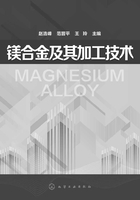
第2章 镁合金铸造成形技术
2.1 镁合金的熔炼技术
2.1.1 镁合金熔炼
2.1.1.1 液态成形镁合金的认识
(1)镁的合金化
①镁的合金化 纯镁的力学性能不高,不能满足工业对材料屈服强度和抗拉强度的要求。加入合金化元素能显著提高镁的力学性能,使镁合金的比强度在各类合金中仅次于钛合金而名列第二,为其工业应用开拓了广阔前途。镁合金材料从1808年问世到1886年始用于工业生产,其间持续了约80年。从1929年推出高强度MgAl9Znl即AZ91开始,镁合金的工业应用获得了实质性的进展。第一次世界大战时在德国广泛地使用了Mg-Al-Zn铸件。这种合金在潮湿环境中有腐蚀问题。1910年德国的Masing在研究镁和钾、锂及钠的相互作用中,发现镁锂合金具有超结构转变。在1925年发现加入少量(0.2%,质量分数)锰能增加合金的抗蚀性后,腐蚀问题才大大减轻了。后来发现锰的作用是使铁和其他杂质转移到害处较小的金属间化合物里去了。铸镁合金有很高的比强度(为14~16),仅次于铸钛合金和合金结构钢,比铸铝合金高,但大部分铸镁合金的屈服极限均远低于铸铝合金,因而降低了它承受载荷的能力。合金化元素的第二个作用是改善镁合金的工艺性能如铸造性能。纯镁的熔点高,流动性差,收缩量大。通过合金化能降低液相温度,增加流动性,提高镁合金的铸造性能,减小收缩倾向。针对镁合金在150℃以上温度其强度显著下降的特点,合金化的第三个作用是增强镁合金的抗蠕变性能。镁合金常用的合金化元素是铝和锌。铝的合金化能提高合金强度及铸造性能。锌也能提高合金的铸造性能。为保证铸造性能,压铸镁合金的铝含量>3%,锌含量<2%,否则容易产生裂纹。基于Mg-Al-Mn系的合金AZ91(含锌)和AM60B(不含锌)是室温使用的主要压铸镁合金。镁合金作为结构材料,很早以压铸件的形式进入汽车制造工业领域。铝和锌是往镁中最先添加的合金化元素,从而研制出工业上最早应用的镁-铝-锌系合金,铝是该系合金主要的强化组元,合金的强度随铝含量的增加而提高。以Mg-Al-Zn系为基的合金现在仍然是常温使用的镁铸件的主要材料。至今镁-铝-锌系合金大多仍广泛用作常温下工作的铸件和塑性加工制品。
②元素及作用 银和镉则分别起时效强化和固溶强化作用,银较稀贵,它们仅作为辅助强化元素。资料报道,加银后显著提高了室温及200℃以下的瞬时拉伸性能,对200~250℃的瞬时拉伸性能影响很小,而对250℃以上的瞬时拉伸性能和在200℃以上的高温长期性能却有一些不利的影响。属于此系的有美国QE22A合金,其成分为:1.8%~2.5%Dy,2%~3%Ag,0.4%~1%Zr。它有很好的室温和高温瞬时性能,其典型力学性能为:σb=275MPa,σ0.1=190MPa,δ=4%;,
,
。此合金是目前室温屈服极限(σ0.1)和100~300℃瞬时拉伸性能较好的铸镁合金之一,它还有很高的疲劳极限(σ-1=109MPa),一直到250℃还优于其他铸镁合金。它在200~250℃下的高温蠕变极限也略优于ZM-3合金,但它更适宜于作高强度或高温下短期工作的零件。其热处理规范(T6)为:在527℃保温4h,淬于80℃水中,在200℃时效8h。此合金的铸造性能也很好,铸件各处的力学性能比较均匀,与单铸试棒十分相近,它的抗蚀性,抗应力腐蚀性及焊接性也均良好。此合金因含Dy和银,故成本较高,且银是货币金属,限制了它的应用。王雪怡等以AZ102镁合金为研究对象,分析微量Ti对其组织、性能的作用机理,并对Ti的分布进行了分析。结果表明:Ti主要分布在α-Mg和β-Mg17Al12之间;随着Ti含量从0.1%到0.4%,合金铸态组织和晶粒尺寸显著减小,抗拉强度达到232.7MPa。
在镁-铝系合金中,元素硅、铜、铁、镍、钴、锡均为有害杂质,它们都会降低合金的抗蚀性。因为这些元素在镁中的固溶度很小,合金中只要有微小的含量就足以在δ(Mg)晶界上生成与基体有较大电位差的不溶相。其有害程度按上述次序逐渐增大,故在合金中其含量的限制亦按上述次序逐渐严格。除降低抗蚀性外,硅、铜还将降低合金的塑性,因为形成了热处理时不溶的Mg2Si等脆性相。上述这些杂质最易在熔铸工艺过程带入的是铁和硅,合金在熔炼时必然要和铁质坩埚、工具接触,铁在镁液中又有一定的溶解度,其溶解度还随着温度的升高而增加。为了减少合金中的铁杂质,希望熔炼温度最好不要过高,如要过热至高温,也希望时间尽可能缩短,并在合金中加入一定量的锰以除去铁。此外,还应注意防止过滤网、铁丝等混入炉料。为了防止硅杂质,应注意清理炉料,勿使炉料上带有砂子,因SiO2与镁液反应即还原出硅,并应注意勿使Al-Si合金混入镁合金的炉料,在同一车间熔化铝、镁两种合金时尤应注意这一点。王玲、赵浩峰等研究了铜元素对镁-锡-铝合金性能的影响,通过拉伸测试了合金的强度和伸长率,并进行了冲击试验。结果表明,合适的铜、锡等元素的含量,可使含镁合金的抗拉强度达到212MPa,伸长率可以达到22%,约是AZ91合金伸长率(7%)的3倍,冲击韧性可达21J/cm2,是AZ91合金冲击韧性(8J/cm2)的2倍多。王玲、赵浩峰等试验研究了Sn对环保型镁-锌合金钎料焊接拉伸性能的影响。拉伸实验表明,镁合金中加入Sn后,接头的强度大大提高;锡含量过高,强度又降低。锡造成合金强度下降的原因是镁-锡脆性化合物增多。
在各类镁合金中,镁-铝类合金(标准镁合金)由于生产工艺简单、价格低、综合性能较好而首先得到广泛应用。但这类合金条件屈服强度较低,使之承载能力不高;铸造时厚大处容易产生疏松和γ相的集聚,集聚的γ相热处理时不能完全溶解致使晶粒粗大,使性能大大低于薄壁处。虽然采取多种办法,例如变质、合金化等,但均不能根本消除。镁-铝类合金的工作温度一般仅为150℃;此外,许多其他性能要求这类合金往往也不能满足。为此,开发了许多镁合金系列,包括高强度的Mg-Zn-Zr系、耐热的Mg-RE-Zr和Mg-Th-Zr系、兼有高强和耐热的Mg-Ag-Nd-Zr系。稀土铸造镁合金较镁-铝系合金有铸件壁厚效应小、铸造性能好、工作温度可达250~300℃、无应力腐蚀开裂问题等特点。含银的富钕稀土铸造镁合金是长期以来广泛用于飞机、导弹的优质铸件。大力开发不含银的、铸造性能和综合性能更好的稀土镁合金是该系发展方向。减震的Mg-Zr系、综合性能优异的Mg-Y-Zr系等,也发展很快。总之,非镁-铝类合金的开发大大扩展了镁合金的应用范围。大力开发不含银的、铸造性能和综合性能更好的稀土镁合金是该系发展方向。其中英国开发的镁-钇-锆系(WE54,WE43)获得较好的效果。这些新型镁合金的共同点是多数含Zr元素,不同合金系Zr的作用也不尽相同。镁-锌-锆系铸造镁合金铸造性能、充型性良好,铸件也较致密。但是,合金在熔化和浇铸时形成氧化膜的倾向很大,在铸造形成复杂、输廓尺寸大而又薄壁的零件时很容易产生热裂缝。这一合金几乎是完全不产生显微疏松,结晶颗粒细而且均匀。合金对截面厚度的敏感性小,因而可以获得力学性能变化范围很小的零件。以锌、锆为主要合金化元素的铸造镁合金,具有强度高、成形性良好的特点。锌在镁中形成过饱和固溶体,时效时过饱和固溶体中析出弥散分布的细小MgZn质点,显著地强化了合金,并随锌含量的增加其强化作用增加。但锌含量的增加增大了缩松和热裂倾向。目前在研究高强度及耐热的镁合金方面,锆已成为主要的元素之一。锆在合金中形成大量难溶的α-Zr弥散质点,起着外来晶核的作用,细化了合金含量和枝晶,既有利于补缩又减少热裂倾向。加锆后显著缩小合金的结晶温度间隔。锆与氢在镁液中形成固态的ZrH2化合物,大大降低了镁液中的含氢量,有利于减轻缩松。锆还能与镁液中的铁、硅等杂质形成化合物下沉,除去杂质的有害作用,因此加锆能显著提高合金的力学性能和抗腐蚀性能。该系合金加入稀土等元素后,其组织由α-Mg加Zn-RE化合物共晶体组成,因而铸造性能得以改善,铸件的充型性、致密性有所提高,焊接性能也较好,显微疏松倾向降低。在砂型中铸造时所得到的组织是锌和锆在镁中的固溶体,以及沿着固溶体晶粒边界分布的Mg2Zn化合物。
锆的主要作用是细化晶粒,这样可减少铸造合金的壁厚效应;锆在镁中还有相当的固溶强化效果,故可全面改善合金的强度和塑性;锆的另一个重要作用是对合金的净化作用,这样就提高了合金的纯度,改善力学性能和抗蚀性能。由此可见,Zr的作用都十分重要,是新型镁合金的基础。例如,在Mg-6Zn合金中加锆可提高性能超过50%以上,见表2-1。含锆镁合金的系列、品种很多,因此生产工艺技术也有很大的差别,但它们有一些共同的要点。由于许多元素阻碍加锆,溶解锆量不足,而这些元素也都是高纯镁,要加以限制的。也就是说生产含锆镁合金最好采用高纯合金的炉料和熔炼技术,主要手段是防止有害元素在熔铸过程中进入熔体。另外,在加锆前把有害元素含量较高的熔体采取物理和化学方法去除,再通过更好的精炼技术手段除气、除非金属夹杂、除氯离子以达到高纯合金的要求。镁合金加锆的方法有多种,包括化合物加锆、混合盐加锆、中间合金加锆等。采用镁-锆中间合金形式加锆有较多的优点:使用方便、非金属夹杂少、合金化效果好。但这种方法其实是将困难留给了镁-锆中间合金的制造,因为制造中间合金仍然存在前述问题。此外,制造镁-锆中间合金还有操作不慎引起爆炸事故的危险。含锆镁合金生产过程的核心是加锆工艺。对于一般含锆镁合金而言,在制定合金的熔炼工艺时主要考虑如何保证获得合格的总锆量和溶解锆量,这就要求在加锆前将一切有害杂质尽可能去除,防止有害杂质进入,并保证锆在合金液中的均匀溶解。因此,合金熔炼的炉料保管准备、加料程序、温度控制、精炼操作、熔剂成分和炉前检验都与普通镁合金有明显的差别。对于特殊含锆镁合金,例如含钇、含钍的合金,则要分别考虑钇的高熔点、钍的放射性安全防护等,以制定合理的生产工艺。新型镁合金的共同点是多数含锆元素,而且锆在合金中起着重要作用。加锆又是生产含锆镁合金的主要问题,解决好加锆问题就能较顺利地生产大批新型镁合金。镁合金加锆实质是提高熔炼技术水平、镁合金高纯净化技术及合金化技术,是一项综合技术。
表2-1 Zr对Mg-Zn合金力学性能的影响

