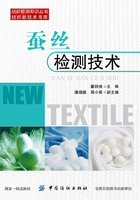
第二节 外观疵点
一、疵点分类
(一)生丝、土丝、双宫丝的疵点
不同的丝类外观疵点名称和说明也不同。生丝、土丝、双宫丝的外观疵点大部分相同,见表5-1,其中,生丝外观疵点根据对品质的危害程度分为主要疵点和一般疵点两类,而土丝、双宫丝外观疵点无此区分。
表5-1 生丝、土丝、双宫丝外观疵点

生丝外观疵点中还有一种常见疵点叫白斑(丝绞表面呈现光泽呆滞的白色斑,长度在10mm及以上者,长度或颜色种类差异较明显),以及一些不常见疵点,发现时也同样作为一般疵点处理,其他疵点如下。
(1)松弛丝。丝绞中有部分丝条松弛。
(2)浮丝。丝把表面丝条显著浮起。
(3)紧丝(吊丝)。丝绞的部分丝条吊紧。
(4)松紧丝。丝片内松外紧。
(5)编丝及留绪不良。编丝位置及留绪方法不合规格要求,扣线不牢,或结头太长。
(6)绞把不良。绞头蓬散,绞法不良;丝绞排列不整齐,打把纱绳捆扎过松或过紧,打结不良。
(7)络交不正。丝条紊乱不整齐。
(8)分层丝。丝片明显分成两层或以上。
(9)无鞘丝。缫丝未经加捻,四条扁平,光泽失常。
(10)直丝。丝条未经络交,重叠一处,形成丝片部分突起。
(11)掬丝。打把纱绳穿过丝绞内部。
(二)生丝主要外观疵点样照
1.颜色不整齐 绞装和筒装颜色不整齐疵点如图5-1所示。

图5-1 颜色不整齐
2.霉丝 绞装和筒装霉丝疵点如图5-2所示。

图5-2 霉丝
3.绞把硬化 绞把硬化疵点如图5-3所示。
4.第或角硬胶 角硬胶疵点如图5-4所示。
5.附着物(黑点)附着物(黑点)疵点如图5-5所示。
6.污染丝 绞装和筒装污染丝疵点如图5-6所示。
7.纤度混杂 绞装和筒装纤度混杂疵点如图5-7所示。

图5-3 绞把硬化

图5-4 角硬胶

图5-5 附着物(黑点)

图5-6 污染丝

图5-7 纤度混杂
8.水渍 绞装和筒装水渍疵点如图5-8所示。

图5-8 水渍
9.夹花(色圈)绞装和筒装夹花(色圈)疵点如图5-9所示。

图5-9 夹花(色圈)
10.绞重不匀(丝筒不匀)绞重不匀和丝筒不匀疵点分别如图5-10和图5-11所示。

图5-10 绞重不匀

图5-11 丝筒不匀
11.双丝 绞装和筒装双丝疵点如图5-12所示。

图5-12 双丝
12.切丝 绞装和筒装切丝疵点如图5-13所示。

图5-13 切丝
13.飞入毛丝 绞装和筒装飞入毛丝疵点如图5-14所示。

图5-14 飞入毛丝
14.凌乱丝 凌乱丝如图5-15所示。
15.白斑 白斑如图5-16所示。

图5-15 凌乱丝

图5-16 白斑
16.宽紧丝 宽紧丝如图5-17所示。
17.缩丝 缩丝如图5-18所示。

图5-17 宽紧丝

图5-18 缩丝
18.重片丝 重片丝疵点如图5-19所示。
19.丝条胶着 丝条胶着疵点如图5-20所示。

图5-19 重片丝

图5-20 丝条胶着
20.绞把不良(成型不良)绞把不良和成型不良分别如图5-21和图5-22所示。

图5-21 绞把不良

图5-22 成型不良
21.虫伤丝 虫伤丝如图5-23所示。
22.跳丝 跳丝如图5-24所示。

图5-23 虫伤丝

图5-24 跳丝
(三)捻线丝的疵点
捻线丝外观疵点也以主要疵点和一般疵点区分,详见表5-2。
表5-2 捻线丝外观疵点

(四)绢丝(丝)的疵点
绢丝和丝类产品的成形状态一般为筒装,筒装绢丝和筒装丝的外观疵点也分为主要疵点和一般疵点,详见表5-3。
表5-3 筒装绢丝和筒装丝外观疵点

