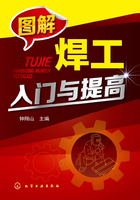
3.6 板材的焊条电弧焊操作
根据焊件接缝所处的空间位置,焊接位置分为平焊、立焊、横焊和仰焊,焊接位置可用焊缝倾角和焊缝转角的不同来区分。
处于不同焊接位置的焊缝,其焊接操作方法也有所不同。操作经验比较丰富的焊工认为,各种位置焊接操作的共同要点是:应当通过保持正确的焊条倾角和掌握好运条的三个动作,把熔池温度严格地控制在一定的正常范围内,使熔池金属的冶金反应完全,气体、杂质排除彻底并与基体金属熔合良好。虽然熔池温度不容易直接测得,但是经验证明,熔池温度与熔池的形状和大小有关。因此,焊接操作中只要仔细观察并控制熔池的形状与大小,并根据其变化情况,不断调整焊条倾角和运条动作,就能达到控制熔池温度,确保操作质量的目的。由于熔池形状与大小,对于控制焊接质量很重要,而且在操作中是可以看到的,因此控制熔池形状与大小是焊条电弧焊操作中最中心的技术要点。为此,应首先对运条的倾角及动作加以分析。
①焊条倾角。掌握好焊条的倾斜角度,可控制住铁水与熔渣,使其很好地分离,防止熔渣的超前现象和控制一定的熔深。立焊、横焊、仰焊时,还有防止铁水下坠的作用。
②横摆动作。横摆动作能保证两侧坡口根部与每个焊波之间相互很好熔合,获得适量的焊缝熔深与熔宽。
③稳弧动作(横摆时电弧在某处稍加停留之意)。稳弧动作能保证坡口根部很好熔合,增加熔合面积。
④直线动作。直线动作能保证焊缝直线敷焊,并通过变化直线速度控制每道焊缝的横截面积。
⑤焊条送进动作。焊条送进动作主要是控制弧长,其作用与焊条倾角相似。
以上动作是相互密切配合的。横摆速度和直线速度在一定焊条倾角条件下,两者间的变化直接影响熔池形状与大小。在两个速度相同或以不同速度配合时,可以使熔池成半圆形、横向半椭圆形或纵向椭圆形。熔池大小的控制,必须在很好地熔合与保持开始形状的情况下,使这两种速度等速增减来加以控制。
以下分别介绍各种焊接位置的操作要点。
3.6.1 平焊
焊缝处在水平位置时的焊接操作,称为平焊。根据焊接接头形式的不同,平焊又有对接平焊、角接平焊和搭接平焊。
(1)对接平焊
对接平焊一般分为不开坡口和开坡口的对接平焊两种,当板厚小于6mm时,不开坡口;当焊件厚度等于或大于6mm时,应开坡口。
不开坡口的对接平焊如图3-39所示。焊接正面焊缝时宜用直径为3~4mm的焊条短弧焊接,使熔深达到焊件厚度的2/3左右,焊缝宽度为5~8mm,加强高小于1.5mm。反面焊缝用直径为3mm的焊条,可用稍大的电流焊接。对于重要的焊缝,在焊反面焊缝前,必须铲除焊根。在不开坡口的对接平焊时焊条的角度如图3-40所示。

图3-39 不开坡口的对接平焊

图3-40 不开坡口对接平焊焊条角度
不开坡口的对接平焊时,采用直线运条法,采用双面焊时,背面焊缝也采用直线运条法,焊接电流应比焊接正面焊缝时稍大些,运条速度要快。当焊接与水平面倾斜的焊缝时,应采用上坡焊,防止熔渣向熔池前方流动,避免焊缝产生夹渣缺陷。
开坡口的对接平焊,坡口有V形和X形,采用多层焊法和多层多道焊法,如图3-41和图3-42所示。

