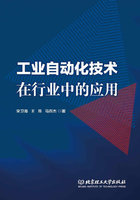
1.2 工业自动化系统的组成
工业自动化系统是一个或一组机器构成的单元。在每一个单元中有四种基本类型的装置,即生产装置、控制装置、反馈装置和辅助装置。
1.2.1 生产装置
生产装置是工业自动化系统中最基础的装置,是工业生产正常进行的基本保证。生产装置按照制造工序运行,如加工、装配、焊接、喷漆及其他增值工序,最后生产出一个完整的零件。生产装置包括机器人、计算机数控(Computer Numerical Control, CNC)设备、刚性自动化装置等。
1.机器人
机器人在一个工业自动化系统中有多种功能,包括移动并定位零件等重复性动作和完成组装零件等生产任务。机器人擅长做重复性强、需求精确而动作快速的工作。
驱动机器人的常用方式有三种类型,分别是气驱动型、电驱动型和液压驱动型。气驱动型机器人价格便宜、动作快速且精确,擅长简单的定位任务,如在装置间移动零件,但是能移动的位置有限,不擅长复杂的动作。电驱动型机器人动作快速、精确,可以完成定位、焊接等许多任务,但价格比较贵;液压驱动型机器人移动快速且平滑,擅长喷漆等重复性强且繁重的工作,在防爆场合应用广泛。
机器人使用专用的编程语言编程,并易于集成在自动化控制系统中。许多机器人只是一个简单的机械臂,能够从一个位置移动到另一个位置。机器人提供输入/输出(I/O)接口,这些接口可以十分容易地连接到可编程序逻辑控制器(Programmable Logic Controller, PLC)、单片机、计算机等控制装置上,方便实现对机器人的控制。
2.CNC设备
计算机技术的飞速发展使用计算机控制其运动和动作的CNC(计算机数字控制机床)设备得到了广泛的应用。工业生产中的CNC设备有数控车床、数字加工中心、电火花加工设备、线切割机,其中最常用的是数控车床和数字加工中心。CNC设备一般由控制器、驱动装置和机器本体三部分组成。
CNC设备摒弃原有的硬件控制方式,采用软件控制方式。新型的计算机控制是开放式PC(Programmable Controller)控制,控制功能强大而且十分灵活,能够轻松接入工业以太网中。工业生产中的编程人员编辑控制程序,并将其载入数控设备或通过以太网连接数控设备,设备的操作将完全按照预期目标来执行。
数控程序可以由编程人员手工编写,也可以通过机器自动生成。编程人员可借助CAPP,使用特殊的语言或通过数控设备屏幕输入方式描述程序的控制过程和道具轨道,计算机将上述语言编译成数控语言,载入数控设备的控制器中。
另外,编程人员可采用机器语言系统编写程序。数控系统的机器语言有G编码语言和M编码语言等。以G编码语言为例,G编码语言指令由简单代码和数字组成,其中代码表示机器执行操作的类型,数字表示机器需移动的距离。例如,G01 X20 F10这条指令中,G01表示直线插补指令,X10表示道具需要沿着X轴移动20mm的距离,F10表示加工刀具以10mm/min的速度进给。该方式要求编程人员具有扎实的编码机器语言的基础知识,熟悉所有代码的含义及编写要求。
CNC设备是一种精密控制设备,设备的控制器一般采用闭环控制方式,设备根据指令驱动伺服电动机,但同时需要检测刀具当前的移动速度和位置,以及时调整设备的运行状态,使其按照程序指令的要求工作。其中,根据检测反馈物理量的不同,闭环控制分为速度环路和位置环路,它们的作用是确保机器按照程序要求的速度和位移进行相应的控制。
随着计算机处理速度和其他性能的不断提高,CNC设备可以不间断地检测机器的运行速度和运行位置,一方面保证设备运行的速度和移动位置的准确性,另一方面也对设备起到了很好的保护作用。如果运行过程中,机器本该移动却没有移动,或移动距离超出最大可移动距离,则计算机可立即得到故障信息并采取相应措施,避免机器受到更大的损坏。伺服电动机的优点是在系统中使用了动力反馈机制,提高了主轴速度,以及速度和位移的精确性。
3.刚性自动化装置
刚性自动化装置通常是为一个特定的生产目标设计的,一般不适用于其他产品的生产过程,当该装置生产的产品不再生产时,就需要淘汰该装置,因此没有灵活性。但是,刚性自动化装置在很多生产过程中必须存在,可用作生产装置或辅助装置。
1.2.2 控制装置
