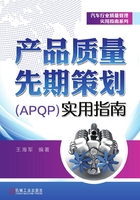
1.5 APQP的五个阶段
汽车零部件开发项目依据APQP方法分为五个阶段或过程(图1-11),即
第一阶段:计划和确定项目
第二阶段:产品设计和开发
第三阶段:过程设计和开发
第四阶段:产品和过程确认
第五阶段:反馈、评定和纠正措施
五个阶段的前一个阶段的输出是后一个阶段的输入;各个阶段在时间上重叠,体现同步工程。“反馈、评定和纠正措施”贯穿整个项目的始终,在APQP的任何阶段发生的需要解决的问题,根据反馈予以纠正解决,并积极不断地持续改进,以增进顾客满意度;并从中吸取教训、积累知识,应用到下一个项目。
1.5.1 计划和确定项目
APQP第一阶段是计划和确定项目,是项目的初始阶段。这一阶段要对顾客的期望和要求进行识别,进行初步的产品质量策划,确保对顾客的需求和期望有一个明确的了解。对于适用于项目的法律法规、产品实现过程的特殊条件、以往的经验和教训、其他项目相关者的要求都应作为项目的输入进行考虑。第一阶段最终要对项目是否可行做出决策,确定项目范围。APQP这一阶段的输入与输出如图1-12所示。

图1-12 APQP计划和确定项目的输入与输出
1.5.2 产品设计和开发
在确定项目之后,将进行产品、过程的设计和开发。产品的设计和开发将第一阶段计划和确定项目的输出作为输入,输出分为两大类,产品设计输出和产品质量策划小组的输出,图1-13所示为APQP这一阶段的输入与输出。

图1-13 APQP产品设计和开发的输入与输出
产品设计和开发要完成产品特征和特性的设计,并完成样件的制作与验证。即使产品设计由顾客或部分由顾客进行,项目小组也要充分考虑所有设计要素。一个可行的设计必须满足产量、工期和工程要求,满足质量、可靠性、投资成本、重量、单件成本和时间目标。尽管可行性研究和控制计划主要是基于工程图样和规范的要求,但是从本阶段的分析工具,如DFMEA等,也能获取到有价值的信息,以进一步确定和优先考虑产品的特殊特性和过程控制的特性。
产品设计和开发要保证对技术要求和其他有关技术资料进行全面、严格的评审;进行初始可行性分析,以评价产品在制造过程中可能发生的潜在问题。
1.5.3 过程设计和开发
过程设计与开发是为保证开发一个有效的制造系统,建立与其有关的控制计划,从而持续稳定地制造出优质产品,这个制造系统必须保证满足顾客的要求、需要和期望。
过程设计与开发对产品实现过程进行规划与设计,包括4M1E(人、机、料、法、环)的规划、过程风险的分析和应对、测量系统和过程能力分析计划等。
过程设计与开发可以最早在确立项目后与产品设计和开发同步进行,但必须在产品设计和开发完成后结束,这一阶段的任务完成依赖于成功地完成了前两个阶段。APQP过程设计与开发的输入与输出如图1-14所示。

图1-14 APQP过程设计与开发的输入与输出
1.5.4 产品和过程确认
产品与过程确认是通过一定数量的小批量试生产,评价和确认产品的符合性和制造过程的有效性。通过试生产运行,确认产品是否满足顾客的要求,确认生产过程是否遵循控制计划和过程流程图,确认产品设计和加工过程有关的问题是否得到解决。
试生产必须在正式工装模具、生产设备、测量系统、人员、环境、生产节拍等要素条件下进行,生产数量一般按顾客计划要求规定,可以超过但不能少于这个数量,一般规定为1~8h的连续生产至少300件样品。这一阶段要完成MSA、PPK(初始过程能力研究)、包装评价和PPAP等工作。这一阶段的APQP输入与输出如图1-15所示。

图1-15 APQP产品和过程确认的输入与输出
1.5.5 反馈、评定和纠正措施
反馈、评定和纠正措施致力于减少变差并持续改进。APQP第四个阶段结束,项目即可移交生产,但质量策划不因产品和过程的确认、产品量产而终止。在量产阶段,生产控制计划是评价产品和服务的基础和依据,必须对计量型和计数型的数据进行评价,采取克莱斯勒、福特和通用汽车公司的基础SPC手册中控制图或其他统计技术,识别过程变差,当出现特殊原因和普通原因变差时,可评价输出,分析原因并采取措施,以减少变差。
这一阶段组织应对质量策划工作进行有效性评价,输出必须满足顾客的所有要求,积极不断地改善产品缺陷,改进交付和服务,以提高顾客满意度。
反馈、评定和纠正措施贯穿APQP的全过程,在APQP的任何阶段发生需要解决的问题,可根据此阶段的方法,根据反馈予以纠正解决,并从中吸取教训、积累知识,应用到下一个项目。APQP反馈、评定和纠正措施的输入与输出如图1-16所示。

图1-16 APQP反馈、评定和纠正措施的输入与输出