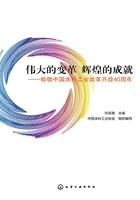
核电涂料40年发展
吴 权
我国核电站的发展,始于1984年开工、1991年建成投入运行的第一台核电站秦山Ⅰ期。中国核电涂料的发展,是伴随着我国核电站的建设发展起来的。伴随着改革开放的不断深化,目前我国核电事业取得了长足进步,相应地我国核电涂料也与国际接轨,经历了三代核电保护涂料的发展,从安全性、防护性等方面取得了很大的成就。
在全球电力产业中,具备规模供电的主流电站,按能源转换形式分主要有火电、水电、核电、风电几类。其中核电站占用土地少、不受自然环境限制、能源转换率高、废气零排放,是理想的电力来源,也是一个国家技术实力的象征和未来的主要能源供应方向。放眼全球,一些发达国家已经把核电产业发展成国家电力供应支柱,如法国能达到50%以上的比例。在我国,随着政府对工业污染的控制越来越严格,尤其是在民众对雾霾控制的关切程度加深的情况下,国家对核电的支持力度正在迅速增强。
核能是一种清洁的能源。它在全世界的能源结构中占有重要的地位。根据《中国电力发展“十三五”规划》的要求,2020年全国核电装机将达到5800万千瓦,在建规模3000万千瓦以上。我国的国民经济更是突飞猛进地快速向前发展,对能源的需求不断增加。可以预见,在不久的将来,在中国的电力系统中,核电将会发挥重要的作用。
1 核电用防护涂料综述
1.1 核电用涂料简述
应用于核电站的涂料,按其使用用途,可分为核级和非核级涂料。非核级涂料用于普通场所,如常规岛钢结构和混凝土表面;核级涂料是用于存在核辐射的场所和结构的防护涂料,涉及辐射的厂房设备和其他结构表面。按其分布区域(见图1),核电站专用涂料可分为3种类型:①安全壳内涂层,即安全壳内全部设备及构筑物表面的涂层;②辐射控制区涂层(不包含安全壳的辐射控制区内全部设备及构筑物表面的涂层);③安全设备涂层,即非辐射控制区内主要核安全相关设备、构筑物表面的涂层,包括一回路海水冷却系统设备、强制通风和通水管道或沟槽、核级储水罐内部涂层、高架烟囱或设施、汽机主油箱及应急柴油机油箱内部涂层。
图1 核电站专用涂层的分布示意
安全壳是核电站的中心部位,由于壳内存在中子、α粒子、β粒子和γ粒子射线,辐照累积剂量高,容易出现表面辐射污染。特别是发生冷却剂失水事故时,瞬间产生的高温高压伴随着大量的放射性物质形成的强辐射,同时喷淋高浓度硼酸水,可能导致涂层剥落、核电站安全功能的丧失及其他潜在腐蚀隐患。因此,应用于核岛安全壳内的防护涂层不可以有严重的剥落、起壳、粉化。否则,大量的残余物进入堆内总应急冷却液中,导致管线、泵、喷嘴及堆总冷却管道堵塞,影响安全系统的功能,会带来严重的安全事故。因此安全壳涂层的主要作用是:首先对于钢或混凝土结构的核岛,作为保护其不受腐蚀的第一道屏障;同时,也可以用来保持密封性能,使钢结构或混凝土不受辐射的污染。通常,安全壳内用涂料不含有铝粉,硫和卤素总含量要求≤1000mg/kg。
辐射控制区涂层内同样存在α粒子、β粒子和γ粒子射线,容易出现表面辐射污染,本类涂层重点关注辐照及去污性能,其中硫和卤素总含量要求≤1000mg/kg。
处于非辐射控制区的安全设备上的涂层受污染后,会影响核电站的安全功能,包括核级储水罐内部涂层对一回路水质的污染;主油箱内部涂层剥落,使汽机运行异常;应急柴油机油箱内部涂层、强制通风通水管道涂层剥落等事故工况下,也影响安全功能的执行。对于核级储水罐内部涂料,硫和卤素总含量的要求≤1000mg/kg,甚至更低。
核电站涂层在服役期间会受到恶劣环境的影响,从而造成老化腐蚀。表1描述了不同种类核电涂层的运行环境和涂覆对象。
表1 核电专用涂层涂覆对象和运行环境
从表1中我们可以看出,应用于不同涂覆对象上的核电站涂层所处的运行环境也不相同,这也对每种分类的涂层提出了不同的要求。
1.2 国外核电涂料的发展及应用概况
国外对于核电站涂层的研究起步很早。在1960年左右,美国已经有公司负责开发核电站防护涂层系统。当时针对涂层系统的研究主要关注于满足当时新建核电站的防护要求和准则。这些系统直接应用于混凝土或者不锈钢设备上。
