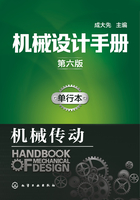
3.5 外啮合齿轮变位系数的选择
3.5.1 变位系数的选择方法
表15-1-16

3.5.2 选择变位系数的线图
图15-1-14是由哈尔滨工业大学提出的变位系数选择线图,本线图用于小齿轮齿数z1≥12。其右侧部分线图的横坐标表示一对啮合齿轮的齿数和zΣ,纵坐标表示总变位系数xΣ,图中阴影线以内为许用区,许用区内各射线为同一啮合角(如19°,20°,…,24°,25°等)时总变位系数xΣ与齿数和zΣ的函数关系。应用时,可根据所设计的一对齿轮的齿数和zΣ的大小及其他具体要求,在该线图的许用区内选择总变位系数xΣ。对于同一zΣ,当所选的xΣ越大(即啮合角α′越大)时,其传动的重合度ε就越小(即越接近于ε=1.2)。

图15-1-14 选择变位系数线图(,α=20°)
在确定总变位系数xΣ之后,再按照该线图左侧的五条斜线分配变位系数x1和x2。该部分线图的纵坐标仍表示总变位系数xΣ,而其横坐标则表示小齿轮z1的变位系数x1(从坐标原点0向左x1为正值,反之x1为负值)。根据xΣ及齿数比u=(z2/z1),即可确定x1,从而得x2=xΣ-x1。
按此线图选取并分配变位系数,可以保证:
1)齿轮加工时不根切(在根切限制线上选取xΣ,也能保证齿廓工作段不根切);
2)齿顶厚sa>0.4m(个别情况下sa<0.4m但大于0.25m);
3)重合度ε≥1.2(在线图上方边界线上选取xΣ,也只有少数情况ε=1.1~1.2);
4)齿轮啮合不干涉;
5)两齿轮最大滑动率接近或相等(η1≈η2);
6)在模数限制线(图中m=6.5,m=7,…,m=10等线)下方选取变位系数时,用标准滚刀加工该模数的齿轮不会产生不完全切削现象。该模数限制线是按齿轮刀具“机标(草案)”规定的滚刀长度计算的,若使用旧厂标的滚刀时,可按下式核算滚刀螺纹部分长度l是否够用。
式中 da——被加工齿轮的齿顶圆直径;
αa——被加工齿轮的齿顶压力角;
α——被加工齿轮的分度圆压力角。
例1 已知某机床变速箱中的一对齿轮,z1=21,z2=33,m=2.5mm,α=20°,,中心距a′=70mm,试确定变位系数。
解 (1)根据给定的中心距a′求啮合角α′
(2)在图15-1-14中,由0点按α′=25°1′25″作射线,与zΣ=z1+z2=21+33=54处向上引的垂线相交于A1点,A1点的纵坐标值即为所求的总变位系数xΣ(见图中例1,xΣ=1.125),A1点在线图的许用区内,故可用。
(3)根据齿数比,故应按线图左侧的斜线②分配变位系数x1。自A1点作水平线与斜线②交于C1点,C1点的横坐标x1即为所求的x1值,图中的x1=0.55。故x2=xΣ-x1=1.125-0.55=0.575。
例2 一对齿轮的齿数z1=17,z2=100,α=20°,,要求尽可能地提高接触强度,试选择变位系数。
解 为提高接触强度,应按最大啮合角选取总变位系数xΣ。在图15-1-14中,自zΣ=z1+z2=17+100=117处向上引垂线,与线图的上边界交于A2点,A2点处的啮合角值,即为zΣ=117时的最大许用啮合角。