工业自动化控制装置的控制方式经历了三个阶段,即机械控制、电动机械化控制和电气化控制。其中,电气化控制是指通过PLC、单片机和计算机等进行的工业自动化控制。一般来讲,根据控制方式的不同,工业自动化控制装置可以分为以下几类:电动机械控制装置、硬接线电气控制装置、可编程的硬接线电气控制装置、PLC控制和计算机控制装置。下面对工业自动化系统最常用的控制器PLC和分散控制系统DCS进行简单介绍。
1.控制器PLC
控制器PLC是工业自动化系统最常用的控制器,是一种专门用于控制工业生产过程的特殊计算机,其硬件特别适用于工业环境,且上位机编程软件简单易懂,便于电气技术人员的学习和使用。PLC执行存储器存放指令,完成相应的开/关控制、计数、定时、逻辑控制和数据处理等功能。
PLC是专门针对工业环境设计的数字运算操作的电子系统。PLC逐步从单台设备的控制到多台联合控制的方向发展。PLC具有控制灵活、可靠性强与抗干扰能力强等优点。目前PLC在智能制造、金属冶炼、生物制药、石油化工、汽车生产等领域有着广泛的应用。
随着计算机技术、通信技术等的发展,PLC控制逐渐替代了传统的继电器控制。继电器控制系统通过硬接线的控制方式进行控制,当系统控制需求改变时,需更改继电器控制电路的接线,甚至要更换整个控制板,工作量巨大。PLC避免了传统继电器电路大量的硬接线工作,使用PLC进行工业自动化生产的系统,体积更小,性价比也更高。PLC控制系统具有以下优点:
(1)高可靠性。PLC控制系统中只需要硬件连线到现场设备,控制逻辑均体现在程序中。控制过程发生改变时,只需要将编写的程序进行更改,并下载到相应的存储器中进行调试和完善即可。程序的引入减少了传统继电器控制系统中的接线数量大大减少,避免了硬件连线易出现的故障和隐患。另外,PLC与一些固态元件联用能提供高可靠性的工业控制过程。
(2)更好的系统灵活性。在PLC中可轻松地进行程序编写和修改,设备的升级和改造变得简单而灵活。如果需要,PLC还可以提供如键盘锁等硬件或软件密码等保护功能,实现对系统的加密,保证系统安全运行。
(3)更低的系统成本。传统继电器控制无法满足越来越庞大、复杂的工业生产过程,因此产生了PLC控制系统。虽然单个PLC比单个继电器要贵很多,但是在复杂工业自动控制系统中,使用PLC的性价比更高。通常,如果一个控制系统中需要使用的继电器数量超过六个,则选择PLC其费用会更低。
(4)通信能力。复杂的工业控制系统不再是单个PLC独立工作,而是多个PLC或PLC与计算机协同作业,PLC具有强大的通信能力,不仅PLC之间可以进行通信,而且其可以与计算机及其他控制设备进行通信。
(5)更快的系统响应时间。工业自动化控制系统需要快速接收系统指令,并根据系统反馈信息做出实时响应。PLC可实现高速和实时的工业控制。
(6)更容易的故障识别。PLC具有自诊断功能,用户在程序执行时可以实时观察显示屏上显示的程序执行过程,找出并改正软件和硬件的故障,可以方便地识别和排除系统故障。
在技术不断革新的情况下,PLC的控制模式从简单的逻辑控制、顺序控制,逐步发展到复杂的连续控制和过程控制。PLC的主要控制模式有以下几种:
(1)顺序控制。PLC的顺序控制是指通过简单的执行指令,进行有序的控制。这是PLC最基本的功能。顺序控制改变了传统继电器控制的触点式控制模式,通过PLC软触点的状态数据来实现控制。
(2)过程控制。过程控制是针对模拟量的工作过程,通过对连续变化的电流、电压、压力、温度、湿度等实时模拟量信息与指定的输入状况进行比较和分析,输出使系统能够按一定要求工作的输出量。这种控制手段在化工、冶金、机械、电力控制等方面应用广泛。
(3)运动控制。运动控制是指对设备运动部件位移和速度的控制,使其按照预定的轨迹和状态运行,是自动化控制的一个重要分支。
(4)信息控制。PLC应信息时代的发展要求,衍生出新的工作属性。信息控制是指通过对采集的信息进行数据处理和数据分析,并进行存储与传输的一种控制方式。
(5)远程控制。随着控制方式和控制规模的不断发展,PLC增加了多种通信接口,以适应远程通信与控制功能。远程控制方式主要有PLC与计算机终端的连接控制方式、PLC与以太网的连接控制方式、PLC与PLC控制网的远程互联控制、PLC与智能终端互联的远程控制等。
