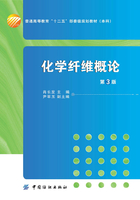
第四节 化学纤维的生产方法概述
化学纤维的品种繁多,原料及生产方法各异,其生产过程可概括为以下四个工序。(1)原料制备:高分子化合物的合成(聚合)或天然高分子化合物的化学处理和机械加工。(2)纺前准备:纺丝熔体或纺丝溶液的制备。(3)纺丝:纤维的成形。(4)后加工:纤维的后处理。
一、原料制备
1.成纤高聚物的基本性质
用于化学纤维生产的高分子化合物,称为成纤高聚物或成纤聚合物。成纤聚合物有两大类:一类为天然高分子化合物,用于生产再生纤维;另一类为合成高分子化合物,用于生产合成纤维。作为化学纤维的生产原料,成纤聚合物的性质不仅在一定程度上决定纤维的性质,而且对纺丝、后加工工艺也有重大影响。
对成纤聚合物一般要求如下:
(1)成纤聚合物大分子必须是线型的、能伸直的分子,支链尽可能少,没有庞大侧基。
(2)聚合物分子之间有适当的相互作用力,或具有一定规律性的化学结构和空间结构。
(3)聚合物应具有适当高的相对分子质量和较窄的相对分子质量分布。
(4)聚合物应具有一定的热稳定性,其熔点或软化点应比允许使用温度高得多。
化学纤维的纺丝成形普遍采用聚合物的熔体或浓溶液进行,前者称为熔体纺丝,后者称为溶液纺丝。所以,成纤聚合物必须在熔融时不分解,或能在普通溶剂中溶解形成浓溶液,并具有充分的成纤能力和随后使纤维性能强化的能力,保证最终所得纤维具有一定的良好综合性能。几种主要成纤聚合物的热分解温度和熔点如表1-6所示。
由表1-6可见,聚乙烯、等规聚丙烯、聚己内酰胺和聚对苯二甲酸乙二酯的熔点低于热分解温度,可以进行熔体纺丝;聚丙烯腈、聚氯乙烯和聚乙烯醇的熔点与热分解温度接近,甚至高于热分解温度,而纤维素及其衍生物则观察不到熔点,像这类成纤聚合物只能采用溶液纺丝方法成形。
表1-6 几种主要成纤聚合物的热分解温度和熔点
2.原料制备
再生纤维的原料制备过程,是将天然高分子化合物经一系列化学处理和机械加工,除去杂质,并使其具有能满足再生纤维生产的物理和化学性能。例如,粘胶纤维的基本原料是浆粕(纤维素),它是将棉短绒或木材等富含纤维素的物质,经备料、蒸煮、精选、脱水和烘干等一系列工序制备而成的。
合成纤维的原料制备过程,是将有关单体通过一系列化学反应聚合成具有一定官能团、一定相对分子质量和相对分子质量分布的线型聚合物。由于聚合方法和聚合物性质不同,合成的聚合物可能是熔体状态或溶液状态。将聚合物熔体直接送去纺丝,这种方法称为直接纺丝法;也可将聚合得到的聚合物熔体经铸带、切粒等工序制成“切片”,再以切片为原料,加热熔融成熔体进行纺丝,这种方法称为切片纺丝法。直接纺丝法和切片纺丝法在工业生产中都有应用。溶液纺丝也有两种方法,将聚合后的聚合物溶液直接送去纺丝,这种方法称一步法;先将聚合得到的溶液分离制成颗粒状或粉末状的成纤聚合物,然后溶解制成纺丝溶液,这种方法称为二步法。
在化学纤维原料制备过程中,可采用共聚、共混、接枝和加添加剂等方法,生产某些改性化学纤维。
二、熔体或溶液的制备
1.纺丝熔体的制备
切片纺丝法需要在纺丝前将切片干燥,然后加热至熔点以上、热分解温度以下,将切片制成纺丝熔体。
(1)切片干燥:经铸带和切粒后得到的成纤聚合物切片在熔融之前,必须先进行干燥。切片干燥的目的是除去水分,提高聚合物的结晶度与软化点。
