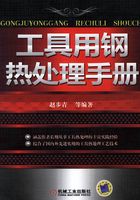
3.6 以渗硼为主的共渗及复合渗
为了提高工模具渗层的综合性能,同一工序同时渗入两种或多种元素的处理称为共渗;不同工序分别依次渗入两种或多种元素的处理称为复合渗。
3.6.1 硼氮共渗
为了提高工模具的寿命,国内有些单位对模具进行了硼氮共渗。共渗后的模具既具有渗硼层的高硬度、高耐磨性和高耐热性,同时渗层又有较小的脆性,从而提高了过渡层的强韧性,而且渗层较单独渗硼层更深,具有更高的压应力和更高的断裂强度、塑性和韧性。
工艺1:
(1)渗剂 工业纯高硼铁、尿素、SiC、氟硼酸钾等。
(2)设备 共渗容器可用低碳钢或不锈钢焊制,可在电阻炉中进行。
(3)工艺3Cr2W8V钢热锻模的共渗工艺为:570℃×3h+900℃×5h。共渗后升温至1050℃,保温2h,油淬,550~650℃×2h×3次回火。共渗温度分别为850℃、900℃和950℃,时间均为4h,渗层的厚度分别为0.0435mm、0.0497mm、0.0750mm。
共渗后的硼化物硬度为1400~1800HV,其表面层组织主要是Fe2B相,过渡层是碳的富集区,主要是Fe3C;氮的富集区主要是Fe3 N。经硼氮共渗的3Cr2W8V模具(热冲头)的寿命有较大的提高。
工艺2:
(1)配方(质量分数)5%B4C+5%KBF4+1%活性炭+0.5%NH4Cl+5%(NH2)2CO,SiC余量。
(2)工艺 将工件清洗干净,烘干,装入共渗箱内。1Cr18Ni9Ti钢模具经580℃×3h+900℃×8h,炉冷至400℃出炉空冷。
(3)结果 模具表面显微硬度为1553~1980HV,共渗层厚度为0.05~0.08mm,表面组织为FeB+Fe2B,次层为Fe2B+α-Fe,第三层为Fe2B+α-Fe+γ-Fe。
经硼氮共渗处理的1Cr18Ni9Ti钢模具使用寿命提高1.5~2倍。
3.6.2 硼铝共渗
硼铝共渗层比单独渗硼层具有更好的耐磨、耐热和耐蚀性,可用于热作模具。常用硼铝共渗工艺见表3-29。
表3-29 常用硼铝共渗工艺
(续)
3.6.3 硼硅共渗
硼硅共渗可提高钢的抗氧化和耐蚀性。可采用固体粉末法、熔盐法和电解法。渗剂中硼、硅含量不同,所获得的渗层相组成也不同。共渗剂中硼、硅含量对渗层组织的影响如表3-30所示。表3-31为硼硅共渗粉末渗剂成分及共渗工艺。
表3-30 共渗剂中硼、硅含量对渗层组织的影响
表3-31 硼硅共渗粉末渗剂成分及共渗工艺
20钢电解硼硅共渗还能提高在w(NaCl)13%、w(HCl)10%、w(H2SO4)10%水溶液中的耐蚀性,见表3-32。
表3-32 20钢电解硼硅共渗工艺与耐蚀性
(续)
3.6.4 硼锆共渗
为了改善渗硼层的脆性,并提高抗动载能力,已开发出硼锆共渗工艺。硼锆共渗是在渗硼剂中添加供锆剂进行硼锆共渗,采用膏剂法950℃×2~10h工艺,可获得0.04~0.10mm的共渗层。共渗剂组成(质量分数%)如下:
1)45%~60%B4C+5%~10%B2Zr+5%~10%NaF+铁屑。
2)50%~55%B4C+4%~7%硼酐+3%~4%Cu+2%~4%Zr+3%~6%NaF+SiO2(余量)。其中NaF是活化剂,铁屑在加热时氧化成氧化铁而成为惰性填充剂,有防止粘结的作用。
