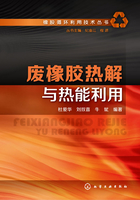
2.4 废轮胎的热裂解机理
2.4.1 废轮胎的组成
废轮胎由许多有价值的组分构成,包括橡胶(天然橡胶、合成橡胶)、炭黑、各种助剂(包括增塑剂、防老剂、硫黄和氧化锌等)和骨架材料(钢丝和织物)等。一般轮胎胎面胶中所含各组分的质量分数大致是橡胶55%~60%,炭黑30%~33%,有机助剂6%~9%,无机助剂3%~6%。表2-5列出了乘用胎和卡车胎各组分的质量分数。
表2-5 典型的轮胎组成(质量分数)

2.4.2 废轮胎热解机理
大多数有机化合物有热不稳定性特征,若将其置于缺氧、高温条件下,在分解和缩合的共同作用下,大分子有机化合物将发生裂解,转化为相对分子质量较小的气态、液态与固态组分,有机物在这种条件下的化学转化过程称为热解。固体废物热解是一个复杂、连续的化学反应过程。其中包括大分子键断裂、异构化和小分子的缩合等化学反应,最后生成较小的分子。在热解过程中,中间产物存在两种变化趋势:一是由大分子变成小分子,直至气体的裂解过程;二是由极小分子聚合成较大分子的聚合过程。这种反应没有明显的阶段性,许多反应是交叉进行的。热解过程可用下式表示:
由于轮胎中含有许多添加剂,组分繁多,因此到1000℃都未完全热解。但是相对于三大主要有机组分而言,添加剂的含量相对较少,因此只讨论废轮胎主要组分的热解规律和特性,可以认为废轮胎在600℃左右已基本热解完成。在废轮胎的热解动力学分析中,为了准确地得到动力学参数(活化能E和指前因子A),废轮胎的热解应该不受系统内热和质传递的影响,因此在进行动力学参数确定时,运行条件的确定至关重要。
废轮胎三种主要有机组分的热物理特性已有研究:天然橡胶初始裂解温度为326℃,对应的最大热分解温度为375℃,至455℃时,裂解过程基本结束;丁苯橡胶初始裂解温度为286℃,对应的最大热分解温度为452℃,至491℃时,裂解过程基本结束;顺丁橡胶初始裂解温度为374℃,对应的最大热分解温度为483℃,至497℃时,裂解过程基本结束。
对废轮胎的三种主要橡胶材料的热解情况研究表明,天然橡胶在350℃左右进行初步热解,反应很不完全,属于α、β键断裂的自由基反应,产物以二聚体和三聚体为主;随着温度的升高,生成了大量异戊二烯单体,同时生成了二甲苯等环化产物,在450~500℃时已基本裂解完全;温度继续升高,热解产物发生二次热解反应和二次无规律断裂反应,从而使裂解产物变得更为复杂。顺丁橡胶在氮气中、550℃热解时热解过程分为两段,最大质量损失分别在370℃和470℃左右。第一段产品主要是丁二烯和苧烯,主要是高聚物自由基的解聚所形成;第二段是复杂的烃类混合物,主要是由剩余的残渣进一步热解所形成。丁苯橡胶在240~450℃温度区间热解时,温度较低时油中的主要成分是丁二烯,温度较高时则是苯乙烯和苯,因此认为热解先开始于共聚物中的丁二烯部分,主要机理是高聚物主链断裂后形成自由基,后通过解聚形成共轭二烯烃,在温度较高和反应时间较长的情况发生Diels-Alder环化反应 ,形成环烯烃化合物,再通过去氢产生如苯的芳烃化合物,进一步反应可生成多环芳烃。
