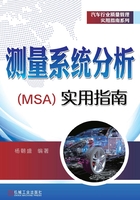
2.2 测量系统分析的应用范畴
2.2.1 测量系统分析在质量管控中的应用
质量管理经过一百多年的发展已臻高峰,在现代工业产品制造的质量管控模式里,我们通常会看到如图2.2.1所示的模式。

图2.2.1 质量管控模式范例
当然,不同的企业会有不同的调整,有些企业对设计端是没有进行质量管控的,有些企业会在FQC与OQC之间增加一个OOBA(开箱检验),但无论何种组合形式,现代企业的质量管理已经迈入了全面质量管理(TQM)阶段。全面质量管理不仅对全面性、全员性参与进行了要求。还对管理的科学性提出了明确的要求。全面质量管理常用的七种管理工具包括:统计分析表和措施计划表、排列图、因果分析图、分层法或分类法、直方图、控制图和散布图。
我们都清楚,上述七种管理工具都是基于对数据的分析而建立起来的管理工具和分析方法,而绝大多数的数据均来源于测量,没有可靠的数据来源,全面质量管理就无从谈起。
两种典型的管理过程如图2.2.2所示。
如果是一般的管理过程,并不产生可见的测量数据。比如你的主管让你打印一份设计图纸。输入的是你主管对图纸的需求,输出的是这份指定的图纸,操作过程就是你打印图纸。
那如果我们要管理的是测量过程呢?毫无疑问,过程中一定是要产生显而易见的数据,这些数据无论是离散的还是连续的,我们均应将此过程看作测量管理过程。而测量管理过程就应该对过程产生的数据进行可靠性、有效性的分析和保证。这种分析和保证的手段通常有两种:数据处理、测量系统分析(MSA)。
数据处理是对数据本身的质量进行分析,比如离群值的判别和处理、正态性检验等;而MSA则是专注于测量系统本身,在未产生数据前,先对测量系统进行分析,保证测量系统的可靠和稳健,使得产生的数据具有很高的可信度。

图2.2.2 一般管理过程和测量管理过程
实际上在质量管理的过程中,测量的含义更宽泛,它不仅仅是局限于用测量系统进行的测量,它还包括对组织管理的效能和业绩进行测量,因此我们在理解质量管理的要求时,要区分这种概念上的差异。图2.2.3所示为IATF16949中以过程为基础的质量管理体系模式。

图2.2.3 以过程为基础的质量管理体系模式
图2.2.3中的“测量”就是一个非常宽泛的过程,它不仅包括我们狭义上的测量,也包括对管理效能和业绩的监测过程,因此在理解质量管理对测量的要求时,需要很好地理解这种概念上的延伸。
要特别提出的是,MSA在质量管控中不仅仅是在质量管控的过程中起到作用,实际上MSA贯穿于TQM的所有测量管理过程。例如产品设计阶段样件的测量、过程设计的测量系统的引进和建立、工艺变更的确认、质量改进的测量和分析、客户投诉的确认过程等。产品制造过程仅仅是MSA最常见的一种应用,千万不能误以为MSA仅仅出现在产品的制造过程中,这样理解容易让MSA的应用陷入困境,这种困境在管理上往往是很被动的。
2.2.2 测量系统分析在过程能力研究中的应用
质量管理中非常重要的一个方向是保证产品制造过程的能力,质量检验关注的是零件或成品是否合格,而过程能力的研究关注的是零件或成品的一致性。2.2.1节提到了MSA在质量管控中的重要作用,本节将阐述MSA在过程能力研究中的重要作用。
1.过程的能力与测量系统分析的关系
为了更好地理解过程的能力与MSA之间的关系,我们先来理解一下统计学中位置变差和宽度变差,以正态分布为例,两种变差如图2.2.4所示。

