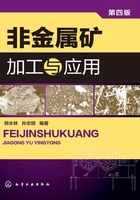
3.1.3 加工技术
(1)选矿提纯 全球方解石资源较丰富,CaCO3含量≥97%的优质方解石资源量也较大,因此,目前工业上一般不对方解石进行机械选矿加工,只进行简单的洗矿和拣选,包括人工和光电机械拣选。
目前方解石的加工主要是粉碎、分级和表面改性。
(2)粉碎、分级 粉碎、分级的目的是加工出满足应用领域细度要求的重质碳酸钙产品。工艺流程和设备依产品细度要求而定,对于400目以下的产品,一般工艺流程是:原矿→破碎→磨矿(粉)→(分级)。主要设备有雷蒙磨(悬辊磨)、旋转筒式球磨机、辊磨机(立式磨、压辊磨、环辊磨等)、旋磨机、振动磨等。大多采用干式开路式粉碎工艺。
(3)超细粉碎与精细分级 国内外方解石超细粉碎工艺主要有干法和湿法两种。干法工艺一般用于生产d97≥3~5μm的产品,湿法工艺一般用于生产d97≤3~5μm(d90≤2μm)的产品。
工业上采用的干法超细粉碎设备主要包括旋转筒式球磨机、辊磨机、搅拌球磨机、高速机械冲击磨机、振动球磨机、分级研磨机等。除具有自行分级功能的超细磨以外,为确保产品细度和粒度分布的要求,实际生产线上一般均配置精细分级设备,配置方式有内置式和外置式两种,内置式均为内闭路生产方式,外置式可以有开路和闭路两种生产方式。开路式通过分级机分级后生产两种不同细度的产品,闭路式只生产一种超细粉体。干法生产线常配的分级机是离心或涡轮式空气或气流分级机。图3-2~图3-4所示是常见的球磨机、环辊磨和立式(辊)磨干式超细粉碎工艺流程。国内目前主要的干法超细粉碎工艺是环辊磨-分级机、立式磨-分级机以及球磨机-分级机超细粉碎工艺,其中环辊磨和立式磨内置分级机,而且不使用磨矿介质,因此,工艺和操作较简单。

图3-2 球磨机干式超细粉碎工艺
1—料仓;2—球磨机;3—提升机;4—涡轮式分级机;5—除尘器;6—多轮分级机;7—成品仓

图3-3 环辊磨干式超细粉碎工艺系统
1—原料仓;2—环辊磨机;3—产品收集器;4—风机;5—控制柜

图3-4 LUM立式磨超细粉碎工艺系统
1—原料仓;2—提升机;3—给料机;4—立磨;5,8—布袋集料器;6—中间仓;7—精细分级机; 9—超细产品仓
湿式超细粉碎设备主要是湿式搅拌球磨机和砂磨机。主要生产造纸涂料或颜料级产品和高档涂料的填料和颜料。图3-5所示是三段连续式搅拌磨超细粉碎工艺流程。该工艺主要由三级湿式搅拌磨及相应的储罐和泵组成。原料经调浆筒1添加水和分散剂调成一定浓度或固液比的浆料后给入储浆罐2,通过储浆罐2泵入搅拌磨3中进行研磨。经搅拌磨3研磨后的料浆经分离研磨介质后给入储浆罐4,通过储浆罐4泵入搅拌磨5中进行第二次(段)研磨;第二次研磨后的料浆经分离研磨介质后进入储浆筒6,然后泵入搅拌磨7中进行第三次(段)研磨;经第三次研磨后的料浆进入储浆罐8,并用磁选机除去铁质污染及含铁杂质。如果该生产线建在靠近用户或离用户较近的地点,可直接用管道或料罐送给用户。由于设备的日趋大型化和控制技术的进步,目前的湿法生产线已很少采用三台搅拌磨连续研磨,大多采用1~2段(1~2台大型搅拌磨)连续研磨工艺。砂磨机超细研磨生产工艺与搅拌基本相同,只是用砂磨机代替搅拌磨而已。