A2点的纵坐标值即为所求的总变位系数xΣ=2.54(若需圆整中心距,可以适当调整总变位系数)。
由于齿数比u=z2/z1=100/17=5.9>3.0,故应按斜线⑤分配变位系数。自A2点作水平线与斜线⑤交于C2点,则C2点的横坐标值即为x1,得x1=0.77。
故x2=xΣ-x1=2.54-0.77=1.77。
例3 已知齿轮的齿数z1=15,z2=28,α=20°,,试确定高度变位系数。
解 高度变位时,啮合角α′=α=20°,总变位系数xΣ=x1+x2=0,变位系数x1可按齿数比u的大小,由图15-1-14左侧的五条斜线与xΣ=0的水平线(即横坐标轴)的交点来确定。
齿数比,故应按斜线③与横坐标轴的交点来确定x1,得
x1=0.23
故 x2=xΣ-x1=0-0.23=-0.23
3.5.3 选择变位系数的线图(摘自DIN 3992德国标准)
利用图15-1-15可以按对承载能力和传动平稳性的不同要求选取变位系数。图15-1-15适用于z>10的外啮合齿轮。当所选的变位系数落在图b或图c的阴影区内时,要校验过渡曲线干涉;除此之外,干涉条件已满足,不需要验算。图b中的L1~L17线和图c中的S1~S13线是按两齿轮的齿根强度相等、主动轮齿顶的滑动速度稍大于从动轮齿顶的滑动速度、滑动率不太大的条件,综合考虑做出的。
图15-1-15的使用方法如下。
1)按照变位的目的,根据齿数和(z1+z2),在图a中选出适宜的总变位系数x∑。
2)利用图b(减速齿轮)或图c(增速齿轮)分配x∑;按(可直接由图a垂直引下)和
决定坐标点;过该点引与它相邻的L线或S线相应的射线;过z1和z2做垂线,与所引射线交点的纵坐标即为x1和x2。
3)当大齿轮的齿数z2>150时,可按z2=150查线图。
4)斜齿轮按zv=z/cos3β查线图,求出的是xn。
例1 已知齿轮减速装置,z1=32、z2=64、m=3,该装置传递动力较小,要求运转平稳,求其变位系数。
由图a,按运转平稳的要求,选用重合度较大的P2,按z1+z2=96,得出x∑=-0.20(图中A点)。按表15-1-17算得a=143.39mm,若把中心距圆整为a=143.5mm,则按表15-1-17可算得x∑=-0.164。由A点向下引垂线,在图b上找出的点B。过B点引与L9和L10相应的射线,由z1=32,得出x1=0.06,则x2=x∑-x1=-0.224。由图15-1-16查出εα=1.79,可以满足要求。
例2 已知增速齿轮装置,z1=14、z2=37、mn=5、β=12°,要求小齿轮不产生根切,且具有良好的综合性能,求其变位系数。
由表15-1-17算出zv1=15、zv2=39.5。因为要求综合性能比较好,因此选用图a中的P4,按zv1+zv2=54.5,求出xn∑=0.3(图中D点)。按表15-1-17算得a=131.79mm,若把中心距圆整为a=132mm,则按表15-1-16可算得xn∑=0.345。过D点向下引垂线,在图c中找出的点E。过E点引与S6、S7相应的射线,由zv2=39.5得出xn2=0.19,则xn1=xn∑-xn2=0.155。因为由zv1和xn1确定的点落在不根切线的右侧,所以不产生根切,可以满足要求。