图3-41 多层焊
1—第一层焊道;2—第二层焊道;3—第三层焊道;4—第四层焊道;5—第五层焊道;6—第六层焊道

图3-42 多层多道焊
多层焊时,第一层打底焊道应采用小直径焊条,运条方法应根据间隙的大小而定。间隙小时可用直线运条法,间隙大时应用直线往复式运条法,以防烧穿。第二层焊道,可用直径较大的焊条,采用直线形或小锯齿形运条法,进行短弧焊。以后各层均可用锯齿形运条法,而且摆动范围要逐渐加宽,摆动到坡口两边时,应稍作停留,防止出现熔合不良、夹渣等缺陷。多层焊时,应注意每层焊缝不能过厚,否则会使焊渣流向熔池前面造成焊接困难。各层之间的焊接方向应相反,其接头也应相互错开,每焊完一层焊缝,要把表面焊渣和飞溅等物清除干净后才能焊下一层,以保证焊缝质量和减小变形。
多层多道焊的焊接方法与多层焊相似,但应选好焊道数和焊道顺序,焊接时,采用直线运条法。
不论采用何种形式的对接平焊,正确地选用好焊接工艺参数是保证焊接质量的关键,表3-29给出了对接平焊推荐使用的工艺参数。
表3-29 推荐对接平焊的工艺参数

(2)角接平焊
角接平焊形成角焊缝,如图3-43所示。角焊缝按焊脚尺寸(在角焊缝中画出的最大等腰三角形直角边的长度)的大小采用单层焊、多层焊和多层多道焊。当焊脚尺寸小于6mm时的角焊缝采用单层焊,采用直径为4mm的焊条;焊脚尺寸为6~8mm时,用多层焊,采用直径为4~5mm的焊条;焊脚尺寸大于8mm时采用多层多道焊。焊条直径的选择,一般焊脚尺寸小于14mm,采用直径4mm的焊条;焊脚尺寸大于14mm,采用直径5mm的焊条,便于操作并提高生产率。

图3-43 角焊缝
对角接平焊多层多道焊,在焊接第一道焊缝时,应用较大的焊接电流,以得到较大的熔深;焊第二道焊缝时,由于焊件温度升高,应用较小的电流和较快的焊接速度,以防止垂直板产生咬边现象。
角接平焊焊条的角度随每一道焊缝的位置不同而有所不同,如图3-44所示。角接平焊的运条手法,第一层(打底焊)一般不做横向摆动,可以采用圆圈形、三角形、锯齿形和直线运条法。

图3-44 焊条角度随每道焊缝位置而改变
在进行角接平焊的实际生产中,如焊件能翻动,应尽可能把焊件放在船形位置进行焊接,如图3-45所示。船形位置焊接可避免产生咬边等缺陷,焊缝美观平整,有利于使用大直径焊条和用大的焊接电流,提高生产率。运条手法可用月牙形或锯齿形。

图3-45 船形位置焊接
表3-30给出了T形接头横角焊推荐使用的工艺参数。
表3-30 推荐T形接头横角焊的工艺参数

(3)搭接平焊
搭接平焊形成的焊缝为一种填角焊缝。焊接时焊条与下板表面间的角度应随下板的厚度增加而增大,如图3-46所示。焊条与焊接方向间的角度以75°~85°为宜。当焊脚尺寸为6mm时,用直径为4~5mm的焊条,按斜圆圈形运条法进行单层焊。当焊脚尺寸为6~8mm时,采用多层焊,焊第一层用直径为4~5mm的焊条,以直线形运条为宜;第二层用直径为5mm的焊条,运条方法为斜圆圈形。当焊脚尺寸大于8mm时,采用多层多道焊。搭接平焊除以上说明外,其他方面与一般角焊缝焊接相同。开始焊接时电流可大些,当焊件温度升高后,电流可小些,以防板边缘熔化过多而咬边,确保焊缝成形良好。

图3-46 搭接平焊的焊条角度
(4)焊接操作注意事项
①焊接过程中应始终注意保持焊条角度的正确。
②斜圆圈形运条时应注意:开始1/4圈要慢,焊条作微微往复的前移动作,以防止熔渣超前;再1/4圈要稍快,以防止熔化金属下淌;在半圈位置处稍作停顿,以填加适量的熔滴,避免咬边;再在3/4圈要稍慢,保持各熔池间形成1/2~2/3的重叠,以利焊成形;最后1/4圈稍快,并在终点处稍作停顿。
③焊道收尾时要填满弧坑。
④焊接过程中要注意焊脚尺寸的一致性。
⑤角焊时电弧对两焊板的加热温度不应有太大的偏差。
a.T形接头平焊。焊条的焊接方向上的倾角为65°~80°,电弧的指向应偏向厚板,以使两板加热温度相等。焊接多层多道焊时,还应根据焊道位置及板厚调整焊条角度,以保证焊缝良好成形,如图3-47所示。

