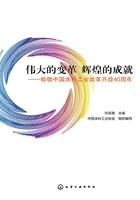
中国集装箱涂料40年
史春晖
集装箱运输是人类社会运输史上的一次重大革命。它把单件杂货成组地装入集装箱,经由水陆空等不同方式联运,将货物从发货方直接运送到收货方手中。集装箱运输可实现“门到门”的服务,从而极大地提高了运输效率,降低成本、减少货损,最大限度地满足货主的要求,其在现代运输中的作用和地位是以往任何一种运输方式不能比拟和替代的。随着经济全球化、贸易全球化和航运业的蓬勃发展,集装箱作为一种安全快捷的运输方式,在海运、陆运和空运以及多式联运中得到广泛的应用。
1 我国集装箱制造行业发展特点
1960年美国标准协会集装箱委员会制定了美国第一个集装箱标准,1961年6月国际标准化组织104技术委员会(ISO TC104)成立,并开始了国际集装箱标准的研究,自1963年至1993年ISO TC104召开了17次年会,其中在1961~1972年的7次年会中确定了集装箱的基本结构,为集装箱制造工业的发展奠定了基础。从1960年开始,欧美、日本、韩国、中国台湾先后成为集装箱制造的中心。
我国的集装箱制造业是从20世纪80年代初期伴随着改革开放的东风逐步成长。最初由中国船舶工业总公司在上海与广州建立了上海船厂集装箱分厂和广州船厂集装箱分厂。之后,国内陆续建立了蛇口集装箱厂、大旺集装箱厂、山海关集装箱厂、武进集装箱厂等,天津、大连、沈阳、辽阳等地也建立了集装箱厂,上海建立了中外合资的远东集装箱厂、华都集装箱厂、太平集装箱厂等。在20世纪我国从事集装箱制造生产的厂家有30余家,集装箱工业蓬勃发展。从最初的几家工厂、年产量几千台标准箱,逐步成长为四大集团、年产量几百万标准箱的行业。目前我国集装箱生产已经成为世界领先行业,无论是生产能力、生产品种还是销售量都是世界第一。并且在集装箱整体创新能力上也是牢牢占据领先位置。我国集装箱制造行业的发展有以下几个特点。
(1)发展速度快是我国集装箱运输发展最显著的特点。我国集装箱运输起步虽晚于世界近20年,却以世界上少有的年均35%的增幅,实现了连续多年雄踞世界第一的跨越式发展。目前我国集装箱生产量占世界总产量超过95%。从图1可以看出,20世纪90年代我国造箱量一直在100万标准箱以下;20世纪最初10年在100万~300万标准箱;而在2010~2017年年产量在300万~500万标准箱,我国沿海港口的集装箱化率已达到或接近国际先进水平,上海港等集装箱港口吞吐量,以及中远、中海等集装箱船队运力都已进入世界前10位。
图1 1991~2017年中国集装箱产量
(2)21世纪后我国集装箱生产集中度不断增加。经过1996年和2009年两次航运业的危机后,从表1中可以看出,进入21世纪后集装箱生产的集中度不断地增加,集装箱生产企业通过不断的优胜劣汰和市场竞争,由20世纪的30余家减少到2018年的中远海东方寰宇集团(DFIC)、中集集团(CIMC)、新华昌集团(CXIC)3家大的集团,使资金更为集中,可以投入更大的人力、物力对集装箱的生产技术、工艺进行改造,从而降低集装箱制造成本、提高集装箱生产效率、改善集装箱生产环境。
表1 2001~2005年集装箱行业集中度
(3)我国集装箱运输有力地支撑了国民经济和对外贸易的发展,也对全球经济的发展发挥了重要作用。如今,高效、便捷的港口集装箱运输体系已经成为外贸运输的“绿色通道”,有力地支撑着我国进出口贸易的高速发展。我国港航业的迅速发展有力地支持了全球航运业的发展。中国现已崛起成为世界上最大的集装箱出口国,占据了全球集装箱吞吐量的1/3。充分说明中国在世界经济和航运业格局中占据重要地位。
