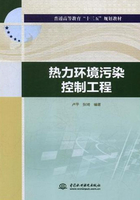
第三节 过滤式除尘器
过滤式除尘器,也称过滤器,是利用过滤材料来分离捕集含尘气流中尘粒的装置。按滤料种类、结构和用途分类,可分为袋式除尘器、颗粒层除尘器和空气过滤器。袋式除尘器是采用纤维织物等作滤料,主要用于工业尾气的除尘;颗粒层除尘器是采用玻璃纤维、金属绒、硅砂、焦炭等颗粒物作为滤料,是20世纪70年代出现的一种除尘装置,主要用于高温烟气除尘;空气过滤器是采用滤纸或纤维填充料作为滤料,主要用于通风及空气调节。
根据粉尘粒子在滤料上捕集位置的不同,过滤式除尘器有内部过滤和外部过滤两种工作形式。内部过滤是以填充在框架或床层中颗粒作为滤层,粉尘粒子在滤层内部被捕集。颗粒层过滤器就属于这种形式。外部过滤是以纤维布料、非纺织毛毡或滤纸等作为滤料,将粉尘粒子阻挡在滤料表面。袋式除尘器和空气过滤器就属于这种形式。本节主要介绍袋式除尘器。
一、袋式除尘器的工作原理
简单袋式除尘器的结构及工作方式如图3-28所示。含尘气流从下部进入筒形滤袋,粉尘被捕集于滤料表面,透过滤料的相对清洁气体由上部排出口排出。沉积在滤料上的粉尘,达到一定的厚度时,在机械振动等作用下从滤料表面脱落下来,落入灰斗中。

