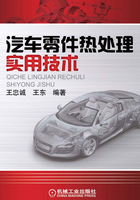
3.3气门传动组零件的热处理
3.3.1凸轮轴
1.工作条件与技术要求
凸轮轴是发动机配气系统中的重要部件,凸轮轴的旋转是依靠曲轴带动的,用来保证各个气缸内进、排气门按一定的时间正常开启和关闭,保证发动机充分换气,使进、排气门持久地确保燃烧室的密封性,确保发动机具有良好的可持续性和动力性。另外凸轮轴还要用来驱动燃烧系统等零件。在低应力作用下凸轮轴与气门阀杆、挺杆构成摩擦副,在工作过程中承受连杆周期性挤压应力的作用,同时还受到一定的弯曲和转矩的作用,此外又要承受与挺杆相接触产生的滑动及滚动摩擦的作用以及周期性的冲击载荷。图3-32所示为凸轮轴与凸轮形状。凸轮轴的主要损坏形式为接触疲劳破坏(粘着磨损,即擦伤)、凸轮磨损、表面压应力反复作用造成麻点和块状剥落等。因此要求凸轮轴必须具有以下特性:良好的接触疲劳强度和抗擦伤性;高硬度和较好的耐磨性;接触表面具有足够的强度和刚性,可承受气门开启的周期性冲击载荷的作用。
2.材料的选用
凸轮轴的材料要根据气门挺杆的材料而定,二者的材料要相匹配,同时要考虑到设计和使用的要求,影响凸轮轴选用材料的因素有:在发动机中的工作条件和使用工作状况;凸轮轴与挺杆间的最大接触应力、相对滑动速度、润滑条件;匹配挺杆材料、硬度以及表面状态等。根据凸轮轴的工作条件,符合要求的材料有钢和铸铁,根据钢的加工方法可分为感应淬火钢、渗碳钢、渗氮钢(或氮碳共渗钢);铸铁分为冷激铸铁、可淬硬铸铁、感应淬火球墨铸铁、氩弧重熔铸铁等,制造凸轮轴的材料及热处理工艺见表3-23。
图3-32 某凸轮轴与凸轮形状
a)凸轮轴 b)凸轮剖面及硬化层分布
表3-23制造凸轮轴的材料及热处理工艺
一般凸轮轴采用渗碳钢和中碳钢制造,高功率的高速发动机凸轮轴采用镍铬钼(或铝)合金铸铁、铜钒钼合金铸铁制造。合金铸铁的弹性模量比中碳钢和球墨铸铁的低,故能够减小接触压力和保持表面的润滑油膜,铸铁中加入合金元素可明显提高铸铁的力学性能或物理化学性能,如铬、铜、镍、钼和钒等显著改变铸铁的耐磨性,铬、铜、镍、磷和硅能提高铸铁的耐蚀性,同时铬、镍、钼、硅等元素增强了耐热性。通常用45钢(最佳碳质量分数0.40%~0.47%可保证合适的淬透性)、50Mn2钢等制作凸轮轴,具有工艺简单、制造成本低等特点,其毛坯晶粒度控制在6~8级,获得的各项技术指标完全符合要求。部分凸轮轴用铸铁及其性能要求见表3-24。
表3-24部分凸轮轴用铸铁及其性能要求
冷激铸铁通常不需要热处理,其表面存在软硬相间的复相组织,使其有很高的硬度和低的摩擦因数,不会发生粘着现象。因此具有最优良的抗擦伤性能、较好的抗点蚀剥落性和较高的耐磨性,该类铸铁一般含碳量高,以保证冷激层的硬度和碳化物的含量。凸轮轴常用合金铸铁和冷激铸铁的化学成分见表3-25和表3-26。
表3-25凸轮轴常用合金铸铁的化学成分
表3-26凸轮轴常用冷激铸铁的化学成分
合金铸铁的加工工艺流程为铸造→去应力退火(590℃×5h加热后炉冷至200℃出炉空冷)→机械加工→等温淬火(870℃加热,在240~300℃硝盐浴中冷却60min后提出空冷)→回火(590℃×5h),其组织由珠光体+少量铁素体变为回火索氏体。
3.凸轮轴的热处理
(1)技术要求 根据材料的不同,其技术要求存在差异,具体如下:
1)低碳钢化学热处理的技术要求为渗碳处理后渗碳层深1.5~2mm,凸轮、支承轴径和偏心轮的表面硬度为55~63HRC,齿轮的硬度为45~58HRC;凸轮轴进行氮碳共渗处理,可明显提高抗擦伤能力和防止出现热咬合的能力,其耐磨性为中碳钢淬火后的两倍。
2)45钢凸轮轴的技术要求为凸轮、支承轴径和偏心轮的表面硬度为55~63HRC,硬化层深2~5mm,齿轮的硬度为45~58HRC,硬化层深2~5mm。
3)合金铸铁凸轮轴的技术要求为凸轮、支承轴径和偏心轮的表面硬度为48~58HRC,硬化层深2~5mm,齿轮的硬度为45~58HRC,硬化层深2~5mm。采用感应加热可提高凸轮轴的强度和耐磨性,确保其在工作过程中具有高的疲劳强度和使用寿命。
(2)热处理工艺参数 对渗碳钢和中碳钢而言,在最终的热处理前要对凸轮轴进行调质处理或正火处理,以获得均匀细化的索氏体组织,确保基体有足够的强度和良好的韧性来满足凸轮轴的工作需要。
