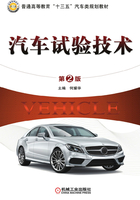
第四节 气体传感器
可用于检测气体浓度或成分的传感器统称为气体传感器。气体传感器的种类很多,分类方法各异。
按结构的不同,气体传感器可分为干式气体传感器和湿式气体传感器。凡是构成气体传感器的材料为固体者称为干式气体传感器;凡是利用水溶性或电解液感知气体浓度或成分者称为湿式气体传感器。
按工作原理的不同,气体传感器可分为接触燃烧式气体传感器、半导体式气体传感器、固体电化学式气体传感器和红外吸收式气体传感器。
一、接触燃烧式气体传感器
1.接触燃烧式气体传感器的工作原理
可燃性气体(H2、CO、CH4等)与空气中的氧气接触,发生反应产生反应热(无焰接触燃烧热),使得作为敏感材料的铂丝温度升高,电阻值相应增大。一般情况下,空气中可燃性气体的浓度都不太高(低于10%),可燃性气体可以完全燃烧,其发热量与可燃性气体的浓度有关。空气中可燃性气体浓度愈大,反应(燃烧)产生的反应热(燃烧热)愈多,铂丝的温度变化(增高)愈大,其电阻值增加得就越多。因此,只要测定作为敏感件的铂丝的电阻变化值(ΔR),就可检测空气中可燃性气体的浓度。但是,使用单纯的铂丝线圈作为检测元件,其寿命较短,所以实际应用的检测元件都是在铂丝圈外面涂覆一层氧化物触媒。这样既可以延长其使用寿命,又可以提高检测元件的响应特性。
接触燃烧式气体敏感元件的桥式电路如图3-27所示。图中F1是检测元件;F2是补偿元件,其作用是补偿可燃性气体接触燃烧以外的环境温度、电源电压变化等因素所引起的偏差。工作时,要求在F1和F2上保持100~200mA的电流通过,以供可燃性气体在检测元件F1上发生接触燃烧所需要的热量的同时,保证电桥的初始平衡状态。当检测元件F1与可燃性气体接触时,由于剧烈的燃烧,释放出热量,使得检测元件的温度上升,电阻值相应增大,桥式电路不再平衡,在A、B间产生电位差E。


图3-27 接触燃烧式气体敏感元件的桥式电路
式中 RF1——检测元件F1的电阻值(Ω);
ΔRF——检测元件F1在测试过程中的电阻值的变化量(Ω);
RF2——补偿原件F2的电阻值(Ω);
R1、R2——电桥电阻(Ω)。
因为ΔRF很小,且RF1R1=RF2R2,式(3-38)可改写为

令K=E0R1/(RF1+R2)(R1+RF2),则有

ΔRF是由于可燃性气体接触燃烧所产生的温度变化(燃烧热)引起的,与接触燃烧热成比例,即ΔRF可用下式表示:

式中 ρ——检测元件的电阻温度系数;
ΔT——由于可燃性气体接触燃烧所引起的检测元件的温度增加值;
ΔH——可燃性气体接触燃烧的发热量;
C——检测元件的热容量;
Q——可燃性气体的燃烧热;
m——可燃性气体的体积百分比浓度;
α——由检测元件上涂覆的催化剂决定的常数。
ρ、C和α的数值与检测元件的材料、形状、结构、表面处理方法等因素有关。Q由可燃性气体的种类决定,因而,在一定条件下均为常数。将式(3-41)代入式(3-40)得

即A、B两点间的电位差与可燃性气体的浓度m成比例。如果在A、B两点间连接电流计或电压计,就可以测得A、B间的电位差E,并由此求得空气中可燃性气体的浓度。若与相应的电路配合,当可燃性气体达到一定浓度时,自动发出报警信号,其感应特性曲线如图3-28所示。

