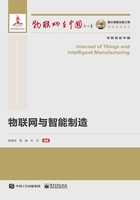
4.2 五大装备
4.2.1 数控机床与机器人
中国智能制造战略规划站在历史的新高度,从战略全局出发,明确提出了我国实施制造强国战略的第一个十年行动计划,将“高档数控机床和机器人”作为大力推动的重点领域之一,提出机器人产业的发展要“围绕汽车、机械、电子、危险品制造、国防军工、化工、轻工等工业机器人应用,以及医疗健康、家庭服务、教育娱乐等服务机器人应用的需求,积极研发新产品,促进机器人标准化、模块化发展,扩大市场应用。突破机器人本体、减速器、伺服电机、控制器、传感器与驱动器等关键零部件及系统集成设计制造技术等技术瓶颈。”并在重点领域技术创新路线图中明确了我国未来十年机器人产业的发展重点主要为两个方向:一是开发工业机器人本体和关键零部件系列化产品,推动工业机器人产业化及应用,满足我国制造业转型升级迫切需求;二是突破智能机器人关键技术,开发一批智能机器人,积极应对新一轮科技革命和产业变革的挑战。
机床是生产机器零部件的机器,简单地说,就是生产机器的机器。数控机床是机床的数字化和智能化,主要通过数控装置发出信号,控制机床按图纸的要求,根据形状和尺寸,自动地将零件加工生产。数控机床较好地解决了复杂、精密、小批量、多品种的零件加工问题。数控机床的出现是机械零部件的生产从手工化到机械化,再到数字化的应用过程。
根据应用环境不同,国际机器人联合会(IFR)将机器人分为两类:制造环境下的工业机器人和非制造环境下的服务机器人。工业机器人是在工业生产中使用的机器人的总称,是现代制造业中重要的工厂自动化设备;服务机器人是服务于人类的非生产性机器人,服务机器人技术主要应用于非结构化环境,结构比较复杂,能够根据自身的传感器,通过通信获得外部环境的信息,从而进行决策,完成相应的作业任务。
而工业机器人是高精尖的高科技产品,很多核心零部件(如伺服电机、驱动器、控制器、减速器等)都需要精确度高的机床来生产,包括转盘、大臂、小臂、箱体、腕体等关键零部件也需要机床来完成,即便人工和机械能生产出来,也很难确保产品的精确度。核心或关键零部件有丝毫的误差都会影响工业机器人的运动和操作精度。尤其是电子产品行业对工业机器人的要求非常苛刻。所以,只有确保关键技术和零部件的精确度,工业机器人应用和推广才有技术和质量基础。目前工业机器人与数控机床融合发展是一种趋势。
为进一步抢占国际市场,提升制造业在全球的竞争性地位,各经济强国跃跃欲试,纷纷制定发展规划,以图抢占先进机器人技术的发展先机。目前,德国政府推行“工业4.0”战略,构建“智能工厂”,打造“智能生产”,其重点课题之一是人与机器、机器与机器之间的交互合作。美国2013年提出了“美国机器人发展路线图”,将围绕制造业攻克机器人的强适应性和可重构的装配、仿人灵巧操作、基于模型的集成和供应链的设计、自主导航、非结构化环境的感知、教育训练、机器人与人共事的本质安全性等关键技术。2015年年初,日本政府公布了《日本机器人新战略》,并在其五年行动计划中,明确提出要“研究开发下一代机器人中要实现的数据终端化、网络化、云计算等技术”。韩国政府近年来陆续发布多项政策,旨在扶植第三代智能机器人的研发与应用,2012年韩国公布的《机器人未来战略2022》,其政策焦点为支持韩国企业进军国际市场,抢占智能机器人产业化的先机。在美国、日本、欧洲等技术强国和地区的大力推进下,近5年来下一代机器人样机、示范应用乃至实用系统不断涌现。
从我国目前来看,下一代工业机器人需求市场尚未完全成熟,但具有战略意义的共性技术研发、储备又尤为迫切。当前我国发展下一代机器人产业,首先应注重夯实机器人产业技术基础,着力推动现有机器人的产业化进程,加快自主品牌机器人在国内市场的推广应用。其次探索新的技术研发模式,鼓励科研院所与企业发挥各自优势,多方建立下一代工业机器人前沿、共性技术研发与储备的国家级平台,从中国的国情、需求出发,突破下一代机器人核心技术,研制出下一代机器人样机系统、产品,并推进产业化进程,抢占下一代机器人国际制高点。对应用于不同领域的机器人产品,实施不同的发展战略:一方面,以企业为核心,以共性技术平台为支撑,优先发展下一代工业机器人,推进产需对接,抢占发展制高点;另一方面,以市场为导向,把握国内需求特点,发展医疗、养老助残等服务机器人和特殊服役环境下作业的特种机器人。
4.2.2 增材制造设备