图2.2.4 正态分布位置变差与宽度变差
从图2.2.4中我们可以看出,位置的变差是由均值发生变化而引起的一种偏离,而宽度变差是由于标准差发生变化而引起的一种集散程度。前者更多地应用于产品的合格性判别,例如质量检验,后者更多地应用于工艺过程能力的研究。两者均可以应用于对过程的监控,IATF16949引用的五大工具中的SPC(统计过程控制)就是基于这两种基本的统计原理而进行展开的。相应地,SPC的控制图中就分别包含有均值()图、标准差(S)图,或替代的极差(R)图,而它们的功能就是监控位置变差和宽度变差。换句话说,均值图监控的是产品是否合格,标准差图(或极差图)监控的就是产品的一致性是否满足要求[3]。
理解了位置变差与宽度变差的概念之后,我们再来考察两个工艺过程A和B,假定标准差σ是相同的,考察均值μ,如图2.2.5所示。

图2.2.5 比较两个过程对产品的合格性判别
通过对比图2.2.5中两个制造过程可以发现,过程A的实际测量值的分布大部分落在规格下限(LSL)的外部,因此其测量的均值μ1与目标均值μ0之间有很大的测量偏倚;而过程B却相反,过程B的实际测量均值μ2与目标均值μ0之间的测量偏倚就相对较小。我们当然有理由相信过程B在产品的合格性判别上优于过程A,从概率上说,过程B判错的概率要比过程A低。
下面再假定均值μ相同来考察标准差σ,如图2.2.6所示,同样比较两个工艺过程A和B。
从图2.2.6我们可以很清楚地知道三个事实:

图2.2.6 比较两个过程得到的测量值
① 过程A制造出的零件一致性较过程B制造出的零件一致性要差。
② 过程A的测量系统波动较过程B的测量系统波动要小。
③ 过程A与过程B在最终的测量结果上并没有明显的差异。
通过三个事实的比较,我们能够很容易获知,过程A的零件波动与最终观测到的结果更接近一点;换句话说,在测量值是否更接近实际值的程度上来看,过程A优于过程B。
而图2.2.6也正是考查一个制造工艺过程的能力的基础。我们用方差来表达这种波动,无论是零件的波动(实际零件变差)、测量系统的波动(测量系统变差),还是最终我们看到的结果的波动(观测总变差),令实际零件变差为:;测量系统变差为:
;观测总变差为:
。
则有关系式:

式(2.2.1)是测量系统与过程能力的关系式,也就是MSA工作在过程能力的研究中起到至关重要的作用。而SPC对工艺过程的监控就是将近似地看成是
,其前提条件是
要足够小,具体是多小?如何降低它?这就是MSA研究的范畴了。
2.SPC与MSA的关联性
从前文内容我们会自然而然地联想到,做SPC一定要以MSA为前提,不能忽略MSA而独立开展SPC,否则会有极大风险。那么,具体地讲,测量系统的能力到底要达到多少才能使得SPC实现有效监控工艺的过程呢?
我们知道,过程能力指数(Cpx)可用下式计算:

式中,USL、LSL分别为规格上限和下限;x=Obs或Act,参见式(2.2.1)。
关于测量系统的变差,我们通常研究重复和再现能力,用GRR表示。GRR的计算有两种方式,一种是基于过程变差,另一种是基于规格公差,基于过程变差如下式:

式中,k一般取6。
基于规格公差如下式:

如果乘上100%就是GRR%了:

理论上,,因此GRR≤1或GRR%≤100%。
基于过程变差,观测的总变异与零件实际变异之间的关系由下式确定:

代入式(2.2.1)得:

令式(2.2.4)中k=6,将式(2.2.4)代入上式可得:

得:

基于规格公差,根据式(2.2.2)和式(2.2.4)可得:

通过变换上式并联合式(2.2.6)可得:

至此,我们分别获得基于过程变差和规格公差的关系式(2.2.7)和式(2.2.8)。根据式(2.2.7)和式(2.2.8),我们考虑实际应用,令:短期的过程能力CpObs短期=1.67(近似于5σ水平);长期的过程能力CpObs长期=1.33(近似于4σ水平)。
我们对测量系统GRR的要求通常有两个节点,一个是10%,一个30%(参见本书第8章)。超过30%的测量系统变异太大,不适用于过程能力的研究,我们就不考虑GRR%>30%的情况,为了方便对比,我们就考察0%、10%和30%这三个点。
1)令:GRR=0或GRR%=0%,代入式(2.2.7)和式(2.2.8)可得出工艺过程的实际能力CpAct=CpObs,见表2.2.1。
表2.2.1 GRR=0的情况

