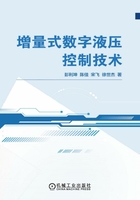
2.3 增量式数字阀仿真分析
阀芯是液压控制阀的关键组成部分,阀芯设计对电液伺服控制系统的位移、流量控制特性及冲击特性等影响十分明显。增量式数字阀控液压系统同样如此,尤其是对增量式数字阀的典型应用对象——数字液压缸而言,更是如此。数字液压缸对使用者而言近似于“开环控制”,使用极其简单,但设计复杂,一旦制造完成后参数固定无法调节,因此其设计过程就显得尤为重要。但阀芯形面的设计是一项复杂的工作,德国、美国等发达国家已采用调节阀阀芯形面的参数化设计技术,而国内阀芯形面的设计目前仍主要采用流量试验或者修形的方法,设计周期长、成本高、精度低,难以满足现代化生产发展的需要。
为深入研究增量式数字阀的阀芯特性,下面利用基于AMEsim建立的增量式数字阀控液压伺服系统模型,结合不同的阀口截面形状、阀芯遮盖形式、输入信号形式等设计使用因素进行仿真分析,研究增量式数字阀的阀芯特性及其对液压伺服控制系统的影响,为增量式数字阀阀芯的设计选型提供一定的参考依据。
2.3.1 阀口截面形式影响分析
1.不同截面形状阀口过流面积计算
为了研究数字阀阀芯型面对系统的影响,这里选择三种阀口形式进行研究,分别为:圆柱形阀口、锥形阀口、矩形阀口,其结构如图2-15所示。
图2-15 阀口形式
a)圆柱形 b)锥形 c)矩形
圆柱形阀口过流面积及水利直径的计算公式为
式中 D——阀芯直径(m);
x——阀口开度(m);
C——湿周长度(m);
W1——圆柱形阀口面积梯度(m)。
锥形阀口过流面积及水利直径的计算公式为
式中 β——半锥角(rad);
W2——锥形阀口面积梯度(m)。
矩形阀口过流面积及水利直径的计算公式为
式中 n——矩形槽个数;
b——矩形槽宽(m);
W3——矩形阀口面积梯度(m)。
仿真中圆柱形阀的阀芯直径D为16mm,根据式(2-13)圆柱形阀的阀口面积梯度为
锥形阀的半锥角β为45°,圆台长度为2mm,根据式(2-15)锥形阀的阀口面积梯度为
式中x为阀芯的位移,由图2-21可知,阀芯的位移是很小的,故式(2-20)进行的简化是合理的。
矩形节流槽的个数n为8,槽的宽度b为2mm,根据式(2-17)矩形阀的阀口面积梯度为
由式(2-19)~式(2-21)的计算结果可知,三种阀的阀口面积梯度关系为:W1>W2>W3,即阀芯位移相同时三种阀过流面积的关系为:A1>A2>A3。在三种阀的压差Δp相同的情况下,根据阀口流量方程:
可知,通过三种阀的流量关系为:q1>q2>q3。
2.不同截面形状阀口过流面积及流量对比
利用AMESim软件HCD库当中的自定义阀块(Spool with Specific Orifice)来定义三种形式的阀芯,只需要设置阀芯的过流面积和水利直径的计算公式即可模拟不同形式的阀芯,其他参数保持不变进行仿真。仿真输入为步进电动机的角位移,信号按照400sin(0.2πt)(单位为rad)正弦规律变化,而液压缸的位移输出以中位为零点,向两侧延伸。
图2-16所示为三种滑阀在液压缸运动过程中进油阀口过流面积的变化曲线,阀口首先打开,然后关闭。通过前1s的仿真曲线可知,圆柱形阀过流面积梯度最大,锥形阀次之,矩形阀最小,与它们的数学模型是一致的。矩形阀过流面积曲线相位滞后约0.2s。
图2-17所示为滑阀一侧回油口流量变化曲线。由图2-17可知,圆柱形阀与锥形阀的流量差别不大,基本保持一致;而矩形阀的流量小,相位滞后约0.2s。通过以上对比分析可知,圆柱形阀与锥形阀的流量特性相似,矩形阀的过流面积小,导致其阀口流量小,降低了系统的灵敏度,进而导致阀口关闭滞后,相位滞后,可从图2-16和图2-17中看到。
图2-16 进油阀口的过流面积曲线