图15-1-15 选择变位系数的线图
3.5.4 等滑动率的计算
G.Nimann & H.Winter在《机械零件》一书中指出,在啮合几何参数中,最重要的影响量为相对滑动速度。因此,在有胶合危险时,应当把齿形选择得使啮合线上的啮出段与啮入段的长度差不多一样长(由于有不利的啮入冲击——推滑,啮合线上啮入段要稍微短一些)。
大部分有关齿轮的手册都有滑动率计算公式,大小齿轮齿顶与对应齿轮啮合位置是滑动率最大的地方,对于高速传动,基本都计算最大滑动率大致相等去分配总变位系数。外啮合的最大滑动率的计算公式如下:
这组公式只是在现有参数下计算出η1max和η2max,想要η1max≈η2max还需要在控制一定需要精度下迭代运算(见等滑动率变位系数分配程序)。美国标准ANSI/AGMA 913-A98中,不仅有外啮合的等滑动率的计算,也有内啮合的计算,这样就弥补了内啮合变位分配问题。
这里有几个重要代号,SAP-LPSTC-HPSTC-EAP。
SAP(start of the active profile)——齿廓啮合起始点;
EAP(end of the active profile)——齿廓啮合终止点;
LPSTC(HPSTC)(The lowest and highest point of single-tooth-pair contact)——单对齿啮合的内(外)界点。
AGMA 913-A98给出了内、外齿轮副等滑动的条件,下面是外啮合的计算(参见图15-1-16)。
C6=(rb1+rb2)tanαwt=awsinαwt
C2=C5-pbt
C3=rb1tanαwt
C4=C1+pbt

图15-1-16 AGMA 913-A97外齿轮副沿啮合线的几个特征点的距离
对AGMA 913-A98的算法与本手册增加的等滑动率方法,进行反复对比。结果两者在相同控制精度内是完全一样的(见图15-1-19)。外啮合确认了就扩展到内啮合。这就补充了国内没有等滑动的内啮合计算方法。
下面就是内啮合的情况(见图15-1-17)。

图15-1-17 AGMA 913-A98内齿轮副沿啮合线的几个特征点间的距离
经过大量运算,作出图15-1-18。

图15-1-18 小齿轮z1=21对应各种齿数比等滑动率曲线,对于z±2也适用
每一个u(z2/z1),从总变位-0.4开始到总变位3,每次按照0.05增量,计算出等滑动率的x1,用(∑x,x1)在图中描绘出一个点,每个u由70个点连接。连续作出全部规定的数值。
同图15-1-14左侧图形比较,图15-1-18考虑了如下情况。
1)同样的齿数比u(z2/z1),对于不同的小齿数z1,左面曲线密集区位置(如图15-1-18中∑x0.8~∑x1.0之间)有很大变化。图15-1-18是按z1=21计算的。
2)对于一级(多级也是单个的组合)的u,规定如下:1.25、1.4、1.6、1.8、2.0、2.24、2.5、2.8、3.15、3.55、4.0、4.5、5.0、5.6、6.3、7.1。
计算过程可以采用全部u,为了图形清晰有的u被忽略了。
按照这个比值,u≥3,还有多个组别,图上的u=3.15为界限的图形。

图15-1-19 外啮合的等滑动率计算与ANSI/AGMA913A98的比较

图15-1-20 ANSI/AGMA913-A98内啮合等滑动率的计算
3)x1的比例,适当增大比例,可以看得清楚一些。
即便是这样放大了的图形,对于∑x=0.5~1这个范围,还是很难获得准确的选择点,大多数情况又是这个范围(例如德国西马克就明文规定,这个范围就是他的设计规范)。
为了等滑动系数分配,可以按z1=15~40,每个齿绘制一张上述的图片,这样才是等滑动系数分配。每张按照间隔齿数3,即z1=15、18、21、24、27、30、33、36、39、42做成10张上述图形,基本上也可以得到近似的分配,就如同封闭图那样,不过这个数量很少。
美国ANSI/AGMA 913-A98将等滑动率计算和等闪温计算并列,说明两者对胶合计算还是有差别的。更详细的计算,请参阅有关标准。
3.5.5 AGMA 913-A98关于变位系数选取
变位的选择要考虑以下因素:
①避免根切;
②避免齿顶过窄;
③平衡滑动率;
④平衡闪温;
⑤平衡弯曲疲劳寿命。
变位不应该太小以防止根切,同时也不应该太大以避免齿顶过窄。通常来说,平衡滑动率、平衡闪温和平衡弯曲疲劳寿命的变位是不相同的。因此,变位系数的值应该根据具体应用中最重要的因素来选择。
图15-1-21展示了不同齿数和不同变位系数对齿形的影响。任何一列可以看出齿数对齿形的影响。对于齿数较少的齿轮,轮齿的曲率较大,并且齿顶的齿厚较小,随着齿数的增加,齿顶厚增大,齿廓的曲率减小。对于具有直线齿廓和理论上齿数为无穷大的齿条来说,齿顶齿厚达到最大。