图3-47 T形接头平焊
b.角焊接头平焊。根据角接接头不同坡口形式,采用不同的施焊方法,包括控制焊缝热输入,短弧焊,电弧偏向竖板一边等,以保证焊缝两侧熔化程度相同(图3-48)。

图3-48 角焊接头平焊的施焊方法
c.搭接平焊。为避免产生焊缝单边、咬边、顶角焊不透和焊缝夹渣缺陷,应根据两板的厚薄来调整焊条的角度,同时电弧要偏向厚板一边,以使两边熔透均匀。焊条倾角过大或过小都会使焊缝成形不良(图3-49)。

图3-49 搭接平焊的施焊方法
3.6.2 立焊
焊缝处在垂直位置时的焊接操作,称为立焊。立焊分为对接立焊和角立焊两种。
(1)对接立焊
对接立焊除了要控制熔化金属不下淌外,还要求焊缝保持平直。因此,常采用小直径焊条和较小的焊接电流,并采用短弧焊接法。
对于不开坡口的对接立焊,当焊接薄板时,容易产生烧穿、咬肉和变形等缺陷。对接立焊采用自下而上和自上而下两种焊接方法;后一种方法也称立向下焊。采用自下而上的方法时,如选用碱性焊条,焊条直径为2.5mm或3.2mm,焊接电流均应较平焊小。采用短弧焊接,可使熔滴过渡的距离缩短,易于操作,有利于避免烧穿,缩小受热面积,减小变形。运条手法可用直线形、月牙形或锯齿形等。在操作中,当观察到有咬肉等缺陷时,焊条可在咬肉部位稍微停一会儿,然后再抬起电弧。如发现有熔化金属下淌,焊缝成形不良的部位应立即铲去,一般可用电弧吹掉后再向上焊接。当发现有烧穿时应停止焊接,将烧穿部位焊补后,再进行焊接。
对于不开坡口的对接立焊,当立向下焊时,应采用向下焊焊条。当采用酸性焊条时,也必须用小直径焊条,并注意焊条的角度,一般采用长电弧焊接法。在操作中应注意观察焊缝的中心线、焊接熔池和焊条的起落位置。由于酸性焊条为长渣;所以要求焊条摆动的速度快而且准确。焊条的摆动方法,是以焊缝中心线为准的,应从左右两侧往中间作半圆形摆动。
对于开坡口的对接立焊,坡口形式有V形或U形等,一般采用多层焊,层数的多少根据焊件的厚度而定。在焊接时,一定要注意每层焊缝的成形,如图3-50(a)所示。如果焊缝不平,中间高两侧低,甚至形成尖角,如图3-50(b),则不仅给清渣带来困难,而且因成形不良造成夹渣、未焊透等缺陷。

图3-50 开坡口对接立焊的焊缝成形
开坡口的对接立焊可分为以下三个环节。
①封底焊 封底焊即正面的第一道焊缝。封底焊时应选用直径较小的焊条和较小的焊接电流。对厚板可采用小三角形运条法,对中厚度板或较薄板,可采用小月牙形或跳弧运条法。封底焊时一定要保证焊缝质量,特别要注意避免产生气孔。如果在第一层焊缝产生了气孔,就会形成自下而上的柱贯穿气孔。在焊接厚板时,封底焊宜采用逐步退焊法,每段长度不宜过长,应按每根焊条可能焊接的长度来计算。
②中间层焊缝焊接 中间层焊缝的焊接主要是填满焊缝。为提高生产效率,可采用月牙形运条,焊接时应避免产生未熔合、夹渣等缺陷。接近表面的一层焊缝的焊接非常重要,一方面要将以前各层焊缝凸凹不平处加以平整,为焊接表层焊缝打下基础;另一方面,这层焊缝一般比板面低1mm左右,而且焊缝中间应有些凹,以保证表层焊缝成形美观。
③表层焊缝焊接 即多层焊的最外层焊缝,应满足焊缝外观尺寸的要求。运条手法可按要求的焊缝的余高加以选择。如果余高要求较高时,焊条可作月牙形摆动;如果对余高要求稍平整时,焊条可作锯齿形或不等八字形摆动。在表层焊缝焊接时应注意运条的速度必须均匀一致。当焊条在焊缝两侧时,要将电弧进一步缩短,并稍微停留,这样有利于熔滴的过渡和减少电弧的辐射面积,以防止产生咬肉等缺陷。
不等八字形运条法,如图3-51所示。当表层焊缝较宽时,若采用月牙形或锯齿形手法,一次摆动往往达不到焊缝边缘良好的熔合,采用八字形运条法能得到较宽的焊波,焊缝表面是鱼鳞状的花纹。不等八字形运条法焊接时自左向右把熔滴放置在焊缝宽度的1/3处,稍微停顿一下,接着把焊条抬高并引到焊缝的2/3处,再向焊缝右边瞬间划弧以后,将焊条降落到焊缝的2/3处,瞬间变成短弧,停顿一下,使熔化金属与前面的焊波熔合好,然后把焊条抬高向左引到焊缝宽度的1/3处……,这种有规律的运条方法要求焊条有节奏地均匀摆动,摆动时要求快而稳,熔滴下落的位置要准确。