1)凸轮轴的感应热处理工艺是广泛采用的,一般汽车、拖拉机等内燃机凸轮轴大多采用感应加热完成表面的热处理,可提高凸轮轴基体表面的抗拉强度、硬度、耐磨性和疲劳极限,而心部仍保持足够的塑性和韧性,根据其结构和技术要求可对凸轮轴的凸轮、支承轴径、偏心轮和齿轮等主要工作表面在精加工前分别进行感应处理。为获得要求的硬度,应选择理想的感应器。感应器一般分为两类:圆形感应器应用于中频感应淬火,使凸轮轴旋转,感应器内径大于支承轴径,间隙较大;仿凸轮轴形感应器是根据高频感应淬火或特殊形状的具体要求而制作的,凸轮与感应器的间隙很小,因此硬度均匀,可根据凸轮轴各部分硬化层的深度来改变仿形形状,该类感应器分为单圈和双圈两种。凸轮轴感应加热用双圈圆形感应器如图3-33所示。另外为了获得凸轮周边均匀的硬化层,可使用分开式感应器。
图3-33 凸轮轴感应加热用双圈圆形感应器
在一根凸轮轴上的若干个凸轮、主轴径、齿轮和偏心轮要进行感应淬火,而它们之间的距离较近,淬火时必然会影响到彼此的硬度,故中频淬火感应器必须有屏蔽装置来进行保护,磁场屏蔽方法有三种。第一种为铜环屏蔽法,在感应器的两侧加上云母片或胶木板,外侧加上铜管或铜板制成的铜环,如图3-34所示。其原理为磁力线穿过铜环时产生感应电流,而感应电流产生的磁力线与有效圈上产生的中频电流产生的磁力线方向相反,故削弱或抵消了逸散的磁力线,使得两侧的凸轮或主轴径的边缘不会被加热。第二种为低碳钢环屏蔽法,与铜环屏蔽法相似,装上低碳钢或工业纯铁制造的环,如图3-35所示。其工作原理为钢环或纯铁环的相对磁导率高于空气,对逸散的磁力线有吸引或约束作用,因此可保护相邻的凸轮或主轴径的边缘免受加热,资料介绍同时采用两种屏蔽方法效果更好。第三种为硅钢片屏蔽法,即在有效圈外侧卡上一圈硅钢片,经过磷化处理后,同样具有良好的屏蔽作用。
图3-34 铜环屏蔽装置示意图
图3-35 钢环屏蔽装置示意图
对于材料为中碳钢的凸轮轴来说,由于感应淬火是易控制、节能、生产率高、产品质量好、便于实现机械化自动化的热处理工艺,因此在实际热处理过程中得到了极为广泛的应用,它避免了使用盐浴炉、电阻炉等时工件必须完全加热的弊端。考虑到6102发动机凸轮轴要求的硬化层深,因此选择中频感应淬火,常用的频率为2500Hz和8000Hz。该凸轮轴的热处理安排在粗磨凸轮、偏心轮之前,在淬火机床上进行中频感应淬火,硬化层深度为2~5mm,淬火后硬度为55~63HRC。需要注意的是感应器的合理设计与淬火质量问题,表3-27为6102发动机凸轮轴(45钢)感应淬火(中频感应淬火)工艺规范。
表3-276102发动机凸轮轴(45钢)感应淬火(中频感应淬火)工艺规范
(续)
电流的频率不同则淬硬层的深度不同,频率越高淬硬层的深度越小,因此在生产过程中应根据零件的具体技术要求和工作状况来确定合理的工艺参数。中碳钢制作的凸轮轴采用中频感应淬火处理是正确的,凸轮轴主要工作表面的中频感应淬火分步进行,首先进行支承轴径和齿轮表面的淬火,最后完成凸轮、偏心轮表面的淬火处理。45钢和合金铸铁凸轮轴表面淬火的工艺参数及质量要求见表3-28。
表3-2845钢和合金铸铁凸轮轴表面淬火的工艺参数及质量要求
2)球墨铸铁凸轮轴的贝氏体等温淬火工艺见表3-29。球墨铸铁凸轮轴一般选用QT600-3,除少数采用中频感应淬火或进行氮碳共渗外,绝大部分凸轮轴在毛坯正火或去应力退火加工后,进行贝氏体的等温淬火处理,获得理想的下贝氏体组织和硬度,使凸轮轴具有良好的综合力学性能。
表3-29球墨铸铁凸轮轴的贝氏体等温淬火工艺
球墨铸铁凸轮轴的热处理工艺包括一般的正火、等温或分级淬火、表面改性处理等,表面热处理和化学热处理与普通的热处理工艺相比,可获得最佳的表面硬化层,提高了凸轮轴的疲劳强度、抗弯强度,并使其具有良好的耐磨性和耐蚀性等,具体见表3-30。当硬度不足则将造成性能和使用寿命的降低,而过厚的硬化层,会增加凸轮轴的脆性和内应力,出现早期的失效和损坏,因此选择合理的工艺方法,对于凸轮轴的寿命有重大的影响。
表3-30球墨铸铁凸轮轴经不同热处理后耐磨性对比
目前对球墨铸铁凸轮轴采用热处理强化和冷加工复合强化新工艺,即球墨铸铁凸轮轴经热处理后再进行滚压处理。如正火+滚压轴颈与曲柄臂过渡圆角处,在表面形成了0.5mm深的冷加工硬化层,增大了残留压应力的作用,提高使用寿命70%以上,效果十分明显,在生产中得到了十分广泛的应用。
凸轮轴在表面处理前要进行正火或调质处理,以使其得到良好的力学性能。为提高凸轮轴的耐磨性和耐蚀性,可对其进行化学热处理(如氮碳共渗等)。图3-36所示为SH760汽车凸轮轴的氮碳共渗工艺曲线,材质为合金铸铁,渗层深0.10~0.15mm,化合物层为4~6μm,硬度在900HV以上,使用寿命可提高三倍以上,在表面形成了CrN、MnN等合金渗氮物。
