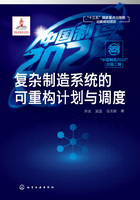
1.4 复杂制造系统的发展趋势
1.4.1 新一代互联网技术驱动下的制造系统发展趋势
遵循一般的科技发展规律,制造业也是受两种力量的驱动——技术的推动和需求的拉动,两者共同促成了制造业的发展。自从工业革命以来,制造业需求由早期强调制造的时间、质量和成本(Time,Quality,Cost,TQC),扩展到进一步对效率、应变、服务等的追求。制造相关的技术进步也走过了机械化、电气化、自动化、信息化的历程。伴随着需求的增强和技术的进步,制造业的发展经历了刚性自动线、柔性制造系统、计算机集成制造、敏捷制造等发展阶段。
进入21世纪,制造业迈入互联网时代,由互联网引发的新兴IT技术,包括物联网、信息物理系统(Cyber Physical System,CPS)、云计算和大数据等,使得制造业面临着进一步转型提升的机遇。一方面,社会发展对制造业提出了更高的要求,在追求TQCS(TQC和Service)的传统需求之外,越发强调对于节能、环保和适应力等方面的新需求;另一方面,新兴信息技术和新型IT设施与条件飞速发展和普及,先进的信息通信技术(Information and Communication Technology,ICT)和自动化技术也进一步发展融合,这一切都对制造业产生了深刻的影响。
在这样的背景下,涌现出一批制造领域的新理念、新思想。例如,“可重构制造”借助于快速调整制造的能力和制造的功能,来提升市场的响应能力;“分布式制造”用一种分布式的方式解决各类制造问题;“网络制造”把网络技术和不同的软件硬件集成在一起,寻找新的制造解决方法;“泛在制造”以泛在感知信息为基础,来实现工业生产的精细化控制;“预测制造”解决生产过程中不确定事件,提高透明度;“云制造”是一种面向服务的网络化产品的开发模式;“绿色制造”更强调环保、节能等。
对于新一代互联网技术驱动下的制造业变革,不仅学术界有非常活跃的新观点,近年来世界各国政府也都纷纷提出了自己的应对战略。例如,德国的工业4.0、美国的先进制造战略、日本的产业振兴战略、英国的重振制造业的战略等。我国也提出了中国制造2025战略,制高点就是制造业的数字化、网络化、智能化,切入点是加快信息通信技术和制造业的深度融合。可见,无论国内国外,都在以国家战略的高度积极应对制造业的新一轮发展机遇。
随着互联网与大数据等新一代信息技术在制造领域的全面渗透,复杂制造系统的生产经营管理模式及运行方式也呈现出新的发展特征。
①互联物联 借助于信息和网络技术与环境,构建虚实结合、互联互通的融合系统,为跨地域、跨层次、跨领域的信息共享与互联协作奠定基础。
②综合协同 从更大的系统范围和更全面的研究视角来考察复杂制造系统的运行与管理,包括:纵向上从经营、规划、执行到控制的上下贯通,横向上的全生命周期管理,以及生产、能源或者环保等不同领域的协同。
③智能化的方法 用智能优化的理论和方法处理复杂性,将制造问题与智能化方法相结合,增强制造系统自主分析和决策的能力。
④适应性效果 当来自外部需求和内部扰动的不确定因素影响到生产计划和调度方案的正常执行时,通过实时感知、科学分析和及时调整,提升对复杂制造不确定性的应对能力。
⑤基于数据 充分利用由大量离线和在线数据构成的工业大数据,通过数据分析和信息挖掘提炼其中蕴涵的价值,并进一步借助知识的表达、共享和更新提高制造管理的智慧化。
总之,通过自适应和协同,达到智慧制造的效果,代表着以新一代信息技术为支撑的未来制造模式的共同特点。具体在未来的制造场景中,纵向层面上,企业内部从上到下的信息高度自动化和集成化,达成从经营、规划、执行到控制各个环节的贯通;横向层面上,借助于跨生命周期管理、制造服务外包和全球供应链管理,也是一个有机贯通的协作体。
1.4.2 新型制造模式下计划调度的可重构意义
在新型制造模式下,信息通信技术和制造技术深度融合,使得制造资源和制造能力逐步远程共享,为使得制造系统能够根据加工产品的差异、加工状况的改变,进行自动、及时的调整,达到“自省”[23],需要计划与调度控制系统具有相应的“自适应”能力,首要的是能够“可重构”,其本质是计划调度信息集成系统的可重构,从而为达成具有自感知、自适应、自决策、自执行等功能的新型制造模式奠定基础。
可重构的概念最早来源于制造系统生产资源级的物理重构,为了响应市场需求的突然变化,迅速调整在一个零件族内的生产能力和功能性,快速改变制造系统的结构以及硬件与软件组元[24]。将此概念借用到生产计划与调度领域,则可将计划调度系统的可重构定义为:为了响应生产需求变化,以重排、重复利用、更新子系统的方式,实现快速调整计划调度方案的可变计划调度系统。其基本特点如下。
①模块化 计划调度的功能组件采用模块化设计。
②集成性 系统及其组件易于集成和更新。
③可转换性 计划调度层次内部功能组件的快速替换以及层次之间系统化调整。
④可诊断性 迅速发现计划调度过程中的关键问题。
⑤定制性 调整计划调度的功能以适应生产需求的变化。
在生产计划与调度的集成研究方面有三种主要的思路:集中集成、递阶集成与协同集成。制造过程包含许多动态、离散、随机的事件,整个制造系统是一个确定和随机混杂的系统,很多时候无法建立精确的解析模型,需要借助计算机仿真对系统进行模拟分析,可重构的计划调度体系结构的核心是模块化的开放式结构,将解析模型与计算机仿真结合起来,通过模块化设计,改变计划调度的配置,适应生产需求变化,易于集成和重构,同时具有递阶控制的稳定性与协同控制的柔性,是实现协同集成的较好方式。