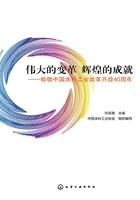
木木用涂料40年
王鹏
1 木用涂料的黄金发展期
新中国成立后至1980年左右,历经几十载的艰辛发展,中国木用涂料经历了从无至有、由少变多的过程。在这期间,国内各大涂料厂家,对当时世界领先新品种、新技术均有研究、生产,但受材料、生产、环境等诸多因素的局限性影响,国内木用涂料在量与质两方面,终未能有大的突破。
中国木用涂料真正的黄金发展期,是近40年,在改革开放大潮的涌动下,伴随着中国经济的腾飞,得以极速发展、壮大!
这一时期,大致分为3个阶段:
① 1980~2000年,低点起步阶段;
② 2000~2010年,高速发展阶段;
③ 2010至今,全面提升阶段。
1.1 1990~2000年,低点起步
1980年之后,改革开放号角吹响,涂料行业也闻风而动,由于珠三角地区开始有外资家具厂,在木用涂料及涂装方面均可接触到很多外来信息,受此启发,珠三角有涂料相关企业及个人开始在国内进行新产品、新技术、新工艺的研究开发,并通过各种渠道,进口最新的涂料原材料,零星地生产一些用于家具的涂料。现在看来,虽然这只是探索阶段,但国内木用涂料行业的发展,就这样打开了大门,星星火种,就此点燃。
时至1990年前后,凭借改革春风浪潮,大批民营涂料、家具企业相继成立,同时,随着家具行业的兴盛,引发了木用涂料的快速发展,虽然各涂料企业起点较低,却逐渐形成气候。
木用涂料发展初期,固化剂、树脂、助剂等几乎所有的原料均需进口,但这一现象仅持续了一两年,之后,国内树脂及固化剂合成技术便迎头赶上,涂料主体原料迅速国产化。技术进步方面主要体现在:创新地采用价格低廉、配方成熟的醇酸树脂作为双组分体系的多元醇,固化剂配方及合成工艺的改进。这些技术进步为木用涂料的快速起步创造了极其有利的条件。
随着行业发展提速,涂料品种逐渐丰富,从硝基(NC)涂料等产品开始,在一两年内快速升级至双组分聚氨酯(PU)涂料,同时开发了不饱和聚酯(UPE)涂料体系。这一时期,解决了PU涂料可使用时间短的难题,并快速完成NC、PU、UPE木器涂料的推广、普及。
期间也曾走入误区,早年曾开发出种类繁多的美术涂料,一度追求家具表面涂饰所谓的美术效果,被市场错误地认为这便是木用涂料的主流,而忽略了木用涂料与涂装的真正意义。所幸,这种情况很快得以纠正。
家具涂料厂与家具厂就是对孪生子,早期的家具厂大多仓促成立,在制造家具,特别是对涂料知识、涂装工艺方面几近白纸。一方面靠涂料厂的售后应用服务进行启蒙,另一方面也向在内地建厂的外资、港台家具厂全面地模仿、学习,使本土家具厂的涂装工艺、技术水平得以迅速提升,从手刷到喷涂应用,再到喷房的普及仅用了一到两年时间而已,反之,也同样促进了涂料配方、制漆工艺、产品配套、应用技术的进步。
随着NC、PU、UPE木器涂料质与量的高速增长,产品开始划分系列,涂料生产工艺从无序变得有序,涂装工艺从无理变得有理。从开始的粗制滥造、全无章法,发展到讲究配套、讲求原理。10年过去,木用涂料制造、涂装应用在“品种专业化、产品系列化、工艺规范化、质量标准化”几方面有了长足的进步。
由于创业门槛低、技术含量不高、厂房易建易得等原因,使得木用涂料厂群起,仅顺德就有几百上千家不同规模的木用涂料厂。
至2000年,我国木用涂料总产量已达到70万吨左右,相当于当时欧洲木用涂料的总需求量。
1.2 2000~2010年,高速发展(主要体现为量的发展)
2000~2010年,木用涂料进入高速发展阶段,包括原料选用、配方确定、涂料生产、产品检验、涂装应用、设计到家具涂装效果的判定、家具终端消费者的评价以及售后跟踪,整条产业链得到全面、快速的提升。
