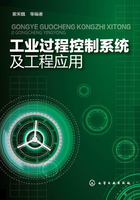
1.2 分布式控制系统
分布式控制系统采用微处理机分别控制各个回路,而用中、小型工业控制计算机或高性能的微处理机实施上一级的控制。各回路之间和上、下级之间通过高速数据通道交换信息。分布式控制系统具有数据获取、直接数字控制、人机交互以及监控和管理等功能。分布式控制系统是在计算机监督控制系统、直接数字控制系统和计算机多级控制系统的基础上发展起来的,是生产过程的一种比较完善的控制与管理系统。在分布式控制系统中,按区域把控制站安装在测量装置与控制执行机构附近,将控制功能尽可能分散,管理功能相对集中。这种分散化的控制方式能改善控制的可靠性,不会由于个别计算机的故障而使整个系统失去控制。当管理级发生故障时,过程控制级(控制回路)仍具有独立控制能力,个别控制回路发生故障时也不致影响全局。与计算机多级控制系统相比,分布式控制系统在结构上更加灵活、布局更为合理和成本更低。
分布式控制系统是一个由过程控制级和过程监控级组成的以通信网络为纽带的多级计算机系统,综合了计算机(Computer)、通信(Communication)、显示(CRT)和控制(Control)等4C技术,其基本思想是分散控制、集中操作、分级管理、灵活配置、方便组态。目前,大部分的复杂过程控制系统都采用这种结构类型。
1.2.1 分布式控制系统的结构
对于集中式计算机控制系统,其两大应用指标是中央计算机的处理和计算机自身的可靠性。若计算机的处理速度快,它在一定时间范围内就可以管理更多的被控设备。和以往一样,工厂中已有的仪器仪表装置都不得不连接到计算机上,这样在计算机和仪器仪表间存在着很多连接装置。若是利用中央计算机来进行技术改造,利用现存的连接装置,整个控制系统的完成就比较省事;若是要重建工厂就不太容易,因为计算机变得越来越便宜,而连接装置的造价相对变化不大,这样连接装置比计算机的花费还大。另外,所有的控制功能都集中到单台计算机上来完成,一旦计算机出了问题,就意味着所有功能都将失效,对于这种状况,必须寻求一种更加可靠的计算机自动化控制系统。
20世纪60年代末到70年代初,出现了小型、微型计算机,使得小型、微型计算机的功能更加完善,并且价格便宜。因而可以用这种小型计算机来代替中央计算机的局部工作,以对其周围的装置进行过程监控,有人将这些小型机组成为第一级计算机;而中央计算机只处理中心自动化问题和管理方面的问题,从而产生了两级自动化控制系统的结构(图1.2),也有人把这种结构称为分散式计算机系统。这种结构在当时得到了广泛应用。20世纪70年代末,一开始集散控制系统是以多个计算机自动化系统的形式由制造商推出,而一旦用户采用了分散式计算机控制系统,就必然会在满足自己应用的前提下,选择价格更加合理的不同厂家的计算机产品,而且当分散式控制系统逐渐建成后,就会与现存的过程控制计算机集成起来,一起完成它们的主要功能,这些小型计算机主要是完成实时处理、前端处理功能,而中央计算机只充当后继处理设备。这样中央计算机不用直接与现场设备打交道,从而把部分控制功能和危险都分散到前端计算机上,如果中央计算机一旦失效,设备的控制功能依旧得到保证。

图1.2 二层结构的分布式控制系统
图1.2中所示的多计算机结构比较适合小型工业自动化过程,在这些系统中存在的前端计算机较少,然而当控制规模增大后就得有很多前端计算机才能满足应用需求,从而使中央计算机的负载增大,难以在单台中央计算机的条件下及时完成诸如模块上优化、系统管理等方面的工作。在这种应用条件下,就出现了具有中间层次计算机的控制系统。在整个控制系统中,中间计算机分布在各车间或工段上,处在前端计算机和中央计算机之间并担当起一些以往要求中央计算机来处理的职能,系统结构就形成了三级计算机之间并担当起一些以往要求中央计算机来处理的职能,系统结构就形成了三级计算机控制模式(图1.3)。这种结构模式在工厂自动化方面得到了很广泛的应用,至今仍经常见到。

