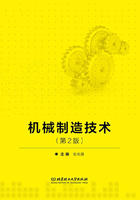
任务七 工序尺寸及其公差的确定
工序尺寸是加工过程中各工序应保证的加工尺寸,其公差即工序尺寸公差。正确地确定工序尺寸及其公差,是制定工艺规程的重要工作之一。
在确定了工序余量和工序所能达到的经济精度后,便可计算出工序尺寸及其公差。计算分两种情况,一种情况是基准重合,另外一种情况是基准不重合。
一、基准重合时工序尺寸及其公差的确定
零件上外圆和内孔的加工多属这种加工情况。当表面需经多次加工时,各工序的加工尺寸及公差取决于各工序的加工余量及所采用加工方法的经济精度,计算的顺序是由最后一道工序向前推算。例如加工某工件上的孔,其孔径为, Ra=0.8 μm(图1-58),需淬硬,加工步骤为粗镗—半精镗—精磨。工序尺寸及公差的确定步骤如下:

图1-58 内孔工序尺寸计算
(a)精磨;(b)半精镗;(c)粗镗;(d)毛坯
(1)确定各工序的加工余量。根据各工序的加工性质,查表得它们的加工余量(见表1-16中的第2列)。
表1-16 工序尺寸及公差的计算 mm

(2)根据查得的余量计算各工序尺寸。其顺序是从最后一道工序往前推算,图样上规定的尺寸,就是最后的磨孔工序尺寸(计算结果见表1-16中的第4列)。
(3)确定各工序的尺寸公差及表面粗糙度。最后磨孔工序的尺寸公差和表面粗糙度就是图样上所规定的孔径尺寸公差和表面粗糙度。各中间工序尺寸公差及表面粗糙度是根据其对应工序的加工性质,查阅有关经济精度的表格得到(查得结果见表1-16第3列)。
(4)确定各工序的上、下偏差。查得各工序尺寸公差之后,按“入体”方向确定各工序尺寸的上、下偏差。对于孔,基本尺寸值为公差带的下限,上偏差取正值(对于轴,基本尺寸为公差带的上限,下偏差取负值);对于毛坯尺寸的偏差应取双向值(孔与轴相同),得出的结果见表1-16第5列。
二、工艺尺寸链
零件的尺寸及技术要求一般是设计人员按其工作情况及配合要求而提出的。如图1-59(a)的箱体,为了保证传动齿轮有合适的中心距及齿侧间隙,以孔Ⅰ为孔Ⅱ的设计基准,标注尺寸A及B,为了保证孔Ⅰ与安装基面P与Q的正确位置,以P、Q为孔Ⅰ的设计基准,标注尺寸C与D。这种尺寸标注方法从设计角度来讲完全合理,但在进行机械加工时却有一定的困难。用面P、Q定位加工孔Ⅰ,保证尺寸C、D是很方便的,但难以用孔Ⅰ为定位基准来加工孔Ⅱ并保证尺寸A与B。

图1-59 基准不重合的尺寸换算
(a)零件图;(b)工序卡片图
实际加工中以面P、Q定位加工孔Ⅱ是可行且方便的,因调整机床只能保证刀具轴线到定位元件的距离,因此加工孔Ⅱ时,工序卡片只能按图1-59(b)的方法标注尺寸E及F。怎样计算尺寸E及F,使基准变换后所加工的零件仍能符合产品图样要求,这就是基准不重合时的尺寸换算。当基准不重合时,就必须应用尺寸链的原理进行分析计算。
1.工艺尺寸链的定义和特征
图1-59的尺寸A、C、E的关系可简单地用图1-60(图中A1、A2、A0分别表示原尺寸C、E、A)来表示,从图中可以看出:A1、A2、A0形成1个封闭的图形。这种由互助联系的尺寸按一定顺序首尾相接形成封闭的尺寸组就定义为尺寸链。由单个零件在工艺过程中的有关尺寸所形成的尺寸链,就称为工艺尺寸链。