图3-36 SH760汽车凸轮轴的氮碳共渗工艺曲线
4.凸轮轴热处理工艺分析与操作要点
1)为防止相邻的部位由于磁场逸散发生退火,凸轮轴感应器上设计安装了聚磁装置,用高导磁材料制作,如硅钢片、铁氧体等。为提高生产率,还开发了凸轮轴多部位同时淬火技术。该技术可以同时对一根凸轮轴上的所有淬火部位进行淬火加工,已在东风的EQ491发动机凸轮轴生产线上得到使用。
2)凸轮轴中频感应淬火后利用余热进行自回火,可消除淬火组织应力,在正火+中频感应淬火后,心部为细片状珠光体,硬度为255HBW,心部具有良好的强度和高的韧性。
应确保感应器上直径为1.5~2mm的喷射孔无堵塞,水压符合设计要求,凸轮轴可旋转或静止不动。大批生产时,所有凸轮轴上的各淬火部位应一次同时加热完成,如分段加热则容易出现软点或软带,影响到凸轮轴表面的耐磨性等,对其使用寿命等有直接的影响。
感应淬火后的凸轮轴要立即放进井式回火炉内或硝盐回火炉中,如要采用感应回火或自回火则要掌握好加热的工艺参数,自回火的温度要高于炉内回火50~70℃。
3)球墨铸铁制作的凸轮轴大多进行等温淬火,以获得贝氏体组织,其淬火冷却介质为硝盐浴,由于凸轮轴在盐浴中加热,淬火时带入的氯化盐使硝盐的老化明显加快,因此要定期捞渣和补充新硝盐。
淬火后的零件用煮沸的热水清洗,将凸轮轴上粘附的硝盐清除干净,否则会出现吸潮和表面锈蚀,将直接影响到产品的尺寸和表面质量。
4)中碳钢制作的凸轮轴采用中频感应淬火,凸轮轴主要工作表面的中频感应淬火应分步进行,首先进行支承轴径和齿轮表面的淬火,最后完成凸轮、偏心轮表面的淬火处理,这样可确保热处理后的硬度和组织不受影响。
5)高频感应加热的感应器应根据要求制作,可制成仿形或圆形。其高度比凸轮轴高4~8mm,内径与轴径的间隙为3~4mm;高频加热器上有直径为1.5~2mm的喷射孔,凸轮轴可旋转或静止不动。大批生产时,所有凸轮轴上的各淬火部位是一次同时加热完成的。
6)有资料指出,QT600-3球墨铸铁凸轮轴可采用等温淬火处理(ADI),具有提高韧性,变形小,耐磨性良好等特点,在260~290℃的硝盐浴中进行等温淬火处理后,如果出现淬裂现象,在化学成分合格的前提下,采取确保井式炉温度均匀,将加热炉与等温硝盐浴的温差控制在5~10℃,将等温硝盐槽的温度控制在要求的温度范围内,定期捞硝盐渣与补充新盐等措施,即可使凸轮轴等温淬火裂纹得到有效的控制。
7)凸轮轴感应淬火的质量检验见表3-31。
表3-31凸轮轴感应淬火的质量检验
5.凸轮轴感应淬火的常见缺陷及产生原因和防止方法(表3-32)
表3-32凸轮轴感应淬火的常见缺陷及产生原因和防止方法
(续)
3.3.2气门挺杆
1.工作条件与技术要求
气门挺杆是汽车发动机上的关键部件,气门挺杆在发动机气缸体导管内上下往复运动,将凸轮作用于它的推力传给推杆,以此来传递动力,同时绕自身轴线作旋转运动,它处于凸轮和摇臂之间。在工作过程中与凸轮反复进行高应力的接触,彼此之间的摩擦力较大,挺杆与凸轮接触的端面为内球面,与凸轮相对滑动为点接触,故要承受较大的接触应力作用。挺杆有菌式、筒式和滚轮式三种,其底部分球面和平面两类。对挺杆的技术要求为表面有高的硬度和耐磨性,基体组织具有良好的综合力学性能。
一般气门挺杆的构造如图3-37所示,从图中可以看出,挺杆的下部有油孔,经推杆流入挺杆的机油从油孔流出润滑凸轮和挺杆。其损坏形式为磨损、擦伤和接触疲劳破坏。
从挺杆的工作条件可知,为满足需要挺杆应具有以下力学性能:一定的强度和韧性,表面有高的硬度和良好的耐磨性,高的抗擦伤能力等。
2.材料的选用
从上述挺杆的受力分析可知,气门挺杆与凸轮构成一对摩擦副,合金铸铁制挺杆与凸轮轴之间相互作用,因此必须提高它们的耐磨性和抗擦伤性,经过表面强化处理的合金铸铁挺杆和凸轮轴,耐磨性和抗擦伤性得到提高。凸轮与挺杆组合后,其失效形式多为二者异常磨损,一般为点蚀(Pit-ting)和刮伤(Scuffing)两大类,二者的相互摩擦短时间内会早期的熔化磨损。气门挺杆材料一般选用渗碳钢、中碳钢和铸铁等,气门挺杆与凸轮轴材料的选用见表3-33。凸轮和挺杆产生异常磨损的原因和对策见表3-34。目前世界各国用合金铸铁制作挺杆,并进行淬火处理,在润滑油中加入添加剂可降低表面的磨损。可用磷酸膜或铁氧体(Ferrox)进行表面处理,这种方法对提高早期的磨合性十分有效,从而防止刮伤。
图3-37 气门挺杆的构造
