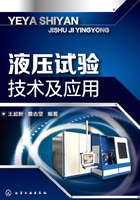
2.3.5 基于WinCC的液压缸CAT系统
利用西门子公司的组态软件WinCC5.1和可编程控制器S7-300配合组建液压缸试验台的测控系统,应用效果较好。对于动态指标要求不高的液压CAT系统,都可采用上述模式,这有利于缩短研发周期,提高可靠性和可维护性。
(1)液压缸试验台液压系统
图2-63所示为按照液压缸测试国家标准GB/T 1562设计的试验台液压系统原理。该系统能完成试运行、全行程、内泄漏、外泄漏、启动压力特性、耐压试验、耐久性试验等各出厂检验项目的测试。

图2-63 液压缸试验台液压系统原理
1—加热器;2—液位继电器;3—油箱;4—温度传感器;5—空气过滤器;6—落地式双筒过滤器;7—冷却器;8—冷却水阀;9,10,15,24,26,30,31,41—截止阀;11,16—连接件;12,17—手动变量液压泵;13,18—溢流阀;14,19—单向阀;20—比例溢流阀;21—比例放大器;22—压力继电器;23,32,35,36,39—过滤器;25—蓄能器;27—M型电液换向阀;28—电磁换向阀;29,33,34,37,38—压力传感器;40—液压缸;42—双单向节流阀;43—恒力收绳位移传感器
该系统采用手动变量液压泵12和17供油,当测试小缸时,只需启动一台变量泵,并将变量泵的流量调整到与被试缸所需流量相适应;当测试大缸时,采用双泵联合供油,提供最大流量为200L/min。溢流阀13和18安装在两台液压泵出口,作安全阀用。系统工作压力由比例溢流阀20进行精确控制,最高可达31.5MPa,比例压力控制便于计算机自动测试液压缸启动压力特性曲线。电液换向阀27中位设计成M型,主要用于液压泵空载启动及工作中卸荷,左右两位用于实现被试液压缸运动方向的换向。电磁换向阀28用于更换被试液压缸时,卸除A、B腔中的残余高压。双单向节流阀42用于实现被试缸精确的流量调整。为了避免被试液压缸内大量残液污染系统,减少过滤器更换频率,在总回油路上设置了一个落地式双筒过滤器6。为保障系统油温符合标准要求,设置有冷却水阀8、冷却器7、加热器1和温度传感器4。系统还设置了5个压力传感器:压力传感器29用来检测泵出口压力;压力传感器34和37用来检测被试液压缸A、B腔压力,用于耐压试验;压力传感器33和38为低压、高精度,用来检测被试液压缸A、B腔启动压力,可提高测试精度。恒力收绳位移传感器43用于液压缸全行程自动检测。
(2)液压缸试验台测控系统
①测控系统硬件 常规液压缸试验台由控制面板、操作台、继电接触器控制柜或可编程控制器、传感器、计算机、数据采集卡和高级语言开发的测试程序等构成测控系统。而基于组态软件WinCC5.1的测控系统取消了控制面板、操作台、继电接触器控制柜、数据采集卡、测试程序,直接用组态软件和可编程控制器、传感器组成,具有友好的人机接口和较高的稳定性。测控系统硬件组成框图如图2-64所示:所有传感器的模拟量信号全部进入可编程控制器(PLC)的AI模块;开关量监测信号进入PLC的DI模块;模拟控制信号由PLC的AO模块输出;开关量控制信号由PLC的DO模块输出;PLC与计算机通过MPI接口模块进行数据交换,实现对试验台的各参数进行检测、控制和报警。检测人员可通过由组态软件WinCC5.1开发的人机接口(HMI)对测试系统进行干预。

图2-64 测控系统硬件组成框图
②测控系统软件 软件开发分为PLC程序和计算机程序两部分。PLC程序采用模块化梯形图方式进行编写,每个子功能模块(FB)完成某一特定的测控功能,所有的FB由组织块(OBI)统一调用,PLC采集到的现场数据存放在数据块(DB10)中的相应位置,接收到的指令数据也保存在DB10中的相应位置,DB10是PLC与现场及计算机进行数据交换的中转站,其数据根据实际情况不停刷新。计算机程序是利用组态软件WinCC5.1进行开发的,它分为显示区域、控制区域、报警区域、绘图区域、操作区域等几个部分。显示区域主要用来实时显示系统各运行参数;控制区域是对系统状态进行操作的窗口,测试人员可用鼠标对电机、阀、加热、冷却、压力等进行手动控制;报警区域用来对系统各运行参数进行安全监测,一旦发现异常,马上启动声光报警系统,同时屏幕上显示提示语言;绘图区域可实时测绘液压缸启动压力曲线及各运行参数的趋势图;操作区域是测试人员对试验进程及数据进行控制处理的窗口。软件系统通过西门子公司的接口卡CP561l与PLC的DB10进行实时数据交换,对HMI进行实时刷新。
组态软件WinCC5.1已经将很多常用功能做成了ActiveX控件,在程序开发时可以直接利用这些控件,快速搭建出测试软件系统,避免了自己编写代码的繁重劳动,提高了可靠性,同时也节约了时间,缩短了开发周期。
基于WinCC的液压缸CAT系统测试精度达到B级。系统操作简便、工作可靠。