图3-51 不等八字形运条法
表3-31给出了对接接头立焊推荐使用的工艺参数。
表3-31 推荐对接接头立焊的工艺参数

(2)角立焊
角立焊操作时应注意以下问题。
①焊条的位置 为了使两块钢板均匀受热,保证熔深和提高工效,在角立焊时应注意焊条的位置和倾斜角度。当被焊的两块钢板厚度相等时,焊条与两块钢板之间的夹角应左右相等,焊条与焊缝中心线的夹角,应根据板厚的不同来改变其大小,一般应保持60°~80°。
②熔化金属的控制 角立焊操作的关键是如何控制熔化金属,要求焊接时精力集中,注意观察金属的冷却情况,焊条要根据熔化金属的冷却情况有节奏地摆动。在角立焊的过程中,当引弧后焊出第一个焊波时,电弧应较快地提高;当看到熔池瞬间冷却成一个暗红点时,电弧又降到弧坑处,并使熔滴凝固在前面已形成的焊波2/3处,然后电弧再抬高。如果前一熔滴未冷却到一定的程度,就过急地下降焊条,就会造成熔化金属下淌;而当焊条下降动作过慢时,又会造成熔滴之间熔合不良。如果焊条放置的位置不对,就会使焊波脱节,影响焊缝的美观和焊接质量。
③焊条的摆动 应根据板厚的不同和对焊脚尺寸的要求,选择适当的运条手法。对焊脚尺寸较小的焊缝,可采用直线往复形运条手法;对焊脚尺寸要求较大的焊缝,可采用月牙形、三角形、锯齿形等运条手法,如图3-52所示。为避免出现咬肉等缺陷,除选用合适的焊接电流外,焊条在焊缝两侧应稍停片刻,使熔化金属能填满焊缝两侧的边缘部分。焊条的摆动宽度应不大于所要求的焊脚尺寸,例如要求焊出10mm宽的焊缝时,焊条的摆动范围应在8mm以内,否则焊缝两侧就不整齐。

图3-52 角立焊焊条的摆动
④局部间隙过大的焊接方法 对角立焊缝当不要求焊透或遇到局部间隙超过焊条直径时,可预先采用立向下焊的方法,使熔化金属把过大的间隙填满后,再进行正常焊接。这样做不仅可以提高工效,而且还大大减少金属的飞溅和电弧偏吹。对间隙过大的薄板焊接,采用这种方法还有减小变形的效果。
表3-32给出了T形接头立焊推荐使用的工艺参数。
表3-32 推荐T形接头立焊的工艺参数

(3)焊接操作注意事项
立焊是焊接垂直平面上垂直方向的焊缝。由于在重力的作用下,焊条熔化所形成的焊滴和熔池中熔化的金属要下淌,使焊缝成形困难,不如平焊美观,相对于平焊来说,立焊的操作更有一定难度。立焊时应注意以下问题。
①焊条直径和电流强度应比平焊小 立焊时选的电流强度可比平焊小10%~15%,以避免过多的熔化金属下淌;其次,应采用短弧焊接法,以避免电弧过长所造成的熔滴下滴及严重飞溅。
②焊条的运动 在立焊过程中眼睛和手要协调配合,采用长短电弧交替起落焊接法。当电弧向上抬高时,电弧自然拉长些,但不应超过6mm;电弧自然下降在接近冷却的熔池边缘时,瞬间恢复短弧。电弧纵向移动的速度应根据电流大小及熔池冷却情况而定,其上下移动的间距一般不超过12mm,如图3-53所示。焊条与焊缝中心线夹角应保持在60°~80°,并保持焊条左右方向的夹角相等。焊条的运条手法要根据焊缝的熔宽来决定。

