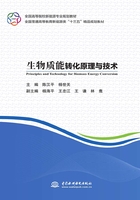
2.2 生物质成型工艺与设备
2.2.1 生物质成型工艺
将松散的生物质加工成成型燃料需要经过一系列步骤。生物质成型燃料的生产工艺流程需要根据原料种类、特性、成型方式以及生产规模等进行具体确定。图2.7和图2.8所示分别为某棒状成型燃料厂及颗粒燃料生产厂所采用的工艺流程。

图2.7 棒状成型燃料生产工艺流程
1—热风炉;2—螺旋上料机;3—干燥仓;4—涡轮研磨机;5—旋风分离器;6—气闸;7—锤式粉碎机;8—风机;9—中间料仓;10—成型机;11—冷却槽;12—旋风除尘器
生物质成型所用设备包括4类,具体如下:
(1)原料预处理设备,包括切割机、粉碎研磨机以及干燥系统。

图2.8 颗粒状成型燃料生产工艺流程
(2)原料输送设备,包括螺旋上料机、气动输料设备以及中间料仓等。
(3)压缩成型及其配套的控制装置。
(4)成型燃料处理及包装设备,包括燃料切割设备、冷却装置以及包装设备等。
生物质压缩成型过程受多种因素影响,从大的方面可以分为外部因素和内部因素两类。外部因素主要包括温度和压力;内部因素主要指生物质的物理和化学特性,其中物理特性包括原料的粒度、含水率,化学因素主要指原料中木质素的分子结构及其含量,以及其他天然黏结剂的含量。
1.压力
压力是保证生物质成型的最基本条件,只有施加足够的压力,生物质才能够被压缩成型。研究表明,制备棒(块)状成型燃料的压力条件是50~200MPa,制备颗粒成型燃料的压力条件是50~100MPa。当压力较小时,成型燃料密度随压力增大而增大的幅度较大,而当压力超过一定值后,成型燃料密度的增加幅度就显著下降,所以在满足生物质成型性能后,不宜再过度增加压力。
2.温度
温度主要起三个方面的作用:①使木质素软化熔融起到黏结剂的作用;②使原料颗粒变软,提高其塑性变形性能,从而更容易被压缩成型;③使成型燃料表面炭化,炭化层能阻碍成型燃料吸收水分,提高燃料的存放时间。成型过程中,加热温度应控制在300℃以下,因为超过该温度后生物质会发生裂解反应。一般螺旋挤压成型机要求将成型套筒的温度控制在280~290℃,而活塞冲压成型套筒的温度要求控制在160℃左右。对于颗粒燃料成型机,成型过程中原料与成型部件之间摩擦产生的热量足以满足成型温度要求,所以不需要设置加热设施,有时为了控制温度还需要对成型部件进行冷却。
3.原料含水率
原料含水率是影响其成型和成型燃料质量的关键因素。①水能够在颗粒表面形成水化膜,水化膜通过增加颗粒之间实际的接触面积,从而增强由范德华力导致的颗粒间的黏合;②在热量作用下,水分使生物质的物理化学特性发生显著变化,比如可以使木质素软化、蛋白质变性、淀粉糊化等,这些都会影响颗粒间的黏合特性;③原料的水分含量还直接影响所制备的成型燃料的含水量,从而影响成型燃料的储存性能,因为如果成型燃料中水分含量过低时,存放时会因为吸收空气中的水分而使成型燃料粉碎。适合生物质成型的水分含量范围为8%~20%。水分含量过低时,黏结剂的黏合作用难以发挥,而当水分含量过高时,颗粒间存在大量自由水,同样会减弱颗粒间的黏合力,所以水分过高或者过低,生物质都不能成型。
4.木质素
木质素是生物质成型过程中最主要的黏结剂成分,其含量和分子量对成型有重要影响。一方面,木质素分子量越小,其玻璃化温度越低,就可以在较低的温度条件下成型;另一方面,木质素含量越高,越有利于成型,且能提高成型燃料的强度。表2.2为木质素不同含量对玉米秸秆压缩成型的影响,从中可以看出,随着木质素含量的增加,成型燃料的强度显著提升。通常情况下,木屑等木质原料比秸秆类原料更易压缩成型,一个主要原因就是木质原料的木质素含量高于秸秆类原料。
表2.2 木质素不同含量对玉米秸秆压缩成型的影响

