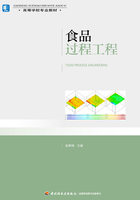
第二节 流体动力学基础
一、流体的流动形态
流体流动包括层流(Laminar Flow)、湍流(Turbulent Flow)以及过渡流。当液体流速较小时,惯性力(Inertia Force)较小,黏滞力(Viscous Force)对质点起调控作用,使各流层的液体质点互不混杂,流体呈层流运动。当液体流速逐渐增大,质点的惯性力也逐渐增大,黏滞力对质点的调控作用逐渐减弱,当流速达到某一数值后,各流层的液体瞬间弥漫开来,液体质点互相混杂,流体呈湍流运动。
边界层(Boundary Layer)是指高雷诺数绕流中紧贴物面的黏滞力不可忽略的流动薄层,又称作流动边界层、附面层。边界层厚度通常定义为从物面(当地速度为零)开始,沿法线方向至速度与当地自由流速u0相等时(严格地说是等于0.990u或0.995u)的位置之间的距离,记为δ。如图3-3所示,当流体靠近物面,因受黏滞力的作用,流体速度减小;由物面向外,边界层内流体速度逐渐增加,直到与自由流速u0相等;在远离物面的区域内,流体速度梯度小,黏滞力可忽略不计,惯性力起主要作用。

图3-3 边界层示意图
流体的流型不仅与流速u有关,还与流体的密度ρ、黏度μ以及流动管道的直径D有关。这些变量组合成一个数群,以其数值的大小作为判断流动形态的依据。这个数群成为雷诺准数(Reynolds Number),用Re表示,即:

式(3-7)表明,雷诺准数可以用来表征惯性力和黏滞力的相对大小,是一个无因次准数,数群中各物理量必须采用同一单位制。Re的大小可以用来判断流体的流动类型。Re<2000为层流,Re>2000为湍流,Re在2000~4000之间为过渡流。在食品加工过程中,层流是最为常见的流动形态,食品流体的剪切速率相对较低,但黏度相对较大。
二、流体层流运动
在工业生产中,流体流动存在多种分布特征。假设流体为牛顿流体并且保持层流运动时,其剪切力可以用黏性定律表示。
(一)圆管内的层流运动
如图3-4所示,选取半径为R的圆管以管轴为中心,任取一流体单元,半径为r,长度为l,对该流体单元进行受力分析。

图3-4 流体层流运动
由推力与阻力平衡可知

又因为

所以

由此推出

上述为圆管层流的速度分布规律,说明层流时的速度分布特征为:流体质点无返混,整个流动区域都存在速度梯度,速度分布呈二次抛物线型(图3-5)。当r=R时,管壁处流速最小;当r=0时,管中心处流速最大:

同样地,整个流动区域都存在线型分布的剪应力梯度(图3-5)。当r=0时,管中心处剪应力最小;当r=R时,管壁处剪应力最大:


图3-5 圆管中流体的层流运动
若流体流量为qv(m3/s),则:

式(3-11)称作哈根—泊肃叶(Hagen-Poiseuille)定律,它是测定液体黏度的重要依据。
圆管内的平均速度:

因此,流体为层流运动时其平均流速是最大流速的一半,即:

(二)平面表面的层流运动
实际生产过程中,流体在管道或各工序间的传输常常会以液膜的形式存在,如薄膜蒸发器、液膜涂层食品等。此时,流体的流动主要受重力控制。
假设流体在一倾斜平面上做稳态层流运动(图3-6),液体层的厚度为dz,倾斜角度为α。

图3-6 倾斜平面上层流运动的速度分布
因此,

式中 g——重力加速度,m/s2。
当管道宽度为W(单位m)时,体积流量qv:

式(3-16)通常运用于已知体积流量qv,计算液膜厚度Z的情况。
(三)固液共混时的层流运动
流体的流动并非只是以液态形成存在,有时还会有固体颗粒的存在。如悬浮、离心、流态化以及气力输送等过程。假设球形固相颗粒与液态流体共混进行层流运动。
当流体在半径为dp的球形颗粒周围以速度u流动时,沿流动方向会存在黏滞阻力FD。阻力系数(Resistance Coefficient)CD:

其中,Ap为流动方向上颗粒的投影面积,球形Ap=πdp/4。George Gabriel Stokes发现,流体呈层流运动时,阻力系数与雷诺数的关系如下:

综上,流体黏度、速率和球形颗粒大小的关系为:

假设固体的密度ρS>流体密度ρL,球形颗粒的受力情况为:

黏滞阻力如式(3-19),方向与沉降方向相反。因此垂直方向的受力为:

球形颗粒在静止时速度为零,其所受的黏滞阻力为零,由于颗粒所受的重力>浮力,垂直方向受重力加速度作用加速下沉。当速度逐渐增大,黏滞阻力逐渐增强,当阻力与重力相等时,此时颗粒沿垂直方向匀速下沉,此速度即终极速度或沉降速度ut。当式(3-20)中Fnet为0时,可求出ut值:

上式即为斯托克斯定律(Stokes Law)。固体颗粒在液体中的沉降速度取决于颗粒大小和液体性质。
[例3-1] 管道输送中酸奶的压力预测(H.J.O'Donnell,2002)。
目前,已有大量的研究使用传统的旋转黏度计来描述酸奶的流变行为,但有关酸奶输送过程的流变性能研究却较为少见。本例主要对管道输送过程中酸奶的层流运动及其流动特性进行讨论。
现有研究表明,酸奶加工中的泵送和混合过程会降低酸奶的黏度。在酸奶的管道输送中,在不考虑时间的情况下,压降与流速的关系可用式(3-22)表示:

式中 ΔP——管道中压降,Pa;
l——管道长度,m;
K——流体的稠度系数,K;
R——管道半径,m;
n——流变指数;
u——流速,m3/s。
其中,系数K和n可通过初始状态及平衡状态黏度计的测量数据进行计算,并代入式(3-22)中预测恒定流速下的管道压降。
但将实验测得的压降与预测结果进行比较后发现,实验数据一般小于初始状态的预测值,大于平衡状态的预测值。因此,推断酸奶的流动特性与时间的长短有关。与达到平衡状态的时间相比,酸奶在管道中的停留时间相对较短,故测量值将更接近于初始状态的预测值,尤其是在较高流速时。初始状态下,单位长度压降预测值的误差随着流速的增加而减小;相反,在平衡状态下,单位长度压降预测值的误差随着流速的增加而增大。
为了使预测值更加接近实际情况,考虑到酸奶在管道内的停留时间,对系数K和n进行了修正。该模型可用于预测在一定时间、恒定剪切速率和剪切力的条件下,从初始0s至400s的流动状态(停留时间始终<400s)。

如图3-7所示,使用修正后的方程预测管道压降能比初始状态的预测值(误差0%~129%)或平衡状态的预测值(误差37%~83%)更接近于实验值(误差0%~41%)。综上所述,考虑到时间对酸奶流动特性的影响,因此对幂律方程中的K和n进行了修正,能更加准确地预测酸奶加工过程中管道内的压力变化。

图3-7 1.0m管中流速与压降的关系
0.25m预剪切部分:■测量值 □预测值;2.0m预剪切部分:◇测量值 ▲预测值
三、圆管中的非牛顿流体流动
流体在管道中进行层流运动,剪应力与管道中心至管壁距离的关系如下:

假设流体的流动符合赫—巴模型式(3-3),那么流速可进一步变形,得:

此时,牛顿流体(n=1)的速度分布曲线并不是抛物线。并且当剪应力τ>屈服应力τ0时,式(3-25)才能成立。

图3-8 圆管中非牛顿流体的流动
如图3-8所示,当流体处于管壁附近时,剪应力最大。当流体处于管中心时,剪应力为零。当τ<τ0时,流体做匀速运动;当流体处于管中心至τ=τ0区域时,流体做活塞运动;当流动区域继续扩大至管壁附近时,流体则停止流动。因此,流体静止的条件为:

四、流体湍流运动
当雷诺数较大时,流体呈湍流运动。在实际生产中,单独研究湍流是很困难的,由于其剪切力不能用数学式简单表示,因此湍流的速度分布一般只通过实验研究,采用经验式近似表示。通常在实验中,当Re>2000时,即认为是湍流运动。但是,只有Re>4000时,流体才会进行完全湍流运动。Re介于2000~4000范围内,称为过渡状态,此时流体可进行层流或湍流。
(一)圆管内的湍流运动
在食品加工中,常见的有关湍流的计算主要围绕流体的摩擦压降。因此,摩擦系数f为:

式中 ΔP——压降,Pa;
D——管道直径,m;
l——管道长度,m;
u——流体的平均流速,m/s;
ρ——流体密度,kg/m3。
摩擦系数的大小取决于雷诺数Re以及管道壁面的粗糙度。但对于光滑管道,如不锈钢管,摩擦系数只与Re有关。
层流运动中,结合式(3-27)与式(3-11),f与Re的关系为:

若管道直径为D,长度为l,已知黏度μ、密度ρ和体积流量qv,通过管道截面面积可以求得平均流速u。再通过计算雷诺数判断流体的流动状态。如果Re<2000,则为层流,压降可通过泊肃叶方程进行计算。如果Re>2000,则为湍流,压降可通过摩擦系数进行计算。由式(3-27)得:

在工程学中,压力通常用液体压头Hf表示,压降通常用液体压头损失表示。压力与液体压头之间的转换如下:

(二)固液共混时的湍流运动
与上述讨论的摩擦系数类似,固体颗粒存在时流体的阻力系数CD也与雷诺数有关。当Re介于2~500之间,阻力系数的经验公式为:

当雷诺数增大,阻力系数趋于常数(与Re值无关),即CD=0.44。
[例3-2] 豆浆湍流模型的应用(S.M.Son,2002)。
与传统罐头杀菌相比,无菌加工的优点在于它能利用连续流热交换器来提高加工效率。在湍流条件下,流体停留时间的分布较为均匀,整体的传热系数较高,无菌处理的优势会表现得更加明显。由于食品湍流模型的复杂性和湍流剪应力方程的缺乏,因此该类模型在食品加工领域的应用受到了极大的限制。本例阐述了豆浆湍流模型的建模过程,并用来模拟豆浆在管式加热器中的速度和温度分布。
对于豆浆体系,在圆管内进行湍流运动下的平均剪应力方程可以用式(3-31)表示:

式中 τ——剪应力,Pa;
K——稠度系数,Pa·sn;
u——轴向分速度,m/s;
r——径向坐标;
n——流变指数;
D——直径,m;
下标lam——层流;
t——湍流;
w——管壁。
其中,Kt取决于流体的位置、方向及湍流的性质。将湍流分为两个区域,即湍流核心区和层流亚层区。
对湍流核心区有:

对层流亚层区有:

式中 u+——无量纲变量u/ue;
r+——无量纲变量(rnρus2-n)/k;
r++——无量纲变量(r+)1/n;
y——轴向坐标;
y+——无量纲变量(ynρus2-n)/K;
y++——无量纲变量(yρ1/nus(2-n)/n)/K1/n;
K——热导率,W/(m·K)。
为了验证加热管出口处的速度、温度分布,采用螺旋管式换热器(长度30m)进行实验验证,对豆浆的停留时间和温度进行测量。豆浆初始温度为60℃,高压蒸汽使壁温保持130℃,流速固定为37.8L/min。

图3-9 豆浆在螺旋管换热器中的流速分布
模拟—流速变化(9%豆浆)
模拟—流速变化(16%豆浆)
实验测定—流速变化(9%豆浆)
实验测定—流速变化(16%豆浆)
由图3-9可知,速率曲线中实际值和模拟值的相关性非常密切。16%的豆浆最大偏差为7%,9%的豆浆最大偏差为5%。