硼锆共渗层与渗硼层没有明显的区别,渗层内除FeB、Fe2B外,还有硼化锆(ZrB2)和碳化锆(ZrC)。硼锆共渗的工件具有较高的耐磨性,在动载荷下的耐磨性高于渗硼的工件。经硼锆共渗的工模具在某些介质中具有较高的耐蚀性,在盐酸水溶液中,其化学稳定性比渗硼钢高。
3.6.5 硼碳复合渗
美国专利提出,在重载荷下工作的要求非常耐磨的零件,如地质钻机钻头轴承,对其进行硼碳复合渗,耐磨性可与钨钴系钴基硬质合金在轴承枢轴的槽底内沉积相媲美。其工艺路线为:先在轴承枢轴表面进行气体渗碳(渗层深度为1.52mm),再经渗硼(渗层深度为0.103mm)、淬火、回火。
硼碳复合渗(先渗碳后渗硼)用于既要求高的接触疲劳强度、又要求高的耐磨性的牙轮钻头(轴颈部分)等工件。
滚子接触疲劳试验表明,20CrMnTi钢硼碳复合渗后,接触疲劳强度高于单一渗碳处理。在MM200磨损试验机上进行滚动摩擦试验,20CrMnTi钢经硼碳复合渗的耐磨性比单纯的渗碳处理高1.5倍以上,而且在较高载荷、较高滑动速度下,不会出现咬合现象。
3.6.6 硼和其他元素共渗
(1)硼钒共渗 硼钒共渗既能提高渗层硬度、耐磨性,又能降低渗硼层引起的脆性。硼钒共渗在硼砂盐浴中进行,不需要添置多少专用设备,工艺简单,操作方便,易于推广。
将硼砂放入坩埚中熔融后,加硼铁粉、钒铁粉,边加边搅拌,待炉温达到共渗温度(900~1000℃)后放入工件,在盐浴表面覆盖一层木炭。共渗后,将工件取出空冷,煮掉残盐,表面呈深灰色。
低于950℃共渗处理,渗层主要是(Fe、V)2B型化合物,表面硬度为1800~2250HV;共渗温度超过950℃时,渗层的相结构则以V3B2为主,并失去齿状特征,渗层梯度变得平坦,且没有明显的双层现象。表面硬度为2250~2900HV。
(2)硼铬共渗 硼铬共渗采用电解盐浴法。盐浴成分(质量分数):4%~6%氧化铬+18%~23%NaCl+硼砂(余量)。共渗温度为900~1000℃。渗层硬度为1850~2250HV。通过抗弯、耐蚀及热硬性试验表明,与单一渗硼层相比,共渗层具有良好的耐蚀性、热硬性和较低的脆性。
(3)硼铜共渗 渗剂成分(质量分数):92%~97.6%(84%B4C+16%Na2B4O7)+2.4%~8%Cu。共渗工艺为950℃×6h。在共渗过程中铜溶于硼化层,形成以硼化铁为基的固溶体,降低了渗硼层的脆性。渗硼层的硬度相应地降低10%~20%,如45钢硼化层的硬度由1800HV降到1400~1600HV。在有润滑的滑动摩擦条件下,碳钢工件硼铜共渗与单独渗硼耐磨性相同。
(4)硼钼共渗 有时为了提高工模具的耐热性,往往采用硼钼共渗。渗剂成分(质量分数):40%~60%B4C+10%~15%钼粉+4%~6%NaF+氧化铁(余量)。
(5)硼钛共渗 共渗方法有粉末法和电解法。粉末法可用以碳化硼和钛铁(或纯钛)为基的粉末介质,由碳化硼、钛铁(47%Ti)、硼砂、氯化铵和氯化钠等组成,见表3-33。电解法共渗在Na2B4O7-TiO2熔盐中进行,温度为950~1050℃,电流密度为0.2~0.4A/cm2。
硼钛共渗层具有较高的耐磨性。在旋转拉丝机的加热元件喷嘴上渗B或B-Cr、B-Al和B-Ti共渗等渗层的对比试验中,B-Ti渗层耐磨性最高。
表3-33 硼钛共渗介质成分(质量分数)(%)