1—圆柱形阀 2—矩形阀 3—锥形阀
图2-17 回油口流量曲线
1—圆柱形阀 2—矩形阀 3—锥形阀
针对矩形阀流量较小的问题进行改进,将矩形槽增加至10个和12个。利用AMESim软件的批处理功能得到的矩形阀槽数N为8、10、12对应的过流面积曲线和阀口流量曲线,如图2-18和图2-19所示。由图2-18可知,随着矩形槽数目的增多,滑阀的过流面积增大,过流面积的相位则会相应的提前。图2-19显示,矩形槽数目增多,阀口流量增加,曲线相位相应提前。结合图2-18和图2-19可知,矩形槽数目增多,滑阀过流面积增加,阀口流量加大,会增加数字液压缸系统的反馈灵敏度,阀口关闭及时,曲线相位滞后减小。
图2-18 矩形阀阀口过流面积曲线
1—N=8 2—N=10 3—N=12
图2-19 矩形阀阀口流量曲线
1—N=8 2—N=10 3—N=12
3.不同截面形状阀口油压对比
图2-20所示为与有杆腔一侧相连滑阀阀口的压力曲线。三条曲线的走势一致,但矩形阀的相位明显滞后约0.2s,滞后的原因上文已经提到过。圆柱形阀的压力曲线有明显的抖动,而矩形阀与锥形阀的压力曲线平滑无明显抖动。圆柱形阀与矩形阀在阀口开关过程中压力有跃变,可以从图2-20中看出,而锥形阀曲线平缓,没有跃变。通过以上分析可知,矩形阀和锥形阀都有改善系统压力振动的作用,且锥形阀还可抑制压力跃变的作用。
图2-20 阀口油压-时间曲线
1—圆柱形阀 2—矩形阀 3—锥形阀
4.阀口截面形状对阀芯位移的影响
图2-21所示为数字阀的阀芯位移-时间曲线,可知圆柱形阀、矩形阀、锥形阀的阀芯位移是依次增加的,且液压缸反向运动(有杆腔为工作腔)时阀芯最大位移大于正向运动时的最大位移,这主要是由液压缸为非对称缸造成的。前文已给出三种阀的过流面积关系为A1>A2>A3,根据阀口流量方程,为了获得相当的流量,圆柱形阀、矩形阀、锥形阀的阀芯位移需依次增加。三种结构的阀芯整个运动过程中所能达到的最大位移分别为0.35mm、0.45mm和0.9mm,圆柱形阀的开度最小且阀口边缘较为锐利,可将其阀口看成薄壁小孔,薄壁小孔会对通过的液压油产生剪切,容易使油液变质降低液压油的使用寿命;另外圆柱形阀芯较大的面积梯度也不利于实现稳定的控制,在阀芯加工精度不高的情况下会对系统控制精度产生较大的影响。锥形阀芯和矩形阀芯的位移量较大,且优化的阀芯型面减小了对油液的损害,油液使用寿命延长;两阀的面积梯度较小,容易控制,其流量微调性能优良。
5.阀口截面形状对系统速度响应的影响
图2-22所示为液压缸活塞运动速度曲线。圆柱形阀对应的速度曲线噪声最大,锥形阀次之,矩形阀最小。圆柱形阀与锥形阀的速度曲线基本保持同步,但矩形阀对应的速度曲线相位明显滞后。图2-22中速度为0处出现的短线,是由于速度方向变化时由于螺纹间隙的存在导致的。由此图可知,圆柱形阀的短线最长,锥形阀次之,矩形阀最小,矩形阀由于流量较小,灵敏度下降,对换向时的螺纹间隙不敏感。
图2-23所示为矩形阀槽数N为8、10、12对应的液压缸活塞运动速度曲线。三条速度曲线都较平滑,说明矩形阀的减噪效果很好。随着槽数的增多,活塞的运动速度加快,则系统的灵敏度增加,从而导致曲线相位提前,这与前面的过流面积及流量曲线一致。
图2-24、图2-25所示为采用不同阀口截面形状时数字液压缸的流量曲线和活塞速度曲线,曲线1、2、3分别对应圆柱形阀口、矩形阀口和锥形阀口。通常滑阀阀芯采用圆柱形或矩形截面,以保证阀芯位移与流量具有良好的线性关系以及较高的压力增益,但是数字液压缸不同:圆柱形或矩形阀口的数字液压缸会出现较大的换向冲击。经过改进设计,阀口形状成为非圆柱形,如锥形或者矩形槽截面,一定程度上可使阀口流量减缓,从而降低阀芯换向时油液的冲击速度,使得整个数字液压缸的换向冲击减少。在图2-24、图2-25中,换向点处锥形阀口的流量最小,锥形阀控制的液压缸活塞速度最小。