图15-1-21 变位对渐开线齿廓的影响
图中每一行显示了不同变位的齿形,顶部几行可以看出,齿数较少的齿轮,齿形受变位系数的影响比较大。对于齿数少的齿轮来说,变位的敏感性限制了变位系数的选择,因为变位太小将导致根切,相反变位系数太大,将导致齿顶过窄。例如,对于12个齿的齿轮来说,可接受的变位系数范围为0.4到0.44,x=0.4时,接近根切,x=0.44时,齿顶厚等于0.3个模数。相反,图15-1-21底部几行,显示了多齿数齿轮的齿形受变位影响的敏感性降低。也就是说,当为齿数比较多的齿轮选择变位时,齿轮的设计人员有较大的空间。
通常来说,齿轮的性能随着齿数的增加和最佳变位的选择而增强。对于已经确定了直径的齿轮来说,除了弯曲强度外,承载能力随齿数的增加和恰当的变位而提高。抗点蚀、胶合和划伤能力得到改进,通常齿轮运转也会更加平稳。另外,最大齿数受弯曲强度的限制,因为齿数越多,轮齿越小,弯曲应力越高。因此,为了保证足够的弯曲强度,齿轮设计人员必须限制小齿轮的齿数。在平衡点蚀和齿轮副弯曲强度的情况下,承载能力可能达到最大(见AGMA 901-A92)。一个平衡的设计,小齿轮有相对较多的齿。这使得齿轮副对变位相对不敏感,从而允许设计人员为小齿轮和大齿轮选择能实现最小滑动率、最小闪温或平衡弯曲疲劳寿命的变位。
3.5.6 齿根过渡曲线
对于展成加工的齿轮,过渡曲线是加工中自动形成的。由于塑料齿轮、粉末冶金齿轮应用的扩展,这类齿轮是由模具形成的,齿根过渡曲线如果处理得不好,会影响啮合性能。
(1)过渡曲线的类型
用齿条型刀具加工的时候,齿根过渡曲线,随变位系数、刀具齿顶圆弧的变化而变化。图15-1-22是在刀具齿顶圆弧固定时,不同变位系数的情况。图15-1-22a是齿条刀具参数。

图15-1-22 齿根过渡曲线与变位系数的关系
刀具齿顶圆弧中心轨迹如下:
①当x<(hfP-ρfP)时,齿根过渡曲线是延伸渐开线的等距线,见图15-1-22b、c;
②当x=(hfP-ρfP)时,齿根过渡曲线的曲率半径恰好等于齿条刀具齿顶圆弧半径,见图15-1-22d;
③当x>(hfP-ρfP)时,齿根过渡曲线是缩短渐开线的等距线,见图15-1-22e。
将齿条刀具变成齿轮型刀具,延伸渐开线变成延伸外摆线。
图15-1-22d的过渡曲线,在理论上是一个与刀具齿顶圆弧一样的圆弧,但是由于刀具是有限齿槽,不可能正好在那个位置有刀刃切削,可能由1~2个刀刃切出来。
(2)过渡曲线与啮合干涉
在AGMA相关标准和DIN 3960标准中,都十分注意一对齿轮啮合状况的图形。在ISO 1328-1:1995和我国GB/T 10095.1—2008和GB/Z 18620—2008中,也引入了这方面的概念。图15-1-23中A-B-C-D-E的符号已经规范,T1、T2分别表示啮合线与小齿轮和大齿轮的基圆的切点,DIN 3960—1987又增加了F1和F2两个点,表示小齿轮与大齿轮渐开线的起点,这个起始点直径在DIN 3960—1987中用dFf表示(与基本齿条齿廓中的hFfP符号的表示有关)。在一些国外图纸中,用“T.I.F”表示这个点。