图3-10 螺旋换热器出口(l/D=1000)的温度分布
模拟—温度变化(9%豆浆)
实验测定—温度变化(9%豆浆)
模拟—温度变化(16%豆浆)
实验测定—温度变化(16%豆浆)
由图3-10可知,9%的豆浆测定值和模拟值基本一致。而16%的豆浆测量值略高于模拟温度,最大偏差为10%。
综上所述,通过对湍流条件下豆浆速度、时间分布的模拟,可找到理想的加工条件,无须大量的实验摸索,最大限度地提高了无菌豆浆的质量。
[例3-3] 湍流对果泥结构的影响(P.Perona,2002)。
新鲜果泥对机械应力的承受能力取决于其内部结构、含水量、果胶及纤维含量等,尤其是苹果泥。结构裂化(Structure Breakdown)通常是不可逆的,终产品的液体基质中仍然会存在大量的固体纤维。本例阐述了湍流运动对果泥内部结构裂化的影响。
在食品加工中,通常以建立结构模型来模拟流体的时间依赖性流变行为,表示在恒定剪切速率下,其剪应力与表观黏度会随着时间的增加而减小。事实上,这种降低可能是由于机械应力作用流体,使其内部结构发生裂化所致,并引发某些触变性行为。通过监测流体黏度或剪应力的变化可以预测其结构的裂化程度。
根据拉比诺维奇—莫尼(Rabinowitsch-Mooney)方程,令流变指数n′为常数,即:

式中 τw——管壁处的剪应力,Pa;
um——流体流速,m/s;
D——内管直径,m。
由此可得,管壁处的剪切速率γw可用式3-37表示:

由图3-11中流动曲线可知,新鲜苹果泥的稠度和屈服应力相对较高,即在相同的流速及温度条件下,苹果泥的压差比油桃泥更大。

图3-11 新鲜果泥的流动曲线和裂化过程
+苹果 ◇油桃
注:曲线1、曲线3表示天然果泥;曲线2、曲线4表示裂化后的果泥。
若流体的结构易受机械应力作用,那么当流体的流速越高,其结构裂化的程度越大、速度越快[图3-11(2)]。在层流运动中,由苹果泥的流动曲线[图3-11(1)中曲线1、曲线2]可以看出,其经历了明显的结构裂化。相反,对于油桃泥,这种变化并不显著[图3-11(1)中曲线3、曲线4]。
为了研究湍流对流体结构的影响,将果泥稀释,使其能从层流转为湍流运动。如图3-12(1)所示,湍流运动时的流体流动行为(曲线3)与初始状态(曲线1)大不相同。

图3-12 湍流对流体结构的影响
+裂化前 〇层流运动(8um/D=450s-1)裂化过程 ▲湍流运动(8um/D=1000s-1)裂化过程
如图3-12(1)所示,湍流运动使流体结构发生裂化,使其流变行为(曲线3)与最初状态(曲线1)有所不同。图3-13为果泥固相纤维在发生结构裂化后的微观图片,对比(1)与(2)图可明显看出,湍流运动使大分子纤维破碎,结构裂化。

图3-13 稀释苹果泥(55%水)结构裂化后的内部结构
湍流运动是导致固态纤维结构裂化的首要因素,液体中纤维呈短杆状扩散,这将影响流体的流变性能。因此,湍流运动对苹果泥的内部结构有着重要影响。
在果汁产品的实际生产中,要想提高生产效率并不能只靠提高原料的泵送速率,还需根据稀释度和温度对层流—湍流过渡点做进一步研究,分析纤维的受力分布,以此改善产品的感官性能。
五、温度对流体流变性能的影响
在食品的生产、贮藏、运输、销售以及消费过程中,液态食品会受外界温度的连续性变化而发生流变性能的改变,进而影响产品品质。因此,了解温度与产品流变性能之间的关系对食品的质量调控具有十分重要的意义。
在牛顿流体中,黏度与温度之间的关系可以用阿伦尼乌斯(Arrhenius Type)方程表示。但对非牛顿流体而言,表观黏度通常与剪切速率有关。

式中 μ∞——无限变形时的黏度,常数;
R——气体常数,J/(mol·K);
T——热力学温度,K;
Ea——流动活化能,kJ/mol。
温度能影响流体的不同流变学参数,如黏度μ、屈服应力τ0、稠度系数K以及流变指数n等。现将温度对流体流变行为的影响规律,总结如下:
①黏度μ和稠度系数K通常随温度的升高而减小。
②流变指数n通常不受温度的影响,但在某些特殊情况下,温度的升高会改变流体流变指数的大小(如在卡拉胶中,流变指数会随温度的升高逐渐上升)。
③屈服应力τ0也会随温度的变化而发生改变,当温度升高时,屈服应力降低(如使柠檬汁由假塑性流体变为牛顿流体)。