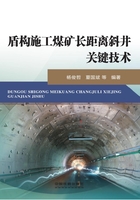
1.2 国内外盾构技术发展现状
1.2.1 国外盾构(TBM)技术现状
自20世纪50年代美国罗宾斯公司研制出第一台真正具有实用价值、能够可靠完成对岩石地层隧道掘进任务的盾构产品以来,全世界盾构隧道施工总里程累计已经超过10000km,盾构施工工法已经成为世界上大中型硬岩隧道工程的首选工法。盾构产品设计与施工技术主要集中在日本、德国、美国和法国等国家的隧道施工装备企业,其中以日本三菱、德国海瑞克、美国罗宾斯、德国维尔特和加拿大挪瓦特最为突出,日系盾构主要突出的是产品类型的多样性、地质适应性和经济性,而欧系或美系盾构主要突出的是产品的安全性和可靠性高。盾构设计直径大多为6~10m,最大设计直径已达14m,盾构类型已由最初的敞开式发展为以敞开式和护盾式盾构为主的结构类型。随着新材料技术、液压技术、电机变频驱动技术、PLC控制技术、现场总线技术、信号传感技术、激光制导技术等不断应用到盾构产品上,现代盾构已经成为世界上大型工程施工先进成套装备的典型产品之一,已经完成的重大隧道工程有美国芝加哥蓄水工程隧道(隧长211km)、英吉利海峡隧道工程(隧长151km)、南非莱索托引水隧道工程(隧长45km)等,其施工规模和难度均体现出盾构隧道工程的最高技术水平。
自19世纪20年代开始,盾构由最初的手掘式、半机械式开挖发展到现如今的机械式、自动化开挖,开挖断面也呈现出圆形、双圆形及矩形等多种形式。1967年,日本人应用英国人提出的泥水加压系统成功研制出第一台功能较完善的泥水平衡盾构,1974年,日本人又成功研制出符合现代施工要求的土压平衡盾构,之后,土压平衡盾构技术得到飞速发展,成功应用于各种地铁隧道、公路隧道、市政管道工程等。同时,伴随着控制技术、液压驱动技术、测控技术、高压密封技术、耐磨材料制备技术等相继出现实质性进展,土压平衡盾构的制造与应用技术不断提升,以日本和德国企业最突出,盾构最大直径超过17m(工程在美国,盾构制造商在日本),已成为全球地质适应能力最强的全断面隧道掘进机的首选工法和设备。
由于工程地质的复杂性和多变性,为了提高单台设备适应具有复杂地质情况的隧道工程,特别是特长重大隧道工程的应对能力,降低施工风险,国外企业如日本的川琦重工、奥村等、德国的海瑞克、法国的NFM等企业相继研制了土压平衡与泥水平衡、土压平衡与盾构相结合的双模式盾构(掘进机)产品,在盾构(掘进机)施工过程中可根据不同区段的工程地质条件采用相对应的掘进模式,并能够实现硐内模式转换,主要应用工程有巴塞罗那地铁9号线(NFM,土压平衡+泥水平衡)、香港地铁九龙南线工程(海瑞克,泥水平衡+盾构)以及南京机场轻轨工程(奥村,土压平衡+盾构)(图1.1和图1.2),但由于双模式全断面掘进机制造工艺复杂、设备成本较高且特定工程地质的施工效果较单模式掘进机差,尚未得到广泛应用。