a)菌式 b)筒式 c)滚轮式
表3-33气门挺杆与凸轮轴材料的选用
表3-34凸轮和挺杆产生异常磨损的原因和对策
凸轮和挺杆材料的典型组合实例见表3-35。
表3-35凸轮和挺杆材料的典型组合实例
3.机械加工工艺流程
(1)渗碳钢挺杆 常用渗碳钢主要有15Cr、20Cr、20等,它们正火后具有良好的韧性、强度和理想的金相组织,经渗碳或碳氮共渗处理表面形成高的硬度和耐磨性,而内部有一定的强度和良好的韧性。其流程为:下料→锻造→机械加工成形→渗碳或碳氮共渗→热处理→精加工→表面处理。渗碳层和碳氮渗层深0.6~1.5mm即可满足工作需要,内螺纹应避免渗碳或碳氮共渗,否则螺纹的硬度高、脆性大,会在工作过程中出现早期失效。
(2)中碳钢挺杆 通常选用45钢和45Cr钢,中碳钢经调质处理后,整体形成索氏体组织,具有最佳的综合力学性能,最终热处理方式为高频感应淬火,硬化层深度在2mm以上,硬度大于55HRC。
(3)合金铸铁挺杆 合金铸铁在磨削时会产生表面应力,在机械加工中采用的材质有镍铬钼合金铸铁、铬钼铜合金铸铁等。合金铸铁挺杆有三大类:①整体铸造合金挺杆;②用钢制造杆体,在头部焊上合金铸铁;③单体铸造合金铸铁挺杆头与钢制杆体对焊。
以整体铸造合金铸铁挺杆为例,其加工流程为:铸造→间接端部冷激→机械加工→去应力退火→精加工→表面处理→成品,其硬化层深度应大于2mm。
筒式挺杆的简单工艺流程为:棒料切割→料头淬火→抛丸、磷化、皂化→冷挤压→齐总长和堆焊槽→堆焊合金→回火→磨外圆→磨端面→倒角→磨外圆→精抛球面→磷化→精磨外圆→成品检验。
(4)20钢挤压、堆焊合金 通常采用20钢或25钢进行反挤压成形,其冷挤压工艺流程为:制备毛坯→软化退火→酸洗→磷化、皂化处理→反挤压成形→堆焊合金→抛丸→机械加工等→磷化→成品检验。
4.挺杆的热处理工艺
挺杆和凸轮轴是一对摩擦副,因此两者材料的选用和热处理的要求是相互制约的。在大批生产中,钢制气门挺杆通常通过冷挤压或热镦成形。挺杆和凸轮轴材料的选用与热处理工艺见表3-36,凸轮和挺杆的表面硬度见表3-37。
表3-36挺杆和凸轮轴材料的选用和热处理工艺
表3-37凸轮和挺杆表面硬度
(1)渗碳钢挺杆的热处理 这里以15Cr钢为例,分析其热处理工艺规范和注意事项。
1)挺杆在井式渗碳炉或可控气氛炉内完成渗碳工艺,选择的渗碳温度为900~920℃,所用渗碳剂为煤油,稀释剂为甲醇,具体流量根据渗层厚度、炉膛体积以及装炉量的多少而定,试样抽查合格后,随炉冷却。
2)渗碳后的挺杆需重新进行热处理。目的是使挺杆获得较高的表面硬度、高的接触疲劳强度和耐磨性。为防止挺杆表面出现脱碳现象,热处理的加热是在盐浴炉中进行的,淬火工艺装备具有吊挂式结构,材料为Q235钢,上面焊有许多短柱,将挺杆挂在上面。加热温度为840~850℃,每挂保温8min,在机械油中油冷,淬火后的端面硬度大于62HRC;为了确保硬度符合要求,在硝盐炉中的回火温度为180~200℃,保温90min,硬度为54~62HRC。
挺杆回火后应清洗干净,除净回火粘附的硝盐等,防止其表面锈蚀,影响挺杆的使用性能。该类挺杆的缺点为储油性差和耐磨性较差,容易出现表面擦伤。
渗碳钢经渗碳或碳氮共渗热处理后的金相组织为细针状马氏体组织,不允许有网状游离渗碳体和游离状态的铁素体,从渗层至中心不能有骤然转变的金相组织,挺杆心部为低碳马氏体。
(2)合金铸铁挺杆的热处理 采用合金铸铁制造挺杆,可使基体硬度提高,其使用性能与挺杆的显微组织、表面及心部硬度、表层和次表层的残留应力等有关,当出现网状碳化物时会造成挺杆的早期失效——点蚀剥落和快速磨损等。研究表明,显微组织中回火马氏体基体上分布的针状碳化物以及出现的点状、片状石墨均提高使用性能,表面硬度越高则耐磨性越好。几种常见合金铸铁挺杆的化学成分见表3-38。
表3-38几种常见合金铸铁挺杆的化学成分
(3)冷激合金铸铁挺杆的热处理 冷激铸铁(采用干砂型铸造,端面加冷铁激冷获得的)具有大量的针状碳化物,具有坚固的骨架作用,表面部分珠光体经磨削成微凹坑又起到储油的作用,从而使得其耐磨性、减摩性和储油性较好。经淬火、回火后形成马氏体组织,提高了挺杆的接触应力和挺杆的疲劳性能。冷激合金铸铁的失效形式为疲劳剥落,因此热处理的目的是提高抗擦伤性能,目前挺杆一般使用铬钢或铬镍钼合金铸铁。为了确保挺杆表面无氧化脱碳,使用盐浴炉加热,要严格控制加热温度,确保脱氧彻底。
冷激合金铸铁挺杆的热处理工艺见表3-39。
表3-39冷激合金铸铁挺杆的热处理工艺