PLC在工业自动化控制系统的应用领域不断扩大,工业生产对PLC的功能提出了新的要求,使PLC在实际应用中得到研发人员和客户的深入研究和探讨,功能和性能更加完善。例如,PLC日益完善的通信功能使其更加适用于复杂多变的工业生产场合,并且为工业生产提供了更加方便、可靠的数据。
2.分散控制系统
工业自动化控制系统可以分为单站控制系统、多站控制系统,也可以分为集中控制系统和分散控制系统(Distributed Control System, DCS)。
单站控制系统是一个控制器控制一个单独机器的系统,一般控制器之间不需要协同工作,早期的工业自动化控制系统多采用此种控制系统。多站控制系统中一个机器由多个控制器控制。
集中控制系统是指用一个中央处理单元(Central Processing Unit, CPU)集中控制多个设备或进程,每个设备或进程的状态和信息都需要经过进行处理和控制。因此,CPU的工作量很大,作用也十分重要,增加了控制系统因一个小故障而瘫痪的可能性。DCS又称为集散控制系统,与集中控制系统最大的不同是,每台设备或进程有各自专有的控制系统,且各专有控制系统是完全独立的,其中某个专有控制系统出现故障,不影响其他设备或进程的正常工作。如果生产过程不再需要某个设备或进程,则可以直接从DCS中去除该设备或进程,且不影响整个生产过程。DCS由两台或多台计算机通过与多个控制站进行冗余通信来达到对工业生产过程所需要的工艺环节的完美控制。DCS是由设备过程控制和现场过程监控组成的多层次计算机控制系统,综合了4C技术,即计算机(Computer)技术、阴极射线管显示技术(Cathode Ray Tube, CRT)、通信(Communication)技术和工艺控制(Control)技术。其基本思想是分散控制、集中操作、分级管控,且配置非常灵活、组态便捷等。与常规的控制系统相比DCS有如下特点:
(1)高可靠性。一方面,DCS将系统控制功能分散在各台计算机或控制器上实现,系统结构具有容错功能。某一台计算机或控制器出现故障,不会导致系统其他功能的故障。另一方面,DCS中各台计算机或控制器所承担的控制任务比较单一,可以针对每一个独立控制系统需求的功能选用具有特定结构和软件的专用计算机或控制器,从而使系统中每个独立控制系统的可靠性达到最高。
(2)开放性。DCS采用标准化、模块化、开放式的设计模式。当系统需要删减和增加部分功能时,删减或添加相应的功能模块不影响系统的整体结构。
(3)灵活性。根据不同的控制流程,选择不同的组态软件进行软硬件组态。控制设备、组态软件、控制算法等均可以灵活选择。
(4)易于维护。DCS中每一个站点都是一台微型计算机,都具有计算功能。其控制系统具有算法结构简单、维护方便的特点。当某一站点出现故障时,能够快速、准确定位故障点,第一时间了解故障信息,在整个系统运行的情况下可以进行快速“带电”点位更换,快速解决问题,保障安全生产。
(5)协调性。DCS可实现信息资源共享,具有全网发布功能,各种数据通过通信网络在各工作站点之间传输,各站点协调工作、相互配合,最终完成控制系统的总体功能。
(6)控制功能齐全。DCS中各独立专用控制系统控制算法独立运行,互不影响。系统中可集成丰富的控制算法,可以集顺序控制、连续控制和批处理等控制方式于一体,并且工程师可以方便地在系统中加入自己所需的特殊控制算法。
DCS的系统架构十分灵活,从结构上划分,DCS包括控制层、操作层和管理层。控制层是系统控制计算的核心,主要由现场设备和仪表、I/O单元、过程控制站组成。DCS的过程控制站是一个由电源、CPU、网络接口、I/O接口组成的完整的计算机系统,执行为完成某一工业生产过程而设定的控制程序,完成过程控制的大部分决策。DCS中一般采用模块结构,过程控制站的机架用来摆放一定数量的模块。例如,用来连接传感器和执行器(调节阀)的一个或多个I/O通道构成一个模块,一个CPU是一个模块。同一个过程层中只能有一个CPU模块,但可以有一个或多个I/O模块。操作层包括操作员站和工程师站,完成系统的操作和组态。管理层主要是指工厂管理信息系统(Management Information System, MIS),用于完成更高性能的集中管理功能,如计划调度、仓储管理、能源管理等。