图2-21 阀芯位移-时间曲线
图2-22 液压缸活塞运动速度曲线
1—圆柱形阀 2—矩形阀 3—锥形阀
图2-23 矩形阀活塞运动速度曲线
1—N=8 2—N=10 3—N=12
图2-24 阀口流量-时间曲线
1—圆柱形阀口流量q1 2—矩形阀口流量q2 3—锥形阀口流量q3
图2-25 活塞速度-时间曲线
1—圆柱形阀口时活塞速度v1 2—矩形阀口时活塞速度v2 3—锥形阀口时活塞速度v3
图2-26所示为活塞加速度曲线及其局部放大曲线,除在液压缸起停位置及换向点时活塞加速度较大外,整个活塞运动过程中加速度基本趋于零,说明液压缸的工作过程较为平稳。由图2-26b可知,圆柱形阀、锥形阀、矩形阀对应的活塞加速度峰值依次减小,加速度变化过程延长,可见锥形阀和矩形阀可以抑制较大加速度的产生,使系统工作过程更加平稳,而圆柱形阀的面积梯度较大,灵敏度高,不易控制,稳定性较差。
图2-26 活塞加速度-时间曲线
a)活塞加速度曲线 b)局部放大
1—圆柱形阀 2—矩形阀 3—锥形阀
6.阀口截面形状对系统位移精度的影响
图2-27所示为液压缸的步进电动机输入角位移与活塞位移对应曲线。曲线环越平直说明液压缸的线性度越好,这样控制起来精度就会提高。从图2-27中可知:圆柱形阀的线性度最好,锥形阀次之,矩形阀最差。矩形阀虽然减噪的效果良好,但不能满足数字液压缸对准确度的苛刻要求。锥形阀有一定的减噪效果,可以抑制压力跃变,且与圆柱形阀的线性度相差不多,可以满足数字液压缸的工作要求,优于其他两种滑阀。
图2-27 液压缸位移-角位移曲线
1—圆柱形阀 2—矩形阀 3—锥形阀
图2-28所示为矩形阀槽数N为8、10、12对应的液压缸步进电动机输入角位移与活塞位移对应曲线。随着矩形槽数目的增加,活塞的最大位移变大,系统的线性度提高。但总的来说矩形阀的线性度没有其他两种阀好,原因是其过流面积小,流量小,使系统反应迟滞,造成准确度下降。
图2-28 矩形阀液压缸位移-角位移曲线
1—N=8 2—N=10 3—N=12
图2-29和图2-30分别所示为三角波输入时的液压缸位移和跟踪误差曲线,其输入信号对应的液压缸理论位移输出曲线为周期40s、幅值0.225m的三角波,如图2-29中粗实线所示。其余曲线1、2、3分别对应圆柱形阀、锥形阀、矩形阀时液压缸的实际位移输出曲线。
结合图2-29和图2-30可以看出圆柱形阀和锥形阀的位移曲线较为接近,与理论位移曲线相比分别滞后约0.15s和0.2s,所能达到的最大位移分别为222mm和221mm,输入信号停止后10s的位移误差都为0.25mm,这两种形式的阀芯对应的跟踪误差曲线趋势也较为接近,两跟踪误差曲线始终保持约1mm差异;矩形阀的位移跟踪效果明显较差,与理论位移曲线相比滞后约0.45s,所能达到的最大位移为217.6mm,输入信号停止后10s的位移误差也为0.25mm,但其动态跟踪误差比其他两种结构的阀芯要大得多,最大误差可达14mm,且输入信号停止后需较长时间才可达到稳定状态。
图2-29 活塞位移-时间曲线
a)位移曲线 b)局部放大
1—圆柱形阀 2—矩形阀 3—锥形阀
图2-30 液压缸跟踪误差-时间曲线
1—圆柱形阀 2—矩形阀 3—锥形阀
前面已经得出结论:流量越小跟踪误差越大,这也就不难理解图2-29和图2-30中曲线的对比关系了。可见锥形阀和矩形阀在数字阀中的使用不利于提高数字液压伺服系统的控制精度,但是三种阀芯在系统稳定后的静态误差相差不大且都能满足系统要求,对不追求动态跟踪精度的系统,锥形阀和矩形阀仍是可以考虑的。
