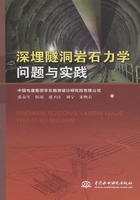
第五节 深埋脆性岩石无损取样技术
一、初始损伤
在大理岩单轴压缩配合声发射试验的过程中观测到在加载前期出现了大量的声发射现象,意味着大理岩可能在加载之前就已经受到损伤,不论从科研还是从工程建设角度看,都有必要了解和论证传统采样方式下获得的大理岩试样内初始损伤裂纹的形成原因。估计初始裂纹或者产生于地质历史时期,是岩石的原状特性,或者在取样钻进过程形成,并非岩石的原状特性。因此,论证深埋条件下钻孔取样是否会导致岩芯损伤成为一项基础性的工作。
在深埋条件下进行钻孔时,从力学角度考虑,是在岩体一个狭小的圆环区域内移除岩体,形如开挖。这样一来,在钻进过程中该圆环区域一带可以出现强烈的应力变化,如孔底一带(相当于掌子面)可能出现的强烈应力集中,以及所形成岩芯的应力释放,即与孔底相连的岩芯可能受到应力集中的影响,而远离孔底的岩芯会出现强烈的应力松弛,因此,在深埋部位的钻进过程岩芯可能经历一个剧烈的应力变化过程,使岩芯部分乃至全部经历屈服,即产生破裂损伤。
为证实上述分析结果的现实可能性,在开展任何现场工作之前,先进行了钻进过程的计算机模拟,以了解钻进过程中岩芯的应力变化过程,并判断这种应力变化可能造成的影响。
图3-24表示了计算模型和相关成果,计算成果显示,对于Ⅱ类大理岩而言,当埋深超过1000m以后进行76mm的钻进时,岩芯可以局部受损。其中在2000m埋深条件下的钻进可能导致岩芯除核部以外接近70%的体积出现不同程度的损伤。也就是说,前述试验岩样的损伤可能主要集中在浅表,而核部一带相对完整,使得试验成果的深化解译可能相对复杂。

图3-24 钻孔导致的岩芯应力变化历程和潜在损伤可能性的3DEC模拟
在2000m埋深Ⅱ类大理岩中的钻孔可以普遍出现岩芯饼化现象,如在2~4号引水洞之间2号横通道一带(埋深大约1800m)距洞壁20m以外完整岩体中获得钻孔岩芯基本全部饼化,揭示了深埋大理岩钻进过程中岩芯损伤的可能性。
二、无损取样
把国际上关于脆性结晶岩石破裂特性的研究成果和认识引用到锦屏工程以后,相关分析和补充测试成果揭示了大理岩可能具备的脆性破裂特性,特别是由于大理岩强度相对岩浆岩较低、而初始条件下所处的地应力水平相对更高一些,取样过程可能导致岩石损伤,首先要求在取样和试验环节均进行相应的改进,尽可能获得原状条件下的岩石样本。其次是在整个室内试验过程中需要对岩样损伤情况进行检测,希望能够获得反映现实中岩石所具有的实际强度,为设计工作提供可靠的信息资料。
由此可见,如何获得深埋原状岩样成为需要解决的一个现实问题,解决这一问题的途径有如下几种:
(1)二次套钻采样技术。计算结果揭示的岩芯损伤是从表面向核部发展,因此在埋深相对不大的情况下,采用大口径的钻孔获得岩芯以后再进行二次套钻可望获得避免深埋钻进导致的损伤。
(2)用浅埋样代替深埋样。至少要求为同一地层的相同岩性段,但现实中可能仍然存在缺乏足够可比性的问题,即浅埋样试验结果能否反映深埋原状岩石的力学特性问题。
(3)无损取样技术。这是针对锦屏工程现实条件和要求提出的专项技术,需要从理论上叙述和论证这一技术的合理性和有效性。
在上述三种方法中,前两者都有一定的局限性,套钻适合于钻进过程中岩芯损伤相对不严重的情形,否则对钻进要求过高而难于实施。第二种方式显得有些间接,并不是直接“深埋”岩样。
第三种方法的力学原理与套钻相同,即解除被采样区岩体的应力,如图3-25所示,但这种解除过程是可控的、逐渐的。从力学原理上讲,就是通过控制被采样区岩体应力解除过程应力路径的方式,即控制屈服区的范围达到维持围岩的完整性,在工程中类似于通过改变开挖方式为维持围岩稳定。