绞装绢丝和绞装丝的外观疵点检验中,没有具体内容,只有处理方法。本章第四节批注规定中将进行介绍。
二、常见疵点形成原因
(一)霉丝形成原因
霉丝主要是由于生丝干燥不足,回潮率过高(13%以上),储存保管不善所造成。
(二)丝把硬化(丝条胶着)形成原因
丝把硬化(丝条胶着)产生原因主要是因为生丝本身回潮率过高,储存过久或储放条件潮湿,丝胶发生了变化,加以堆放、运输途中受重压,以致丝条与丝条粘固。具体表现为大丝片干燥程度不够。编丝、绞丝、整理等工序相对湿度过高,丝片回潮率超过13%,其水分又不能及时散发;不能及时成包、成件的丝绞过多,久堆在整理室,而整理室又潮湿,丝绞长时间堆叠受潮。
(三)角硬胶、粘条形成原因
角硬胶和粘条的形成原因相近,由于小丝片太湿或者给湿过多,并且复摇烘力不够,如果复摇车厢温度低,相对湿度高、车速快、烘丝时间短,大丝片必然干燥不够,粗条容易出现硬胶、粘条。或者因为复摇采取高温急干,使丝条极力收缩、相互施压,也易产生硬胶、粘条。其次,如果丝胶膨润溶解过度,丝条干燥慢,也会产生硬胶、粘条。
(四)附着物(黑点)形成原因
丝胶和它的吸附作用是产生黑点丝的内因;污物、毛屑丝、机械破损、丝条通道不清洁是产生黑点的外因。缫丝索绪汤温过高和索绪时间长都会使丝胶溶解量增加,丝胶溶解后大量凝聚在缫丝汤面。当丝条卷上子时,如果丝条通道的零件安装位置不正确或者清洁工作不到位,丝条通过时,就有一种形同小水珠的丝胶液积聚在那里,一段时间后,或者停车之后再开车时,或者丝条上有糙粒或裂丝时,这些丝胶液便被带上丝,干燥后就形成黑点。丝胶本身并非黑色,如果不是尘埃、污物污染,即使缫丝时将丝胶带上丝,烘干也不至于成为黑点。因此,污物、机械状况不好是构成黑点丝的外因。内染茧是一种由于病蚕或蛹体腐烂后污染所致的蚕茧,选茧时不易发现剔除。内染茧的污染微粒被带上小后,丝条就出现密集的、一连串的小黑点,即散布性黑点。
(五)污染丝
污染丝产生的原因有以下几方面:煤灰、煤烟和其他尘土随空气流入车间内进入大运转车厢;在霜降时期,雾大的地区,特别是早晨雾大的时候容易产生污染丝;复摇车厢的机件产生的铁粉末。
(六)颜色不整齐
造成颜色不整齐的原因比较多,主要有以下几方面。
1.茧色 用颜色混杂的蚕茧缫丝,丝色必然不齐,具体表现为:油茧、黄斑茧缫丝的丝色为乳色;霉茧、米黄色茧、微绿色茧缫丝的丝色为白色带微绿;而内染茧缫丝的丝色为灰白。蚕品种对丝色有着不同的影响,春蚕较白,夏秋茧自带微绿。
2.制丝用水水质 在缫丝过程中,茧丝表面的丝胶对水中的杂质,如盐类(Fe2+、Fe3+、Mn2+、Cu2+、Al3+、Na+、Ca2+、Mg2+)、色素以及胶体和悬浮物,具有较大的吸附性,水中杂质被吸附在茧丝表面,杂质的不同含量对生丝色泽、手感产生不同的影响。其次,煮汤、索汤、缫汤温度高,蛹体溶出物、色素脂酸和蜡质物溶解量多,丝条吸附量大,对丝色影响大。两种丝胶含量差异大的茧混合缫丝,丝色容易不整齐。缫丝用水流量不统一,也会对丝色造成一定的影响。
3.缫丝机械 如煮茧机、缫丝机、小真空给湿机、复摇机等,若制造材料不统一,会影响丝色。因为这些材料都是和蒸汽、水接触,有的金属离子要被氧化而带入水中,被丝条吸附,影响丝色。