Williams、Leung、崔洪等学者认为废轮胎的热解顺序依次分为三个主要阶段:低沸点添加剂的分解、天然橡胶的分解、合成橡胶的分解,如图2-17所示。废轮胎一般在200℃左右时开始失重,主要是增塑剂及其他有机助剂的分解;300℃时天然橡胶和合成橡胶开始热解,500℃左右热解基本完成。Sennecao等人将上述机理进行了归纳,提出了废轮胎两段热解机理,如图2-17所示。轮胎内高聚物组分中有机分子主链先发生断裂(它可能是丁苯橡胶中的丁二烯和苯乙烯分子,也可能是天然橡胶中的异戊二烯分子,还可能是顺丁橡胶中的丁二烯分子),形成中间体R1和挥发物V1,R1可以沿着2a直接解聚并释放出另一挥发物V2,或者沿2b转变成第2个中间体R2,之后再沿着2c释放出挥发物V3,反应(1)、(2)构成了初级热解(0~500℃);中间体自由基R2沿着路径(3)发生环化反应形成R3,R3在更高温度下进一步分解产生最终残余物R4和挥发物V4,反应(4)是二次热解(500~900℃)。采用热重法(TG)与微分热重法(DTG)研究橡胶热解过程时发现:如果温度缓慢上升(温度较低时主要是天然橡胶的热解,温度较高时主要是合成橡胶的热解),将形成DTG双峰(如图2-18所示);而温度迅速上升时,轮胎中的合成橡胶与天然橡胶的热解失重温区相互交叉,使得混合胶样的TG和DTG图中呈现出一个共同的失重平台或一个DTG峰,如图2-19所示。

图2-17 废旧轮胎热解机理示意图

图2-18 升温速率为10℃/min时轮胎样品的TG/DTG图

图2-19 不同升温速率下轮胎样品的DTG曲线
升温速率/℃·min-1:1—10;2—30;3—50;4—100
2.4.3 废轮胎热解产物
废轮胎热解是在缺氧或无氧气氛中进行的热降解过程,可产生液态、气态烃类化合物和炭残渣。轮胎的热裂解过程属于自由基降解反应,热解产物的形成遵循自由基降解反应的规律。
热解过程的主要产物有可燃性气体、有机液体和固体残渣。
(1)可燃性气体 可燃性气体按产物中所含成分的多少排序为:H2、CO、CH4、C2H4和其他少量高分子烃类化合物气体。这种气体混合物是一种很好的燃料,其热值可达6390~10230kJ/kg(固体废物),在热解过程中维持分解过程连续进行所需要的热量约为2560kJ/kg(固体废物),剩余气体变成热解过程中有使用价值的产品。
(2)有机液体 有机液体是复杂的化学混合物,有焦油和高分子烃类油等,也都是有使用价值的燃料。
(3)固体残渣 主要是炭黑。炭渣是轻质碳素物质,其热值约为12800~21700kJ/kg,含硫量低。此外还有少量废钢丝。
热解产物的产量及成分与热解原料成分、热解温度、加热速率和反应时间等参数有关。表2-6、表2-7分别是废轮胎裂解产物近似分析和元素分析。
表2-6 废轮胎裂解产物的近似分析

表2-7 废轮胎裂解产物的元素分析

2.4.4 废轮胎热解动力学
2.4.4.1 热解反应动力学模型
橡胶的热解是一个十分复杂的过程,其中有许多平行、连串的反应进行,包括C—H和C—C键的断裂、自由基的形成、分子重排、热聚合、芳环缩合、侧链断裂等过程。轮胎的热解过程可以认为是由其组分(天然橡胶、顺丁橡胶、丁苯橡胶、丁基橡胶以及添加剂等)的热解反应线性叠加而成,各种组分的热解过程彼此之间相互独立,互不干扰。
废橡胶热解研究初期,人们通常将其视为单步反应,如Bouvier早在1987年就建立了单步反应动力学模型,由热重分析和微分热重分析结果计算反应的活化能为125kJ/mol,指前因子为1.08×109min-1。但单步模型显然过于简化,不能解释轮胎失重曲线中有多个失重峰的现象,此后学者们又建立了多步反应和平行反应的动力学模型。