(2)类型 根据成形工艺,镁合金则可分为铸造镁合金和变形镁合金,两者在成分、组织性能上存在很大差异。铸造镁合金是目前应用最多的镁合金,其铸造方法主要有砂型铸造、永久模铸造、半永久模铸造、熔模铸造、挤压铸造、低压铸造和高压铸造等。铸造镁合金主要应用于汽车零件、机件壳罩和电器构件等。铸造镁合金多采用压铸工艺生产,其主要特点是生产效率高、精度高、表面质量好、铸态组织优良、可生产薄壁及复杂形状的构件等。较常见的铸造镁合金有Mg-Al、Mg-Zn-Zr、Mg-RE等系列。然而,铸造镁合金的力学性能不够理想,产品形状尺寸存在一定的局限性且容易产生组织缺陷,导致镁合金的使用性能和应用范围受到较大限制。铸造镁合金优异的性能使其应用会越来越广泛。卫爱丽、赵浩峰等讨论了镁合金的生产及应用。随着汽车需求量的逐年上升,镁合金的应用将具有巨大的潜力。要不断地开发新的、具有更多优越性能的镁合金来满足不同场合的需要。价格和生产技术是阻碍镁合金发展的两大因素,需不断完善和改进已有的成形方法开发新的成形技术。
按化学成分,一般根据镁与其中的一个主要合金元素将其划分为Mg-Al、Mg-Mn、Mg-Zn、Mg-RE、Mg-Li等二元系,以及Mg-Al-Zn(AZ)、Mg-Al-Mn(AM)、Mg-Zn-Zr(ZK)、Mg-Gd-Y(GW)等三元系及其他多元系。但铸造镁合金主要使用的是三大类。镁-铝系合金性能优良,不含稀贵元素,熔炼工艺较易掌握,生产成本较低,故应用较普遍,如ZM-5、ZM-10、AZ91A、AS41A、AM60A等。镁-锌-锆系合金的屈服极限比镁-铝系合金高,并且铸件各处有较为均匀的力学性能。此外,还可加入稀土、银、钍等元素以进一步改善它的性能。如ZM-1、ZM-2、ZM-7等。镁-稀土金属锆系合金中的Mg-RE-Zr系合金,可用于较前两类合金高的温度下工作,如ZM-3、ZM-4、ZM-6。根据是否含锆可划分为无锆镁合金和含锆镁合金两大类。现代镁合金按成分可分为两大系列,一类是镁-铝系如AZ81、AZ91(ZM-5),这些合金因为价格低廉会继续被大量使用,但要发展相应的高纯合金来提高其价值和扩大其应用范围。高纯镁合金要严格限制合金杂质如铁、镍、熔剂夹杂等的含量,目前我们采用的熔炼技术及设备尚存在明显的差距。另一类是含锆的镁合金,包括镁-锌-锆系高强度合金、镁-稀土-锆系和镁-钍-锆系耐热合金以及综合性能好的镁-钇-锆系合金。
热处理是改善或调整镁合金力学性能和加工性能的重要手段。镁合金的常规热处理工艺分为退火和固溶时效两大类。其中一些热处理工艺可以降低镁合金铸件的铸造内应力或淬火应力,从而提高工件的尺寸稳定性。镁合金能否进行热处理强化完全取决于合金元素的固溶度是否随温度变化。当合金元素的固溶度随温度变化时,镁合金可以进行热处理强化。根据合金元素的种类,可热处理强化的铸造镁合金有六大系列,即Mg-Al-Mn系(如AM100A)、Mg-Al-Zn系(如AZ63A、AZ81A、AZ91C和AZ92A等)、Mg-Zn-Zr系(如ZK51A和ZK6A等)、Mg-RE-Zn-Zr系(如EZ33A和ZE41A)、Mg-Ag-RE-Zr系(如QE22A)和Mg-Zn-Cu系(如ZC63A);可热处理强化的变形镁合金有三大系列,即Mg-Al-Zn系(如AZ80A)、Mg-Zn-Zr系(如ZK60A)和Mg-Zn-Cu系(如ZC71A)。某些热处理强化效果不显著的镁合金通常选择退火作为最终热处理工艺。镁合金热处理的最主要特点是固溶和时效处理时间较长,其原因是合金元素的扩散和合金相的分解过程极其缓慢。由于同样的原因,镁合金淬火时不需要进行快速冷却,通常在静止的空气中或者人工强制流动的气流中冷却。
(3)镁合金的合金化特点 考虑到镁的合金化一般都是利用固溶强化、沉淀强化和弥散强化来提高合金的室温及高温力学性能,因此其合金化设计应从晶体学、原子的相对大小、原子价以及电化学因素等方面进行考虑。选择的合金化元素应在镁基体中有较高的固溶度,并且随温度变化有明显变化,在时效过程中合金化元素能形成强化效果较突出的析出相。除了对力学性能进行优化外,还需考虑合金化元素对抗蚀性、加工性能及抗氧化性能的影响。在已得到应用的合金元素中,考虑合金化元素对二元镁合金的力学性能的影响。
按照强化或增塑的效果,镁合金的合金化元素可以划分为以下几类。按强度递增顺序为:Al、Zn、Ca、Ag、Ce、Ga、Ni、Cu、Th;按塑性递增顺序为:Tb、Ga、Zn、Ag、Ce、Ca、Al、Ni、Cu;只提高塑性,而对强度影响很小,如Cd、Tl、Li;牺牲塑性,但提高强度的元素有Sn、Pb、Bi和Sb。
按照强化机制不同,镁合金的合金化元素具有以下三方面的内容。原则与Al合金相似,固溶强化和时效硬化是主要强化手段,但作用没有Al合金那样明显。因此,凡是能在Mg中大量固溶的元素,都是强化镁合金的有效合金元素。根据合金元素的作用特点和极限溶解度,可大致分成两大类。一类是包晶反应类:Zr(3.8%),Mn(3.4%)。包晶反应型元素的主要作用是细化晶粒,但也有净化合金(消除杂质Fe)、提高抗蚀性和耐热性的作用。另一类是共晶反应类:Ag(15.5%),Al(12.7%),Zn(8.4%),Li(5.7%),Th(4.5%);稀土元素(RE):Y(12.5%),Nd(3.65%),La(1.9%),Ce(0.85%),Pr(0.5%),混合RE(以Ce或La为主)。共晶反应型元素是高强度镁合金的主要合金元素,如Mg-Al-Zn和Mg-Zn-Zr系合金等。这类元素形成的Mg4Al3(Mg17Al12)、MgZn2和Mg23Th6等在Mg中有明显的溶解度变化,是镁合金的主要强化相,有明显的时效硬化效应。
(4)主要合金元素在镁中的作用 Al:在镁中加入各种合金元素时,铝、锌、银、镉等元素有较好的强化效果。Al元素的含量对合金性能的影响极大,随着Al元素含量的增加,合金的结晶温度范围变小、流动性变好、晶粒变细、热裂及缩松现象等倾向明显得到改善,而且随着含铝量的增加,抗拉强度和疲劳强度得到提高。铝元素在镁中的极限固溶度为12.7%,并且随着温度的降低显著减少,室温下的固溶度为2.0%左右,利用其固溶度的明显变化可以对合金进行热处理。因铝在镁中这种较大的固溶度,并且铝原子与镁原子半径相差较大(铝比镁小13%),所以Mg-Al合金有较好的固溶强化效果。Mg-Al合金时效时,γ(Mg4Al3)相在基体晶界附近以层片状析出(类似于珠光体),并在晶内以细小弥散状析出,也有一定的时效强化效果。但是Mg17Al12在晶界上析出会降低其蠕变抗力,特别是在AZ91、AZ80合金中Mg17Al12的析出量很高。在铸造镁合金中含铝量可达到7%~9%,而变形镁合金中含铝量一般控制在3%~5%。在Mg-Al-Zn系合金中铝是主要组元,是在Mg-Al的基础上再加入锌和其他组元。Mg-Al系共晶成分为32.3%Al,在437℃发生共晶反应:L→δ(Mg)+γ(Mg4Al3)。δ(Mg)固溶体的最大固溶度为12.7% Al。不平衡状态的固相线和铝在镁中最大固溶度点移动[移至(4%~6.5%)Al]。当铝量>8%时,合金的铸造性能比较好,并且随着铝量的增加而进一步改善。当铝量大于4%~6%时,随着铝量的增加,合金的结晶温度间隔逐渐缩小,其铸态组织中的δ+γ6(Mg4Al3)共晶体量则逐渐增多,所以合金的铸造性能不断改善。同时,由于结晶时铝富集于晶界(因分配系数K0=Cb/Cl),能减缓δ(Mg)固溶体晶粒的长大,故铝量增加时合金的晶粒逐渐变细,也有利于降低热裂和缩松倾向。因此从合金的铸造性能来说,铝量≥8%时较好。铝量变化对Mg-Al合金力学性能的影响研究表明,在T4状态随着铝量的增加,合金的强度(σb)及条件屈服强度(σ0.2)均不断增加。与铸态相比,高铝量的合金在经淬火(T4)后力学性能有很大的提高,这是由于铝原子半径与镁原子半径相差较大(相差约13%),而且铝在镁中的固溶度又比较大(最大固溶度达12.7%),铝溶入δ(Mg)固溶体后其晶格产生很大的畸变,因此铝对镁有较高的固溶强化效果。研究表明,当铝量>9%时合金的强度和延伸率将发生突然的下降,其原因是铝量大于9%时,γ相溶入δ固溶体的溶解速率将大大下降,在通常的热处理保温时间内,其组织中常有未溶的脆性γ相分布于δ相的晶界,使力学性能显著下降。当铝量大于9%,合金热处理时γ相溶解速率变慢的原因在于溶入δ相中的铝原子较多,显著阻缓原子的扩散;当铝量较高时,组织中的γ相较为粗大,数量也较多,使其溶解变慢。因此,从合金的力学性能来说,虽然也希望铝量尽量高些,但一般应不大于9%。Mg-Al合金在T6状态的力学性能与铝量间的关系曲线与T4状态十分相似,所不同的只是T6状态的条件屈服强度(σ0.2)较高,而延伸率(δ)值则较低。故上述结论也适用于T6状态。
综上分析,为兼顾合金的铸造性能和力学性能,铝量应取8%~9%。但在实际生产中,铸件后凝固处的组织中常存在有较多量的γ相,其尺寸也较粗大。这是因为Mg-Al状态图有较大的结晶浓度间隔,后凝固的合金液中含铝量较多,故在铸件厚大处的中心部位铝量较高,此即铝的正偏析现象;此外,铸件厚大处冷却较慢,晶粒比较粗大。这些都使壁处的γ相比较粗大,数量也较多。在热处理时厚壁处的γ相常不能完全溶解,显著降低了该处的力学性能,为了防止和减轻这种情况,通常将铝量定为8.0%~8.5%。在Mg-Al合金中随铝量的增加其抗蚀性也有所降低,这是因为其组织中的γ相与δ(Mg)基体间的电位显著不同。
Zn:锌元素在镁中固溶度约为6.2%,其固溶度随温度降低而显著减少。锌提高合金应力腐蚀的敏感性与镁合金的疲劳极限。锌元素含量大于2.5%时则会对合金的防腐性能产生不利影响,原则上含Al镁合金中,锌元素含量一般控制在2%以下。在Mg-Zn-Zr系合金中锌是主要组元。共晶成分为51.2%Zn,在340℃发生共晶反应:
L→δ(Mg)+β(Mg7Zn3)
温度下降至312℃时又发生共析反应:
β(Mg7Zn3)→δ(Mg)+γ'(MgZn)
理论分析表明,Mg-Zn系的结晶温度间隔较Mg-Al系大得多,这是Mg-Zn二元合金的铸造性能较差的一个重要原因。Mg-Zn二元合金在不平衡状态下的最大结晶温度间隔处的成分约为3.5%Zn。当锌量大于3.5%时,随着锌量的增加,合金组织中的共晶体量亦增多,按一般理论来说,合金的热裂和缩松倾向似乎也应不断下降,但实际情况却并非如此。试验表明:当将Mg-Zn-Zr合金中的锌量由2%增至6%时,其缩松和热裂倾向均不断增加。对于锌量增加时缩松倾向反而增大的原因,有人解释为:当合金中含锌量增高时,其后凝固的富锌的合金液的密度亦增大,而先凝固的δ(Mg)固溶体晶体的密度却比较小,在凝固过程中就容易使δ(Mg)晶体不断上浮,而富锌的合金液却向下移动,在一定的小范围内,中间不容易得到补缩,因此锌量升高时反使缩松更加严重。同时,锌量增多时还会使合金组织中出现粗大的树枝状晶体,例如,含8% Zn时,即使合金中有锆存在也不能使树枝晶消除,而粗大的树枝状晶体亦将促使缩松加剧。锌量增加时合金的热裂倾向变大,可能是由于Mg-Zn共晶体中的γ'(MgZn)相具有热脆性,同时锌量增加时合金的缩松加剧也使合金容易热裂。正因为如此,和其他系镁合金相比,Mg-Zn系合金的热裂倾向一般来说是比较大的。
锌对镁有很好的时效强化作用,Mg-Zn合金时效时,过饱和固溶体中析出弥散分布的细小的γ'(MgZn)相质点,显著地强化了合金。随着合金中锌量的增加,其强化作用也不断地增加;当锌量增加到5%~6%时,其强度(σb)和条件屈服极限(σ0.2)均达到最大值,锌量更多时由于其在热处理时不能再溶入δ(Mg)固溶体中,所以σb和σ0.2也不再继续增加。目前应用最多的是Mg-Al和Mg-Zn两类合金。由于Mg-Zn合金的铸造性能较差,故Mg-Al类合金最先得到发展和广泛应用。在Mg-Al合金中加入少量锌后,能大大提高合金的抗蚀性,还可提高合金在T6状态的条件屈服强度(σ0.2),对T4状态下的强度(σb)和条件屈服强度(σ0.2)及T6状态下的强度(σb)也略有影响,故在Mg-Al合金中加锌是有利于合金性能的。另一方面,Mg-Al合金中加锌后显著增大了合金的结晶温度间隔,例如,在Mg-8.5% Al合金中加入2%Zn后,其不平衡结晶温度间隔增加了约40℃,因而使合金的缩松倾向显著增加,因此加锌量一般都小于1%。由上述可知:从力学性能角度来看,锌量为4%~5%比较有利,过低则对强度不利,过高又使塑性过于降低;再从铸造性能角度来看,锌量低些(低于5%)较为有利,过高则使缩松、热裂倾向增大。赵浩峰等研究了锌元素对镁-锡合金塑性的影响。实验合金在电阻坩埚炉中熔制,镁合金成分有1%~5% Sn和1.0%~4.0% Zn,并含适量钙、硅和铅。拉伸强度测试和冲击试验表明,合适的锌和锡含量可使含镁合金的抗拉强度达到190MPa,伸长率可以达到18%,约是AZ91合金的伸长率(6%)的3倍,冲击韧性可达20J/cm2,是AZ91合金冲击韧性(9J/cm2)的2倍多。锌和锡元素的结合对镁合金的力学性能改善有较大的促进作用。卫爱丽、赵浩峰等研究了新型镁-铝-锌合金的性能,分析了不同含量的Al、Zn、Pb等元素对镁合金性能的影响。结果表明,随着Al含量的增加,合金的冲击韧性下降而硬度提高;随着Zn含量的增加,冲击韧性和硬度都下降;而随着Pb含量的增加,合金的冲击韧性和硬度都提高。
Mn:Mn通过除去镁合金液中的铁及其他重金属元素、避免产生有害的金属间化合物来提高Mg-Al合金和Mg-Al-Zn合金的抗海水腐蚀能力,在熔炼过程中部分有害的金属间化合物会分离出来。在镁合金中添加Mn并不能提高合金的抗拉强度,但是能轻微改善屈服强度。镁合金中锰的含量通常低于1.5%,而在含铝的镁合金中,锰的固溶度仅为0.3%。此外,锰还可以细化晶粒,提高可焊性。Mg-Al合金中加入少量锰后,大大提高了合金的抗蚀性,其原因是:①锰降低了铁在镁液中的溶解度,使铁以Mn-Fe化合物形式从镁液中沉淀出来,因而减少了合金中有害于抗蚀性的杂质铁的含量;②锰溶入δ(Mg)固溶体后提高了它的电位,使其不易被腐蚀。此外,锰的存在对细化合金的晶粒是有利的。但锰量不能过多,否则将引起锰偏析而显著降低力学性能,通常锰量不大于0.5%。赵浩峰等试验研究了Mn含量对镁合金耐蚀性的影响。通过PS-1型恒电位恒电流仪对不同Mn含量的镁合金进行腐蚀试验,并通过金相检验和X射线对合金的组织和结构进行了分析。结果表明,在一定的Mn含量范围内,Mn能够有效提高镁合金的抗环境腐蚀作用。张志强等通过对不同含Mn量的Mg-6 Al-xMn合金进行熔炼、制坯和反向挤压,研究Mn含量对Mg-6Al镁合金组织与力学性能的影响。实验表明,在试验范围内,随着Mn含量的增加,Mg-6Al-xMn合金凝固组织逐渐细化,β-Mg17Al12相逐渐减少,而出现Al-Mn相,晶粒大小由含Mn量0.3%(质量分数)时的137μm减小到含Mn量0.9%时的73μm,幅度降低为47%。不同含Mn量的Mg-6Al-xMn合金经400℃、12h均匀化处理后,β-Mg17Al12相消失。不同含Mn量的Mg-6Al-xMn合金经挤压后,挤压棒材的晶粒也随Mn含量的增加而逐渐变小;挤压棒材的抗拉强度、屈服强度和延伸率均随着Mn含量的增加先增加后降低。Mn含量为0.5%的挤压棒材抗拉强度和屈服强度最高,分别为293MPa、173MPa;Mn含量为0.7%的挤压棒材延伸率最大,达20%。
Si:硅可改善压铸件的热稳定性能与抗蠕变性能。因为Si可与Mg在晶界处形成细小弥散的析出相Mg2Si,它具有CaF2型面心立方晶体结构,有较高的熔点和硬度。20世纪70年代德国大众公司开发成功了替代AZ80生产其Beetle空冷发动机曲轴箱的AS系耐热压铸镁合金(AS41和AS21),该合金可在150℃以下的场合工作。AS系耐热压铸镁合金的强化机理为晶界处形成细小弥散分布的稳定析出相Mg2Si,它具有CaF2型面心立方结构,较高的熔点(1085℃)和硬度(HV460)、较低的密度(1.9g/cm3)和热膨胀系数(7.5×10-5K-1)。AS41A合金含4.3%Al、1%硅、0.35%锰,合金的蠕变强度在170℃范围内,大大改善了合金在150℃以上的抗蠕变能力,同时具有较好的伸长率、屈服强度和极限抗拉强度。由于含铝量较低,AS41A要求较高的铸造温度。AS系列镁合金由于Si的引入,在组织中易形成硬的硅质点,钠和锶能从根本上改善硅相的结构,起到很好的变质效果。AS21的蠕变强度和抗蠕变温度高于AS41,但室温抗拉强度、屈服强度和铸造性能却较差。AS41在温度高达175℃时的蠕变强度稍高于AZ91和AM60,且具有较好的伸长率、抗拉强度和屈服强度,大众公司用AS41生产的零件还有风扇壳体和发动机支架。AS系镁合金的缺陷在于:a.压铸性能差,合金的流动性随含铝量降低而变差,同时硅提高了液相线温度,因而浇铸温度要求较高;b.不能用于砂型铸造,因为铝不仅改变了Mg-Si相图的共晶温度和共晶成分,而且还影响Mg2Si相的形态,在铝含量较低时,共晶Mg-Si相易呈汉字形,因而会降低合金的强度和韧性。
Zr:镁-铝-锌系合金、镁-锰系合金因屈服强度低和晶粒粗化倾向性大,促使对镁合金进一步开展研究。1937年德国人索尔沃尔德(F.Sauerwald)发现锆对镁有强烈细化晶粒的作用,发现了加锆能显著改善Mg-Zn合金的工艺性能和力学性能。经过相当长的时间找到了一个锆和镁合金化的可靠方法,解决了加锆工艺问题,Mg-Zn合金才得到广泛的应用。由于锆的细化效果使强度显著提高,镁-铝-锌系的铸造合金和变形合金也相继问世并得到大量应用。锆加入Mg-Zn合金中,能缩小结晶温度间隔,并能细化晶粒,起变质作用,对固溶体也有一定的强化作用。从含锆镁合金发展历史来看,怎样加锆,是生产含锆镁合金的主要问题,也就是说解决了镁加锆问题就解决了大批新型镁合金的主要生产问题。1937年,人们发现在Mg-Zn类镁合金中加锆能显著使晶粒细化,但由于加锆工艺没有解决,并没有得到实际应用,直到1947年才初步解决了加锆工艺。目前,加锆工艺仍然是含锆镁合金生产中的关键问题。镁合金加锆的主要困难在于:锆熔点高(为1850℃)、密度(为6.5g/cm3)大,而镁的熔点为651℃,密度为1.74g/cm3,因此锆加入镁合金中呈固态,难以溶解;加之和镁液密度差大,易于沉淀或形成密度偏析;锆在镁及镁合金液中溶解度小,在镁液中为0.6%,在镁-锆合金液中<1%。这造成既难于把锆加入镁形成合金也难于以此制造成分均匀的镁锆中间合金;锆的化学活性很强,高温易和大气或炉气中的O2、N2、H2、CO2、CO反应,生成不溶化合物(ZrO2、ZrN、ZrH2、ZrC),使锆损耗增加;许多元素阻碍加锆,镁液中的Fe、Al、Si、Mn、Co、Ni、Sb、P、H等均能和锆形成不溶化合物(Fe2Zr、Al3Zr、SiZr2……),并在坩埚底部沉淀,因而降低了合金液中的含锆量。由于以上几个方面的障碍,对含锆镁合金熔炼工艺的要求很严格。有许多因素尚不被认识,例如,可溶锆量分总锆量和溶解锆量的控制,其中溶解锆量是有效锆,如溶解锆量不足,既使总锆量足够,仍不能保证镁合金的性能,当然总锆量也必须保证。值得注意,最有效的晶粒细化剂,对于含Zn、Ag、RE、Th的镁合金,可添加Zr细化晶粒,改善性能;但对于含有Al、Mn的镁合金不能加Zr进行晶粒细化。因为Zr会清除掉熔体中的Al、Mn和Si等有益元素。
由于Mg-Zn二元系合金的结晶温度间隔较大(特别是不平衡状态下),其最大不平衡结晶温度间隔达290℃,故二元合金的铸造性能很差。但在Mg-Zn合金中加入少量锆后,便显著改善了合金的铸造性能,尤其是大大地降低了合金的缩松倾向,并使铸件中的缩松比较集中在铸件壁的中央,这样分布的缩松对铸件的力学性能影响较小。资料表明,加锆能改善合金铸造性能的原因如下。一是锆与镁组成包晶型反应,其状态图形式类似于Al-Ti状态图,在包晶温度下镁液中仅能溶解约0.6%的锆,当合金中加入锆量大于包晶成分时,即能在镁液中形成大量难熔的α-Zr弥散质点。由于α-Zr与δ(Mg)均为密排六方晶格,晶格常数十分相近[δ(Mg):a=3.20Å,c=5.21Å,α-Zr:a=3.23Å,c=5.14Å],故这些α-Zr质点就起着外来晶核的作用。因此加锆能对合金起变质作用,细化δ(Mg)的晶粒,这样既有利于补缩,又能减少热裂倾向。二是加锆后显著缩小了合金的结晶温度间隔,例如,在Mg-4.5Zn合金中加入0.7%Zr后,其平衡状态的结晶温度间隔由180℃降至170℃,不平衡状态的结晶温度间隔则由290℃降为110℃。三是锆与镁液中的氢形成固态的ZrH2化合物,大大降低了镁液中的含氢量,也有利于减轻缩松。由于加锆能细化晶粒和晶枝,并对δ(Mg)固溶体有一定的强化作用,因而可显著提高合金的力学性能。随着含锆量的增加,其力学性能也不断增加,但锆量不可能加得很多,因为即使温度升高锆在镁液中的溶解度也是不大的,加入过多的锆,均将沉于坩埚底部。由于锆能与镁液中的铁、硅等杂质形成化合物下沉,故有去除铁杂质的作用,并且它还能在合金表面生成致密的氧化膜,因此加锆后显著提高了合金的抗蚀性。在含锆的镁合金中,既规定了总锆量,又规定了“溶解锆”量。在化学分析时,合金中的锆有一部分溶入酸溶液,这部分锆就叫作“溶解锆”,另有一部分锆呈小颗粒状不溶于酸溶液,这部分就叫作“单体锆”,两部分锆的总和即为总锆量。通常认为“溶解锆”大致就是对晶粒细化起作用的那部分锆,“单体锆”中部分是较粗大的锆晶体,部分则可能已是锆与氢、铁等杂质起反应而生成的化合物。故在生产中应重视控制“溶解锆”量。在实际生产中除了应控制“溶解锆”量外,还应作断口检查以控制合金的晶粒度。实践表明,“溶解锆”量最好能保持在0.6%以上,以保证合金有较细的晶粒。
Ca:可细化组织,但是Ca含量超过1%时会产生热裂倾向。Ca会影响合金的腐蚀性能。有关Mg-Ca系合金时效析出过程的研究还不充分,一般认为时效过程可以析出六方晶Mg2Ca稳定相。此外,向Mg-1%Ca合金中添加1%Zn后,时效强化效果会显著增强。Ca与镁形成具有六方MgZn2型结构的高熔点的Mg2Ca相,使蠕变抗力有所提高并进一步降低成本,在改善镁合金的蠕变性能方面起了重要作用。前苏联报道了Ca加入Mg-Al-Zn砂型铸造镁合金中可提高合金的抗拉强度和蠕变性能。随后,开发了可在150~200℃铸态下长期工作的镁合金(5.0%~6.5%Al,0.3%~0.5%Zn,0.3%~0.6%Mn,0.2%~0.5% Ca)。但最近的研究表明,钙的加入量超过1%(质量分数)易产生热裂。Mg-3%~9% Al-1%~5%Ca的系统实验研究表明,Ca能提高350℃以下的高温硬度。当Ca/Al>0.8时,除Al2Ca外,还会析出Mg2Ca耐热相使合金在在中温条件下具有优异的耐热性能。此外,Sr(加入量通常为1/5Ca)、Ba的性质与Ca相近。
Be:铍在镁中的固溶量极微,但应用很微量的铍(通常为0.0015%~0.005%)可以使镁熔融体的燃烧降到最低限度,同时减少氧化,这样就降低了铸件中裹住夹杂物的概率。在这种浓度下对呈压铸状态的合金力学性能没有影响。其保护作用的机理在于铍对通常的氧化膜的变质作用,使它更能抗扩散,因而更能保护其底层的金属不再受氧化。铍以小的含Be 1%(质量分数)或5%(质量分数)的铝中间合金V形块或小球的形式加入到熔融金属中,然后通过搅拌而溶解。用化学分析和观察熔融金属表面上存在的任何氧化物对燃烧的抑制两方面来监控回炉料的使用量。另一种方法是使用已含铍的合金锭,用铍处理过的合金只适于压铸,而不适用任何其他铸造方法。由于铍对于镁是表面活性元素,故在镁合金中加入微量的铍时,铍即富集在表面并优先氧化而在合金液面形成一层致密的氧化膜。前面已经提到:镁液表面的氧化膜是疏松的,因为镁氧化生成MgO后其体积是缩小的,其a值为0.79,而铍氧化成BeO后其a值为1.71,故铍氧化后即可充填MgO膜的空隙,使其致密,阻止合金液继续氧化。因此在镁合金中可加微量铍以提高镁液的抗氧化能力。但铍的加入量不宜过多,过多将引起晶粒粗化,恶化合金的力学性能,并增大热裂倾向。砂型铸造时铍量一般应≤0.002%;金属型铸造时由于冷却较快,故铍量允许较多些(≤0.01%)。铍的抗氧化作用在镁液温度高于750℃时将大为降低,故加铍一般只作为防止镁液氧化的辅助措施。铍的价格甚贵,故非必要时可不用。
Cu:朱红梅等利用光学显微镜、扫描电子显微镜、透射电子显微镜、X射线衍射仪、电子探针、拉伸测试仪研究Cu元素的添加对铸态ZK60镁合金显微组织和力学性能的影响,并讨论了添加Cu改善合金拉伸性能的机制。实验表明,Cu可有效消除ZK60镁合金中存在的晶内偏析,随着Cu含量的增加,合金的晶粒尺寸得到明显细化。在含Cu镁合金中,出现了一种具有面心立方结构的Mg-Zn-Cu三元共晶相,该相主要富集在晶界处且在合金发生塑性变形时成为微裂纹源。拉伸实验表明,当Cu添加量为0.5%~1%时,ZK60镁合金的力学性能得到改善,当添加量达到2%时,合金的力学性能下降。
(5)镁合金液态成形性能
①凝固特点及缩松、热裂 铸镁合金结晶温度间隔一般都比较大,其组织中的共晶体量较少,体收缩和线收缩均较大;镁的单位体积的比热容和凝固潜热都比铝小(分别为铝的75%和36%);镁的密度较轻,镁液的压头较小等。由于这些原因,铸镁合金的铸造性能较铸铝的差,其流动性约为铸铝的1/5,热裂、缩松倾向也较一般铸铝合金大得多,易产生缩松、热裂等缺陷。在压铸条件下,由于液态金属的流速高,金属型冷却作用强,冷却速率很快,二元系相图中共晶点向热稳定组元方向推移。对Al合金而言是向Si增加的方向推移,而对Mg合金来说则是向Mg增加的方向推移。这种推移可以使部分亚共晶的Al合金成为固溶液体单相合金,使部分过共晶的Al合金成为亚过晶合金。Mg合金则正好相反,部分固溶体合金成为亚共晶合金,部分亚共晶合金则成为实际上的过共晶合金。高的冷却速率增加Mg合金共晶体的含量,有利于铸造。另外,比较纯镁和纯铝的熔点与共晶温度的差值,也表明了镁合金易于铸造,对镁而言其值为212℃,而铝则是73℃。
②流动性 从工作温度到凝固温度之间的热量,决定了相同的热导率下,金属液保持可铸性的时间。因此这种热量便作为最大可能充型时间的尺度。充填同一铸型时,镁合金所需的时间为铝合金的65%。用雷诺数来表示充填性能,它不仅考虑到流道的几何形状,而且也考虑到由于速度摩擦而产生的流动阻力。若以GD-MgAl9Zn1和GD-AlSi12(Cn)合金的黏度作比较,得出流动速度,镁合金充填型腔的平均速度约为铝合金充填型腔时的1.25倍。
③吸气倾向与气孔 镁液很易与铸型、工具、熔剂中的水分反应,生成的氢即溶于镁中。由于氢在镁中的溶解度在凝固时有很大的降低,所以也会形成气孔。气孔以各种方式存在于铸件中,一些是冷却过程中气体从液体中析出,主要是H2;另一些是由于浇铸而带入的空气。镁溶解氢的能力很强,即使铸锭上只有极少量的一点水分,也可能通过水的还原而吸收氢。氮易产生氮化物,而氧产生氧化物。因此,大气的影响较小,空气的温度与气体含量有关,也就是镁块必须进行彻底的烘干才能投炉熔化。合金中的气体问题曾有一阶段未引起足够重视,因大部分铸镁的缩松倾向较大,在生产上气体的影响常表现为缩松程度的加剧,难以引人注意,疏松与气孔间很难截然分开,因此常常掩盖了气孔的问题。而且由于镁液凝固时氢在其中的溶解度的相对变化值比较小(仅为固态镁中氢溶解度的0.4倍),其溶解度变化程度约为铝的1/45,这说明镁液凝固时氢气析出的倾向不如铝强烈,因此在冷却较快的铸件薄壁处氢很易过饱和地溶于镁中而不形成气孔,铸件厚壁处在使用冷铁及冒口时易使部分氢被排至冒口中去,部分则过饱和地溶于较快冷却的铸件表层中。因此,气孔问题在生产中表现得不突出。但由于对铸件质量要求日益增高,而且由研究得知,镁合金中的气体常常加剧疏松,故对镁液的除气的研究日益重视。许四祥等利用镁合金定量金相技术和场扫描电镜研究了铸造镁合金中微孔的组织形态及其形成机理。结果表明:随镁合金试样厚度的增加,微孔的量增多,同时微孔的组织形态也由细小的针孔变为显微气缩孔。微孔不同的组织形态是热力学和凝固机理交互作用的结果。
④镁合金在铸造工艺方面的适应性 镁合金在铸造工艺方面具有较大的适应性,除砂型铸造外,根据各类合金的特性和零件的要求,可以采用金属型铸造、压力铸造、壳型铸造、石膏型铸造、低压铸造以及冷凝树脂砂型铸造等几乎所有特种铸造工艺。铸件中的细小油路通道,可以采用预先在铸型中放置特种玻璃管和金属丝编织套等,然后再从铸件中除去的方法而获得;也可以采用直接在铸件中埋设不锈钢管的方法获得。熔融镁对坩埚的侵蚀小,压铸时对压铸模的侵蚀小,与铝合金压铸相比,压铸模使用寿命可以提高2~3倍,通常可以维持20万次以上。镁合金的铸造性能良好,镁合金压铸件的最小壁厚可达0.6mm,而铝合金的为1.2~1.5mm。镁的结晶潜热比铝的小,在模具内凝固快,其生产率比铝压铸件高。粘模倾向是指铸造合金黏附在铸型上的倾向。这种现象对压铸过程的影响很大。合金对铸型材料的溶解度方面,镁合金具有优越性。一般模具钢的主要合金元素,除镍外,其他如铁、钴、锰、铝、钙都不溶解或仅有微量溶解于镁合金,因此粘模不会产生。约300℃时,镁合金的铸件在脱模温度时的强度为铝合金的一半左右,只要型腔表面没有问题,推出平衡,不产生剪切应力,这样的热强度足以保证铸件出模。当摩擦副之间的粗糙度为30μm和摩擦速度为0.1m/s时,铝-钢之间的黏附系数为0.1,而镁-钢之间仅为0.05。由此可知,镁合金有很大的优点。因此镁压铸件可以用最小的脱模斜度,并可获得较高的精度。
⑤其他性能 由于铸镁在弹性系数、屈服极限、抗剪强度等方面均较铸钢、铸铝为低,故在铸件设计中常用加强筋、波纹形结构等以增强其刚度和承受载荷的能力。铸镁的缺口敏感性较高、铸造性能较低(易产生缩松、热裂),故铸件的壁厚变化应较平缓,并应避免出现尖角。铸镁合金(尤其是合金元素含量低的Mg-0.7 Zr合金)有很好的滞振性,故可用作电子仪器的底座。
镁的弹性系数(43000MPa)不高,约为铝的60%,钢的20%。当铸件尺寸相同时,镁铸件具有较低的刚性。当受同样外力时,镁铸件能产生较大的弹性变形,因而在受冲击载荷时能吸收较大的冲击功。正是由于这个原因,它常被用来作飞机的轮毂,民用工业中常被用作风动工具的零件。在某些场合下,用镁合金作高刚性的航空零件十分有利。例如,原来为铝制的蒙皮铆接结构的导弹弹翼改为4.5~6mm壁厚的整体镁铸件后,因为镁的密度比铝小,所以在零件重量相同的情况下,镁铸件由于增加了壁厚,其刚性比原来的铝蒙皮铆接结构件要大得多。
耐热铸镁合金在高温力学性能的绝对值方面要比耐热铸铝合金略低些,但在单位重量的高温性能方面却较铸铝为高,所以航空上耐热铸镁合金的应用亦日渐增多。大多数耐热铸镁合金的工作温度在260℃以下,少数铸镁合金可达300℃。由于高温下镁合金的刚性下降较多,而且其膨胀系数也比较大,故在设计高温工作的镁铸件时应予注意。
镁的标准电极电位较低,而且它的表面形成的氧化膜不致密,故抗蚀性较低。镁在潮气、海水、无机酸及其盐类、有机酸、甲醇等介质中均会引起剧烈的腐蚀,故镁铸件常需进行表面氧化处理和涂漆保护。镁零件在装配中应避免与铝、铜、含镍钢等零件直接接触,否则会引起电化学腐蚀,可用塑料、橡胶或涂料作衬垫来隔离。镁合金的化学腐蚀实质上是镁被氧化成氧化镁或氢氧化镁的电化学和化学过程。从热力学角度看,不同价态的镁及其化合物的电化学电位和自由能都要比单质镁低得多。由此可见,镁的腐蚀过程是自发的、极易发生的,且是不可逆的。镁在潮湿空气及水(尤其是海水)中的化学性不稳定;与大多数无机酸的相互作用剧烈,但不与苛性碱溶液起作用;对硒酸、氟化物、氢氟酸作用稳定,能生成不溶性盐;在汽油、煤油、润滑油中也很稳定。镁合金在干燥空气中有良好的耐腐蚀性能,在普通工业气氛中的耐蚀能力接近于中碳钢,而在盐雾严重的海洋性气氛中则比铝合金低,但明显高于中碳钢。镁铸件经过表面处理后能在大气条件下长期使用。近期发展并应用的镁合金具有极低的铁、镍等杂质含量,所以有耐腐蚀性能;这类镁合金在耐蚀性方面优于美国的380压铸铝合金,比铝-锌-镁系压铸合金好得多。
除了化学及电化学腐蚀外,镁合金还普遍的存在应力腐蚀开裂现象(SCC),即镁合金在几乎不腐蚀的环境介质中,在拉伸应力尚未达到屈服强度一半的情况下仍有可能发生开裂现象。导致这种原因的因素有很多,如工作时构件的受力,热胀冷缩引起的应力,工件装配过程中的扭、压、撞等引入的应力,构件生产的过程以及热处理、成形、机械加工等引入的各种应力。点蚀是AZ91镁合金在该实验体系下的裂纹萌生源,随着服役时间的延长,萌生于点蚀底部的微裂纹会逐渐扩展形成主裂纹,主裂纹靠吞并其前端的微裂纹向前扩展,直至发生SCC失效。一般认为SCC倾向随着残余拉应力的变大而变大。这种应力腐蚀现象通常认为是由一种氢脆的机制引起的。应力导致表面产生裂纹,产生裂纹处的表面没有表面膜保护,氢原子能够轻易地进入镁和镁合金中与镁反应生成氢化镁。这些进入的氢原子属于小分子,它会位于晶格的间隙中,或在裂纹尖端的表面上。它们会影响金属原子在这些位置上的电子密度分布,使其与相邻的金属原子间的键变弱,以致更容易发生滑移,产生开裂。裂纹处的应力较为集中,晶格畸变较大,这就使氢原子更易优先存在于这些地方,降低了位错间弹性的交互作用。氢原子的分布还会根据应力场的变化而进行调整,从而降低位错运动的阻力,提高位错的运动速度。黄发等用电化学实验、浸泡实验与慢应变速率拉伸实验研究铸造AZ91镁合金在不同浓度比例的溶液体系中的应力腐蚀(SCC)行为。结果表明,随着溶液pH值的升高,AZ91镁合金的应力腐蚀敏感性降低。大多数镁合金的应力腐蚀敏感性均低于铝合金,这是它的一个明显的优点。以Mg-Al类合金而言,当铝量大于8%时,才有明显的应力腐蚀倾向。
(6)铸造镁合金分类 在各种铸镁合金中,镁-铝类合金首先得到了广泛的应用。近年由于含锆镁合金的发展,镁-铝系及镁-铝-锌系合金应用的比重不断下降,但它仍然是一类重要的铸镁合金,目前在中国应用甚广。
①Mg-Al系合金 Mg-Al系合金是最早用于铸件的二元合金系,该系既包括铸造合金又包括变形合金,是目前牌号最多、应用最广的系列。大多数Mg-Al系合金实际上还包括其他的合金元素,以此为基础发展的三元合金系有Mg-Al-Zn、Mg-Al-Mn、Mg-Al-Si和Mg-Al-RE共4个系列。Mg-Al合金中往往还含有一些其他的合金元素,但其中最重要的就是Zn和Mn。AZ(Mg-Al-Zn)系和AM(Mg-Al-Mn)系镁合金是目前应用最广泛的商业化Mg-Al基铸造镁合金。AZ系镁合金(如AZ91)的屈服强度很高,广泛用于制造形状复杂的薄壁压铸件,如发动机和传动系的壳体、电子器材壳体、手动工具等。含铝量比AZ系镁合金低的AM系镁合金(如AM60、AM50、AM20)具有优良的断裂韧性,但屈服强度较低,通常用于承受冲击载荷的场合,如轿车侧门、仪表盘、座椅框架、轮毂及体育用品等。然而AZ和AM系镁合金的高温抗蠕变性能比常用铝合金低一个数量级还多,温度高于150℃时拉伸强度迅速降低。为改善Mg-Al基镁合金的高温性能,目前除通过加入合金元素以改善析出相的特性(晶体结构、形态及热稳定性)来提高现有AZ系镁合金的耐热性能外,还开发出AS(Mg-Al-Si-Mn)系、AE(Mg-Al-RE)系和Mg-Al-Ca系铸造镁合金。尽管增加含铝量可提高合金的铸造性能,但为减少非连续析出β相的数量,AS和AE系耐热镁合金的铝含量都较低。
②Mg-Zn系合金 纯粹的Mg-Zn二元合金在实际中几乎没有得到应用,因为该合金的组织粗大,对显微缩孔非常敏感。但该合金的优点是可通过时效硬化来显著地改善合金的强度。因此,Mg-Zn系合金的进一步发展,需要寻找第三种合金元素,以细化晶粒并减少显微缩孔的倾向。一些研究表明,在Mg-Zn二元合金中加入第三种组元铜,将会导致其韧性和时效硬化的明显增加。砂型铸造合金ZC63[w(Zn)=6%,w(Cu)=3%,w(Mn)=0.5%]是这类合金的典型代表,在时效状态其抗拉强度、屈服强度和伸长率分别达到240MPa、145MPa和5%,高于Mg-Al-Zn系合金的AZ91。Mg-Zn合金中的铜被认为可以提高其共晶温度,因而可在较高的温度固溶,使更多的Zn和Cu溶入合金中,增加了随后的时效强化效果。在Mg-Zn合金中铜的存在,使铸态共晶组织随之改变,α-Mg晶界及枝晶臂之间的MgZn相的形态由完全离异的不规则块状转变为片状。Mg-Zn-Cu合金的缺点是Cu的加入导致合金的耐蚀性能降低。Mg-Zn系合金的晶粒容易长大,Zr则被认为在镁合金中具有细化作用,是铸态Mg-Zn合金最有效的晶粒细化的元素,故工业Mg-Zn系合金中均添加一定量的Zr。这类合金都属于时效强化合金,一般都在直接时效或固溶再接着时效的状态下使用,具有较高的抗拉和屈服强度。在Mg-Zn合金中添加少量的其他金属元素,可以得到一些性能得到改善的三元合金,如张喜燕等人在ZM-5镁合金的基础上添加部分Zn元素和少量Ag元素,研究了新合金与ZM-5合金组织及性能的差异,探讨固溶和时效处理对Mg-Al-Zn合金中组织演变的影响以及组织与性能之间的关系。结果表明:在ZM-5合金中添加Zn能较为明显地增加合金中的β相(Mg17Al12)的数量,且使之变得较为粗大,片层的取向也显得比较复杂多样,而且合金在T4(固溶)和T6(固溶+时效)状态下的屈服强度也有较为明显的提高,而延伸率降低;热处理状态对Mg-Al-Zn合金的显微组织有明显的影响;固溶处理后的时效处理能明显提高Mg-Al-Zn合金的屈服强度比;分布在基体晶界处的β相的数量、大小和形态与合金的拉伸性能有着密切的关系。
③Mg-Li合金 Li的密度为0.53g/cm3,用Li作为合金元素,得到比纯镁还轻的超轻合金。1934~1936年德国、美国、英国等国家发现镁-锂合金在锂含有5.7%时具有密排结构向体心结构的转变。1942年美国着手研究镁-锂合金,1957年镁-锂合金开始用于装甲车车体。为了满足航天飞行器的需要,同时还开发了密度很低的镁-锂系合金。1960~1967年,美国将镁-锂合金用于飞机的零件上。德国于20世纪70年代也开始着手镁-锂合金的快速凝固研究。80年代,日本开始研究稀土对镁-锂合金的作用。到90年代美国开始研究镁-锂合金为基体的复合材料。Mg合金通过Li的合金化,使合金结构由hcp结构转变为易变形的bcc结构,使合金塑性明显提高。即镁如用大量(>10%)体心立方晶格的Li进行合金化,Mg-Li合金的晶格就可由六方转变为体心立方晶格,塑性可以根本改变。但Li是稀有金属,化学活性高,给镁合金的化学稳定性却带来了极坏的影响(抗蚀、抗氧化能力低,SCC严重)。另外,Mg-Li二元合金的强度低,一般采用合金化方法来提高合金的性能。常用的合金化元素有Al、Zn、Mn、RE等元素。对于六方晶系的镁,添加Li后减小了六方晶系α-Mg的c/a值,原子间距的减小降低了六方晶格沿{1010}、<1210>棱面滑移的启动能,使得该滑移在室温下与{0001}、<1210>的基面滑移同时发生,提高了合金的室温延展性和变形性。共晶成分范围的Mg-Li二元合金具有极优的变形性能和超塑性。在α+β相区,对合金超塑性非常有利。朱凯等采用电磁半连续铸造方法进行了健身器材用AZ31-0.3Li新型镁合金的制备,并与常规铸造的显微组织和拉伸性能进行了对比分析。结果表明,与常规铸造相比,电磁半连续铸造方法制备出的组织更均匀、拉伸性能较优,铸锭不同部位的平均晶粒尺寸无明显差异;此外,室温抗拉强度明显提高,其中铸锭边缘处的室温抗拉强度较常规铸造增加55MPa。许多研究表明,Mg-Li二元合金(如Mg-8.5Li、Mg-9Li等)在细晶组织中有超塑性现象,在350℃条件下,合金的伸长率为460%~610%。德国汉诺威大学近年来对超轻的体心立方的Mg-40Li合金进行研究,发现合金的高比强度和高延展性被其相对较低的耐热和抗蠕变性能所抵消。Drits等研究二元Mg-Li合金的性能和其成分变化间的关系发现,Li量的增加引起Mg-Li合金电阻率的增加,在α-Mg的富铝区,这种增加明显;在α+β区,变化很小;而在β区,电阻增加较小。Li增加了α-Mg的微观硬度,但α+β两相材料的微观硬度下降较大,β合金的微观硬度比纯镁低。对于α-Mg热压合金,其延伸强度随Li浓度的增加而下降。而≥10%Li的退火合金的延伸率低于热压合金。对于α+β合金,没有这样的差别。对于含足够量Li的合金,拉伸屈服强度比压缩屈服强度低;Mg-Li合金热压过程中,会发生再结晶。1%的Li能使再结晶晶粒减小,但只要超过1%,再结晶晶粒会明显增加。α+β合金的再结晶组织同样如此。但Li含量超过10%的合金在热压过程中会发生完全再结晶并在组织中出现粗大晶粒。将这些合金退火,由于局部再结晶,产生晶粒长大。通过对Mg-Li合金的塑性变形机制研究,发现镁合金中大量Li的存在会降低蠕变抗力。加热过程中α合金的硬度下降比β合金明显小。二元Mg-Li合金高温性能不足,为了提高高温下的晶体生长阻力,需要添加阻止晶体生长的介质和稳定的第二相掺杂颗粒。工业Mg-Li合金分为3类,即α、α+β和β型合金。为提高合金的强度,除Li外尚需添加其他合金元素,如Al、Zn、Mn、Cd和Ce等。Mg-Li合金的缺点是化学活性很高,Li极易与空气中的氧、氢、氮结合成稳定性很高的化合物,因此熔炼和铸造必须在惰性气氛中进行,采用普通熔剂保护方法很难得到优质铸锭。此外,Mg-Li合金的抗蚀性低于一般镁合金,应力腐蚀倾向严重。
④Mg-Mn系 镁-锰系合金是工业上首先使用的变形镁合金,虽强度偏低,但耐蚀性很高。Mg-Mn合金的时效析出过程为:α→α-Mn(立方晶),中间没有生成亚稳相,其中α-Mn相呈棒状。由于Mg与Mn不形成化合物,因此固溶体中析出的α-Mn相实际上是纯Mn,强化作用很小,因此Mg-Mn系合金没有明显的时效强化效果。通常在Mg-Mn合金中添加一些Al以形成MnAl、MnAl6和MnAl4等化合物相粒子,它们在时效过程中析出后起强化作用。MB8合金板材要求较高强度时,可在533~563K退火;要求较高塑性时,可在593~623K退火。赵浩峰等研究了Sr对镁-锰-铅合金力学性能的影响。拉伸实验结果表明,元素Sr能细化合金中晶粒,提高镁-锰-铅合金的抗拉强度及伸长率,但同时也会降低合金的弹性模量。
⑤Mg-Ag系合金 以Mg-Ag系合金为基础的Mg-Ag-RE(Nd)-Zr合金系,如QE22[w(Ag)=2.5%,w(RE)=25%,w(Zr)=0.7%]合金,或Mg-Ag-Th-RE(Nd)-Zr合金系,如QH21[w(Ag)=2.5%,w(Th)=1%,w(RE)=1%,w(Zr)=0.7%]合金,曾用于制造一些飞机零件,如直升机上的着陆舱、齿轮箱壳体和叶轮盖。Ag在镁中的最大固溶度为15.5%,比Y(12.4%)和Al(12.7%)高,并且与Nd和Mg形成Mg12Nd2Ag相,能产生明显的时效强化效应。Mg-Ag-RE(Nd)系合金的时效析出过程极为复杂,当银含量小于或等于2%时合金的析出过程与Mg-RE合金的相同,主要形成MgN相;当银含量大于2%时可以通过两种沉淀反应析出平衡相Mg12Nd2Ag。当β相和γ相共存时合金的硬度最高。QE22合金[Mg-2.5Ag-2RE(Nd)-0.7Zr]的典型热处理工艺(T6)为:798K/4~8h固溶处理,冷水淬火;473K/8~16h人工时效,空冷。
⑥Mg-RE系 稀土元素在镁中的固溶体以及与镁基固溶体共存的化合物相。自从发现了稀土Y的作用后,QE22和QH21已经不再受人们青睐,因为稀土Y不但可起到Ag的作用,既增加合金抗拉强度和蠕变强度,而且还能够改善合金的耐蚀性能,混合稀土RE(Y)还不像Ag那样的贵重。对于QH21合金而言,就像Mg-Th系合金一样,由于Th的放射性,更限制了其广泛的应用。镁-锰-稀土系合金中,因镁、锰不起作用,稀土元素在镁中的溶解度又很小,故基体中除存在Mn相外,还存在镁与镧、铈、钕形成的二元化合物Mg12RE,也有人认为是Mg9RE。镁与钇生成二元化合物Mg24Y5。稀土元素与镁所生成的相既是强化相又是耐热相,强化效果随稀土元素在镁中的溶解度的增大而提高,但强化相的耐热作用不如Mg23Th6。MB8合金中因铈含量少,通常观察不到Mg12Ce相。镁-锌-锆-稀土系合金中,除Mg12RE外,一般认为可形成Mg-Zn-RE三元相作为强化相和耐热相。稀土镁合金在773~803K固溶处理后可以得到过饱和固溶体,然后在423~523K附近时效时均匀弥散地析出第二相,获得显著的时效强化效果。其时效析出的一般规律是在时效初期形成六方D019型结构;时效中期析出β'相,并可以获得最高强度;时效后期的析出相为平衡析出相。由于稀土元素在镁中的扩散速率较低,析出相的热稳定性很高,所以Mg-RE合金具有优异的耐热性和高温强度。有人研究了含钇(Y)、钆(Gd)或镝(Dy)的Mg-RE合金的显微组织和拉伸性能,结果表明,添加Gd后可获得更高体积分数的β1和β相,并加速了β″和β'相的析出,因此含Gd的Mg-RE合金的拉伸性能优于含Dy或Y的Mg-RE合金。有研究表明,对于同时含有两种不同系RE元素的镁合金而言,两种稀土元素均会降低对方在镁基体中的固溶度,并改变对方从过饱和镁基固溶体中时效析出的动力学过程。同时,由于其中一种稀土元素会溶入另一种的析出相中,从而大大提高时效强化效果。
(7)铸造镁合金牌号
①ZM-1合金 ZM-1合金是Mg-Zn-Zr系合金的代表,相应的美国牌号为ZK51A,前苏联牌号为MJI12,其成分为:3.5%~5.5%Zn,0.5%~1.0%Zr(为总锆量,其中“溶解锆”量应≥0.5%);杂质限制为:Si≤0.01%,Fe≤0.01%,Ni≤0.01%,Cu≤0.03%,杂质总量≤0.3%。ZM-1合金已用于多种飞机的机轮铸件,并可广泛用于形状简单的各种受力构件。该合金的晶粒细化程度与合金中的溶解锆含量密切相关,而晶粒细化程度又直接影响合金的力学性能,所以熔炼技术和温度控制是极为重要的。张胜利等在ZM-1(Mg-5Zn-0.6Zr)合金的基础上,适量增加Zn的含量并加入重稀土元素Gd,设计了Mg-5.5Zn-2Gd-0.6Zr实验合金。采用砂型铸造工艺制备实验合金试样,在不同温度和应力条件下对该实验合金和ZM-1合金的蠕变曲线进行了测试。结果表明,在相同条件下,Mg-5.5Zn-2Gd-0.6Zr实验合金的稳态蠕变速率较ZM-1合金的降低了一个数量级;当施加应力为40MPa时,实验合金的蠕变激活能Q(200~250℃)=142.0kJ/mol,接近镁的自扩散激活能,蠕变受位错攀移控制,而ZM-1合金在相同应力下蠕变激活能Q(200~250℃)=88.5kJ/mol,接近镁的晶界扩散激活能,蠕变受晶界滑移控制。合金在200℃条件下的应力指数n=4.21,而ZM-1合金的应力指数n=2.21。因此,认为加入重稀土元素Gd后实验合金的蠕变机制发生改变,200℃时的蠕变机制为位错攀移机制。
ZM-1合金的含锌量一般应控制在4%~5%,合金中的“溶解锆”量应大于0.5%,最好能保持在0.6%以上。当合金中含有很少量的铝、锰、硅、铁以及镍、钴、锡、锑、磷等杂质时,均将使锆在镁液中的溶解度剧烈下降,使合金中的锆从镁液析出而沉淀于坩埚底部,有些杂质还将与锆形成难熔的化合物,会使合金中的锆量达不到成分规定的要求。故对这些杂质均应严格限制,但锰量可略放宽些,因锰量大于0.1%时才会使锆析出。由于上面这些原因,在生产中,ZM-1合金的熔炼坩埚不能与ZM-5合金的混用,炉料也应严格管理,当ZM-5合金回炉料混入ZM-1合金中时,ZM-1合金的晶粒会十分粗大,出现所谓的“冰糖断口”。此外,溶于镁液中的氢和氧化镁夹杂也有使锆沉淀的作用,故炉料应存放在干燥场所,并保持洁净。
ZM-1是镁-锌-锆系砂型铸造合金,具有高的抗拉强度、屈服强度和塑性。ZM-1合金的强度和伸长率与ZM-5合金相近,但其条件屈服极限(σ0.2)却比ZM-5合金高得多,因此它比ZM-5合金有更高的承受载荷的能力。ZM-1合金的热处理规范为如下。T1:(300±5)℃,保温4~6h(或180~200℃,16h),空冷。T6:400℃保温2h,再升温至500℃,保温3~10h,空冷,在170℃时效12h。表2-2为ZM-1合金的低温力学性能。典型的力学性能见表2-3。表2-4为镁-锌-锆系铸造镁合金铸造工艺性能及物理常数。表2-5为镁-锌-锆系合金的室温力学性能。表2-6为镁-锌-锆系合金的高温力学性能。ZM-1合金在铸造时热裂倾向较大而且难以焊补。该合金的疏松倾向较大,不宜用来铸造耐高压的零件。推荐用于小型或形状简单、断面均匀的受力零件。该合金在未经固溶处理的人工时效状态(T1)下使用。ZM-1合金铸态组织分析表明,晶内有树木年轮状或花朵状的偏析,少量γ'(MgZn)化合物分布在晶界上。经人工时效(T6)后,少量γ'(MgZn)相仍留在晶界上,并在基体中弥散析出细小的γ'相质点,但这在一般光学显微镜下是观察不到的。合金经淬火和人工时效(T6)后,其组织中晶界上的T1相已全部溶入基体,同时在基体中出现弥散析出细小的γ'相质点(在光学显微镜下是看不到的)。δ固溶体晶粒中心变暗与锆在淬火前加热中析出有关。有资料认为这是单质锆从过饱和固溶体中析出所致,也有人认为与Zr-H化合物析出有关。合金淬火时锆的析出,部分地抵消了晶界的γ'相溶入固溶体并随后在时效时弥散析出的强化效果。
表2-2 ZM-1合金的低温力学性能