增材制造(Additive Manufacturing,AM)又称为3D打印,是以数字模型为基础,将材料逐层堆积制造出实体物品的新兴制造技术,体现了信息网络技术与先进材料技术、数字制造技术的密切结合,是先进制造业的重要组成部分。
当前,增材制造技术已经从研发转向产业化应用,其与信息网络技术的深度融合,将给传统制造业带来变革性影响,被称为新一轮工业革命的标志性技术之一。世界各国纷纷将增材制造作为未来产业发展新的增长点重点培育,推动增材制造技术与信息网络技术、新材料技术、新设计理念的加速融合,力争抢占未来科技和产业制高点。
增材制造技术起源于20世纪的美国。1983年,美国科学家查尔斯·胡尔(Charles Hull)发明光固化成形技术并制造出全球首个增材制造部件。1986年,查尔斯·胡尔获得了全球第一项增材制造专利,同年成立3D Systems公司。1987年,3D Systems公司发布第一台商业化增材制造设备,全球进入增材制造时代。随后,熔融沉积成型技术(FDM)、激光选区烧结(SLS)、激光选区熔化(SLM)、激光近净成型(LENS)、电子束选区熔化(EBSM)、三维立体打印(3DP)、分层实体制造(LOM)、生物3D打印等成型工艺先后出现。20世纪80年代末,我国启动开展增材制造技术的研究,研制出系列增材制造装备,并开展产业化应用。1988年,清华大学成立了激光快速成型中心。1993年,国内第一家增材制造公司——北京殷华激光快速成型与模具技术有限公司成立。随后,华中科技大学、西安交通大学、西北工业大学、北京航空航天大学等高校开展增材制造技术的研究和产业化。此外,依托社会力量成立的北京隆源自动成型系统有限公司,从1993年开始研发SLS增材制造设备,同年5月,国内首台工业级增材制造设备——激光选区烧结(SLS)设备样机研发成功。2015年,为加快推进我国增材制造产业健康有序发展,工业和信息化部、国家发展改革委、财政部联合发布了《国家增材制造产业发展推进计划(2015—2016年)》。
全球增材制造产业已基本形成了美、欧等发达国家和地区主导,亚洲国家和地区后起追赶的发展态势。美国率先将增材制造产业上升到国家战略发展高度,引领技术创新和产业化。欧盟及成员国注重发展金属增材制造技术,产业发展和技术应用走在世界前列。俄罗斯凭借在激光领域的技术优势,积极发展激光增材制造技术研究及应用。日本全力振兴增材制造产业,借助增材制造技术重塑制造业国际竞争力。
经过20多年发展,我国增材制造产业化步伐明显加快。在《国家增材制造产业发展推进计划(2015—2016年)》等相关规划政策的引导和支持下,我国增材制造产业快速发展,关键技术不断突破,装备性能显著提升,应用领域日益拓展,生态体系初步形成,涌现出一批具有一定竞争力的骨干企业,形成了若干产业集聚区。
我国增材制造产业已初步形成了以环渤海地区、长三角地区、珠三角地区为核心,中西部地区为纽带的产业空间发展格局。环渤海地区,增材制造产业发展处于国内领先地位,形成了以北京为核心,多地协同发展,各具特色的产业发展格局。长三角地区,具备良好的经济发展优势、区位条件和较强的工业基础,已初步形成了包括增材制造设备研究开发、生产、应用服务及相关配套设备的增材制造产业链。珠三角地区,增材制造产业发展侧重于应用服务,主要分布在广州、深圳、珠海和东莞等地。此外,陕西、湖北、湖南等省是我国增材制造技术中心和产业化重镇,集聚了一批龙头企业。安徽省也是增材制造产业的重要集聚区,芜湖市繁昌县的春谷3D打印智能设备产业园已成为华东地区最大的增材制造产业集聚区。
近年来,增材制造技术广泛应用于航空航天、汽车、医疗、文化创意、创新教育等众多领域,越来越多的企业将其作为技术转型方向,用于突破研发瓶颈或解决设计难题,助力智能制造、绿色制造等新型制造模式。
4.2.3 传感器与控制设备
传感器是设备感受外界环境的重要硬件,决定了装备与外界环境交互的能力,是设备智能化的硬件基础,尤其在很多智能设备中,传感器决定着设备的核心能力。在智能制造的传感器应用领域,不同行业间的差距非常大。对于石油化工等流程工业来说,需要用到的新型高端工业传感器较少,但在高端制造领域,传感器的国产化率还很低。智能制造所需的某些特殊部件,如需要耐高温高压的传感器,国内产品的可靠性、稳定性还比较低。
智能传感器作为网络化、智能化、系统化的自主感知器件,已成为实现智能制造和物联网的基础。当今的智能传感器模块包含与原始传感器集成的某些处理能力,它所面临的主要挑战可归结为三点:第一个是技术本身;第二个源于行业宽泛的分散特性;第三个是呈几何式增长的复杂性。
