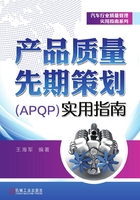
1.1 APQP的背景与历史
1.1.1 APQP与IATF 16949
APQP是IATF 16949的一部分,支持IATF 16949标准的要求。IATF 16949∶2016第8.3章节“产品和服务的设计和开发”规定:组织应建立、实施和保持设计和开发过程,以确保后续的产品和服务的提供。第8.3.2.1“设计和开发策划”中的补充条款,要求使用项目管理工具APQP或VDA-RGA。APQP与IATF 16949的关系如图1-1所示。

图1-1 APQP与IATF 16949的关系
IATF 16949是衡量汽车制造行业企业质量管理水平的标准,其标准名称是《汽车质量管理体系标准—汽车生产件及相关服务件组织的质量管理体系要求》,它是一套能满足各大汽车整车厂要求、国际通用的汽车行业质量体系标准,适用于全球汽车制造业。
2002年4月24日,福特、通用和克莱斯勒三大汽车制造商在美国密歇根州底特律市召开了新闻发布会,宣布对供应厂商要采取统一的质量体系规范,这个规范就是ISO/TS 16949。ISO/TS 16949是国际标准化组织(ISO)公布的一项汽车行业性的质量体系要求,是以ISO 9001为基础的国际汽车行业的技术规范。它由国际汽车工作组(International Automotive Task Force,IATF)通过对三个欧洲规范VDA(德国)、AVSQ(意大利)、EAQF(法国)和QS-9000(北美)进行协调,在与ISO 9001标准结合的基础上,在ISO/TC 176的认可下制定的。IATF 16949标准由TSO/TS 16949迁移而来,并替代原有的ISO/TS 16949技术规范。
2016年10月,IATF正式发布汽车行业新版质量管理标准IATF 16949∶2016。
IATF 16949连同适用的汽车顾客特定要求、ISO 9001∶2015要求以及ISO 9000∶2015一起定义了对汽车生产件及相关服务件组织的基本质量管理体系要求。IATF 16949∶2016不能被视为独立的管理体系标准,必须当作ISO 9001∶2015的补充,并与ISO 9001∶2015结合使用。
IATF 16949标准适用于整个汽车制造业生产零部件与服务件的供应链,包括汽车制造厂。国内大多数汽车制造厂商强制要求其各级供应商通过IATF 16949的认证,可见汽车零部件制造企业通过IATF 16949认证,已成为进入汽车制造业市场的一张入场券。汽车零部件制造企业如没有得到IATF 16949的认证,也将意味着失去作为汽车整车厂供应商的资格。
1.1.2 质量源于设计的理念
20世纪70年代,丰田汽车为提高汽车质量提出了质量源于设计(Quality by Design,QbD)的相关理念,使控制质量理论从检验决定质量和生产决定质量逐步向设计决定质量的理论发展。对产品质量问题的根本原因进行分析,发现54%的质量问题源自研发阶段;若在开发阶段发现问题进行设计更改,比在量产后更改所发生的费用要低得多。质量是指一组固有特性满足要求的程度,在设计开发阶段把这些特性进行分解转化,形成预期目标值,实现生产出低成本且性能稳定可靠的产品。
设计包括产品设计与过程设计,产品设计就是按预期要求对产出物(产品)进行设计,而过程设计就是对产品实现的过程和工艺进行设计。设计质量包括两层含义:一是设计目标的质量,即产品和过程与期望要求的符合程度;二是设计的工作质量,即为满足设计目标所进行工作活动的符合程度。
APQP为汽车零部件产品和过程的设计与开发定义了结构化的方法与步骤,是质量源于设计理念的体现。
1.1.3 APQP与项目管理
从多家媒体得知,汽车整车平均有3万个零部件,这些零部件大部分由汽车零部件供应商提供。当供应商在开发汽车零部件时,要确保每种零部件产品研发的进度,使每项工作都能顺利有序地进行,在各阶段各种资源能够得到合理有效的配置,质量能够达到预期目标。实现项目成功三要素,即时间、成本和质量的平衡,汽车零部件产品的开发需要科学的方法,以项目管理方法进行管理。
美国项目管理协会(PMI)将项目定义为:项目就是为提供某种独特产品或服务所做的一次性的努力。项目管理是为了满足或超过项目有关各方对项目的需要和期望,运用有关知识、技能、方法与工具,所开展的项目起始、计划、组织、控制和结束的管理活动。
项目不同于日常运营,项目与日常运营及管理的主要区别如下:
(1)项目与日常运营的主要区别 项目是在相对开放和不确定的环境下开展的独特性、一次性活动。日常运营是在相对封闭和确定的环境下开展的重复性、周而复始的和持续性的活动。
(2)项目管理与日常运营管理的主要区别 项目管理的对象是一个或多个项目,是面向任务和过程的,项目生命周期相对是比较短暂的。日常运营管理的对象是企业生产和运营的决策、实施与控制,是面向部门和程序化工作的,而且日常运营的周期是相对长远的。
APQP是项目管理在汽车领域中的具体应用。APQP是AIAG提供给供应商在研发新产品时的一种结构化的方法,用来确定和制订确保某产品使顾客满意所需的步骤。其目标是促进所涉及的人员之间的沟通,以确保所有要求的步骤按时完成。它针对具体产品,包括从产品概念的确定、产品设计、过程开发、试生产到生产,以及全过程中的信息反馈、纠正和持续改进活动。
1.1.4 AIAG的五大工具
产品质量先期策划(Advanced Product Quality Planning,APQP)程序是IATF 16949的一部分,是设计和开发策划非常有效的工具,属于AIAG的五大工具(APQP、PPAP、FMEA、SPC、MSA)之一。汽车零部件新产品项目的开发,若顾客没有要求,一般按APQP进行,期间会应用到FMEA、SPC、MSA工具,最后整理PPAP文档,供内外部项目相关方评审,并提交顾客批准。APQP与PPAP、FMEA、SPC、MSA的关系如图1-2所示。
1)APQP是产品和过程设计与开发的一种结构化方法,用来确定和制订确保某产品使顾客满意所需的步骤,它针对具体产品或项目,包括从产品概念的确定、产品设计、过程开发、试生产到生产,以及全过程中的信息反馈、纠正和持续改进活动。APQP分为五个阶段(过程),分别是计划与确定项目,产品设计与开发,过程设计与开发,产品与过程的确认、反馈、评定和纠正措施。