表2-3 镁-锌-锆系铸造镁合金力学性能

表2-4 镁-锌-锆系铸造镁合金铸造工艺性能及物理常数

表2-5 镁-锌-锆系合金的室温力学性能

表2-6 镁-锌-锆系合金的高温力学性能

②ZM-2合金 ZM-2是在ZM-1成分的基础上添加混合稀土金属以改进铸造和焊接性能的一种合金。ZM-2具有较高的强度和中等塑性。ZM-2的高温力学性能和疲劳强度明显高于ZM-1。该合金容易铸造并易焊接,疏松倾向低,铸件致密性高。该合金在无预先固溶处理的人工时效状态(T1)下使用。ZM-2合金已用于涡轮喷气发动机的前支承壳体及盖、飞机电机壳体、液压泵壳体等零件。合金的锆含量与ZM-1中的一样直接影响合金的力学性能。在规定成分范围内,低锌、高稀土的合金具有较好的铸造和焊接性能,但拉伸性能较低;反之,高锌、低稀土合金的拉伸性能较高,而铸造和焊接性能较差。
③ZM-7合金 ZM-7合金有高的室温抗拉强度、屈服强度和良好的塑性,但因含银而且铸造时疏松倾向大而难以焊补。合金在T4和T6状态下使用。
为了使铸造镁合金有较高的耐热性能,需要牺牲室温下的塑性,而加入能够形成硬又脆的难熔组成物;这些加入物,在合金的工作温度下,实际上是不溶于镁中的,而是沿着晶粒边界分布,使合金的蠕变极限降低,提高合金的耐热性能。
④ZM-5合金 ZM-5合金是Mg-Al-Zn系合金的代表,相当于美国标准的AZ81A,前苏联牌号的MJI5合金,合金中杂质为铁、铜、镍、硅、钴等,根据需要可适量加些铍。其成分为:7.5%~9.0%Al,0.2%~0.8%Zn,0.15%~0.5%Mn,其余为Mg。杂质限制为(不大于):0.25%Si,0.1%Cu,0.08%Fe,0.01%Ni,0.001%Co。此外,根据需要还可加≤0.002%Be。根据前面分析的成分对性能的影响可知:铝量一般应取8%~8.5%,薄壁铸件铝量可取高些,厚壁铸件则宜稍低些;锌量一般取0.5%左右,锰量一般取0.3%~0.4%。
ZM-5合金的铸态组织由α-Mg固溶体和晶界不连续的呈网状分布的镁铝块状化合物组成。ZM-5合金的铸态组织特征为:δ(Mg)固溶体为基体,沿它的晶界以不连续网状分布着γ(Mg4Al3)相,以及散布在δ(Mg)固溶体中的Mn-Al化合物小质点。γ(Mg4Al3)相在晶间分布成网状,在晶枝间则呈短条状和球状。高倍观察时可看到铸态组织中的γ相有两种形式,当用2%草酸水溶液或乙二醇及硝酸水溶液(75mL乙二醇,1mL浓硝酸,24mL水)腐蚀时,部分γ相呈白色的多角形块状,以不连续网状分布于δ晶界,这是合金凝固过程中析出的以δ+γ的离异共晶形式出现的初次γ相。在Mg-Al二元合金中,块状初次γ相中还包含有小岛状的δ(Mg),当合金中加入锌后,小岛状的δ(Mg)即消失。另一部分γ相呈灰黑色层片状,以类似粗珠光体的形式分布在初次γ相周围,这是合金凝固后(由于固溶体随温度降低而变小)从δ固溶体中分解析出的二次γ相。δ晶界上网状的白色相为初次γ,灰色的为冷却过程析出的二次γ相,δ基体上散布着Mn-Al化合物小点。由于组织高度偏析,化合物也分布于晶粒的枝晶网之间。化合物的尺寸、数量和形状与凝固时的冷却速率有关。固溶处理后,化合物溶入固溶体中,其组织则由轮廓分明的晶粒和在晶界处的少量块状化合物所组成。如果冷却较慢,晶界上就可能出现片状沉淀物。时效处理会引起固溶体的分解,从而沉淀出细小的魏氏体型组织,在165℃或更高温度下进行时效处理,晶界上会出现较粗的片状沉淀物。ZM-10的显微组织与ZM-5相似,但因铝和锌含量较高而有较多的化合物。在金属补缩不足的部位,有时会在晶界处出现显微疏松(显微孔洞)。镁-铝-锌系合金的显微组织都很相似。在铸造状态下,基本上是由铝和锌固溶于镁中的α固溶体以及分布于α固溶体晶粒边界和晶粒内部的Mg4Al3化合物所组成的。这类合金中的MJI3,由于铝的含量较少,仅在某些情况下才能勉强地观察到Mg4Al3。ZM-5合金的铸态组织由固溶体α-Mg为基体,沿它的晶界以不连续网状分布的γ(Mg4Al3)相,以及分布在固溶体δ(Mg)中的Mn-Al化合物小质点所组成。镁-铝-锌系合金具有树枝状凝固的特点,其显微疏松一般垂直于铸件表面分布。当显微疏松的程度严重时,层与层相互靠拢。ZM-5合金具有较高的显微疏松倾向,即使采用工艺方法也难以完全消除。因此在铸件生产过程中,在保证满足产品技术要求的前提下,常允许存在一定程度的显微疏松。镁-铝-锌系铸造合金结晶间隔较大,充型能力良好。
综上所述,ZM-5合金有良好的力学性能和中等的铸造性能,不含稀贵元素,其熔炼工艺也较简便(与含锆镁合金相比),它的抗蚀性也尚良好,故它在航空工业中得到了广泛的应用。不足之处是σ0.2值较低,T4状态下其σ0.2/σb比值仅1/3,T6状态也只有1/2,它的力学性能壁厚效应较大,因而降低了承受载荷的能力,它也较易形成缩松,故在工艺上应特别注意铸件上温度的合理分布(防止局部过热,造成顺序凝固等)和加强补缩。
ZM-5和ZM-10合金适用于砂型和金属型铸造,也可以用压力铸造及其他特种铸造工艺生产铸件。合金具有良好的流动性、焊接性,热裂倾向低,但疏松倾向较大;固溶处理后具有较高的抗拉强度、塑性和中等屈服强度;后经时效处理则使塑性降低,屈服强度提高。合金可在铸态(F)、固溶处理(T4)以及固溶处理后接人工时效(T6)等状态下使用,可以制造受力构件和一般用途的铸件。与其他各系合金相比,该合金不含稀土金属和锆,是较为价廉的镁合金。但因ZM-5和ZM-10合金有较高的疏松倾向和壁厚敏感性等缺点,或受工作温度限制等原因,有些铸件则可以用含稀土的镁合金如ZM-6或ZM-2来代替。表2-7为镁-铝-锌系合金在铸态时的力学性能。表2-8为镁-铝系合金的高温力学性能。表2-9为镁-铝系合金的低温力学性能。表2-10为ZM-5合金的力学性能。使用螺旋形试样测定了ZM-5合金的流动长度,合金的过热温度分别为15℃及30℃,其流动长度分别为230mm及320mm。测试表明,这种合金的流动性随合金液体过热度的增加而增大。合金的铸造性能见表2-11。
表2-7 镁-铝-锌系合金在铸态时的力学性能

表2-8 镁-铝系合金的高温力学性能

表2-9 镁-铝系合金的低温力学性能

表2-10 ZM-5合金的力学性能(1)

表2-11 ZM-5合金的铸造性能(2)

2.1.1.2 镁合金的熔炼的基本过程
镁合金熔炼的基本过程是:熔炼之前做好准备工作,将工具烘干,然后将原材料和熔剂放在炉板上靠近炉子的地方进行预热。刮干残留锭模表面的涂料(锭模使用一段时间后最好用喷砂去除残留涂料),喷上新的涂料,为了使涂料与锭模结合紧密,最好加入少量水玻璃。喷涂之后将锭模充分预热,使模腔内部干燥。熔炼过程中使用覆盖剂保护,但不能过量,原则上是在充分保护的情况下尽量少用。通过精炼能够减少合金液中的氧化夹杂和其他有害杂质,这是控制合金品质的关键。精炼过程中要控制的几个重要环节是温度、时间、操作方法以及精炼后合金液的静置时间。镁合金精炼温度一般控制在730~760℃。温度太低,合金液黏度大,夹杂难以沉降;太高则合金液氧化严重。精炼时间一般控制在20min左右,而此后的静置时间一般在1h左右。资料表明,为了使精炼剂与合金液进行充分的物理化学反应,应当采用正确的精炼操作。正确方法是将搅拌勺插入合金液的2/3,并选择适当的角度,以便合金液的对流循环更充分。勺子不能插入过深,以免将坩埚底部的熔渣翻上来。注意不能使镁液产生飞溅,同时在合金液刚翻上来的部位撒上精炼剂。镁合金的熔化工艺因合金、熔化炉的种类不同而不同。加强对高性能镁合金熔炼工艺的研究是扩大镁合金应用范围的需要。张诗昌很早就提出镁合金研制集熔化、处理、浇铸为一体的自动化、封闭型、连续化的生产工艺系统。这是实现镁合金安全、清洁、高效熔炼的必然趋势。进一步开发适合镁合金特点的精炼及变质处理工艺是提高镁合金使用性能的重要手段。研制更为经济、实用、无污染的镁合金熔炼保护方法,以提高镁合金利用率、降低生产成本。例如:熔炼高耐蚀性的镁合金AZ91D或AZ91E,需要对重金属杂质元素严格限量。不同性能的合金,对熔炼技术也会有不同要求。
2.1.1.3 熔炼前的准备及熔炼工作
(1)配料 各种铸造镁合金的推荐配料成分见表2-12。资料表明,为减少镁合金的氧化燃烧,配料中允许加入质量分数不大于0.002%的铍。配料中的镁-锆中间合金的加入量(质量分数)可根据生产经验:新料按7%~10%,回炉料按3.5%~5%。钕以镁-钕中间合金的形式加入,钕的质量分数为25%~40%,钕是指钕的质量分数不少于85%的钕混合稀土金属,其中的钕加镨总的质量分数不少于95%。ZM-5合金中铝的配料成分对于大型厚壁铸件应取下限,对于薄壁铸件应取上限。配料时推荐采用表2-13的炉料组成。注意同时采用二级和三级回炉料时,其总和不应超过整个炉料质量的30%。以配制ZM-5合金250kg炉料为例,假设炉料成分(质量分数)为Al8%,Zn 0.5%,Mn 0.4%,其余为镁。炉料计算程序实例见表2-14。炉料及熔炼用辅助材料的准备见表2-15及表2-16。对于熔剂,在使用前需在120~150℃干燥1h以上。对变质剂,菱镁矿在使用前要破碎成10mm,然后在120~150℃烘烤1h以上。精炼剂六氯乙烷在使用前要压成一定形状的块状。防燃剂中硫黄和硼酸在使用前应破碎成小块,按1:1比混合均匀,用40号筛过筛后置于密闭容器中备用。
表2-12 各种铸造镁合金的配料成分

表2-13 炉料的组成

表2-14 炉料组成比例和其化学成分

表2-15 炉料的准备

表2-16 非金属辅助材料的准备

在目前的工艺中,在配料时炉料应先经吹洗,除去表面上的腐蚀物及熔剂、砂粒、氧化皮等,以防止它们与镁反应,使硅、铁、氢、氧化夹杂等进入熔体中。对纯镁锭,启封后首先要除油,再喷砂处理,然后预热到150℃后使用。资料表明,回炉料也需喷砂处理,表面有严重锈蚀等的回炉料要重熔,成锭后预热到150℃后备用。原材料中的纯镁用Mg-3以上,纯铝、纯锌分别用Al-2及Zn-3以上,稀土直接加入,锰及锆制成中间合金形式加入,铍以Al-Be中间合金或铍氟酸钠(NaBeF3)形式加入。资料表明,用粗镁或镁锭生产镁合金的配料操作时,首先准确计量出每炉入炉粗镁数量,以kg为计量单位,精确到一位小数;然后根据入炉粗镁数量乘以95%计算出镁数量(kg);再根据所配合金的主成分要求,来确定主要组元的计算成分。以100kg合金作为配料基数,从而计算出该炉的合金总量(kg)。计算出每炉合金总量(kg)后,按各主要元素的要求成分(%)计算出单个元素的加入数量(kg)。然后根据该元素的加入方式(比如以单质形式或中间合金)计算出中间合金数量(kg)。加入炉内的各种单质或中间合金都必须有详细的成分分析结果,没有结果或分析结果有异议时不能进行合金配料计算,等待重新取样分析后,方可进行配料操作。对于加入的单质和中间合金,在配制前必须将其熔铸成一定数量的饼、块、锭,以便于配料操作。对于已计算好的炉料,要做详细的配料记录,并按炉号分别存放,严禁混淆炉料。对用户有特殊成分要求的合金,除严格进行配料计算外,还要考虑精镁中的杂质成分上限可能对镁合金造成的杂质成分超标,故要严格把握中间合金或单质中的杂质。对于入炉的单质和中间合金,在加入前要预热到120~150℃。对于密度较轻或容易挥发的单质元素,或者密度较大,且熔点较高的中间合金,加入时要采取必要的措施。
(2)设备、坩埚与工具的准备 表2-17为金属熔炼工具的准备,表2-18为熔化用的其他工具用涂料,表2-19为坩埚的准备。在开始工作前必须检查熔炼炉和仪表的电器部分是否正常及仪表是否处在有效的使用期内。资料表明,熔化工具与液体合金接触时,其上往往带有很多的熔渣及氧化物。因此,必须经常洗涤处理。同时,工具需要预热。因而要在熔炉旁边另置一坩埚炉,在坩埚中加入2号熔剂或光卤石,将其熔化并加热至760~800℃,以便熔炼工具在使用之前浸入其中将其洗涤干净,并预热至暗红色,洗涤坩埚中的熔剂在每一个工作班中,应清理1~2次,以除去其中的脏物,并根据熔剂的消耗和洗涤能力的减弱往洗涤坩埚中添加新的熔剂。洗涤熔剂还应定期进行更换。坩埚外表有白色氧化皮或干燥熔剂,表明该处已烧穿渗漏;坩埚局部严重凹陷或坩埚壁减薄至原壁厚的1/2,若捶击坩埚声音嘶哑,表明有裂纹或过烧之处。对不同容量的坩埚,其壁厚应满足要求。如800℃以下使用的容量(kg)分别为120、200、250、300及350的坩埚壁厚分别为5mm、5mm、6mm、6mm及7mm。800℃以上使用的坩埚壁厚相应增加1mm。
表2-17 金属熔炼工具的准备

