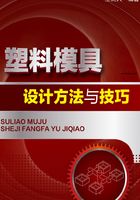
1.2 塑料的成型工艺性能
模具设计必须掌握所用塑料的成型特性及成型时的工艺特性。
1.2.1 热固性塑料的工艺特性
常用热固性塑料有酚醛、氨基(脲醛、三聚氰胺)塑料等。主要用于压塑、挤塑、注射成型;环氧树脂塑料和硅铜塑料等主要作为低压挤塑封装电子元件及浇注成型等用。
(1)成型收缩性
塑件从模具中取出冷却到室温后,发生尺寸收缩,这种性能称为收缩性。塑件的收缩与树脂本身的热胀冷缩有关,同时也取决于各种成型因素,所以成型后塑件的收缩应称为成型收缩。
①成型收缩的形式及特点 塑件成型收缩主要表现在以下几个方面;
a.塑件线性尺寸的收缩。由于热胀冷缩,塑件脱模时的弹性恢复、塑性变形等因素导致塑件脱模冷却到室温后其尺寸缩小,因此,在设计模具型腔或型芯时必须考虑并予以补偿。
b.塑件收缩方向性。成型时塑料分子按方向排列,使塑件呈现各向异性,沿料流方向(平行方向)则收缩大、强度高,沿料流直角方向(垂直方向)则收缩小、强度低。另外,因塑件各部位密度及填料分布不匀,也会引起塑件收缩的不均匀,这使塑件容易发生翘曲、变形、裂纹,尤其在挤塑及注射成型时其方向性更为明显。因此,在设计模具时应考虑收缩方向性,按塑件形状、料流方向选取收缩率。
c.塑件的后收缩。塑件成型时,由于受各种成型因素(成型压力、剪切应力、模温不匀、硬化不匀、各向异性、密度不匀、填料分布不匀、塑性变形等)的影响,会引起一系列的应力作用,在黏流态时不能全部消失,塑件在应力状态下成型时存在残余应力。当脱模后应力趋向平衡和储存条件的影响,使残余应力发生变化而使塑件发生再收缩称为后收缩。一般塑件在脱模后10h内变化最大,24h后基本定型,但最后稳定要经30~60d。通常热固性塑料的后收缩比热塑性塑料小,挤塑及注射成型的比压塑成型的大。
d.塑件后处理收缩。由于塑件按其性能及工艺要求,在成型后需进行热处理,热处理后亦会导致塑件尺寸发生变化,称为后处理收缩。因此,在模具设计时,对高精度的塑件则应考虑后收缩及后处理收缩的误差并予以补偿。
②收缩率计算 塑件成型收缩值可用收缩率来表示,如式(1-1)及式(1-2)所示。
(1-1)
(1-2)
式中 Sp——实际收缩率, %;
S——计算收缩率, %;
a——塑件在成型温度时的单向尺寸,mm;
b——塑件在室温下单向的尺寸,mm;
c——模具在室温下的单向尺寸,mm。
实际收缩率表示塑件实际所发生的收缩,因其值与计算收缩率相差很小,所以模具设计时以计算收缩率S为设计参数来设计型腔及型芯尺寸。
③影响收缩率变化的因素 在实际成型时不仅不同品种塑料其收缩率各不相同,而且不同批次的同品种塑料或同一塑件的不同部位其收缩值也经常不同。影响收缩率变化的主要因素如下:
a.塑料品种。各种塑料都有其各自的收缩范围,同种塑料由于填料、分子量及配比等不同,则其收缩率及各向异性也各不相同。
b.塑件特性。塑件的形状、尺寸、壁厚、有无嵌件、嵌件的数量及布局对收缩率都有很大的影响。
c.模具结构。模具的分型面及加压方向,浇注系统的形式、布局及尺寸对收缩率及方向性影响也较大,尤其在挤塑及注射成型时更为明显。
d.成型工艺。挤塑和注射成型工艺一般收缩率较大,方向性明显。预热情况、成型温度、成型压力、保压时间、填装料形式及硬化均匀性对收缩率及方向性均有影响。
综上所述,模具设计时应根据各种塑料的收缩率范围,并按塑件形状、尺寸、壁厚、有无嵌件情况、分型面及加压成型方向、模具结构、进料口形式、尺寸和位置、成型工艺等诸因素综合来考虑选取收缩率数值。
另外,成型收缩还受各成型因素的影响,但主要取决于塑料品种、塑件形状及尺寸,所以成型时调整各项成型条件也能够适当地改变塑件的收缩情况。
(2)流动性