图3-53 立焊时焊条的运动
③焊工的操作姿势 立焊的操作姿势根据焊缝与焊工距离的不同,一般采用胳膊有依托和无依托两种姿势。如图3-54所示,有依托即胳膊大臂轻轻地贴在上体的肋部或大腿、膝盖部位,随着焊条的熔化和缩短,胳膊自然地前伸,起到调节作用。用有依托的焊接姿势,比较牢靠、省力。无依托即把胳膊半伸开或全伸开,悬空操作,需要通过胳膊的伸缩来调节焊条的位置。胳膊活动范围大,操作难度也较大。

图3-54 立焊时焊工的操作姿势
④握焊钳的方式 正握式如图3-55(a)、(b)所示,反握式如图3-55(c)所示。图3-55(a)为一般立焊时常用的握焊钳方式。当遇到较低的焊接部位和不好施焊的位置时,常用图3-55(b)的握焊钳方式,也可以采用图3-55(c)的拿握方式,由焊工的操作习惯而定。

图3-55 握焊钳的方式
⑤立向焊接不宜使用较大的电流和过长的电弧 立焊时使用电流过大或焊条向前移动速度太慢,会使熔池过热,铁水不能很快凝固,将导致焊缝咬边或产生焊瘤;但电弧过长、电流大,熔池温度过低也会产生夹渣和未焊透缺陷。因此立向焊接应采用适当的运条角度和适宜运条方法:使用较小电流,短弧焊接,以利焊缝成形(图3-56)。

图3-56 立焊时采用的角度
3.6.3 横焊
横焊是焊接垂直或倾斜的平面上的水平方向的焊缝。根据焊接接头形式的不同,横焊法又有对接横焊、搭接横焊等。
横焊时,由于熔化的金属受到重力作用而易下淌,造成焊缝上侧产生咬边缺陷,下侧形成泪滴焊瘤或未焊透,如图3-57所示。因此,横焊时,采用短弧焊接,并且选用较细的焊条和比平焊较小的焊接电流及适当的运条手法。

图3-57 横焊易产生的缺陷
(1)对接横焊
对接横焊根据是否开坡口,可分为开坡口对接横焊及不开坡口对接横焊两种。
①不开坡口的对接横焊 不开坡口的对接横焊当板厚为3~5mm时应采用双面焊。正面焊时焊条直径宜为3.2~4mm,焊条与下板成75°~80°,如图3-58所示。当焊件较薄时,用直线往复式运条法,这样可借焊条向前移动的机会使熔池得到冷却,熔池中熔化的金属就有机会凝固,从而防止烧穿。当焊件较厚时,可采用短弧直线形或小斜圆圈形运条手法,如图3-59所示,以得到合适的熔深。在焊接时,焊接速度应稍快并均匀,避免焊条的熔化金属过多地聚集在某一点上,形成焊瘤并在焊缝上部咬边,而影响焊缝成形。反面封底焊时,应选用细焊条,焊接电流可适当加大,一般可选平焊时的焊接电流强度,用直线运条法进行焊接。

图3-58 横焊焊条的角度

图3-59 不开坡口对接横焊缝
②开坡口的对接横焊 对接横焊坡口加工如图3-60所示。一般下板不开坡口,或下板所开坡口角度小于上板,这样有利于焊缝成形。开坡口对接横焊焊缝如图3-61所示。

图3-60 横焊接头的坡口加工

图3-61 开坡口对接横焊焊缝
对于开坡口的对接横焊,常选用多层多道焊。在焊第一道焊缝时,应选用细焊条,一般直径为3.2mm,运条手法可根据接头的间隙大小来决定,当间隙大时,宜采用直线往复形运条法。第二道用直径3.2~4mm的焊条,采用斜圆圈形运条手法,如图3-62所示。在施焊过程中,应保持较短的电弧长度和均匀的焊接速度。为了有效地防止焊缝表面咬边和下面产生熔化金属下淌现象,每个斜圆圈形与焊缝中心线的斜度不得大于45°。当焊条末端运到斜圆圈上面时,电弧应更短,并稍停片刻,使较多的熔化金属过渡到焊缝上去。然后慢慢将电弧引到焊缝下边,即原先电弧停留的旁边,如图3-63所示,这样做能有效地避免各种缺陷,使焊缝成形良好。