Willianms提出热解过程中动力学参数变化的多步反应模型,该模型假设热解样品为成分单一的纯净物,动力学参数在不同热解温度阶段有不同的值,利用微分法或积分法求出各个热解阶段的动力学参数。Gonzailez研究认为轮胎热解过程经历了三步反应,三个温度区间分别是150~250℃、200~335℃和320~500℃,分别对应的活化能为66.8kJ/mol、44.8kJ/mol和32.9kJ/mol,指前因子为1×105min-1、3×104min-1和756min-1。但由于轮胎样品热解过程是个多组分共同反应,原料间的相互作用掩盖了各自的热特征,该模型不能正确描述不同热解阶段过渡区域的反应特性。
Kim认为轮胎的各组分互不干扰,以各自的动力学参数参加热解,建立了轮胎热解的平行反应动力学模型。Teng等的研究也获得了类似的结论。Lin等人具体研究了顺丁橡胶(BR)和丁苯橡胶(SBR)及混合物的热解规律,研究表明BR热解是两步反应,而SBR则是三步反应,实验证实了混合热解中BR和SBR是基本独立的。Yang研究认为各种添加剂对热失重曲线的形状没有影响,通过分析废旧轮胎中具体胶种和油类成分,确定了每一成分所对应的动力学参数,从而可较好地模拟废旧轮胎热解过程。
Leung和Wang在以上这两种模型的基础上采用DG/DTG技术对废旧轮胎进行热解研究,提出了三组分模拟模型和三弹性体模拟模型。三组分模拟模型认为轮胎粉末由三种主要可降解的组分组成,组分一是增塑剂和其他有机助剂的混合物,组分二和组分三由NR、BR、SBR和SR/BR/SBR的混合物组成,每一组分分别进行不可逆一级降解反应并符合Arrhenius定律,热解速率是三个组分降解速率的总和。这两种动力学模型比较客观地反映了废旧轮胎热解过程中的失重规律。但仅限于常压和惰性气体中的热解,在真空和氧化性气氛中则不适用。Yang等提出了小颗粒和大颗粒状轮胎碎片的真空热解数字模型,即假设颗粒内部的热传递由热交换严格控制,热解反应是一级反应,挥发物在废旧轮胎固体颗粒表面累积到一定程度后突然放出,即挥发物的转移是由“暴沸”传质机制来控制。
张守玉等利用TG/DTG技术对不同来源的三种废轮胎样品的热解特性进行了研究,结果表明,新旧废轮胎样品热解趋势基本一致,均经历了一个不明显的失重过程和两个明显的失重过程,其原因是废旧轮胎中的橡胶组分比较复杂;内胎样品中的组分比较单一,其热解过程比较简单,仅经历了一个不明显的失重过程和一个明显的失重过程;三种样品的主要失重温度为600~800K,转化率为0.2~0.8;使用一级动力学反应模型很好地模拟了三种轮胎样品的主要失重过程。
2.4.4.2 热解反应动力学方程
在选定的运行条件下,气相和固体内的传热和传质的影响可以忽略不计,废轮胎热解可以假设为完全受化学反应动力学控制,动力学参数(动力学活化能和指前因子)可以根据以下原则计算。
假设废轮胎在热重分析仪中的热解反应是简单热裂解,其热解方程见式(2-1)。其中A(s)为原废轮胎固体,是反应物,B(s)是高温热解的固体剩余物——焦炭,C(s)是气体产物,它包括水蒸气、CO、CO2、H2和一些烃类化合物。
(2-1)
热解反应速率是升温速率、终温及热解产物质量的函数。假设把在无限短时间的不等温反应认为是等温反应,热解本征动力学方程可表示为:
(2-2)
式中,t时刻的失重率;m0、m∞分别表示为反应起始和终止时的质量,kg;mt为t时刻的质量,kg;根据阿累尼乌斯公式,反应速率常数k=Aexp(-E/RT),s-1;E是活化能,kJ·mol-1;A是指前因子,s-1;R是通用气体常数,其值为8.314J·(mol·K)-1;T是反应温度,K;f(α)是描述反应过程的机理函数,一般简单表示为f(α)=(1-α)n;n为反应级数,这样式(2-2)转换为:
(2-3)
当升温速率为常数时,可得到:
(2-4)
当n=1时,
(2-5)
取对数则:
(2-6)
对作图,应为一条直线,斜率为
,截距为
。
当n≠1时:
(2-7)
取对数则:
(2-8)
对作图,也为一条直线,其斜率为
,截距为
。
采用线性回归的方法求解上述方程,就可得到反应活化能E和指前因子A。
然而,随着热解温度的变化,热解反应机理可能会有所不同,因此不同温度下的热解动力学参数需进行独立的计算分析。正确的反应机理的确定是基于实验数据和计算结果间的最佳拟合原则。当整个热解过程被分为几个阶段时,E仅为单个温度段的活化能,与整个热解反应过程没有直接关系。
废轮胎的热解和燃烧反应也可用Vachuska和Voboril提出的固体降解方程来表示:
(2-9)
由于降解反应在800℃下发生,该温度是动力学反应的温度范围,反应速率常数ki可由阿累尼乌斯方程得到:
Ki=Aiexp(-Ei/RT) (2-10)
根据式(2-9)和式(2-10),可通过实验得到的热失重曲线和微分热失重曲线计算得到动力学参数。同时也考虑了反应热的影响,样品的温度是随着实际的加热速率而变化。
将式(2-10)代入式(2-9)中,并将两边取常用对数得到:
(2-11)
如果在不同的温度范围存在着两个反应,这两个反应分别对应着两个组分的降解,则动力学描述如下所示:
(2-12)
如果一个反应发生在一个特定的区域,也就是说如果是1级反应,则dα2/dt=0,α2=0,α1=αT,式(2-12)可简化为:
(2-13)
当式(2-13)等号左边的式子对1/T作图,则得到一条直线,斜率为E/R,截距Y则等于lnA。任意时刻的α、dα/dt、T的值可从TG和DTG曲线上计算得到。因此,动力学参数,如表观活化能E和指前因子A可从上述方法中求得。
α、dα/dt的值也可以从αT减去α1和从dαT/dt中减去dα1/dt得到。采用相似的方法,也可以得到式(2-10)中的动力学参数。
α、dα/dt的理论预测:如果除了温度范围和加热速率β外,动力学参数已知,可通过在一定的温度范围内对式(2-9)积分,计算得到归一化的质量损失率α。
(2-14)
上述方程中右边没有确切的积分值,但是通过使用Coats和Redfern关系,可近似为:
(2-15)
因此,α可以表示为:
(2-16)
从上述方程中,可理论预测热解过程参数,如α和dα/dt。
2.4.4.3 热解反应能耗分析
轮胎的热解反应过程中包含挥发分的吸热和热解反应的放热。将轮胎加热到热解温度需要消耗大量的热能,而轮胎中胶料的热解过程包含非常复杂的化学反应,如热分解、环化、交联等,这些反应是过热过程。整个热解过程是一个耗能过程。
Yang等用DTA技术对轮胎中主要胶体NR、BR、SBR的热解焓变进行研究,发现1kg NR、SBR、BR热解总吸热量分别为870kJ、550kJ、325kJ,1kg轮胎热解所需总热量在1410~1530kJ。Labrecque等发现1kg轮胎热解吸热量为706kJ。Roy发现1kg轮胎真空热解吸热量为700kJ。薛大明等人通过理论计算和实验结果表明:热解1kg废旧轮胎约需1953.00kJ(理论)和1994.00kJ(实验)的热量。
以单位质量轮胎为基础的热解气低位热值为4.6~7.6 MJ/kg轮胎,而每公斤轮胎热解需要的热量小于2MJ,在工业化生产中,热解气不易贮存和运输,可以作为轮胎热解的热源。