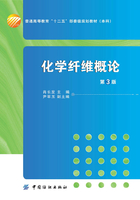
第三节 粘胶原液的制备
粘胶纤维的原料和成品,其化学组成都是纤维素,仅仅是形态、结构以及力学性能发生了变化。粘胶纤维的生产,就是通过化学和机械的方法,将浆粕中很短的纤维制成各种形态并具有所要求品质、适合各种用途的纤维成品。各种粘胶纤维的生产都必须经过下列四个过程:
(1)粘胶的制备。
(2)纺前准备。
(3)纤维成形。
(4)纤维的后处理。
其具体生产工艺流程如图2-5所示。
图2-5 粘胶纤维的工艺流程示意图
一、碱纤维素的制备
1.浆粕的准备
浆粕的生产一般是分批进行的,各批浆粕的品质往往存在着一定的差异,特别是当浆粕的原料品种或质量变化较大以及生产工艺控制出现波动时,就会对粘胶生产产生很大影响。为减小各批浆粕之间的品质差异,通常采用多批混合的方法。在混合时,各批浆粕的品质差异应有一定的允许范围。品质差异太大,特别是相对分子质量分布差异太大的浆粕不能相混。
浆粕的含水率直接影响粘胶生产工艺。但含水率的高低并不是重要因素,只要相应地改变工艺条件亦可制得符合工艺要求的碱纤维素,重要的是浆粕含水率的均匀性。含水率波动,则浸渍时渗透到浆粕内的碱液被稀释的浓度不同,浆粕的膨润不均匀,碱纤维素的生成也不均匀,从而使以后的老成和黄化反应不均匀,制得的粘胶过滤性能变差,成品纤维的品质下降。所以,含水率的波动应控制在±2%范围内,在使用时,应根据浆粕含水率的不同适当调整浸渍工艺,以制得符合要求的碱纤维素。
2.纤维素浸渍
(1)浸渍过程中化学及物理化学变化:浸渍是粘胶纤维原液制备的重要工序。碱与纤维素的相互作用通常可分为两个阶段,首先生成碱纤维素,纤维素结构单元反应如下:
碱纤维素还可进一步形成纤维素钠盐,纤维素结构单元反应如下:
这一过程进行得极快,只需数分钟。生成的碱纤维素的γ值在100左右,即平均二个葡萄糖残基结合一分子的氢氧化钠,其结合形式既有可能是醇钠形式C6H9O4ONa,又有可能出现分子化合物的形式C6H10O5·NaOH·nH2O。一般在纤维素大分子上酸性较强的仲羟基有可能生成醇钠,而在酸性较弱的伯羟基上则生成分子化合物。
纤维素在浸渍过程中除发生以上的化学变化外,还要发生溶胀和部分低分子溶出,纤维素的聚合度有所降低。纤维素的形态结构受到破坏,超分子结构也发生了变化;纤维素对各种化学试剂的反应能力有所提高,从而有利于黄化反应的进行。
(2)影响纤维素溶胀作用的因素:浆粕的膨润作用,包含了纤维间毛细管水的凝聚作用和纤维素分子上羟基的溶剂化作用。纤维素大分子的溶剂化程度受溶液中离子的水化能力和水化层厚度的影响。如果升高温度,使水化层中水分子的热运动加剧,破坏水化层的稳定性而使其减薄,将导致纤维素的溶胀度减小。提高碱浓度会使结合到纤维素大分子上的离子数增加,溶胀度增大。但当碱浓度超过一定限度时,溶胀度反而减小,这是由于碱液中自由离子数大量增加,对结合到纤维素大分子上的水产生了竞争,使离子水化层变薄,则溶胀度反而减小。
如果碱液中含有能降低钠离子水化作用的各种盐类,同样也会削弱纤维素的膨润效果。所以,碳酸钠、氯化钠等杂质存在对纤维素的浸渍是不利的。
(3)浸渍过程的工艺参数:
①碱液浓度:理论上,常温下当碱液中碱的质量分数为10%~12%时,纤维素的溶胀最剧烈。实际生产中,还必须考虑碱化过程中产生的水分和浆粕中的水分。因此,通常浸渍碱的质量分数控制在18%~20%。