4.配色成件 如果不按生产日期顺序成色、成件,每天,丝杂乱堆放,有的丝时间一长,容易使丝色显著变化,人为地造成颜色不整齐。
(七)夹花
产生夹花丝的原因有很多与颜色不整齐的产生原因相同,往往出现丝色夹花时,也会出现颜色不整齐。夹花丝根据夹花的表现形式分为层次夹花、线条夹花和短接夹花。
1.层次夹花 产生原因有以下几方面:一是“三汤”突变,或长时间停车,如节假日休息等,没有用水冲洗煮茧机、索绪锅、缫丝机和丝条通道,管道中积存锈水;二是机油漏入缫汤,尘埃污物溶于缫汤,也会造成层次夹花;三是由于茧丝受霉菌侵蚀,破坏丝胶蛋白质,如蚕茧霉变,小丝片不干燥,浸水后的丝小放置太久。大量的有色茧,也会造成层次夹花。
2.线条夹花 基本是由茧子问题引起的,缫丝茧色不一致,或者不同季节的蚕茧混缫,如秋茧和夏茧,或者因缫剥茧处理不同等都会产生线条夹花。
3.短节夹花 大多是在小上产生的,比如小丝片干燥不好,就会形成一节一节的夹花。或者新木小未处理就投入使用,也会产生短节夹花。不过,目前缫丝厂用的小一般为铝合金材质的,短节夹花已经很少发生。
(八)绞重不匀
造成绞重不匀的原因比较多。缫丝工艺设计的缫折与实际缫折差距很大,络丝桶数没有进行相应的调整,就会造成丝片普遍偏大或偏小;立缫机有的丝停过久,自动缫丝机在运转中部分车位停车时间过长,造成丝片厚薄悬殊;发生疵点丝(伤丝、油污丝、双丝)时弃丝过多;双丝部分过长,会使两片丝绞重差距明显;煮茧室的挖茧亏余量过大,没有挖准茧量,落丝桶数不准,或送茧工将桶数搞错,都可能导致丝片过大、过小。
复摇阶段,复摇工配片工作认真的话,可以有效避免绞重不匀的产生。
(九)双丝
在缫丝、复摇等过程中,丝条断裂后未及时处理或处理不当,使丝条卷入邻近丝条造成两根合并形成双丝。
1.空小上丝 集绪过多(10绪以上),有的丝条运转很久才恢复到正确位置,而在不正确位置运转的那段丝条与正确的相互黏着,在复摇时被拉断而带上其他丝片,就会形成一段双丝。
2.丝条断头 丝条断头后黏附在邻近丝条上,使两根丝条卷上同一个小,或缫丝接头后,误将丝条放在邻近的络交环里,或未放入络交环,而被另一绪丝条带上小,都会产生双丝疵点。
3.复摇 复摇过程中以下几点也会产生双丝。
(1)复摇时小排列不规则,丝条离解方向不一致,丝条在卷绕过程中互碰,断头被带上另一丝片。
(2)复摇巡回慢,无规律,处理断头不及时。
(3)飞毛丝处理不好被风吹上丝条,带上大等。
4.双丝防止棒和络交环 未安装双丝防止棒,或双丝防止棒太短,或丝小未插进双丝防止棒;或上丝、换、接结时丝条未挂进络交环,造成丝条卷绕在另一丝片上导致产生双丝。
5.检查操作 操作人员检查丝片不细致,特别是对邻近丝片大小悬殊没有仔细检查,让双丝混入丝包。
(十)飞入毛丝
缫丝车间、车厢,复摇车间、车厢,小真空给湿装置以及小上毛屑丝多,容易飞入毛丝。缫丝工、复摇工将寻绪、接结后的毛丝,到处乱丢,也会造成飞入毛丝。
(十一)分层丝(脱壳丝)
丝条卷取张力不一致,特别是小丝片内层和外层离解张力不一致,这是造成分层的主要原因。其他原因还有小丝片给湿量、给湿水温差过大,丝条干燥时收缩不一;大丝片回潮率过低,又不进行丝片吸湿平衡而急于编丝、落丝;大丝片待接时间或停车时间过长;复摇车厢温湿度和车速突变。