图1-60 加工尺寸链示例
由图1-59分析可知,尺寸C、E(A1、A2)是在加工过程中直接获得的,尺寸A(A0)是间接保证的。由此可见,尺寸链的主要特征是:
(1)封闭性。尺寸链必须是一组有关尺寸首尾相接构成封闭形式的尺寸。其中,应包含1个间接保证的尺寸和若干个对此有影响的直接获得的尺寸。
(2)关联性。尺寸链中间接保证的尺寸大小和变化,是由这些直接获得的尺寸精度所支配;彼此间具有特定的关系,并且间接保证的尺寸精度必然低于直接获得的尺寸精度。
2.尺寸链的组成
组成尺寸链的各个尺寸称为尺寸链的环。图1-60中的尺寸A1、A2、A0都是尺寸链的环。这些环又可分为:
(1)封闭环。加工或测量过程中最后自然形成的一环称为封闭环,如图1-60中的A0。
(2)组成环。加工或测量过程中直接获得的环称为组成环。尺寸链中,除封闭环外的其他环都是组成环。按其对封闭环的影响又可分为:
①增环,当其余各组成环不变,而这个环增大使封闭环也增大者。例如,尺寸A2就是增环。为明确起见可加标1个箭头,如。
②减环,当其余各组成环不变,而这个环增大使封闭环反而减小者。例如,尺寸A1就是减环。为明确起见可加标1个箭头,如。
3.工艺尺寸链的建立
(1)首先根据工艺过程或加工方法,找出间接保证的尺寸,定作封闭环。
(2)从封闭环起,按照零件上表面间的联系,依次画出有关的直接获得的尺寸(大致按比例绘制),作出组成环,直到尺寸的终端回到封闭环的起端形成1个封闭的图形。必须注意,要使组成环环数达到最少。
(3)按照各尺寸首尾相接的原则,可顺着1个方向在各尺寸线终端画箭头。
工艺尺寸链的构成,取决于工艺方案和具体的加工方法;确定哪个尺寸是封闭环,是解尺寸链的决定性的一步,封闭环定错,必然全盘解错;1个尺寸链只能解1个封闭环。
4.尺寸链的基本计算式
工艺尺寸链的计算方法有两种:极值法和概率法。目前生产中多采用极值法,其基本计算公式如下:
(1)封闭环的基本尺寸A0。

式中 K——增环的环数;
m——组成环的环数。
即封闭环的基本尺寸等于所有增环的基本尺寸之和减去所有减环的基本尺寸之和。
(2)封闭环的最大极限尺寸A0max。

即封闭环的最大极限尺寸等于所有增环的最大极限尺寸之和减去所有减环的最小极限尺寸之和。
(3)封闭环的最小极限尺寸A0min。

即封闭环的最小极限尺寸等于所有增环的最小极限尺寸之和减去所有减环的最大极限尺寸之和。
(4)封闭环的上偏差ES(A0)。

即封闭环的上偏差等于所有增环的上偏差之和减去所有减环的下偏差之和。
(5)封闭环的下偏差EI(A0)。

即封闭环的下偏差等于所有增环的下偏差之和减去所有减环的上偏差之和。
(6)封闭环的公差T0。

即封闭环的公差等于所有组成环的公差之和。
(7)封闭环的中间偏差Δ0。

式中 ——增环与减环的中间偏差。
即封闭环的中间偏差等于所有增环的中间偏差之和减去所有减环的中间偏差之和。
(8)组成环的中间偏差。

即组成环的中间偏差等于组成环的上偏差和下偏差之和的一半。
(9)封闭环的平均尺寸A0av。

式中 →Aiav——增环的平均尺寸;
←Aiav——减环的平均尺寸。
即封闭环的平均尺寸等于所有增环的平均尺寸之和减去所有减环的平均尺寸之和。
(10)组成环的平均尺寸。

即组成环的平均尺寸等于组成环的最大极限尺寸和最小极限尺寸之和的一半。
封闭环的上、下偏差还可用中间偏差和公差来表示;封闭环的尺寸也可用平均尺寸和公差来表示,它们之间的关系如图1-61所示。

图1-61 各种尺寸与偏差及公差的关系
三、基准不重合时工序尺寸及其公差的确定
1.定位基准与设计基准不重合时的工艺尺寸换算
图1-62(a)中,工件在前工序中已加工出平面M、N,并已保证其厚度为。现欲以平面M定位加工平面P(调整法加工),问:须如何调整铣刀端面至夹具定位表面的位置,即保证工序尺寸x为多少,才能使零件加工后的设计尺寸
符合要求?