图3-28 袋式除尘器的结构和工作方式示意图
(a)总体结构;(b) 下进气,外滤式;(c) 下进气,内滤式;(d) 上进气,外滤式;(e) 上进气,内滤式
袋式除尘器的滤尘机制包括筛分、惯性碰撞、拦截、扩散和静电吸引等作用。
(1)筛分作用。筛分作用是袋式除尘器的主要滤尘机制之一。当粉尘粒径大于滤袋纤维间孔隙或粉尘层孔隙时,粉尘在气流通过时将被截留在滤袋表面。清洁滤料的孔隙(5~50μm)一般要比粉尘颗粒大得多,其筛分作用很小,只有滤袋表面上沉积了一定厚度的粉尘层之后,筛分效应才会变得明显。
(2)碰撞作用。当含尘气流接近滤袋纤维时,空气将绕过纤维。粒径大于1μm的颗粒,由于惯性作用,偏离空气运动轨迹,直接与纤维相撞,进而被捕集。粉尘颗粒粒径越大,气体流速越高,其碰撞效应也越强。
(3)拦截作用。含尘气体流经滤袋纤维时,较细尘粒随气流一起绕流,若尘粒半径大于尘粒中心到纤维边缘的距离,尘粒将会与纤维边缘相接触,进而被拦截。该效应与滤袋纤维及粉尘表面特性有关。
(4)扩散作用。当粉尘粒径小于0.2μm时,由于气体分子的碰撞而偏离气体流线,做不规则的布朗运动,碰到滤袋纤维而被捕集。粉尘颗粒越小,不规则运动越剧烈,粉尘与滤袋纤维接触的机会也就越多。
(5)静电作用。滤料和尘粒往往会带有电荷,当滤料和尘粒所带电荷相反时,尘粒会吸附在滤袋上,提高除尘器的除尘效率。当滤料和尘粒所带电荷相同时,滤袋会排斥粉尘,使除尘效率降低。
(6)重力沉降。含尘气体进入布袋除尘器时,粒径、密度较大的粉尘,在重力作用下自然沉降下来,这和沉降室的作用完全相同。
一般来说,粉尘粒子的捕集是多种分离机制联合作用的结果,但是各种分离机制的重要性会有差别,这种差别还会随着粉尘性质、滤袋材料、工作参数及运行阶段的改变而改变。
袋式除尘器在诸多工业领域和燃煤锅炉烟气净化中得到了广泛的应用,其主要原因在于袋式除尘器拥有以下优点:
(1)除尘效率高,尤其对微米以及亚微米级粉尘颗粒具有较高的捕集效率。
(2)不受粉尘比电阻影响,对高比电阻粉尘捕集效率高于使用电除尘器的情况。
(3)对含尘浓度适应性强,含尘浓度在相当大的范围内变化,对除尘效率和阻力影响不大。
(4)对气体流量适应性强,处理烟气量可从每小时几立方米到几百万立方米。
(5)性能可靠,操作维护简单,没有污泥处理和腐蚀等问题。
二、袋式除尘器的结构
袋式除尘器的结构形式多种多样,主要包括滤袋、气流进口、气流出口、振打结构、除尘器筒体等,可根据滤袋的形状、进气方式、气流通过滤袋的方向以及清灰方式等进行分类。
(1)按滤袋形状,可分为圆筒形滤袋除尘器和扁形滤袋除尘器。大多数袋式除尘器都采用圆筒形滤袋,通常滤袋直径120~300mm,袋长2~12m。圆袋受力比较均匀、结构比较简单、清灰操作需要的动力比较小、维修或检查时更为方便、成批换袋容易,但是圆筒形滤袋的袋口更容易损坏。扁袋通常呈平板型,且内部需要安装框架,或者安装弹簧,用以支撑滤袋。扁带结构紧凑,与圆袋除尘器相比,在负荷相同的条件下,扁袋除尘器占地面积较小。但是扁袋的制作要求比圆袋高,而且由于滤袋之间空隙较小,所以容易被粉尘阻塞。
(2)按进气方式,可分为上进气和下进气袋式除尘器。如图3-28(d)和(e)所示,上进气除尘器过滤时,粉尘沉降方向与气流方向一致,有利于除尘。但为了使配气均匀,配气室需设在壳体上部,增加了除尘器高度,也提高了造价。下进气除尘器过滤时,粗尘粒直接落入灰斗,只有小于3μm的细粉尘接触滤袋,故滤袋磨损小,且结构较简单。但下进气除尘器[图3-28(b)和(c)]的气流方向与粉尘沉降的方向是相反的,会造成一些本来被清落的粉尘又重新回到滤袋上,从而降低了清灰效果,增大了系统的阻力。总体来讲,下进气方式设计合理、构造简单、造价便宜,因而使用较多。
(3)按气流通过滤袋的方向,可分为内滤式和外滤式袋式过滤器(图3-28)。内滤式除尘器的含尘气体从滤袋的内部向外部流动,粉尘被捕集在滤袋的内表面,净化气体通过滤袋逸至袋外。滤袋的外面就是清洁的气体,因此在过滤气体对人体无害时可以在不停机的情况下对除尘器进行检修等作业。外滤式除尘器的含尘气体从滤袋的外部向内部流动,粉尘被捕集在滤袋的外表面,净化气体由滤袋内部排出。
(4)按清灰方式的不同,可分为机械振动清灰袋式除尘器、逆气流清灰袋式除尘器、脉冲喷吹清灰袋式除尘器等。详细的清灰方式参见本节第五部分。
三、袋式除尘器的性能
袋式除尘器的性能主要包括过滤速度、除尘效率和压力损失。
1.过滤速度
袋式除尘器的过滤速度是指气体通过滤料的平均速度,即烟气实际体积流量与滤布面积之比,也称气布比。过滤速度vF(m/min)可按下式计算:

