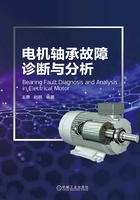
第二节 基于运行状态监测参数的分析方法
第一节中讲述了根据电机轴承设计、安装、储运、使用等各个环节的因素对电机轴承出现故障的诊断与分析。这些是基于设计参数的分析方法。事实上在故障发生之前的状态检查是为了避免故障,而对故障已经出现时候的倒推分析是查找故障原因。这样的分析需要工程师对电机轴承应用技术的所有环节熟练掌握才能迅速找到症结所在。很多时候,工程技术人员会抽取电机轴承的最重要指征,并根据这些指征进行分析就可以做出一定程度的故障诊断与分析。这就是对电机轴承运行状态参数的检查与分析。第二章中提出了这些最常用的运行状态参数,以及测量方法。本节阐述这些测量方法是怎样在故障诊断中应用的。
一、主要使用的状态监测参数
描述电机轴承运行状态的指征参数有很多,电机中最常用的就是轴承的温度参数、振动参数、噪声参数。这些运行参数最终都是通过各种检测手段的信号体现出来的。由于这些运行参数涵盖了电机轴承运行的绝大部分运行状态,所以对这些参数的监测就是我们常说的状态监测,通常也就是对状态参数信号的监测。
一般地,在电机实际投入运行的工矿企业中,噪声信号不易获取,因此更多的时候电机用户使用的是温度信号和振动信号。噪声信号在这种情况下更多的是用人耳聆听的方法作为判断的参考参数出现,很难实现真正的测量。
相应地,在电机进行设计型式试验的时候,往往会做噪声测试。但此时做得更多的是电机总体噪声,而不是轴承噪声检测。一些科研机构可以根据声音的频率分离出某些与轴承相关的噪声特征信号加以分析,原理与振动分析类似。但是,由于条件所限,这种方法在工程实际中所用甚少。
二、基于状态监测信号的时域分析
电机轴承的运行过程是一个随时间推移的过程。状态监测仪器对设备的状态监测(人工或者自动方式)可能是固定时间点的监测,也可能是连续的信号监测。不论怎样,这些状态监测信号在时间轴上如果排列开来,就呈现出一个时序的信号图像。对于设备而言,最著名的状态监测时域图形就是著名的“浴盆曲线”,如图3-4所示。
图3-4中所示的曲线4为“浴盆曲线”,随着时间的推移,这条曲线呈现出中间平滑,两头翘起的形态。这条曲线由三个部分组成:
1)设备投入运行之后的早期失效(infant mortality)。这段曲线中失效率一开始很高,随后持续下降。
2)设备运行时的随机失效(constant mortality/ random mortality)。这段曲线中,失效率是平均持续存在的。对于稳定的设计,这个阶段设备的失效率低并且稳定。

图3-4 浴盆曲线
3)耗损失效(wear out)。随着设备的运行,设备势必出现一定的性能劣化,此时的失效就是耗损失效。它随时间的推移呈现上升趋势。
三部分失效的总和,就组成了“浴盆曲线”,浴盆曲线由其形态可以大致划分为三个阶段:
1)磨合期:设备初装,各种原因引起的失效率偏高,但是随着时间的推移,设备的失效率明显下降。设备的磨合阶段,是各个零部件在磨合期更好地相互协同以达到最终稳定的状态,此时设备的维护成本比正常运行的时候高。
2)稳定运行(稳定)期:经过磨合期,设备各个零部件达到一定的协同,设备稳定于一个低失效率的运行阶段。这就是设备的稳定运行期,在这个阶段里,设备贡献出最大的效能,维护成本最低,是设备用户最重要的使用期。
3)设备耗损期:进入设备耗损期,设备性能劣化带来的失效率上升,逐渐占据主流趋势。设备的维护成本明显增加。此时需要进行设备的维修甚至更换。
