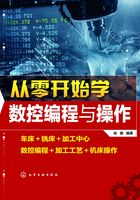
2.3 基本编程指令
2.3.1 刀具快速定位指令G00
G00指令使刀具从所在点快速移动到目标点,用于使刀具快速定位。程序格式:
G00 X(U)_ Z (W)_;
程序中不需要指定快速移动速度,程序中的进给率F与G00不相关,用机床操作面板上的快速移动开关可以调整快速倍率,倍率值为:0、25%、50%、100%。G00指令可以准确控制刀具到达指定点的定位精度,但不控制刀具移动中轨迹,在程序中用于刀具的空行程,一般用于加工前快速定位或加工后快速退刀。G00是模态码,可被同组的其他指令G01、G02、G03或G33功能取代。
例2⁃1:如图2⁃13所示,刀具从P快进到A,分别用绝对坐标方式和增量坐标方式编制程序。
解:
① 工件零点设定在左端面中心处
绝对坐标编程:
G54; 设定左端面中心点为程序原点
G00 X30.0 Z100.0; 刀具从P快进到A点
增量坐标编程:
G00 U⁃270.0 W⁃250.0; 刀具从P快进到A点
② 工件原点设定在右端面中心处
绝对坐标编程:
G54; 设定右端面中心点为程序原点
G00 X30.0 Z0; 刀具从P快进到A点
增量坐标编程:
G00 U⁃270.0 W⁃250.0; 刀具从P快进到A点
例2⁃2:如图2⁃14所示,工件零点设定在右端面中心处,刀具从P快进到A,分别用绝对坐标方式和增量坐标方式编制程序。
解:刀具从P快进到A点(直径编程)
① 绝对坐标编程:G54 G90 G00 X20.0 Z0;
② 增量坐标编程:G00 U⁃80.0 W⁃150.0;
③ X轴绝对坐标编程,Z轴增量坐标编程:G00 X20.0 W⁃150.0;
上述三种表示方法效果等同。
2.3.2 直线插补指令G01
G01指令使刀具以F指定的进给速度沿直线移动到指定的位置。程序格式:
G01 X(U)_ Z(W)_ F_;
G01可用于刀具沿直线的切削运动。绝对坐标编程采用“X”“Z”,表示刀具运动终点在工件坐标系中的位置。增量坐标编程采用“U”“W”,表示刀具运动终点相对起点的移动距离。“F”码给定刀具沿直线运动的进给速度,“F”是模态码,指定的进给速度一直有效,直到指定新值,因此不必对每个程序段都指定“F”。如果没有指令“F”代码,进给速度被当成0,刀具不运动。
进给速度的钳制:用 1422号参数可设定进给速度的上限,如果实际进给速度(用了倍率后)超过指定的上限,就被钳制到上限值。
例2⁃3:图2⁃15中零件各表面已完成粗加工,试分别用绝对坐标方式和增量坐标方式编写精车外圆的程序段。走刀路线:P→A→B→C→D→E→P。

图2⁃15 G00、G01指令练习
解:
① 绝对坐标编程:
G54 G00 X150.0 Z100.0; 设定坐标系,快速定位到P
G00 X18.0 Z5.0; 快速定位P→A
G01 X18.0 Z⁃15.0 F0.2; 切削A→B,进给速度200mm/min
G01 X30.0 Z⁃26 .0; 切削B→C
G01 Z⁃36.0; 切削C→D
G01 X42.0; 切出退刀D→E
G00 X150.0 Z100.0; 快速回到起点E→P
② 增量坐标编程(运动始点P):
G00 U⁃132.0 W⁃95.0; 快速定位P→A
G01 W⁃20.0 F0.2; 切削A→B,进给速度200mm/min
G01 U12.0 W⁃11.0; 切削B→C
G01 W⁃10.0; 切削C→D
G01 U12.0; 切削D→E
G00 U108.0 W136.0; 快速回到起点E→P
③ 绝对坐标和增量坐标混合编程:
G54 X150.0 Z100.0; 设定坐标系,快速定位到P(绝对坐标编程)
G00 X18.0 W⁃95.0; 快速定位到A(混合编程)
G01 W⁃20.0 F0.2; 切削A→B,进给速度200mm/min(增量坐标编程)
G01 X30.0 W⁃11.0; 切削B→C(混合编程)
G01 W⁃10.0; 切削C→D
G01 X40.0; 切削D→E
G00 X150.0 Z100.0; 快速回到起点P(绝对坐标)
上述三种编程方法效果相同。
例2⁃4:如图2⁃16所示工件,试编写车削圆锥面AB程序。走刀路线:P→A→B→P。

