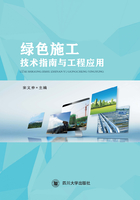
1.15 全预制轨下结构拼装技术
1.15.1 适用条件和范围
该技术适用于地下工程隧道内部轨下结构全预制拼装施工。
1.15.2 技术要点
轨下结构需提前在工厂内预制,利用拼装机等机械设备对轨下预制结构进行快速施工。
利用边箱涵拼装机进行轨下预制结构施工,可达到3人5分钟拼装完成1块边箱涵的效果,极大提高了盾构隧道内轨下结构的施工速度,缩短了工期,节省了成本。
1.15.3 施工要求
全预制轨下结构拼装技术的具体施工步骤如下(见图1-25):

图1-25 全预制轨下结构拼装施工步骤
(1)地面将检验合格且粘贴嵌缝条完毕的边箱涵预制件通过龙门吊吊装至井下,并放置于安装有边箱涵预制件专用托架的运输车上,每辆车一次可运输一环共两块边箱涵预制件。
(2)现场工人对需拼装边箱涵区域内的灰尘、积水、杂物进行全面清理。
(3)拼装机操作人员对拼装机行走系统、起吊系统、箱涵件的吊具及定位调整系统进行全面检查,一切正常后,操作人员操作拼装机前行至边箱涵拼装区域。前行过程中,尤其是在通过管片及箱涵件错台处时,利用驱动系统的变频器进行调速,以确保启动和行走平稳。同时,由于隧道具有向下的坡度,所以应利用驱动系统配备的电磁制动器对行走轮进行及时制动。
(4)拼装机到达指定位置后,起吊小车起吊箱涵件吊具至最高位置,并水平移动至最右端。箱涵件运输车在中箱涵上前进至拼装机正下方。吊具根据边箱涵在运输车上的位置误差进行回转调整,使前一块箱涵与箱涵件吊具保持横向水平。
(5)拼装手操作拼装吊机将U型吊具下落至合适位置,然后向左移动,使U型吊具的U型槽插入边箱涵预制件的顶部混凝土层,在插入过程中留意U型吊具两侧的距离检测装置,避免U型吊具磕碰边箱涵预制件。使用U型吊具上的定位装置控制U型吊具的停止位置,停止后使用夹紧装置夹紧边箱涵预制件。
(6)缓缓起吊边箱涵预制件,待其升至最高处且与支架完全脱离接触后,水平右移吊具,移动至最右端后,逆时针旋转吊具,使边箱涵预制件以正确的姿态处于待拼装区上方。
(7)缓慢下落U型吊具,当箱涵件下落至拼装位置时,伸长U型吊具左右两侧的电动推杆,使其末端顶紧在管片上,来实现箱涵件位置的微动精调。同时,可对边箱涵和中箱涵的接触面产生顶紧力,确保两结构件连接位置的精确度。末端的球铰结构可保证电动推杆的着力点适应管片的圆弧结构。之后松开夹紧装置,退出U型吊具。至此完成一块边箱涵的拼装。
(8)收回U型吊具,运输车前进至合适位置,重复以上步骤,进行左侧边箱涵的拼装。接下来采用螺栓通过预留孔洞将中箱涵与边箱涵连接成为一个整体。起吊后,运输车倒车离开拼装区。至此完成一环共两块边箱涵的拼装作业。
(9)待箱涵全部拼装完成后,对箱涵之间以及箱涵和管片之间的空隙处实施整体注浆,使得隧道内部轨下结构连接为一个整体。至此完成轨下结构全预制施工工作。
1.15.4 实施效果
(1)该施工方法机械化程度高,施工速度快,预制构件运至现场即可利用机械进行拼装,大大提高了工人的工作效率和机械使用效率;预制件工厂化生产可实现构件的标准化,且对其做好防护措施后不受自然环境影响,可以充分保证预制件质量,实现批量化生产。统一生产的标准性和规范性确保了预制构件几何形状的精度,大大提高了混凝土结构的美观性,同时也确保了现场施工的质量和效率,降低了损耗,达到了节约工期、节约材料的目的;另外,构件生产采用定型钢模板,可多次重复使用,节约了模板材料投入。
(2)现场施工无须周转材料,不用占用大量材料堆场,减少施工占地,节约土地,有效降低了盾构隧道的建设成本;厂制构件、养护水循环利用,减少了现浇混凝土养护时水资源浪费,节约用水,且养护质量容易控制。
(3)全预制施工不仅避免了洞内交叉施工影响,还减小了施工中对交通及环境的影响,节能环保,实现了绿色、低碳、环保的施工目标。
(4)全预制施工实现了工厂化生产、现场拼装,除后续砂浆灌封外,无现场混凝土浇筑,避免了受商品混凝土发运、天气情况等因素影响以至无法施工的问题。
1.15.5 工程案例
清华园隧道工程位于北京市海淀区,盾构段为单洞双线隧道,全长4448.5m,隧道管片外径12.2m、内径11.1m,管片环宽2m,壁厚0.55m,轨下架构采取中间预制“口”字件(中箱涵)+两侧预制边箱涵的结构形式。中铁十四局集团有限公司采用全预制轨下结构拼装技术,配置了箱涵拼装机1台(盾构机自带)、边箱涵拼装机1台、边箱涵专用运输车1辆、箱涵运输车1辆。施工进度快,占用井下空间小,节省人工及材料成本,保证了施工的进度及安全要求,节地、节材、节能,减少了污染,环保效果显著,取得了显著的经济效益和社会效益。