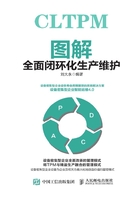
第2篇 CLTPM简介
第3章 提出CLTPM的背景
3.1 推行TPM对企业设备管理有较大的改善
笔者所从事的工作是长期在各类中国企业里,通过推行TPM,辅导企业在设备管理方面取得进步,具体而言是按照TPM的改善体系,推行以下5个方面的工作。
1.个别改善
通过推行个别改善,消除与设备相关的各类损失,消除企业管理中存在的各类损失,改善企业的P、Q、C、S、D、M等。
2.自主维护
推行自主维护,发动操作人员参与设备维护保养,使操作人员做到会操作、会清扫点检、会维护保养、会排除小故障。
3.计划维护
推行计划维护,运用不同的设备维修策略(定期维护、预知维护、事后维护、改良维护等),优化企业设备的计划维护,增强设备的可靠性。
4.教育训练
推行教育训练,对设备的操作人员、维修人员、技术人员、管理人员等进行教育训练,提升他们的能力,从而有效地开展TPM活动、巩固TPM活动的成果。
5.初期管理
通过推行初期管理,建立设备寿命周期成本(Life Cycle Cost,LCC)及维修预防(Maintenance Prevention,MP)的管理机制。
上述5个方面的推进经实践证明,对企业设备管理有较大的改善。
3.2 什么是闭环管理
3.2.1 闭环管理的定义
闭环管理是一个封闭的圆环,包含P、D、C、A 4个方面,PDCA闭环如图3-1所示。

图3-1 PDCA闭环
P:英文单词“Plan”,译为“策划”,即明确某项工作或某项管理活动的目标和开展方式,明确开展的计划,建立该项工作或管理活动的管理机制。
D:英文单词“Do”,译为“执行”,即按计划执行已经建立的管理机制。
C:英文单词“Check”,译为“检查”,即检查管理机制是否被执行,评估执行的程度。
A:英文单词“Action”,译为“改善”,即处理检查的结果,肯定和推广取得的成果,改善发现的问题,跟踪改善的结果并将改善的结果标准化。
所以,P=策划,D=执行,C=检查,A=改善。
3.2.2 PDCA闭环的阶梯式上升
PDCA闭环的阶梯式上升,即从一个PDCA闭环提高到另一个更高的闭环,形成阶梯式上升。每上升一个阶梯就代表取得了一次提升,PDCA闭环不断持续上升的过程就是持续改善的过程。PDCA闭环的阶梯式上升过程如图3-2所示。

图3-2 PDCA闭环的阶梯式上升过程
3.3 在中国企业推行TPM时遇到的问题
在中国企业推行TPM的过程中,笔者也发现了一些问题并将其总结为8个方面。
3.3.1 先进的设备管理模式与落后的设备管理模式并存
中国的设备密集型企业主要有两类:一类企业由于生产工艺的要求,必须是设备密集型的,如钢铁、水泥、发电、石油冶炼等行业的企业;另一类企业由于近年来人力缺乏、人工成本的急剧上升,为了降低成本、稳定品质并提高生产效率,用自动化的设备取代人工,由人工密集型转为设备密集型。
在中国企业尤其是设备密集型企业里,它们中的大多数并不缺乏先进的设备,却缺乏与先进设备相匹配的设备管理模式。例如,深圳××高档无纺布生产企业拥有目前世界上最先进的德国公司生产的全自动化生产线,生产高档无纺布,但是××公司的设备管理与维修人员流动频繁,培训欠缺,采用事后维修的管理方式,设备故障频发,设备不能恒定发挥最大的产能,满足不了客户对高档无纺布产品的交期与质量的要求。企业主一度承认:“这个投资(购买先进的全自动化无纺布生产线)有可能无济于事。”
随着企业的快速发展、设备的日益先进,企业缺乏独创的设备管理的系统理论、方法与工具,这导致先进的设备管理模式与落后的设备管理模式并存,在中国的企业尤其是设备密集型企业里,这并不是个别现象。
3.3.2 企业急需设备管理的系统解决方案