表2-18 熔化用的其他工具用涂料

表2-19 坩埚的准备

(3)熔化操作 表2-20及表2-21为镁合金的熔炼工艺。陆大中早于1952年熔制镁-铜合金时,在配料方面采用“镁-铜二”的比例来加料。使用的炉子是普通的坩埚炉,底部由鼓风机送风,附有开关。由于风力较强,升温很快,最高温度可达1500℃左右。在熔化开始时先将坩埚放入炉中徐徐烧红,而后把截成100mm长的镁锭放入,这时便开始强烈送风。由于熔化所用的炉型不同,因此熔化操作时的具体程序略有不同。资料表明,固定式和可提式坩埚炉中熔化的工艺程序为:坩埚预热到400~500℃(呈暗红色);然后炉料预热,120~200℃(最高不得高于300℃);往坩埚底部放入熔剂,将占炉料质量0.1%~0.25%的BH3熔剂撒在坩埚壁上和底部(当用带挡渣板的坩埚时,可将占炉料质量0.1%~0.25%的BH2熔剂撒在坩埚壁上和底部);装入和熔化炉料,待回炉料、中间合金及镁全部炉料熔化后,于温度为690~720℃时加入锌,当合金表面燃烧时,可分别用BH2或BH3熔剂熄灭,于温度700~720℃加入铝-铍或铝-镁-铍中间合金;搅拌合金后,于合金液中部舀取合金液,浇铸炉前分析化学成分用试样;进行合金精炼;进行合金的变质处理,检查变质效果,当变质不良时,允许重复进行变质处理;760~780℃加入金属钙,金属钙在加入前应将其表面的煤油挥发干净;用钟形罩压入合金液使合金液在780℃下静置15~20min;从坩埚炉中提出坩埚,接着浇铸于铸型中,在浇铸时,应往注流上撒以硫黄和硼酸的混合物(1:1),用茶壶式浇包从坩埚中舀取合金液浇铸于铸型中;钙加入合金中后,于30min内浇铸完毕。合金变质后,应在45min内浇铸完毕。
表2-20 镁-锌-锆系和镁-稀土金属-锆系合金的熔炼工艺

表2-21 镁-铝系合金的熔炼工艺

在反射炉中熔化,然后转注于保温炉中进行变质处理时,首先要将炉预热到750~850℃,接着加入占炉料质量0.3%~0.5%的BH2(或NO2)熔剂洗涤炉底;将炉料装入前膛预热至120℃以上,然后用专用工具,将炉料送于熔池中,这时应有1/3~2/3的喷嘴进行工作;在炉料上面覆以占炉料质量2%~3%的NO2熔剂或BH2熔剂;使全部喷嘴进行工作,通过观察孔口观察炉料熔化情况,当金属表面燃烧时,可用熔剂熄灭;当合金液温度达到690~710℃时清除其表面的熔渣并撒以新熔剂。对含锌的合金,在温度为690~720℃时加入锌,然后根据需要再加入铍中间合金(如果加铍氟酸钠,应在合金液转注于保温炉时,在730~750℃的温度下),以1:1的比例与熔剂混合均匀而加入;在撒有干燥粉状熔剂的金属液中,用搅拌器激烈地由下至上搅拌4~6min,此时的熔剂消耗量为炉料质量的0.81%,精炼温度为700~730℃;精炼后除去合金液表面的熔剂,并撒以新熔剂,静置15~20min后,取炉前分析试样;将合金液转注于预热的保温坩埚炉中。
2.1.1.4 合金元素的加入方法及中间合金
为了降低金属的熔点,合金元素常以中间合金的方式加入。中间合金的质量对镁合金铸件的性能影响很大。一些中间合金的成分及配制见表2-22及表2-23。关学丰等很早就镁-稀土中间合金品位对变形镁合金性能的影响进行试验。以镁-锌-锆-钕、镁-锌-锆-钇系变形镁合金为例,研究了镁-钕、镁-钇中间合金中钕、钇的品位对其性能的影响。结果表明,镁-钕、镁-钇中间合金钕、钇的品位高于80%时,合金的室温拉伸性能较佳,反之,则合金的室温拉伸性能低劣。资料表明,对于加入的单质或中间合金,在加入前将其熔铸成一定数量的饼、块、锭利于操作。中间合金配制需要注意:①熔炼镁合金时,应尽量避免坩埚中的金属与燃料的燃烧产物相接触,以防合金吸氢;②在配制镁合金时,要清除干净所有金属(粗镁、中间合金等)外表的腐蚀产物和油污等,特别是对粗镁要进行严格筛选,选择适合的粗镁作合金基料;③对镁合金来说,配料的各组分的加料次序如下:镁或粗镁→中间合金→铝→锌和镉等易挥发金属→钙、铍最后加入。
表2-22 镁合金用中间合金的化学成分

表2-23 配制常用中间合金的工艺参数

镁-铍中间合金的配制:В.Е.Ивaнов、谢燮揆等很早就论述过镁铍合金。当必须往合金中掺入铍时,可往配料中加入Al-Be中间合金、铝-铍-镁中间合金或氟铍酸钠化合物。但铍的总含量不能超过全部配料的0.002%;铝-铍中间合金和铝-铍-镁中间合金在合金精炼之前加入。若采用氟铍酸钠,在精炼时同熔剂一起加入,精炼温度应当提高到730~760℃。早于1958年周峻山也提出,镁合金的氧化膜多孔、不密集,不能保护金属不被氧化(其他金属表面附着一层很厚的氧化膜时,对金属具有防护作用)。在空气中,特别是在高温下,随着温度与时间的增加,氧化程度也随着增加,液态的镁甚至会燃烧起来。因此,在空气中熔锻镁合金是不可能的,需要采取特殊方法。这种特殊熔炼方法需要真空系统,合金中需加入降低氧化性的金属,并且需在熔剂层覆盖保护下工作。但是,在真空中熔炼镁合金有许多困难,而在合金中加入降低氧化性的金属问题,目前可用的金属也只有铍(Be)一种,其他还不适合。虽然铍可以使金属表面氧化膜严密,但加入数量有限。当超过一定限量时,会影响材料的性能,同时也不能从根本上解决氧化问题(只能减少氧化的程度)。因此,采用熔剂保护是较为现实的方法。
镁-锆中间合金配制:周明付应用N235-H2SO4分离技术,使锆与其他多种杂质元素分离,以提高原料K2ZrF6质量,降低合金杂质含量,通过控制炉料配比,稳定提高Zr的含量,采用机械搅拌替代传统的人工搅拌,加速生产过程中的还原反应进程,使合金成分均匀化,从而解决了合金成分偏析难题。锆以氯锆酸盐或氟锆酸盐[如氟锆酸钠(Na2ZrF4)]状态加入镁合金中时,氟锆酸盐加入量为计算量的8~10倍,温度必须加热至900℃;锆以氯化锆形式加入镁合金中时,困难较小,尽量采用氯化锆盐的形式加入,但必须注意合金的耐蚀性能要求,防止氯离子超标。
镁-锂中间合金的配制:镁-锂合金在75%~85%LiCl2、15%~25%LiF2混合熔剂下进行精炼;熔炼镁-锂合金时,先加入除锂以外的其他组元,最后加入锂,在加锂之前,全部熔剂都分布在金属液的上层,待加入锂后,熔剂则下沉至坩埚底部,因为此时熔液的密度已小于熔剂密度。为了使熔剂与金属更好的分离开,采用数量不超过30%的溴化锂作浓稠剂,溴化锂在加入锂之后加入熔剂中。
镁-锰中间合金配制:锰在镁中的溶解度随着温度的降低而急剧减小,在500℃时溶解度为0.8%,在200℃时实际上为0。镁-锰合金在651~653℃发生包晶反应,其含锰量为2.45%~3.4%。李锐等为了提高镁-锰中间合金中锰元素的利用率,制备具有高耐腐蚀性、力学性、焊接性以及生物相容性的新型镁合金,应用搅拌铸造法制备了含锰量超过10%(质量分数)的中间合金。通过试验,获得了兼顾锰含量以及锰元素均匀度的工艺,Mn粉末粒径为68.18~150.00μm,搅拌4min,铜模空冷,感应熔炼炉工作功率为12.5kW。通过理论研究,发现了锰粉末粒径太小导致中间合金锰含量下降的原因;阐明了细锰粉和铜模冷却能提高中间合金中锰均匀度的机理。锰能提高镁的耐蚀性,在大多数镁合金中一般加入0.15%~0.5%。
2.1.1.5 镁合金的精炼处理
(1)精炼的目的 目前生产中使用的精炼方法有熔剂精炼法、C2Cl6精炼法及氯气法。镁的化学活性很强,镁及镁合金在熔炼过程中容易受周围环境介质的影响,空气中的氧、氮、水汽等均能使镁氧化形成难熔的氧化镁等非金属夹杂,非金属夹杂的存在不仅严重恶化合金的力学性能,而且影响合金熔体的质量,导致铸件中出现气孔、夹杂、夹渣和缩孔等缺陷。因此,需要对镁合金熔体进行净化处理。精炼的目的在于清除混合在镁液中的氧化夹渣物及气体,以提高其纯度,避免缩松、气孔等缺陷,获得力学性能和抗蚀性较高的铸件。通常可以从正确使用熔剂、加强熔体液面的保护和对熔体进行充分的净化处理等三个方面来进行控制。目前生产中主要使用精炼熔剂进行精炼。熔剂精炼法是用熔剂洗涤镁熔液,利用熔剂与熔液的充分接触来润湿夹杂物,并将其聚合于熔剂中,随同熔剂沉析于坩埚底部。为达到此目的,熔剂应当具有良好的润湿、吸附夹杂能力。梅显芝等很早就研究了镁合金精炼熔剂表面张力。镁合金精炼用精炼剂和覆盖剂,其表面张力是重要的理化性质之一。用气泡最大压力法测定熔体表面张力是适用的,熔体表面张力随MgCl2含量增高及KCl与NaCl百分含量比值增高而下降,其温度系数为负值。精炼工艺还应当设计正确以防止产生新的夹杂。精炼温度一般控制在710~730℃,精炼后静置10~60min,使熔渣充分沉析。
(2)除气精炼 像铝一样,溶入镁熔液中的气体主要是氢气。镁合金中的氢主要来源于熔剂中的水分、金属表面吸附的潮气以及金属腐蚀带入的水分。氢是溶解于熔融镁中的仅有气体,氢在镁中的固溶度(平均每100g约30mL)较高。氢在镁熔液中的溶解度比在铝熔液中大2个数量级,凝固时的析出倾向也不如铝那么严重(镁熔液中氢的溶解度为固态的1.5倍),用快冷的方法可以使氢过饱和固溶于镁中,因而除气问题往往不大引起重视。资料表明,在研究镁合金铸件最常见缺陷——缩松时,发现合金中含气量与缩松程度密切相关。这是因为镁合金结晶间隔大,尤其是在不平衡状态下,结晶间隔更大。在凝固过程中如果没有建立顺序凝固的温度梯度,熔体几乎同时凝固,形成分散细小的孔洞,不易得到外部金属的补充,引起局部真空,在真空的抽吸作用下,气体很易在该处析出,而析出的气体又进一步阻碍熔体对孔洞的补缩,最终缩松更加严重。镁合金中的氢主要来源于熔剂中的水分、金属表面吸附的潮气以及金属腐蚀带入的水分,因此,如果对这些材料采取适当的预防措施就可以降低含氢量。由表2-24可以看出,受腐蚀的镁合金含氢量增加,而用氯气除气后含氢量大大下降。低的氢量会降低形成气孔倾向,在Mg-Al和Mg-Al-Zn合金中形成气孔的倾向是很普通的。试验表明,在生产条件下,当镁合金中含氢量超过14.5cm3/100g就会出现缩松。
表2-24 镁-铝-锌合金不同状态下的含氢量

传统除气工艺方法类似于铝熔炼所采用的通氯气方法。在740~760℃下往熔体中通入Cl2,氯气经石墨管引入镁熔液中,处理温度为725~750℃,时间5~15min。熔体温度低于740℃时,反应生成的MgCl2将悬浮于合金液面,使表面无法生成致密的覆盖层,不能阻止镁的燃烧。熔体温度高于760℃时,则熔体与氯气的反应加剧,生成大量的MgCl2,形成夹杂。即温度高于750℃生成液态的MgCl2有利于氯化物及其他悬浮夹杂的清除。如温度过高,形成的MgCl2过多,产生熔剂夹杂的可能性增加。氯气除气会消除镁-铝合金加“碳”的变质效果,因此用氯气除气应安排在“碳”变质工艺之前进行。生产中常常用C2Cl6和六氯代苯等有机氯化物对镁熔液进行除气,这些氯化物以片状压入熔液中,与氯气除气相比具有使用方便、不需专用通气装置等优点,但C2Cl6的除气效果不如氯气好。现在生产中多采用边加精炼剂边通入氮气或氩气的方法精炼,既可以有效地去除熔液中的非金属夹杂物,同时又除气,不但精炼效果好,而且可以缩短作业时间。氯气通入量应合适,一般控制在使熔体的含氯量低于3%,以2.5~3L/min为佳。
在镁熔体中通入氩气、氦气等也能取得一定的除气效果,但不能有效地去除熔体中的非金属夹杂物。因此不能像铝熔体那样,通过除气达到精炼目的,故镁熔体的精炼处理还必须进行。通入惰性气体(如Ar、Ne)法是在750~760℃下往熔体中通入占熔体质量0.5%的Ar,可以将熔体中的氢含量由150~190cm3/kg降至100cm3/kg。通气速度应适当,以避免熔体飞溅,通气时间为30min,通气时间过长将导致晶粒粗化。
含碳的物质如CCl4、C2Cl6和SiC等对Mg-Al系合金具有明显的晶粒细化作用。如果采用占熔体质量(1~1.5)% Cl2+0.25% CCl4的混合气体在690~710℃下除气,则可以达到除气和细化的双重效果,而且除气效果更佳,但是容易造成污染。因此,生产中常使用C2Cl6作为精炼剂进行精炼,用C2Cl6处理镁熔液兼有变质和精炼双重作用。特别是在无熔剂精炼(以防护性气氛熔炼)镁-铝合金时,更显示了它的优越性。其机理是C2Cl6在镁熔液中迅速分解出氯、碳等,氯与镁能生产出MgCl2,起精炼作用,碳则起晶粒细化作用。此外,C2Cl6分解所产生的气体还兼有除氢的作用。C2Cl6精炼的主要问题是在坩埚下部较大范围内产生絮状的悬浮性熔渣,经X射线衍射和电子探针分析,其主要成分为MgCl2及MgO。解决办法是通氩气再行吹洗,使熔渣上浮、下沉,或者再用熔剂精炼1min,亦可获得去除夹杂的良好效果。精炼结束后,为防止表面金属氧化燃烧,要向金属表面撒覆盖剂。
含锆合金通常没有气孔问题,因为锆本身会以ZrH2的形式除氢,这类合金一般不需要除气。但是除气能改善某些Mg-Zn-Zr合金的拉伸性能,原因是减少了ZrH2的形成而引起的锆损失。在这种情况下,应该是在加锆以前先完成除气工序。
(3)去除夹杂物精炼
①精炼工艺 镁合金的熔剂精炼工艺及操作顺序见表2-25。表2-26为镁合金的精炼工艺。镁合金中主要的夹杂物是MgO,同时还有MgF2、MgCl2等。MgO及MgF2的熔点分别为2642℃及1263℃,均高于镁合金的熔炼温度,在镁合金液中以固态形式出现。MgO的密度为3.58g/cm3,高于镁的密度。因此,MgO会沉于合金液底部作为氧化渣排出。由于镁易氧化,高温下产生大量的MgO,不可能被全部排出,所以在镁合金中会残存一部分MgO夹渣。MgCl2的熔点为718℃,在镁合金的熔炼温度范围内,因此MgCl2在镁合金液中以液态形式出现。此外,MgCl2在液态时的密度与镁的密度接近,因此MgCl2残留在镁合金液中的概率较大。另外,MgCl2还具有很强的吸湿性,会加速镁合金的腐蚀。这些问题的存在使得在熔炼镁合金时必须要对其进行精炼处理。
表2-25 镁合金的熔剂精炼顺序