图3-62 开坡口对接横焊斜圆圈运条法
1—焊条慢下;2—电弧压缩并稍停;3—电弧拉长并迅速向上

图3-63 厚板多层多道焊焊条的角度
1~3—焊道
当横焊板厚大于8mm时,除打底焊的焊缝,应采用多层多道焊,如图3-63所示,这样可以较好地避免由于熔化金属下淌造成的焊瘤。在多层多道焊时,要特别注意控制焊道间的重叠距离。每道叠焊,应在前面一道焊缝的1/3处开始焊接,以防止焊缝产生凹凸不平。多层多道焊时运条手法用直线形,并应始终保持短弧和适当的焊接速度,同时焊条的角度也要根据焊缝的位置来调节,如图3-63所示。焊条直径可用3.2~4mm。在施焊过程中,焊缝的排列顺序如图3-64所示。

图3-64 对接横焊缝排列顺序
1~12—焊缝
表3-33给出了对接横焊推荐使用的工艺参数。
表3-33 推荐对接横焊的工艺参数

(2)搭接横焊法
搭接焊缝横焊的操作方法较容易,要求焊条角度与水平成45°,与前进方向成75°,采用顶弧焊法,参44见图3-65。

图3-65 搭接横焊焊条角度
一般第一遍采用直线运条。运条速度不宜过快,运条时要看到一半熔池发亮,而另一半熔渣逐步随着焊条前进而覆盖焊肉,否则易造成夹渣。第二遍采用斜线形运条,电弧要短,速度稍慢,这样可使焊缝两边熔合良好,焊肉饱满。
(3)焊接操作注意事项
①尽量采用短弧焊接,由于焊接时上坡口温度高于下坡口,因此在上坡口处不做稳弧动作,迅速将电弧拉至下坡口的根部上,做微小的横拉稳弧动作。同时根据坡口间隙大小适当调整焊条角度,间隙较小时,增大焊条角度。反之,减小焊条角度。
②用小直径焊条和较小电流,防止金属流淌。
③保持适当的焊条角度和正确的运条方法。对于不开坡口的对接横焊,薄板正面焊缝选用往复直线式运条方法,较厚工件采用直线或斜环形运条方法,背面焊缝采用直线形运条,电流可适当加大些;开坡口的对接横焊,采用多层焊时,第一层采用直线形或往复直线形运条,其余各层采用斜环形运条。
④横焊时不得减弱电弧对熔滴的承托作用。横焊时,熔化金属在重力作用下发生流淌,操作不当易在上侧产生咬边,下侧因熔滴堆积而产生焊瘤或未焊透缺陷。施焊时应选择较小直径的焊条,配合恰当的焊条角度和运条方法,以短路过渡形式进行焊接。多道焊时运条的角度还应针对焊缝所在位置,适当改变焊条角度,以使电弧推力对熔滴产生承托作用,以获得高质量的焊缝(图3-66)。

图3-66 横焊时采用的角度
3.6.4 仰焊
仰焊是四种焊接位置中焊接最困难的一种。仰焊时熔化金属因重力作用容易下坠使熔滴过渡和焊缝成形困难,焊缝正面容易形成焊瘤,背面则会出现内凹缺陷,同时在施焊中还常发生熔渣超前现象,流淌的熔化金属以飞溅扩散,如果防护不当,容易造成烫伤事故,因此在运条方面要比平焊、立焊、横焊的难度大且焊接效率低。
(1)操作方法
仰焊操作时,必须注意尽可能地采用最短的弧长施焊,使熔滴金属在很短的时间内由焊条过渡到熔池中去,促使焊缝成形。焊条直径和焊接电流应比平焊时小,以减小焊接熔池的面积,使焊缝容易成形。
当焊件厚度为4mm左右时,仰焊可采用不开坡口的对接焊,焊条直径为3.2mm,焊条与焊缝两侧成90°夹角,与焊接方向保持80°~90°的夹角,如图3-67所示。在整个施焊过程中,焊条要保持在上述位置均匀地运条。