注 强度指制备的成型燃料所能承受的最大压力。
5.原料粒度
原料粒度既影响成型燃料质量,又影响成型过程。从有利于提高成型燃料强度角度考虑,原料的粒度应有差异,不宜均匀一致。此外,原料的粒度应根据成型机的具体情况和所加工的成型燃料类型来决定。生产棒(块)状燃料时,可以采用较大尺寸的原料,而生产颗粒燃料时,则需要小颗粒原料。例如,螺旋挤压成型适合加工粒度为6~8mm,且含有10%~20%小于4目颗粒的粉末状原料。活塞冲压成型则要求原料有较大的尺寸和较长的纤维,原料粒度小反而容易产生颗粒脱落现象。颗粒燃料的生产一般要求原料的粒度在2mm以下。粒度对成型过程的影响主要表现为可能导致进料部位发生堵塞。
2.2.2 生物质成型设备
根据成型方式不同,可将生物质成型设备分为螺旋挤压、活塞冲压、模压三种类型,其中,模压成型又分为环模成型和平模成型。颗粒燃料主要由模压成型设备生产,而棒(块)状成型燃料则可以由这三种类型的成型设备加工而成。生物质成型燃料生产方式如图2.9所示。

图2.9 生物质成型燃料生产方式
1.螺旋挤压成型机
图2.10和图2.11所示分别是螺旋挤压成型机及其成型部件的结构示意图。这种成型机的工作过程为:经干燥和粉碎的原料从料斗连续加入,经进料口进入成型套筒,物料通过传动螺杆表面的摩擦作用被不断地向前推送,由于强烈的剪切和摩擦产生大量热量,使物料温度逐渐升高;在到达压缩区前,原料被部分压缩,密度增加,进入压缩区后,原料在较高温度下变软,在压力作用下,颗粒间通过固体架桥、机械镶嵌和分子间作用力成为一个整体,继续向前进入成型筒的保型区,并最终被挤出成型筒,经导向槽 (防止成型棒因重力自然断开)至切断机处被加工成一定长度的棒状燃料。

图2.10 螺旋挤压成型机结构示意图
1—工具柜;2—电器柜;3—电机;4—传动皮带;5—传动轴;6—料斗;7—进料口;8—电热丝;9—保温罩;10—切断机;11—导向槽;12—压紧套;13—成型筒;14—热电偶;15—机座

图2.11 螺旋挤压成型机成型部件结构示意图
螺杆在整个长度方向上分为进料段和压缩段,进料段通常采用圆柱形等螺距螺旋;压缩段通常采用具有一定锥度的等螺距或变螺距螺旋。螺杆的压缩段处于较高温度和压力下,且螺杆与物料始终处于摩擦状态,因此螺杆存在严重的磨损问题,这是制约这种成型设备推广应用的主要问题。
螺旋挤压成型机的优点包括:成型燃料生产过程连续,生产过程中成型机由于不承受振动负荷而运行平稳,生产的成型燃料质量均匀,燃料棒中心孔有利于燃料燃烧,燃料棒表面的炭化层能阻止空气中水分进入,从而防止燃料棒因吸水而破碎。此外,由于设备结构简单,所以成型机造价低。如图2.12所示为螺旋挤压成型机与成型螺杆。