表2-26 镁合金的精炼工艺

熔剂精炼是用熔剂洗涤熔体,利用熔剂与熔体的充分接触来润湿吸附夹杂,并将其聚合于熔剂中,随同熔剂沉析于坩埚底部。在操作中,熔剂应具有良好的润湿、吸附夹杂的能力或与夹杂能生成复杂化合物。另外,精炼工艺要正确,并应防止产生新的夹杂物。覆盖剂可用20%的硫粉和80%的精炼剂的混合物。表面精炼剂熔化后,逐渐向金属中渗透,即使在浇铸过程中,倾斜抬包中的金属表面保护膜破裂后,要向正待浇铸的金属表面撒覆盖剂。这些精炼后的工作,无疑给金属增加了外来杂质。有的制造厂采用氩气保护方法,防止气体杂质的进入,但要在较密闭的氩气环境中进行精炼和浇铸才有效,在敞开容器表面喷氩气阻止表面燃烧效果不大。在精炼及浇铸温度不太高的情况下,采用喷硫粉的方法制止熔体金属的表面氧化和燃烧效果较好。将出口管朝向熔融金属的装有硫粉的盒中通入一定的风量,喷出的硫粉冲向金属表面燃烧,减轻了金属的表面氧化,防止了外来精炼剂的进入。精炼温度一般控制在710~730℃,精炼后静置10~15min,使熔渣充分沉析。资料表明,镁合金的精炼是建立在提高合金液的温度以后,一些非金属夹渣物能很快地沉淀至坩埚底部的基础上。张军等研究了镁合金再生过程中熔体内夹杂物含量、尺寸与静置时间的关系,以及主要合金成分和杂质元素含量的变化规律。应用Stokes公式模拟了夹杂物沉降距离与静置时间的关系,分析了影响夹杂物沉降速度的因素。结果表明:在镁合金废料完全熔解后静置5~10min,可以将熔体内夹杂物的含量降至0.5%以下,夹杂颗粒尺寸小于0.3mm,234熔剂的精炼效果好于RJ-1熔剂,经234熔剂精炼后静置8min,镁合金熔体中的夹杂物含量降至0.02%以下,夹杂颗粒尺寸小于10μm。夹杂物沉降速度与夹杂半径的平方、夹杂密度成正比,与镁合金液黏性系数及镁合金液密度和夹杂密度的比值成反比。实践表明,氯化镁可润湿悬浮在合金液中的夹杂物质点,将其吸附聚合而沉入底部,同时熔剂中的氟盐(如CaF2)能部分熔解一些氧化物。因此,为了熔剂能很好地和这些质点结合或作用,必须在加入熔剂的情况下,激烈地搅拌合金液,然后静置一定的时间,以使这些被熔剂吸附的氧化物质点能完全地沉淀至坩埚底部。静置时间越长,则沉淀得越彻底,随着温度的提高,合金液与熔剂的密度差增加,合金液的黏度降低,这样就加速了氧化物质点的沉淀速度。由此可见,合金液在搅拌后静置的温度与时间,对精炼的效果起着很重要的作用。
镁合金的精炼处理也采用加入MgCO3和CaCO3等精炼剂的方法,这主要是因为MgCO3和CaCO3容易分解产生大量的CO2气体,从而起到除气和排渣的作用。熔剂精炼处理是利用熔剂洗涤镁熔体,利用熔剂与镁熔体的充分接触来润湿夹杂物,并将其聚合于熔剂中,随同熔剂与镁熔体沉积于坩埚底部。这种精炼方法实现的基础是熔剂必须要具有良好的润湿、吸附夹杂的能力。
②AZ91合金熔剂法熔炼工艺 将坩埚预热至暗红色(400~500℃),在坩埚内壁及底部均匀地撒上一层粉状RJ-2(或RJ-1)熔剂。炉料预热至150℃以上,依次加入回炉料、镁锭、铝锭,并在炉料上撒一层RJ-2熔剂,装料时熔剂用量占炉料重量的1%~2%。升温熔炼,当熔液温度达700~720℃时,加入中间合金及锌锭。在装料及熔炼过程中,一旦发现熔液露出并燃烧,应立即补撒RJ-2熔剂,炉料全部熔化后,猛烈搅动5~8min,以使成分均匀。接着浇铸光谱试样,进行炉前分析。如果成分不合格,可加料调整,直至合格。将熔液升温至730℃,除去熔渣,并撒上一层RJ-2熔剂保温,进行变质处理。即将占炉料总重量0.4%的菱镁矿(使用前破碎成ф10mm左右的小块)分作2~3包,用铝箔包好,分批装于钟罩内,缓慢压入熔液深度2/3处,并平稳地水平移动,使熔液沸腾,直至变质剂全部分解(时间6~12min);如采用C2Cl6变质处理,加入量为炉料总重量的0.5%~0.8%,处理温度为740~760℃。变质处理后,除去表面熔渣,撒以新的RJ-2熔剂。调整温度至710~730℃,进行精炼。搅拌熔液10~30min,使熔液自下而上翻滚,不得飞溅,并不断在熔液的波峰上撒以精炼剂。精炼剂的用量视熔液中氧化夹杂含量的多少而定,一般为炉料重量的1.5%~2.0%。精炼结束后,清除合金液表面、坩埚壁、浇嘴及挡板上的熔渣,然后撒上RJ-2熔剂。将熔液升温至755~770℃,保温静置20~60min,浇铸断口试样,检查断口,以呈致密、银白色为合格。否则,需重新变质和精炼。合格后将熔液调至浇铸温度(通常为720~780℃),出炉浇铸。精炼后升温静置的目的是降低熔液的密度和黏度,以加速熔渣的沉析,也使熔渣能有较充分的时间从镁熔液中沉淀下来,而不混入铸件中。过热对晶粒细化也有利,必要时可过热至800~840℃,再快速冷却至浇铸温度,以改善晶粒细化效果。熔炼好的熔液静置结束后应在1h内浇铸完,否则需重新浇铸试样,检查断口,检查合格方可继续浇铸,不合格需要重新变质、精炼。如断口检查重复两次不合格,该熔液只能浇锭,不能浇铸件。整个熔炼过程(不包括精炼)熔剂消耗占炉料总重量的3%~5%。
2.1.1.6 变质细化处理
(1)细化的类型及原理 镁合金的一个重要缺点是晶粒粗大和分布不均匀,给强度和理化性质带来极坏的影响。因此,晶粒细化是Mg合金化必须考虑的重要问题之一。可见,通过晶粒细化的方法改善镁合金的工艺性能和力学性能是十分必要的。变质细化处理在镁合金铸造生产实际中的应用非常广泛。晶粒细化是提高镁合金铸件性能的重要途径。资料表明,镁合金晶粒越细小,其力学性能和塑性加工性能越好。在熔炼镁合金过程中晶粒细化操作处理得当,则可以降低铸件凝固过程中的热裂倾向。此外,镁合金经过晶粒细化操作处理后铸件中的金属间化合物相更细小且分布更均匀,从而缩短均匀化处理时间或者至少可以提高均匀化处理效率。因此,镁合金的晶粒细化尤为重要。寻找一种有效的晶粒细化剂和适宜的加工方法是拓展镁合金应用前景的途径。变质细化的基本原理是,往合金液中加入某种难熔物质,以使其在合金液结晶过程中形成多量的结晶核心,以达到细化晶粒的目的。镁合金具有晶粒粗化倾向,某些铸锭及铸件易产生局部晶粒大小悬殊现象,所以要对镁合金进行变质处理,变质处理能显著提高镁合金的力学性能,改善铸造性能,减少热裂、缩松等铸造缺陷。赵浩峰等也较早介绍了常规的细化镁合金晶粒的方法,并研究了细化镁合金晶粒的新方法。
常用的镁合金晶粒细化工艺一般分为几种:一是液态时加入各种晶粒细化剂;二是借助外部能量使枝晶破碎,从而细化铸造组织;三是半固态成形细化晶粒;四是铸锭变形处理,如等静道角压(ECAE)和大比率挤压等细化变形组织;五是铸造粉末冶金成形工艺;六是过热处理;七是强外场作用。变质处理机理是在合金液中加入高熔点物质,形成大量的形核质点,以促进熔体的形核结晶,获得晶粒微细的组织。早期人们采用一种过热变质处理法,即将经过精炼处理的镁合金熔体过热到875~925℃,保温10~15min后快速冷却到浇铸温度,再进行浇铸,具有细化晶粒的作用。研究表明,过热变质处理能显著细化ZM-5合金中的Mg17Al12相,但是这种工艺存在很大的缺点。在过热变质处理过程中,镁合金熔体的过热温度很高,从而明显增加镁的烧损,降低坩埚的使用寿命和生产效率,增加熔体中的铁含量和能源消耗。因此,过热变质处理在生产实际中应用并不普遍,已经基本淘汰了。过热处理是浇铸前将熔体温度升高并保温一段时间后再降温至浇铸温度进行浇铸的工艺过程。如Mg-Al合金晶粒细化的传统方法是对液态合金进行过热处理,将合金过热到850℃左右保温30min,然后快冷到铸造温度浇铸。过热处理对Mg-Al系合金有明显的细化作用。将AZ91E合金过热处理(850℃保温15min)后以2.5℃/s的速度冷却,经600℃铜型淬火得到的试样与未过热处理的600℃铜型淬火试样相比,过热处理后的试样中晶粒明显细化,且形成以“外来物质”为中心的树枝晶,而未过热处理的试样中的“外来物质”并未生成树枝晶。能谱分析表明,该“外来物质”由Al、C和O或由Al、C、Mn、Si和O组成,其中AZ91E合金中Mn和Si是杂质元素,据此推测过热处理过程中形成了Al4C3或Al2CO化合物(Al2CO中的氧可能是磨试样过程中与水反应而引入的)。过热处理对Mg-Al系合金的细化机理是在过热处理过程中生成大量可以作为非均质结晶的晶核,从而增多晶粒的形核数量,细化晶粒组织。过热处理虽然可以细化晶粒,但是熔体温度的升高使氧化和吸气现象更加严重,而且由于杂质和熔体合金的密度均减小,不利于杂质的分离,反而降低了铸锭质量。这种处理最适于砂模铸造,尤其是含Al、Mn和杂质Fe的合金细化效果最为明显。但细化原因还没有一致的看法,Nelson用电子衍射研究Mg-8Al-0.2Mn合金后指出,过热处理的合金有MnAl4相(六方晶格)存在,但在715℃以下或1000℃加热的合金,没有这种含Mn相存在。据此他认为MnAl4或具有六方晶格的其他高熔点化合物在结晶过程中起晶核作用,是晶粒细化的主要原因。过热处理法的缺点是只适用于Mg-Al系合金,而且必须快速冷却到铸造温度,在短时间内即铸造完毕,否则过热处理效果即消失,铸造工艺难于控制。外场作用的基本原理是对合金熔体施以外场(如电场、磁场、超声波、机械振动和搅拌等)以促进熔体形核,并破坏已形成的枝晶,成为游离晶体,使晶核数量增加,还可以强化熔体中的传导过程,消除成分偏析。此外,快速凝固技术、半固态成形技术、铸锭变形等也能提高镁合金的形核率,抑制晶核的长大而显著细化晶粒。
在生产中,镁合金所采用的变质细化剂易与其他高熔点杂质形成高熔点金属间化合物而沉降于炉底。这些难熔杂质和变质剂在镁合金中的溶解度小,熔点高,且密度比镁大。当他们相互作用时,可将合金中的可熔杂质去掉,这对镁合金是有利的。但降低了变质剂的效果,甚至失效。减少镁合金中铁、镍、硅杂质的含量可提高其抗蚀性。由于钛在800~850℃时在镁中的溶解度较大,当低于700℃时溶解度急剧降低,并和铁、硅形成高熔点金属间化合物而沉降,因此,近年来在工业上已开始采用钛废料和低质量的氯化钛来去掉熔体中的铁、硅和部分镍,以提高合金的耐蚀性能。如MB-3合金用低质量的氯化钛(TiCl3+TiCl2)和镁-钛中间合金(含钛24%)处理后,可将合金中的铁、硅含量由0.01% Fe、0.01%Si降低到0.002%Fe、0.001%Si。含锆的镁合金,应严格限制硅、铝、锰杂质的含量。当铝、硅、锰含量各超过0.1%时,合金中的锆含量将大为降低。
(2)晶粒细化剂 目前,熔炼镁合金时常用的变质剂有含碳物质、C2Cl6和高熔点添加剂如Zr、Ti、B、V等。下面简单介绍以下几种常用变质剂的晶粒细化机理及效果。
①添加含Zr的晶粒细化剂 晶粒变质细化处理主要是通过添加晶粒细化剂对液态镁合金熔液进行处理,目前广泛应用的晶粒细化添加剂主要有含Zr的晶粒细化添加剂和含C的晶粒细化添加剂。Zr是Mg合金的有效晶粒细化剂,锆对Mg-Zn系、Mg-RE系和Mg-Ca系等合金具有明显的晶粒细化作用,加入0.2%~0.7%Zr即能显著细化晶粒,消除铸件的显微缩孔或疏松,改善铸锭质量和塑性加工性能。此外,Zr还有净化作用,同杂质Fe形成Zr2Fe3和ZrFe2化合物,沉积于坩埚底部,使合金的纯度和抗蚀性提高。它是目前镁合金熔炼中较常用的晶粒细化剂,但其晶粒细化机理尚不十分清楚。1937年,人们发现Zr对镁晶粒有明显的细化效果,并开始了对镁及镁合金晶粒细化剂的研究。从Mg-Zr相图可以看出:Zr在液态镁中的溶解度很小,发生包晶反应时镁液中仅能溶解约0.6%Zr(质量分数),Zr和Mg不形成化合物,凝固时Zr首先以α-Zr质点的形式析出,α(Mg)包在α-Zr质点外部形成包晶组织。Zr在液态Mg中的溶解度虽不大(645℃,0.58%),但在固态Mg中却有很高的溶解度。α-Zr和Mg均为六方晶型,两者的晶格常数很接近(镁的晶格常数为a=0.320×10-9m,c=0.520×10-9m;α-Zr的晶格常数为a=0.323×10-9m,c=0.514×10-9m)。α-Zr符合作为晶粒形核核心的“尺寸结构相匹配”原则,所以α-Zr能成为α(Mg)的结晶核心。当加入的Zr含量大于0.6%时,镁液中形成的大量α-Zr弥散质点使晶粒显著细化。但是,Zr的加入量不可能很大,当温度达到90℃时镁液中仅能溶解0.7%Zr。此外,溶于基体中的Zr还起到一定的强化作用,故随着Zr含量的增加,合金的力学性能也不断提高。
②合金熔剂法熔炼工艺 含锆ZK40(ZM-1)镁合金的熔炼工艺为:首先与AZ91合金一样进行坩埚、炉料等准备,锆以Mg-Zr中间合金形式加入,并仔细清理炉料,绝不允许与Mg-Al系合金混料。熔化工具也专用,不得与Mg-Al系合金的熔化工具混用。炉料组成(质量分数):新料1%~20%,回炉料80%~90%(其中一级回炉料应占60%以上)。将坩埚加热至暗红色,在其底部撒以适当的熔剂。加入预热150℃以上的镁锭及回炉料,升温熔化。当熔液温度达720~740℃时加入锌。继续升温至780~810℃,分批缓慢加入Mg-Zr中间合金。全部熔化后,搅拌25min以加速锆的溶解,使成分均匀。在熔液温度不低于760℃时浇铸断口试样,若断口不合格,可酌情补加质量分数为1%~2%的Mg-Zr中间合金,重新检查断口,允许第二次补加,若仍不合格,该炉合金只能浇锭。断口合格的熔液可调至750~760℃,将搅拌机叶轮沉至熔液2/3处,搅拌4~6min,并不断在液流波峰上撒以熔炼熔剂,熔剂用量为炉料总重量的1.5%~2.5%。然后清除浇嘴、挡板、坩埚壁及熔液表面上的熔渣,再撒入新的覆盖熔剂。将熔液升温至780~820℃,静置保温15min,必要时可再次检查断口,直至静置总时间为30~50min,即可出炉浇铸。覆盖、精炼均采用RJ-4熔剂。在整个熔炼过程中,熔剂的消耗量占炉料总重量(不包括精炼用熔剂)的2%~3%。精炼后静置时间不允许超过2h,并且保持温度在780~820℃,以免锆沉淀。锆还可以氯锆酸盐或氟锆酸盐(Na2ZrF4)状态加入镁合金中,这时需要注意的是:盐的加入量一般为计算组成的8~10倍;以氟锆酸盐状态加入锆时,由于要求必须过热至900℃,操作中比较困难;以氯锆酸盐状态加入锆时,虽然加入难度小了,但所获得的铸件耐蚀性能不足。含锆镁合金的关键是锆能否加入到镁合金中去,晶粒细化效果是否合格。为此,第一,要仔细清理炉料,采用较纯净的炉料,以减少铁、硅、铝等各种杂质的影响,否则不仅会损耗一定数量的锆,而且会严重影响合金的质量。第二,锆的温度不低于780℃,否则锆很容易沉淀在坩埚底部,造成合金中锆量不足。温度高于820℃,熔液表面氧化加剧,且将从大气中吸氢,同时因铁的溶入量增加,锆与铁、氢形成的化合物增多,也会加大锆的损耗,削弱锆的细化效果。为避免锆的沉淀析出,应尽量缩短合金液的停留时间,特别是760℃以下的停留时间。
值得说明的是,Zr必须充分溶解在Mg液中才有细化晶粒的作用,在理论上溶于Mg液中的Zr必须超过0.58%,才能得到预期的效果。为了保证这一点,在坩埚底部必须保持过剩的Zr,才能保证Mg液中溶解足够的Zr。因此在浇铸前应避免倒换坩埚,应直接用原坩埚铸造,否则Mg液中溶解的Zr量会立即下降。如果必须倒换坩埚,应向新坩埚中补加Zr,以保证晶粒细化效果。Zr的晶粒细化作用可用包晶反应的形核机理来说明。但应注意同Zr共存元素的影响,有些元素如Zn、Cd、Ce、Ca、Th、Ag、Cu、Bi、Tl和Pb等,能促进Zr的晶粒细化作用,有的元素如Al、Si、Mn、Ni、Sb、Fe和H等,通过降低Zr在Mg液中的溶解度,或者形成锆化物,而起阻碍作用。因此,Zr在Mg-Zn-Zr、Mg-Ce-Zr和Mg-Th-Zr合金中的晶粒细化作用非常有效,但应限制Mn含量,也不能用Al作这类合金的合金元素。Zr对Mg铸件力学性能的影响非常显著,0.7%Zr既能显著细化晶粒,又能同时提高强度和塑性。王顺成等采用K2ZrF4和KBF4混合粉末与铝熔体直接反应制备镁合金晶粒细化剂Al-5Zr-1B合金,利用光学显微镜、X射线衍射仪和扫描电镜,研究了Al-5Zr-1B合金的显微组织及其对纯Mg和AZ31镁合金的晶粒细化作用。结果表明:Al-5Zr-1B合金中含有大量细小的ZrB2粒子,平均尺寸为0.2μm,ZrB2粒子作为异质形核核心使纯Mg和AZ31镁合金晶粒得到细化。随着Al-5Zr-1B合金添加量的增加,纯Mg和AZ31镁合金的晶粒尺寸逐渐减小。添加0.3%(质量分数)的Al-5Zr-1B合金,可使纯Mg晶粒从1400μm细化到120μm。添加0.6%的Al-5Zr-1B合金,可使AZ31镁合金晶粒从170μm细化到45μm。
在添加等量锆的情况下,锆合金化条件不同,其晶粒细化效果存在显著差异。Sauerwald认为只有浇铸时溶入镁液中的那部分锆才具有晶粒细化作用,这种观点在20世纪60年代中期以前得到普遍认可。基于光学显微组织观察,Emley提出包晶温度下Zr粒子从熔体中分离出来并与镁液反应生成富锆的镁基固溶体,直到剩余熔体内锆含量下降至较低值。同时他指出在包晶温度附近形成的富锆粒子具有促进熔体形核的作用。由于α-Zr是镁合金的形核质点,Tamura等研究了不同工艺条件下(包括搅拌时间、熔体静置时间等)往720℃镁液中添加1%Zr对所形成的Mg-Zr合金晶粒尺寸的影响。他们发现,在镁熔体浇铸前重新搅拌时晶粒细化效果更显著,由于重新搅拌前后固溶的锆没有发生变化,这说明部分不溶于镁液的锆也具有晶粒细化作用。M.Qian等认为镁-锆合金的晶粒细化效果主要来自于固溶于镁中的锆,而没有固溶的那部分锆只有约30%的晶粒细化作用。通常,Mg-Zr合金熔体中的加锆量稍高于理论值,只有熔体中可溶于酸的锆过饱和时,Mg-Zr合金才能取得最佳的晶粒细化效果。由于熔体中还可能存在各种污染物,导致生成不溶于酸的锆化物,因此熔体中尽可能不要含铝和硅。此外,有必要保留坩埚底部含锆的残余物质(包括不溶于酸的锆化物)。为了防止液态残渣浇铸到铸件中,铸型浇铸后坩埚中要预留足量的熔融合金(大约为炉料质量的15%)。浇铸时要尽量避免熔体过分湍流和溢出,并且熔炼工艺中要保证足够的静置时间。对于Mg-Zn合金系,加入0.5% Zr可以起到很好的变质效果。采用0.5% Sc+(0.3~0.5)%Sm可使Mg-Mn系合金的晶粒细化,(0.2~0.8)%La也可以使Mg-Mn系合金的晶粒细化。Zr和Al易形成稳定的化合物(Al3Zr),而Al3Zr晶体为体心正方型,晶格常数为a=0.4.315nm,c=16.93nm,与Mg相差很大,而且形成Al3Zr将造成合金中Al和Zr的损失,所以Mg-Al系合金中不能用Zr细化晶粒。由于锆的熔点高(1855℃)、密度大(6.45g/cm3),在镁熔体中难以熔解,无法以纯锆的形式加入;而锆在镁中的溶解度又很低,难以制成含锆量高、成分均匀的Mg-Zr中间合金,锆的化学活性很强,与炉气中的氧、氮、氢、CO、CO2及合金中的铁、铝、硅、锰、钴、镍、锑、磷等均能生成不溶于镁的化合物,沉积于坩埚淤渣中,从而使合金中的含锆量下降。因此,生产中锆的实际加入量一般为合金成分需用量的3~5倍,并多以Mg-Zr中间合金形式加入。
③氯盐方法 这种方法起源于德国,在熔体中加入少量无水FeCl3,晶粒细化的原因是含铁化合物的形核。这种方法也有它的缺点,由于FeCl3容易吸潮,因此这种方法有一定危险性。此外,少至0.005%的铁的存在就能降低合金的抗蚀性,加锰可以抵消铁对抗蚀性的影响,但同时却阻止了FeCl3的晶粒细化作用。对以铝为主要合金元素的合金目前用的方法是在熔体中加入易挥发的含碳化合物,通常把小团块形式的六氯乙烷(0.025%~0.1%,质量分数)保持在熔体的底部,分解成碳和氯。晶粒细化作用归因于Al4C3或AlN·Al4C3对熔体的孕育作用。氯的释放对熔体有一些除气作用,这是这一方法的另一个优点。可以使用MnCl2(化学纯,MgCl2>99.99%,质量分数)。
④金属银细化法 有人试验研究了典型镁合金ZM-5的各组元对性能的影响,特别研究了添加金属银对组织细化及合金性能的改善。在此基础上采用正交试验法优选出新型镁合金GQMZ96的成分和配比,该合金与国内外常用镁合金相比,具有较好的力学性能和铸造性能。试验时在不改变ZM-5基本成分的前提下,合金中Ag的质量分数分别为0.1%、0.15%、0.2%、0.25%、0.30%、0.40%,经浇铸试棒、测定性能、观察断口并用热裂环法确定显微缩松和热裂环宽,发现显微缩松和热裂环宽等缺陷有明显改善。在ZM-5中添加质量分数为0.25%的Ag,再加质量分数分别为7.5%、8.0%、8.5%、9.0%、10.0%的Al,看出铝质量分数的增加对性能的影响。提高锌的质量分数有利于提高屈服强度,但会引起合金晶粒粗大,加大铝的质量分数可细化晶粒,加入银也可抵消锌的质量分数增加引起的晶粒粗大现象,从总体上基本消除合金晶粒粗化。基于以上分析和认识,在ZM-5基本成分中加入质量分数分别为0.2%和9.0%的Ag和Al,然后分别加入质量分数为1.0%、2.0%、3.0%、4.0%的Zn,经熔制测试,其结果为随着锌的质量分数增加,屈服强度大幅度增长。加入少量的锰,可降低铁在镁中的溶解度,减少杂质铁的有害作用,同时提高合金的电位,提高抗蚀性,细化晶粒。但锰对合金的性能不起主要作用,因此取锰的质量分数为0.2%。
(3)六氯化碳变质工艺 对于不能用Zr细化的Mg-Al系合金,可以采用碳质孕育法,其原理是镁合金熔液中的碳化物(MgCO3或C2Cl6)在高温下分解出碳原子,碳原子与Al化合,形成大量弥散的Al4C3质点,该质点是高熔点的稳定化合物,并与Mg的晶格常数接近,可作为结晶时的非均质晶核。C2Cl6是镁合金熔炼中最常用的变质剂之一,可以同时达到除气和细化晶粒的双重效果。有人认为用C2Cl6处理镁-铝系合金能显著细化晶粒,比用MgCO3变质处理的力学性能提高10%~20%,而且变质后两小时浇铸,仍具有良好的力学性能。有人开展了C2Cl6对AZ31合金晶粒细化效果的研究,研究表明,铸件中形成了Al-C-O化合物质点来充当晶核的核心。AZ31经过C2Cl6变质处理后晶粒尺寸由280μm下降到120μm,抗拉强度明显提高。对ZM-5合金而言,C2Cl6的变质处理效果比MgCO3好得多。此外,也可以采用C2Cl6和其他变质剂进行复合变质处理,其效果更好。在Mg-Al合金熔体底部放置C2Cl6或环氯苯片也可以达到细化晶粒和除气的双重目的。现在熔炼含Al合金常用的挥发性含碳化合物,如甲烷、丙烷、四氯化碳、六氯乙烷或固体炭粉等有明显的细化晶粒作用,就可能是液态合金中的Al与C反应生成Al4C3或AlN·Al4C3等结晶核心的结果。然而经过研究发现,作为核心的棒状物由Al、C和O组成,而并非仅仅是Al和C。目前,人们对C细化镁合金晶粒的机理还没有明确的认识,尚需要进一步的研究。
(4)碳酸钙变质工艺 对镁-铝合金较成功的晶粒细化工艺是碳质孕育法。其原理是镁液中的碳化物在高温下分解并发生下列反应:,生成的二氧化碳与镁反应
生成碳原子。新生成的碳原子与铝化合
形成大量的碳化铝质点。碳化铝是镁原子良好的非均质晶核,使镁晶粒细化。碳不能固溶于镁中,但可与镁反应生成Mg2C3和MgC2化合物。碳对Mg-Al系或Mg-Zn系合金具有显著的晶粒细化作用,而对Mg-Mn系合金的细化效果非常有限。人们对含碳变质剂细化镁合金晶粒的机理提出了多种假设。Battelle Memorial研究所认为C加入到Mg-Al系合金熔体后,C与Al反应生成大量细小、弥散的Al4C3质点,其晶格常数与镁的非常接近,可作为形核质点,从而可以细化镁合金的晶粒。目前这种假设得到了普遍认可,但仍缺乏试验依据。工业上常用的含碳变质剂有菱镁矿(MgCO3)、大理石(CaCO3)、白垩、石煤、焦炭、CO2、炭黑、天然气等。其中MgCO3、CaCO3最为常见。
目前在工厂实际生产中广泛采用的变质方法是用“碳”变质处理,即往合金液中加入碳酸钙,发生下列反应:
(2-1)
(2-2)
在熔体中加入的CaCO3含碳的化合物,在高温下碳化物分解还原出碳。同样,加入C2Cl6等在高温下碳化物分解还原出碳,碳又与铝生成大量弥散分布的Al4C3难熔质点。Al4C3是高熔点高稳定化合物,其在镁液中以固态质点形式存在,Al4C3与α(Mg)均为六方晶系,两者晶格常数接近,晶格常数与δ(Mg)仅差4%。根据金属结晶原理,错配度小于9%即可成为晶核,故Al4C3是Mg原子的非均直晶核,大量弥散的Al4C3晶核使Mg晶粒细化。碳质孕育后的合金若迅速搅拌或短时升温至800℃,再快速冷却到浇铸温度,则可以使合金液中的Al4C3质点更加弥散分布,从而使晶粒进一步细化。但是也有研究认为,作为核心的棒状物由Al、C和O组成,而并非仅仅是Al和C,提出该化合物的分子式为Al2OC。目前,人们对C细化镁合金晶粒的机理还没有明确的认识,尚需要进一步的研究。表2-27为镁合金中某些相的晶格常数。
表2-27 镁合金中某些相的晶格常数

碳酸钙可用白垩(ROCT1498-42A级)或大理石。在使用前,白垩应在150~200℃下烘干,并经过0.2~0.5mm的筛子过筛。而大理石则应以经过洗涤后干燥过的小块的形状加入。在过加入时,用铝箔将变质剂包好,借助于钟形罩分1~2次加入合金中。含有钙的合金,因为钙已具有细化晶粒的作用,因而,不需进行变质处理。
生产实践发现,变质处理后,随着熔体静置时间的增加,晶粒将逐渐变粗(低温静置更为明显),所以工艺上规定变质处理后45min之内必须浇铸完毕;用“碳”变质与加强搅拌或短期升温至800℃,随后快冷至浇铸温度。合金中含有一定量的锰,有利于细化晶粒,Al-Mn中间合金中,锰的质点越细小、分布越均匀,对合金的细化效果越好。
(5)碳酸镁变质工艺 由于镁合金在减轻产品质量、节省能源及增强产品可靠性等方面具有优势,它的开发应用近年来受到高度重视。一般镁合金的力学性能强烈地依赖晶粒尺寸。Z91D镁合金属于密排六方结构,它在塑性变形性能和力学性能上呈现较低的特征。采用晶粒细化的方法可在很大程度上改善镁合金的力学性能。生产中还加碳酸镁,其变质细化工艺见表2-28。碳酸镁可用天然菱镁矿(如东北的大石桥菱镁矿)和工业无水碳酸镁。前者应经过洗涤、粉碎(10~15mm或粉状)和干燥;后者则只需在150~200℃下烘干1~2h。用时,将其用铝箔包好,借助于钟罩分1~2次加于合金液中。处理工艺对变质细化效果影响很大,如将熔体过热到850℃或更高的温度保持30min,然后快冷到正常的铸造温度进行浇铸能得到好的效果。虽然原因不十分清楚,但这种方法可相当成功地得到较细晶粒。张永忠、赵浩峰选用MgCO3、La2(CO3)3及两者的混合物分别作为AZ91D镁合金的细化剂。实验结果表明,MgCO3和La2(CO3)3作为镁合金的细化剂各有特点,而用MgCO3与La2(CO3)3的混合物细化效果更好。为了进一步了解碳酸镁的细化能力,刘红梅、赵浩峰等详细研究了碳酸镁的作用。采用1号镁锭(Mg>99.99%)、1号铝锭(Al>99.7%)、1号锌锭(Zn>99.99%)为原料来熔制AZ91D合金,在熔化过程中,采用RJ-2号作为覆盖剂,并用MgCl2+水玻璃作为涂料刷坩埚。用SG-3-10型坩埚电阻炉及30mL铁坩埚熔制合金液,采用熔剂保护。进行试验时,熔制和变质处理合金的顺序如下。①预热。因镁在高温情况下遇水会发生激烈反应,所以所有的炉料及设备必须严格干燥出去水分,然后先将坩埚在1500W电炉预热,刷涂料,干燥,将镁块、铝块、锌块依次置于坩埚内,将坩埚放入坩埚电炉内,升温至200℃,预热干燥,将氯化锰、熔剂、细化剂、铁铸模置于1500W电炉上预热备用。②装料。将预热好的坩埚取出,将氯化锰和熔剂依次加入,然后再将坩埚置于电阻坩埚炉内。③熔化。将电炉升温,融化,保温10min。④加入细化剂。在熔化后的镁合金液中加入细化剂并保温10~25min。⑤用坩埚钳将处理完毕的坩埚取出,拔渣后在700℃浇铸。⑥打开铸模,取出镁合金锭。硬度试样用金相试样,用HBRV-187.5型布洛维氏硬度机测试硬度,压头直径为2.5mm,负荷为187.5kgf(1kgf=9.8N),保持时间为30s,通过查表换算为布氏硬度。金相试样从距冲击试样底部30mm处截取,用金相砂纸磨光后在P-2型金相试样抛光机上抛光(用Cr2O3粉作抛光剂),用85%盐酸水溶液+15%的硫酸水溶液腐蚀,由XJ-16A型立式金相显微镜观察金相组织。采用KYKY2800型扫描电镜,深腐蚀观察初生α相的晶核的形貌,以及各相的形貌与分布等。微区成分分析确定元素的分布以及晶内偏析等。AZ91D晶粒细化工艺是合金升温至730~820℃熔化后,加入MgCO3细化剂,炉内保温10~25min,700℃浇铸试样。在试样端部30mm处切取金相试样,然后从计样边缘到中心全面观察晶粒尺寸变化。实验结果表明,未处理的AZ91D合金的金相组织为粗大的树枝晶,平均枝晶间距d=400μm;添加MgCO3处理后的AZ91D合金晶粒明显细化成为等轴晶组织,其细化效果与细化剂的加入量以及工艺条件有关。实验结果表明,当细化剂中折算的碳量为0.1%(质量分数)时,已有明显的细化效果。当加入量为0.4%时,效果已达到理想状态。进一步增大细化剂加入量,细化效果不明显。分别取温度730℃、760℃、790℃和820℃来处理合金,温度过大或过小细化效果都会受到影响,当温度为790℃时细化效果最好,这是因为温度太低,生成的Al4C3在合金液中不能很好地扩散甚至发生凝聚现象;而温度太高使得MgCO3烧损过大造成有效的C原子减少。当保温时间为10min时细化效果已达到理想效果。延长保温时间,细化效果无多大变化。在不同的过热度下对细化剂处理后的合金液进行长时间保温,可以较好地检验复合盐细化剂的细化效果和抗衰特性。从金相观察看出,连续保温直到1.5h晶粒并没有粗化且晶粒分布比较均匀一致,从2h开始晶粒开始有所增大。说明没细化剂具有比较长时间的抗衰退性。经过电镜分析,证实了合金中碳的存在,说明碳可能与铝形成了化合物,起到了晶核的作用。Mn与Zn原子在合金中的分布比较均匀,而Al与C原子的分布有一定的聚团倾向,这充分说明了Al4C3在合金中充当了异质晶核作用。
表2-28 镁合金的变质工艺过程

在镁液中加入碳酸镁,会有如下反应:
(2-3)
(2-4)
(2-5)
上面三式中的ΔG值在700~900℃均小于0,即在700~900℃Al4C3很容易生成。从热力学角度分析,式(2-3)和式(2-4)的反应在高温下很容易发生,而生成的C原子与镁的润湿性很好,所以在实验条件下生成的C原子迅速扩散到镁液中与其中的Al反应生成Al4C3颗粒。镁合金熔体中会产生大量细小而难熔的Al4C3质点,呈悬浮状态并在凝固过程中充当形核基底。MgCO3的加入量一般为合金熔体质量的(0.5~0.6)%,熔体温度为760~780℃,变质处理时间为5~8min。
对于Mg-Al系合金较成功的晶粒细化工艺是碳质孕育法,其原理是镁液中的碳化物(MgCO3、C2Cl6等)在高温下分解并发生下列反应:
新生的C原子与Al化合(3C+4Al→Al4C3)形成大量弥散的Al4C3质点,Al4C3是高熔点、高稳定性化合物,其在镁液中以固态质点形式存在,而Al4C3与α(Mg)均为六方晶系,两者晶格常数相近。根据金属结晶原理,晶格常数错配度小于9%即可成为晶核,故Al4C3是Mg原子良好的非均质晶核,因而大量弥散的Al4C3晶核使Mg晶粒细化。碳质孕育后的合金若迅速搅拌或短时升温至800℃,再快速冷却到浇铸温度则可以使合金液中的Al4C3质点更加弥散分布,从而使晶粒进一步细化。
(6)含镧碳化物在镁合金中的细化及强化作用 早在20世纪30年代,人们就发现稀土对镁的细化及强化作用。随着镁合金在高强和高温应用领域的开发,稀土在铸造镁合金中的应用得到了进一步的发展。刘红梅、赵浩峰等采用碳酸镧来处理AZ91D镁合金,并与碳酸镁的实验效果作对比。实验结果表明,未处理的AZ91D合金的金相组织为粗大的树枝晶,平均枝晶间距d=400μm。添加La2(CO3)3处理后的AZ91D合金晶粒明显细化成为等轴晶组织,其细化效果与细化剂的加入量以及工艺条件有关。平均晶粒尺寸与折算C(质量分数)的关系如图2-1所示。由图中看出,随着La2(CO3)3加入量的增加,平均晶粒尺寸在C=0.4%(质量分数)以前急剧下降,在0.4%(质量分数)以后则基本无多大变化。加入La2(CO3)3(C=0.4%)后晶粒尺寸可以细化到30μm;与加入MgCO3作比较,相同质量分数下晶粒尺寸可以细化到50μm。

图2-1 平均晶粒尺寸与C(质量分数)含量的关系
温度过高或过低细化效果都会受到影响,温度为790℃时细化效果最好。原因是温度太低,生成的化合物在合金液中不能很好地扩散,而温度太高使得La2(CO3)3烧损过大造成有效的C原子和La原子减少。当保温时间为10min时细化效果已达到理想效果,延长保温时间,细化效果无多大变化。连续保温后期晶粒并没有粗化且晶粒分布比较均匀一致,说明La2(CO3)3作为细化剂比MgCO3具有更长久的抗衰退性。通过电镜分析发现,加入La2(CO3)3后合金中有两种不同的物质生成,一种是C原子与Al化合形成弥散的Al4C3质点,另一种是La与Mg在晶界处形成化合物Mg12La。这些化合物不仅能细化合金,而且对晶粒起到钉扎作用,进一步提高了合金的力学性能。由图2-2可知,冲击韧性随细化剂加入量的增加先增大后减小,当C含量等于0.4%时,冲击韧性达到最大值。这是因为继续增大细化剂加入量时,硬而脆的Mg12La相增多,使冲击韧性有所降低。细化剂加入量对冲击韧性的影响大,而对硬度的影响小。在硬度略有提高的情况下,冲击韧性却提高2~4倍。

图2-2 冲击韧性随细化剂加入量的变化
(7)含镁、含镧混合碳化物在镁合金中的细化及强化作用 韩世平、刘红梅、赵浩峰等对镁-铝系合金晶粒细化工艺过程进行了研究,传统的变质剂采用的是MgCO3或C2Cl6等,而他们分别用MgCO3和La2(CO3)3处理AZ91D镁合金。实验结果表明,La2(CO3)3的细化效果要优于MgCO3对镁合金的晶粒细化效果。平均晶粒尺寸与MgCO3和La2(CO3)3比例的关系如图2-3所示。由图2-3可以看出,当MgCO3/La2(CO3)3(0.4% C)=1/4时,平均晶粒尺寸为10μm,比加入MgCO3(0.4% C)晶粒尺寸小将近40μm,比加入La2(CO3)3(0.4% C)晶粒尺寸小将近20μm。由图中还可以看出,MgCO3/La2(CO3)3=1/4时平均晶粒尺寸为最小值。随着MgCO3/La2(CO3)3的增大,平均晶粒尺寸有所增大,这是因为随着MgCO3/La2(CO3)3的增大,有效的镧原子减少。连续保温直到2h以内平均晶粒尺寸并无多大变化,从2.5h开始晶粒尺寸有所增大。说明以MgCO3和La2(CO3)3的混合物作细化剂比用单一的一种具有更长时间的抗衰退性。

图2-3 保温时间与平均晶粒尺寸的关系
图2-4列出了细化剂比例与冲击韧性的关系。由图中曲线看出,在La2(CO3)3/MgCO3=1/4处,730℃的冲击韧性值最低,而790℃的值最高。随着细化剂比例MgCO3/La2(CO3)3的增大,730℃和760℃曲线缓慢下降,790℃和820℃曲线则下降速度很快。在La2(CO3)3/MgCO3超过2/3后,四个系列的曲线都呈缓慢下降趋势。