图3-67 仰焊时焊条的角度
仰焊的运条手法可采用直线形和直线往复形,直线形用于焊接间隙小的接头,直线往复形用于间隙稍大的接头。焊接电流不应过小,否则得不到足够的熔深,而且电弧也不稳定,使操作难以掌握,而且焊缝质量也难以保证。
当焊件厚度大于5mm时,对接仰焊均开坡口。对于开坡口的对接仰焊打底层焊接的运条方法,应根据坡口间隙的大小,决定选用直线形或往复直线形的运条方法。其后各层均宜用锯齿形或月牙形运条方法,如图3-68所示。在进行仰焊时,无论采用哪种运条手法,均应形成较薄的焊道。焊缝表面要平直,不允许出现凸形。

图3-68 开坡口对接仰焊时的各种运条方法
1—月牙形;2—锯齿形;3—直线形;4—直线往复形;5—第一道焊缝;6—第二道焊缝
图3-69所示为对接仰焊时多层多道焊焊缝的排列顺序。操作时,焊条的角度应根据每一道焊缝的位置作相应的调整,以利于熔滴金属的过渡,并能获得较好的焊缝成形即为正确操作。

图3-69 开坡口对接仰焊时的多层多道焊法
T形接口的填角仰焊比对接坡口仰焊较易掌握。当焊脚尺寸小于6mm时,采用单层焊,用直线形和往复直线形的运条方法;当焊脚尺寸大于6mm时,采用多层多道焊,第一层用直线形运条方法,其后各层可选用斜三角形或斜环形的运条方法。
T形接头填角仰焊的运条方法如图3-70所示。如果填角仰焊操作技术熟练,可使用较大直径的焊条和稍大的焊接电流,以提高工作效率。

图3-70 T形接头填角仰焊运条方法及焊缝排列顺序
A—用直线形运条法;B—用斜三角形或斜圆圈形运条法
表3-34给出了对接接头仰焊推荐使用的工艺参数。
表3-34 推荐对接接头仰焊的工艺参数

表3-35给出了T形接头仰焊推荐使用的工艺参数。
表3-35 推荐T形接头仰焊的工艺参数

(2)操作注意事项
①采用小直径焊条、小电流焊接,一般焊接电流在平焊与立焊之间。
②为了保证坡口两侧熔合良好和避免焊道太厚,坡口角度应略大于平焊,以保证操作方便。
③必须采用短弧焊接,以利于熔滴过渡。
④保持适当的焊条角度,焊接带坡口的仰焊缝的第一层时,焊条与坡口两侧成90°角,与焊接方向成70°~80°角。熔池尽量要薄些,当熔池的温度过高时,可以将电弧稍稍抬起,使熔池温度稍微降低。
⑤选用正确的运条方法。对于不开坡口的对接仰焊,接头间隙小时宜采用直线形运条,接头间隙大时宜采用往复直线形运条;开坡口的对接仰焊采用多层焊时,第一层焊缝根据坡口间隙大小选用直线形或直线往复形运条方法,其余各层均采用月牙形或锯齿形运条方式。多层多道焊宜采用直线形运条。对于焊脚尺寸较小的T形接头采用单层焊,选用直线形运条方法。焊脚尺寸较大时,采用多层焊或多层多道焊,第一层宜选用直线运条方法,其余各层可采用斜环形或三角形运条方法,如图3-71所示。

图3-71 不同接头的仰焊焊条角度
⑥仰焊焊接忌用长弧施焊。仰焊时,熔池倒悬在焊件下面,焊缝成形困难,容易在正面产生焊瘤,背面产生塌陷。焊接时为使熔滴金属在很短的时间内由焊条过渡到熔池中去,必须使用最短的电弧长度、较小直径的焊条、稍快的焊接速度及合适的焊接电流。多层焊接时,可采用月牙形和锯齿形运条方式焊接,为控制熔池面积,摆幅不宜太大,焊道应薄一些,以防止产生焊接缺陷(图3-72)。

图3-72 仰焊时焊条角度
3.6.5 多层多道焊
角焊缝中当焊脚尺寸大于10mm时,采用多层单道焊会因为焊脚较宽,坡度较大,熔化金属容易下淌,影响焊缝成形。在这种情况下采用多道多层焊较为适合。
(1)焊接接头的形式
用焊接方法连接的接头(简称接头)称为焊接接头。焊接接头包括(OA)、熔合一区(AB)和热影响区(BC)三部分(图3-73)。