图2.12 螺旋挤压成型机与成型螺杆
螺旋挤压成型机的主要缺点是螺杆磨损快,这是制约螺旋挤压成型机推广应用的瓶颈。成型过程中,由于螺杆和原料之间的相对运动,受成型过程中压力和温度的影响,螺杆会被快速磨损,比如,普通碳钢生产的螺杆,使用寿命还不到8h。当螺杆磨损到一定程度时,螺旋叶片顶部直径变小,叶片厚度变薄,高度减小,螺杆与成型套筒配合间隙增大,产生的挤压力变小,致使成型速度变慢,生产率降低,成型效果变差。螺杆磨损到一定程度后将无法生产出成型燃料。
针对螺杆磨损问题,人们提出了两个解决思路:
(1)对螺杆头进行局部热处理,使其表面硬化。如采用喷焊钨钴合金、碳化钨焊条堆焊、局部炭化钨喷涂或局部渗硼处理等方法对螺杆磨损严重部位进行强化处理。
(2)把磨损最严重的螺杆前部用耐磨材料做成可拆卸的活动螺旋头,磨损后仅更换活动螺旋头即可,螺杆本体还可继续使用。
这些方法虽然可延长螺杆使用寿命,但并不能从根本上解决磨损问题。
2.活塞冲压成型机
活塞冲压成型机的成型部件由活塞(或冲杆)与成型套筒(包括冲杆套筒、成型锥筒、成型锥筒外套及保型筒)组成,如图2.13所示。

图2.13 活塞冲压式成型机成型部件结构示意图
1—冲杆;2—冲杆套筒 3—成型锥筒;4—成型锥筒外套;5—保型筒;6—夹紧套
成型筒设计时,成型锥筒内壁的曲面形状应能满足多种生物质成型工艺的要求,保型筒应有足够的长度且末端孔径可调节。成型锥筒是磨损速度最快的部件,因此可设计成能够更换的套筒,套筒材料可以采用铸铁、合金钢、非金属陶瓷等。
按驱动力不同,活塞冲压式成型机可分为机械驱动活塞冲压式成型机和液压驱动活塞冲压式成型机两大类,如图2.14和图2.15所示。机械驱动活塞式成型机是由电机带动惯性飞轮转动,利用惯性飞轮储存的能量,借助曲柄连杆机构或凸轮机构,带动活塞做往复运动。这种成型机由于冲杆运动速度快,所以可以实现较高的产率。但是由于存在较大的振动负荷,所以机器运行稳定性差,噪音较大。而且由于冲杆快速往复运动时会在冲杆和套筒间形成负压,使得细颗粒进入润滑油系统导致其被污染。

图2.14 机械驱动活塞冲压式成型机

图2.15 液压驱动活塞冲压式成型机
液压驱动活塞式成型机是利用液压油泵所提供的压力,驱动液压缸活塞推动冲杆将生物质冲压成型,这种成型机运行较平稳,油温便于控制,驱动力大。但是,由于液压驱动的特点,使得冲杆运动缓慢,所以该类成型机的燃料产率受到很大制约。
与环模或平模等模压成型方式相比,冲压成型的优势集中体现在两个方面:①生产的成型燃料密度大、抗机械破碎能力强;②便于根据需要加工成规格统一的产品,满足燃料作为家用商品销售的需要。从成型机冲压出来的成型燃料,既可以依靠重力自然断裂,也可以根据需要切割成统一的规格,并进行包装,如图2.16所示。

图2.16 冲压成型生产的各种成型燃料及燃料棒切割设备
3.环模成型机
环模成型机成型部件主要由环模和压辊组成,如图2.17所示。环模上均匀开设成型孔,运行过程中,环模成型机在动力驱动下使压辊或环模转动,在此过程中将进入压辊和环模间隙的生物质挤入环模成型孔内。物料在不断地摩擦、挤压过程中产生高温,在高温高压作用下,进入成型孔中的生物质先软化进而发生塑性变形,被压缩成一个整体。通过压辊和环模的旋转,持续将已经成型的燃料从成型孔中挤出。