从功能上划分,DCS由专用管理员站、工程师站、操作员站、现场控制站等组成,也可由通用服务器、工业控制计算机和PLC构成。控制层处于DCS最底层,也是最重要的一层,一般由分散的现场控制站、数据采集站等组成,实现数据采集和控制。
各厂家生产的DCS自成体系,如横河YOKOGAWA、ABB,这是因为在控制层使用的是各厂家自己制定的通信协议。但是,DCS操作层大部分以以太网为网络通信平台,采用TCP/IP通信协议,因此DCS仍然具有开放的可扩展能力。在DCS中,控制器、计算机均作为一个节点,在以太网中可以随意增减节点数量和布置节点位置。另外,基于Windows系统的用于过程控制的OLE(OLE for Process Control, OPC)、动态数据交换(Dynamic Data Exchange, DDE)等开放协议的发展壮大,完善了DCS实现资源共享的途径。
1.2.3 反馈装置
控制装置的作用主要是进行数据处理、数据分析进而控制一系列生产设备的运行。控制器可以根据输入信号进行高精度、高速度的控制,但本身无法直接从被控设备获得运行的状态。在运行过程中,工业自动化系统会受到干扰信号的影响,无法确定系统是否正常运行,所以需要检测运行结果是否达到了预期要求。工业自动化系统常常需要根据生产过程中的实时状态信息对控制误差进行修正。检测系统运行过程中状态信息的装置称为反馈装置。工业自动化系统是利用传感器监测生产过程的,如利用传感器监测运动部件移动的位移、移动速度和工作温度等。
传感器是一种检测装置,其按一定规律将被测量的物理信号转换成电信号等输出形式,从而获取信息并产生反馈数据,以满足系统对信息传输、处理、存储、显示、记录等的控制需要。在工业自动化控制领域,自动化程度越高,传感器的作用越重要。传感器根据被测量的物理特性可以检测各种信息。传感器检测的信息不仅可以用于校正控制系统,还可以用于运算、存储、显示等。传感器的输出与输入之间的关系,使测量值具有一定的准确度、线性度和灵敏度,以及阈值等。
传感器的核心是敏感器件,它们可以直接感受被测量并快速做出响应,将被测量信号进行相应的转换并输出。例如,热电偶温度传感器的敏感器件是热电极,当热电极两侧的温度不同时,根据热电效应产生热电势,并根据温度与热电势的关系,得出当前测量的温度值并将其输出。敏感器件得到的电信号不一定适合直接输出,有时电信号需要经过调理和转换后才能输出。用于信号调理和转换的器件称为辅助器件,它们的作用是将敏感器件输出的电信号转换为便于传输、处理、显示、记录的信号。
在工业自动化系统中需要检测的物理量有很多种,如温度、压力、液体流量、风力、气体密度、磁力、转矩等。传感器的种类很多,一种物理量的测量可以通过不同类型的传感器实现,如温度可以通过热电偶、热电阻、二极管、晶体管等来测量;同一类型的传感器可以测量不同的物理量,如超声波传感器既可以测量距离,也可以测量液位等。
传感器的分类方式有多种形式。根据是否必须与感知对象接触,传感器通常可分为接触式传感器和非接触式传感器。如果传感器必须与被测对象接触才可以进行检测,则为接触式传感器,如限位开关,当工件移动至接触到限位开关时,产生一个开关量,当工件离开时,产生相应的输出信号。非接触式传感器不需要与感知对象有物理上的接触就可以工作,可避免对生产过程产生干扰,如感应式限位开关,当工件接近传感器时,改变了振荡器的振幅,从而检测工件是否到位。非接触式传感器(电子传感器)比接触式传感器更可靠,不易出错,常用于高速生产线和需要精密控制的生产线。
根据检测信号的不同,传感器可以分为数字传感器和模拟传感器。数字传感器只检测“断开”和“闭合”两种状态,即利用开、关逻辑,比模拟传感器简单、容易使用。数字传感器的输出是经过内部运算之后的结果,其内部通常利用晶体管作为输出级,数字传感器的输出连接到PLC的输入端。若数字传感器检测到某特定状态,晶体管导通,有电流通过;若检测到另外一种状态,晶体管处于截止状态,无电流通过。大部分数字传感器的输出门限电流较小,一般小于100mA,在打开电源前,应该先检查传感器,保证其输出电流在门限值以下,以免损坏传感器。模拟传感器又称为线性输出传感器,其结构较复杂,但可以提供更丰富的信息。例如,超声波液位测量传感器,它将液位值转化为电流值,测量的液位量程为5~30m,其输出电流为4~20mA,该传感器测量的液位与输出电流成正比,液位越高,传感器的输出电流越大,根据电流值的大小即可获得液位值。需要注意的是,数字传感器的输出只有0、1两个值,而模拟传感器则可以提供在量程范围内连续变化的多个数值,两者试用的场合不同,根据工业自动化系统的需求选用合适的传感器类型,才能更好地控制生产过程。