塑料在一定温度与压力下填充型腔的能力称为流动性。流动性是模具设计时必须考虑的一个重要工艺参数。流动性大易造成溢料过多,填充型腔不密实,塑料组织疏松,树脂、助剂分头聚积,易粘模、脱模及清理困难,硬化过早等弊端。但流动性小则填充不足,不易成型,成型压力大。所以选用塑料的流动性必须与塑件要求、成型工艺及成型条件相适应。模具设计时应根据流动性能来考虑浇注系统、分型面及进料方向等。热固性塑料流动性通常以拉西格流动性(以mm计)来表示,数值大则流动性好。每一品种的塑料通常分三个不同等级的流动性,以供不同塑件及成型工艺选用。一般塑件面积大、嵌件多、型芯及嵌件细弱,有狭窄深槽及薄壁的复杂形状对填充不利时,应采用流动性较好的塑料。注射成型时应用拉西格流动性200mm以上的塑料,挤塑成型时应选用拉西格流动性150mm以上的塑料。为了保证每批塑料都有相同的流动性,在实际中常用并批方法来调节,即将同一品种而流动性有差异的塑料加以配用,使各批塑料流动性互相补偿,以保证塑件质量。但必须指出塑料的流动性除了取决于塑料品种外,在填充型腔时还常受各种因素的影响而使塑料实际填充型腔的能力发生变化。如粒度细匀(尤其是圆状粒料),湿度大、含水分及挥发物多、预热及成型条件适当、模具表面粗糙度好、模具结构适当等则都有利于改善流动性。反之,预热或成型条件不良、模具结构不良、流动阻力大或塑料储存期过长,储存温度高(尤其对氨基塑料)等则都会导致塑料填充型腔时实际的流动性能下降而造成填充不良。
(3)质量体积及压缩率
质量体积为每一克塑料所占有的体积(以cm3/g表示)。压缩率为塑粉与塑件两者体积或质量体积之比值(其值恒大于1)。它们都可被用来确定压模装料室的大小,其数值大即要求装料室体积要大,同时又说明塑粉内充气多,排气困难,成型周期长,生产效率低。质量体积小则相反,而且有利于压制。但质量体积的值也常因塑料的粒度大小及颗粒不匀而有所不同。
(4)水分及挥发物含量
各种塑料中含有不同程度的水分、挥发物含量,过多时流动性增大、易溢料、保持时间长、收缩增大,易发生波纹、翘曲等弊病,影响塑件机电性能。但当塑料过于干燥时也会导致流动性不良,成型困难,所以不同塑料应按要求进行预热干燥,对收湿性强的原料,尤其在潮湿季节即使对预热后的原料也应防止再吸湿。
由于各种塑料中含有不同成分的水分及挥发物,同时在缩合反应时会产生缩合水分,这些成分都需在成型时变成气体排出模外,有的气体对模具有腐蚀作用,对人体也有刺激作用,因此在模具设计时应对各种塑料的此类特性有所了解,并采取相应措施,如预热、模具镀铬、开排气槽或成型时设排气工序等措施。
(5)硬化特性
热固性塑料在成型过程中在加热受压下软化转变成可塑性粘流状态,随之流动性增大填充型腔,与此同时发生缩合反应,交联密度不断增加,流动性迅速下降,融料逐渐固化。模具设计时对硬化速度快、保持流动状态短的物料则应注意便于装料,装卸嵌件及选择合理的成型条件和操作等,以免过早硬化或硬化不足,导致塑件成型不良。
硬化速度与塑料品种、壁厚、塑件形状、模具温度有关,但还受其他因素影响,尤其是预热状态。适当的预热是在使塑料能发挥出最大流动性的条件下,尽量提高其硬化速度,一般预热温度高、时间长(在允许范内)则硬化速度加快。另外,成型温度高、加压时间长则硬化速度也随之增加。因此,硬化速度也可通过调节预热或成型条件予以适当控制。
硬化速度还应适合成型方法要求,例如注射、挤塑成型时应要求在塑化、填充时化学反应慢、硬化慢,应保持较长时间的流动状态,但当充满型腔后在高温、高压下应快速硬化。
1.2.2 热塑性塑料的工艺性能
这类塑料品种繁多,性能各异。即使同一品种也由于树脂分子量及附加物配比不同而使其使用及工艺特性也有所不同。另外,为了改变原有品种的特性,可通过共聚、接枝、共混、交联、改性及增强等各种化学或物理方法,成为具有新的使用及工艺特性的改性品种。由于热塑性塑料品种多、性能复杂,即使同一种类的塑料也有供注射用或挤出用之分。这里主要介绍各种注射用的热塑性塑料。