图1.1 NFM双模式盾构

图1.2 奥村双模式盾构
1.2.2 国内盾构(TBM)技术现状
我国自主研制盾构设备大致经历了三个阶段,第一阶段为20世纪60年代中期到70年代中期,属于盾构研制的起步阶段。由原水电部上海水工机械厂与原北京水电学院联合攻关,设计生产出我国第一台直径为3.4m的盾构,并在杭州人防隧道工程中进行了工程试验,初步掌握了盾构基本设计理论和技术。第二阶段为20世纪70年代中期到80年代末期,属于盾构研制的实用性阶段。先后由煤科院上海分院联合上海重型机械厂以及原水利部杭州机械设计研究院联合上海水工机械厂研制出直径3~5m左右的盾构产品10余台,并陆续投入到河北引滦、福建龙门滩、青岛引黄济青等隧道建设工程,取得了一定的工程业绩,但在设备可靠性、设备寿命、掘进速度等方面远远落后于国外同类型产品。第三阶段为20世纪90年代至今,属于联合制造阶段。为了满足我国重大隧道工程施工需要,国家陆续引进国外先进的盾构产品,国内多家企业分别与国外著名盾构制造商合作,在我国国内联合制造盾构,其中包括美国罗宾斯公司分别与上海隧道股份、中国二重、大连重工,法国NFM公司与上海重型机械厂(现中国北方重工已经收购法国NFM公司)、德国海瑞克与广州重工等,完成了用于我国隧道工程的盾构产品总计20余台套,使我国部分企业初步掌握了高水平盾构产品组装和施工技术,但受制于国外企业对盾构核心技术的垄断和我国本身基础工业的相对薄弱,特别是在刀盘刀具(尤其是大直径滚刀)、高性能耐磨材料、主轴承、密封技术、高精度液压元件等关键零部件领域仍主要依靠进口。随着我国多项重大盾构隧道工程的完成,如秦岭隧道、中天山隧道、大伙房水库输水工程隧道、桃花铺铁路隧道、万家寨引黄隧道等,国内施工企业在盾构施工工法领域已经达到世界先进水平,加上我国逐步掌握并完善土压平衡盾构与泥水平衡盾构核心技术、基础工业的逐步提升以及国家政策的大力扶持,我国自主研制的高性能盾构产品已经具备较好的基础。
在土压平衡盾构方面,自20世纪90年代初开始,我国从工程总体外包、盾构整机进口加参与施工、技术引进/合作制造加自主独立施工逐步走到现如今的设备自主研制加完全自主施工及技术加设备出口阶段,实现了一个个重大跨越。特别是近3年来,通过原始创新、集成创新等手段,国内自主品牌的土压平衡盾构产品国内市场占有率超70%,涌现出了以上海隧道、中铁装备、铁建重工、沈阳重工等为代表的盾构研制企业,掌握了盾构总体设计、复合式刀盘研制、大功率驱动系统设计、液压传动与控制系统集成、密封系统集成等多项关键技术(图1.3),完全摆脱了国外盾构整机企业长期以来的技术垄断和市场垄断,部分国内企业的盾构产品也逐步进入新加坡、马来西亚等东南亚国家市场。

图1.3 盾构国产化
在双模式盾构方面,随着隧道工程领域的不断扩大,为了满足部分特殊工程的建设需要,在引进吸收国外先进技术及自主掌握的部分关键技术的基础上,结合特定工程实际特点和要求,创新盾构设计方法,国内企业也逐步尝试着研制双模式盾构产品,如广东华隧通过引进日本技术,合作研制完成了双模式盾构(土压平衡+泥水平衡,盾构开挖直径6.8m),应用于广州地铁9号线的隧道工程施工。
盾构集开挖、支护和出渣运输工序于一体,可有效实现长大隧道施工的工厂化作业,是世界上先进的大型综合性地下隧道施工设备,代表着国际地下工程技术的最高水平,已广泛应用于交通、水电、市政、国防等工程领域,但盾构施工煤矿斜井国内尚无先例。
1.2.3 盾构(TBM)法斜井施工案例
目前,国外盾构(TBM)法施工大角度隧道(斜井)有一些相关案例,其中典型案例见表1.1。从国外典型案例来看,虽然有较大纵坡的斜井案例,如最大坡度向上45°(100%)等,但从其工程技术来看,大坡度条件下隧道长度较短,检索的39个案例中长度超过2km的仅3例,还没有超过4000m的工程案例,且实例均硐径小,地质条件好,采用全敞开式盾构施工,技术难度较小。国内盾构(TBM)法施工隧道的最大坡度为5.5%,见表1.2。
表1.1 国外大坡度隧道施工实例

续上表

表1.2 国内大坡度隧道工程实例

国外盾构施工煤矿斜井的实例相对较少,美国采用盾构法完成了西桑长度为945m,硐径3.05m,坡度为14°的某矿井施工。联邦德国20世纪70年代初,采用2级联合盾构掘进法先开挖3.0m直径导硐、后扩孔至5.3m直径,完成长1550m的采煤巷道施工。加拿大布雷顿角发展公司1984年采用全断面护盾式盾构,以0~20%的不同坡度掘进,完成直径7.6m、长度达3.5km的煤矿斜井的掘进和支护。澳大利亚Anglo-American煤矿两条通往新的矿层的采矿通道,采用一台直径为8.0m的罗宾斯双模式掘进机进行施工,每条倾斜隧道300m左右,坡度分别为16.67%和12.5% 。
盾构施工煤矿斜井在国内鲜有报道,国外斜井长度最长不超过3500m,断面在35m2以内,斜井穿过地层条件相对简单。总体上国内外学者虽然对煤矿斜井采用盾构(TBM)法施工进行了初步研究,也有相关的工程实践,但斜井长度、断面都是有限的,还未形成理论体系及成熟的配套施工技术。对于长度超过3500m,倾角6°,掘进断面为45m2左右,地层条件复杂的煤矿斜井,采用盾构法施工还需进行深入研究和探索,以便满足现代化矿井建设的需要。