图3-28 接触燃烧式气体传感器的特性
注:%LEL是爆炸下限,体积百分比浓度。
2.接触燃烧式气体传感器的结构
图3-29是接触燃烧式气体传感器的结构示意图,接触燃烧式气体传感器用铂丝绕制成线圈,为了使线圈具有适当的阻值(1~2Ω),一般绕10圈以上。在线圈外面涂以氧化铝或氧化铝和氧化硅组成的膏状涂覆层,干燥后在一定温度下烧结成球状多孔体。将烧结后的小球,放在贵金属铂、钯等的盐溶液中,充分浸渍后取出烘干。然后经过高温热处理,使在氧化铝(氧化铝和氧化硅)载体上形成贵金属触媒层,最后组装成气体敏感元件。作为补偿元件的铂线圈,其尺寸、阻值均应与检测元件相同,并且也应涂覆氧化铝或氧化硅载体层,只是无须浸渍贵金属盐溶液或混入贵金属触媒粉体,形成触媒层。
3.接触燃烧式气体传感器的应用
1958年,Mewillan和Harley等分别研制成功氢火焰离子检测器(FID),其工作原理是:以氢气和空气燃烧生成的火焰为能源,当有机化合物(如碳氢化合物)进入以氢气和氧气燃烧的火焰中时,便产生化学电离,化学电离所产生的离子在高压电场的定向作用下形成离子流。离子流经过高阻(106~1011Ω)放大便产生与所测有机化合物质量成正比的电信号,如图3-30所示。氢火焰检测器结构简单、工作可靠、测试精度高。

图3-29 接触燃烧式气体传感器结构示意图
二、半导体式气体传感器
半导体式气体传感器的敏感元件大多是以金属氧化物半导体为基础材料。当被测气体吸附在半导体表面后,会使半导体敏感材料的电学特性 (例如电导率)发生变化,这一现象称为气敏效应,具有气敏效应的半导体材料叫气敏电阻。常用的气敏 材 料 有 SnO2、ZnO、Fe2O3、MgO、NiO、BaTiO3等。通过测量气敏电阻的阻值变化,就可以实现对气体的检测。半导体式气体传感器可以有效地用于甲烷、乙烷、丙烷、丁烷、酒精、甲醛、一氧化碳、二氧化碳、乙烯、乙炔、氯乙烯、苯乙烯、丙烯酸等很多气体的检测。半导体式气体传感器低廉的成本使其在各个领域得到了广泛的应用。

图3-30 氢火焰离子型气体传感器
1—离子收集器 2—信号放大器 3—空气分配器4—氢气和待测气体入口 5—助燃空气入口 6—燃烧喷嘴
1.气敏电阻的特性参数
(1)气敏电阻的固有电阻值 将半导体气体传感器在常温下置于洁净空气中所测得的电阻,称为气敏电阻的固有电阻值Ra,其值为103~105Ω。由于地理环境的差异,各地区空气中含有的气体成分差别较大,即使对于同一气敏电阻在温度相同的条件下,在不同地区进行测量,其电阻值也会各不相同。
(2)气敏元件的加热电阻和加热功率 气敏电阻一般工作在200℃以上的高温中。为气敏元件提供必要工作温度的加热电路的电阻(指加热器的电阻值)称为加热电阻,用RH表示。直热式的加热电阻值一般小于5Ω;旁热式的加热电阻大于20Ω。气敏元件正常工作所需的加热电路功率,称为加热功率,用PH表示,其数值为0.5~2.0W。
(3)气敏电阻的响应时间 在工作温度下,从气敏电阻与一定浓度的被测气体接触到气敏电阻的阻值达到在此浓度下稳定电阻值的63%所经历的时间,称为气敏电阻的响应时间,用tr表示。
(4)气敏电阻的恢复时间 在工作温度下,气敏元件脱离被测气体时至其阻值恢复到在洁净空气中阻值的63%时所需的时间,称为气敏电阻的恢复时间,用tf表示。
(5)初期稳定时间 长期在非工作状态下存放的气敏电阻,因表面吸附空气中的水分或其他气体,导致其表面状态的变化。因此,使气敏电阻恢复正常工作状态需要一定的时间,此时间称为气敏元件的初期稳定时间。通常,气敏电阻在刚通电的瞬间,其电阻值会先下降后上升,最后达到稳定值。从接通气敏电阻的电源到电阻值到达稳定值所需的时间,称为初期稳定时间。初期稳定时间是气敏电阻存放时间和环境状态的函数。存放时间越长,其初期稳定时间也越长。在一般条件下,气敏电阻存放两周以后,其初期稳定时间即可达到最大值。
2.气敏电阻的结构形式
气敏电阻分为烧结型、薄膜型和厚膜型,其中烧结型应用最为广泛。气敏电阻主要用于检测可燃的还原性气体,其工作温度约300℃。根据加热方式,气敏电阻分为直接加热式和旁热式。
(1)直接加热式 直接加热式气敏电阻由芯片(加热器和测量电极一同烧结在金属氧化物半导体管芯内)、基座和金属防爆网罩组成,如图3-31所示。因其热容量小、稳定性差,测量电路与加热电路间易相互干扰,加热器与气敏电阻基体间由于热膨胀系数的差异而容易导致接触不良,因此,此种形式的气敏电阻在工程实践中应用相对较少。

