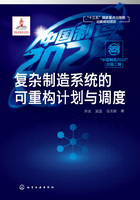
1.1 制造系统的复杂性
1.1.1 制造系统的分类与特点
制造系统按照产品加工路线的特征不同,可以分为:作业车间、流水车间与多重入制造系统。这三类生产制造系统分类及特点如表1-1所示。
按照产品生产工艺的特征不同,制造系统又可以分为连续制造和离散制造,它们各自的概念及特点如表1-2所示。
表1-1 生产制造系统分类及特点(按照产品加工路线特征的不同划分)

表1-2 生产制造系统概念及特点(按照产品生产工艺特征的不同划分)

制造系统还可以按生产组织方式的不同分为备货型生产(Make to Stock,MTS)和订货型生产(Make to Order,MTO),如表1-3所示。备货型生产基于对市场需求的研究和预测组织生产,生产出的产品不断补充成品库存,再通过库存满足用户的需求;订货型生产则是基于用户的订单组织产品的设计、装配和生产,又可细分为按订单组装(Assemble to Order,ATO)、狭义的按订单生产(Make to Order,MTO)和按订单设计(Engineer to Order,ETO)三类,如表1-4所示。各类生产方式的制造系统和用户交界面不尽相同,由图1-1可知,从MTS、ATO、MTO到ETO,用户介入制造过程的时间依次提前,相应地,订货提前期也逐次增大。而各类制造系统在产品产量方面的比较如图1-2所示。
表1-3 生产制造系统分类及特点(按照生产组织方式的不同划分)

表1-4 生产制造系统分类及特点(按照订货型生产方式的不同划分)


图1-1 不同生产方式对内特性的比较

图1-2 不同制造系统在产品产量方面的比较
关于制造系统的分类还可以有多种,比如按产品使用性能分为通用产品生产类型和专用产品生产类型;按照生产稳定性和重复性分为大量生产、成批生产和单件小批生产等。
本书将重点讨论一类具有重入性特征的离散型制造系统,按照复杂系统组成元素多且互相存在强耦合作用的定义,这是一类典型的复杂系统。
1.1.2 工业制造系统的复杂性
制造系统的复杂性可以从数量、关系、状态、信息等方面理解[1~4],包括工程复杂性和管理复杂性。工程复杂性是复杂制造系统的自然属性,体现的是系统细节复杂性。在企业生产管理实践中,表现为具有多个连续或平行加工的生产工艺流程,半成品和产成品种类繁多,生产时间、空间跨度大等。
管理复杂性是复杂制造系统的关系属性,体现的是系统动态复杂性。具体表现为:问题规模大带来的结构复杂性、约束条件多对应的过程复杂性、目标多样化体现的高耦合复杂性以及不确定因素多反映出来的制造环境复杂性。
①问题规模大 现实生活中的复杂制造系统大多具有设备数目多、产品种类多、在制品数目多、工件加工流程长等特点,因此,针对小规模问题的寻优方法一般不具备解决实际规模问题的能力。故而,针对实际复杂制造系统的生产管理决策通常只做满意决策,随着新兴信息技术的发展,找到满意决策的优良解空间的方法也在不断发展,再加上对实用性和计算成本的考虑,更使得对计划和调度的研究和设计没有止境。
②约束条件多 计划和调度问题求解过程中,受到物料、设备、工艺、时间、人员等多种因素的影响和制约:工艺约束指产品生产过程必须遵循加工工序的顺序及各工序的工艺参数要求;设备约束主要指生产过程受相关的设备产能、设备性能、设备加工方式等约束;时间约束指生产过程需满足工艺要求的加工时间和满足客户要求的交货时间。在实际生产过程中,以上各类约束大都具有不确定性,而且需要同时被满足,否则会带来质量、拖期等一系列问题。
③目标多样化 面向复杂制造系统的计划和调度问题往往是多目标的,大致可分为三类:设备相关的目标,如设备利用率、设备排队队长等;工件相关的目标,如准时交货率、加工周期等;生产过程相关的目标,如在制品数量、工件移动步数等。上述目标之间又存在着错综复杂的关系,在不同工况下可能体现为不同的耦合关系,而生产实际往往需要达到多个目标的协同优化,这也增加了复杂制造系统计划与调度的复杂性。
④不确定因素多 复杂制造系统中的不确定因素也是多方面的,比如,由于工艺特性等造成的加工时间不确定、由于市场需求波动引起的加工任务不确定(工件优先级变化、急件投放等)、由于设备故障或维修带来的生产资源不确定等。这些不确定扰动因素对生产过程的冲击,增加了复杂制造生产计划与调度的难度。