根据信号转换过程的不同,传感器可以分为直接转换型传感器和间接转换型传感器两大类。直接转换型传感器将非电量信号直接转换为电信号输出,如光敏电阻,将光信号转换为电阻值输出。间接转换型传感器将非电量先转换成另外一种非电量,再转换成电信号输出,如以弹簧管为敏感器件的压力传感器是先将压力转化为弹簧管的弹性形变,再将变形量转换为电信号输出。
根据被测物理量的不同传感器可以分为温度传感器、湿度传感器、压力传感器、位移传感器、流量传感器、液位传感器、力传感器、速度传感器和加速度传感器等。
根据工作原理的不同,传感器可以分为电学式传感器、磁学式传感器、光电式传感器、电势式传感器、电荷式传感器、半导体式传感器、谐振式传感器、电化学式传感器。
在典型的工业自动化系统中,传感器和变送器的功能是将待检测的机械信号或电信号转换为标准输出信号,一般输出信号为4~20mA的电流信号或0~5V的电压信号。典型的传感器检测系统如图1-1所示。

图1-1 典型的传感器检测系统
1.电学式传感器
电学式传感器是非电量检测技术中应用范围较广的一种传感器,常用的有电阻式传感器、电容式传感器、电感式传感器、磁电式传感器及电涡流式传感器等,如表1-1所示。
表1-1 电学式传感器类比

2.磁学式传感器
磁学式传感器是利用铁磁物质的物理效应制成的,主要用于位移、转矩等参数的测量。例如,磁体依附在轴上,当磁体通过时,绕制在磁体上的线圈就会接收一个脉冲,通过测量脉冲的频率,即可确定轴的转速。
3.光电式传感器
光电式传感器是利用光电效应和光学原理制成的,用于测量发光强度、光通量、位移和浓度等参数。光电式传感器一般使用发光二极管(Light Emitting Diode, LED)作为光源,光敏晶体管作为接收器。反射型光电式传感器根据反射回来的光束探测目标;透射型光电式传感器通过测量透过目标的光量的变化探测目标信息。
4.电势式传感器
电势式传感器是利用热电效应、光电效应和霍尔效应等原理制成的,主要用于温度、磁通量、电流、速度、发光强度和热辐射等参数的测量。半导体薄片置于磁感应强度为B,且磁场方向垂直于薄片的磁场中,当薄片有电流I流过时,将产生一个垂直于电流和磁场方向的电动势E,这种现象称为霍尔效应。例如,将线性霍尔元件及磁路系统安装在转轴或机械系统的齿轮上,齿盘的转动使磁路的磁阻随气隙的改变而周期性地变化,霍尔元件将输出的微小脉冲信号,经电容隔直、放大电路放大和信号调理电路整形后可以得到稳定的检测信号,从而可以确定被测物体的转速。
5.电荷式传感器
电荷式传感器是利用压电效应原理制成的,在外力作用下,电荷传感器以力敏感元件作为核心器件,在电介质表面产生电荷,从而实现非电量检测的目的,主要用于动态力、振动加速度等动态参数的测量,但不适用于静态参数的测量。
6.半导体式传感器
半导体式传感器是利用半导体的磁电效应、压阻效应、内光电效应、半导体与气体接触产生不同物理和化学反应等特性制成的,主要用于压力、温度、湿度、磁场、加速度和有害气体的测量。其具有体积小、质量小、灵敏度高、响应速度快、便于集成的特点。
7.谐振式传感器
谐振式传感器利用谐振元件把被测参数转换为频率信号,通过振动元件固有振动频率的改变,得到与被测参量成一定关系的电信号。谐振筒、谐振梁、谐振膜和谐振弯管、声表面波传感器的频率范围是从音频(20Hz~20kHz)到100MHz,主要用来测量压力。
8.电化学式传感器
电化学式传感器是以离子导电为基础制成的,主要用于分析气体、液体或溶于液体的固体成分,以及液体的酸碱度、电导率和氧化还原电位等参数的测量。根据电特性的形成不同,电化学式传感器可分为电位式传感器、电导式传感器、电量式传感器、极谱式传感器和电解式传感器等。
1.2.4 辅助装置
工业自动化系统的辅助装置主要包括自动存储/自动提取设备、传送带、刚性自动化装置等。其中,自动存储/自动提取设备按照先进先出原则来存储和提取原材料、生产中的半成品和成品。传送带用来对产品进行移动和分类,通过条形码阅读器或简单传感器,就可以感知所传送的产品明细,并把产品移动到相应的地方。