式中 Q——通过滤料的气体量,m3/h;
AF——滤料总面积,m2。
过滤速度是表征袋式除尘器处理气体能力的重要技术经济指标。过滤速度的选择要考虑经济性和除尘效率等各方面因素。从除尘机理上考虑,过滤速度主要影响着惯性碰撞作用和扩散作用。滤料对粒径为1μm以下的微尘的捕集,主要借助扩散效应,因而适当降低过滤速度可以提高除尘效率;而对于粒径为5~15μm以内的大尘粒,滤料主要借助惯性作用对其进行有效捕集,提高过滤速度可以提高除尘效率。从经济上考虑,提高过滤速度可节省滤料,提高滤料的处理能力,进而也相应减小了除尘设备的体积、占地面积和投资费用,但会增加除尘器的压力损失。过滤速度的选取还与清灰方式和滤料的结构有关。因此,实际过滤速度的选择要综合烟气特点、粉尘性质、进口含尘浓度、滤料种类、清灰方法以及工作条件等因素来决定。
2.除尘效率
袋式除尘器的除尘效率一般可达99%以上。影响袋式除尘器除尘效率的因素主要有粉尘特性、滤袋结构、积尘量和过滤速度等。
(1)粉尘特性对除尘效率的影响。粉尘粒径分布对除尘效率有显著影响。在不同积尘状态下,滤料对0.2~0.4μm粒径范围内的粉尘的去除效率都最低。原因在于这一粒径范围内的尘粒惯性、拦截捕集作用和扩散捕集作用都很弱。
(2)滤料结构与积尘量对除尘效率的影响。不同结构的滤料其滤尘效率是不同的。不起绒的素布滤料除尘效率较低,且清灰后效率急剧下降;呢料、毛毡等起绒滤料,由于其容尘量大,能够形成强度较高和较厚的多孔粉尘层,且有一部分粉尘成为永久性容尘,因而其除尘效率比素布结构的滤料高,清灰后效率下降也不多。起绒性面料中,绒长的比绒短的除尘效率高;单面起绒滤布,从无绒面过滤比从起绒面过滤时的除尘效率高。
同种滤料在不同状态下的滤尘效率也不同。清洁滤料的除尘效率最低。积尘后滤料的除尘效率较高。当滤料上的积尘达到一定程度,需要清灰,清灰后的滤料除尘效率又有所降低。图3-29给出了典型滤袋在清洁状态和形成颗粒层后的除尘分级效率曲线。对于粒径0.1~0.5μm粒子,清灰后滤料的除尘效率在90%以下;对于1μm以上的粒子,效率在98%以上。当形成颗粒层后,对所有粒子效率都在95%以上;对于1μm以上的粒子效率高于99.6%。一般用颗粒物负荷W表示滤布表面颗粒层的厚度,它代表单位面积滤布上的积尘量。
(3)过滤速度对除尘效率的影响。过滤速度对除尘效率的影响,在前文已有阐述。丹尼斯(Dennis)和克莱姆(Klemm)提出了下列方程来预测袋式除尘器的颗粒物出口浓度和穿透率:

图3-29 袋式除尘器的分级效率曲线

式中 C1——颗粒物入口浓度,g/m3;
C2——颗粒物出口浓度,g/m3;
Pns——无量纲常数;
CR——脱落浓度,g/m3;针对玻璃纤维滤袋和飞灰,可取0.5g/m3;
W——颗粒物负荷,g/m2。
丹尼斯和克莱姆也提出,对于玻璃纤维滤袋,粒子的穿透主要是由于通过滤布上的针孔漏气所致,穿透的颗粒物几乎具有和滤袋入口颗粒物相同的粒径分布。
3.压力损失
袋式除尘器的压力损失是重要的经济技术指标,它不但决定能量消耗,而且决定除尘效率及清灰周期。袋式除尘器的压力损失ΔP由结构压力损失ΔPC和过滤压力损失ΔPF两部分组成。

结构压力损失是指气流经过除尘器进口、出口和花板等的压力损失,其值一般为300~500Pa。过滤压力损失(ΔPF)由通过清洁滤料的压力损失(ΔPF0)和通过黏附在滤袋上粉尘层的压力损失(ΔPp)两部分组成。假设通过滤袋和颗粒层的气流为黏滞流,ΔPF0和ΔPp则均可以用达西(Darcy)方程表示。达西方程的一般形式为

式中 K——滤料或粉尘层的渗透率(K0,Kp),m2;
x——滤料或粉尘层的厚度(x0,xp),m。
式(3-58)实际上是渗透率K的定义式,需要通过实验测定。它代表了沉积粉尘的性质,是孔隙率、比表面积、孔隙大小分布和粉尘粒径分布的函数。根据达西方程,则