图15-1-23 齿轮的啮合线
T1(2)——小(大)齿轮基圆与啮合线的切点,对应db1(2);F1(2)——小(大)齿轮渐开线起始点与啮合线的交点,对应dFf1(2);A——进啮点,大齿轮有效齿顶圆dNa2与啮合线的切点,对应小齿dNf1;E——出啮点,小齿轮有效齿顶圆dNa1与啮合线的切点,对应小齿dNf2;AE——啮合线长度,符号ga。εα=ga/pbt;AD=BE=pet=pbt[DIN 3960—1987(3.4.12)];AC——进啮点到节点的长度;CE——节点到出啮点的长度;dFa1(2)——小(大)齿轮与啮合线上的点F2(1)的直径
F1、F2点的位置与加工刀具有关,用滚刀、插齿刀最后加工为成品与磨齿是有差异的。对齿轮1,进啮点A是磨齿时的最大极限直径位置。对于没有根切的齿轮,用各点在啮合线上的位置表示,可以清楚看出啮合关系。
在DIN标准中,重视各点的直径大小;在AGMA中,重视T1点到各点的距离和各点的“滚动角”。按照AGMA 2101-C95的定义,滚动角(Roll Angles)就是该点到切点T1的距离(Ci)与基圆半径(Rb)的关系:εi=Ci/Rb。
将图15-1-23转化到真实齿轮的啮合关系得图15-1-24,图中将dFa1(2)与dNa1(2)都按da1(2)处理。图中给出了原始参数,齿轮相关参数用对应公式算出。着重分析啮合线上各点,国际上已经通用了的T1-F1-A-B-C-D-E-F2。在GB/T 10095.1中,将AF2定义为“可用长度”,AE定义为“有效长度”,这些参数在齿轮精度和齿轮修形都是不可少的。

图15-1-24 齿轮啮合干涉(啮入点,dFf1<dA1;啮出点,dFf2<dE2)
(3)齿条刀具齿根过渡曲线的图解与计算
图15-1-25的解释如下。

图15-1-25 齿轮齿根过渡曲线计算图解
1)D1~Dn是齿根过渡曲线,它是C1~Cn的等距线;
2)B1~Bn与b1~bn是对应的纯滚关系,即B1B2的弧长等于b1b2直线长度;
3)A0C0是刀槽纯滚点到滚刀齿顶圆弧中心的距离,这个距离随变位系数而改变,但是对确定了x后,这个数值就是确定的了;
4)A1C1=A2C2=A3C3=…=A0C0,这个可以视作是刚体连接;
5)B1C1→D1、B2C2→D2、B3C3→D3、…、BnCn→Dn,这个是图解法的核心,就是啮合基本定理,即共轭齿廓接触点的法线应当通过啮合节点;
6)以展开角φ0作自变量,按照纯滚动关系,很容易求得上述各点。
上面过程看起来很复杂,掌握了要领用程序实现起来是很容易的。
(4)对于塑料模具齿根圆弧替代注意事项
齿轮齿根圆角对于齿廓系数YF(YFa)、齿廓修正系数YS(YSa)有重要影响,对于传动载荷的传动中,在允许条件下,尽量将刀具齿顶圆弧做大。塑料齿轮也逐渐从运动传递到传递载荷发展,加大齿轮齿根圆角还便于注塑过程液体的流畅,有利于成型。
好多齿数少的齿轮,流行的处理方法是从渐开线基圆生成点作向心线,如图15-1-26所示,配对齿轮与替代直线产生了干涉。产生这种情况后,噪声增大。好多靠适当加大中心距,从设计角度是不合适的。

图15-1-26 齿根过渡曲线用直线、圆弧替代的干涉问题