2)令:GRR=0.1或GRR%=10%,代入式(2.2.7)和式(2.2.8)可得出工艺过程的实际能力CpAct,见表2.2.2。
表2.2.2 GRR=0.1的情况

3)令:GRR=0.3或GRR%=30%,代入式(2.2.7)和式(2.2.8)可得工艺过程的实际能力CpAct,见表2.2.3。
表2.2.3 GRR=0.3的情况

从上述结果来看,在GRR%=30%的情况下,观测的过程能力CpObs与实际过程能力CpAct有一定差异,且CpObs<CpAct,这意味着我们低估了工艺的过程能力;当GRR%=10%的情况下,观测的过程能力CpObs与实际过程能力CpAct差异非常小,即CpObs≈CpAct,这就意味着我们可以很准确地评估工艺的过程能力;当GRR%=0%时,CpObs=CpAct。
因此,通过对比GRR%分别等于0%、10%和30%这三个点的情况,我们就会发现,测量系统的变异越小越好,当然实际情况是GRR%不可能为零;而当GRR%≤10%时,测量系统的变异对过程能力的研究影响非常小。
我们可以尝试计算一下当GRR%>30%,比如50%或80%的时候是什么情况,GRR=0.5或GRR%=50%时的情况和GRR=0.8或GRR%=80%的情况分别见表2.2.4和表2.2.5。
表2.2.4 GRR=0.5的情况

