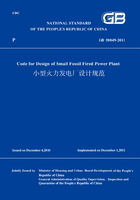
9.2 Coal Pulverizing System
9.2.1 The type of coal mills shall be selected based on the coal quality characteristics,possible variation of coal type,load nature and applicable conditions of mills through techno-economic comparison and in accordance with the following requirements.
1 When the power plant operates on anthracite,low volatile lean coal and highly abrasive coal,or the coal quality and type are hard to keep unchanged,ball tube mills should be used.Double-inlet-and-doubleoutlet tube mills may be used instead if justified through techno-economic comparison.
2 When the power plant operates on lignite with less abrasiveness,high moisture content,less ash content and high volatile mater,beater-wheel mills should be used.
3 Medium-speed mills should be given priority if the coal quality is satisfactory.
9.2.2 The type selection of coal pulverizing system shall comply with the following requirements:
1 If typical ball tube mills are employed,a bin storage pulverizing system shall be provided.If double inlet and outlet tube mills are employed,a direct-fired pulverizing system shall be provided instead.
2 When high-speed and medium-speed mills are employed,a direct-fired pulverizing system shall be provided.When medium-speed mills are employed,the coal handling system shall be provided with complete facilities for removing iron,wood,stone,coal blocks as well as mill rejects.
3 When medium-speed mills and double-inlet-and-double-outlet tube mills are employed,positive pressure cold primary air direct-fired pulverizing system should be used.
4 The direct-fired pulverizing system should be used for flammable and explosive coal types.
9.2.3 The number and output of mills shall comply with the following requirements:
1 The number and output of the ball tube mills for bin storage pulverizing system shall comply with the following requirements:
1)For boilers rated 220t/h-410t/h,each boiler shall be provided with two mills and no standby mill shall be equipped.For boilers rated 130 t/h and below,each boiler should be provided with one mill.
2)The total calculated output of mills provided for each boiler(at maximum ball loading amount)shall not be less than 115% of the coal consumption of the boiler when burning design coal at BRL,and shall not be less than the coal consumption of the boiler when burning check coal at BRL.
3)In cases where two or more mills are provided for each boiler,if one of them is shut down,the calculated output of the rest mills when burning design coal shall meet the requirement of the boiler minimum stable load without oil supporting.When necessary,the boiler may be fed with pulverized coal delivered from adjacent boilers through conveyors.
2 The number and output of the mills for direct-fired pulverizing system shall comply with the following requirements:
1)If double-inlet-and-double-outlet tube mills are used,no standby mill shall be provided.For boilers rated 220t/h-410t/h,each boiler shall be provided with two mills.For boilers rated 130t/h and below,each boiler should be provided one mill.The total calculated output of mills provided for each boiler(at the ball loading amount recommended by the manufacturer)shall not be less than 115% of the coal consumption of the boiler when burning design coal at BRL,and shall not be less than the coal consumption of the boiler when burning check coal at BRL.
2)If a direct-fired pulverizing system equipped with high-speed and medium-speed mills is used,standby mills shall be provided.For boilers rated 220t/h-410t/h,each boiler should be provided with three mills,one for standby.For boilers rated 130t/h and below,each boiler should be provided two mills,one for standby.The total calculated output of the mills shall include the output of standby mills.When design coal is burned,the total calculated output of mills(excluding standby ones)for each boiler shall not be less than 110% of the coal consumption of the boiler at BRL.When check coal is burned,the total calculated output of the mills(including standby ones)before maintenance for each boiler shall not be less than the coal consumption of the boiler at BRL.
9.2.4 The type,number and output of coal feeders for pulverized coal fired boilers shall comply with the following requirements:
1 Coal feeders shall be selected based on the arrangement of pulverizing system equipment,load requirements of boiler,regulation performance of coal feeder,operation reliability in conjunction with the measuring requirements.Coal feeders of positive pressure direct-fired pulverizing system must have satisfactory tightness and pressure withstand capacity.The coal feeders of a bin storage pulverizing system shall have satisfactory tightness to prevent air leakage.
2 The type of coal feeders shall match with that of coal mills and shall be selected in accordance with the following requirements:
1)For the bin storage pulverizing system in which ball tube mills are used,scraper,belt,or vibration type coal feeders may be used.
2)For the direct-fired pulverizing system,belt or scraper weighing type coal feeders equipped with metering devices which have satisfactory tightness and regulation performance shall be used.