图3-5 三段连续湿式搅拌磨超细粉碎工艺流程
1—调浆筒;2,4,8—储浆罐;3—搅拌磨Ⅰ;5—搅拌磨Ⅱ;6—储浆筒;7—搅拌磨Ⅲ;9—磁选机;10—成品储槽;11—介质分离筛
(4)表面改性 用方解石等碳酸盐矿石加工的重质碳酸钙是目前有机高聚物基材料中用量最大的无机填料。但是,未经表面处理的重质碳酸钙与高聚物的相容性较差,难以在高聚物基料中均匀分散,从而造成复合材料的界面缺陷,降低填充材料的机械强度。随着用量的增加,这些缺点更加明显。因此,为了改进重质碳酸钙填料的应用性能,要对其进行表面改性处理,提高其与高聚物基料的相容性或亲和性。
重质碳酸钙的表面改性主要是通过添加有机改性剂对其进行表面改性。采用的表面改性剂主要是硬脂酸(盐)、钛酸酯偶联剂、铝酸酯偶联剂、无规聚丙烯、聚乙烯蜡及其他聚合物等。根据所用的表面改性剂,目前重质碳酸钙的表面改性方法可以分为脂肪酸及其盐改性、偶联剂改性和聚合物改性。
表面改性要借助设备来进行。常用的表面改性设备是SLG型连续粉体表面改性机以及涡流磨和流态化改性机。
重质碳酸钙的一般有机改性工艺流程如图3-6所示。碳酸钙经干燥后(水分含量较低的干粉也可不进行干燥)给入表面改性机,同时加入一定量的表面改性剂,作用一定时间后即得表面有机改性后的活性重质碳酸钙。