②浸渍时间:生成碱纤维素的反应时间很短,但浆粕从湿润到碱液逐步向纤维素内部渗透达到均匀的程度,需要一定的时间,而半纤维素的溶出则需要更长的时间。浸渍时间的长短主要取决于浆粕的结构形式、浸渍方式以及浸渍工艺。通常,古典法需要45~60min,连续法需要15~20min,五合机法需要30min。
③浸渍温度:碱化反应是放热反应,低温有利于溶胀和使半纤维素充分溶出。升高温度会使碱纤维素发生水解反应。因此,浸渍温度不宜太高。对于不同的浆粕原料和设备,浸渍温度有较大的差异。一般,古典法为20℃左右,连续法为40~60℃,五合机法为30~60℃。
④浸渍浴比:浆粕的绝对干燥重量和碱液体积之比,称为浴比。增大浴比,可以增加碱液与纤维素的接触机会,提高浸渍碱的均匀性。但浴比过大,会影响单机生产能力,反而会造成碱化不匀。一般,连续法为(1∶20)~(1∶40),五合机法为(1∶2)~(1∶3)。
3.碱纤维素的压榨与粉碎
浆粕经过浸渍以后,必须与过剩的碱液分离,因为过量的水和碱会直接影响黄化反应的正常进行,还会发生多种副反应,消耗大量的二硫化碳。所以,浸渍后的纤维素需要进行压榨,使α-纤维素含量控制在28%~30%,NaOH含量控制在16%~17%。
经过压榨后的碱纤维素非常致密,表面积减小,所以必须进行粉碎,使其成为细小的松屑粒状,从而增加碱纤维素反应的表面积,使以后各工序中的反应能够更加均匀地进行。
4.碱纤维素的老成
老成是借空气中的氧化作用,使碱纤维素分子链断裂,聚合度下降,以达到适当调整粘胶黏度的目的。
碱纤维素老成的程度,主要通过调节老成时间、老成温度及采用氧化剂或催化剂来控制。延长老成时间,可以增加碱纤维素氧化降解的程度;提高老成温度,可以加快碱纤维素氧化降解反应进行的速度,但是温度过高,裂解剧烈,纤维素分子链分布均匀性变差。因此,低温长时间老成比高温老成效果好。实际的老成温度应根据生产的纤维品种和设备而定。另外,如含锰、钴等化合物能明显加速碱纤维素降解,缩短老成时间。
二、纤维素黄原酸酯的制备
1.碱纤维素的黄化反应
黄化是粘胶制造工艺中非常重要的一步,在此工序中,使难溶解的纤维素变成可溶性的纤维素黄原酸酯。纤维素结构单元反应过程如下:
或
黄化反应首先发生在纤维素大分子的无定形区及结晶区表面,并逐步向结晶区内部渗入。与此同时,碱纤维素的超分子结构受到破坏,从而提高其溶解性。
2.黄化时的副反应
在黄化时,碱纤维素中存在的大量游离碱与二硫化碳可发生一系列的副反应:
2CS2+4NaOHNa2CS3+Na2CO3+H2S↑+H2O
2CS2+6NaOHNa2S+Na2CO3+Na2CS3+3H2O
3CS2+6NaOH2Na2CS3+Na2CO3+3H2O
CS2+4NaOHNa2CO3+2NaHS+H2O
副反应产物三硫代碳酸钠(Na2CS3)是一种油状橘红色物质,它使黄原酸酯着色。由于黄化反应中主、副反应是同时进行的,所以,根据体系色泽的变化可以判断黄化反应的终点。
3.黄化反应的机理
黄化反应主要是气固相反应,反应过程包括二硫化碳蒸气按扩散机理从碱纤维素表面向内部渗透的过程以及二硫化碳在渗透部分与碱纤维素上的羟基进行反应的过程。黄化反应是放热反应,所以低温有利于黄化反应,而较高温度则容易生成更多的副产物。