随着微机电系统(MEMS)、激光技术、高科技材料等的技术进步,传感器的研发呈现多样化的趋势,有的利用生物材料模拟人类皮肤,创新传感器的触觉;有的利用MEMS技术研发微型智能化传感器,从而有利于复杂系统的集成;有的利用高精度的激光技术创造激光雷达,从而有利于系统实时感知周边障碍物与环境,等等。总体而言,传感器的研发过程呈现两个阶段的趋势。
第一个阶段:技术创新,根据未能满足的需求开发新产品。在第一阶段中,传感器研发创新的方向源于智能装备、创新设备的需求,研发人员根据使用需求,创新出新型传感器。
第二个阶段:成本降低,应用落地,产品逐步切合产业化需求。在第二阶段研发创新的过程中,为了满足人们对智能装备产业化应用的需求,研究人员从对技术开发的关注转为对成本下降的关注,以实现传感器大规模生产,智能装备产业化应用的愿景。
我国当前的传感器研发除了要丰富产品技术品种,更多的还要与市场形成一个完整的产业链条,最终通过完美的市场化运作来进行产品推广,特别是某些应用范围相对有些窄的高端产品,通过市场运作,才能更好地使业界人士了解国内最新的技术动态,为之后的业务拓展留有充足的时间。
此外,由于传感器模块中的存储器成本非常高,云存储成为本地存储和处理可行的替代方案,因此必须使传感器智能化,并确保传感器能够过滤掉大部分无用的数据,从而防止超出内存。总体来说,我国传感器产业,除在品种上要努力追赶之外,更多的还要进行技术上的创新,顺应行业发展潮流,进行新功能、新特性的传感器研发,从而打入主流传感器市场。
4.2.4 装配与检测设备
随着新一代信息通信技术与先进制造技术的深度融合,全球兴起以智能制造为代表的新一轮产业变革。自动化精密零部件机械加工装配、自动化装配生产线是智能制造的组成部分,不但可以大幅度减少人工,同时可保证产品组装的质量。欧美先进制造业都已大量采用自动化装配检测线,我国随着智能制造、供给侧改革的推进,自动化、智能化的发展需求与日俱增。
制造,检测先行。对于制造业来说,越来越重视对制造业过程的控制,必须采用先进的测量技术对制造过程进行全面、严格的监控,最终可以使工业制造过程更加稳定、更加可控制与预测。智能检测方式可以决定智能制造水平的高低。
而当前,生产工艺流程和人工操作严重制约了企业的产能和产品质量,在生产线上引入自动化装备提高生产效率已形成业内共识。汽车零部件、航天航空、军工装备、航天军工行业装配自动化、生物医药装备等制造业企业陆续进场,对生产装配线进行自动化、智能化改造。
装配与检测设备是以现代信息技术为核心,集成计算机技术、人工智能技术、传感技术等,涵盖自动装配生产线、自动检测生产线、自动校核生产线等成套装备。可完成融生产线信息采集监控系统、ANDON系统、输送系统、自动化设备等为一体的完整系统解决方案,在汽车及零部件、低压电器、厨电、电梯、安防、新能源等行业领域进行广泛应用。
可以预见,物联网、协作机器人、预测性维护、机器视觉等技术迅速兴起,为制造企业推进自动化建设提供了良好的技术支撑。加上国家和地方政府的大力扶持,使各行业越来越多的制造企业开启了机器换人的进程,加快自动化装配和检测设备的投入。
4.2.5 智能物流设备
在智能制造的发展背景下,实现智能物流系统与智能制造系统的互通互联、深度融合是目前很多企业研究的课题。
智能物流设备实现了物料在生产工序间流转,支持智能制造系统高效运行,是实现智能制造的核心与关键,主要具有以下应用。
(1)企业外部供应链中的应用
在制造企业的外部供应链中,将供应商、制造商、分销商、零售商到最终用户各个节点串联起来的关键就是物流;智能物流的出现使供应链更加高效、透明。
(2)企业内部供应链中的应用
企业内部的生产制造是由生产工艺与生产物流共同组成的,物流系统将整个工厂的各个加工工序有效衔接。智能物流系统以物联网为基础,利用射频识别(RFID)、光电感应、红外感应器、激光扫描器、机器视觉识别等信息传感设备,将被处理对象与互联网连接,实现智能制造与智能物流的有效融合。因此,智能物流不仅是连接物料供应和生产的重要环节,还是构建智能工厂的基石。
(3)智能制造与智能物流无缝集成应用
智能物流系统将工厂内的智能识别设备(如RFID、传感器等)、智能物流装备、信息控制系统(如MES等)有效串联,应用于从采购、生产、仓储到发货等全部作业环节。因此,智能物流系统是智能制造企业提高生产效率、订单交付能力、库存周转水平三大智能制造关键指标的重要支撑,也是保证产品品质、提升制造企业竞争力的核心。