(续)
需要注意的是气门挺杆(CA141)采用铬钼铜合金铸铁制造,其工艺为时效处理+淬火处理+磷化处理,时效处理为550℃×3h空冷,淬火处理为840~860℃×0.5h油冷,金相组织为淬火马氏体+少量点状石墨+碳化物,硬度为58~62HRC,提高了挺杆的硬度与耐磨性。
另外为提高使用寿命,在冷激铸铁端面上高频堆焊合金,然后在300℃进行回火处理,其作用为减小加热引起的应力集中,同时不会降低表面的残留压应力,因此使挺杆的使用寿命明显提高。
合金铸铁的铸态金相组织如下:基体为细珠光体,挺杆底部经冷激后工作表面为针状渗碳体、莱氏体和适量石墨。挺杆的热处理工艺参数和技术指标见表3-40。
表3-40挺杆的热处理工艺参数和技术指标
通常挺杆热处理后工作面部分的硬度如下:钢制挺杆和冷激铸铁挺杆渗碳后为58~65HRC,不淬火冷激铸铁挺杆硬度不低于52HRC。而挺杆杆部和底座硬度为:钢制挺杆不低于36HRC,铸铁挺杆为241~285HBW。
根据挺杆的工作特点,既可对其进行整体热处理(盐浴淬火等),也可对其工作面进行高频感应淬火,事实上用这两种方法处理的挺杆存在下列缺陷:裂纹、变形、表面性能不高等。考虑到上述因素,选用火焰淬火可确保产品质量合格和质量稳定,同时降低了生产成本,取得了良好的效果,挺杆的火焰自动淬火设备示意图如图3-38所示,挺杆经振动料斗进入排料槽,由送料机构送入带有旋转机构的孔座内,同时乙炔加热喷嘴对挺杆底面进行加热,加热到设定时间后,挺杆被打料杆弹出滑入油槽冷却,然后进行下一轮循环。
挺杆的材料选用铬钼铜(CrMoCu)冷激合金铸铁,其火焰淬火工艺参数为:加热温度为860~900min,挺杆的转速30~60r/min,在180~200℃回火120min后空冷。
检测结果:硬化层深度大于3mm;冷激层深度大于4mm;挺杆端面的硬度为63~69HRC,杆部硬度为93~104HBW;金相组织要求石墨1~2级,渗碳体1~3级,渗碳体数量1~3级。
图3-38 挺杆的火焰自动淬火设备示意图
1—油槽 2—挺杆 3—乙炔加热喷嘴 4—振动料斗 5—排料槽 6—送料机构 7—旋转打料装置
经机械加工后的挺杆成品工作表面不应有裂纹、蜂窝孔、黑点、刻痕、凹坑等有害缺陷,其非工作表面允许有少量的黑点和加工痕迹等。
对于需要磷化或其他表面处理的挺杆,其底部表面应进行磁粉无损检测,以确保挺杆的内在质量合格,同时也避免了后面工序的无价值的加工。
(4)挺杆的表面处理 在气体或液体介质中进行表面处理后,挺杆表面的硬度提高、耐蚀性增强,端面和内球窝抗冲击性提高,因此其使用寿命得到提高。挺杆的氮碳共渗一般采用液体氮碳共渗工艺,氮碳共渗的技术要求和工艺参数如下:加热温度560~585℃,共渗时间2~3h,氮碳层深≥0.05mm,表面硬度≥850HV0.2,处理后明显提高了挺杆端面和球窝的硬度,延长了挺杆的使用寿命。
1)挺杆的氮碳共渗处理。可进行氮碳共渗处理的气门挺杆材料通常为Cr12W和合金铸铁两种。氮碳共渗的技术要求为:氮碳共渗层深度≥0.05mm,白亮层深度在0.006mm以上,表面硬度在850HV0.2以上,基体硬度≥43HRC,挺杆的氮碳共渗工艺流程参见气门氮碳共渗部分的内容。
图3-39所示为气门挺杆的液体氮碳共渗工艺曲线,图3-40所示为气门挺杆的金相照片,实际测出氮碳共渗层深度为0.06mm,硬度在900HV0.2以上,符合技术要求。从图中可看出白亮层十分明显,因此表面的硬度较高,达到了挺杆表面强化的目的。
图3-41所示为Cr12W钢制挺杆工作面的氮碳共渗腐蚀缺陷,其是由渗氮盐腐蚀产生的,而花斑则为盐渣沉积在工作面上所致,图3-42所示为Cr12W钢制挺杆工作面的抛丸花斑,这是抛丸前表面有水造成的,图3-43所示为Cr12W钢制挺杆工作面的剥落情况,是氧化后激冷所致。
图3-39 气门挺杆液体氮碳共渗工艺曲线
图3-40 气门挺杆氮碳共渗后的金相组织(×600)
图3-41 Cr12W钢制挺杆工作面的氮碳共渗腐蚀缺陷
图3-42 Cr12W钢制挺杆工作面的抛丸花斑
Cr12W钢制挺杆氮碳共渗后开裂。钢制气门挺杆是采用Cr12W钢制造的,其工艺流程为下料→加热→热挤压→球化退火→车加工→磨加工→钻孔→淬火→高温回火→空冷→磨削加工→磁粉无损检测→氮碳共渗→发蓝处理→清洗→抛丸→防锈→磨外圆→研磨球窝→检验→刻字→包装等,在成品检验时发现有部分挺杆出现端面裂纹,甚至为通裂,沿着出油孔开裂,如图3-44与图3-45所示。钢制挺杆的热处理要求为基体硬度≥43HRC,氮碳共渗层深度≥0.033mm,表面硬度在850HV0.2以上,脆性小于2级。