浴盆曲线同样适用于电机轴承的运行时域表现。轴承在电机中安装完毕投入运行之后也将经历磨合期、正常运行期和耗损期。
电机轴承的磨合期:轴承在刚刚装入电机投入运行的时候,轴承滚道和滚动体之间的运行就进入了磨合期。轴承在出厂之后运行之前,其滚道和滚动体表面都会有加工过的刀痕。滚动体和滚道之间的接触存在尖峰与尖峰的接触。此时轴承的振动信号表现会比正常运行的时候偏大。同时,轴承内部填装的润滑脂分布在最初期也没有达到最优,随着轴承滚动体的滚动,轴承内部润滑脂重新分布,逐渐达到最优状态。当然这个过程比滚动体和滚道的磨合过程要快。所以很多轴承刚刚投入运行和刚刚完成补充润滑脂之后会出现短时的温度上升,随着匀脂的完成,温度会回到较低的正常水平。
经过磨合期,轴承滚动体和滚道表面的金属经过一些滚动,完成了金属表面“削峰填谷”的过程,金属的部分高点被压平,金属和金属的接触面积达到比较优良的状态。轴承持续稳定运行。此时轴承的振动信号呈现相对较低的稳定水平,轴承的运行温度也保持稳定。
但是随着轴承的运行,轴承滚动体和滚道内部或者表面逐渐出现劣化。如果润滑正常,此时的劣化多数发生在金属内部;如果由于润滑等其他原因,也可能出现在金属表面。如果再考虑保持架、密封件等的原因,轴承的故障率逐渐增加,进入耗损期。此时不论哪个地方开始出现劣化,当劣化达到一定程度,轴承的振动、温度等信号就会有所反应。感官上可能出现振动变大、噪声变大、温度升高等现象。
综上所述,可以看出,轴承的振动、温度、噪声等信号随着轴承投入运行时间的变长呈现一定的规律,基于时序的信号变化趋势分析,就是我们常说的时域分析方法。时域分析方法相当于对轴承整个运行生命周期内的体征监测,同时时域监测更多的是分析趋势变化,从而做出状态判断或者预警。具体不同信号的时域分析方法可以参考本书后续相关章节。
三、基于状态监测信号的特征量分析
基于状态监测的电机轴承故障诊断与分析中时域分析是判断电机轴承“健康体征”的正常与否,或者是否有预警。但是如果想对电机轴承已经出现的“健康体征”预警进行更深入的分析,以初步确定问题的某些原因,那就需要借助基于状态监测信号的特征量分析方法。
基于状态监测特征量分析的方法在振动和噪声分析中经常用到。这个分析方法的基础就是对信号的分解和解耦。将标志某些基本特征的信号从总体信号中分离出来。在振动分析中最典型的就是使用傅里叶分析的方法,将振动信号分离成不同频率的振动信号。是通过对不同频率信号的幅值分布与电机轴承或者电机本身某些零部件的特征频率分布进行对比分析,从而确定故障发生的部位的一种方法,这种方法就是电机轴承振动信号的“频域分析”。本书第五章会就振动的频域分析做详细介绍。
对于噪声信号的特征量分析方法和对于振动信号的特征量分析方法原理一致。只是噪声的采集在现场相对于振动而言比较困难,同时容易受到干扰。一旦干净的信号得以采集,分析方法就大同小异了。
需要说明的是,即便是基于特征量的振动信号分析,依然只能进行大致定位和判断,诸如对中不好,地脚松动或者判断轴承某个零部件存在问题。但是如果想更深入地对电机轴承故障或者失效进行分析,就只能借助专业的失效分析技术了。
前面关于设备运维与故障分析的部分描述的“定位”与“定责”的概念中,振动频域分析的地脚松动问题和对中问题的结论属于以电机为对象的“定责”判断,但是如果界定出轴承“内圈失效”“外圈失效”“滚动体失效”“保持架失效”的时候,只能看作对轴承的“定位”判断。此时失效分析就成为判断原因的“定责”分析手段。通过定责,才能找到根本原因。