图1.3 三层结构的分布式控制系统
1.2.2 分布式控制系统的功能层次
目前,层次化已成为控制系统的体系特点,使其体现集中操作管理、分散控制思想。典型的控制系统的体系结构目前一般分为四层结构:过程控制级,集中监控级,生产管理级,综合管理级,如图1.4所示。

图1.4 分布式控制系统层次结构
过程控制级:主要由现场控制站、I/O单元和现场各类装置(如变送器、执行器、记录仪表等)组成,是系统控制功能的主要实施部分。控制系统的现场控制站接受现场送来的测量信号,按照指定的控制算法,对信号进行输入处理,控制算法运算,输出处理后向执行器发出控制指令。同时接受上层的管理信息,并向上传递过程控制级的现场装置的特性参数和现场采集到的实时数据。
集中监控级:包括操作员站和工程师站,用于完成系统的操作和组态,综合监控各过程控制站的所有信息,集中显示操作,控制回路组态和参数修改,优化过程处理。
生产管理级(产品管理级):位于这一级的管理计算机根据生产的产品情况,协调各单元级的参数设定。
综合管理级:位于这一级的管理计算机主要用于企业的生产调度、计划、销售、库存、财务、人事以及企业的经营管理等方面信息的传输。
1.2.2.1 过程控制级
过程控制级是控制系统的基础,其主要任务如下。
(1)进行过程数据采集:即对被控设备中的每个过程量和状态信息进行快速采集,为进行数字控制、开环控制、设备监测、状态报告的过程等获得所需要的输入信息。
(2)进行直接数字的过程控制:根据控制组态数据库、控制算法来实施过程量(开关量、模拟量等)的控制。
(3)进行设备监测和系统的测试、诊断:把过程变量和状态信息取出后,分析是否可以接受以及是否可以允许向高层传输。进一步确定是否对被控装置实施调节,并根据状态信息判断计算机系统硬件和控制模块的性能,在必要时实施报警、故障诊断等措施。
(4)实施安全性、冗余化措施:一旦发现计算机系统硬件或控制模块有故障,立即实施备用件的切换,保证整个系统的安全运行。
1.2.2.2 集中监控级
集中监控级主要是处理单元内的整体优化,并对其下层产生确切的命令,在这一层可完成的功能主要有以下几点。
(1)优化过程控制。这可以根据过程的数学模型以及所给定的控制对象来进行,优化控制只有在优化执行条件确保的条件下方能达到,但即使在不同策略条件下仍能完成对控制过程的优化。
(2)自适应回路控制。在过程参数希望值的基础上,通过数字控制的优化策略,当现场条件发生改变时,经过过程管理级计算机的运算处理就得到新的设定值和调节值,并把调节值传送到直接过程控制层。
(3)优化单元内各装置,使它们密切配合。这主要是根据单元内的产品、原材料、库存以及能源的使用情况,以优化准则来协调相互之间的关系。
(4)通过获取过程控制层的实时数据以进行单元内的活动监视、故障检测存档、历史数据的存档、状态报告和备用。
1.2.2.3 生产管理级
产品规划和控制级完成一系列的功能,要求有比系统和控制工程更宽的操作和逻辑分析功能,根据用户的订货情况、库存情况、能源情况来规划各单元中的产品结构和规模,并且可使产品重新计划,随时更改产品结构。这一点是工厂自动化系统高层所需要的,有了产品重新组织和柔性制造的功能,就可以应付由于用户订货变化所造成的不可预测的事件。因此,一些较复杂的工厂在这一控制层就实施了协调策略。此外,纵观全厂生产和产品监视,以及产品报告也都在这一层实现,并与上层交互传递数据。在中小企业的自动化系统中,这一层可能就充当最高一级管理层。
1.2.2.4 综合管理级
综合管理级处于自动化系统的最高层,它的管理范围很广,包括工程技术方面、经济方面、商业事务方面、人事活动方面以及其他方面的功能。把这些功能都集中到软件系统中,通过综合的产品计划,在各种变化条件下,结合多种多样的材料和能量调配,以及达到最优化地解决这些问题。在这一层中,通过与公司的经理部、市场部、计划部以及人事部等办公自动化相连接,实现制造系统的最优化。在综合管理这一层,其典型的功能有:市场分析,用户信息的收集,订货统计分析,销售与产品计划,合同事宜,接受订货与期限检测,产品制造协商,价格计算,生产能力与订货的平衡,订货的分发,生产与交货期限的监视,生产、订货和合同的报告,财务方面的报告等。