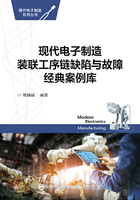
No.052 某OEM代工背板加电试验中被烧损
1.现象描述及分析
(1) 现象描述
由某外协公司手工代工焊接的背板产品,在上机架调试中,机柜发出很浓的焦味,随即对该机架断电检查,发现机架上某背板被严重烧毁。某背板的局部烧毁区域外观如图No.052-1所示。
(2) 现象分析
① 从烧损的外观特性看,表面及内层的铜导线均未变色 (短路电流将使铜颜色变暗),也未出现熔化的金属瘤。显然,造成烧损的大电流不是来源于铜导线的短路电流,因而可以排除内部铜导线短路的因素。

图No.052-1 某背板的局部烧毁区域外观
② 从烧毁区域的外观形貌看,可以判断烧损是从基板表面开始的,然后再往内层渗透及至烧穿,烧毁区域呈盆形,表面面积最大,随向底面的深度的增加而递减。由于基板材料基本上是不导热的,若事故是由内层铜导线短路所形成的大电流引起的,热量基本上均应集中在短路导线周围的有限空间内,在该区域中首先被烧损掉的是基材中的环氧树脂,环氧树脂分解后便会只留下分层的玻璃纤维布。
③ 从事故中机架电源的保护开关未跳闸,汇流条-48 V电源线完好的情况看,也可以排除出现过短路的情况。
④ 从两件缺陷样品看,烧损均发生在X134插座处,如图No.052-2所示。
⑤ 背板是通过X134电源插座为子板供电的。从第二块样品烧毁情况来看,最初的烧毁是发生在-48 V和48 V GND引脚间,如图No.052-3所示。

图No.052-2 烧损均发生在X134插座处

图No.052-3 最初烧毁是发生在-48 V和48 V GND引脚间
⑥ 在拆卸X134、X135后,发现一些器件的底面上有黄色黏稠物,经过烙铁加热后,该黏稠物散开。经过与外协厂沟通确认,此黄色黏稠物为个别员工使用了禁用的助焊剂膏,焊后又未对焊接过的背板进行仔细的清洗。
⑦ 现场查看证明,造成烧损事故的根源就在于手工焊接过程中使用了一种由日本大洋电机产业株式会社生产的BS-10焊接用助焊剂膏。在该产品的使用说明中明文规定:在印制电路板上不能使用。
(3) 复现故障现象
① 测试环境:常温。
② 测试工具与方法:
● 采用2块某背板产品,模拟外协厂加工手法,焊接电源插座,涂上助焊剂膏;
● 模拟使用现场,对这2块板加电 (DC 48 V)。
③ 复现试验结果。
给这2块背板加电 (DC 48 V) 不到一分钟,背板开始燃烧,有较大的明火,与以前在机架上测试时发生的现象极为相似,故障现象的复现如图No.052-4所示。

图No.052-4 故障现象的复现
2.形成原因及机理
(1) 形成原因
外协厂使用了禁用的BS-10焊接用助焊剂膏是导致本次某背板烧损的主要原因。
(2) 形成机理
本故障形成的机理是:表面存在的某种离子污染物产生的漏电流造成短路故障。
BS-10焊接用助焊剂膏属于一种弱酸性手工焊接用助焊剂膏,这种助焊剂膏大多使用凡士林和弱酸调配而成。由于此助焊剂膏的酸性以及凡士林的吸湿性,焊接后在PCB表面及引脚周围残留下来的离子 (极性) 残留物过多,这些极性污染物在一定的环境中,譬如阴雨天气,在PCB上会产生轻微的凝露现象,极性污染物与水等液体形成导电溶液,在电场的作用下,使两个引脚 (-48 V和48 V GND) 之间出现短路现象。这种因电化过程产生的漏电流,其峰值虽然不如铜导体短路电流峰值大,然而由于其作用于绝缘体表面的电化过程时间长,热量积累多,对电气产品照样能形成极大的危害。
3.解决措施
① 严格遵守工艺纪律,按工艺规范要求操作,未经主管工艺师许可,任何人不得私自滥用禁用材料。
② 手工烙铁焊接的焊点,焊后的各种残留物均必须仔细清除。