图2⁃16 G01指令编程练习
解:程序如下。
O304 程序名
N10 G50 X180.0 Z245.0; 设定坐标系,工件原点在工件的左端面,如图2⁃16所示
N20 M03 S500; 启动主轴
N30 G00 X20.0 W⁃44.0; 定位到A点
N40 G01 U30.0 Z50.0 F0.2; 切削AB
N50 G00 X180.0 Z254.0; 定位到P点
N60 M30; 程序结束
2.3.3 圆弧插补指令G02、G03
指令刀具按顺时针(逆时针)进行圆弧加工用指令G02(G03)。程序格式:
X(U)_ Z(W)_
F_;
G02(G03)指令刀具从圆弧起点向圆弧终点进行圆弧插补,沿圆弧的进给速度用F指令给定。程序段中各指令含义如下。
G02——顺时针方向圆弧插补 (CW);
G03——逆时针方向圆弧插补 (CCW);
X,Z——绝对坐标编程,数值为圆弧终点在工件坐标系中的坐标;
U,W——增量坐标编程,数值为圆弧终点相对圆弧起点的位移量;
I,K——X、Z轴上圆心相对于圆弧起点的增量(圆心的坐标减去圆弧起点的坐标获得的值),注意在直径或半径编程中,I都是半径值;
R——圆弧半径,当圆弧圆心角小于180°时R为正值,否则R为负值,程序段中同时编入R与I、K时,R有效;
F——沿圆弧轨迹的合成进给速度。
说明如下。
① G02为顺时针圆弧插补指令,G03为逆时针圆弧插补指令。圆弧的顺、逆时针方向规定是:朝着与圆弧所在平面垂直的坐标轴的负方向看,刀具沿圆弧顺时针运动为G02,沿圆弧逆时针运动为C03。后置刀架车床[图2⁃9(b)]刀具在机床上圆弧的顺、逆时针运动方向如图2⁃17(a)所示。前置刀架车床[图2⁃8(b)]由于Y轴正向指向纸内,规定观察方向是从纸里向外看确定圆弧的顺、逆时针运动方向,所以正面看如图2⁃17(b)所示。为避免出现错误,编程时不用考虑刀架位置,一律按后置刀架[图2⁃17(a)]的刀具位置编程,这样不会出错。

图2⁃17 刀具圆弧运动的顺、逆方向
② 采用绝对坐标编程时X、Z为圆弧终点坐标值;采用增量坐标编程时U、W为圆弧终点相对圆弧起点的坐标增量(距离)。
③ I、K后面的数值分别是在X、Z轴方向上,圆弧起点到圆心的距离(用半径值表示,与绝对坐标编程和增量坐标编程无关),圆心在起点的正向是正值(+),圆心在起点的负向为负值(-),即I、K为圆弧起点到圆心的矢量分量,如图2⁃18所示(图中I、K都是负值)。I、K为零时可以省略。
④ R是圆弧半径,当圆弧所对圆心角为0°~180°时,R取正值;当圆心角为180°~360°时,R取负值。
例2⁃5:工件如图2⁃19所示,走刀路线为P→A→B→C→D,试分别用数据R和数据I、K编写圆弧程序。
解:

图2⁃18 圆弧指令中I,K的含义

图2⁃19 圆弧指令练习
① 用数据R编写圆弧程序:
N10 G54; 设定左端面中心点为程序原点
N20 G00 X0 Z70.0; 快速定位到切入点P
N30 G01 Z65.0 F0.1; 切入到A
N40 G03 X30.0 Z50.0 R15.0 F0.1; 切削弧AB
N50 G01 Z40.0; 切削直线BC
N60 G02 X50.0 Z30.0 R10.0; 切削弧CD
N70 M02; 程序结束
② 用数据I、K编写圆弧程序:
N10 G54; 设定左端面中心点为程序原点
N20 G00 X0 Z70.0; 快速定位到切入点P
N30 G01 Z65.0 F0.1; 切入到A
N40 G03 X30.0 Z50.0 I⁃5.0 F0.1; 切削弧AB(程序中K=0,可不写)
N50 G01 Z40.0; 切削直线BC
N60 G02 X50.0 Z30.0 K10.0; 切削弧CD(程序中I=0,可不写)
N70 M02; 程序结束
例2⁃6:工件如图2⁃20所示,精车外圆,走刀路线为P→A→B→C→D→E→F,试分别用绝对坐标方式和增量坐标方式编程。