2 我国集装箱涂料发展历程
集装箱常年海上运输的特点要求集装箱的各种原材料都要承受严酷的海上运输的考验,也为各种新材料的发展提供了机会和挑战,如1.6mm和2.0mm的耐候钢(CORTEN钢)、高抗压的木地板、高性能的密封胶等,尤其是作为集装箱海上运输防腐中最重要保障的涂料更是如此。20世纪80年代初,我国涂装行业还处在一把除锈锤、一把油漆刷的敲铲、刷涂阶段;涂料产品也主要以天然树脂为主,性能较差。伴随着集装箱工业的快速发展,现在的集装箱涂料已经从最初完全进口,到现在实现全部本土生产,并且在水性涂料和辊涂车间底漆应用方面已经达到世界领先水平。经历了近40年的发展,目前年产几十万吨集装箱涂料,品种覆盖集装箱各个领域。在这40年的时间里,中国的集装箱涂料及涂装产业从无到有、从弱到强,主要经过以下几个阶段。
2.1 集装箱涂料的原装引进(1980~1990年)
在这个时期,我国正处在改革开放的初期,涂料工业的发展极为落后,尤其是海洋重防腐方面。在涂料施工过程中,底材处理以敲铲和化学清洗为主,涂装主要是辊涂和刷涂。涂料产品较为单一,缺少对涂料综合性能的检测和评价方法。为了保证集装箱的防腐质量,涂料产品都是由国外原装进口,这一时期的集装箱涂料和涂装的主要特点有以下几个方面。
2.1.1 新的底材表面处理方法
在集装箱的涂装过程中,引进了“喷砂”底材处理方法和检测标准,如表2所列。这一阶段,底材处理主要分为平板喷砂和整箱喷砂两种方法,均采用表面喷砂清洁度、表面灰尘清洁度和喷砂后粗糙度的评价标准,这些标准在国内以前均没有系统应用或只是简单涉及。在这一时期,引进了大量的检测设备并由涂料供应商对工厂进行标准培训,工厂、工人逐步了解、熟悉这些标准。
表2 集装箱底材处理要求
2.1.2 新的涂装方法
这一时期,新型的高压无空气喷涂涂装设备开始应用(见图2)。高压无空气喷涂具有涂装效率高、涂膜质量好、污染少和可以喷涂高黏度涂料等特点。同时该涂装方法对涂料的流挂性、流平性、贮存稳定性、干燥性等都提出了很高的要求。当时我国国内的涂料产品均不能满足这种涂装方法的要求。

图2 高压无空气喷涂内面
2.1.3 新的涂装节奏
由于集装箱的生产是连续化的生产线生产,每道涂料的涂装间隔只有10~15分钟。在这十几分钟的时间里,工人还要进行预涂、喷涂、修整等多种操作。这种生产节奏对涂料的干燥和复涂时间都有近乎苛刻的要求,并且在实际生产中还存在各种工位的交叉作业,不能由于这种交叉施工而对涂膜成膜状态造成影响。这样对集装箱涂料的厚涂性、干燥性等提出了很高的要求。因而涂料公司要对集装箱涂料树脂的选择、助剂的选择等方面进行大量的筛选试验,使涂料性能可以满足这种快节奏的要求。
2.1.4 严格的涂料性能要求
由于集装箱在海上运输,为了保证集装箱涂膜的防腐性能,国际集装箱标准化委员会建议,集装箱涂料必须通过专门试验的认可后方可使用在集装箱上。表3是当时对集装箱涂料的性能要求。从表3中可以看出来,这都是较为严酷的环境模拟条件,对涂料的防腐性、耐化学品性、耐渗性、耐老化性等长期性能都有极高的要求。
表3 集装箱涂料的性能要求
2.1.5 集装箱涂料配套
集装箱用于运营始于20世纪60年代,所用涂料经历了不同的发展阶段,到了70年代逐步形成富锌(包括无机和环氧)/环氧/氯化橡胶体系,如表4所示。
表4 1980~1990年集装箱涂料配套体系