通过对圆柱形阀、矩形阀及锥形阀芯特性及其数字液压伺服系统特性的对比研究,可以得出如下结论:
1)同一规格下,圆柱形阀阀口过流面积最大,锥形阀次之,矩形阀最小;三种阀的过流面积梯度与流量也遵循此规律。
2)圆柱形阀产生的换向冲击较大,矩形阀与锥形阀可以相应地减小系统的换向冲击,其中锥形阀还可以抑制系统的压力跃变,使系统更加稳定。
3)圆柱形阀与锥形阀的线性度较好,矩形阀由于过流面积较小,阀口流量小,线性度较差,且系统反馈的灵敏度降低,导致相位滞后。但是,矩形阀的缺点可通过增加槽数和增大槽宽进行改善,也可采用将矩形槽与圆柱形阀芯结合来改进。
通过上述分析可知:三种阀芯的阀口过流面积不同,阀口过流面积通过影响阀口流量对整个系统产生影响。圆柱形阀由于阀口面积梯度较大,响应速度快,动态跟踪效果最好;锥形阀与圆柱形阀的控制效果较为接近,只比圆柱形阀的控制效果略差;矩形阀由于阀口面积梯度小,响应较慢,动态跟踪误差大,但三者的静态误差接近。锥形阀和矩形阀对系统的平稳性改善效果明显,且两者还具有改善流道的作用,因此对中间跟踪过程要求并不苛刻的操舵系统可以考虑使用锥形阀,既可以保证系统响应速度和跟踪误差,又可以改善系统的平稳性。
2.3.2 阀芯遮盖形式影响分析
通常,液压滑阀根据中位遮盖情况可分为零遮盖(零开口)、正遮盖(负开口)和负遮盖(正开口)三种形式,如图2-31所示。其中,零遮盖是一种理想情况,由于其对阀芯、阀套壳体的材料、加工、装配等要求极高,而且阀口易磨损,很难保持为理想的零遮盖;正遮盖液压阀密封性好、零位泄漏量小、控制精度高,但在系统中引入了死区非线性,响应速度受限;而负遮盖液压阀在零位的流量增益是零遮盖伺服阀的2倍,具有提高系统的快速性、增加系统的频宽、增加系统的稳定性等优点,在快速高精度负载和位置控制系统中应用广泛。下面结合仿真结果,具体分析阀芯遮盖形式对数字阀及其液压伺服系统的影响。
1.遮盖形式对系统精度的影响
为研究数字阀遮盖对系统产生的影响,在其他参数一致的情况下取数字阀的遮盖分别为1—(+0.2mm)、2—(0mm)和3—(-0.2mm)进行仿真,所得液压缸的位移曲线及跟踪误差曲线如图2-32和图2-33所示。图2-32中粗实线为理论位移曲线,是周期40s、幅值0.225m的三角波。仿真结果显示,负遮盖、零遮盖和正遮盖的实际位移曲线滞后理论位移的时间分别为0.1s、0.12s和0.25s;最大位移分别为223mm、222.6mm和220mm。零遮盖与负遮盖的实际位移曲线非常接近,而正遮盖的实际位移曲线滞后明显,且曲线“削顶”现象明显,这主要是因为正遮盖数字阀在换向时存在滑阀死区,此时虽然滑阀仍在运动,但所有阀口处于关闭状态,活塞运动停止,故出现“削顶”现象。易知正遮盖量越大,最大位移越小,位移曲线滞后越明显,“削顶”越严重。
图2-31 液压滑阀遮盖形式
a)零遮盖 b)正遮盖 c)负遮盖
图2-32 活塞位移-时间曲线
a)位移曲线 b)局部放大
1—遮盖+0.2mm 2—遮盖0mm 3—遮盖-0.2mm
图2-33所示为负遮盖、零遮盖和正遮盖的位移跟踪误差曲线,正向运动时三者的最大跟踪误差分别为2.4mm、3.4mm和6.4mm;反向运动时最大跟踪误差分别为2.8mm、4.8mm和7.7mm;停止运动时静态误差分别为0.2mm、0.04mm和3mm。对比可知负遮盖、零遮盖和正遮盖的动态跟踪误差依次增大,且正向跟踪误差小于反向跟踪误差,零遮盖的静态误差最小。正遮盖由于存在滑阀死区,跟踪误差明显大于其他两种遮盖形式,对于有精度要求的系统来说阀芯应尽量采用负遮盖或零遮盖形式。负遮盖和零遮盖跟踪误差曲线较为接近,但由于负遮盖存在预开口量,滑阀反应灵敏,跟踪效果较好。
图2-33 液压缸跟踪误差-时间曲线
