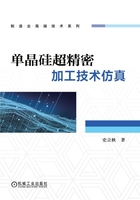
2.4 Marc超精密切削的有限元建模
有限元模型是解决整体结构问题的理想化的模型。这些问题包括研究对象的几何外形、材料特性、接触、初始条件、边界条件与加载等。建立有限元模型时,首先要对真实的结构进行简化,转化为力学模型[69,70]。本书将单晶硅在溶液中“自上而下”的加工过程简化为二维正交切削过程模型。
为了便于力学分析,对单晶硅超精密切削过程做如下基本假设:
1)假设单晶硅为各向同性的连续固体介质,有等向硬化的弹塑性,并且材料的力学性能随温度变化而变化。
2)单晶硅的超精密切削二维切削为正交切削,简化为平面应变问题;假设切削宽度远远大于切削深度,单晶硅在塑性域切削形成连续切屑,切削过程中无积屑瘤存在。
3)本书中单晶硅的超精密切削速度较低,在此条件下认为切削温度不足以导致单晶硅发生晶相变化和其他一些化学变化。单晶硅在塑性域切削,发生变形符合Von Mises应力屈服准则。
2.4.1 建立超精密切削的几何模型
几何外形就是金刚石刀具和单晶硅片几何形状的转换与简化。本书是金刚石刀具超精密加工单晶体硅,确定最佳切削刻划参数,得到最优表面质量和高精度的微纳结构。利用大型商业化软件Marc建立单晶硅正交超精密切削过程的有限元模型。在这个转化后的超精密切削模型中假定单晶硅为具有一定厚度的长方形。长方体的右边单元水平方向的位移设为零,底部单元所有位移和转动均设置为零(表示工件的固定)。金刚石刀具定义为可传热刚体,且作为主运动件,按照需求施加一定的速度。假定刀具在切削过程中不产生变形,内部单元不参与计算,如此可加快求解速度。由于本课题模拟的切削为超精密切削,这时金刚石刀尖的钝圆半径在切削过程中不能忽略,这也是精密加工与普通加工最大的区别。根据实际中使用的金刚石刀具,其钝圆半径ρ采用不同的值,并以一定的切削速度从左向右运动。在模型中指定金刚石刀具的后角α为6°,钝圆半径ρ为40nm,前角γ为−20°,背吃刀量ap为100nm,切削速度v为2µm/s,采用4节点实体单元对其进行网格划分。工件总长度应该至少大于切削深度的10倍,这样可以提供足够的切削长度,保证切削过程持续到稳定状态。
网格划分后的超精密切削的几何模型如图2-8所示。

图2-8 网格划分后的超精密切削的几何模型
2.4.2 建立刀具和工件的材料模型
正确描述材料特性是能否成功模拟单晶硅超精密切削的关键。用于材料成形分析的材料模型有两大类[71]:刚塑性模型和弹塑性模型。刚塑性模型是采用小变形的计算方法处理大变形问题,相对于弹塑性模型,其计算的增量步长取得比较大,因此计算效率高一些;但是该模型没有考虑材料的弹性变形,故计算精度比弹塑性模型低,且无法计算残余应力。本书是在塑性域对单晶硅进行超精密切削,研究应力、应变和温度分布,所以本书中单晶硅的材料采用的是基于Von Mises屈服准则弹塑性材料本构模型。
单晶硅和金刚石刀具的材料特性[72,73]见表2-1,金刚石刀具与单晶硅之间的摩擦因数µ是0.07。单晶硅的精密切削是在塑性域进行的,所以把工件材料看作弹塑性材料,采用平面应变单元。切削过程中基于热机耦合考虑了温度对单晶硅晶体材料特性的影响。
表2-1 单晶硅和金刚石刀具材料特性

2.4.3 建立接触摩擦模型
接触主要指刀具和工件,刀具和刀具,工件和工件接触,以及热量在工件与刀具间,工件、刀具和周围环境间的转移,变形功与切削变形热之间的转换关系,工件与刀具之间的摩擦生热作用等。Marc中接触有两种基本类型[74]:刚体对变形体的接触,变形体对变形体的接触。在单晶硅精密切削中,由于金刚石刀具的强度比单晶硅高得多,因此金刚石刀具一般被视为刚体,单晶硅被当作弹塑性变形体。因此本书将切削中的接触定义为刚体对变形体的接触问题,这与真实超精密切削单晶硅的过程是吻合的。在单晶硅的精密切削中,刀具和工件相互不能穿透。因此,刀具和工件间必须满足无穿透的约束条件,即满足下式:

式中 ΔuA——A点增量位移向量;
n——单位法向量;
D——接触距离容限。
如果某一节点的空间位置位于接触距离容限之内,就被当成节点与接触段相接处。Marc软件确定了接触距离容限的默认值,对实体单元,它是系统最小单元尺寸的1/20[75],所以本书定义的接触距离容限的值为0.0025。
由工件材料受到强烈挤压产生的变形热以及刀具和工件间摩擦而产生的摩擦热将在切屑、刀具、工件中传递,引起温度、应力、应变等物理量的重新分布,而这些物理量之间的相互耦合作用使工件产生塑性变形[76]。变形热在边界条件中激活塑性变形热选项即可。摩擦热是由刀具和工件之间合理的摩擦模型所决定的,因此正确建立摩擦模型是切削加工模拟成功实现的关键因素之一。切削时切屑和前面之间有两个接触区域,如图2-9所示,从刀尖O点到前面上的A点为黏着区,在黏着区刀屑接触点处的临界摩擦应力等于工件材料的剪应力,摩擦应力为常数[77,78]。AB段为滑动区,在滑动区服从库仑摩擦定律。两种摩擦应力可分别由式(2-22)和式(2-23)表示[79]。