综上所述,在集装箱引进国内的最初10年里,国内的涂料无法满足集装箱涂装的要求,因此集装箱所用的涂料基本都是从国外原装进口,主要使用的品牌为Hemple、Chougko、Kansai、International、KCC等。
2.2 集装箱涂料逐步国产化的过程(1990~2000年)
涂料国产化的实践工作基本上与集装箱工业进入中国同步展开。1981年广州化工研究所曾研制集装箱涂料,上海船舶研究所和上海开林造漆厂也曾立项开发集装箱涂料,但由于各种原因没有成功,但中国涂料人从没有放弃过这种努力。
这一时期的集装箱制造行业是竞争最为激烈的一个阶段,成本和供货周期成为各箱厂首先考虑的问题。世界各知名集装箱涂料公司纷纷在中国建厂。由于1996年航运业不景气,导致箱厂接单量急剧下降,各箱厂均出现不同程度的亏损。为了维持生存,箱厂之间出现恶性竞争,争相降价。涂料供应商也面临着巨大的成本压力,虽然为了争抢订单,涂料供应商甚至采取包单箱涂料用量的方法。在此情况下,集装箱涂料生产商纷纷扩大产量、降低涂料原料成本和生产成本,并带动了上游原材料供应商纷纷在国内建厂。进口集装箱涂料品牌本土化也带动了国内涂料行业纷纷进军集装箱涂料。
2.2.1 国外供应商在华建厂
在这一阶段,集装箱厂飞速发展,从1993年开始中国成为世界集装箱生产量最大的国家,之后一直保持至今。各集装箱厂之间的竞争也愈加激烈,为了占领市场,抢夺订单,各集装箱厂的成本压力也在不断地增加。为了降低生产成本,各集装箱涂料的供应商纷纷在国内建立合资、独资企业(见表5),通过劳动力成本的降低而降低整体的涂料成本。
表5 集装箱涂料主要供应商在国内建厂时间
2.2.2 集装箱配套体系固定化
由于国内的市场竞争越来越激烈,为了形成稳定的产品质量和产量,环氧磷酸锌、环氧酯、乙烯等涂料品种逐步被集装箱厂弃用。逐步形成了一套固定的涂装配套和施工工艺,各箱东也基本采用同样的品种,只是对每道涂层的涂装膜厚提出不同的要求。集装箱涂料配套体系见表6。
表6 集装箱涂料配套体系
2.2.3 集装箱涂装新技术的应用
在这个阶段,为了节约涂装成本,提高涂装效率,外面漆自动喷涂设备逐步被各箱厂采用。箱厂对高压无空气喷涂的进口压力采用精细化的控制,增加了稳压装置,甚至可以控制每一把枪的压力,以便可以根据不同的部位、不同的枪距调整不同的喷涂压力,使集装箱涂膜更加均匀,涂料的损耗也大幅度降低。
各箱厂根据不同的工艺路线,在外面的自动喷涂设备选择中,采用了往复喷涂和排喷两种形式(见图3)。往复喷涂是最早采用的自动喷涂形式,但由于喷车架运行过程中容易抖动,从而使喷涂涂膜表面较为粗糙,经常出现漆渣、漆绺和不均匀的状况;而排喷则是喷枪不动,集装箱在移动过程中进行喷涂,但由于集装箱运行速度不容易控制均匀,容易造成涂膜不均匀。虽然存在着这样或那样的问题,但自动喷涂的采用使外面漆喷涂工位人员可以减少一半,大大提高了生产效率。

(a)往复喷涂外面漆

(b)排喷外面漆
图3 外面的自动喷涂设备
2.2.4 集装箱涂料环保要求的提高
随着集装箱行业的发展,一些环保课题在这一阶段也逐步提上了议事日程,如:由于氯化橡胶在生产过程中会影响臭氧层,使用丙烯酸树脂的外面漆逐步被各箱东所认可,并开始在某些集装箱上取代了氯化橡胶的面漆。
2.3 溶剂型集装箱涂料成熟阶段(2000~2010年)
在这个时期,中国集装箱的产量一直稳居世界第一,全球90%以上的集装箱出自中国,而集装箱涂料也得到迅猛的发展,并且有关集装箱涂料的标准也逐步国产化。集装箱生产过程中涉及的底材处理、涂膜检验和涂料性能检测等标准基本上都有了对应的国家标准,并且还制定了集装箱涂料行业标准,对集装箱涂料、涂装过程、检验方法等拥有了中国自己的标准。