木用涂料品种已基本发展齐全,产品检验严格、规范,质量稳定。售后服务、应用工艺水平有了极大的提升,此时除一线的高端产品外,我国木用涂料的生产工艺、产品品质和木家具涂装工艺、整体效果,在主流上与国际水平越趋接近。行业内产品及市场细分化,各企业发展出符合自身特点的专攻领域。销售网络基本成型,供求伙伴关系稳定,并且涂装设备升级、更新换代。这些因素造就了木用涂料高速发展的10年,这种发展速度是中国涂料界乃至世界涂料行业中所少有的。
木用涂料市场的发展,首先着力于各省会城市,到本阶段中期,产品普及至三线城市后,产、销量便有了突飞猛进的增长。
高速发展同时促进了涂料技术的进步,国产固化剂游离TDI含量逐步降低,国产树脂的合成工艺逐渐进步、成熟,产量逐年增长。同时,进口助剂、颜料、高档树脂、固化剂以及溶剂在我国木用涂料中、高档产品及关键节点的发展上,也发挥了重要作用。
UV在木器涂料的配方技术、施工应用及涂装设备在这一时期也得到较大发展与普及。
至2009年年底,我国木用涂料总产量已达到120万吨左右。
1.3 2010年至今,全面提升(主要体现在质的提升)
由于市场相对稳定、产品成熟、工艺合理、服务到位、资金充足、税务正规化,整个产业链趋于成熟。因此,各企业对自身发展的定位、规划明确,不再一味追求业绩的增长,而是更多地关注企业文化、品牌建设、主攻领域、自主创新以及环保建设的发展,行业的整体发展方向明确,实施可持续发展战略。与此同时,各涂料企业重视并实抓环保,结合国家环保政策、法规,完善企业环保设施,大力发展环境友好型涂料,减少VOC的排放。
优胜劣汰的市场规则在这段时间里使木用涂料领域的企业经历了最大的重整过程,市场重组的结果,使得十多个中大型企业跃升行业前列,表现特点大致为:市场占有率大增、产品线特点明显、在市场细分中得益、产业链向上下游有效延伸、企业自身正规化、规模化显现的效益非常明显。
2 水性木用涂料
不得不提的便是20年前已起步,充分酝酿并准备了10年的水性木器涂料,无论从产品质量或应用技术方面都有了质的飞跃,并得到全面加速发展。2015年,号称“史上最严”的新环保法出台,同年,开始对涂料征收消费税,同时,各地区相继出台地方环保法规,在环保与政策法规双重压力下,各家具、涂料企业不约而同地吹响了应用、推广水性木用涂料的总攻冲锋号。
随着市场打开,由家具、涂料标杆企业牵头发力,水性木用涂料在家具市场逐渐活跃起来。相应地,随着产量的提高,自上游原料开始至终端消费体验,整个产业链均获得无限发展和进步的空间。
可以说,在水性木用涂料近两三年的发展中,使涂料上下游的供求关系有了颠覆性的巨变。上游从天价进口原料难觅至亲民国产原料遍地开花,下游从被动观望变为主动配合,水性木用涂料已成为产业链中不可或缺的一个关键结点。与此同时,水性木用涂料从原料种类、原料品质、制漆工艺、涂装工艺,涂装设备、干燥设备等方面均有突飞猛进的发展。
原料从最初比较单一的丙烯酸乳液(AC)发展到后来的核壳结构丙烯酸乳液、改性丙烯酸乳液、聚氨酯分散体(PUD)、聚氨酯-丙烯酸共聚体(PUA)、羟基丙烯酸乳液以及用于水性UV的各种树脂,满足了研发不同性能产品的需求。
水性木用涂料产品种类现在已形成主流清晰、加强配套、功能明确、应用成熟的特点。主流产品从初期的单组分水性木器涂料发展到现在的水性双组分聚氨酯涂料、水性UV涂料。各种配套产品,如各种封闭底漆、各种着色、修色用辅料都应运而生,有了很大的进步。
同时,随着产业链转型逐步深化,位于产业链中后段的涂装、干燥设备也在市场巨大的推动力下不断提升、进步,其中典型的是各种适用于水性木用涂料的涂装设备,如往复喷涂机、静电旋碟喷涂机、往复式静电旋杯喷涂机、机械臂+静电旋杯喷涂机等。无溶剂的粉末涂料也在改革的涂装线上成功地用于木器涂装。
干燥设备(冷红外隧道、热风风道隧道、微波干燥隧道、空气能除湿加热烘干房、立式多层烘干塔等),以及设备组合,如:静电+热风烘干隧道、往复机+微波烘干隧道、往复机+立式多层烘干塔等,各类设备的应用、普及,比较有效地解决了水性涂料在木家具上的施工、干燥难题,水性木器涂料的涂装工艺、涂装设备、干燥工艺以打破传统理念的姿态出现并取得令人信服的实际效果。