从挺杆裂纹的形态分析,其在氮碳共渗前进行磁粉无损检测,由于Cr12W钢为高合金钢,回火后采用空冷,故排除了热处理过程中出现裂纹的可能性,液体氮碳共渗处理的流程为串筐→清洗→预热→氮碳共渗→发蓝处理→清洗→抛丸→防锈。氮碳共渗后进行发蓝处理,有效减小了内外温差,避免因冷却过于激烈而导致开裂,经过检验得知,图3-45中裂纹处的白色物质为氮碳基盐与氧化盐,进行金相分析未发现裂纹处有氧化脱碳现象,也未发现有氮碳共渗层存在。
大部分挺杆开裂时是穿过出油孔的,表明此处流动性强,散热快,冷却十分激烈,而工作面底部的厚度比壁厚大得多,故内外热应力大。挺杆发蓝处理后的清洗水温为40~80℃,采用的氮碳共渗工艺装备如图3-46所示,挺杆紧密排列在一起,从氧化炉提出后的挺杆表面温度为300~350℃,停留一段时间后进行清洗,由于筐边缘的挺杆温度低,而筐心(中间)部分的挺杆仍会有较高的温度,故在清洗时温差较大,产生大的热应力导致开裂。
针对此问题,可采取的措施为:发蓝处理后的挺杆放置到室温后清洗;提高生产率,改进氮碳共渗工艺装备,采用可抽拉式的,将发蓝处理后的挺杆网板取出空冷,可避免挺杆冷却不当而产生的裂纹缺陷。
图3-43 Cr12W钢制挺杆工作面的剥落情况
图3-44 Cr12W钢制挺杆抛丸后的裂纹(毛坯)
图3-45 Cr12W钢制挺杆的端面裂纹(成品)
2)挺杆的磷化处理。挺杆的磷化处理是在某些酸性磷酸盐为主的溶液中进行的,是使挺杆表面发生沉积,形成一层不溶于水的结晶磷酸盐转化膜的过程。磷化膜是由一系列大小不等的晶粒组成的,形成有许多细小裂缝的多孔结构,可以使挺杆表面的耐磨性、减摩性和吸附性得到较好的改善。处理后磷化膜的厚度为1~50μm,基体的硬度和磁性等均保持不变。
图3-46 挺杆氮碳共渗工艺装备简图
磷化的工艺流程为:化学脱脂→热水洗→冷水冲洗→酸洗→冷水冲洗→磷化处理→冷水冲洗→去离子水洗→干燥。为了确保磷化膜的结晶致密、细小,满足挺杆表面耐磨性、耐蚀性等的要求,在磷化前增加表面调整工序,通常用钛盐溶液作调整剂。在实际生产过程中,化学脱脂溶液的配方为氢氧化钠60~100g/L、碳酸钠30~60g/L、磷酸三钠40~50g/L、水玻璃10~20g/L,溶液的温度为90~100℃,时间为10~15min。然后使用8080清洗剂,所配体积分数为10%,温度为30~60℃,时间为10~15min。酸洗采用18%~24%的盐酸,温度为50~70℃,时间为5~10min即可。
挺杆的磷化通常采用中温磷化工艺,温度为50~70℃,溶液中游离酸度与总酸度比值为1∶(10~15),时间为5~15min。此时游离酸度比较稳定,具有时间短、生产率高、磷化膜稳定和耐蚀性高等特点,常用中温磷化处理的溶液成分和工艺条件见表3-41。需要说明的是配方1~4为常用的磷化配方,配方5为合金铸铁耐磨防锈磷化工艺,配方6为高磷灰铸铁磷化配方,配方7为45钢用配方,配方8为激光热处理前的预磷化处理配方。
表3-41常用中温磷化处理的溶液成分和工艺条件
(续)
磷化后的处理完全取决于产品的用途,通常磷化膜后处理溶液的成分及工艺条件见表3-42。
表3-42磷化膜后处理溶液的成分及工艺条件
挺杆磷化膜的质量检验分为外观检验、耐蚀性检验和厚度与质量检验等几项,外观上应为连续、均匀且致密的晶体结构,表面呈灰色或灰黑色,表面不应有未磷化的残余空白或锈迹。耐蚀性检验可用浸入法、点滴法等,浸入法是将磷化后的样板浸入3%的氯化钠溶液中2h后取出,表面无锈蚀为合格;点滴法是将按要求配好的试剂滴在磷化膜上,观察其变色的时间,厚磷化膜、中等厚度磷化膜和薄磷化膜的时间分别为5min、2min和大于1min时,视为合格。厚度可用非磁性测厚仪检验,也可切片测磷化层厚度。质量测量是通过测量磷化膜剥离前后样品的质量实现的(用于精密产品)。
5.热处理工艺分析与操作要点
1)15Cr、20、20Cr等材料的挺杆渗碳过程与普通的渗碳无大的区别,其渗碳层的深度以试样来进行间接检测,不允许出现网状或块状的碳化物、表面到内部渗碳层的浓度梯度过陡等情况,该类缺陷将造成热处理后挺杆表面掉块、耐磨性差等,导致使用寿命明显降低。
2)渗碳钢经渗碳或碳氮共渗热处理后的金相组织为细针状马氏体,不允许有网状游离渗碳体和游离状态的铁素体,从渗层至中心不能有骤然转变的金相组织。挺杆心部为低碳马氏体组织。