图1-2 五大工具的关系
2)统计过程控制(Statistical Process Control,SPC)是一种制造过程控制方法,利用统计的方法来监控制造过程的状态,确定生产过程在管制的状态下,以降低产品品质变异。将制造中的控制项目依其特性收集数据,使用控制图等统计技术来分析制造过程能力,找出这些特性变差的大小和原因,以便采取适当的措施,从而提高或改进制造过程能力。
3)测量系统分析(Measurement System Analysis,MSA)指通过数理统计和图表的方法对测量系统的分辨率和误差进行分析,以评价整个测量系统的测量能力是否满足被测量的特性值。测量系统是用来对被测特性定量测量或定性评价的设备或量具、标准、操作、程序、方法、检具、软件、人员、环境和假设的集合,用来获得测量结果的整个过程。测量系统分析可分为计量型和计数型两类。计量型测量系统分析通常包括稳定性、偏倚、线性、重复性、再现性(即五性)的分析、评价,计数型测量系统分析一般从一致性比率和Kappa值方面进行分析。
4)潜在失效模式和效果分析(Failure Mode and Effects Analysis,FMEA)是一个以预防为主的“事前的行为”,而不是“事后的行为”。它是在产品和过程的设计前,对产品及产品的子系统、零部件以及制造过程的每个工序进行分析,找出所有潜在的失效模式,并分析可能出现的后果和影响,从而预先采取必要的预防措施,避免或减少这些潜在失效的发生,以提高产品的质量和可靠性的一种系统化归纳分析方法。FMEA通常分为三类:系统失效模式及后果分析(SFMEA)、设计失效模式及后果分析(DFMEA)和过程失效模式及后果分析(PFMEA)。
5)生产件批准程序(Production Part Approval Process,PPAP)是指将使用正式生产设备、工装模具、原材料、生产工艺、操作者和量具由操作者在生产现场生产制造出来的零部件和相关的文件、记录提交顾客,并由顾客进行评审和批准的过程。向顾客提交的PPAP文件视为供应商对顾客的质量保证,等同于质量保证协议的效力。
PPAP用来确定供应商是否已经正确理解并满足顾客工程设计记录和规范的所有要求。检验供应商是否具有量产供货能力,满足顾客质和量的要求,能够持续稳定地按规定的生产节拍为顾客提供合格产品。
在进行APQP时,第二阶段要进行DFMEA,第三阶段要进行PFMEA,第四阶段要使用SPC、MSA,并进行PPAP。如果把APQP看作是一个过程,PPAP则可看作是一个结果,FMEA、SPC、MSA是质量管理的工具。APQP各阶段与FMEA、SPC、MSA、PPAP的关系如图1-3所示。

图1-3 APQP各阶段与FMEA、SPC、MSA、PPAP的关系
1.1.5 APQP版本
至目前为止,APQP发布了两版,第一版于1994年6月发布,第二版于2008年7月发布。第二版于2008年11月1日生效,除顾客特别说明外,APQP第二版生效后取代第一版。
第二版与第一版的主要变化如下:
1)强调以顾客为中心的过程方法。
2)对术语进行了更新,将APQP的术语与16949和克莱斯勒、福特和通用汽车的其他核心工具的术语相统一。
3)强调对顾客的特殊要求进行适当参考。
4)强调管理者的支持。
5)细化了APQP的输入和输出。
6)强化了检查表的应用,以更有效地确认APQP进度的准确完成。
7)强调经验的积累与知识的储备和运用。