切片中含有水分会给最终纤维的质量带来不利影响。因为在切片熔融过程中,聚合物在高温下易发生热裂解、热氧化裂解和水解反应,使聚合物相对分子质量明显下降,大大降低所得纤维的质量。另外,熔体中的水分汽化,会使纺丝断头率增加,严重时使纺丝无法正常进行。在涤纶和锦纶的生产中必须对切片进行干燥。干燥后切片的含水率,视纤维品种而异。例如,对于聚酰胺6切片,要求干燥后含水率一般低于0.05%;对于聚酯切片,由于在高温下聚酯中的酯键极易水解,故对干燥后切片含水率要求更为严格,一般应低于0.01%;对于聚丙烯切片,由于其本身不吸湿,回潮率为零,所以不需干燥。
切片干燥的同时,也使聚合物的结晶度和软化点提高,这样的切片在输送过程中不易因碎裂而产生粉末,也可避免在螺杆挤出机中过早地软化黏结而产生“环结阻料”现象。
(2)切片的熔融:它是在螺杆挤出机中完成的。切片自料斗进入螺杆,随着螺杆的转动被强制向前推进,同时螺杆套筒外的加热装置将切片加热熔融,熔体以一定的压力被挤出而输送至纺丝箱体中进行纺丝。
与切片纺丝相比,直接纺丝法省去了铸带、切粒、干燥切片及再熔融等工序,这样可大大简化生产流程,减少车间面积,节省投资,且有利于提高劳动生产效率和降低成本。但是,利用聚合后的聚合物熔体进行直接纺丝,对于某些聚合过程(如己内酰胺的聚合)留存在熔体中的一些单体和低聚物难以去除,这不仅影响纤维质量,而且恶化纺丝条件,使生产线的工艺控制也比较复杂。因此,对产品质量要求比较高的品种,一般采用切片纺丝法。
切片纺丝法的工序较多,但具有较强的灵活性,产品质量也较高,另外还可以使切片进行固相聚合,进一步提高聚合物的相对分子质量,生产高黏度切片,以制取高强度的纤维。目前,对于生产产品质量要求较高的帘子线或长丝以及不具备聚合生产能力的企业,大多采用切片纺丝法。
2.纺丝溶液的制备
目前,在采用溶液纺丝法生产的主要化学纤维品种中,只有腈纶既可采用一步法又可采用二步法纺丝,其他品种的成纤聚合物无法采用一步法生产工艺。虽然采用一步法省去了聚合物的分离、干燥和溶解等工序,可简化工艺流程,提高劳动生产率,但制得的纤维质量不稳定。
采用二步法时,需要选择合适的溶剂将成纤聚合物溶解,所得溶液在送去纺丝之前还要经过混合、过滤和脱泡等工序,这些工序总称为纺前准备。
(1)成纤聚合物的溶解:线型聚合物的溶解过程是先溶胀后溶解,即溶剂先向聚合物内部渗入,聚合物的体积不断增大,大分子之间的距离增加,最后大分子以分离的状态进入溶剂,从而完成溶解过程。
用于制备纺丝溶液的溶剂必须满足下列要求:
①在适宜温度下具有良好的溶解性能,并能使所得聚合物溶液在尽可能高的浓度下具有较低的黏度;
②沸点不宜太低,也不宜过高。如沸点太低,溶剂挥发性太强,会增加溶剂损耗并恶化劳动条件;沸点太高,不易进行干法纺丝,且溶剂回收工艺比较复杂;
③有足够的热稳定性和化学稳定性,并易于回收;
④应尽量无毒和无腐蚀性,并不会引起聚合物分解或发生其他化学变化。
合成纤维生产中常用的纺丝溶剂如表1-7所示。
在纤维素纤维生产中,由于纤维素不溶于普通溶剂,所以,通常是将其转变成衍生物(纤维素黄原酸酯、纤维素醋酸酯等)之后,再溶解制成纺丝溶液,进行纺丝成形及后加工。采用新溶剂(N-甲基吗啉-N-氧化物)纺丝工艺时,纤维素可直接溶解在溶剂中制成纺丝溶液。
纺丝溶液的浓度根据纤维品种和纺丝方法的不同而异。通常,用于湿法纺丝的纺丝溶液浓度为12%~25%;用于干法纺丝的纺丝溶液浓度则高一些,一般为25%~35%。
表1-7 合成纤维生产中常用的纺丝溶剂
(2)纺丝溶液的混合、过滤和脱泡:
①混合的目的是使各批纺丝溶液的性质(主要是浓度和黏度)均匀一致。