对于给定的滤料和操作条件,通过清洁滤料的压力损失基本上是一个常数,其值大约为100~130Pa。因此,粉尘层的压力损失决定了除尘器的总压力损失。粉尘层的压力损失主要由粉尘层厚度xp和粉尘层渗透率Kp。随着粉尘层厚度的增加,粉尘层压力损失增加。
在时间t内,沉积在滤袋上的粉尘质量m可以表示为

式中 C——烟气中粉尘浓度,g/m3;
ρc——粉尘层的密度,kg/m3。
由式(3-60)可以得到,xp=vFCt/ρc,因此,气流通过沉积粉尘层的压力损失为

对于给定的含尘气体,μ、ρc和Kp的值均为常量,令粉尘比阻力系数,则式(3-61)变为

对于给定的烟气特征和粉尘层渗透率,显然ΔPp与粉尘浓度C和过滤时间t呈线性关系,而与过滤速度vF的平方成正比。比阻力系数Rp主要由粉尘特征决定,应当由实验测定。一些工业性粉尘的比阻力系数参见表3-7。假如已知粉尘的粒径分布、堆积密度和真密度,可以利用丹尼斯(Dennis)和克莱姆(Klemm)提出的公式估算:

式中 S0——比表面参数,cm-1;
Cu——坎宁汉修正系数;
MMD——粉尘的质量中位径,cm;
σg——粉尘直径的几何标准偏差;
ρp——粉尘的真密度,g/cm3;
β——无量纲数,β=ρc/ρp。
袋式除尘器处理的粉尘的浓度一般在0.5~30g/m3,滤料上堆积的粉尘负荷一般为0.2~0.3kg/m2。当通过粉尘层的压力损失为500~570Pa时,除尘效率可达99%;当通过粉尘层压力损失接近1000Pa时,一般需要对滤袋进行清灰。清灰后,粉尘层压力损失应该恢复到500~570Pa。随着入口粉尘浓度的增加,清灰周期缩短,进而导致清灰次数增多,滤袋寿命缩短。
表3-5列出了各种袋式除尘器的过滤风速和压力损失。
表3-5 各种袋式除尘器的过滤风速和压力损失

四、袋式除尘器的滤料
1.对滤料的要求
滤料是袋式除尘器最关键的组成部分,其性能和质量的好坏,直接关系到袋式除尘器的性能和使用寿命。在实际工作中,通常根据含尘气体的性质、粉尘特性、清灰方式以及安装方式等因素,选择最适宜的滤料。袋式除尘器对滤料的基本要求如下:
(1)除尘效率高。滤料的除尘效率是由滤料结构和附着其上的粉尘层共同决定的。过薄的滤料在清灰后粉尘层会遭到破坏,导致除尘效率降低很多。
(2)容尘量大。容尘量是指单位面积滤料上的粉尘存积量。容尘量大,可以延长清灰周期,从而延长滤袋的寿命。
(3)透气性好。在保证滤料过滤效率的前提下选择透气率高的滤料可以增大单位面积滤料上的过滤风量,从而节省过滤面积,降低除尘器成本。
(4)物理和化学性能优良。滤料要具有耐高温、耐化学腐蚀的性能,同时也要有良好的机械性能,有较高的抗拉、抗弯折的能力,还要有耐磨性。
(5)剥落性良好。对滤料表面进行烧毛处理或者进行覆膜可以使滤料表面具有较好的光洁性,捕集的粉尘也能相对容易地被清理下来。
2.滤料的种类及特性
常用滤料按所用的材质可分为天然纤维(如棉毛织物)、合成纤维和无机纤维等。
(1)天然纤维。天然纤维包括棉织、毛织及棉毛混织品。天然纤维的特点是透气性好、阻力小、容量大、过滤效率高,粉尘易于清除,耐酸、耐腐蚀性能好,其特点是长期工作温度不得超过100℃。
(2)无机纤维。无机纤维主要是指陶瓷玻璃纤维。这种纤维作为滤料,具有过滤性能好、阻力小、化学稳定性好、耐高温、不吸潮和价格便宜等优点;其缺点是除尘效率低于天然、合成纤维滤料,此外,由于这种纤维挠性较差,不耐磨,在多次反复清灰后,纤维易断裂。在采用机械振打法清灰时,滤袋易破裂。为了改善这种易破裂的状况,可用芳香基有机硅、聚四氟乙烯、石墨等物质对其进行处理。用硅酮树脂处理玻璃纤维滤料能提高其耐磨性、疏水性和柔软性,还可使其表面光滑易于清灰,可在250℃下长期使用。
(3)合成纤维。随着有机合成工业、纺织工业的发展,合成纤维滤料逐渐取代天然纤维滤料,合成纤维有聚酰胺、芳香族聚酰胺、聚酯、聚酯化合物、聚丙烯、聚丙烯腈、聚氯乙烯、聚四氟乙烯等。其中芳香族聚酰胺和聚四氟乙烯可耐温200~250℃,聚酯纤维可耐温130℃左右。
几种常用滤料的性能见表3-6。
表3-6 几种常用滤料的性能