图2-4 细化剂比例与冲击韧性的关系
在相同的细化剂比例下,温度对合金力学性能的影响如图2-5所示。图中系列1为Mg-CO3/La2(CO3)3=1/4、保温时间为10min的情况,图中系列2为MgCO3/La2(CO3)3=2/3、保温时间为15min的情况,图中系列3为MgCO3/La2(CO3)3=3/2、保温时间为20min的情况,图中系列4为MgCO3/La2(CO3)3=4/1、保温时间为25min的情况。由图(a)可知,系列1曲线冲击韧性值最高,而系列4的值最低,随着温度升高,四个系列冲击韧性都增大。当温度超过790℃时,四个系列冲击韧性又都下降。系列1曲线变化幅度最大,系列2、3曲线次之,系列4曲线则几乎呈直线。总的来说,随温度的升高,冲击韧性与硬度先增大后减小,在T=790℃处达到最大值,表明温度过大或过小冲击韧性与硬度都会降低。这可能是因为温度越低,一方面合金的黏度越大,加入的细化剂不能充分扩散反应,另一方面生成的Al4C3在合金液中不能很好地扩散甚至发生凝聚现象;而温度太高则使MgCO3和La2(CO3)3烧损增大,从而使有效的C原子和La原子减少。

图2-5 温度与合金力学性能的关系
2.1.1.7 镁合金的阻燃处理
(1)镁合金表面阻燃途径
①阻燃技术 镁合金表面防燃技术是一个世界范围的课题,早期曾尝试采用气体保护系统,但效果并不理想。后来,人们开发了熔剂保护熔炼的工艺。在熔炼过程中,必须避免坩埚中熔融炉料出现“搭桥”现象,将余下的炉料逐渐添加到坩埚内,保持合金熔体液面平稳上升,并将熔剂轻轻撒在熔体表面。每种镁合金都有各自的专用熔剂,必须严格遵守供应商规定的熔剂使用指南。在熔化过程中,必须防止炉料局部过热。采用熔体氯化工艺熔炼镁合金时,必须采取有效措施收集Cl2。在浇铸前,要对熔体仔细撇渣,去除液体表面化合物,特别是影响抗蚀性的氯化物。浇铸后,通常将硫粉撒在熔体表面以减轻其在凝固过程中的氧化。铸造镁合金,在熔化、浇铸及冷却过程中,镁合金容易与空气接触,发生氧化甚至燃烧。王媛媛等阐述镁合金防燃技术的研究与实际应用,为镁合金防燃起到指导作用。将熔体表面与氧气隔绝是安全地进行镁合金熔炼的最基本要求。
镁合金防燃的方法有两个途径。一是改善合金液表面的致密度系数;二是采用覆盖剂或惰性气体阻碍反应的进行。目前,主要是通过以下三个方法:一是以易熔的盐类熔剂进行覆盖;二是在有活化反应的气氛下进行熔体处理以形成较薄的防护膜;三是以抑制性的元素添加在熔体中。具体的方法大致如下:以盐类溶剂覆盖于熔体上;在惰性气氛下处理熔体;将抑制元素添加在熔体上作为覆盖层;在反应性气氛下处理熔体,在其上形成薄的保护层。在熔炼镁合金过程中必须有效地防止金属的氧化或燃烧,可以通过在金属熔体表面撒熔剂或无熔剂工艺来实现。通常添加微量的金属铍和钙来提高镁熔体的抗氧化性。熔剂熔炼和无熔剂熔炼是镁合金熔炼与浇铸过程的两大类基本工艺。1970年之前,熔炼镁合金主要是采用熔剂熔炼工艺。熔剂能去除镁中杂质并且能在镁合金熔体表面形成一层保护性薄膜,隔绝空气。然而熔剂膜隔绝空气的效果并不十分理想,熔炼过程中氧化燃烧造成的镁损失比较大。此外,熔剂熔炼工艺还存在一些问题,一方面容易产生熔剂夹杂,导致铸件力学性能和耐蚀性下降,限制了镁合金的应用;另一方面熔剂与镁合金液反应生成腐蚀性烟气,破坏熔炼设备,恶化工作环境。为了提高熔化过程的安全性和减少镁合金液的氧化,20世纪70年代初出现了无熔剂熔炼工艺,在熔炼炉中采用六氟化硫(SF6)与氮气(N2)或干燥空气的混合保护气体,从而避免液面和空气接触。混合气体中SF6的含量要慎重选择。如果SF6含量过高,会侵蚀坩埚,降低其使用寿命;如果含量过低,则不能有效保护熔体。总的来说,无论是熔剂熔炼还是无熔剂熔炼,只要操作得当,都能较好地生产出优质铸造镁合金。
②镁合金熔体表面燃烧机制 和氧及氧化物的反应有:
燃烧/氧化:
(2-6)
液体镁合金中的水分迅速汽化:
(2-7)
和水反应/氢气爆炸:
(2-8)
和氧化硅的反应:
(2-9)
③致密度系数的影响 金属液抗氧化能力的强弱由其表观膜阻碍反应物质通过的难易来反映。
G=V1/V2 (2-10)
式中,V1为金属氧化物体积;V2为金属体积;G为致密度系数。Mg的致密度系数是0.79,Al的致密度系数是1.28。Al液的表面是一层致密的氧化物保护膜,隔绝了金属与空气的接触。而镁液表面则是多孔性的疏松组织,应力状态呈张应力,镁易于蒸发,并且与空气接触氧化燃烧。起始合金液表面只有菜花状的氧化物,散发出红色光芒,随氧化反应的加剧,释放出大量的热量,温度最高可达3000℃。最终导致散发出耀眼的亮光,并出现镁蒸气燃烧产生的白烟,原料成废渣。苏桂花等讨论了稀土氧化膜的致密度系数,他们分析了稀土元素及其氧化物的电负性、氧化反应Gibbs自由能变及相关物性参数,系统指出稀土元素对镁合金抗氧化性能的影响,并分别从热力学和动力学的角度对相应的作用机理进行了分析。研究表明,稀土与氧的亲和力大于镁与氧的亲和力,且重稀土比轻稀土的亲和力更强,但Yb的性质与La、Ce等轻稀土的相近。温度为1023K及溶液中稀土的摩尔分数大于0.14时,所有稀土都有可能与MgO发生置换反应。氧化物物性分析显示,除Yb和Eu外的稀土氧化膜的致密度系数都大于1,有较好的保护作用。加入适量稀土的镁合金熔液表面的氧化膜分两层,外层为MgO,内层为MgO和RE2O3的复合氧化膜,且RE2O3填补了MgO氧化膜中的疏松和孔洞,可以有效抑制镁合金的进一步氧化。
④抑制性元素 起抑制性作用的元素有Be、Ca、Zn。Be在镁熔体中有高的扩散速率,所产生的BeO有高的热力学稳定性,且挥发倾向性小,BeO在熔体表面形成压应力,在熔体上覆盖有足够BeO,致密度系数为1.68,起到甚佳的防护作用。取Zn的上限成分约1.5%时,Zn也可以作为合金元素在镁熔体上构成致密的覆盖层。少量Ca(小于0.1%)可以延缓镁的燃烧反应,但超过0.8%的Ca时有强烈的热裂及黏膜倾向。
(2)熔剂阻燃处理
①对熔剂的要求 在镁合金的熔炼过程中,熔剂起着极为重要的作用。盐类溶剂以400℃的温度在熔融状态下覆盖于镁熔体表面,切断镁液与空气接触,阻碍镁氧化反应的发生。盐类以光卤石为基础,加上由MgCl2、KCl所组成的低熔点共晶混合物,添加高熔点萤石粉(CaF2)约20%,除可作为覆盖物外,还可以对熔体起净化作用。覆盖盐所起的防护作用可以维持在800℃以上。盐类熔剂的缺点是在与潮湿的空气接触时产生腐蚀性的氯化物以及形成盐酸性气体,对机器设备和工作环境有很大的不利影响。另外,盐类熔剂很容易在铸件中形成夹杂,损害铸件质量。资料表明,镁液表面熔剂层覆盖的好坏、精炼效果的优劣,以及浇铸过程中能否避免熔剂混入铸型等问题均在很大程度上对所用的熔剂的性能有重要影响。根据实践和对熔剂功能的理论分析,对熔剂的性能提出一些要求。
a.熔化温度。熔剂的熔化温度应低于所熔金属的熔点,这样可使熔剂在整个熔炼过程中均能保持为液态,这对于覆盖熔剂来说,是在金属熔化前即形成完整、严密的覆盖层的必要条件之一。对于精炼熔剂来说,在熔炼温度下处于液态也是保证它能很好地吸附夹杂并且在混入金属液时能很快地排出的一个必要条件。这是由于液态的熔剂易于汇成较大的球形液滴,有利于从金属液中分离。
b.密度。熔剂应与金属液间有较大的密度差,特别是内部熔剂法所用的精炼熔剂。这样当熔剂混入金属液中时也就能使它易于排出而不致产生熔剂夹杂。覆盖熔剂的密度应小于金属液以保证它能很好地浮在金属液面上,但在熔镁时由于镁液的密度很小(在700℃下约为1.55g/cm3),很难找到密度明显小于镁液的熔剂,此时就只能选用与镁液间有适当密度差的熔剂,另外再利用表面张力来使它停留在镁液表面上。
c.黏度。从覆盖的观点来看,熔剂的黏度应小些,这样可使表面覆盖熔剂层在熔炼操作中被推开以后能较快地闭合,即能使铺展过程进行得比较快,可显著减少金属的氧化,这一点在用浇包舀取镁液时,表现得甚为明显。但从浇铸操作的角度出发,希望在浇铸时熔剂的黏度应稍大些,例如,在固定式坩埚中熔炼镁合金时,如果液面上的覆盖熔剂层的黏度过小,流动性过大,用浇包将熔剂层刚推开不久,熔剂层就迅速闭合,因此就很难避免熔剂混入浇包中去。又如在可提式坩埚中熔炼镁合金时,如果在熔炼后期不采取措施使表面熔剂层稠化、结壳,则即使采用挡渣工具,熔剂也很易随同液流混入铸型中去。总结上述可知:在熔炼过程中为了覆盖良好,应使黏度较小些;但在浇铸时,特别是直接用熔化坩埚浇铸,则又希望熔剂尽可能稠些,使表面熔剂层在浇铸时很容易被挡住而不致落入液流中去。此外,对于精炼熔剂,黏度亦应适当,如果黏度过大,则其吸附夹杂的能力将大大降低,因而影响精炼能力。
d.夹杂物。熔剂中不应带有对金属液质量有害的杂质及夹杂物,对精炼溶剂应具有良好的精炼能力。熔剂吸湿性应小,为避免从熔剂中将水分带入金属液,熔剂在使用前应经充分烘干并很好地保存。
e.化学稳定性。熔剂的化学稳定性要高,即熔剂在熔炼温度下应不与合金液(包括基本金属及各合金元素)、炉衬及炉气间发生化学反应,以及熔剂本身不挥发、不分解。这样可使合金中各元素的损耗较少,成分较为准确,以及可以避免由于化学反应产生新的杂质和非金属夹杂物进入镁液,不致使炉衬很快受到侵蚀而损坏,并且避免使熔剂由于发生反应而很快失去效用。此外,熔剂本身应对人体无毒,其成本应低,且能大量供应,最好能结合当地资源就地取材。为了满足上述对熔剂性能提出的多方面的要求,采用一种物质是不可能达到的。因此实际使用的熔剂常是多种组元的混合物,通过各个性能不同的组元来使混合物的性能基本上达到上面所提出的要求。熔炼铝、镁合金时所用的熔剂绝大多数是卤素盐类的混合物,在卤盐中又大多数采用碱或碱土金属的卤盐,原因是它们的化学稳定性较高,熔炼时不致与金属等发生化学反应。
②熔剂层的作用 熔剂对镁熔体的铺展、覆盖、精炼能力的好坏和熔剂的成分配比有密切关系,配制好的合格熔剂如保存不当,吸湿后(因熔剂吸湿性强,特别是MgCl2),含水量超过标准,加到镁熔体中就会产生大量氧化夹杂。熔剂中的MgCl2与水作用生成MgO,在液面上结成小团,不能很好地铺展、覆盖,失去精炼作用。水量较多时,熔剂与熔体接触时会产生火花,甚至会引起镁熔体的飞溅性爆炸。为了防止镁液的氧化燃烧,生产中一直采用在熔剂层保护下熔炼的方法。其作用是:覆盖作用,熔融的熔剂借助表面张力的作用,在镁液表面形成一连续、完整的覆盖层,隔绝空气,阻止Mg与O2、Mg与H2O反应,防止镁的氧化,亦能扑灭镁的燃烧;精炼作用,熔融的熔剂对非金属夹杂物有良好的润湿能力、吸附能力、聚合造渣能力,并利用熔剂与金属的密度差,把非金属夹杂物随同熔剂自熔体中排除。
传统的覆盖和精炼用熔剂的化学成分由MgCl2、KCl、CaF2及BeCl2等氯盐、氟盐混合物组成。熔剂中采用碱金属和碱土金属的卤化物是因为它们的化学稳定性高。几种盐按一定比例混合,使熔剂的熔点、密度、黏度及表面性能等均能较好地满足使用要求。
③MgCl2在镁合金熔化中的作用 镁合金熔剂的主要成分是MgCl2,它的熔点为708℃。它易与其他盐混合形成低熔点盐类混合物,如无水光卤石(含44%~52% MgCl2及32%~46% KCl),这种混合物的熔点仅为400~480℃。因此,流动性很好,在镁熔体表面能迅速地铺展成一层连续、严密的熔剂层。MgCl2亦能很好地润湿熔体表面的氧化镁,并将其包覆后转移到熔剂中去,消除了由氧化镁所产生的绝热作用,使镁在氧化过程中产生的热能较快地通过熔剂层散出,避免镁熔体表面温度急剧上升。MgCl2还能与空气中的氧气及水汽反应生成HCl、Cl2、H2等,其反应如下:
(2-11)
(2-12)
(2-13)
(2-14)
反应生成的Cl2、HCl又能迅速和镁反应生成一层MgCl2,盖住无熔体表面。这样,HCl、Cl2、H2等保护性气体及MgCl2薄层覆盖均能有效地阻止镁与氧、水的作用,防止氧化,扑灭燃烧。实验证明,即使镁熔体表面撒上一层干的MgCl2粉,即使没有形成连续的覆盖层,同样也能扑灭燃烧,而其他熔剂只能起机械隔绝作用。MgCl2良好的精炼作用在于液态MgCl2对MgO、Mg3N2的润湿性好,能有效地吸附悬浮于镁熔体中的上述夹杂。此外,MgCl2还有化学造渣作用,形成的产物MgCl2·5MgO能从熔体中沉析出来,其反应如下:
(2-15)
MgCl2还能较好地润湿坩埚壁,因而光卤石亦具有很好的覆盖性。
④溶剂中其他组分的作用 资料表明,KCl有两个作用,一个是在MgCl2中加入KCl后能显著降低MgCl2的熔点、表面张力和黏度。另一个作用是提高熔剂的稳定性,即减少高温时MgCl2蒸发损失,使MgCl2的蒸气压下降。KCl和MgCl2各占50%的熔剂蒸气压最小。KCl的存在还大大抑制MgCl2加热脱水的水解过程(部分转化为MgO及HCl),减少MgCl2在脱水操作时的损耗。
BaCl2密度大,液态(964℃)密度为3.06g/cm3,固态(20℃)为3.87g/cm3。可作为熔剂的加重剂,以增大熔剂与镁熔体间的密度差,使熔剂和熔体更易分离。BaCl2熔点为960℃,黏度较大,加到熔剂中亦能加大熔剂的黏度。
CaF2比无水光卤石密度大,其固态(20℃)密度为3.18g/cm3,液态(1380℃)密度为2.53g/cm3,而光卤石的密度仅1.58g/cm3,因而它也可加大熔剂密度。CaF2加到KCl、NaCl、CaCl2等盐中,如加入量超过共晶点,则使熔剂黏度剧增,故可作稠化剂使用。在含有足够量MgCl2的熔剂中,加入CaF2可提高熔剂的稳定性和精炼能力,因两者之间可发生反应:
(2-16)
MgF2在氯盐中溶解度很小,它的存在改变了CaF2的溶解度随温度变化而显著改变的特点。所以加入少量CaF2即可使熔剂稠化,也不会因温度波动而使熔剂性能不稳定。MgF2的存在,还可提高熔剂的精炼能力,其原因是MgF2对MgO有化合造渣能力。亦有人认为加入氟盐后,提高了MgO在熔剂中的溶解度。少量的氟离子可适当提高熔剂与镁熔体间的表面张力,改善精炼效果。因此,熔剂中一般均加入CaF2。
⑤传统熔剂的组成及缺点 国际上通用的熔剂以光卤石为基料,由MgCl2、KCl及NaCl组成低熔点共晶混合物,再添加高熔点CaP2(萤石)作为填料,使被覆盖的熔体得到进一步净化。这类覆盖剂皆为带有腐蚀性的氯化物,在与潮湿的空气接触时产生盐酸性气体,在小批量、单件的砂型铸造中尚可使用,但是对于自动化程度较高的压铸作业而言,并不合适,容易对周边环境造成污染,侵蚀设备。周岩等对自制的两种用于熔炼变形稀土镁合金的专用熔剂,采用差热分析和扫描电子观察及能谱分析方法研究了其对熔炼的镁合金显微组织的影响,并对比两种覆盖剂在熔炼的不同阶段所起的作用。其中,1号覆盖剂在低温熔炼阶段具有较好的保护熔体的效果,但高温下其黏度大幅下降而降低保护效果;2号熔剂因含较多的CaF2和MgF2,可加大熔剂密度和稳定性,不但有良好的保护熔体的作用,同时还可提高熔剂的造渣能力而起到更好的精炼效果。企业一般使用的熔剂为RJ-2号熔剂,虽然RJ-2号熔剂同时具有覆盖和精炼作用,但RJ-2号熔剂精炼不彻底,铸锭中多有非金属夹杂物,也容易因熔剂腐蚀造成大量废品。除此之外,RJ-2号熔剂还容易潮解、污染金属并使铸锭易于产生显微疏松,黏度和密度小,难于从金属中分离。考虑到将覆盖剂和精炼剂分开,同时综合考虑密度和黏度等因素,在RJ-2号熔剂的基础上,对熔剂进行了改进。在覆盖剂中添加发泡剂增大浮力,而且发泡剂产生的惰性气体覆盖在合金上可增强保护作用,还使熔剂使用时产生的有毒HCl和Cl2得到稀释。增加精炼剂中的CaF2以提高精炼性能,添加少量发泡剂降低精炼剂沉降速度。使用黏度较低的洗涤熔剂,可以很容易地将工具上的黏渣和水分去掉。它的缺点是精炼不彻底,铸锭中有许多非金属夹杂物。RJ-3、RJ-4号熔剂最主要的缺点是在熔化过程中与镁合金中的其他组元反应,造成合金中钙以及一些稀土元素的大量损失。其次,RJ-2、RJ-3、RJ-4号熔剂溶解性高、污染金属并使铸锭易于产生显微疏松;黏度和密度小,难于从金属中分离出来。RJ-4号熔剂中含有AlF3和MnF2,这些材料稀缺、昂贵,不适于制造熔剂。同时其中的铝和锰能和稀土金属发生反应,造成稀土金属损失。RJ-5号可克服RJ-4号熔剂的缺点,但它的缺点与RJ-2、RJ-3号熔剂相似。RJ-6号熔剂则主要用于含锂的镁合金。另外,传统熔剂使用前要重熔脱水,加到镁液表面时立即化成水状,同时释放出呛人的气味(Cl2、HCl)。由于熔剂的密度比合金液的大,会逐渐下沉,需不断添加,故熔剂的用量大,精炼效果也不佳,铸件常因熔剂夹杂而报废。使用过程中释放出大量有害气体,污染环境,厂房严重锈蚀,操作者呼吸道职业病多。
⑥新熔剂的研究及实践
a.无公害熔剂。镁的化学活性很强,所以熔炼时必须加熔剂保护。传统的熔剂(RJ-2)覆盖不持久,精炼不彻底,特别是使用过程中放出超过国家标准的有害气体,污染环境,造成设备厂房严重锈蚀,影响工人及周围居民的身体健康。有人研制成功并已在生产上广泛使用的无公害覆盖剂具有较低的熔点(380~400℃)、适当的表面张力,在合金熔炼温度下熔化成液态,自动形成连续的覆盖层。覆盖剂中有特殊的无机添加物,此无机添加物会持续地放出惰性气体,使覆盖剂发泡。镁液表面从而受到熔剂-气体的复合保护。此覆盖剂还能在炉中长时间静置不破碎下沉,有效时间大于3h,大大减少了覆盖剂的使用量,从而减少有害气体产生。同样无公害的精炼剂JDMJ,由于配方独特,液态密度、黏度合适,具有良好的精炼效果,另同时兼有覆盖保护作用。这两种熔剂的化学成分见表2-29。组成中,BaCl2密度大,作为加重剂加入;NaCl与KCl和MgCl2形成三元系,调整密度;KCl是溶剂的基本组元,用以降低溶剂的表面张力和黏度;MgCl2是溶剂的核心组元,通常表达式为MgCl2·6H2O,有6个结晶水,加热时会失去2个结晶水。会发生水解形成HCl和MgO。在高温下形成的HCl及H2为保护性气体。MgO作为熔剂的稠化剂,它所形成的MgCl2·5MgO复合化合物具有较强的除氧化夹杂能力。
表2-29 无公害覆盖剂、精炼剂化学组成

轻熔剂覆盖也是一种可行的镁合金件生产方法。有人研制出的一种熔剂比常用的镁熔炼用覆盖剂轻,并且不含有害的钡盐,容易与镁液分离。用这种熔剂覆盖,熔炼AZ88(8%Al,8%Zn,0.2%Mn)镁-锌-铝合金,保护效果很好,生产的铸件夹杂少,纯净度高。因为AZ88密度(1.91g/cm3)比AZ91B的(1.81g/cm3)高,更容易与熔剂分离,这种生产方法适于在铝、锌合金压铸车间批量生产镁合金压铸件。
b.镁-稀土合金专用熔剂。铸造镁合金中改善耐高温性能的最有效元素是稀土,它可以增强镁合金原子间结合力,减小原子扩散速率,而且稀土和镁的化合物具有较高的热稳定性。国标中的ZM-2、ZM-3、ZM-4、ZM-6均含有稀土元素。由于稀土元素活性强,易和MgCl2反应生成稀土氯化物,所以使用普通的熔剂将使稀土的收得率大大下降,为此需用一种镁-稀土合金专用熔剂,其化学组成如表2-30所示。
表2-30 镁-稀土合金专用熔剂化学组成

c.除硅熔剂。硅是镁合金中的有害夹杂,它在镁中固溶度很小,但微小含量就能在晶界上生成与基体有较大电位差的不溶相Mg2Si,降低合金的抗蚀性。脆性相Mg2Si热处理不能溶解,从而降低了合金的塑性。电解法生产的镁锭含硅量低,但中国绝大多数采用硅还原法生产镁,故镁中含硅量较高,为此可以采用表2-31中的熔剂来除掉Mg2Si。另外,也可以采用在熔剂中添加Fe2S的方法来去除镁熔体中的硅。
表2-31 除硅熔剂的化学组成