图3-25 深埋条件下岩石无损取样方法实施布置示意图
最终采用的应力解除孔布置方案如下(图3-26):应力解除孔(Y孔)14只,孔径110mm,孔深11m,呈圆形布置(半径50cm),孔中心间距22.3cm,相邻两孔间岩壁厚11.3cm;取芯孔5支,孔径也为110mm(经与试验方沟通,需要采用直径为90mm的岩样,故作此改变),其中中心孔(E孔)深19m,5~15m段取无损岩样;其余4只取芯孔(A~D孔)布置在以E孔中心为圆心,半径为20cm的圆周上,孔深15m,取芯段为5~15m。

图3-26 修改后的应力解除钻孔平面布置图(单位:mm)
图3-27给出了取芯孔现场放样及取芯完成后的情况,图3-28则给出了所取芯样的情况。

图3-27 取芯孔现场布置情况

图3-28 现场取出的直径90mm的芯样
取样后对岩样进行整理,发现经过周边孔应力解除后,内部取芯孔(图3-29)的岩芯饼化现象较应力解除孔中的岩芯(图3-30)有了明显的改善,证明前期设计的应力解除方案基本达到设计目的。
三、效果验证
岩石损伤程度的判别可以通过很多方法研究,其中最直接的观测方法是CT或者电镜扫描(SEM)。这两个方法虽然非常有效,但是为了研究在持续荷载作用下裂纹的发展,不得不停止加载,然后利用SEM或者CT来观察裂纹情况。然而,这个过程会产生新的裂纹,对分辨由应力产生的裂纹造成了困难。更进一步说,在没有压力作用的状态下,可能会使人对裂纹的形状产生错误的认识。
第二种方法测试在加载过程中弹性波来判断微破裂的发展。这个方法的不利条件是声波传感器不是很敏感,而且很容易被冲击破坏。对破裂界限的判断测量也是很困难和危险的,这也同样限制了这个方法的应用。
第三个方法便是测定由微裂纹扩展的声发射信号。这个测量方法的好处便是对试验没有任何的扰动。

图3-29 无损取样钻孔中的岩芯情况

图3-30 应力解除孔中岩芯饼化现象
声发射(AE)是在材料内部能量迅速释放而产生的短暂弹性波。因为声发射监测是被动地接受信号,因此它提供了一种研究对受载状态下试验破坏机理的无损的测试方法。
目前声发射已经被广泛地应用于岩石地下工程,被证明是对测试试件完全无损的有效的测试方法。声发射的监测是通过在试件表面的声发射探头来实现的。声发射探头将声波信号转换成电信号。这个信号通过前置放大器增强,并将其数字化,最后由声发射监测仪记录(图3-31)。

图3-31 Disp声发射测试系统

图3-32 液压加载试验机
本次试验所采用的声发射测试系统是由美国物理声学公司(PAC公司)生产制造。该声发射系统包括声发射卡、声发射主机系统、声发射传感器、声发射前置放大器、声发射处理软件,其核心部件为声发射卡,依据其声发射卡型号不同而构成三个声发射系统。声发射处理软件Aewin-TM可以在WINDOWS环境下进行实时声发射采集、外参量输入采集及分析软件包,包括前端数字滤波、图解滤波,AE特征提取、报警输出,各种定位功能,2D、3D图形,多参数分析、相关分析、聚类分析;波形处理及相关分析,FFT分析;灵活的图形功能,图形打印及输出;HIT数据线形显示、统计及重放功能等。另外,在WINDOWS环境下AE信号后处理分析软件AEwinPOST可以完成特征增强的滤波功能;重新特征提取、数据文件融合;灵活的图形分析功能;丰富的波形/FFT分析功能及HIT统计等功能。
本次声发射测试是在YE-200A液压加载试验机上完成的(图3-32),获得了较为理想的声发射撞击记录,尤其是无损样和损伤样前期加载过程中出现的声发射信号有明显的区别,在图3-33中声发射信号在前期较图3-34有明显减少,也证明了无损取样技术的有效性。

图3-33 无损样D38-2声发射事件数

图3-34 有损样Y11-3声发射事件数