图2-9 刀屑接触表面的摩擦模型

式中 τ*——工件材料的剪应力;
µ——刀-屑接触表面摩擦因数;
p——刀-屑接触表面的法向应力;
s——刀-屑接触表面的摩擦应力。
在有限元中有限元模拟切削时采用MSC.Marc提供的修正库仑摩擦模型。此模型的优点是,有限元程序可以根据刀具和工件接触应力的实际情况,自动确定刀具和切屑间处于何种摩擦状态。
Marc修正的库仑摩擦模型公式为

式中 σn——接触节点法向应力;
σfr——切向(摩擦)应力;
t——相对滑动速度方向上的切向单位矢量;
µ——摩擦因数;
vr——相对滑动速度;
rvcnst——修正系数,物理意义是发生滑动时接触体之间的临界相对速度。
另外,刀具与工件的运动都是有规律或限定条件的,例如固定位移、温度边界等。这些限定条件给出了已知的边界条件,简化了计算,一般有利于问题的解决。
2.4.4 边界条件的定义
边界条件是用来建立包含施加于模型上的载荷及约束边界条件等的分析工况。设定模型的边界条件,单晶硅底部所有位移完全固定,右侧固定x方向位移。热边界条件中,工件和刀具表面以辐射、对流等方式与外界传热,定义热辐射系数和导热系数;在变形区内,考虑工件塑性变形生成热;刀具与工件进行热交换,即定义接触传热系数,以及工件与刀具间的摩擦生热。热传导云图如图2-10所示。

图2-10 热传导云图
以上设定的边界条件还要在载荷工况LOADCASE这一步骤中选择添加后,用JOB提交运行,才能真正在分析过程中得到应用。
2.4.5 建立切屑的分离模型
在以往的有限元模拟中,学者们采用人为地设定分离线的方法实现切屑与工件的分离,而实际材料中是没有分离线的。到目前为止,使用的分离线大致分为几何准则和物理准则。几何准则是基于刀尖与刀尖前工件单元节点距离,在切屑形成过程中的距离小于给定的某个值时,该节点被分成两个:一个形成切屑,另一个形成已加工表面。而物理准则是基于刀尖前工件单元的某些物理量,例如应力、应变、应变能等。当单元中所选定物理量的值超过建立的材料模型中的相应物理条件时,即认为单元节点分离。
Marc提供的自适应网格重划分准则,也称为单元畸变准则。切削模型不依赖于分离准则,当单元达到畸变准则的,程序就会进行自动重划分网格,网格不断地自适应重划分,实现材料的逐步去除。图2-11所示为相同参数下Marc建立的切削有限元模型。本书是金刚石刀具超精密切削,Marc提供的自适应网格重划分作为分离切-屑准则,使得模拟过程中可以考虑到切削刃钝圆半径对切削过程的影响。且刀尖处材料的流向并不是人为设定,而是在网格自适应重划分的过程中自动实现[30]。这也使得建立的切削有限元模型更能描述真实的加工过程。

图2-11 网格自适应重划分
Marc软件的重划分准则有以下几种:
(1)单元畸变准则 如果单元畸变趋于严重,工件的网格自动调整重划分。单元畸变量系统默认参照为单元内角,在当前增量步结束时检查此时单元角度以及对下一个增量步单元角度变化的预测,如图2-12所示。设Xn为增量步开始时的坐标、ΔUn为本增量步的位移,因而有


图2-12 单元角度变化
(2)接触穿透准则 当接触体的曲率达到当前网格不能准确探测穿透时,物体的网格重划分。
(3)增量步准则 在网格自适应重划分设置中,按预先给定的增量步间隔,Marc软件自动进行网格重划分。
(4)内角偏差准则 当单元内角与理想角度的偏差大于一定值时,工件的网格重划分。
(5)直接准则 在进行任何分析之前,首先对物体的网格进行重划分。
这些准则可以单独使用,也可以任意两个或多个组合使用。本书是将单元畸变准则、接触穿透准则、内角偏差准则组合使用的。
由于超精密切削过程模拟是一个典型的高梯度问题[80],在切削变形区域内材料产生高温、大变形。切屑是产生塑性变形最大的部位,随着切削变形的加剧,工件的初始网格会产生严重的畸变,会对求解产生影响,降低求解的精度,甚至无法求解。另一后果就是刀具会嵌入工件内部,与实际超精密切削情况不符。因此,自适应的网格重划技术的另一个优点是能够纠正因过度变形产生的网格畸变,自动重新生成保证后续计算的正常进行、形态良好的网格单元,提高计算精度。
2.4.6 热机耦合
在切削过程变形分析中,切削热通过改变本构关系的材料模型以及热应变来实现与传热过程的耦合。在切削过程热传导分析过程中,切削三个变形区域形成的变形场通过改变热传导空间、边界条件和能量转化来实现和变形过程的耦合。Marc提供的热机耦合分析可精确反应这两种场耦合的影响。本书所考虑的是切屑-工件-刀具系统连续切削过程中的生热传热过程。该系统具有以下特点:工件在第I变形区和第II变形区经受弹塑性变形,产生变形热。此外,刀具前面和切屑的强烈摩擦,产生摩擦热。本书对热传播进行有限元计算分析时,忽略了刀具和工件表面的热辐射作用,这里假设刀具只发生热传导,刀具和工件的初始温度也即环境温度设置为20℃。
平面正交切削的热传导方程为

式中 T——温度分布;
x,y——笛卡儿坐标系;
ux,uy——运动热源在x、y方向的分量;
λ,Cp——导热系数和比热容;
Q.——单位体积内变形区塑性功转换为热量的微分。