1980年2月,华盛顿公共电力供应系统(西北能源的前身)对美国国家核电导则R.G.1.54,水冷堆防护性涂层质量保证需求开展了一系列研究,确定了核电站内部涂层的技术方向:对于化学降解有着较强的抵抗力;常温下为高分子网络;对不同应用表面有强附着力;对基底有较强的辐射防护力;事故工况下有很强的持久性和良好的力学性能。这为今后涂层的研究确定了基本方向。
1994年,华盛顿公共电力供应系统进行了一系列测试/评价核电站内部涂层系统的项目。在其项目中考虑了35种可能的涂层材料。经过MSDS、屏幕测试、辐照和DBA测试之后,最终有机环氧涂层在各项指标中均取得了最好成绩。之后在1998年,国际标准协会颁布了ISO 12944-5,规定了钢结构的防腐涂装规范,其中第5部分着重介绍了防护涂料体系。
根据1998年美国电力研究院(EPRI)对全美31座核电站专用涂层的调查,美国核电站涂层应用情况如表2所示。
表2 美国核电专用涂料的主要类型
1.3 国内核电涂料的发展及应用概况
从2005年到现在,我国每年都有新开工建设的核电站。截至2018年12月31日,我国投入商业运行的核电机组共44台(不含中国台湾地区核电信息),装机容量达到44645.16MWe(额定装机容量)。其中,7台核电机组在2018年投入商业运行,装机容量为8838.00MWe。我国在建核电规模全球领先,工程项目有序推进,在建规模继续保持世界第一。
中国当前已建成投产和在建的核电站情况如表3所示。
表3中已建成和在建的核电站除了山东海阳核电站一期、浙江三门核电站一期采用第三代核电AP1000技术,其他都采用第二代或“二代加”核电技术。第三代核电技术与二代技术主要区别是:第二代核电技术在安全上不满足《国际原子能机构安全标准》(第2版)对预防和缓解严重事故的要求,也不符合我国新颁布的安全法规预防和缓解严重事故的要求,而第三代核电技术能够满足上述机构和法规要求。
表3 中国当前已建成投产和在建的核电站情况
国内核电发展初期,核电标准和装备技术都是参照国外先进国家的标准所制定。如今我国核电涂料存在以秦山一期为代表的自主研发涂料技术路线和以大亚湾核电站为代表的全面引进涂料技术路线。
第一代核电站均为实验性质,第一代核电涂料采用常规工业防腐涂料产品,产品配套为环氧底漆+环氧面漆。真正意义上的核电涂料,是从第二代核电开始采用。第二代核电涂料开始,有了核级标准和核级概念。目前最严格的第三代核电涂料,要求以“华龙一号”和AP1000标准为主。
秦山一期核电专用涂料由我国自主生产,主要供应商有上海开林造漆厂和中海油常州涂料化工研究院有限公司。其专用涂料主要类型如表4所示。
表4 秦山一期核电专用涂料的主要类型
大亚湾核电涂料由国外涂料供应商生产,主要有式玛卡龙涂料和Carboline涂料,所用涂料的主要类型见表5。
表5 大亚湾核电专用涂料主要类型
2 核电用防护涂料发展
2.1 第二代核电保护用涂料
作为核电站重要配套产品的涂料产品,我国从无到有,经历了一个飞速发展的历程。核电站用涂料作为核电技术中重要的组成部分,对其各项性能指标要求比普通工业防腐涂料要求严格和苛刻许多,其中一些性能要求是一般重防腐涂料不具备或达不到的。
以秦山一期、秦山二期涂层技术的成功应用为前提,提出了核电专用涂层的EJ标准。这些标准的编写分别参照了ASTM、NF对应标准的内容和技术要求。一般来说,30万千瓦核电厂的标准参照ASTM标准编写,其余参照NF标准编写。表6给出了应用于不同核电站专用涂层的EJ标准。
表6 应用于不同核电站专用涂层的EJ标准
第二代及“二代加”核电涂料涂层常用配套如下。
(1)非核区域内涂层系统(PIA,PIB系列)
金属钢结构底材:核级环氧底漆+核级环氧面漆;
混凝土底材:核级环氧清漆+核级环氧腻子+核级环氧底漆+核级环氧面漆。
(2)反应堆厂房内涂层系统,核区域内(除反应堆厂房)涂层系统(PIC、PID系统)
金属钢结构底材:核级环氧底漆+核级环氧面漆;