TPM在中国企业推行时,确实可以让设备管理取得较大的改善。笔者发现企业急需这些改善,也迫切需要有关设备管理的系统解决方案。也就是说,企业希望TPM辅导专家从设备管理的方针目标、机构职责设置、前期管理、使用维护、点检管理、状态监测、润滑管理、故障管理、计划维修、备件管理、改造管理、后期(更新、调拨、租赁、报废、处置等)管理、资财(资产财务)管理等方面全方位地提供管理升级的方案并落地实施。
3.3.3 企业员工的流动率较高
就员工流动而言,国有企业稍好点,外资企业次之,民营企业员工的流动性最高。在一些情况较好的外资企业中,其人力资源部往往将每月员工的流动率低于5%作为工作目标。中国企业的员工流动率较高的原因较为复杂,有社会环境的因素(如城镇房价太高、城乡的二元结构等),有企业自身的因素(如待遇偏低、工作环境欠佳、企业文化不佳等),也有员工个人的因素(如敬业精神不强等),在此不做过多的分析。总之,中国企业的员工流动率较高是事实。
日本企业雇员多为终身制,雇员的命运与企业紧密相连,雇员的知识与经验能够在企业内部积累、运用与传承。在这样的环境里推行TPM,好的机制与做法比较容易维持下去。
在《新TPM加工组立篇》(日本设备维护协会编著,中卫发展中心编译)一书中,有关自主维护的推行计划是这样表述的:“基本进度因企业体质不同而异,一般而言,3年左右是恰当的时间,有些公司希望在两年到两年半内完成,但太快了不易定著,5~6年又嫌太长,体质改善恐有困难。如果包括准备期(事前教育),整体计划以3~4年最为恰当。”结合这段话的上下文,这段话阐述的意思就是,自主维护在企业的推行从建立样板机台到覆盖全部设备3~4年最合适。
可是中国企业的现实就是员工的流动率较高,可能不到一年,一线员工就换了一茬儿,这对推行TPM来说是一个挑战。刚在员工层面落地没多久的一些好的机制与做法,长久持续下去存在困难,这对员工的培训管理提出了较高的要求,也要求TPM的推行与维持必须特别注重按PDCA闭环进行。其中,C环节与A环节应该是重中之重。
3.3.4 一些企业存在急功近利的思想
2008年以前的中国制造业企业基本上是怎么做都能赚钱,而且利润可观,企业的管理异常粗放。2008年以后,竞争激烈迫使企业重视内部挖掘与管理,于是企业通过各种方式改善体系(例如,精益生产、TPM及瓶颈管理(Theory of Constraint,ToC))来寻求解决之道。
但是相当多的企业由于以前改善的根基(改善的理念、方法与措施)较弱,因此缺乏耐心耕耘的意愿,容易产生急功近利的思想,希望改善体系能够药到病除、立竿见影。
在“第1章 TPM简介”里,我们知道TPM是美国的PM在日本电装推行后,以PM为基础融入日本的理念与做法后被日本提炼出来的一套管理方法。结合一些企业坚持推行TPM 20多年所获得的实践经验来看,理论提炼经历了由生产部的TPM到全公司的TPM的过程。从引进美国的PM到经过实践,再到提炼出全公司的TPM,总共耗时30年左右。据此可以理解,企业推行TPM不可能一蹴而就。
从事TPM咨询业务的咨询公司去企业推介咨询业务时,企业往往会提出需要3~6个月才能见到效果,咨询公司也会答应这种短期见效的做法,其实这只是一种咨询公司无奈之下的商业运作模式,因为咨询公司为客户实施短期见效的项目是其为后续从客户那里拿到更多订单的策略。
用3~6个月见效是指咨询公司针对企业某个具体的点制订方案并与企业一起改善,产生改善效果。如果企业不能系统地、长期地贯彻实施TPM,即使在某个点上有改善,也难以实现企业整体经营效益的最大化。况且有时针对企业的某个具体的点进行改善,做的也是无用功。例如,虽然提高了某道工序的生产效率,但该工序如果不是企业的瓶颈工序,效率越高,由该工序生产的在制品就会越多,浪费也就越大,这样的改善其实对企业的整体效益是有反作用的。
所以,推行TPM不能急功近利,要有短期、中期、长期的规划,全方位地系统推进。一般来说,企业应制订3年规划并坚持PDCA循环改进。
3.3.5 部分企业员工对规则的执行力较弱