1—遮盖+0.2mm 2—遮盖0mm 3—遮盖-0.2mm
2.遮盖形式对系统平稳性的影响
图2-34 无杆腔压力-时间曲线
1—遮盖+0.2mm 2—遮盖0mm 3—遮盖-0.2mm
图2-34和图2-35分别所示为液压缸无杆腔和有杆腔压力曲线,图中1、2、3曲线分别为正遮盖、零遮盖和负遮盖对应的压力曲线。负遮盖对应的压力曲线变化较为平滑,无明显压力跃变,而正遮盖和零遮盖对应的压力曲线在换向点处有明显的压力跃变,且有杆腔的压力跃变更加明显,跃变幅度可达2MPa。可见负遮盖阀芯可以改善液压腔的工作压力,抑制压力跃变,提高系统的平稳性。
图2-35 有杆腔压力-时间曲线
1—遮盖+0.2mm 2—遮盖0mm 3—遮盖-0.2mm
3.遮盖形式对系统流量的影响
负遮盖也会对系统产生不利影响,图2-36所示为系统供油流量曲线,其中1、2、3分别为正遮盖、零遮盖和负遮盖对应的供油流量曲线。正遮盖的流量曲线除因滑阀死区引起的滞后外,与零遮盖的流量曲线基本一致,但负遮盖由于滑阀开口始终存在,流量大于其他两种遮盖形式下的流量,从图中也可以看出负遮盖的流量曲线明显高于其他两条曲线。这意味着负遮盖的数字阀在工作过程中始终有油液通过且流量较大,那么供油系统必须不断地供油才能维持系统的正常运行,但由正遮盖和零遮盖的流量曲线可以看出系统真正需要的流量并不是很大,对于负遮盖的数字阀来说大部分的油液是直接回流到了油箱,这将导致系统能耗较高,效率较低。
图2-36 系统供油流量-时间曲线
1—遮盖+0.2mm 2—遮盖0mm 3—遮盖-0.2mm
通过本节分析可知:在提高系统精度方面,由于正遮盖滑阀死区的存在控制精度明显不如零遮盖和负遮盖的控制精度。零遮盖和负遮盖的控制精度相近,但零遮盖中位无泄漏,效率高于负遮盖,应该说零遮盖是较为理想的情况,但零遮盖在实际应用中由于阀口的磨损,很难保持为理想的零遮盖。在实际使用中,建议数字阀采用零遮盖形式,如果加工精度不能满足要求可以趋向于加工为遮盖量极小的负遮盖,以期达到零开口的效果,这样做既可以提高系统的精度和灵敏度,抑制压力跃变,也可以提高系统效率。
2.3.3 输入信号形式影响分析
图2-37 活塞位移-时间曲线
a)位移曲线 b)局部放大
1—三角波 2—正弦波
1.输入信号类型对系统的影响
为探究输入信号频率对增量式数字阀控制特性的影响,探究合适的控制方式,这里选取三角波信号和正弦信号两种不同的输入信号形式进行对比研究,频率都为0.025Hz,幅值皆为1080°,则两种输入信号对应的理论位移曲线为频率(0.025Hz)和幅值(0.225m)都相同三角波曲线和正弦曲线,如图2-37中粗线所示,实际位移曲线分别对应图中1和2曲线。仿真过程中进一步考虑液压缸所受负载力的影响,设定活塞向两侧运动至最大伸缩量过程中所受负载力与活塞位移成正比,最大负载力为164kN,因此理论负载力曲线也是频率为0.025Hz,幅值为164kN的三角波曲线和正弦曲线。
由图2-37可知三角波和正弦输入信号下的活塞最大位移分别为224.6mm和222.3mm,正弦信号在最大位移处的误差极小,另外两位移曲线都出现了“削顶”现象且正弦信号的更为明显,“削顶”现象主要是由于滑阀死区造成的,由于正弦信号在最大位移处的速率低,所以“削顶”现象表现的更加明显。
图2-38和图2-39分别所示为液压缸的跟踪误差及速度曲线,对比图2-38中两种信号下的跟踪误差可知:正弦信号对于液压缸最大位移处的跟踪误差改善效果明显,但在液压缸中位时误差较大,由图2-39可知这是由于正弦信号下中间过程活塞运动速度较大引起的。三角波信号下虽然速度始终较为恒定,但由于负载的作用致使最大位移处的误差较大,其值与正弦信号下的最大跟踪误差相当,输入信号的形式对静态误差影响不大,两者的最终静态误差都为0.25mm。