图1-62 定位基准与工序基准不重合时的工艺尺寸换算
(a)尺寸图;(b)尺寸链
经分析,该问题可列出尺寸链如图1-62(b)所示。在该尺寸链中,尺寸是本工序未加工前已经具有的,尺寸x是本工序加工时直接保证的,只有尺寸
是依赖于前两个尺寸而间接形成的。所以
为封闭环。尺寸
为组成环的增环、尺寸A1=x则是减环。
按式(1-1)计算基本尺寸:
25=60-x
得
A1=x=35 mm
按式(1-4)计算下偏差:

得
EI(A1)=-0.25 mm
按式(1-5)计算上偏差:

得
ES(A1)=-0.1 mm
所以本例欲求的工序及公差:

将其按入体原则标注,则

2.测量基准与工序基准不重合时的工艺尺寸换算
图1-63中,零件在车床上加工内孔。确定大孔孔底台肩面位置的是设计尺寸。但该尺寸不易测量,加工中改用测量尺寸x控制孔底台肩面位置。为使加工后尺寸
符合要求,问:尺寸x大小及公差应为多少?

图1-63 测量基准与工序基准不重合时工艺尺寸核算
(a)尺寸图;(b)尺寸链
据分析作出尺寸链如图1-63(b)。其中尺寸为间接获得的,是封闭环。
为增环,A2=x为减环。
由前述基本公式可求出:
A2的基本尺寸: A2=60-10=50(mm)
A2的公差: T2=0.4-0.2=0.2(mm)
A2的中间偏差:Δ(A2)=(-0.1)-(-0.2)=0.1(mm)
A2的极限偏差:


所以,欲求的新测量尺寸:
应指出的是,在利用换算后的新测量尺寸进行加工时,有时会出现假废品的情况,例如在该例中,如孔深加工为50.4 mm,则超过了求算的新测量尺寸x的公差范围,似乎应为废品。但如果加工直接获得的A1的实际尺寸为60.0 mm。这时A0为9.6 mm,仍符合设计尺寸要求,实际上仍为合格品。这说明,在用换算的新测量尺寸控制加工时,如该尺寸超差值不大于另一组成环公差时,就可能产生假废品。但是,按计算结果控制加工尺寸不超差,则得到的一定是合格品。
3.尚需继续加工的表面标注的工序尺寸计算
在确定某些加工表面的工序尺寸时,这些加工表面的工序基准是还需进一步加工的设计基准,两者之间相差1个加工余量,仍属于“基准不重合”问题。此时也要进行工序尺寸的计算。例如,图1-64(a)为变速器拨叉轴零件简图。外圆为, R槽底尺寸为
。外圆和R槽的加工顺序是:

图1-64 尚需继续加工的表面标注的工序尺寸计算
(a)零件简图;(b)尺寸链
(1)精车外圆至。
(2)铣R槽,工序尺寸为A。
(3)热处理。
(4)磨外圆至。
从以上加工顺序可以看出:最后磨削外圆时,直接保证的是外圆的设计尺寸而R槽底的尺寸
是磨削外圆后自动形成的。因此,必须正确确定精车后铣R槽的工序尺寸A。图1-62(b)为尺寸链简图,其中精车后外圆的半径为
,铣R槽的工序尺寸为A,磨削后的外圆半径为
,这些尺寸都是直接获得的,为组成环。R槽底的尺寸
是间接获得的,为封闭环。按工艺尺寸链原理,计算工序尺寸A。
(1)经分析,为增环,
为减环。
(2)计算基本尺寸:
因为
16.4=A+9.5-9.7
所以
A=16.4+9.7-9.5=16.6(mm)
(3)计算上、下偏差:
因为
0=ES(A)+0-(-0.042)
所以
ES(A)=-0.042 mm
因为
-0.12=EI(A)+(-0.007)-0
所以
EI(A)=-0.113 mm
(4)最终得到的铣R槽时的工序尺寸为

4.渗碳或电镀时工艺尺寸的计算
如现有一环状零件,要求内孔磨至后保证渗碳淬硬层厚度为
,渗碳淬火前内孔尺寸为
。问:渗碳淬硬层厚度尺寸控制为多少才能保证磨后的淬硬层厚度[要求如图1-65(a)所示]?

图1-65 渗碳淬硬层厚度的求解
(a)尺寸图;(b)尺寸链
根据分析作出尺寸链如图1-65(b)所示。其中磨后保留的淬硬层厚度为封闭环,各组成环尺寸及增减性如图1-65(b)所示。利用前述公式计算可得渗碳时应控制的渗碳淬硬层厚度尺寸
,即最小厚度应为0.62 mm,而最大厚度应为0.775 mm。