混凝土底材:核级环氧清漆+核级环氧腻子+核级环氧底漆+核级环氧面漆。
(3)露天环境下(海洋大气环境)的涂层系统(PEC)
金属钢结构底材:环氧富锌底漆+环氧厚浆型中间漆+聚氨酯面漆;
有色轻金属底材:特种环氧底漆+环氧厚浆型中间漆+聚氨酯面漆。
(4)埋入土中和液体介质中的涂层系统(PLA-PLJ系统)
金属钢结构底材:特种厚涂型环氧涂料;
混凝土底材:核级环氧清漆+特种厚涂型环氧涂料。
2.2 第三代核电保护用涂料
三代核电以我国自主研发的“华龙一号”及AP1000为代表,二者使用涂料的标准有所不同。
2.2.1 “华龙一号”系列核电保护用涂料
“华龙一号”系列核电保护用涂料执行能源行业标准(NB标准),标准见表7。
表7 “华龙一号”系列核电保护用涂料执行的能源行业标准(NB标准)
“华龙一号”系列核电保护用涂料和第二代及“二代加”核电涂料涂层常用配套相同,保护的区域相同。最大的区别在于LOCA试验部分,NB/T 20133.2—2012《压水堆核电厂设施设备防护涂层规范 第2部分:涂层系统在模拟设计基准事故条件下的评价试验方法》,对比EJ/T 1086—1998《压水堆核电厂用涂料漆膜在模拟设计基准事故条件下的评价试验方法》,试验原理和方法相同,对喷淋液进行了修改、对模拟DBA试验前涂层的预处理进行了修改。试验条件更为苛刻,对涂层的性能提出了更高的要求。
核电站不同部位典型的涂层配套(华龙一号)如表8所示。
表8 涂层系统适用区域(PIA/B/C/D 100、101、102、103、120、121、122、123)
用于混凝土表面的常规配套如表9所示。
表9 核岛及核辅助厂房墙和天花板以及地板薄涂层(PIA/B/C/D 151、152、155)
常用配套技术要求见表10。
表10 涂装配套技术要求汇总
2.2.2 AP1000系列核电保护用涂料
第三代核电站AP1000(美国)及我国的CAP1400系列是当前世界上最先进的核反应堆。2009年开工建设的浙江三门核电站为世界上首座采用此堆型建造的核电站,三门核电一期是我国三代核电自主化依托项目,采用从美国西屋公司引进的AP1000核电技术,由国家核电负责技术引进、消化、吸收和再创新。三门核电1号机组于2009年3月29日浇注第一罐混凝土,2018年4月25日开始首次装料,6月30日首次并网成功,9月21日AP1000全球首堆三门核电1号机组顺利完成168小时满功率连续运行考核,机组具备商业运行条件。三门核电2号机组于2018年8月24日首次并网,11月5日投入商业运行。由国家电投控股投资、建设及运营的海阳核电1号机组于2018年8月17日首次并网,于10月22日投入商业运行,海阳核电2号机组于8月8日首次装料。
与传统的压水堆安全系统相比,CAP系列采用“非能动”的安全系统,“非能动”设计概念就是利用固有的热工水力特性,简化安全系统的设计,使核电站保证安全的措施不再依赖泵、风机等能动设备的运行,从而大幅度地减少了安全级的阀、泵、电缆及抗震厂房;降低了大宗材料用量;减少了运行人员的操作,通过这些设计改进,CAP系列机组的安全性得到显著的提升。
与传统压水堆型核电站一样,CAP系列核电站中的金属部件及混凝土结构表面也广泛使用各种保护性涂层。根据CAP系列非能动核电站系统、构筑物和部件所在区域及运行条件(包括正常运行温度、有无辐照),将防护涂层应用在安全壳容器(CV)、安全壳内部、安全壳外辐照控制区(RCA)、非辐照控制区及其他区域(NRCA)。
CAP系列核电站采用双层安全壳,其内层钢制安全壳与外层混凝土安全壳基本为相互独立的实体。保护涂层设计与传统压水堆核电站相比具有以下显著特征。
(1)内层的钢制安全壳为完整的密闭碳钢容器,在正常运行期间,为保证碳钢的耐腐蚀性,需对其内外表面进行涂层防护,故CV用涂层应具有较好的耐蚀性。由于在发生DBA事故时,CV内温度和压力迅速升高,布置于混凝土安全壳结构顶部的非能动安全壳冷却水箱将冷却水喷淋到CV顶部,水流沿着CV容器上半部的外壁而下,故外壁上的涂层应具有较好的润湿性和导热性,以利于水流带走CV内的热量,使CV温度和压力得到缓解而不损害容器,避免核素释放到安全壳外环境中。