3 木用涂料产品的发展
至今为止,木用涂料共发展出硝基(NC)、溶剂型聚氨酯(PU)、不饱和聚酯(UPE)、酸固化(AC)、光固化(UV)、水性(WB)涂料6大门类,NC、PU、UPE木器涂料在过去的40年间得以广泛应用,在总量中占绝对大比例还会延续一段不短的时间。UV木器涂料在2000~2010年间得以迅速发展壮大,而2010以后,特别是2015年至今,水性木用涂料异军突起并显现出强劲的发展态势,以双组分、UV为主的水性木用涂料,以每年极高的增长率逐步引领着涂料市场。
但是,水性木用涂料仍存在问题:与溶剂型同类产品比较,硬度、丰满度仍需提高;高光产品前景不错但难度不低;反而溶剂型产品的高固体方向仍然有其生命力;对水性木用涂料、涂装中封闭的重要性认识不足,并没能真正解决封闭问题;水性木用涂料的涂装过程特别是干燥成膜过程,仍有很多问题制约着它的市场表现。
4 木用涂料最新相关涂装、干燥设备
木用涂料最新相关涂装、干燥设备见表1。
表1 木用涂料最新相关涂装、干燥设备一览表
5 木用涂料产业部分数据
20世纪90年代初期至中期,木用涂料生产企业主要集中在珠三角地区,后逐渐向长三角及华北地区发展,到90年代末期,开始向全国各区域扩散。近年来,随着国家政策法规调整,化工行业入园,企业由分散向园区集中。如今全国木用涂料生产企业总数超过600家,前10位企业产量占总量比达到49%,前30位企业产量占总量比超过73%。虽然外资企业也占据了一定的市场份额,但民营企业一直是中国木器涂料行业的绝对主力军。
截至2010年,国内各类木用涂料产品市场占比:PU涂料约为60%、NC涂料约为21%、UPE涂料约为12%、UV涂料约为5%、水性涂料约为2%,AC涂料由于其危害性逐渐淡出市场,NC涂料已逐渐下滑,PU涂料仍处于主导地位,UPE涂料仍需提升,UV、水性木器涂料还处于起步阶段。
截至2017年,国内各类木用涂料产品市场占比:PU涂料约为60%、NC涂料约为12%、UPE涂料约为12%、UV涂料约为8%、水性涂料约为8%;PU涂料仍处于主导地位,NC涂料的生产逐步转向东南亚区域,UPE涂料提升空间不大,UV涂料逐渐改善,水性木器涂料将以高速发展的态势,逐步提升占有率。
至2017年,中国木用涂料总产量约为260万吨以上。
6 木用涂料行业特点
中国木用涂料,在起步发展、生产规模、市场流通这几个关键点上,均体现出“民先官后、民大官小”的鲜明特点。民营企业先发展、行业内的本土代表企业均为民营企业,市场化营销网络建立最早、最健全、最有效,这几个特点,在国内各大门类涂料中是唯一一个。
木用涂料领域中的本土企业、民族品牌得到充分的发展壮大,40年的发育结果,使国内木用涂料绝大部分产品及市场都由民营企业提供及掌控,避免了国内木用涂料以进口产品为主的被动局面的形成。
木用涂料领域中的民营企业,能够生存发展至今的,其中相当一部分进入了企业发展的“瓶颈”阶段,这些企业,从产品开发、生产工艺、营销管理、环保安全等方面都存在很多亟待解决的问题,而这一切都受到企业文化、管理能力以及企业可持续发展水平的制约。与其他门类的企业相比,木用涂料领域中此类问题比较突出。
木用涂料的产销量在行业中属第二三大门类,在中国涂料产业构成中举足轻重;整体发展水平与国际先进水平相去不远。
在降低VOC排放、部分溶剂型涂料向水性涂料过渡,发展高固体分、无溶剂涂料等环保问题上,其迫切性、复杂性、难度居于所有涂料门类之首。
特别值得一提的是,在未来涂料行业的发展中,环保始终会是第一主题,涂料水性化、低VOC化必定是市场的主流思想,但由于水性木器涂料的材料特殊性,降低了VOC的同时,也使得性能有所牺牲,在行业发展的助推下,相信不久的将来会有革命性的突破。
致谢:本文的资料收集撰写得到了行业资深专家叶汉慈、陈寿生的大力支持。特此表示感谢!