图2⁃20 精车外圆工件图
解:精车外圆(走刀一次)程序如下。
① 绝对坐标编程程序:
G54 设定右端面中心点为程序原点
G00 X12.0 Z5.0; 快速定位到切入点P
G01 Z0 F0.1; 切入到A
G03 X34.0 Z⁃5.0 K⁃5.0(或R5.0) F0.1; 切削弧AB
G01 Z⁃20.0; 切削BC
G02 Z⁃40.0 R20.0; 切削弧CD
G01 Z⁃58.0; 切削DE
G02 X50.0 Z⁃66.0 I8.0(或R8.0); 切削弧EF
M02; 程序结束
② 增量坐标编程:
G54; 设定右端面中心点为程序原点
G00 X24 .0 Z5.0; 快速定位到切入点P
G01 Z0 F0.1; 切入到A
G03 U10.0 W⁃5.0 K⁃5.0(或R5.0) F0.1; 增量坐标编程切削弧A→B
G01 W⁃15.0; 切削B→C
G02 W⁃20.0 R20.0; 切削弧C→D
G01 W⁃18.0; 切削D→E
G02 U16.0 W⁃8.0 I8.0(或R8.0); 切削弧E→F
M02; 程序结束
③ 绝对坐标和增量坐标混合编程:
G54; 设定右端面中心点为程序原点
G00 X24.0 Z5.0 快速定位到切入点P;
G01 Z0 F0.1; 切入到A
G03 X34.0 W⁃5.0 K⁃5.0(或R5.0)F0.1; 混合编程切削弧A→B
G01 W⁃15.0; 切削B→C
G02 W⁃20.0 R20.0; 切削弧C→D
G01 W⁃18.0; 切削D→E
G02 X50.0 W⁃8.0 I8.0(或R8.0); 切削弧E→F
M02; 程序结束
例2⁃7:工件如图2⁃21所示,编写精车孔程序。

图2⁃21 精车孔工件图
解:程序如下。
O320 程序名
N10 T0101; 选车刀和刀具补偿
N20 G50 M03 S600; 选择工件坐标系(原点在右端面),启动主轴
N30 G00 X80.0 Z10.0; 定位到起始点P
N40 X30.0 Z3.0; 定位到切入点A
N50 G01 Z⁃20.0 F0.1; 切削直线AB
N60 G02 X26.0 Z⁃22.0 R2.0; 切削圆弧BC
N70 G01 Z⁃40.0; 切削直线CD
N80 X24.0; 径向退刀DE
N90 G00 Z3.0; 退出工件外
N100 X80 Z10.0; 返回到始点P
N110 M30; 程序结束
2.3.4 程序暂停指令G04
G04指令用于暂停进给,其指令格式如下。
G04 P_;或G04 X(U)_;
暂停时间的长短可以通过代码“X(U)”或“P”来指定。其中“P”后面的数字为整数,单位是ms;“X(U)”后面的数字为带小数点的数,单位为s。有些机床,“X(U)”后面的数字表示刀具或工件空转的转数。
该指令可以使刀具做短时间的无进给光整加工,在车槽、钻镗孔时使用,也可用于拐角轨迹控制。例如,如图2⁃22所示,用径向进给车削环槽,若径向进给到位后立即退刀,其环槽外形为螺旋面,用暂停指令G04可以使工件空转几秒钟,将环形槽外形光整圆,例如欲空转2.5s时其程序段为:“G04 X2.5”或“G04 U2.5”或“G04 P2500”。G04为非模态指令,只在本程序段中才有效。
2.3.5 返回参考点指令
参考点是机床上的固定点,用参数(1240~1243)可在机床坐标系中设定4个参考点。返回参考点指令是使刀具移动到该位置,该指令用于回到建立机床坐标系的位置(G28),或用作回到自动换刀点位置(G30)等。
(1)返回到参考点指令(G28、G30)
① 返回第1参考点指令G28,格式如下。
G28 X(U)_ Z(W)_;
第1参考点位置由参数1240设定。程序段中的“X(U)”“Z(W)”是返回参考点时的中间点坐标,如图2⁃22所示。