2.3.1 集装箱产量稳步提高
集装箱产量稳步提高,至2007年达到年产400万标准箱的峰值。集装箱涂料在这段时间里,产品的品种没有大的变动,产品标准逐步细化。集装箱各道涂料的标准逐步统一。富锌涂料、环氧涂料、丙烯酸涂料等都有了各自的标准。而且各涂料公司从单纯的成本降低逐步开始走向差异化竞争的道路,涂料的施工适应性、涂料的涂覆率、涂料的表面状态等都有了大幅度的提升。
2.3.2 集装箱新工艺的采用
在这个阶段成本的竞争依然是各个集装箱厂的主战场,为了降低涂装成本,各个集装箱厂不惜投入大量资金对生产线进行改造,对涂装设备进行更新。
除外面的自动喷涂得到普遍应用外,内面漆的“套喷”工艺也得到推广(见图4),该工艺的采用使内面的涂装时间由原来的3~4分钟,缩短到几十秒左右。该装置采用红外控制开关(见图5)的固定喷涂设备,集装箱在喷涂小车的牵引下,以极快的速度移动,在集装箱移动的过程中完成涂装过程。喷涂方式的改变使涂膜的均匀度大幅度地提高,涂料用量也大幅度地降低,减少了人工喷涂时涂膜质量受工人喷涂水平的影响,降低了工人在高污染环境下的工作时间。但该设备对涂料的流平性和流挂性提出了极高的要求,因而各涂料供应商都对内面漆的配方进行了调整,使用了高性能的流平剂与防流挂剂,使涂料的厚涂性和流平性有了极大的改进。

图4 内面套喷装置

图5 红外控制开关的喷嘴
车间底漆辊涂工艺广泛推广。为了降低锌粉涂料的用量,箱厂在车间底漆施工环节逐步推广采用辊涂方式施工环氧富锌车间底漆。各涂料供应商对环氧富锌车间底漆的干燥性、溶剂的挥发性等方面进行了彻底的改进,使这一工艺得到广泛的应用。通过这种工艺改进,集装箱厂富锌车间底漆的用量降低了约60%。
2.3.3 环境友好型产品得到应用
在此阶段内对大气臭氧层没有破坏作用的丙烯酸面漆彻底取代了氯化橡胶面漆,成为集装箱外面漆的主流。
各大涂料供应商为了适应世界各国对环保要求的提高,纷纷进行水性涂料的开发与试用,如Hemple、Cosco Kansai、Valspar等均进行了数量不等的水性集装箱涂料的涂装应用试验,但由于各种原因均未扩大推广效果,但是这种探索为将来的水性集装箱涂料的广泛使用进行了有益的尝试。
2.4 集装箱涂料全面水性化阶段(2010~2019年)
为了响应国家环境保护的要求,自2018年4月开始,国内的所有标准箱的生产厂家都采用水性涂料进行生产,这是标志性的事件。首先是大大降低了集装箱涂装过程中VOC的排放量,满足了“把青山绿水留给子孙后代”的要求。另一方面,水性涂料在集装箱上的使用,标志着经过近40年的努力,中国水性涂料在工业防腐领域的应用已经站在了世界的前沿。目前集装箱使用的水性涂料都是在中国本土研发出来,并在相当短的时间内做到全行业推广。这是值得中国涂料人骄傲自豪的一件事。
2.4.1 集装箱行业越来越集中
到2018年,全国集装箱行业集团只剩下中集集团、中远海东方寰宇集团和新华昌集团3个大规模的造箱集团。这些造箱厂投入大量的资金对自身的生产线进行改造。完善工厂布局、改进生产工艺、提高生产效率,使箱厂的工艺条件在使用水性涂料生产时,达到溶剂型涂料的产量。各工厂的改造至少要保证以下几个方面。