黄化反应是可逆反应,主要取决于烧碱和二硫化碳的浓度。二硫化碳对碱纤维素的渗透,在无定形区易于进行,而结晶区的二硫化碳主要在微晶表面进行局部化学反应。在溶解过程中,甚至在以后的粘胶溶液中,二硫化碳继续向微晶内部渗透,称之为“后黄化”。因此,二硫化碳的扩散和吸附对反应起着重要作用。
三、纤维素黄原酸酯的溶解和混合
1.纤维素黄原酸酯的溶解
纤维素黄原酸酯与溶剂接触,首先黄酸基团会发生强烈的溶剂化作用,纤维素开始溶胀,大分子之间的距离增大。当有足够量的溶剂存在时,纤维素黄原酸酯就大量吸收溶剂分子而无限溶胀,纤维素的晶格彻底破坏,大分子不断分散,直至形成均相的粘胶溶液。
纤维素黄原酸酯的溶解过程在带搅拌的溶解釜内进行。块状分散的纤维素黄原酸酯在其中经连续搅拌和循环研磨,逐步被粉碎成细小颗粒,从而加速溶解过程。
溶解过程中,甚至溶解结束后若干小时内,黄酸基团沿着纤维素大分子链继续再分配,使黄化比较充分的黄酸基团部分结合在黄化不充分的部分上,这种作用称为脱黄化和再黄化。
2.碱纤维素黄原酸酯的混合
纤维素黄原酸酯的溶解过程实际包括两个阶段,即粉碎和混合阶段。在开始溶解时,存在着黄原酸酯团块,研磨粉碎作用是主要的,随着黄原酸酯团块的消失,粉碎逐渐不起作用。在溶解的最后阶段主要是混合作用。溶解结束后,为尽量减小各批粘胶间的质量差异,需将溶解终了的数批粘胶进行混合,使粘胶均匀,易于纺丝。
四、粘胶的纺前准备
1.粘胶的熟成
纤维素黄原酸酯在热力学上是不稳定的,即使在常温下放置也会逐步分解,酯化度下降。粘胶在放置过程中发生一系列的化学和物理化学变化,称为粘胶的熟成。
(1)粘胶在熟成过程中的化学变化:
①水解反应:
②皂化反应:
粘胶在熟成过程中,水解反应和皂化反应同时存在。当粘胶中碱的质量分数低于8%~9%时,则以水解为主。一般,粘胶中碱的质量分数都在4%~7%,因此,粘胶在熟成过程中主要发生水解反应。除以上反应外,在熟成过程中,一些热力学上潜能较高的副产物,如过硫代碳酸盐及过渡的硫氧化合物等,也不断地转化为潜能较低的碳酸钠和硫化钠等。
(2)熟成过程中粘胶黏度的变化:粘胶在熟成开始黏度就急剧下降,粘胶中游离的二硫化碳进入纤维素的结晶部分,引起后黄化,使部分结晶区继续分散溶解于碱液中,分散粒子逐渐变小。黏度经最低点缓慢上升,这是因为随着熟成的继续进行,酯化度下降,使脱溶剂化和结构化程度增加,因而粘胶的黏度开始上升。随着副产物的不断增加,酯化度进一步下降,纤维素大分子因氢键的作用而不断凝集,使粘胶的黏度开始急剧上升,直至形成凝胶。
(3)熟成过程中黄酸基团的再分配及熟成度的变化:粘胶在熟成过程中,由于仲羟基上黄酸基和伯羟基上黄酸基的离解速度不同,随着熟成过程的进行,总的酯化度呈缓慢下降的趋势,仲羟基位置上的酯化度急剧下降,伯羟基位置上的酯化度稍有上升,结果使黄酸基团在纤维素分子链上分布均匀,从而使粘胶均匀稳定。
粘胶的熟成度是指粘胶对凝固作用的稳定程度,一般以NH4Cl值或NaCl值来表示。熟成开始时,稳定值急剧上升,达到最大值后便逐渐减小。随着黄酸酯分解,粘胶的结构化程度增加,降低了溶液的稳定性。熟成度是粘胶的重要指标之一,它直接影响纺丝成形过程的快慢及成品纤维的性能。
2.粘胶的过滤