图3-6 重质碳酸钙表面改性工艺流程
影响表面有机改性效果的主要因素是:表面改性剂的品种、用量和用法(即表面改性剂配方);表面改性温度、停留时间(即表面改性工艺);表面改性剂和物料的分散程度(影响改性剂与颗粒作用的均匀性和颗粒的团聚)等。其中,表面改性剂和物料的分散程度主要取决于表面改性机。
表面改性剂配方是重质碳酸钙表面改性的关键技术。选择表面改性剂配方首先要考虑改性重质碳酸钙的应用体系,其次要考虑重质碳酸钙的粒度大小、分布特性及比表面积,还要考虑表面改性剂的成本。
配方确定以后,还要选择好表面改性设备。好的表面改性设备应具备以下基本工艺特性:对粉体及表面改性剂的分散性好、粉体与表面改性剂的接触或作用机会均等、改性温度可调、单位产品能耗低、无粉尘污染、操作简便、运行平稳等。以下对重质碳酸钙的主要表面改性方法进行介绍。
①脂肪酸及其盐改性 硬脂酸及其盐是碳酸钙最常用的有机表面改性剂。其改性工艺可以采用干法,也可以采用湿法。一般湿法工艺要使用硬脂酸盐,如硬脂酸钠。干法改性时,先将碳酸钙进行干燥(如果碳酸钙的水分含量小于1%可以不进行干燥),然后加入计量和配制好的硬脂酸在表面改性机中完成碳酸钙粉体的表面改性。采用SLG型粉体表面改性机和涡旋磨等连续式粉体表面设备时,物料和表面改性剂是连续同步给入的,用量依粉体的粒度大小或比表面积而定,一般为碳酸钙质量的0.6%~1.5%;用高速混合机及其他间歇式改性机进行表面包覆改性时,首先将计量和配制好的物料和硬脂酸一并加入改性机中,搅拌混合15~60min后出料包装。改性时也可适量加入其他助剂。
湿法改性是在水溶液中进行表面改性。一般工艺过程是先将硬脂酸皂化,然后加入碳酸钙浆料中,经过一定时间的搅拌反应后,进行过滤和干燥。碳酸钙在液相中的分散比在气相中的分散较为容易,因此,在液相中碳酸钙颗粒与表面改性剂分子的作用更均匀。当碳酸钙颗粒吸附了硬脂酸盐后,表面能降低,即使经压滤、干燥后形成二次粒子,其团聚结合力减弱,用较小的剪切力即可将其重新分散。
湿法表面改性常用于湿法研磨的超细重质碳酸钙及轻质碳酸钙的表面改性。
用脂肪酸(盐)改性后的活性碳酸钙主要应用于填充塑料、电缆材料、胶黏剂、油墨、涂料等。
②偶联剂改性 用于碳酸钙表面改性的偶联剂主要是钛酸酯偶联剂和铝酸酯偶联剂。改性工艺与设备与用硬脂酸改性相同。
用钛酸酯偶联剂处理后的碳酸钙,与聚合物分子有较好的相容性。同时,由于钛酸酯偶联剂能在碳酸钙分子和聚合物分子之间形成分子架桥,增强了有机高聚物或树脂与碳酸钙之间的作用,可显著提高热塑料复合材料等的力学性能,如冲击强度、拉伸强度、弯曲强度以及伸长率等。用钛酸酯偶联剂表面包覆改性的碳酸钙和未处理的碳酸钙填料相比,某些性能有显著改善。
铝酸酯偶联剂已广泛应用于碳酸钙的表面处理和填充塑料制品,如PVC、PP、PE及填充母粒等制品的加工中。研究表明,经铝酸酯处理后的轻质碳酸钙可使CaCO3/液体石蜡混合体系的黏度显著下降,可显著提高CaCO3/PP(聚丙烯)共混体系的力学性能,如冲击强度、韧性等。
经偶联剂改性后的重质碳酸钙,除了用作硬质的聚氯乙烯的功能填料外,还广泛用作胶黏剂、油墨、涂料等的填料和颜料。
③聚合物改性 采用聚合物对碳酸钙进行表面改性,可以改进碳酸钙在有机或无机相(体系)中的稳定性。这些聚合物包括低聚物、高聚物和水溶性高分子,如聚甲基丙烯酸甲酯(PMMA)、聚乙二醇、聚乙烯醇、聚马来酸、聚丙烯酸、聚丙烯、聚乙烯等。
聚合物表面包覆改性碳酸钙的工艺可分为两种,一是先将聚合物单体吸附在碳酸钙表面,然后引发其聚合,从而在其表面形成聚合物包覆层;二是将聚合物溶解在适当溶剂中,然后对碳酸钙进行表面改性,当聚合物逐渐吸附在碳酸钙颗粒表面上时排除溶剂形成包膜。这些聚合物定向吸附在碳酸钙颗粒表面,形成物理、化学吸附层,可阻止碳酸钙粒子团聚,使碳酸钙在应用中具有较好的分散稳定性。
母料填料(master batch pellet)是一种新型塑料填料。方法是按一定比例将碳酸钙填料和树脂母料混合,并添加一些表面活性剂,经过高剪切混合挤出、切粒而制成母粒填料。这种母料填料具有较好的分散性,与树脂结合力强,熔融均匀,添加量高,机械磨损小,应用方便。因此,广泛应用于打包带、编织袋、聚乙烯中空制品(管材、容器等)、薄膜、聚烯烃注射器。根据基体树脂的不同,常用母料填料主要有无规聚丙烯碳酸钙母粒(APP母料)、聚乙烯蜡碳酸钙母粒和树脂碳酸钙母粒填料等几种。
APP母料是以重质碳酸钙和无规聚丙烯为基本原料,以一定比例配制,通过密炼、开炼、造粒生产。碳酸钙在和无规聚丙烯复合前必须经表面有机改性。无规聚丙烯和活性碳酸钙的配比一般为(1∶3)~(1∶10)。为了改善无规聚丙烯的加工成型性能,一般成型时加入部分等规聚丙烯或部分聚乙烯。无规聚丙烯和活性碳酸钙的配比影响APP母料的产品质量。
用聚乙烯蜡或聚乙烯代替无规聚丙烯作为基料与活性碳酸钙填充复合,即可制备聚乙烯蜡碳酸钙母料填料和聚乙烯碳酸钙母料填料。