②过滤的目的是除去杂质和未溶解的高分子化合物。纺丝溶液的过滤一般采用板框式压滤机,过滤材料选用能承受一定压力、具有一定紧密度的各种织物,一般要连续进行2~4道过滤。后一道过滤所用滤材应比前一道的更致密,这样才能达到应有的效果。
图1-3 熔体纺丝示意图
1—螺杆挤出机 2—喷丝板 3—吹风窗 4—纺丝甬道 5—给油盘 6—导丝盘 7—卷绕装置
③脱泡是为了除去留存在纺丝溶液中的气泡。这些气泡会在纺丝过程中造成断头、毛丝和气泡丝而降低纤维质量,甚至使纺丝无法正常进行。脱泡过程可在常压或真空状态下进行。在常压下静置脱泡,因气泡较小,气泡上升速度很慢,脱泡时间很长;在真空状态下脱泡,真空度越高,液面上压力越小,气泡会迅速胀大,脱泡速度可大大加快。
三、化学纤维的纺丝成形
将成纤聚合物熔体或浓溶液,用纺丝泵(或称计量泵)连续、
定量且均匀地从喷丝头(或喷丝板)的毛细孔中挤出,成为液态细流,再在空气、水或特定凝固浴中固化成为初生纤维的过程,称作“纤维成形”,或称“纺丝”,这是化学纤维生产过程的核心工序。调节纺丝工艺条件,可以改变纤维的结构和力学性能。
化学纤维的纺丝方法主要有两大类:熔体纺丝法和溶液纺丝法。在溶液纺丝法中,根据凝固方式不同又可分为湿法纺丝和干法纺丝。化学纤维生产绝大部分采用上述三种纺丝方法。此外,还有一些特殊的纺丝方法,如乳液纺丝、悬浮纺丝、干湿法纺丝、冻胶纺丝、液晶纺丝、相分离纺丝和反应纺丝法等,用这些方法生产的纤维量很少。下面着重介绍三种常用的纺丝方法。
1.熔体纺丝
熔体纺丝是切片在螺杆挤出机中熔融后或由连续聚合制成的熔体,送至纺丝箱中的各个纺丝部位,再经纺丝泵定量压送至纺丝组件,过滤后从喷丝板的毛细孔中压出而成为细流,并在纺丝甬道中冷却成形的工艺过程。初生纤维被卷绕成一定形状的卷装(对于长丝)或均匀落入盛丝桶中(对于短纤维)。图1-3为熔体纺丝示意图。
由于熔体细流在空气介质中冷却,传热和丝条固化速度快,而丝条运动所受阻力很小,所以熔体纺丝的纺丝速度要比湿法纺丝高得多,目前熔体纺丝一般纺速为1000~3500m/min或更高。为加速冷却固化过程,一般在熔体细流离开喷丝板后与丝条垂直的方向进行冷却吹风,吹风形式有侧吹和环吹等,吹风窗的高度一般在1m左右。纺丝甬道的长短视纺丝设备和厂房楼层的高度而定,一般为3~5m。
2.湿法纺丝
湿法纺丝是纺丝溶液经混合、过滤和脱泡等纺前准备后,送至纺丝机,通过纺丝泵计量,经烛形过滤器、鹅颈管进入喷丝头(帽),从喷丝头毛细孔中挤出的溶液细流进入凝固浴,溶液细流中的溶剂向凝固浴扩散,浴中的凝固剂向细流内部扩散,于是聚合物在凝固浴中析出,形成初生纤维的工艺过程。湿法纺丝中的扩散和凝固不仅是一般的物理及化学过程,对某些化学纤维如粘胶纤维同时还发生化学变化,所以,湿法纺丝的成形过程比较复杂。受溶剂和凝固剂的双扩散、凝固浴的流体阻力等因素限制,纺丝速度比熔体纺丝低得多。图1-4为湿法纺丝示意图。
图1-4 湿法纺丝示意图
1—喷丝头 2—凝固浴 3—导丝盘 4—卷绕装置
图1-5 干法纺丝示意图
采用湿法纺丝时,必须配备凝固浴的配制、循环及回收设备,工艺流程复杂,厂房建筑和设备投资费用都较大,纺丝速度低,成本高且对环境污染较严重。目前,腈纶、维纶、氯纶、粘胶纤维以及某些由刚性大分子构成的成纤聚合物都需要采用湿法纺丝。
3.干法纺丝
干法纺丝是从喷丝头毛细孔中挤出的纺丝溶液不进入凝固浴,而进入纺丝甬道;通过甬道中热空气的作用,使溶液细流中的溶剂快速挥发,并被热空气流带走;溶液细流在逐渐脱去溶剂的同时发生浓缩和固化,并在卷绕张力的作用下伸长变细而成为初生纤维的工艺过程。图1-5为干法纺丝示意图。