以上CV表面用涂层系统的耐蚀性、导热性和润湿性对于AP1000/CAP1400核电站的正常运行和DBA后的事故处理都有着重要的安全功能,故CV内外表面用涂层均被划分为安全相关涂层。
(2)CAP系列核电站的结构和涂层设计可避免DBA后安全壳内失效的涂层迁移到过滤器堵塞滤网,或进入主回路而影响安全停堆:通过规定安全壳内物项用涂层的干膜密度(无机锌涂层≥3000kg/m3,环氧涂层1500kg/m3)及内部结构设计,使事故后再循环冷却水的流速迟缓,以确保事故后失效的涂层沉积于各楼层底板而不迁移到再循环过滤网口;同时在过滤网附近不使用任何涂层,且设置不锈钢挡板以使迁移到再循环滤网的涂层最少化。由于滤网为竖直布置,网口距底板有一定高度,故即使有极少量涂层碎片迁移到安全壳再循环滤网,也会沉积到底板而不会堵塞过滤网。
AP1000/CAP1400核电站根据业主的要求和保守的考虑,对CV内物项用涂层系统也均要求经过模拟DBA试验鉴定。
设计推荐的涂层系统中,所选用涂料如表11所示。
表11 CAP系列核电站涂料品种
第三代(AP1000/CAP1400)核电涂料涂层常用配套如下。
钢结构底材:
① 无机锌涂层(IOZN),适用于CV内外表面和所有耐高温要求部位;
② 无机富锌涂层(IOZN)+高固体分环氧涂层(SPHSEN),适用于CV内表面部位;
③ 高固体分环氧涂层(SPHSEN),适用于CV内金属,RCA与NRCA区域常温部位;
④ 无机富锌涂层(IOZN)+高固体分环氧涂层(SPHSEN)+聚氨酯面漆(PUE),适用于NCRA外海洋气候钢结构部位。
混凝土底材:
① 高固体分环氧封闭清漆(ESN)+无溶剂环氧腻子(SURFN)+高固体分环氧涂料(SPHSEN),配套不同的膜厚,适用于一般区域,墙裙及墙裙以上部位;
② 高固体分环氧封闭清漆(ESN)+无溶剂环氧自流平(SLEN),适用于地面高频通过部位。
涉及的涂装配套技术要求如表12所示。
表12 涂装配套技术要求
3 第二代与第三代核电涂料产品对比
3.1 第二代核电主流涂料
钢结构主要使用传统溶剂型环氧涂料,产品为中低固体分,便于施工,但是不能满足未来的环保要求。
混凝土结构使用涂料:有些公司使用水性环氧涂料体系,有些公司使用溶剂型涂料体系,使用方会依据自己的实际需求,选择不同的体系。
3.2 第三代核电涂料
无机富锌涂料的引入,提高了产品的长期防腐蚀性能,能够满足第三代核电非能动的要求,但是对施工环境及施工人员要求较高。
高固体分环氧涂料的使用,比第二代采用的传统溶剂型环氧涂料性能有了极大提升,能满足最苛刻的核电性能要求。降低了体系中VOC的含量,满足环保要求。
混凝土系统无溶剂产品的使用,提高了环保性能,提高了施工效率,既满足设计方的要求,又能满足施工方的要求。
随着国内核电事业的蓬勃发展,国内的涂料厂商逐渐形成供应商的中坚团队,而且形成了自己的技术体系的拳头产品。目前国内核电涂料主要供应商是中远关西涂料化工有限公司、中海油常州化工研究院有限公司和信和新材料股份有限公司。其中能同时供应AP1000与华龙一号这两个第三代核电标准涂料的只有中海油常州院和中远关西涂料两家。
4 国内核电部分涂装业绩
(1)连云港田湾核电站(见图2)


图2 连云港田湾核电站
项目名称:连云港田湾核电站
设计院:中国核工业第二研究设计院
施工单位:中核二二建设公司、中核二三建设公司、中核华兴建设公司
(2)中国实验快堆(见图3)


图3 中国实验快堆
项目名称:中国实验快堆
设计院:中国核工业第二研究设计院
施工单位:中核二四建设公司、中核二三建设公司
(3)绵阳NP项目(见图4)


图4 绵阳NP项目
项目名称:绵阳NP项目
设计院:上海核工程研究设计院
施工单位:中核二四建设公司、中核二三建设公司
(4)秦山核电二期扩建工程(见图5)


图5 秦山核电二期扩建工程