3 The number of coal feeders shall match with that of mills.For the units equipped with double-inletand-double-outlet tube mills,one mill shall be provided with two coal feeders.
4 The calculated output of scraper or belt type coal feeders shall not be less than 110% of that of mills.The calculated output of vibration type coal feeders shall not be less than 120% of that of mills.For coal feeders equipped with double-inlet-and-double-outlet tube mills,the calculated output of a single feeder shall not be less than the maximum coal feeding demand when mills are operating at single side.
9.2.5 For CFB boilers,at least two coal feeders shall feed coal symmetrically.When one of the coal feeders fails,the total output of the rest feeders shall accommodate the coal consumption of the boiler at BRL.
9.2.6 The number and maximum output of pulverized coal feeders shall comply with the following requirements:
1 The number of pulverized coal feeders should be the same as that of the primary air connections for the boiler burners.If the boiler is provided with a pre-combustion chamber,additional coal feeders shall be provided for this chamber.
2 The maximum output of each pulverized coal feeder shall not be less than 130% of the maximum design output of the burners connected.
9.2.7 If a bin storage pulverizing system is used,the pulverized coal conveying equipment of screw,scraper or chain type or other types with reliable quality may be provided as required in accordance with the following requirements:
1 The pulverized coal bunkers of two boilers may be connected through a pulverized coal conveyor when conditions permit.
2 The capacity of the pulverized coal conveyor shall not be less than the calculated output of the largest coal mill connected.
3 When the length of the conveyor is 40m or below,single drive at either end of the conveyor should be used.When the length of conveyor is more than 40m,double drives from the both ends of the conveyor should be used.
4 The pulverized coal conveyors shall have satisfactory tightness.
5 For highly volatile bituminite and lignite,no pulverized coal conveyor should be provided.
9.2.8 The number,flow and pressure of pulverized coal exhaust fans shall comply with the following requirements:
1 The number of pulverized coal exhaust fans shall be the same as that of mills.
2 The base flow of pulverized coal exhaust fan shall be determined according to the thermal calculation of coal pulverizing system based on design coal type.
3 The pulverized coal exhaust fan shall have a flow margin of not less than 5% and a pressure margin of not less than 10%.The maximum flow of the fan shall be designed to provide the flow required by the mill with the maximum ball loading.
9.2.9 Medium-speed mills and double-inlet-and-double-outlet tube mills of positive pressure direct-fired pulverizing system shall be provided with sealing fans.The number,flow and pressure of sealing fans shall comply with the following requirements:
1 Each boiler shall be provided with at least two sealing fans,including one for standby.If sealing fans are provided for each mill,no standby sealing fan is required.
2 The flow margin of sealing fans shall not be less than 10%(the base flow calculated based on all the mills)and the pressure margin of sealing fans shall not be less than 20%.
9.2.10 The pulverizing system for coal other than anthracite shall be provided with anti-explosion and fire extinguishing facilities,which shall comply with the relevant provisions in current national standards GB 50229 Code for Design of Fire Protection for Fossil Fuel Power Plants and Substations and DL/T 5203 Technical Code for Explosion Prevention Design of Coal and Pulverized Coal Preparation System of Fossil Fuel Power Plant.
9.2.11 The types,number,flow,and pressure of the primary air fans of pulverized coal fired boilers should be determined in accordance with the following requirements:
1 If a trisector air preheater is used in conjunction with a positive pressure direct-fired pulverizing system,the cold primary air fans should be of centrifugal type.Other speed-regulating fans may be used if justified through techno-economic comparison.
2 The number of cold primary air fans should be two,and no standby fan shall be provided.
3 The flow and pressure of primary air fans should be determined based on the characteristics of air preheaters and type of pulverizing system.If a trisector air preheater is used in conjunction with a positive pressure direct-fired pulverizing system,the cold primary air fans should be selected in accordance with the following requirements:
1)The base flow of the cold primary air fans is calculated based on the design coal type,and shall include the primary air flow required by the boiler at BRL,the primary air leakage of the air preheaters after one-year operation as guaranteed by the manufacturer,and the sealing flow required to be supplied to mills by primary air fans(calculated based on the total number of mills).
2)The flow margin should be 20%-30% plus a temperature margin,which can be determined based on"outdoor air temperature used for ventilation calculation during summers".
3)The pressure margin should be 20%-30%.