五、袋式除尘器的清灰
如前文所述,袋式除尘器的清灰方式有机械振动清灰、逆气流清灰、脉冲喷吹清灰等。
1.机械振动清灰
机械振动式清灰是利用机械传动使滤袋振动来达到清灰的目的,其工作过程如图3-30所示。机械振动清灰大致有水平振动、垂直振动和扭转振动3种方式,如图3-31所示,其中水平振动可分为上部摆动和腰部摆动两种方式;垂直振动可以定期地提升滤袋框架,也可利用偏心轮装置振打框架;扭转振动则是利用机械传动装置定期将滤袋扭转一定的角度,使粉尘脱落。

图3-30 机械振动袋式除尘器工作过程
(a)过滤;(b) 清灰
机械振动清灰袋式除尘器的过滤风速一般采用1.0~2.0m/min,相应压力损失为800~1200Pa。该类型袋式除尘器工作性能稳定,清灰效果较好。但由于滤袋经常受机械力的作用而损坏较快,滤袋的检修与更换工作量大;而且一般机械振动式清灰都必须在除尘停止时进行,所以为了保证除尘器的连续运转,一般是将除尘器分为很多个分室,清完一个袋室,再清下一个袋室,不停地运转。
2.逆气流清灰
逆气流清灰系指清灰时的气流方向与过滤时气流方向相反,其形式包括反吹风和反吸风两种。逆气流吹风清灰袋式除尘器的过滤和清灰过程如图3-32所示。清灰过程开始时,先关闭除尘器顶部净化气体的排出阀,然后引入与含尘气体方向相反的气流,在这个气流的作用下,滤袋发生变形,并产生振动,使粉尘在滤袋的振动下清落下来落到灰斗中。为了保证除尘器的连续运行,逆气流清灰袋式除尘器一般划分为多个袋室,并通过阀门控制,对每个袋室依次提供反方向气流进行清灰。

图3-31 机械清灰的振动方式
(a)水平振动;(b)垂直振动;(c)扭转振动
逆气流吹风清灰袋式除尘器的过滤风速一般取0.3~1.2m/min,压力损失控制在1000~1500Pa。其特点是清灰比较均匀,对滤袋的损坏比较小,特别适合于玻璃纤维袋。

图3-32 逆气流清灰袋式除尘器工作过程
(a)过滤;(b)反吹;(c)沉降
3.脉冲喷吹清灰
脉冲喷吹清灰也包括逆气流反吹过程。这种清灰方式利用4~7个标准大气压的压缩空气反吹,产生强度较大的清灰效果。压缩空气的脉冲产生冲击波,使滤袋振动,导致积附在滤袋上的灰尘脱落。这种清灰方式有可能使滤袋清灰过度,继而使粉尘通过率上升,因此,必须选择适当压力的压缩空气和适当的脉冲持续时间(通常为0.1~0.2s)。每清灰一次,叫作一个脉冲,全部滤袋完成一个清灰循环的时间称为脉冲周期,通常为60s。
脉冲清灰的控制参数为脉冲压力、频率、脉冲持续时间和清灰次序。脉冲喷吹清灰袋式除尘器如图3-33所示,脉冲喷吹清灰经常采用上部开口、下部封闭的滤袋。含尘气体通过滤袋时粉尘被阻留于滤袋外表面上,净化后的气体由袋内进入上部净气箱,然后由出气口排出。为防止滤袋被压扁,滤袋内安置笼形支撑结构。