(1)成型收缩性
热塑性塑料成型收缩的形式及计算与热固性塑料类似。影响热塑性塑料成型收缩的因素如下:
①塑料品种 热塑性塑料成型过程中由于存在结晶化引起的体积变化,内应力强,塑件内的残余应力大,分子取向性强等因素,因此与热固性塑料相比收缩率大,方向性明显。另外,脱模后收缩和后处理也比热固性塑料大。
②塑件特性 塑件成型时,熔料与型腔表面接触外层立即冷却,形成低密度的固态外壳。由于塑料导热性差,使塑件内层缓慢冷却而形成收缩大的高密度固态层。因此塑件壁愈厚则收缩愈大。另外,有无嵌件及嵌件布局、数量都直接影响料流方向、密度分布及收缩阻力大小等,所以塑件的特性对收缩大小、方向性影响较大。
③浇口形式、尺寸及分布 这些因素直接影响料流方向、密度分布、保压补缩作用及成型时间。采用直接浇口,浇口截面大时则收缩小,但方向性明显,浇口宽及长度短则方向性小。距进料口近或与料流方向平行则收缩大。
④成型条件 模具温度、注射压力、保压时间等成型条件对塑件收缩均有直接影响。模具温度高,熔料冷却慢,密度高,收缩大,尤其对结晶料,因其体积变化大,故收缩更大。模温分布是否均匀也直接影响到塑件各部分收缩量的大小及方向性。注射压力高,熔料黏度差小,层间剪切应力小,脱模后弹性回跳大,收缩也可适量减小。保压时间对收缩也有较大影响,保压时间长则收缩小,但方向性明显。因此在成型时调整模温、注射压力、保压时间等诸因素也可适当地改变塑件的收缩情况。
模具设计时根据各种塑料的收缩范围,塑件壁厚、形状、进料口形式、尺寸及分布情况,按经验确定塑件各部位的收缩率,再来计算型腔尺寸。对高精度塑件及难以掌握收缩率时,一般用以下方法设计模具。
a.对塑件外径取较小收缩率,内径取较大收缩率,以留有试模后修正的余地。
b.试模确定浇注系统形式、尺寸及成型条件。
c.要后处理的塑件经后处理确定尺寸变化情况(测量时必须在脱模后24h以后)。
d.按实际收缩情况修正模具。
e.再试模并可适当地改变工艺条件略微修正收缩值以满足塑件要求。
(2)流动性
①塑料流动性分类 塑料流动性大小,可从塑料的分子量、熔融指数、阿基米德螺旋线长度、表观黏度及流动比(流程长度/塑件壁厚)等进行分析。分子量小、熔融指数高、螺旋线长度长、表观黏度小、流动比大的塑料,则流动性好。对同一品名的塑料必须检查其说明书判断其流动性是否适用于注射成型。按模具设计要求,可将常用塑料的流动性分为3类:
a.流动性好。尼龙、聚乙烯、聚苯乙烯、聚丙烯、醋酸纤维素、聚4-甲基-1-戊烯。
b.流动性中等。改性聚苯乙烯(例如ABS、AS)、有机玻璃、聚甲醛、聚氯醚。
c.流动性差。聚碳酸酯、硬聚氯乙烯、聚苯醚、聚砜、聚芳砜、氟塑料。
②影响各类塑料流动性的因素 各种塑料的流动性也随各成型因素而变,主要影响的因素有如下几点:
a.温度。料温高则流动性增大,但不同塑料也各有差异,聚苯乙烯(尤其耐冲击型及MI值较高的)、聚丙烯、尼龙、改性聚苯乙烯(例如ABS、AS)、有机玻璃、醋酸纤维素、聚碳酸酯等塑料的流动性随温度变化较大。对聚乙烯、聚甲醛等则温度增减对其流动性影响较小。
b.压力。注射压力增大则融料受剪切作用大,流动性也增大,特别是聚乙烯、聚甲醛较为敏感,所以成型时宜调节注射压力来控制流动性。
c.模具结构。浇注系统的形式、尺寸、布置,冷却系统设计,融料流动阻力(如型面的表面粗糙度、料道截面厚度、型腔形状、排气系统)等因素都直接影响融料在型腔内的实际流动性,凡促使融料降低温度,增加流动阻力的则流动性就降低。
模具设计时应根据所用塑料的流动性,选用合理的结构。成型时也可控制料温、模温及注射压力和注射速度等因素来适当地调节填充情况以满足成型需要。
(3)结晶性
热塑性塑料按其冷凝时有无出现结晶现象可划分为结晶型塑料和非结晶型(又称无定形)塑料两类。
塑料结晶现象是指塑料由熔融状态到冷凝的过程中,分子由无次序的自由运动状态而逐渐排列成为正规模型倾向的一种现象。