图2-38 液压缸跟踪误差-时间曲线
1—三角波 2—正弦波
图2-39 活塞速度-时间曲线
1—三角波 2—正弦波
根据上述分析,液压缸的跟踪误差不仅和运动速度有关,而且和负载的大小也有关系,具体关系为:速度越大跟踪误差越大,负载越大跟踪误差越大。针对不同的负载应采用不同的控制策略,基本原则是大负载低速运行,小负载高速运行,且必须进行合理的匹配,这样才能将跟踪误差控制在较小的范围内。
图2-40 活塞位移-时间曲线
a)位移曲线 b)局部放大
1—1/30Hz 2—1/40Hz 3—1/50Hz
2.输入信号频率对系统的影响
为了研究输入信号频率对增量式数字阀控制特性的影响,在其他参数不变的情况下设定步进电动机角位移输入信号频率分别为1/30Hz、1/40Hz、1/50Hz,幅值都为1080°,各频率下计算所得的理论位移曲线分别为周期30s、40s、50s,幅值0.225m的三角波,则对应的液压缸运行速度分别为30mm/s、22.5mm/s、18mm/s。各频率下的理论位移曲线及仿真所得的活塞实际位移曲线如图2-40所示,图中粗线为理论位移曲线,细线为实际位移曲线。从图2-40可以看出,三种频率下活塞的实际位移曲线滞后理论位移曲线约0.1s,随着输入信号频率的降低(即运行速度降低),液压缸所能达到的最大位移略有增大。
由于输入信号频率不一致,这里使用跟踪误差与液压缸位移的对应关系曲线进行观察,仿真曲线如图2-41所示。可以明显看出:对应1/30Hz、1/40Hz、1/50Hz输入信号的正向最大跟踪误差分别为4.9mm、3.7mm、3mm;反向最大跟踪误差分别为6.7mm、5mm、4mm。可见输入信号频率越低,液压缸的跟踪误差越小,这也可以理解为液压缸的运行速度对跟踪误差也是有影响的,速度越慢,跟踪效果越好。对于单个频率来讲反向跟踪误差大于正向跟踪误差,主要原因是由于反向运动时有杆腔为工作腔,为了承受同样大的负载有杆腔内压力要高于无杆腔内压力,致使其与供油压力间压差减小,较小的压差导致流量下降,进而造成有杆腔为工作腔时的跟踪误差增大。
图2-41 活塞跟踪误差-位移曲线
1—1/30Hz 2—1/40Hz 3—1/50Hz
图2-42、图2-43所示为输入信号为正弦输入时不同频率下的液压缸活塞位移和步进电动机角位移曲线、活塞速度曲线,1、2、3曲线分别代表0.1Hz、0.2Hz、0.3Hz的仿真结果。图2-42中上侧是回程曲线,下侧是推程曲线,曲线环中部曲线是由液压缸中位启动产生的。可以看出,输入角位移信号频率较低时,活塞位移与角位移基本上呈线性关系;随着频率的升高,它们之间的线性度变差。回程曲线与推程曲线不重合是由于液压缸的非对称性造成的。由图2-43可知,随着信号频率的升高,滑阀死区与螺纹间隙对系统的影响减小,系统的低速抖动减弱,换向冲击也减小。改变信号的幅值也可以得到类似的结论,这两种方式本质上都是由于输入角速度发生变化而对系统产生了影响。
图2-42 缸位移和角位移曲线
1—f=0.1Hz 2—f=0.2Hz 3—f=0.3Hz
图2-43 活塞速度曲线
1—f=0.1Hz 2—f=0.2Hz 3—f=0.3Hz
由以上分析可知:输入信号频率幅值选择要合适,结合实际要求合理设置输入信号,兼顾系统的准确性与稳定性。要提高数字液压缸系统的准确度,步进电动机角速度变化不易过快;但同时角速度变化也不能过慢,否则,液压缸容易产生爬行现象。
通过本节分析可知:随着步进电动机角位移输入信号频率的降低,液压缸的跟踪误差减小,液压缸所能达到的最大位移增大。步进电动机输入角速度越快,系统的跟踪误差越大。选取合适的输入信号,能够使增量式数字阀控液压系统运行相对平稳。