在溶解以后的粘胶溶液中含有大量的微粒,其数量可达3万~4万/cm3,尺寸0.1~50μm,含量一般不超过粘胶重量的0.01%~0.02%。这些微粒主要是未反应的纤维及其片断、未溶解的纤维和溶解不完全的凝胶粒子以及半纤维素与Fe、Ca、Cu的螯合体等,此外还有原料、设备和管道中带入的各类杂质。这些微粒在纺丝过程中会阻塞喷丝孔,造成单丝断头,或在成品纤维结构中形成薄弱环节,使纤维强伸度下降。
通常,粘胶在纺丝前要经过三道过滤。过滤介质一般为绒布和细布。目前,大多数还是采用板框式过滤机,也有采用以PVC粒子作为载体的桶式过滤机和连续筛滤机进行头道过滤的。
3.粘胶的脱泡
粘胶的黏度越高,越容易因搅拌、输送和过滤而带入大量尺寸不一的气泡,如果不加以去除将加速粘胶的氧化过程。过滤时,气泡会破坏滤材的毛细结构,使凝胶粒子渗漏;成形时,气泡会使纤维断头和产生疵点,而微小的气泡则容易形成气泡丝,降低纤维的强度。因此,必须严格控制粘胶中的气泡含量。一般采用抽真空的方法加速气泡的去除,控制气泡在粘胶中的体积分数在0.001%以下。
五、粘胶的质量指标及分析方法
粘胶的过滤性能及组成、黏度、熟成度是粘胶的主要质量指标,对纤维产量及质量有很大影响。
1.过滤性能
浆粕制造、浸渍、压榨、粉碎、黄化和溶解各工序中存在的质量问题,将集中体现在粘胶过滤性能的好坏上。因此,过滤性能是衡量浆粕质量和粘胶制造工艺的一个重要指标,并直接影响原材料的消耗和纺丝能否顺利进行。
在生产中,常采用阻塞值表征粘胶的过滤性能。阻塞值(Kw)用下式表示:
式中:P1——恒压下20min后通过规定过滤介质的粘胶量;
P2——同一试验中继续测定40min后通过规定过滤介质的粘胶量。
阻塞值越小,表明粘胶的过滤性能越好。
2.粘胶的组成
粘胶的组成与成品纤维的线密度、染色均匀性和耐多次变形性有关。
纤维的粗细与粘胶中纤维素含量及泵供量有关。纤维素含量或泵供量的波动直接影响最终纤维的线密度偏差及不匀率。线密度不匀会造成染色不匀。
粘胶中游离碱含量对粘胶的性能影响很大。未与纤维素及其他杂质结合的碱含量增加时,粘胶的黏度降低,过滤性能改善,熟成变缓。
粘胶组成的化学分析比较复杂,实际生产中一般通过黄化及溶解工序中加入的碱量、二硫化碳量和水量来控制粘胶的组成。
3.粘胶的黏度
纤维的强度随纤维素聚合度的增加而提高,在实际生产中,粘胶的黏度间接表示纤维素聚合度,所以粘胶的黏度直接影响纤维的强度。
生产中采用落球法测定粘胶的黏度,先将粘胶灌入垂直安放的测定管内,然后在粘胶中放入一粒直径3mm、重0.12~0.13g的小钢球,使其靠自重下降,用秒表计测小钢球在粘胶中沉降20cm所需的时间(s),表示粘胶黏度。
黏度低于20s时,粘胶几乎没有形成丝条的可能性;黏度大于50s后,最大喷丝头拉伸则随黏度的上升而下降,可纺性也变差。
4.粘胶的熟成度
粘胶的熟成度对成品纤维的染色均匀性和强伸度有较大影响。熟成度越低(即NH4Cl值越高),成形速度越慢,所形成的纤维结构紧密,染色越浅;熟成度高,成形速度快,纤维结构不均匀,则染色深且不匀,纤维的强伸度也明显降低。
生产上熟成度的测定方法:在烧杯中放入20g粘胶和30mL蒸馏水,搅拌后,用质量分数为10%的NH4Cl溶液滴定。在滴定时一边用玻璃棒搅拌,一边徐徐加入NH4Cl溶液,待至玻璃棒上的粘胶在玻璃棒约呈45°倾斜时5min内不落下为止。此时,所消耗的NH4Cl的毫升数即为粘胶的NH4Cl值,表示粘胶的熟成度。