d.除铁熔剂。铁也是镁合金中的有害夹杂,它能降低合金的耐蚀性,消除镁合金中的铁的方法通常是在镁合金中加入一定量的Mn,以形成高熔点的Mn-Fe化合物,并使其从镁液中沉淀出来。此外还可用K2ZrF6及TiCl4来去除镁中的硅和铁,其原理是K2ZrF6或TiCl4和镁反应生成微细的Zn及Ti质点,它们与硅、铁相遇生成化合物而下沉到坩埚底部。
(3)气体阻燃处理
①气体阻燃的发展 1970年之前,熔炼镁合金主要是采用熔剂进行保护,这种方法虽然能够起到良好的阻燃作用,但容易产生熔剂夹杂,导致产品力学性能和抗腐蚀性能下降,制约了镁合金的应用;而且,熔剂与镁液反应生成腐蚀性烟气,破坏设备,恶化工作环境。压铸技术中采用熔剂熔炼工艺会带来一些操作上的困难,特别是在热压室压铸中,这种困难更加严重。同时,熔剂夹杂是镁合金铸件最常见的缺陷,严重影响铸件的力学性能和耐蚀性,大大阻碍了镁合金的广泛应用。20世纪70年代初,无熔剂熔炼工艺的开发成功是镁合金应用领域中的一个重要突破,对镁合金工业的发展有着革命性的意义。20世纪后期,民用镁合金压铸工业迅速发展,这有赖于以下三项技术的进步:高纯镁合金的开发、无熔剂熔炼技术和新型压铸技术。无熔剂熔炼技术的开发与应用,特别是保护气体SF6的应用,对镁合金工业的发展有着革命意义。目前,世界上多数镁合金压铸厂和部分镁冶炼厂采用气体保护熔炼方法,保护气体有空气/SF6、空气/CO2/SF6、SF6/N2和SO2/N2/空气等混合气体,熔炼质量和工作环境均得到极大改善。然而,今天,采用SF6进行气体保护又面临新的挑战,“温室效应”使SF6的使用受到限制,探索新的保护气体或开发新的熔炼阻燃技术已经迫在眉睫。
②气体阻燃机理 镁合金在熔炼及加工过程中必须采取一定的防止熔体氧化燃烧措施。目前在工业上大量应用的氮气和氩气都可以用来作镁熔体保护,目的是断绝氧气的来源。氮气能阻止燃烧,与Mg缓慢反应,产生粉末状Mg3N2膜,其所提供的防护温度在650℃以下,氩气不会与Mg发生反应,但同样存在Mg蒸发问题。镁化学性质极其活泼,在空气中被氧化,表面生成MgO,其致密度系数为0.79,这种疏松的氧化膜不能阻止反应继续进行。当温度超过熔点(650℃)时,氧化迅速转变为燃烧,并放出大量的热,所以镁合金熔炼过程中必须采取保护措施。赵伦等详细介绍了镁合金熔体气体保护的防燃机理和优缺点,替代或减少SF6气体、减少环境污染、提高气体保护的防燃效果是目前的研究重点,含氟有机化合物有望成为未来镁合金熔体的高效无污染保护气体。
a.镁与N2及Ar、Ne等惰性气体的作用。SO2与SF6都可以作为反应性气体用于镁熔体防护,使用温度最高可达740℃。SO2的消耗量在大气下占的总体积很小,在铸造车间作为防护性气体成本最低。但缺点是,在与空气接触时反应生成H2SO4,形成气体状的SO3,对机器及周边设备起到促进腐蚀作用。所有设备附件及管道都要采用优质的钢材。SO2及SO3存在毒性及刺激性气味,对人体健康有害。SO2和SF6一样,在很低的浓度下,也有良好的防护效果,并且SF6无毒,SF6与镁熔体接触时共同构成一种MgF2的致密的防护层。实验表明,纯净的N2及Ar、Ne等气体虽然对镁熔体起到一定的阻燃作用,但均不能完全隔绝镁液与周围环境的接触,所以起不到良好的保护效果。
N2与镁发生如下反应:
(2-17)
生成的Mg3N2系粉状化合物结构疏松,不能阻止反应继续进行。
Ar、Ne等惰性气体虽然不与镁液反应,但不能防止镁的蒸发,形成一定蒸气压的镁遇到冷壁会发生反应,所以也不是理想的保护气体。
b.镁与CO2、SO2、SF6等气体的作用。实验表明,这三种气体均能起到较好的保护效果,而尤以SF6与其他气体按一定比例混合保护效果最佳。
CO2与镁在高温下发生如下反应:
(2-18)
镁液在干燥、纯净的CO2中,其氧化速率很低,这与表面膜中出现了无定形碳密切相关,这种无定形碳存在于氧化膜的空隙处,提高了镁表面膜的致密度系数,使α=1.03~1.15。带正电荷的无定形碳还能强烈地抑制镁离子透过表面膜的扩散运动,故也能抑制镁的氧化。
镁与二氧化硫发生如下反应:
(2-19)
在镁熔体表面生成很薄较致密的带有金属色泽的MgS、MgO复合表面膜,可抑制镁的氧化。
镁与含SF6的混合气体发生如下反应:
(2-20)
(2-21)
(2-22)
其中主要产物是MgO,也含有少量MgF2。MgF2的致密系数为1.6,由MgO+MgF2组成的混合膜变为连续、致密的膜,因而含SF6的气氛有防止镁合金熔体氧化燃烧的作用。
c.镁与水蒸气的作用。镁与H2O的反应方程式为:
熔融镁与液态水接触会导致猛烈爆炸,引起镁熔体的剧烈燃烧和飞溅。一般来说,含有水蒸气对气体保护效果起到负面的影响,比如采用SF6气体保护,水分的存在大大加剧了镁的氧化,还会生成有毒的HF。
d.气体保护的机理。综上所述,保护气体的阻燃机理主要是气体与镁液发生反应,在熔体表面生成不同防护作用的表面膜,这些膜致密度大,能够阻止反应继续进行,也能够阻止镁液的蒸发。其次,这些气体密度大于空气,能在一定程度上隔绝镁与氧的反应。
如上所述,纯净的N2、Ar、Ne等惰性气体虽然能对镁及其合金熔体起到一定的阻燃和保护作用,但效果并不理想。N2易与镁反应,生成Mg3N2粉状化合物,结构疏松,不能阻止反应的进行。Ar和Ne等惰性气体虽然与Mg不反应,但无法阻止镁的蒸发。大量试验研究表明,CO2、SO2、SF6等气体对镁及其合金熔体可以起到良好的保护作用,其中以SF6的效果最佳。熔体在干燥纯净的CO2中氧化速率很低。高温下CO2与镁的化学反应方程式为:
(2-23)
反应产物为无定形碳,它可以填充在氧化膜的间隙处,提高熔体表面氧化膜的致密性。此外,还能强烈地抑制镁离子透过表面膜的扩散运动,从而抑制镁的氧化。SO2与镁的化学反应方程式为:
(2-24)
反应产物在熔体表面形成一薄层较致密的MgS/MgO复合膜,可以抑制镁的氧化。20世纪70年代,在SF6的保护效果得到认可前,人们广泛采用SO2气体来抑制镁合金的氧化与燃烧。
SF6是一种人工制备的无毒气体,相对分子质量为146.1,密度是空气的4倍,发生化学反应可能产生有毒气体,在常温下极其稳定。含SF6的混合气体与镁可以发生一系列的复杂反应。
(2-25)
(2-26)
(2-27)
MgF2的致密度高,它与MgO一起可形成连续致密的氧化膜,对熔体起到良好的保护作用。应当注意的是,采用含SF6保护气氛时,一定不能含有水蒸气,否则水分的存在会大大加剧镁的氧化,还会产生有毒的HF气体。然而,气体对镁合金熔体的保护效果可能与合金系有关。有人研究了保护性气体对Mg-Ca系合金熔体氧化特性的影响,发现Ar、N2、和CO2三种气体中N2的保护效果最好。流速较小时,CO2与镁合金熔体反应生成的氧化层具有双层多孔性结构,表层富碳,内层富氧,不能抑制Mg-Ca系合金熔体的氧化与燃烧。
③SF6保护气氛 目前,人们在镁合金熔炼与生产过程中广泛采用SF6保护气氛。SF6保护气氛是一种非常有效的保护气氛,能显著降低熔炼损耗,在铸锭生产行业和压铸工业中得到普遍应用。实验研究表明,含0.01%SF6的混合气体可有效地保护熔体,但实际操作中,为了补充SF6与熔体反应及泄漏造成的损耗,SF6的浓度要高些。在配制混合气体时,一般应采用多管道、多出口分配,尽量接近液面且分配均匀,并且需要定期检查管道是否堵塞和腐蚀。采用SF6保护气氛熔炼合金时,应尽可能提高浇铸温度、熔体液面高度和给料速度的稳定性,以避免破坏液面上方SF6气体的浓度。此外,要注意保护气体与坩埚发生反应,否则反应产物(FeF3、Fe2O3)将与镁发生剧烈反应。SF6保护气氛主要有两种,一种是干燥空气与SF6的混合物,另一种是干燥空气与CO2和SF6的混合物。SF6保护气氛中SF6浓度(1.7%~2%)较低,且无毒无味,压铸温度比较低,且金属熔体密封性好,SF6浓度(通常小于0.25%)较低的空气混合物就可以对镁合金熔体提供保护。在熔剂熔炼工艺中,细小的金属颗粒会陷入坩埚底部的熔渣中而难以回收,因而熔体损耗较高。在无熔剂工艺中,由于没熔剂,坩埚底部熔渣量大大减少,从而熔体损耗相对较低。由于在镁合金熔炼温度下SF6会缓慢分解及与其他元素发生反应生成SO2、HF和SF4等有毒气体,在815℃还会产生剧毒的S2F10,但S2F10在300~350℃会分解出SF6和SF4,因此镁合金的熔炼温度一般不应超过800℃。SF6浓度低于0.4%的保护气氛便能对镁合金熔体提供有效保护,因而产生的有毒气体可以忽略。SF6价格高且存在潜在的温室效应,因而要尽量控制SF6的排放量。保护性气氛中SF6的浓度不容许超过2%,否则会引起坩埚损耗。特别是在高温下,SF6浓度超过某一特定的体积分数时,坩埚内可能发生剧烈反应甚至爆炸,因此必须对混合气体中SF6浓度进行严格控制。此外,带盖的坩埚不能采用纯SF6气氛进行保护。SF6是影响镁合金寿命周期指标(LCA)的主要因素,也是制约镁合金成为21世纪绿色材料的关键因素。2000年,国际镁协会(IMA)呼吁镁界人士重视开发保护性气体以代替SF6。
④SF6气体的基本性质 尽管“温室效应”使SF6的使用受到了限制,但在找到合适的保护气体之前,国内外在熔炼镁合金中使用最多的还是SF6混合气体。SF6是一种无色、无味、无毒的气体,相对分子质量为146.1,比空气重4倍。从分子结构看,一个硫原子被六个氟原子紧紧包围,具有化学惰性结构,在常温下极稳定,通常将SF6气体加高压后变成液态,储存于专用的耐高压钢瓶中备用。SF6气体无毒,但密度大,如果在空气中累积,有可能引起缺氧,产生窒息,所以车间必须注意通风。在高温下,SF6会缓慢分解,生成多种有毒的氟化物如S2F10、SF4。它们进一步水解后生成氟化氢、氟化磺酰和氟化亚硫酰。这些反应生成物非常活泼而且具有腐蚀性。所以保护气体使用的SF6必须纯净。正常情况下,这些生成物体积分数很低,对人体基本没有危害。SF6虽然不是毒性气体,但是如果提炼不纯,混进去的低氟化硫如SF4却是剧毒物质,能致人死亡。
在镁合金的熔炼温度下,SF6会发生缓慢分解或与其他元素反应,形成SO2、HF、SF4等有毒气体。据报道,在815℃时会产生有毒的S2F10,但S2F10在300~350℃会分解为SF6和SF4。熔化镁合金的温度不会超过800℃,足以保护镁合金熔液的SF6体积分数在0.4%以下,保护时混合气体的流量又极小,所产生的有毒气体可忽略不计或不存在。在实际生产应用中没有任何危险,可以认为是一种无毒、无腐蚀的保护方法。
⑤SF6的防护作用 SF6连同空气一起作用于合金液表面,会形成一种和合金液暴露于空气中所形成的氧化镁完全不一样的改性氧化镁薄膜,其间混入了少量的致密度大的MgF2,这一层薄膜是有金属色泽、致密、连续的,以此来阻止镁合金液的进一步氧化而获得保护能力,但它只能维持几分钟,故混合气体要不间断地供应。对镁合金的保护主要是通过形成厚层保护膜来实现的。
通过对表面膜分析,大多数物质为MgO,也有少量的MgF2,MgF2是最稳定的一种化合物。氧化膜的形成过程可描述为:首先在镁合金液表面,镁与氧反应生成MgO,镁进一步与SF6反应生成MgF2,然后MgF2与MgO结合形成致密的膜层,从而达到有效保护的目的。
当镁合金熔液温度较高,或搅动频繁,或先前已受到覆盖剂污染时,在空气/SF6混合气体中,再混入干燥的CO2气体,用以改善和加强SF6的保护效果。
气体的保护作用还受组元气体干燥程度影响,水分的存在会极大地削弱混合气体的保护作用。压缩空气和CO2必须经干燥处理,至少经冷冻式气体干燥器处理过。
⑥SF6混合气体的浓度与流量 为了得到SF6混合气体保护镁合金熔液的满意效果,关键是SF6的浓度与混合气体的流量,φ(SF6)过高或混合气体流量过大,不仅会造成浪费,而且有严重副作用。所以在调整浓度与流量时,必须做到有效、安全、节约。
在用SF6混合气体保护镁合金熔液时,空气是一种必不可少的组元,空气中有氧存在才使这一抗氧化剂起作用,如果剔除空气,只用SF6一种气体则不能保护镁合金熔液。因为MgO膜中只要混入少量的MgF2后就能成为有效的保护膜,所以SF6这一组元是极微量的,体积分数仅在0.1%~0.4%范围内,当体积分数小于0.05%或大于0.7%时氧化会加重。
混合气体的消耗量取决于熔液的表面积、熔液温度、罩壳密封有效性、密封罩容积的大小、加料和舀料的频率以及熔液的搅动程度。究竟需要多大容量,根据实践可以这样估算:每分钟流量是密封容积的5%。在使用时按实际工况再作调整,如按估算的流量通入密封罩后,熔液表面出现火苗,说明流量不够,这时应试着缓慢地加大流量,直到火苗熄灭;若按估算的流量通入密封罩后未见火苗,则试着缓慢地减少流量,当微微出现火苗时,再适当地增加一些流量,直到火苗熄灭。
⑦采用SF6气体保护须注意的问题
a.操作实践。操作人员应认识到气体保护在每个工序的重要性,这些工序包括加料、熔化、处理、出料、合金化、晶粒细化等辅助工序。需要注意,稍不留心忘记关闭窗口就会使供应的SF6大量流失。浇铸温度、液面高度和给料速度都是影响保护气体供应的重要工艺参数。浇铸温度应在许可的范围内控制的尽量低,温度波动应控制的尽量小,液面高度应在保护气体出口处尽量保持恒定。初始液面形成保护层需要的保护气体比维持保护层需要的保护气体量要小,为保持平衡,液面的破坏要尽量小,特别是在搅拌、出料等操作时要尤其注意。
b.保护气体与设备的反应。保护气体可能与设备发生反应,如SF6与坩埚反应形成多孔状FeF3和FeO3。SF6体积分数过高会使坩埚起皮增加,起皮会与镁液进一步发生剧烈反应;此外,反应还可能生成SO2和SO2F2,它们会与水蒸气发生反应,然后被起皮吸收,进一步腐蚀坩埚。温度升高和体积分数增加会使腐蚀加剧,因而应避免纯净的SF6气体通入坩埚。
c.环境保护问题。SF6具有很强的吸收长波能力,并在空气中滞留时间长,有人估计有3200年,其温室效应为CO2的23000多倍。虽然目前对温室效应贡献不大,但其潜在的影响很大。
d.节能措施。在开发出新的保护气体之前,估计SF6的应用还会进一步扩大。为减少SF6的消耗,改进熔炉设计是重要的措施。设计熔化炉时,要使镁液表面积与体积比最小,坩埚和盖子之间要很好的配合与密封,并且设计工艺时尽量减少开盖的次数。在设计炉盖时应充分考虑几何因素,如果熔体上方空间太大,则发送保护气体时产生对流,且保护气体高温区域过大,与熔体反应产生的副产品较多,会影响熔体质量;为防止炉盖变形,需采用10mm以上的低碳钢,也可以使用加强筋。耐火纤维垫圈可以在炉盖、炉体、坩埚之间实现很好的密封,要特别小心防止其机械破坏或被镁液损坏。
e.气体混合装置。混合装置由压缩空气经球阀、滤油减压器、储气罐、精滤器、聚油过滤器、调节减压阀等组成。调节减压阀的压力就可以使减压阀的出口压力,即压缩空气、CO2、SF6的压力同时增加或减少,从而使各自的流量亦同时增加或减少,其目的是维持三种气体原来设定的比例近似不变。为此要求减压阀的出口压力为同一数值并与控制压力相等。用空气压力来控制三种气体的压力与流量,必须保证正常的空气压力。李新雷等研制了一种镁合金铸造专用混合保护气体系统。该系统可实现压缩空气、SF6以及CO2三种气体按比例混合,并提供常压熔炼、低压过程保护、泄漏保护三路供气支路。实际应用表明,该混气系统可实现对镁合金低压铸造全过程的有效阻燃保护。
⑧减少SF6用量或代替SF6的方法 未来的环保法规将限制或禁止使用SF6。如何有效利用SF6,减少其消耗和逸散,能否代替SF6,是当前镁熔炼技术研究的热点之一。用氩或氦气代替SF6混合气的简单方法是不可行的,因为镁液蒸气压较高,当镁液表面无保护膜时,大量蒸发的镁以很细小的粉末态沉积于坩埚盖内封闭的空间中温度较低的表面,一旦因加料或操作需要,开启这一封闭空间,冷空气进入,会立即引燃这些粉末,产生燃烧或爆炸。代替SF6的可行方法是用0.5%~0.8%(体积分数)的SO2与空气混合,可以使镁液表面的氧化速度降低到可允许的范围。在SO2气体中,镁液的表面氧化膜比在SF6中厚,且弹性较差。SO2本身有刺激性气味,对环境有害,并且对设备腐蚀较重。因此,用SO2代替SF6不是很好的解决办法。国际镁协会提出在当前情况下可以采取以下4项措施来减少SF6的消耗:改进镁坩埚炉盖的密封性,减少SF6的泄漏;研究自动加料、吸取镁液装置;优化保护气体的供气系统,使气体在镁液表面分布更合理,更有效:优化混合气体的组成及SF6的含量。
美国的Air Liquide公司开发了一种回收SF6的方法。这种方法是把用后的含SF6混合气体回收,分离出SF6,再循环使用,使SF6不散失到大气中。该方法利用的是聚合物薄膜对空气中不同气体具有不同的透过能力的特性。这种聚合物膜在多年之前就已用于石油化工业,用来从混合气体中分离氢和二氧化碳,现在又用于制取低成本氮气。分离SF6比分离氮气更容易,因为SF6的分子动力学直径(4.9Å,1Å=10-10m)比N2的大30%。Air Liquide公司已研制出回收SF6的成套设备,用于半导体制造业。实践证明,用后的混合气体中含SF6体积分数通常是0.01%~0.5%,经分离后气体中SF6的含量可提高到0.5%~5%。SF6回收率达到98%。
德国的Aachen大学和Volkswagen AG公司合作开发出一套全密封的镁熔炼炉和压铸工艺设备,成功地用纯氩气代替SF6混合气体进行保护。Audi公司的铸造试验厂正试用一种三室的镁熔炼炉,用于真空压铸机,这种密闭的炉子通常可以用CO2气体保护。但在清渣和检测操作过程中还必须用SF6。适当合金化也可以使镁液表面生成保护膜,防止燃烧。镁液中加入铍,含铍质量分数达到0.012%时,镁液暴露于空气中短时间内不发生燃烧。当镁液含铍质量分数为(50~80)×10-6时,用氮气保护,可以进行正常的压铸操作。镁中加钙也有与铍类似的阻燃效果。
⑨具有创造性的防燃新技术 开发新的炉型的主要目的除了既能预热、熔化和保温外,还要具备操作安全、成本合理、对环境保护有利的诸多条件。采用分隔式的炉体,各司其职,再用真空定量吸铸,操作简便,铸件中无气孔及夹渣,组织致密,材料能达到良好的延性,铸件既可施焊,也可进行热处理,对后道高温涂层处理,表面也不会出现皮下气泡。这种新的炉型现已设计出来,投入试生产。三室熔化、保温定量浇铸炉共分为三个组成部分,各室之间都设有隔板,所划分的锭料加入室,其熔池表面积较小。中间室与取料室的周围为全密封,用惰性气体如CO2、Ar或Ar/SF6混合气体充入作为缓冲垫。在作业中各室之间的温度是有所差别的:加料室一般为630℃,最高达650℃,用纯CO2充气,在温度达到650℃以上时,要加入抑制性气体如SF6或SO2;中间室加热到浇铸温度;取料室达到均匀的熔化温度,其温度波动范围处于680~750℃之间。在中间室与取料室中都有气垫存在,加料室处于大气下,要经常性地加料以保持足够高的液面,达到常规的熔化效率。炉室上方另外装有气体导管,在进行检验及清理工作时要再通入SF6气体加以防护。中间室及取料室皆处于密封状态,无空气窜入的可能性。整个炉子坐于地坑中。取料室处布有升液管,通过真空吸铸充入到压室底部,达到平稳地层流浇铸的目的。
镁合金压铸中如果要求达到最为优化的程度,有许多条件是必须得到满足的。例如:切断铸件产生气孔的来源;不许带有潮气的原料进入熔池中;金属液在勺料入压室时平稳而无冲蚀;防止在压室中与熔体接触局部凝固;充型时无涡流;杜绝采用盐类溶剂;尽可能采用无公害的气体作为辅助性的防护气垫;不会有有害物质向空间散发;熔渣量降低到最低程度。为了达到上述诸要求,设计出了全封闭式熔化及浇铸集成系统。这种全封闭式集成系统,一方面除了通过密封式炉型连续加料外,另一方面有固定式升液管与压铸机1压室底部直接相连接,其优点甚多,如:在熔化和浇铸时,熔体全盘得到防护;有效地防止熔渣的形成,通过一排接一排连续式地加入炉料,使炉中熔池的温度始终保持均匀,熔体由下部定量浇铸,以100%的充满率层流式地输入到压室中,在压室与冲头的结合处由氩气补入防护。此外,在压室中不会出现熔体有任何氧化反应,不会出现局部凝固,不包气,冲头通过第一级压射行程即可作快速充型。新型的熔化及浇铸集成化以后,对环境保护方面也有重大的改观,不再采用SF6及SO2,强烈地降低了有害物质的排放,也减少了熔渣量。可以肯定地说,新开发的全封闭式熔化及浇铸集成系统,完全能满足镁合金生产过程的总体要求,达到工艺过程最优化的程度,也为镁合金优质铸件的生产创造有利的条件。
⑩无熔剂熔炼工艺(使用SF6、CO2作防护性气体) ZM-5(AZ91)合金无熔剂熔炼基本上与熔剂熔炼时相同。无熔剂熔炼用气体及C2Cl6的技术要求见表2-32。对熔炼工具应涂以涂料,涂料成分见表2-33。工具必须清理干净,预热至200~300℃喷涂料。配料时,二、三级回炉料用量不大于炉料总重量的40%,其中三级不得大于20%。SF6、CO2气体防护熔炼设备由两部分组成:一是由熔炉、坩埚、防护罩等组成的熔炼装置;二是防护气体配气、送气装置。熔化时,先将坩埚预热至暗红色,再装满经预热的炉料,装料顺序为合金锭、镁锭、铝锭、回炉料、中间合金和锌等(如无法一次装完,可留部分锭料或小块回炉料待合金熔化后分批加入),盖上防护罩,通入防护气体,升温熔化(第一次送入SF6气体时间可取4~6min)。当熔体升温至700~720℃时,搅拌2~5min以使成分均匀,然后清除熔渣,浇铸光谱试样,当合金成分不合格时进行调整,直至合格。升温730~750℃,并保温,用0.1%C2Cl6自沉式变质精炼剂进行处理。其配方见表2-34。精炼变质处理后除渣,并在730~750℃用流量为1~2L/min的氩气补充精炼(吹洗)2~4min(吹头应插入熔体下部),通氩气量以液面有平缓的沸腾为宜。吹氩结束后,扒除液面熔渣,升温至760~780℃,保温静置10~15min,浇铸断口试样。如不合格,可重新精炼变质(用量取下限),但一般不得超过3次。熔体调至浇铸温度进行浇铸,并应在静置结束后2h内浇完,否则,应重新检查断口,不合格时需重新进行精炼变质处理。浇铸前,从直浇口往大型铸型内通入防护性气体2~3min,中小型铸型内通防护性气体0.5~1min,并用石棉板盖上冒口。浇铸时,往浇包内或液流处连续输送防护性气体进行保护,并允许撒硫黄和硼酸混合物,其比例可取1:1,以防止浇铸过程中熔体燃烧。
表2-32 无熔剂熔炼用气体及C2Cl6的技术要求

