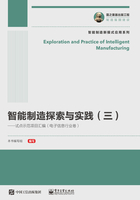
二、项目主要实施内容
该项目将综合应用自主可控智能装备,包括工业机器人、高速高精加工中心、AGV 小车、自动化生产线集中控制系统、视觉化品质检测设备、RFID 标签及读写器及系统、自动化夹具,打造便携式电子产品结构模组精密加工智能制造车间。
车间分为上下两层,由 179 台高速高精钻攻中心、10 台高光机、97 个六关节机器人组成 19 条机加生产线,每条生产线配备独立的工件清洗机和高精度激光在线检测机。其中一层 8 条、二层 11 条,还有一条由 5 台打磨机器人组成的自动打磨线。现场配备一座总容量为 3 600 个库位的数字化立体仓库,利用 7 台 AGV 小车为 19 条机加工生产线配送物料、回收工件。二层还配置有一座智能刀具库,通过车间物联网管理整个车间的刀具。如图4-1 所示为胜利精密智能工厂整体布局。
图 4-1 胜利精密智能工厂整体布局
工厂按纵向集成的技术需求,分为四个层次(见图 4-2)。最底层是由高档数控机床、机器人以及自动化物流设备构成的智能设备层,在智能设备层之上是由各类传感器、数据采集装置构成的用于多源异构数据采集的数据传感层,数据传感层之上,是由MES、CAPP、APS等构成的智能软件层,最后是由大数据中心、展示终端等构成的智能决策层。通过信息的功能、清晰的层次划分及各层次之间的有机整合,形成了拓扑结构合理、兼容性强、具有先进性的国产集成方案。
图 4-2 胜利精密智能工厂整体架构
本项目技术特点——“三国、六化、一核心”。
(1)“三国”。
本项目采用完全自主可控的国产智能装备、国产数控系统及国产工业软件。
①智能制造车间核心设备全部采用国产智能装备。
a. 高速钻攻中心/高光机:由加能精机提供,国产化率100%。主轴最高转速20 000/40 000rpm,定位精度0.01mm,重复定位精度0.006/0.003mm。
b. 高精度检测机:由项目单位富强科技与苏州凡目视觉联合自主研发的在线检测装备,借助激光线扫描相机,采用 2D/3D 视觉检测技术,在自动生产线上自动完成工件的量测,避免了人工操作,确保量测的精确性和可重复性,测量精度达到 3μm,实现快速高精在线测量。
c. 华数机器人(自主品牌):由苏州华数提供的六轴工业机器人,有效载荷 12/20kg,重复定位精度±0.08mm。
②国产智能装备全部采用国产数控系统。
a. 高速钻攻中心/高光机采用完全自主知识产权的华中 8 型全数字开放式高档数控系统。
b. 工业机器人采用具有自主知识产权的华数 II 型机器人控制系统。
③智能制造车间全部采用国产工业软件。
a. 三维机加工工艺规划系统(CAPP):由开目信息开发提供,快速生成工件的机加工工艺。
b. 产品全生命周期管理系统(PLM):由开目信息开发提供,支持海量数据处理。
c. 生产执行系统(MES):由艾普工华提供,包括制造数据管理、生产过程控制、底层数据集成分析、上层数据集成分解等管理模块,支持移动端展示。
d. 虚拟智能工厂(VIF)建模仿真软件:由创景可视提供,基于完全自主研发的虚拟仿真平台,为行业领先产品。
(2)“六化”。
本项目形成了高度柔性化自动生产线系统,在国产工业软件和云数控大数据平台的支持下,实现便携式电子产品结构模组在批量定制环境下的高质量、规模化、柔性化生产。
①加工过程自动化。
车间建立了由立体仓库、AGV 小车、标准料箱、通用托盘、倍速链传送带以及工业机器人组成的车间自动化物流系统,并部署了自动清洗机、检测机等自动化设备。物料从入库到出库之间的全部生产环节均可自动完成。
同时,生产线具有高度的柔性,通过 APS、MES、WMS 的实时监控和快速调度调整,可以进行单线生产、混线生产、串线生产等多种生产模式,适应不同种类工件的生产需求,发挥最大的生产效率。
②制造资源物联化。
项目应用 RFID 技术,通过与设备控制系统集成,以及外接传感器等方式,实现了机机互联、机物互联和人机互联,并由 SCADA 系统实时采集设备的状态、生产报工信息、质量信息等,从而将生产过程中涉及的全部制造资源信息进行高度集成,并且打通了所有系统的信息通道,实现了生产过程的全程可追溯。
③制造系统数字化。
基于制造资源的物联化,通过实时数据驱动的动态仿真机制,形成人、产品、物理空间和信息空间的深度融合,建立虚拟工厂与物理工厂相互映射、深度融合的“数字双胞胎”,实现实时感知、动态控制和信息服务。通过信息系统对物理工厂进行可视化监控,实时查看设备状态、质量信息、生产实况和生产实绩,同时进行分析与决策,对物理工厂进行智能控制。
④质量控制实时化。
工件在机床中加工完毕后由机器人送入在线检测机检测,检测完毕后机器人根据检测结果将不合格品放入不合格品料箱,合格品放入工件托盘,保证不合格品即时分拣;同时将检测数据上传至云平台,对同一机床加工的产品历史检测数据进行检索与对比,当对比结果符合设定的情形时,触发自动刀补流程,将信息传递给生产线控制器,再由生产线控制器计算刀补参数并下发给目标机床调整刀补,将刀具误差补偿回来,实现工件质量的实时全闭环控制。
⑤决策支持精准化。
本项目从生产排产指令的下达到完工信息的反馈,实现了全闭环控制。通过建立生产指挥系统,使管理者可以随时精确掌握工厂的计划、生产、物料、质量和设备状态等资源信息,了解和掌控生产现场的状况,提高各级管理者决策的准确性。
⑥制造环境绿色化。
胜利精密坚持可持续发展战略,在本项目中使用太阳能供电、CNC 油雾分离系统、切削液循环利用系统以及生产线集中排屑系统,实现能源的高效利用、减少污染排放,践行绿色制造理念。
(3)“一核心”:大数据云平台。
本项目以大数据云平台为数据集成核心(见图 4-3),与以往车间网络化的重大区别在于智能车间的工业软件不再是不可或缺的数据节点,而是“生长”在大数据中心之上的一个应用,提升了系统集成的便利性。
同时,对采集到的机床大数据进行分析、建模、比对,实现了一定程度上的智能化应用。例如对加工工艺进行评估和优化、实时监控机床健康状况、自动补偿机床热变形、实时监测刀具状况、自动规避主轴共振等。通过建立机床故障维修数据库,对机床出现的异常状况进行远程在线诊断,大大缩短机床维护及维修时间,降低运维难度。
图 4-3 胜利精密智能工厂云平台架构