表2.2.5 GRR=0.8的情况

显而易见,GRR=0.5时的测量系统已经非常不适合做过程能力的研究了;当GRR%=80%时,基于规格公差我们无法用式(2.2.8)算得,但从基于过程变差的研究我们更加有理由确定,这种测量系统的变异太大,完全无法适用于过程能力的研究了。
当我们要用SPC对过程进行监控时,我们应保证测量系统的变异GRR%≤10%,当然考虑到投入产出比,并非所有的测量系统都能达到这种要求。因此,有些企业干脆就根据不同的工艺要求对工序进行分类,例如将工序分类为关键特性、安全特性、非关键特性工序等,然后根据不同的工序要求对GRR%指标定义也不一样。比如,有些企业就把非关键特性的GRR%范围定义为GRR%∈(10%,30%],这种分类法实际上是可取的,这也正是MSA手册的指导精神。
2.2.3 测量系统分析在研发领域的重要作用
我们知道,制造业尤其是现代制造业通常是批量性制造产品,由于要满足产能和交期的要求,通常情况下,会对工序或生产线进行复制,换句话说就是在同一道工序中,会有多套一样的测量系统,这样的情况便于做MSA的研究。
而研发领域则不同于制造业,研发领域的测量系统很多时候是一个孤立的样本,要比较的话,只能是研发实验室与其他研发实验室之间进行比对,或者客户与供方之间进行比较。研发领域尤其是涉及材料研发、破坏性和可靠性研究等方面,通常试验过程是不可重复的,这就无法用MSA常规的分析手段对测量系统进行分析,必须用到MSA手册提到的“复杂测量系统”的评估和分析方法或“其他替代的方法”。
当然,无论是哪一种情况,我们对研发过程用到的测量系统进行评估可以采用很多种手段,诸如实验室间的计量比对、测量结果的不确定度的评定、MSA、失效模式的分析、因果分析等。其中,MSA更注重于系统思维,对测量系统本身的特性(如重复的能力、再现的能力、准确的程度、稳定的能力等)更加关注,且有一套与管理相结合的改进指导策略。这种策略往往是具有工程思维的,这就非常便于组织内部的交流和沟通,更能调动组织内部的资源而用于测量系统的改进目的。
调查发现,研发领域的测量过程有如下方面的典型特点:
1)样品数量少。例如轨道高速撞击试验用的汽车样品。
2)样品单价成本高。例如金属材料Pt、Au、Ag以及汽车样品。
3)取样频次低。例如每三个月来一次样或半年来一次样。
4)样品的均匀性不好。例如粉末材料比表面积的测定。
5)样品的性能会随时间的推移而发生变化。例如悬浮溶液的旋转黏度的测定。
6)不能重复测量。例如材料的热稳定性分析。
7)部分样品有复杂的前处理。例如ICP重金属含量检测。
8)操作人员是唯一的。大部分专业性测量仪器的操作都是指定单一的技术人员。
9)测量仪器是唯一的。这是研发实验室常见的情况。
10)测量仪器的准确度是行业最高的。例如SEM扫描电镜、特种等级电子天平等。
11)测量仪器的稳定性较高。例如激光粒度分析仪。
12)测量过程耗时长。例如K-F微量水分测定仪。
13)实验室环境控制比较稳定。包括实验室环境的温、湿度控制。
上述的特点代表了研发实验室测量系统的大部分情况。其中大部分看似不适用MSA,实际不然,AIAG(美国汽车工业行动集团)在2002年发布的第三版就已经有了大篇幅的改进和更新,其中就包括对复杂测量系统的分析方法的指导建议。另外,在手册中也提到对复杂测量系统应尽可能应用专业知识、统计手段等对其进行变差研究。
本书在第10章会专门针对不可重复的测量系统分析如何应对进行论述,其他章节也会针对上述状况进行探讨。当然,借用MSA手册的话说,我们编写本指南的目的并不意味着能够涵盖所有类型的测量系统,指南的最终目的还是提供一种MSA的应用性思维去解决实际测量工作中遇到的问题。
而在研发领域,如果用不确定度评定、实验室比对、失效模式分析、因果分析、根本原因分析等手段无法达到探讨测量系统变异的目的,那么不妨从系统性的思维,应用MSA的思想去做测量系统的变异研究。
2.2.4 测量系统分析在六西格玛管理中的地位
在质量管理中,我们会用到大大小小的质量工具,小而单一的工具如7M1E、5W3H、8D报告、QC七大手法、PDCA循环[4]等;大而系统的工具如六西格玛管理、IATF16949五大工具[5]、精益生产等。而其中六西格玛管理已得到广泛的推广与好评,六西格玛的方法论中无论是质量改进模式的DMAIC,还是设计流程的DMADV[6],其中的“M”就是指测量阶段。六西格玛作为一套科学的、严谨的质量管理工具,其方法论中均给“测量”留了一席之地。质量管理大师戴明(W. Edwards Deming)说过:“如果我们不进行测量,我们将不能知道更多。”不得不说,我们在对待“测量”的问题上,已不再是讨论测量重不重要了,而是应该讨论如何做好测量。
我们以DMAIC为例来探讨MSA如何扮演着它的角色。
表2.2.6是DMAIC五个阶段的主要工作内容。
表2.2.6 DMAIC五个阶段的主要工作内容

从表2.2.6中不难发现,当六西格玛项目的范围和收益被界定清楚后,后期所有的改进工作都绕不开“Measure(测量)”。可以说,在测量阶段获得的Y和X是决定整个六西格玛项目改进成败的关键所在,因此在做Y与X的测量之前,我们首先需要对测量系统的可靠性进行检验,所用的手段就是MSA了。
现实状况是很多六西格玛工程人员总会忽略MSA而直接开展Y和X的测量,这样一来,我们测量出的Y和X有出现偏差的风险,即我们的改进方向可能会发生偏离,后期的控制阶段再投入多少资源可能都达不到预期的项目收益。
正确的做法是,在进行任何测量之前,先问一个问题:测量系统可靠吗?在核实测量系统的可靠性之前,请不要进行任何的测量工作,这是非常值得强调的一件事情。包括后期的过程控制对SPC的应用,我们也要先问一下:测量系统可靠吗?关于SPC与MSA之间的关联性,本书在第2.2.2小节中已有详细的说明,这里就不赘述了。