表2-33 无熔剂熔炼工具涂料的组成

表2-34 自沉式精炼变质剂配方

(4)现有防燃技术的对比 金属熔体中带有盐类熔剂氯化物造成的污染以及盐类蒸气对周围环境造成的破坏作用,不适合现代化大量生产的压铸作业。对于改善氧化状态而言,加入Be、Ca、Zn等元素,能改变镁合金的铸造性能,对力学性能也有一定的影响,3个元素中以Be的效果最好,不影响材料的切削加工性能。当前,SF6是基本的、不可缺的防护气体,在密闭炉上加入效果好;其缺点是SF6气体产生温室效应。以SO2作防护气体,简单实用,可与SF6混合使用。惰性气体Ar、He、N2等单独使用在大气下并不能抑制Mg的蒸发,但是在全封闭功能的炉型中,还是能发挥其主导作用的。从目前的防燃技术看,各种方法均存在问题,如SF6具有温室效应,SO2使用不够安全,加入合金元素有可能改变合金的性能,溶剂操作对压铸而言有可能将溶剂带入铸型等。因此,防燃问题仍然是目前镁合金研究和实践的中心问题。
2.1.1.8 镁合金熔炼装置
(1)常规熔化设备
①反射炉 反射炉是熔炼有色金属常用的设备,其结构与铝合金所用的大同小异。反射炉的热源有固体燃料(煤和焦)、流体燃料(液体和气体)以及电热。在熔炼镁合金时多采用流体燃料。一些国家以发生炉煤气或天然气为主要燃料。熔炼镁合金用的反射炉按其用途分为熔炼炉和静置炉。反射炉的炉顶为弧形,热量由炉顶和炉墙反射到炉料,因此炉料的加热是以传导和辐射的方式由上向下传递的,同时使火焰及废气缓缓流过液面,使炉料与热流直接接触。反射炉的燃烧速度较快,适于大规模生产,但热效率较低。反射炉的炉底一般采用镁砖、镁砂来砌筑。近年来,已有用铸铁作为炉底的,而不使用含SiO2的耐火材料,因为SiO2很容易与金属及熔剂之中的MgCl2发生反应,而使炉衬受到损失,并且增加合金中杂质硅的含量。
②坩埚炉 在镁合金的熔炼中,也使用坩埚炉。在使用典型的戽出型燃料加热静态坩埚炉(镁合金熔炼用)时,采用铸勺从坩埚内舀取金属液并手工浇铸制备小型铸件。这种坩埚通过凸缘从顶部支起坩埚使坩埚底部留出空隙。这不仅有利于坩埚传热,而且为清理熔炼过程中坩埚表面形成的氧化皮提供了足够的空间。此外,炉腔底部朝出渣门倾斜。由于火苗的冲击,燃料炉坩埚壁局部会出现逐渐减薄现象,因而需要定期检查坩埚壁厚,否则可能发生熔体渗漏事故。坩埚炉的烧损比反射炉大为降低,劳动环境比反射炉好。坩埚炉按其加热方式可分为电阻坩埚炉和煤气坩埚炉。把电阻材料装于坩埚四周之炉壁上,电阻材料为丝状或带状。煤气坩埚炉的燃料主要是发生炉煤气。煤气借喷嘴喷入炉膛,喷射沿着切线的方向,以保证燃烧位置适当。否则,喷嘴直接喷射到坩埚壁上,易引起金属局部过热,甚至使坩埚烧坏。镁熔体不会像铝熔体一样与铁发生反应,因此可以用铁坩埚熔化镁合金并盛装熔体。通常采用低碳钢坩埚来熔炼镁合金和浇铸铸件,特别是在制备大型镁合金铸件时,大多采用低碳钢坩埚。用于熔炼镁的坩埚容量一般在35~350kg范围内。小型坩埚通常采用含碳量低于0.12%的低碳钢焊接件制作。镍和铜严重影响镁合金的抗蚀性,因此钢坩埚中这两种元素的含量应分别控制在0.10%以下。在镁合金的熔炼过程中,特别是采用熔剂熔炼工艺时,通常会在坩埚底部形成热导率较低的残渣。如果不定期清除这些残渣,则会导致坩埚局部过热,并且坩埚表面会生成过量的氧化皮。坩埚壁上沉积过量的氧化物也会导致坩埚局部过热。因此,记录每个坩埚熔化炉料的次数应作为一项日常安全措施。坩埚必须定期用水浸泡,除去所有的结垢,通常无熔剂熔炼方法的结垢比较少。一旦钢坩埚表面形成了氧化皮,氧化铁与镁熔体之间可能发生镁热反应,放出大量热量,产生3273K以上的高温,有可能发生爆炸。因此必须保证炉底没有氧化皮碎屑,并且在坩埚底部放置一个能盛装熔体的漏箱盘以防坩埚渗漏。特别是在某些难以确定是否形成了氧化皮的部位,可以在钢坩埚加热面上包覆一层Ni-Cr合金来减少氧化皮形成,这样做并不会降低炉子的热效率。此外,镁合金熔体也易与一些耐火材料发生剧烈的反应,因此有必要合理选择燃烧炉衬用耐火材料。生产实践表明,高铝耐火材料和高密度“超高温”铝硅耐火砖(57%Si43%Al)的使用效果很好。设计燃料炉时,出渣门要便于开启。电阻加热型坩埚炉通常采用低熔点材料如锌薄板将出渣门封住。发生熔体泄漏时,锌虽然不能阻止镁合金熔体渗漏,但是可以抑制“烟囱”效应,“烟囱”效应往往会加速坩埚氧化。接近或高于熔点时,熔体会发生燃烧,在熔体表面撒熔剂或使用1%SF6混合气体下的无熔剂工艺可以抑制燃烧。当前,对铸造行业的环境控制日益严格,淘汰老式SO2顶戽出型燃料加热炉已成为发展趋势。熔炼炉的种类和规格很大程度上取决于铸造生产的规模。小型铸造车间分批生产多种不同合金,通常采用升出式坩埚炉。大规模生产镁合金,特别是有严格限制的铸造合金时,可以采用大型熔化装置,合金熔剂添加到一系列坩埚炉中,在坩埚炉内进行熔体处理,包含合金熔炼、稳定化和存储。通常熔体通过倾倒从一个坩埚转移到另一个坩埚,然后从最后的坩埚中直接浇铸或手工浇铸到铸型中。在熔体转移过程中,必须尽可能地避免熔体湍流,以防止氧化,否则会增加最终铸件中的氧化皮和夹杂物。直接燃烧型反射焰炉由于存在过度氧化问题,已经被淘汰了;间接加热型坩埚熔炼方法热效率较低,很少采用;与燃料炉相比,无芯感应电炉初始成本比较高,但运行成本较低,占用空间小。
③无铁芯工频感应电炉 在熔炼镁合金时,无铁芯工频感应电炉已开始使用。熔炼镁合金的感应电炉不能采用熔沟式的,因为密度大的熔剂及熔渣沉积炉底易使熔沟堵塞。感应电炉所用的坩埚可用10~25mm厚的钢板焊成,也可直接铸成壁厚为40~60mm的厚壁坩埚。由于铸造坩埚易产生缺陷,同时体积较大,故一般多采用焊接坩埚。无铁芯工频感应电炉由炉架、炉体、密封炉盖、通风系统、液压系统、冷却系统、电磁输送或低压转注系统组成。由多台感应电炉组成的坩埚群,不仅生产能力高,且由于在熔化过程中炉料和火焰不直接接触,可减少熔剂用量,改善劳动条件,提高金属质量。用这种熔炼设备,采取可靠的净化措施,并在铸造时采用密封转注,可获得质量较好的铸锭。
(2)专用熔化设备 镁合金活性强,在熔融状态下极易氧化燃烧,故对镁合金熔炼设备要求严格,并且熔炼时需要用熔剂或保护性气体严密覆盖金属液表面。镁合金的熔炼设备主要包括预热及装料设备、熔化炉及保护性气体混合装置。熔化炉又根据熔化室的数量分成单室熔炼炉、双室熔炼炉、三室熔炼炉和低压铸造炉等。另外,根据熔化炉的加热方式不同,分为电阻加热炉、感应加热炉及燃气加热炉等。相对来讲,电阻加热比较安全。有人认为电阻加热炉的废气处理系统是不需要的,而且,燃气中凝结的水蒸气不会与镁液接触。现有的最大熔化保温炉容量达到5400kg,连续熔化率达到1500kg/h。
①单室熔化炉 镁合金熔炼炉有单室、双室和三室炉。单室是加料熔化、保温和镁液出炉都在一个坩埚内完成。这种单室炉适于非流水生产的砂型铸造,或小批量压铸。双室炉是坩埚内有一隔板,把坩埚内的空间隔成两部分,隔板下部有孔,使两熔池连通,也可采用两个坩埚,用能加热的输液管使两者连通。双室炉中的一个熔池用于熔化镁锭,向另一熔池提供镁液,同时起集渣作用,另一个熔池保温,并直接向压铸机提供镁液。双室炉有利于使氧化渣集中于熔化室,使提供给压铸机的镁液纯净,温度恒定。
单室炉熔炼和保温在同一炉内进行;单室是加料熔化、保温和镁液出炉都在一个坩埚内完成。这种单室炉适于非流水生产的砂型铸造,或小批量压铸。
传统的铸造镁合金熔化都是用单个坩埚炉熔炼的。坩埚的形状有圆桶形、方箱形或茶壶形,可以用普通中碳钢焊接或铸造成形。碳钢坩埚成本低,但外表面易氧化起皮,最后损坏。镁液一旦与氧化铁接触,会发生激烈反应,甚至可能爆炸。采用铁素体不锈钢或碳钢外包镍基合金的坩埚可以防止外表面氧化,且使用寿命可比碳钢坩埚提高几倍。铁素体不锈钢不宜用来制造大容量坩埚,因为太厚的不锈钢板焊后容易发生焊接裂纹。
坩埚盖的设计对合理利用SF6和确保熔炼过程安全方便十分重要。首先盖上进气管和喷嘴的设置应当使保护气体直接、均匀地吹到镁液的整个表面,不应有气体不易到达的死角。由于镁液的高温使表面气体受热迅速上浮,SF6也被不断带离镁液表面,为克服这种倾向,供气装置应使SF6混合气保持低温和高密度,从喷嘴喷出的速度要高,当喷嘴距液面100~150mm时,气体喷出速度应达到5~10m/s。坩埚盖内的空间过大会使保护气体不易喷达镁液表面,空间内气体上下温差大,对流强烈,不利于SF6到达液面,同时也增加钢质盖内侧腐蚀消耗的SF6。在保证足够操作空间的情况下,这个空间越小越好。但降低坩埚内液面保证操作空间的方法是不可取的。坩埚盖与坩埚之间应加耐热垫密封,盖上的加料口、观察孔等开口都要适当密封。加料口的结构设计应当尽量减少加料时空气卷入和镁液的液面搅动,严格防止镁液飞溅。目前采用的加料口形式有双隔板式和圆盘式。通常加料口下部与一滑道相连,使炉料进入加料口后,沿滑道滑到炉底部,以防止镁液飞溅。炉料必须预热,至少达到150℃以上,这不但可防止炉料带入水分,发生事故,还可减少炉内镁液温度波动。目前已有同炉料预热装置相连接的自动加料装置投入使用,有效解决了加料时把空气带入炉内的问题。但市场供应的镁锭料尺寸差别较大,常使自动加料机卡料。镁坩埚炉的热源可用燃气、燃油、电阻或电感应加热。用燃气或油加热时升温速度快,但燃烧产物中的水蒸气与镁液接触会发生爆炸,必须严格隔离。感应加热需冷却水,一旦漏水,会增加发生事故的危险性。电阻加热比较安全、可靠,且设备成本低。常规的电阻加热方法功率低,速度慢,电阻元件易损坏。现在Dynarad公司开发出大电阻高功率的电阻元件,这种元件可以单个直接联入常规工业供电电压,不必几个串联在一起。多个元件并联,既使一个元件损坏,对整个炉子的加热功率影响也很小。这种并联式电阻加热炉大大提高了电阻炉的加热速度和使用的可靠性。
②双室炉 双室炉是熔炉、保温炉各自独立工作,通过能加热且温度可控制的U形管输送金属液,由于加料时引起的温度波动和炉渣只存在于熔化炉中,因此可以保证镁合金熔液的纯净。双室炉是坩埚内有一隔板,把坩埚内的空间隔成两部分,隔板下部有孔,使两熔池连通。也可采用两个坩埚:一个熔池用于熔化镁锭,向另一熔池提供镁液,同时起集渣作用;另一个熔池保温,并直接向压铸机提供镁液。双室炉系统是最佳方案,因为一个用作熔化,一个用作保温,彼此独立。双室炉有利于使氧化渣集中于熔化室,使提供给压铸机的镁液纯净,温度恒定。双室熔炼炉的熔化炉、保温炉各自独立工作,用能加热的U形输液管使两者连通,镁液在被转运到保温炉之前温度已经被补偿,U形管是从熔化炉的中部吸取金属液,因此几乎没有杂质进入到保温炉中,保证了保温炉中金属液的纯净度。这一系统的另一优点在于一台熔化炉可供应几台保温铸造炉,如热室坩埚炉,当然前提条件是它们在同一高度水平和使用同种合金。
③三室熔化炉 Audi公司的三室镁熔化炉的熔化室保持较低的温度(650℃),向压铸机提供镁液的供液室温度较高,是适合压铸的镁液温度。中间的保温室温度由熔化室一侧到供液室一侧逐渐升高。熔化室温度低有利于实现CO2气体保护。中间室是密闭的,平衡熔化室和供液室之间的压差,同时也起到第二次集渣的作用。供液室与真空压铸机相接。三室熔炼炉包括熔化炉、中间保温炉和供液炉,中间保温炉起平衡压力和二次集渣的作用,使金属液更加纯净。并且由于供液炉温度较低(约650℃),有利于实现CO2气体保护。三室炉中熔化室的温度较低,一般为650℃左右,因而有利于CO2气体保护,中间室起集杂作用,供液室提供压铸用较高温度的镁合金熔液。通常采用间接加热式坩埚炉来熔炼铸造镁合金,其结构与熔炼铝合金用坩埚炉类似。由于镁合金的理化性质不同于铝合金,因而坩埚材料和炉衬耐火材料不同,并且需要对炉子结构进行适当修改。三室由隔板分开,中间室与供液室为全封闭,充有CO2气体或氩气。镁合金料熔炼前必须预热到150℃以上,少量的合金料可放在炉盖上预热,大量的则需要用预热机预热。德国史杰克公司开发的镁锭预热加料机安装有可转动的加料盘,可放置24块镁锭。这种炉子的熔化室保持较低的温度(650℃),向压铸机提供镁液的供液室温度较高,是适合于压铸的镁液温度。中间的保温室温度由熔化室一侧到供液室一侧逐渐升高,熔化室温度低有利于实现CO2气体保护。中间室是密闭的,平衡熔化室和供液室之间的压差,同时也起到第二次集渣的作用。供液室与真空压铸机相接。
④低压铸造炉 低压铸造炉同铝合金低压铸造炉相似,只是镁合金低压铸造炉在坩埚内外均有压力。它的优点是坩埚壁没有压力差,所以不会变形,这一点很重要,在温度达到800℃时材料塑性很差,氯气可以作为坩埚内的压力气体,压缩空气作为炉内的压力气体。新的研究表明可以利用泵,因而只有泵需要耐压,而坩埚和炉壁都不需要。这是一个很大的优点,因为炉体和坩埚不必设计为“压力容器”。所有的炉子都有一个共同点,即必须满足镁合金熔化的特殊要求。耐热炉衬必须选择隔热材料,一方面炉体由内到外能很好地隔热,另一方面可防止坩埚泄漏时镁液和炉衬材料中的游离SiO2发生放热反应。多数镁合金熔炼炉采用电阻加热(加热元件以并联方式接入效果好),少数采用燃气加热,燃气加热比较经济,但燃气中的凝结水汽有和镁液发生反应的危险。
(3)铸造镁合金的熔炼炉的设计 铸造镁合金都是用坩埚炉熔炼的。坩埚的形状有圆桶形、方箱形或茶壶形,可以用普通中碳钢焊接或铸造成形。碳钢坩埚成本低,但外表面易氧化起皮。镁液一旦与氧化铁接触,会发生激烈反应,甚至可能爆炸。采用铁素体不锈钢或碳钢外包镍基合金的坩埚可以防止外表面氧化,且使用寿命可比碳钢坩埚提高几倍。铁素体不锈钢不宜用来制造大容量坩埚,因为太厚的不锈钢板焊后容易发生焊接裂纹,意大利Ditta Musto开发了坩埚壁预置测温技术,不但在坩埚侧壁,也可以在底部测温,这可以更有效地防止坩埚局部过热,延长使用寿命。
坩埚盖的设计对合理利用SF6和确保熔炼过程安全十分重要。首先进气管和喷嘴的设置应当使保护气体直接、均匀吹到镁液的整个表面,不应有气体不易到达的死角。由于镁液的高温使表面气体受热迅速上浮,SF6也被不断带离镁液表面,为克服这种倾向,供气装置应使SF6混合气保持低温和高密度,从喷嘴喷出的速度要高,当喷嘴距液面100~150mm时,气体喷出速度应达到5~10m/s。坩埚盖内的空间过大时,空间内气体上下温差大,对流强烈,不利于SF6到达液面,同时也增加了钢质盖内侧腐蚀消耗的SF6。在保证足够操作空间的情况下,空间越小越好。但降低坩埚内液面保证操作空间的方法是不可取的。
坩埚盖与坩埚之间应加耐热密封垫。盖上的加料口、观察孔等开口都要适当密封。加料口的结构设计应当尽量减少加料时空气卷入和镁液的液面搅动,严格防止镁液飞溅。目前采用的加料口形式有双隔板式和圆盘式,通常加料口下部与一滑道相连,炉料进入加料口后,沿滑道滑到炉底部,以防止镁液飞溅。炉料必须预热,至少达到150℃以上,这不但可防止炉料带入水分,发生事故,还可减少炉内镁液温度波动。目前已有同炉料预热装置相连接的自动加料装置投入使用,有效解决了加料时把空气带入炉内的问题。但市场供应的镁锭料块尺寸差别较大,常使自动加料机卡料。
镁坩埚炉的热源可用燃气、燃油、电阻或电感应加热。用燃气或油加热时升温速度高,但燃烧产物中的水蒸气与镁液接触会发生爆炸,必须严格隔离。电感应加热需冷却水,一旦漏水,会增加发生事故的危险性。电阻加热比较安全、可靠,且设备成本低。常规的电阻加热方法功率低、速度慢,电阻元件易损坏。现在Dynarad公司开发出大电阻高功率的电阻元件,这种元件可以单个直接联入常规工业供电电压,不必几个串联在一起。多个元件并联,即使一个元件损坏,对整个炉子的加热功率影响也很小。这种并联式电阻加热炉大大提高了电阻炉的加热速度和使用的可靠性。
镁合金的电导率与其氧化夹渣的多少有关,试样夹渣多,电导率低。从双室炉的两熔池分别取样,测定试样的电导率。实践表明,向压铸机供液的供液室中试样的电导率高,而且稳定;熔化室中的试样电导率低,且波动很大。这说明熔化室中镁液夹渣多,质量不稳定,供液室的镁液纯度高,质量稳定。
2.1.1.9 镁合金熔炼过程中的安全与保护
镁合金熔炼铸造过程中的安全涉及个人防护、熔炼安全和铸造安全。镁合金的熔炼是生产中的重要环节,也是镁合金生产安全的关键环节。一般应该注意以下几点。
(1)工作人员及场地 镁合金熔炼时的常规保护措施比其他熔融金属的要求更加严格,要求生产人员必须使用面罩和防水衣。对镁而言,水汽不论其来源如何,都会增大熔体发生爆炸和着火的危险,尤其是当水汽与镁熔体接触时,会产生潜在的爆炸源H2,因此必须采取以下最基本的防护措施:所有镁碎屑必须是干净的,并保持干燥,腐蚀产物应该预先清理干净;所有溶剂都必须密封保存,并保持干燥,含水量小于3%;避免镁熔体与铁锈接触;工作场地应经常保持干燥、整洁、通风良好和道路畅通;在镁的熔炼及浇铸场所应严格注意防水,安放熔炉的地坑内应保证干燥无水,熔炉附近的天窗结构应能防止雨水飘入,不准水管和蒸汽管道在其附近通过;熔炉周围地面一般用铸铁板铺成,因为当镁液落在混凝土地面上时,后者所含的水分将会引起镁液的飞溅;熔炼及浇铸镁液处的厂房应采用防火墙并与车间其他部分隔开;镁合金生产厂房中一般均应禁止烟火。
(2)防护措施及操作 熔炼场地应常备滑石粉、RJ-1和RJ-3溶剂、干石墨粉、氧化镁粉等灭火剂。如发生镁液着火时,严禁用水、二氧化碳或泡沫灭火剂灭火,这些物质会催化镁的燃烧并引起爆炸。小火源可用干砂、干燥石墨粉、干菱苦土、粉状MgO或铸镁用含防护剂的型砂来扑灭;但当火源大时,用上述物质不能扑灭火灾,砂子中的SiO2甚至会与燃烧着的镁发生放热反应,反而促使镁的燃烧,此时就只能用干燥熔剂来扑灭。因熔剂吸湿性很强,故用于灭火的备用干燥剂应装在密封的筒(或箱子)内,存放于工作地点。筒盖通常应用蜡封严,熔剂灭火筒应每三个月检查一次。在熔镁工段中防火熔剂储备总量应不少于熔炉容积的10%,每一熔炉通常都应备有1~2筒干熔剂。另外,也可采用中国研制的7150泡沫灭火剂。
(3)设备及操作安全 炉体最好为双层结构设计,当内层坩埚破裂时,镁液可流到内外层之间的夹层中,同时报警并停止加热,使熔化的镁溶液不致流到外面造成危险。要经常检查炉子有无锈蚀,如有锈蚀应及时清理,坩埚使用前必须经过煤油渗透及X射线检验,证明没有缺陷才能使用。坩埚每半年至少要吊出炉外全面检查一次,或熔化一定量镁合金,当壁厚为原来一半时,停止使用。小的孔洞及锈蚀可以清理后补焊使用,不过一定要经过检查。为了防止坩埚烧穿,镁液漏入炉膛而产生爆炸事故,坩埚在每次使用前应进行严格的检查,特别是新坩埚更应注意检查,坩埚炉的构造也应使坩埚万一烧穿时镁液能顺利地从炉膛内排出而不致燃烧。
镁压铸时熔炉镁液面随加料期少许升降,液面与坩埚壁面的交界上方受到高温镁液和SF6的作用,SF6浓度过高会使坩埚迅速腐蚀。
镁锭在投入熔炉前,一定要预热到150℃以上。熔炉旁要备一有盖的装渣箱,从熔炉里面舀出来的炉渣要放到容器内,并马上盖上密封。熔化现场一般要始终保持有一瓶混合保护气,以备突然停电或发生其他突发事件时急用。
在熔镁的整个过程中操作者应密切注意熔炼进行的情况。如果发现坩埚中镁液表面在逐渐下降,从坩埚法兰边与炉膛的间隙中冒出熔剂气化时的黄色烟雾和白色的MgO烟雾,随后就冒出火苗,此即坩埚已漏的征象。此时首先应关闭电源开关(或停止送风及停供燃料),如果坩埚漏得不严重,应立即将坩埚吊出,放入一盛有干燥MgO粉的容器内,或迅速将镁液浇入预热的锭模;如果坩埚漏得严重,则不能提出坩埚,因空气进入炉膛将使镁液燃烧更剧烈,此时应在坩埚中撒入大量干燥熔剂,让其也漏入炉膛中覆盖燃烧的液面。
坩埚使用前必须严格检查以防穿孔,其底部应备有安全装置以防渗漏。炉料和锭模必须预热,熔炼和浇铸工具使用前应在洗涤溶剂中洗涤,并预热后方可使用。炉料不得超过坩埚实际容量的90%。由于使用钢坩埚生成的铁锈积存在炉底,若坩埚泄漏,镁溶液与铁锈接触会发生剧烈的炽热反应。为了使与铁锈的反应控制到最小限度,必须定期清除炉底铁锈和定期检查坩埚泄漏情况并及时处理。
通常,坩埚的维护应注意以下几点。①坩埚的检查。用水冲洗坩埚,去除挂着的铁锈,目检龟裂孔、坑等。这些缺陷处通常是漏液的地方,使用中应经常检查。作为定期检查项目,需测定坩埚厚度,用卡钳、超声波测厚仪进行全面的测定。如果有比规定厚度薄的地方,整个坩埚就要报废。②溶液从坩埚漏出的情况。溶液从坩埚漏出时会产生剧烈的白烟,若大量漏出,接近火焰是很危险的。因此一旦发现白烟,应立刻将坩埚吊出炉外,放到安全地方或放入有溶剂的事故箱里,使溶液凝固不再漏出。在有火焰的情况下,因有爆炸危险,应立刻停止供给燃料,采用铁板围挡等紧急措施,操作人员应迅速撤离。
(4)工作氛围 由于镁粉尘易自燃和爆炸,因此在切割浇冒口及铸件打磨处应加强通风,以消除空气中的镁粉尘,打磨处还应单独隔开,防止该处有火花产生,镁粉和锯屑应定期清理,并及时妥善处理。切屑的存放处应注意干燥和良好的通风。
由于镁的熔炼浇铸场所产生的大量有毒气体,如HF、HCl、SO2、NH3、NH4Cl烟雾等,均有害人体健康,故应加强通风。
2.1.2 镁合金的浇铸工艺
2.1.2.1 浇铸类型
镁液的浇铸方法大体可分为人工浇铸及自动浇铸。Stdko Westofen综述了镁合金液的浇铸方式:手动舀取,用于浇铸质量小的铸件;取出式坩埚并将合金液体浇铸到模型中,主要用于砂型铸造机械注入;热室压铸采用加压装置(活塞)进行浇铸;泵入到填充室中,用于冷室压铸机;通过一个气泵和脚踏阀以及虹吸管,在虹吸管内,金属液面始终比管口低一点(Norsk Hydro系统);根据浇铸信号完成金属液的定量,然后通过氩气压出;活塞泵通过活塞输送需要的量并通过一个双向阀使金属液流入,特别是在浇铸流出前短暂地保持一定的液面水平;电控提升的离心泵,使金属液面始终比管口低一点(Suiko Dynarad系统),并通过浇铸信号加速使准确定量的金属液流出;螺线泵在间歇时通过关闭来定量和填充金属(Rauch系统);感应泵通过它产生的磁场进行金属液的定量和填充(DOW系统);真空吸附系统,铸模中产生真空,通过一个吸附管将金属液吸入(Vacura系统)。另外还有,在炉体或泵室内的高压使金属液升入到低压铸造模中的方式和在真空压铸中将金属液吸入到铸模中的方式。人工浇铸的特点是简便易行,缺点是不够安全。自动浇铸可借助离心泵、活塞泵、气体排代泵及虹吸装置。这些装置均不需人工操作。离心泵可快速输送大量的镁液,但铸件的质量小于0.45kg不能使用,需要另外加传输管道。活塞泵的缺点是活塞易于卡住,但不受零件重量的限制。气体排代泵也与离心泵一样,受到零件重量的限制,但优点是在镁液中无运动的部件。虹吸装置的优点也是在镁液中无运动的部件,缺点是受到零件重量的限制,需要加热传输管道,另外镁液阀易漏。目前在重力铸造中还多采取人工浇铸方式,而在压力铸造中,采用自动浇铸。
2.1.2.2 用浇包舀取金属液的浇铸工艺
表2-35为用浇包舀取金属液的浇铸工艺。注意一包浇铸两个或两个以上的铸型时,在浇完第一个铸型后,浇包必须保持倾斜状态,不应回复至浇铸前的垂直位置。坩埚内的合金液最后剩余量应不少于坩埚容量的15%~20%(含锆合金)或10%~15%(含铝合金)。表2-36为有挡板坩埚的浇铸工艺。
表2-35 用浇包舀取金属液的浇铸工艺

表2-36 有挡板坩埚的浇铸工艺

2.1.2.3 人工浇铸
在浇铸过程中应该注意舀取合金液之前要将茶壶式浇包在洗涤熔剂中洗净,撇去合金液表面的熔剂,不要往坩埚中撒硫黄粉;茶壶式浇包的茶壶嘴不允许浸入到合金液以下;浇铸温度控制在670~700℃,锭模温度控制在150~250℃;开始浇铸速度较慢,以免产生冲击而产生大量氧化皮,整个充型过程要求平稳;浇完后刮净合金锭表面产生的氧化皮,避免氧化皮堆积;为了防止燃烧,可以在合金锭表面撒少许硫黄与硼酸的混合物(1:1混合);一般浇铸10模后要洗涤浇包一次,如浇包壁上黏附有较多的氧化物或熔剂渣时则应立即洗涤浇包。
浇铸工序直接影响镁合金铸件的质量,在通常的浇铸条件下,镁铸件中的氧化夹杂及熔剂夹杂都来自浇铸过程。因浇铸时镁熔体与大气的接触机会大大增加,很易氧化而生成新的氧化夹杂。为此,浇铸时应在保证充填铸型的条件下,尽可能采用较低的浇铸温度(一般为720~780℃),以降低熔体的氧化速度。浇铸中应尽量减少熔体外露的机会。当暴露于空气中时,应迅速在其周围建立起防护性气氛(如撒硫黄、硼酸混合物充当防护性气体)。浇铸时浇包嘴尽可能接近浇杯,熔体流动力求平稳,防止涡流及飞溅,浇铸不可断流,浇口杯始终保持有2/3以上熔体。浇铸工具每次进入熔体前,应先在熔剂中充分洗涤或预热,喷以防护性涂料。另外,浇熔时熔剂也很容易随熔体混入铸型中而形成熔剂夹杂。因此,在固定式坩埚熔炼时,必须用茶壶式浇包浇铸,浇包应先在熔剂中洗涤,力求抖尽所黏附的熔剂,舀取镁熔体时,应先用浇包推开熔体表面的熔剂层,平稳地以宽口舀取镁熔体,切勿使熔剂进入浇包中。浇铸前,应先从浇嘴倒出少量带有熔剂的熔体,浇包和坩埚底部的剩余熔体不允许浇入铸型(前者约占浇包容量的10%,后者应占坩埚容量15%左右)。可提出式坩埚熔炼时,应选择合适的熔剂,并过热至850℃,或添加CaF2、MgF2等稠化剂,以使熔体表面稠化、结壳,避免熔剂夹杂在浇铸时混入铸型中。
2.1.2.4 自动浇铸系统
大量生产必须设计自动浇铸装置,因为人工浇铸易因失误导致镁液燃烧。由于镁液极易燃烧,如何把质量和温度适宜的镁液浇入冷室压铸机的压室或砂型铸造的浇口杯是一个难题。浇包手工浇铸法可用于少量件和小件,同时要采取措施,防止镁液过度氧化。目前由熔炉的供液室向压铸机压室提供镁液的方法主要是通过加热的管道,用泵或虹吸管定量输送。可采用的泵有惰性气体排代泵、活塞泵、螺杆泵、离心泵、电磁泵等。几种镁液传输方法的优点和不足列于表2-37。
表2-37 不同镁液浇铸方法的优缺点

2.1.2.5 镁液的计量和浇铸
有关镁供液泵、供液辅助装置和供液控制系统已有许多研究和专有技术。加拿大的Norsk Hydro公司改进设计的气体排代泵克服了以往的泵在两次注射之间供液管中镁液排空,导致管内镁发生氧化问题和注射时间滞后的问题,增加了生产效率和使用的可靠性,可以连续使用几个月,不需从炉中提出检修。美国的W.E.Mercer等人发明的镁压铸自动浇铸装置和控制系统,采用的是电磁泵,多点温度和液位监测,PLC控制系统,可以精确地为压铸机提供恒温镁液。美国某公司制造的新型镁液计量泵不需要在镁液中设置阀门,从而解决了镁液阀易损坏的问题。这种供液装置能使镁液始终保持在供液管出口处,可随时向压铸机压室注射。设备的特点是:能高精度自动加液,加液精度为2%;生产率高;能实现高流动性注射,注射室的镁充型率为30%~50%,热压射室的温度为450~500℃,模温度为220~280℃;具有高的充模率,压射室的长径比不大于2,浇口速度为50~100m/s;具有高的精密稳定性。
2.1.2.6 熔炼浇铸安全技术
熔融状态的镁在空气中剧烈氧化和燃烧。因此,镁合金的熔炼一般采用熔剂覆盖工艺,并严格遵守操作规程。熔炼工作场地应保持干燥、整洁、通风良好、道路畅通。地面用铸铁板铺成,不准使用混凝土地面,因为镁液落到混凝土地面上时,与混凝土内所含水分相互作用可能引起爆炸。熔炉底部应备有坩埚渗漏时应用的安全装置,坩埚装料不得超过其容量的90%,以免操作时溢出。熔炼镁合金所用熔剂都是吸水性的,所以熔炼工具大都黏附有上次操作时残留的潮湿熔剂,因此,工具、热电偶等在浸入合金液进行操作之前,必须预热干燥并在熔剂洗涤坩埚中洗涤干净并加热至亮红色。炉料、光谱试样模、断口模及锭模等在使用前也必须预热,保证干燥作业。
如果通过使用潮湿工具将水分带入熔融金属中,或合金液浇入未预热烘干的锭模中,因镁的密度小,较其他熔融金属更易外溅,熔融的镁与水反应产生氢,氢又重新和空气中的氧化合,会增加爆炸的猛烈程度。爆炸飞溅成小滴的镁液能着火、燃烧并放出高的热量。为防止坩埚穿孔,每次使用前应严格检查。熔炼过程中,炉内冒出熔剂气化的黄色烟雾或白色氧化镁烟雾是坩埚已漏的迹象。如坩埚穿漏不甚严重,对于固定式坩埚,应该用手提式浇包迅速将合金液舀出浇入锭模;对于带挡板的坩埚,则立即将坩埚从炉内吊出,将合金浇入锭模。如穿漏严重,则不应取出坩埚,在可能的情况下用浇包舀出合金液,浇铸成锭。炉中或坩埚中剩余的金属液用熔剂覆盖。由于这些原因,存在引起严重的爆炸危险。
在任何情况下严禁用水灭火。一般的泡沫、干粉或二氧化碳等类型灭火剂也扑不灭镁的燃烧,使用这些灭火剂只能加速镁的燃烧并引起爆炸。因此,只能使用表2-38所列专用灭火剂灭火。必须注意,燃烧着的镁能使二氧化硫分解,使二氧化碳还原而继续燃烧并放出大量热。严禁用砂子来扑灭镁液和熔化坩埚中燃烧的镁。同样,禁止用砂来扑灭坩埚烧穿时流入炉膛内的镁的燃烧。因为火源相当大时,二氧化碳会与燃烧的镁反应,放出大量的热并促使镁燃烧加剧。此外,镁合金熔炼时会逸出大量有害气体,因此熔炼工作场地必须有良好的通风设施。
表2-38 熔炼工作场地常用的灭火剂