图3-31 直接加热式气敏电阻
1—测量电极 2—烧结体 3—加热电极
(2)旁热式 旁热式气敏电阻以陶瓷管为基底,管内穿有加热丝,管外侧有两个测量极,测量极之间为金属氧化物气敏材料经高温烧结而成,如图3-32所示。

图3-32 旁热式气敏电阻
1—烧结体 2—不锈钢网罩 3—引脚 4—塑料底座 5—加热回路电源 6—加热电极 7—工作电极 8—测量回路电源
3.气敏电阻型氧传感器的应用
二氧化钛氧传感器是利用TiO2材料的电阻值随排气中氧含量的变化而变化的特性制成的,故又称气敏电阻型氧传感器,如图3-33所示。TiO2氧传感器的外形和二氧化锆氧传感器相似,在传感器前端的护罩内是一个TiO2厚膜元件(图3-33)。TiO2在常温下是一种高电阻的半导体,但表面一旦缺氧,电阻随之减小。由于TiO2的电阻也随温度不同而变化,因此,在TiO2氧传感器内部也有一个电加热器,以保持TiO2氧传感器在发动机工作过程中的温度恒定不变。TiO2氧传感器的输出电压在0.1~0.9V间不断变化,这一点与氧化锆式氧传感器很相似。

图3-33 TiO2氧传感器
1—保护套管 2—连接线 3—TiO2厚膜元件
三、固体电解质式气体传感器
导电体有两大类:一类是金属导体,依靠自由电子导电,当电流通过导体时,导体本身不发生任何化学变化;另一类是电解质导体,依靠离子的运动导电,在相界面有化学反应发生,其电导率随温度升高而增大,电解质导体有液体和固体之分,固体电解质是离子迁移速度较高的固态物质,具有一定的形状和强度。对于多数固体电解质而言,只有在较高温度下,电导率才能达到10-6s/cm数量级,因此固体电解质的电化学实际上是高温电化学。
ZrO2具有很好的耐高温性能和化学稳定性。它在常温下是单斜晶系晶体,当温度升高到大约1150℃时发生相变,成为正方晶系,同时产生大约9%(有资料介绍为7%)的体积收缩,当温度下降时相变会逆转。由于ZrO2晶形随温度变化,因此它也是不稳定的。但若在ZrO2中加入一定数量阳离子半径与Zr4+ 相近的氧化物,如CaO、MgO、Y2O3、Sc2O3等,经高温煅烧后,它们与ZrO2形成置换式固溶体。掺杂后,ZrO2晶形将变为萤石型立方晶系,并且不再随温度变化,称为稳定的ZrO2。掺入CaO的ZrO2可记作ZrO2-CaO或ZrO2(CaO),其余类同。稳定的ZrO2和用类似的方法制作的TiO2固体电解质是制造气体传感器较为理想的材料。固体电解质式气体传感器可用来测量O2、H2、C4H10、CH4、CO、CO2、NO2、H2S、NO、NH3、PH3等多种气体。
安装在汽车发动机排气管上的氧传感器大多用ZrO2制成,图3-34是ZrO2氧传感器的结构图,其结构原理是:ZrO2氧传感器的基本元件是陶瓷体9,固定在管座2中。多孔陶瓷电极板(ZrO2固体电解质)10的一边与环境空气接触。多孔陶瓷的外面有一带槽的保护套1,一旦氧气渗入到多孔陶瓷就会发生电离,若陶瓷体内(大气)外(废气)侧氧含量不一致,即存在浓度差时,在多孔陶瓷内部的氧离子从大气一侧向废气一侧扩散,在多孔陶瓷电极板间便产生电压,即电信号。当混合气稀时,废气中所含氧多,多孔陶瓷两侧的氧浓度差相对较小,电极间只产生小的电压;当混合气浓时,废气中氧含量少,同时伴有较多的未完全燃烧的中间产物CO、HC等,这些成分在氧传感器外表面的作用下,消耗废气中残余的氧,使多孔陶瓷外表面氧浓度变为零这样就使其两侧的氧浓度差突然增大,两极间产生的电压便突然增大。氧传感器输出的电压在空燃比为理论空燃比(14.7)时发生突变。当可燃混合气浓度较稀时,氧传感器的输出电压几乎为0;当可燃混合气浓度相对较浓时,氧传感器的输出电压接近1V(图3-34b)。

图3-34 ZrO2氧传感器
1—带槽保护套 2—管座 3—外壳 4—绝缘体 5—电极 6—传感器加热线7—簧片 8—加热电阻 9—陶瓷体 10—多孔陶瓷电极板