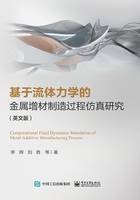
3.1 Introduction
L-PBF,used to be known as Laser-based Powder Bed Fusion (L-PBF),is a major technological approach in the additive manufacturing of metal materials. The technology uses laser as the energy source,and scans the metal powder bed layer-by-layer according to the planned path in the three-dimensional slice model.The scanned metal powder is melted and solidified to achieve the effect of metallurgical bonding,and finally obtain the metal designed by the model Components. There are many types of metals that can be used in metal additive manufacturing,such as titanium alloys,nickel alloys,steel,aluminum alloys,magnesium alloys,and other alloys. In the process of parts manufacturing,the metal powder is melted under the action of high-energy density laser,and the molded part can directly reach a density of more than 99%;the entire working chamber is sealed in an inert gas environment to avoid oxidation of metal materials at high temperatures. Processing titanium alloy and other active metals;through the design of the support structure,it is possible to print products of various complex shapes,including complex curved surfaces with empty parts,structures with internal flow channels,and empty complex shapes.
Many problems have been raised for L-PBF technology these years,and among these the reduction of part quality caused by the spatters introduced by the molten pool is significant [1]. The spatters eject randomly and absorb or scatter partial laser energy during the printing process [2],and their re-deposition on the workbench leads to a limited surface quality of products,because insufficient removal of spatters can result in the interaction between the laser beam and spatter particles,leading to attenuation of the laser energy and re-deposition of the particles on the surfaces exposed to the laser [3].
A practicable solution is to improve the uniformity of the shielding gas flow above the workbench,because uniform airflow can more effectively take away sputtered particles,reducing the number of particles adsorbed on the surface of the part,thereby improving product quality. The calculation results of the flow field inside the printer show that the protective argon gas flow used to blow out the particles above the workbench will be disturbed by the argon gas flow in the printer chamber,causing the argon gas flow to deflect or even form a swirling argon gas flow. The removal rate of sputtered particles is reduced,which directly affects the quality of parts.
In order to improve the uniformity of the flow field above the workbench,a fluid stabilizing cover is added to the printer chamber. The fluid stabilizing cover was designed with consideration of interruption with other parts inside the printer,and would not affect the powder feeding mechanism,the optical path of the high-energy laser,etc.,and also took into account the characteristics of the flow field inside the printer. In this chapter,to numerically investigates its feasibility,a CFD model coupled with a discrete phase model (DPM) for the flow field in the L-PBF printer is developed and used to simulate the flow field above the workbench and the adsorption of particles after using the fluid stabilizing cover. The influence of the fluid stabilizing cover on the flow field above the workbench,the change of particle removing rate,etc.,are investigated numerically.