可根据塑料的厚壁塑件的透明性来判别这两类塑料,一般结晶型塑料是不透明和半透明的,非结晶型塑料是透明的。但也有例外情况,如聚4-甲基-1-戊烯为结晶型塑料,却有高透明性,ABS为非结晶形塑料,但却不透明。
对结晶型塑料在模具设计及选择注射机时应注意以下几点:
①料温上升到成型温度所需的热量多,要选用塑化能力大的设备。
②冷凝时放出热量大,模具要充分冷却。
③塑件成型后收缩大,易发生缩孔、气孔。
④塑件壁薄,冷却快,结晶度低,收缩性小。塑件壁厚,冷却慢,结晶度高,收缩性大,物理性能好。所以对结晶型塑料应按塑料要求控制模温。
⑤塑料各向异性明显,内应力大,脱模后塑件易发生变形、翘曲。
⑥塑料结晶熔点范围窄,易发生未熔粉末注入模具或堵塞进料口。
(4)热敏性和水敏性
①热敏性 指某些塑料对热较为敏感,在料温高和受热时间长的情况下就会产生变色、降聚、分解的特性,具有这种特性的塑料称为热敏性塑料,如硬聚氯乙烯、聚甲醛、聚三氟氯乙烯、醋酸乙烯共聚物等。热敏性塑料在分解时产生单体、气体、固体等副产物,特别是有毒气体,对人体有刺激,对设备、模具有腐蚀作用。因此,在模具设计、选择注射机及成型时都应注意。为防止热敏性塑料在成型过程中出现变色、分解现象,一方面可在塑料中加入热稳定剂,另一方面应选用螺杆式注射机,正确控制成型温度和成型周期,同时应及时清除分解产物,对模具和设备采取防腐措施。
②水敏性 有的塑料(如聚碳酸酯)即使含有少量水分,但在高温、高压下也会发生分解,这种性能称为水敏性,对此必须预先加热干燥。
(5)应力开裂及熔融破裂
①有些塑料对应力敏感,成型时易产生内应力且质脆易裂,塑件在外力作用下或在溶剂作用下会发生开裂现象。为此,除在原料内加入附加剂提高抗裂性外,对原料应注意干燥,同时选用合理的成型条件和使塑件形状结构尽量合理。在模具设计时应增大脱模斜度,选用合理的进料口和顶出机构。在成型时应适当调节料温、模温、注射压力及冷却时间,尽量避免塑件在冷脆的情况下脱模。在塑件成型后要进行后处理以提高抗裂性,消除内应力。
②当一定熔融指数的聚合物熔体,在恒温下通过喷嘴孔时,其流速超过一定值后,挤出的熔体表面发生明显的横向裂纹称为熔融破裂。发生熔融破裂会影响塑件的外观和性能,故若选择熔融指数高的聚合物,在模具设计时应增大喷嘴、流道和浇口截面,减少注射速度和提高料温。
(6)热性能及冷却速度
①各种塑料有不同的比热容、热导率、热变形温度等热性能。比热容高的塑料在塑化时需要热量大,应选用塑化能力大的注射机。热变形温度高的塑料冷却时间短,脱模早,但脱模后要防止冷却变形。热导率低的塑料冷却速度慢,必须充分冷却,要加强模具冷却效果。热浇道模具适用于比热容低、热导率高的塑料。比热容大、热导率低、热变形温度低、冷却速度慢的塑料则不利于高速成型,必须用适当的注射机及加强模具冷却。
②各种塑料按其品种特性及塑件形状,要求必须保持适当的冷却速度。所以模具必须按成型要求设置加热和冷却系统,以保持一定模温。当料温使模温升高时应宜冷却,以防止塑件脱模后变形,缩短成型周期,降低结晶度。当塑料余热不足以使模具保持一定温度时,则模具应设有加热系统,使模具保持在一定温度,以控制冷却速度,保证流动性,改善填充条件或用以控制塑件使其缓慢冷却,防止厚壁塑件内外冷却不匀及提高结晶度等。有流动性好、成型面积大、料温不均的则按塑件成型情况需加热或冷却交替使用或局部加热与冷却并用。为此模具应设有相应的冷却和加热系统。
(7)吸湿性
塑料中因有各种助剂,使其对水分各有不同的亲疏程度,所以塑料大致可分为吸水、黏附水分及不吸水也不易黏附水分两种。塑料含水量必须控制在允许范围内,不然在高温、高压下水分变成气体或发生水解作用,使树脂起泡、流动性下降、外观及机电性能不良。所以对吸湿性塑料必须按要求采用适当的加热方法及规范进行预热,在使用时还需用红外线照射以防止再吸湿。