图3-33 脉冲喷吹清灰袋式除尘器
脉冲喷吹耗用压缩空气量按下式计算:

式中 n——滤袋总数,条;
T——脉冲周期,min;
α——安全系数,取1.5;
V0——每条滤袋喷吹一次好用的压缩空气量,在喷吹压力不小于6×1.01325×105Pa时,V0=0.002~0.0025m3/条。
脉冲喷吹袋式除尘器是实现了全自动清灰,可实行定时控制或定压控制。毡制的滤袋常采用脉冲喷吹清灰,过滤风速较高,一般为2~4m/min,压力损失控制为1200~1500Pa。脉冲袋式除尘器,滤布磨损较轻,使用寿命较长,运动安全可靠,已成为袋式除尘器的一种主要清灰方式。
六、袋式除尘器的选型、设计与应用
1.袋式除尘器选型
首先确定采用除尘器的形式。例如对除尘效率要求高、厂房面积受限制、投资和设备订货都有条件的地方,可以采用脉冲喷吹袋式除尘器,否则采用另两种清灰方式。其次应根据含尘气体特性,选择合适的滤布。如气体温度超过140℃、低于250℃时,可选用玻璃丝袋;对纤维性粉尘应选择表面光滑的滤料(如平绸、尼龙等);对一般工业粉尘,可采用涤纶绒布等合成纤维滤袋。最后根据除尘器滤料的形式、允许的压力损失和气体的含尘浓度,就可以确定清灰方式。
2.过滤面积的计算
根据含尘浓度、滤料种类及清灰方式等,确定过滤气速vF(m/min),按下式计算过滤面积:

过滤气速是最重要的设计和操作指标之一。过滤气速选择过大,虽能减少总过滤面积,降低投资,但却会使压力损失迅速提高,增多清灰次数,缩短滤袋寿命,使运行费用增大。若vF偏小,会使设备费增加。一般情况下的过滤气速归纳如下:简易清灰,0.20~0.75m/min;逆气流反吹清灰,0.5~2.0m/min;机械振动清灰,1.0~2.0m/min;脉冲喷吹清灰,2.0~4.0m/min。
3.袋式除尘器设计
若选择定型产品,则根据处理风量和总过滤面积A就可选定除尘器的型号规格。若自行设计,其主要步骤如下:
(1)确定滤袋尺寸(直径d和高度l)。
(2)计算单只滤袋面积a=πdl。
(3)计算滤袋条数n=A/a。
(4)在滤袋条数较多时,可根据清灰方式及运行条件,将滤袋分为若干组。每组内相邻滤袋的净距一般取50~70mm。组与组之间、滤袋与外壳之间的距离一般取600~800mm。
【例3-6】 采用机械振动式布袋除尘器净化含尘气体。气体流量为1130m3/min,含尘浓度为23g/m3,试估算所需的过滤面积。若布袋尺寸为长2.5m,直径为15cm,计算所需布袋的总数和布袋室的数目。
解:从表3-5选取vF=0.6m/min,那么所需布袋面积为

单个布袋的过滤面积为

所以,布袋总数为

选择每个布袋室安排400条布袋,则所需的布袋室数目为4,考虑到连续运行中一个布袋室可能要停下来清灰,最终选择5个布袋室,结果实际所需的布袋总数为2000条。
4.袋式除尘器的应用
袋式除尘器作为一种高效除尘器,已被广泛地应用于各种工业部门的废气除尘。它比电除尘器结构简单、投资省、运行稳定,可以回收高比电阻粉尘;与文丘里洗涤器相比,动力消耗小,回收的干颗粒物便于综合利用。因此采用袋式除尘器捕集微细的干燥颗粒物是适宜的选择。表3-7给出了袋式除尘器一些工业除尘领域的使用情况。
表3-7 袋式除尘器使用情况