图3-73 焊接接头
在手工电弧焊中,由于焊件的厚度、结构的形状及使用条件不同,其接头形式和坡口形式也不同。根据国家标准规定,焊接接头的基本形式为对接接头、T形接头、角接接头、搭接接头四种。有时焊接结构还有一些其他类型的接头形式,如十字接头、端接接头、卷边接头、套管接头,斜对接接头、锁底对接接头等(图3-74)。

图3-74 焊接接头的形式
(2)焊缝的形式
焊缝是焊件焊接后所形成的结合部分,焊缝按不同分类方法可分为下列几种形式。
①按焊缝在空间位置的不同,可分为平焊缝、立焊缝、横焊缝和仰焊缝四种形式。
②按焊缝结合形式不同,可分为对接焊缝、角焊缝和塞焊缝三种形式。
③按焊缝断续情况可分为以下三种形式。
a.定位焊缝。焊前为装配和固定焊件的位置而焊接的短焊缝,称为定位焊缝。
b.连续焊缝。沿接头全长连续焊接的焊缝。
c.断续焊缝。沿接头全长具有一定间隙的焊缝,称为断续焊缝。它又可分为并列断续焊缝和交错断续焊缝。断续焊缝只适用于对强度要求不高,以及不需要密封的焊接结构。
(3)焊条电弧焊用装配夹具
为保证焊件尺寸,提高装配效率,防止焊接变形所采用的夹具称为焊接夹具。焊条电弧焊常用的装配夹具主要有以下几种。
①夹紧工具 用于紧固装配零件,见图3-75。

图3-75 夹紧工具
②压紧工具 用于在装配时压紧焊件。使用时夹具的一部分往往要点固在被装配的焊件上,焊接后再除去,见图3-76。

图3-76 压紧工具
③拉紧工具 是将所装配零件的边缘拉到规定尺寸的工具,有杠杆、螺钉和导倒链等几种,见图3-77。

图3-77 拉紧工具
④撑具 是扩大或撑紧配件的一种工具,一般是利用螺钉或正反螺钉来达到,见图3-78。

图3-78 撑具
(4)操作方法
以下通过两块规格尺寸为300mm×100mm×12mm的Q235钢板或16Mn钢板的单面T形焊为例,简述多层多道焊的操作方法。
①焊前准备
a.焊机。直流或交流焊机。
b.焊条。E4303(J422)型,直径为3.2mm,焊前焊条烘干100~150℃,1~2h。
c.焊件。Q235钢板或16Mn钢板,规格尺寸为300mm×100mm×12mm。要求钢板在焊接处两侧20~30mm范围内除锈去污。
②焊接步骤
a.定位焊。与其他T形接头相同。
b.第一层焊接。与单层焊相同。
c.第二层焊接。将第一层焊缝表面熔渣清理干净,焊条直径和焊接电流不变,进行第二层共两道焊缝的焊接,见图3-79。应该注意的是,在多层多道焊中要获得良好的焊缝成形,在同一层焊缝中各焊道之间的搭配是关键。

图3-79 焊条角度
第一道焊缝(总二道)的焊接:在焊接第二层第一道焊缝时,应使焊缝覆盖第一层焊道的2/3以上,并保证这条焊道的下边缘是所要求的焊脚尺寸线。此时,焊条角度在45°~55°之间,以使水平板与焊道熔合良好。焊条与焊接方向的夹角为70°~80°,运条采用斜圆圈运条(也可采用直线运条),这条焊道应保持平直而且宽窄一致,以获得良好成形的基础。
第二道焊缝(总第三道)的焊接:第二道焊缝的焊接应覆盖第一道焊缝的1/3~1/2,焊条的落点应在第一道母缝与立板的夹角处,焊条与水平板的夹角为40°~45°,采用直线运条。
(5)操作注意事项
①若T形接头采用两面焊时,可采用图3-80所示的顺序进行焊接。

图3-80 两面焊时焊道的排列
②当焊脚尺寸大于12mm时,可采用三层六道、四层十道进行焊接,参见图3-81。

图3-81 大焊脚尺寸焊道的排列