所谓规则,就是规定和法则。在执行规定方面,部分企业员工刚开始能认真执行规则,不久之后就会打折扣执行。久而久之,如果没有检查、督促、处罚,他们就会放弃执行。所以,在中国企业推行TPM建立的好规则,要特别在PDCA的C环节与A环节上下功夫,让员工持续执行。
3.3.6 TPM改善的方法论与工具存在不足
笔者在企业长期推行TPM的实践中发现,TPM改善的方法论与工具在支撑目标的实现方面存在着一定的不足。表3-1是对比全员生产维护与全面生产管理的改善方法论与工具。我们根据此表得出的结论是,在进行企业经营效益最大化的改善中,改善的方法论与工具存在着一定的不足。
表3-1 TPM改善的方法论与工具对比

从企业经营的角度来看,企业经营效益最大化的改善包括产品的各个环节,如市场营销、产品规划、设计开发、采购、制造、品质、仓储、物流、安全、环保、行政人事、售后服务等。但是TPM阐述的改善方法论与工具在进行企业经营效益最大化的改善方面存在着一定的不足。这个话题牵涉的面比较广,需要系统地将TPM与精益管理、瓶颈管理、六西格玛等管理模式进行对比研究。这里仅举两个例子予以简单说明。
1.没有涉及价值流分析
为了使企业局部的改善对整体效益的提升产生良好的影响,运用价值流分析(Value Stream Mapping,VSM)是较为理想的方法,即:
(1)企业从整个价值链(供应商、企业本身、客户)的角度来分析自己的现状,从而找出改善点;
(2)企业从整个价值链的角度规划企业的未来状况。
TPM不涉及价值流分析的理论与工具。
2.提升P、Q、C、D的改善理论与工具欠缺
例如,实行整流化生产(又称小批量生产或单件流)、均衡化生产、自动化等改善企业的P、Q、C、D,TPM中没有类似的改善方法论与工具。
3.3.7 如何结合中国企业的实际情况推行TPM
南橘北枳这个成语出自《晏子春秋·内篇杂下》:“橘生淮南则为橘,生于淮北则为枳,叶徒相似,其实味不同。所以然者何?水土异也。”成语的本意是淮南的橘树移植到淮河以北就变为枳树,说明同一物种的生长情况因环境条件不同而发生变化。
南橘北枳在现代汉语的使用中多含贬义的成分,形容某种事物因为环境的变化而“异化”或者“变质”。TPM的推行也要因时因地发生变化,否则会“水土不服”。
TPM毕竟是基于日本的国情和日本企业的实际情况产生的企业改善体系,我们在应用时不能“照葫芦画瓢”,否则不会取得跟日本企业推行TPM一样的效果。因此在引进应用TPM的时候,我们主张依据中国国情和企业的实际情况做相应的变化、完善和补充。也就是说,要消化吸收TPM的原理、原则与精髓,找出适合中国企业的TPM推进的做法,而不是全盘照搬。只有结合中国的国情与中国企业的实际情况,将TPM改善体系转化为适合中国企业的改善体系,TPM的推行才会取得成功。
3.3.8 如何结合工业发展的新趋势推行TPM
社会在不断地向前发展,工业也是如此。工业正在从工业1.0阶段,经过工业2.0阶段、工业3.0阶段向工业4.0阶段发展(请详见“26.2.2 工业革命的4个阶段”),随之而来的是智能工厂、智能制造、智能物流(请详见“26.3 工业4.0计划的三大主题”),以及为适应智能制造发展起来的智能运维的快速发展。
面对这些新的发展,企业在推行TPM时会遇到很多新的挑战。企业对新的挑战要有相应的解决方法。例如,在智能制造的条件下,人与机器的关系被改变,操作人员从管理机器的工作中解脱出来,他们在几乎无人值守的工厂中工作时需要掌握哪些新的知识与技能?他们的能力结构模型应该是怎样的?在推行TPM的“教育训练”支柱时,如何提出相应的解决方案?
再如,在智能制造的条件下,让设备管理组织从传统的直线职能制转变为扁平化,设备管理组织中各个岗位的职责如何被重新划分与定义?
笔者在“第26章 智能运维4.0”中就传统运维存在的问题与智能运维的解决方案进行了初步探讨,请详见“第26章 智能运维4.0”中的相关章节。