为了适应高温和大烟气量净化的需要,袋式除尘器还有不少问题有待解决。例如,由于过滤速度较低,袋式除尘器一般存在体积庞大、耗钢量大、滤袋材质差、寿命短、压力损失大、运行费用高等缺点。目前,高温滤料研制、清灰方式改进与优化、大型袋房应用以及在线检漏监控等已经成为袋式除尘器的研发重点方向。随着过滤材料和清灰方式等方面的进一步改善,同时也伴随着烟气净化要求的进一步提高,袋式除尘器将有更广阔的应用前景。
七、颗粒层除尘器
颗粒层除尘器是过滤式除尘器的一种,是利用颗粒状物料(如硅石、砾石、焦炭等)作填料层的一种内部过滤式除尘装置。由于具有耐高温、耐腐蚀、耐磨损、除尘效率高、维修费用低等优点,已得到了人们的关注。颗粒层除尘器的除尘机理与袋式除尘器类似,主要靠惯性碰撞、截留及扩散作用等。过滤效率随颗粒层厚度及其沉积的粉尘层厚度的增加而提高,压力损失也随之增大。
图3-34为一种带有梳耙的旋风式颗粒层除尘器。图3-34(a)为正常运行状况,含尘气体以低速切向引入预分离器(旋风筒),粗粉尘被分离下来,然后经中心管进入过滤室,由上而下地通过过滤层,使细粉尘被阻留在颗粒填料层表面或层空隙中。气体通过净气室和打开的切换阀,从净气出口排出。该颗粒层除尘器的过滤层厚度一般为100~200mm,比负荷一般为2000~3000m3/(m2·h),含尘浓度高时采用1500m3/(m2·h)。过滤速度一般为33~50m/min,含尘浓度高时可采用25m/min,进口含尘浓度最高可允许到20g/m3,一般在5g/m3以下。除尘效率约为90%,设备压力损失约为1000~2000Pa(与颗粒层厚度等有关),承受温度一般在580K,短时可耐680K。

图3-34 带有梳耙的旋风式颗粒层除尘器
(a)正常运行状况;(b) 清灰状况
1—含尘气体进口;2—旋风筒;3—卸灰阀;4—中心管;5—过滤室;6—颗粒填料床;7—净气室;8—换向阀;9—净气出口;10—梳耙;11—驱动电机
图3-34(b)为清灰状况,这时关闭切换阀,切断单筒和净气出口,反吹空气按相反方向进入颗粒层,使原粒层处于流态化状态。与此同时,梳耙旋转搅动颗粒层,这样便将沉积粉尘吹走,同时颗粒层又被梳平。被反吹风带走的粉尘通过中心管进入旋风筒,由于气流速度突然降低和急转弯,使其中所含大部分粉尘沉降下来。含有少量粉尘的反吹空气由入口管排出,同含尘气体总管汇合在一起,进入其他单筒内净化。
这种形式的颗粒层除尘器一般采用多筒结构,目前常用的筒数为3~20,排列成单行或双行,用一根含尘气体总管、净化气总管和反吹风总管联结起来。单筒直径有1.3m、1.5m、1.7m、2.0m、2.5m及2.8m等多种规格。每个单筒可连续运行1~4h(视含尘浓度而定)。反吹清灰时只有一部分(50%~70%)粉尘从颗粒层中分离出来。反吹空气量取决于过滤器大小和粉尘特性,约为总气量的3%~8%。一般反吹空气是用预热过的环境空气,由一台单独的小型风机提供。
已有的试验研究表明,过滤层的磨损很小,除了滤料耐磨的因素外,还由于即使在反吹后,滤料仍覆盖有一薄层粉尘。在暂时耙松期间,也只是粉尘本身相互接触。颗粒层除尘器的滤料耐温性能好,其操作温度仅受钢材本身的限制。按照标准设计,入口温度可取至645K。移动床颗粒层除尘器已开始应用于工业锅炉,流化床沸腾反吹的颗粒层除尘器虽尚未被广泛应用于工业实践中,但已进行了许多探索性的试验。