3)合金钢和合金铸铁淬火后均获得了高的硬度,需要注意的是合金铸铁(含冷激铸铁)的热处理淬火温度为860~880℃,保温时间的长短将对硬度有直接的影响,在盐浴炉中的保温时间超过15min时,碳化物分解,淬火后的硬度无法满足技术要求,而时间过短则无法消除白口组织。热处理检查内容有硬度、石墨数量(体积分数<10%)以及碳化物的数量(体积分数>30%)。
4)挺杆火焰淬火时,应关注设备各部件、流量计及压力表运转是否正常,挺杆中心与火焰喷嘴的同轴度应小于1mm,端面与喷嘴的垂直度应小于1mm,喷嘴距离加热表面的距离应为50mm左右,乙炔、氧气的流量与压力应符合工艺要求,淬火油温应控制在40~80℃范围。
5)挺杆的表面处理主要包括氮碳共渗和磷化,其中氮碳共渗多应用于高合金钢和合金铸铁等材料,它们的回火温度均高于氮碳共渗温度,共渗层深度大多在0.03mm以上,硬度在850HV以上,质量缺陷多为表面粗糙度超差(腐蚀)、硬度低以及清洁度低等。
6)钢制挺杆氮碳共渗后表面缺陷有腐蚀、花斑等,故应防止渗氮时间过长,应彻底渗氮盐以及加强过程清洗等,避免表面存有残盐以及水痕迹等。
7)需要注意的是20钢、25钢挺杆的反挤压过程中,如果未进行退火处理,毛坯硬度在121HBW以上,则容易引起挤压时变形困难,将导致挤压凸模断裂。图3-47所示为一支挺杆毛坯未进行退火处理,出现凸模断裂的实物图片。
图3-47 20钢反挤压挺杆与挤压凸模的断裂图片
a)凸模断在挤压挺杆中 b)凸模的断口
8)挺杆热处理质量检验。渗碳钢挺杆的热处理质量检验与合金铸铁的热处理质量检验分别见表3-43和表3-44。
表3-43渗碳钢挺杆的热处理质量检验
表3-44合金铸铁挺杆的热处理质量检验
6.挺杆的热处理、磷化缺陷分析与预防或补救措施
挺杆的热处理时常见缺陷的产生原因和预防或补救措施见表3-45。挺杆磷化时常见缺陷的产生原因和预防或补救措施见表3-46。
表3-45挺杆热处理时常见缺陷的产生原因和预防或补救措施
(续)
表3-46挺杆磷化时常见缺陷的产生原因和预防或补救措施
(续)
3.3.3推杆、摇臂和摇臂轴
1.内燃机推杆
(1)工作条件与技术要求 推杆是与挺杆有直接关系的零件,它由杆身、上端头和下端头组成,下端头呈球状,在装配时与挺杆内的凹球面配合,上端头呈凹坑状,与摇臂上调整螺钉下端的球面相配合,因此推杆的作用是将凸轮轴经过挺杆传来的推力传给摇臂,是传递动力的关键部件,是气门机构中最容易弯曲的零件,因此推杆的两端面应具有高的硬度、刚度和良好的耐磨性,用钢或硬铝制作,钢制推杆应经过淬火和磨光,以保证其有足够的耐磨性。
(2)材料的选用和热处理工艺 整体结构钢制气门推杆用45钢,组合气门推杆两端头材质为20钢、45钢,球头和球面经渗碳淬火后硬度符合要求,45钢渗碳层深度大于1mm,硬度≥58HRC,20钢渗碳层深度大于0.8mm,硬度≥52HRC。为了减轻质量,常做成空心结构,但必须保证有足够的刚度。
组合气门推杆的头部不允许松动,焊缝要牢固,要求表面无裂纹、飞边、毛刺、锈蚀等。
2.汽车发动机的摇臂和摇臂轴
(1)摇臂 摇臂为一不等臂的杠杆件,也称为双杠杆,摇臂和摇臂轴如图3-48所示,摇臂中间的圆孔用来装摇臂轴。长臂端部与气门的杆端接触,短臂端部的螺孔用来安装调整螺钉,摇臂孔内有润滑油孔。摇臂的作用是把推杆经调整螺钉传给它的力改变方向传给气门端部,使气门打开进行工作。常采用钢或球墨铸铁制造摇臂,为了提高圆弧的耐磨性,提高其使用寿命,通常在感应淬火处理后进行工作面的磨削,如果存在磨削参数不当或零件定位尺寸不准等因素,则时常会产生磨削裂纹,具体如图3-49所示,在裂纹处可看到因磨削而造成的二次淬火的白亮层等。摇臂安装在摇臂轴上。目前气门摇臂的摇臂体采用铝合金材料,摇臂头部即摇臂镶块为合金材料,与传统的铸钢摇臂相比,提高了刚度,又减轻了运动部分的质量,降低了惯性力,减少了磨损,故延长了使用寿命。
图3-48 摇臂和摇臂轴
1—开口销 2—弹簧圈3—垫片 4—摇臂 5—支座 6—调整螺钉 7—摇臂轴 8—弹簧
CA141汽车摇臂采用QT600-3球墨铸铁制造,热处理的目的是提高工作表面的硬度,提高耐磨性等,热处理后的抗拉强度≥600MPa,伸长率≥3%,淬硬层深度为1.2~2.5mm,淬硬层表面硬度≥53HRC,采用高频感应淬火后淬硬层为马氏体组织,然后进行低温回火。
高频感应淬火的工艺为:摇臂依次安装在夹具上,用超音频进行工作面的感应加热,加热完毕自动转至淬火工位进行淬火,最后进行低温回火(加热温度180±10℃,时间1h),目的是消除应力与稳定组织。