图2⁃22 返回参考点指令中的参考点与中间点
② 返回第2、3、4参考点指令G30,格式如下。
G30 P2 X(U)_ Z(W)_; 返回第2参考点(该点位置由参数1241设定),P2可省略
G30 P3 X(U)_ Z(W)_; 返回第3参考点(该点位置由参数1242设定)
G30 P4 X(U)_ Z(W)_; 返回第4参考点(该点位置由参数1243设定)
程序段中的“X(U)”“Z(W)”同G28指令,是返回参考点时的中间点坐标。
(2)返回参考点检查(G27)
G27用于检验X轴与Z轴是否正确返回参考点。指令格式如下。
G27 X(U)_ Z(W)_;
“X(U)”“Z(W)”为参考点的坐标。执行G27指令的前提是机床通电后必须曾经手动返回一次参考点。
(3)从参考点返回(G29)
使刀具由机床参考点经过中间点到达目标点。
指令格式:G29 X_ Z_;
其中,“X”“Z”后面的数值是指刀具的目标点坐标,中间点就是G28指令所指定的中间点,刀具经过中间点到达目标点位置。在用G29指令之前,必须先用G28指令,否则G29不知道中间点位置,而发生错误,如图2⁃22所示。
例2⁃8:如图2⁃23所示,刀具运行到A点,编程由当前点A经过中间点B返回到参考点R,然后再从参考点R,经由中间点B,到目标点C。

图2⁃23 回参考点编程练习
解:程序如下。
O412; 程序名
N10 G54 T0101; 选择坐标系,选择1号刀
N20 G00 X50.0 Z100.0; 快速移动到A点
N30 G28 X80.0 Z200.0; 由A点到达中间点B,再快速到达参考点R
N40 G29 X40.0 Z250.0; 从参考点R,经由中间点B,到达目标点C
N50 G00 X50.0 Z100.0; 回A点
N60 M30; 程序结束
2.3.6 恒表面切削速度控制指令G96、G97
主轴回转中在“S”后指定表面速度(刀具与工件间的相对速度)保持恒定,与刀具位置无关,称为恒表面切削速度控制。指令格式如下。
G96 S××××(恒表面切削速度控制。S指定值为切削的恒表面切削速度,单位m/min。)
G50 S××××(极限主轴转速限定。S指定值为最大主轴速度,单位r/min。)
G97 S××××[取消恒表面切削速度控制。S指定值为取消恒线速度后,指定的主轴转速(r/min),如未给出S指定值,执行G96指令前的主轴转速。]
恒表面切削速度控制指令G96是模态代码。指定G96指令后程序进入恒表面速度控制方式(G96方式),以S指定值作为表面速度。在恒表面切削速度控制时,主轴速度若大于“G50 S_ ”(最大主轴转速)中规定的值,就被限定在最大主轴转速。G97指令取消G96方式。
注意:
① 使用恒表面切削速度控制功能,主轴必须能自动变速(如伺服主轴、变频主轴)。
② 为执行恒表面切削速度控制,设定工件坐标系必须使X轴(用恒表面切削速度控制的轴)的中心坐标值为0,如图2⁃24所示。
③ 在指定的快速移动G00的程序段中,恒表面切削速度控制不是根据刀具位置的瞬间变化计算表面速度,而是根据该段的终点计算的表面速度实现控制的,因为快速移动时不切削。
例2⁃9:零件如图2⁃24所示,已粗车完毕,编写用恒表面切削速度控制功能精车外圆的程序。

图2⁃24 采用恒线速度车削例题
解:程序如下。
O528;
N1G54 T0101; 设立坐标系,选一号刀
N2 G00 X40.0 Z5.0; 移到起始点的位置
N3 M03 S460; 启动主轴,转速460r/min
N4 G96 S80; 恒表面切削速度控制有效,切削速度为80m/min
N5 G50 S900; 限定主轴最大转速900r/min
N6 G00 X0; 刀定位到中心,转速升高,直到主轴到最大限速900r/min
N7 G01 Z0 F60.0; 工进接触工件
N8 G03 U24.0 W⁃24.0 R15.0; 车“R15”圆弧段
N9 G02 X26.0 Z⁃31.0 R5.0; 车“R5”圆弧段
N10 G01 Z⁃40.0; 车“ϕ26”外圆
N11 X40.0 Z5.0; 回对刀点
N12 G97 S300; 取消恒表面切削速度控制功能,设定主轴按300r/min旋转
N13 M30; 主轴停,主程序结束并复位