采用干法纺丝时,首要的问题是选择溶剂,因为纺丝速度主要取决于溶剂的挥发速度。所以选择的溶剂应使溶液中聚合物的浓度尽可能高,而溶剂的沸点和蒸发潜热应尽可能低,这样就可减少在纺丝溶液转化为纤维过程中所需挥发的溶剂量,降低热能消耗,并提高纺丝速度。除技术经济要求外,还应考虑溶剂的可燃性,以保证达到安全防护要求。最常用的干法纺丝溶剂为丙酮、二甲基甲酰胺等。
目前,干法纺丝速度一般为200~500m/min,高者可达1000~1500m/min,但受溶剂挥发速度的限制,纺速还是比熔体纺丝低,而且还需要设置溶剂回收等工序,故辅助设备比熔体纺丝多。干法纺丝一般适宜纺制化学纤维长丝,主要生产品种有腈纶、醋酯纤维、氯纶和氨纶等。
四、化学纤维的后加工
纺丝成形后得到的初生纤维其结构还不完善,力学性能较差,如断裂伸长率过大、断裂强度过低、尺寸稳定性差,不能直接用于纺织加工,必须经过一系列的后加工。后加工随化纤的品种、纺丝方法和产品要求而异,其中主要的工序是拉伸和热定型。
1.拉伸
拉伸的目的是提高纤维的断裂强度,降低断裂伸长率,提高耐磨性和对各种形变的疲劳强度。拉伸的方式有多种,按拉伸次数分,有一道拉伸和多道拉伸;按拉伸介质分,有干拉伸、蒸汽拉伸和湿拉伸,相应拉伸介质分别是空气、水蒸气和水浴、油浴或其他溶液;按拉伸温度又可分为冷拉伸和热拉伸。总拉伸倍数是各道拉伸倍数的乘积,一般熔体纺丝纤维的总拉伸倍数为3.0~7.0倍;湿法纺丝纤维可达8~12倍;生产高强度纤维时,拉伸倍数更高,甚至高达数十倍。
2.热定型
热定型的目的是消除纤维的内应力,提高纤维的尺寸稳定性,并且进一步改善其力学性能。热定型可以在张力下进行,也可以在无张力下进行,前者称为紧张热定型,后者称为松弛热定型。热定型的方式和工艺条件不同,所得纤维的结构和性能也不同。
3.上油
在化学纤维生产过程中,无论是纺丝还是后加工都需进行上油。上油的目的是提高纤维的平滑性,柔软性和抱合力,减少摩擦和静电的产生,改善化学纤维的纺织加工性能。上油的形式有:油槽或油辊上油及油嘴喷油。不同品种和规格的纤维需采用不同的专用油剂。
除上述工序外,在用溶液纺丝法生产纤维和用直接纺丝法生产锦纶的后处理过程中,都要有水洗工序,以除去附着在纤维上的凝固剂和溶剂或混在纤维中的单体及低聚物。在粘胶纤维的后处理工序中,还需设脱硫、漂白和酸洗工序。在生产短纤维时,需要进行卷曲和切断。在生产长丝时,需要进行加捻和络筒。加捻的目的是使复丝中各根单纤维紧密地抱合,避免在纺织加工时发生断头或紊乱现象,并使纤维的断裂强度提高。络筒是将丝筒或丝饼退绕至锥形纸管上,形成双斜面宝塔形筒装,以便运输和纺织加工。生产强力丝时,需要进行变形加工。生产网络丝时,在长丝后加工设备上加装网络喷嘴,经喷射气流的作用,单丝相互缠结呈周期性网络点。网络加工可改进合成纤维长丝的极光效应和蜡状感,又可提高其纺织加工性能,免去上浆、退浆,代替加捻或并捻。为赋予纤维某些特殊性能,还可以在后加工中进行某些特殊处理,如提高纤维的抗皱性、耐热水性和阻燃性等。
随着合成纤维生产技术的发展,纺丝和后加工技术已从间歇式的多道工序发展为连续、高速一步法的联合工艺,如聚酯全拉伸丝(FDY)可在纺丝—牵伸联合机上生产,而利用超高速纺丝(纺丝速度5500m/min以上)生产的全取向丝(FOY),则不需进行后加工便可直接用作纺织原料。