摇臂在工作过程中,要克服气门弹簧的预紧力,同时承受冲击作用。一般摇臂与气门杆部端面的失效形式为疲劳磨损。推荐的粉末冶金材料成分为w(C)=2.0%~2.3%、w(Cr)=11.9%~13.9%、w(Ni)=3.13%~4.00%和w(Mo)=1.40%~1.90%等。粉末冶金合金镶块采用压力成形,然后经过真空烧结处理,随后进行热处理:1100~1120℃盐浴炉加热,保温时间按10~13s/mm计算,在80℃以下的油中冷却,硬度为51HRC以上;通常采用箱式或井式炉回火530℃×1h两次,回火基体组织为回火马氏体+残留奥氏体,显微镜下可以看到细小条状和小块状碳化物均匀分布在基体上,硬度为50~62HRC。
(2)摇臂轴 汽车发动机摇臂轴及淬火区如图3-50所示,采用中空的45钢管制造,最佳碳质量分数为0.42%~0.47%,45钢毛坯预先调质硬度为207~247HBW,有6处需要表面淬火处理,硬度为58~63HRC,硬化层深度为1~1.5mm。
图3-49 摇臂磨削裂纹及附近区域的金相组织(×100)
图3-50 汽车发动机摇臂轴及淬火区
45钢属于中碳钢,如果要求采用整体淬火+低温回火处理,硬度为50~55HRC,则采用的热处理工艺为820~850℃×7~8min(中温盐浴炉),淬火冷却介质为20℃以下的10%的氯化钠水溶液,200~240℃×60~90min(硝盐浴中)回火。
3.3.4曲轴链轮和链条
1.工作条件和技术要求
曲轴链轮和链条为动力传动机构,要求其自重轻、阻力小、安全性高。链轮的运转速度快,变换频繁,因此所受冲击力大,同时要承受弯曲应力、表面接触应力等作用,应具有高的硬度和耐磨性。链条由外链板、中间链板、内链板、销轴、衬套和滚子组成,其中链板要承受交变的法向拉应力和弯曲应力的作用,并承受多次的冲击载荷等,而滚子在链传动时,也承受很大的交变挤压力和多次冲击力的作用,另外销轴同样要承受周期性的冲击弯曲载荷。链条的失效的形式为碎裂、过载损坏、磨损和疲劳(或脆性)断裂等。
2.材料的选用
根据链条的工作特点,要求其表面具有良好的韧性和足够的耐磨性来保证其具有高的使用寿命,同时又必须具有足够的强度,通常链条零件如链板(片)、销轴、滚子和衬套等采用低碳钢经碳氮共渗处理或采用低碳合金钢进行低碳马氏体处理,也可用中碳优质低合金钢进行淬火、中温回火处理。
链板材 料 选 用35 CrMo、42 CrMo、40 Cr、30 CrNi3等;滚子的材料为20 CrMo;销轴材料为20 CrMnMo、20 Cr2 Ni4等。这些材料经过热处理或化学热处理后能获得要求的力学性能,满足工作需要,并确保具有高的使用寿命。
3.链条零件的热处理
(1)链板(片)的热处理 链板(片)材料为中碳合金钢35CrMo、42CrMo、40Cr、40Mn、30CrNi3和低碳钢27SiMn、20Mn2,低碳钢经淬火后获得低碳马氏体,其淬火工艺如图3-51所示,35CrMo、42CrMo、40Cr、40Mn、30CrNi3中碳合金钢制链板的热处理工艺如图3-52所示。
图3-51 27SiMn、20Mn2链板的热处理工艺
图3-52 中碳合金钢等链板的热处理工艺
40Mn链片处理后的硬度为35~45HRC。而35CrMo的热处理硬度为42~47HRC,42CrMo硬度为38~45HRC。
(2)销轴、滚子和衬套的热处理 部分低碳钢曲轴链条零件销轴、滚子和衬套碳氮共渗热处理的技术要求见表3-47。
表3-47部分低碳钢曲轴链条零件销轴、滚子和衬套碳氮共渗热处理的技术要求
用20CrMo钢制作的滚子淬火后获得低碳马氏体组织,经180~220℃回火后,明显提高了使用寿命。销轴用材料和热处理后的技术要求见表3-48。
表3-48销轴用材料和热处理后的技术要求
通过分析链条的工作状况可知,这些零件既要有良好的耐磨性,又要具有一定的强度和韧性,因此选用低碳钢进行渗碳或碳氮共渗处理,最后低温回火,这样表面可获得高的硬度,而零件心部硬度低,以满足其工作需要,避免在运动过程中出现断裂的现象。
曲轴链条的销轴、滚子和衬套的气体碳氮共渗工艺如图3-53所示。
图3-53 曲轴链条的销轴、滚子和衬套的气体碳氮共渗工艺
通常选用网带式碳氮共渗炉或滚筒式渗碳炉,零件的碳氮共渗采用滴注方式,渗剂主要有煤油和甲醇,其中甲醇为稀释剂。资料介绍,采用RX气体进行碳氮共渗效果更好。
为了提高链板、滚子和销轴的寿命,必须进行喷丸强化处理,处理后可明显提高零件的疲劳抗力和多冲抗力。