项目名称:秦山核电二期扩建工程
设计院:核工业第二研究设计院
施工单位:中核二四建设公司、中核二三建设公司、中核二二建设公司、中核第五建设公司
(5)福清核电一期(见图6)

图6 福清核电一期
项目名称:福清核电一期
设计院:核工业第二研究设计院
施工单位:中核二四建设公司、中核二三建设公司
5 核电涂料展望
2018年4月28日,被戏称为“全球最大移动电源”的世界首个海上民用浮动核电站开启新的航程。“罗蒙诺索夫号”浮动核电站(见图7)被拖出圣彼得堡造船厂,开始其通往该国最北部城市佩韦克的行程。在装载核燃料后,“罗蒙诺索夫号”将于2019年夏天被拖往北极港口佩韦克,并交付使用。浮动核电站是利用浮动平台建造的可移动核电站,与标准核电站相比,水上核电站抗震能力更强以及放射性物质流失可能性更小。

图7 “罗蒙诺索夫号”浮动核电站
中国浮动核电站项目也已开始,公开资料显示,2015年,国家发改委复函同意中核集团的ACP100S、中广核的ACPR50S、中船重工的HHP25被纳入能源科技创新“十三五”规划。浮动核电站的开启,对核电涂料的开发又提出了新的要求。虽然浮动核电站涂料的技术要求还没有公布,和常规核电站涂料相比,浮动核电站用涂料除了要考虑NB-T 20133—2012标准以外,还应该考虑海洋腐蚀环境下的要求,可以参考NORSOK_M-501-2012 Surface preparation and protective coating 和ISO 20340:2009 Paints and varnishes ——Performance requirements for protective paint systems for offshore and related structures的相关要求。
核电涂料的设计开发过程中,最为重要的原则是:安全与可靠。核电涂料开发,不追求最先进的技术、最领先的材料,首要的是要考虑涂料的安全性与可靠性。与发达国家相比,我国核电涂料起步较晚,我们为评估核电涂料性能建立了NB-T 20133—2012标准,但是对核电涂料长期使用状况评估、性能评测还没有建立适合的评测方法及标准。从2015年开始,国家核电上海核工业研究设计院联合中远关西涂料化工有限公司、中海油常州涂料化工研究院分别进行了“CAP系列核电站安全壳涂层寿命及可靠性试验”研究,在CAP系列核电站用涂料的使用研究上迈开了坚实的一步。
核电有了半个多世纪的发展,目前在运的核电站大部分在未来10年内将面临退役或者延寿的选择。根据美国的经验,一般核电站设计寿命是40年,再延寿20年。我国核电AP1000、CAP1400、华龙一号、EPR等项目如火如荼发展的同时,秦山核电站、大亚湾核电站运行已经超过20年,到了该考虑退役还是延寿的时候了。核电站退役是指核电站在达到其使用寿命后,对其进行妥善管理和处置的工作。退役主要包括“去污”与“拆除”两个过程。“去污”即是去除表面松散或较坚固的放射性沉积物的清洗过程;“拆除”即是拆除所有带放射性的设备和材料。核电涂料面临的“去污”与“拆除”问题尤为突出,目前没有任何数据显示使用中的核电涂料表面放射性沉积物的数量及对应的清洗方法、处理方法。那么,拆除方法、退役相关的技术如何制定,当地居民对于退役拆除过程中对其生活环境的忧虑等因素均会增大退役实施的难度。退役核电涂料的相关研究已经迫在眉睫了。
中国核电涂料从无到有,经过研发人员的不懈努力,近几年更是有了飞速的发展。但是我们还应该看到差距与不足,期望研发人员加强核电涂料全面性研究工作,为我国核电事业的发展做出更大的贡献。
参考文献
[1] 刘会成,程煜,吴权,等.核级无机富锌保护涂层表面润湿性能的研究[J].中国涂料,2014,29(9):49-52.
[2] 程煜,吴权.第三代核电用环氧涂层的开发与研究[J].中国涂料,2015,30(4):69-73.
[3] 史春晖,殷勇.我国核电涂料现状和第三代核电涂料技术[J].中国涂料,2015,30(3):40-43,58.