可以与圆螺母同时转动而不能防松。图1⁃53的结构中,件1为被紧固件,件2为圆螺母,件3为轴。图1⁃53(a)中的件5采用的是我国标准圆螺母止动垫圈;图1⁃53(b)中的件4为近年来国外采用的新型圆螺母止动垫圈,不需内舌插入轴槽中,因此轴槽加工量较小,对轴强度削弱较小。

图1⁃53 圆螺母止动垫圈防松结构