(1)延长生产线。在保证产量的前提下使集装箱在涂装后有充足的静置和干燥时间,对于水性涂料涂装过程中对干燥时间和温度的要求,也为了套喷工艺的使用,各箱厂设计出模块化的涂装模式,将整个涂装生产线分为主要3个模块,每个模块又分为预热、预涂、套喷、自然干燥、强制干燥和冷却几个工位,根据各生产线的不同布置,采用将纵向移动改为横向平移的方法,使生产线延长了4~5倍,以达到适应水性涂料涂装的要求。
(2)自动喷设备(套喷)彻底取代了手工的喷涂,降低了工人的劳动强度,提高了涂装的稳定性。
(3)增加了对循环水的处理工艺,使废水的排放达到国家的要求。
(4)在长江以北地区的造箱厂改进调漆间环境条件,改善了涂料存储和运输条件(见图6),从而使水性涂料具备冬季施工的条件。

(a)带保温设备的水性涂料仓库

(b)保温车运输水性涂料
图6 涂料存储和运输条件
2.4.2 集装箱水性涂料标准的制定
随着集装箱涂装水性化的呼声越来越高以及前期的水性集装箱涂料的涂装试验工作,制定一套切实可行的集装箱水性涂料标准成为箱东、造箱厂和涂料供应商迫切的实际需要。由中国集装箱行业协会牵头,各涂料供应商、造箱集团和中国船级社等相关单位联合组织制定了有关集装箱水性涂料的相关标准:JH/T E06—2015《集装箱用水性涂料》、JH/T E07—2015《集装箱用水性涂料施工规范》、JH/T E08—2015《集装箱用水性涂料涂膜检验方法和验收标准》。
虽然这些标准中的某些地方依然存在着需要探讨的地方,但是不可否认的是,这些标准使集装箱涂料水性化有了衡量的依据,使集装箱涂料的水性化得到了质的飞跃。该系列标准已经得到了国内外主流箱东的认可,并且在各造箱厂、涂料供应商中得到推广。自该系列标准在2016年颁布后,集装箱水性涂料使用量逐步占据了所有集装箱涂料的90%以上。
2.4.3 集装箱水性涂料的日臻完善
由于水有较大的蒸发潜热,水性涂料有较强的表面张力,以及一定的触变性,因而水性涂料对涂装及干燥条件的要求很高。经过各涂料供应商的努力,对水性涂膜性能影响较大的针孔、膜内泡、附着力差、初期耐水性差等问题都得到了很好的解决,现在集装箱水性涂料各方面性能已经日臻完善。
2.5 集装箱水性涂料的发展展望
2.5.1 更加完善的性能
随着中国“一带一路”倡议的实施,已经在某种意义上改变了集装箱的性质,原来在海上航行的集装箱,可能会长期在穿越沙漠、极寒地区的铁轨上运输;原来装在船舶货仓内的煤炭、化工原料等有可能会装在集装箱内进行内陆运输,因而箱东对集装箱载货的通用性和普遍性都提出了新的要求。如在国内某箱东使用集装箱运输碱性物料,由于包装袋破损,使集装箱内面漆成片脱落,对箱东造成了很大的损失。
所以箱东对集装箱水性涂膜的性能提出了新的要求,如提高内面漆的耐化学性使集装箱内面涂膜在受到一定化学介质污染时不会产生大的破坏;如提高内面涂膜的耐磨性,减少箱东在承运颗粒物料时对涂膜的损坏;提高外面漆的抗风沙性和耐阳光曝晒等性能,使集装箱在经过大风沙和阳光炙烤后仍能保持良好的外观。
2.5.2 更加环保的要求
虽然现在集装箱水性涂料得到大面积的应用,但是集装箱水性涂料仍然存在着一些影响环境的因素,如由于在涂装过程中产生的漆雾,经后期环保处理后也会产生固体废料,而且对固体废料的处理也是较大的资金投入。如何解决漆雾固体废料,是集装箱厂和涂料供应商需要考虑的问题。现在已经有供应商提出了粉末涂料、静电喷涂等解决方案。无论采用何种方案,随着环保要求越来越严格和固体废料的处理成本压力的增加,这个问题终将得到解决。
集装箱涂料工业随着改革开放大潮,在中国已经走过40年的历程。从无到有、从落后到领先,始终不断前行。集装箱涂料行业也必将随着中国的发展继续前行。