图2.17 环模成型机部件
环模成型机的环模分为一体式环模和分体式环模两种,如图2.18和图2.19所示。环模是成型机最易磨损的部位,一体式环模磨损后需整体更换,维修费用相对较高。分体式环模可在一定程度上解决该问题。这种结构的环模由外部“母环”和中间的成型模块组成。磨损只发生在由成型模块组成的成型腔部位,当成型腔磨损程度不能满足生产需求时,只需更换成型模块即可。而分体式环模只适应于生产棒(块)状燃料,用于生产颗粒燃料时,只能用一体式环模,这是因为生产颗粒燃料的环模上成型孔数量太多,难以做成分体式成型模块。

图2.18 环模成型机内部的一体式环模
环模成型机的优势在于生产率可以设计的比较大,可以满足成型燃料规模化生产的需要。环模成型机用于生产块状或棒状燃料时,存在的突出问题是所生产的成型燃料密度较低、燃料块有明显的裂缝,如图2.20所示。这种质量的燃料虽然对燃烧的影响并不明显,但影响燃料的运输和储存。由于抗机械破碎能力差,所以在运输过程中容易破碎,且在储存过程中容易吸收水分导致粉碎,导致这一问题的主要原因是这种成型方式难以在成型孔上设计足够长的保型段。

图2.19 环模成型机内部的分体式环模

图2.20 有缝隙的成型燃料
对于环模颗粒燃料成型机,由于其成型孔小,要求原料粒径小于10mm,所以适合采用木屑做原料,当采用秸秆做原料时,仅粉碎就需要消耗较高的能量,使得经济性变差。
4.平模成型机
平模成型机的成型部件主要由平模和压辊两部分组成。平模成型设备的压辊有锥体压辊和圆柱体压辊两种类型,如图2.21所示,图2.22所示为平模成型机成型部件实物图。压辊数量2~4个,成型过程中成型部件有三种运动方式:平模运动、压辊运动、平模和压辊同时运动。

图2.21 平模成型机成型部件结构示意图
平模盘作为成型机的核心部件,是成型孔的载体。其结构形式有两大类,即一体式平模盘和套筒式平模盘。一体式平模盘按成型孔直径的大小分为颗粒燃料平模盘、棒(块)状燃料平模盘,如图2.23所示。套筒式平模盘是目前平模成型机的发展趋势,套筒内孔可设计成圆孔或方孔结构。套筒平模成型机最大优点是母盘为永久型部件,可以设计多种形状的成型腔,生产不同原料的成型燃料,套筒可以采用廉价的铸铁,也可以采用陶瓷类非金属材料。

图2.22 平模成型机成型部件实物图

图2.23 一体式(左)和套筒式平模盘
平模成型机上的压辊多采用直辊式。一体式平模盘配用的压辊宽度较大,与套筒式平模盘配套的压辊直径要尽可能大,以便使转速降低,压辊自转速度一般为50~100 r/min。平模成型机压辊外缘的结构形状与整体式环模压辊类似,如图2.24所示。从平模成型技术的发展来看,套筒式平模棒(块)状成型机是重要的发展方向。
当用于生产棒(块)状成型燃料时,平模盘最好采用套筒式结构。平模盘厚度设计首先要满足成型质量要求,即满足成型和保型需要,其次要考虑原料适应性,以及能耗及生产率的要求。

图2.24 平模成型机压辊
平模成型机结构简单、成本低廉、维护方便。由于喂料室的空间可以设计得比较大,所以可采用大直径压辊,加之模孔直径可设计到35 mm左右,因此原料适应性较好。当用秸秆做原料时,进行切断处理就可满足成型要求。这种成型方式对原料水分的适应性也较强,含水率15%~25%的物料都可挤压成型。
当用于生产颗粒燃料时,平模式成型机仍然存在整体式平模磨损后维修费用高,原料粉碎粒度要求高,以及粉碎耗能高的问题。