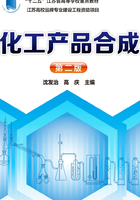
1.4 知识拓展
1.4.1 关于衡量有机反应的量度指标
(1) 转化率 转化率是反应程度的指标,它是某种反应物转化掉的量占投入该反应物的量的百分比。
(2) 选择性 选择性是反应质量指标,指某一反应物转化为目的产物,其理论消耗的物质的量占该反应物在反应中实际消耗的总物质的量的百分数。
(3) 理论收率 理论收率是化学反应的经济指标,是指目的产物的实际产量占按反应物参加反应的总量计算所得该产物的理论产量的百分数。
转化率X、选择性S与理论收率Y三者的关系是:Y=SX。
(4) 质量收率 在工业生产中还常用质量收率来衡量反应效果,即目的产物的质量占某一投入反应物质量的分数。
【例1-1】 在苯一氯化时,为了减少二氯化产物的生成量,每100mol苯用40mol氯,反应物中含38mol氯苯,1mol二氯苯,还有61mol未反应的苯,经分离后可回收60mol苯(见图1-3)。

图1-3 苯一氯化制备氯苯总转化率分析计算
苯的单程转化率:
苯的总转化率:
氯苯的选择性:
苯转化为氯苯的单程收率:
苯转化为氯苯的总收率:
【例1-2】 100kg苯胺(纯度99%,分子量93)经烘焙磺化后制得217kg对氨基苯磺酸钠(纯度>97%,分子量231.2)。求按苯胺计,对氨基苯磺酸钠的理论收率和质量收率。
理论收率:
质量收率:
(5)原料消耗定额 指每生产1t产品需消耗的某种原料的质量(t或kg)。 对于主要反应物来说,它实际上就是质量收率的倒数。如在例1-2中,每生产1t对氨基苯磺酸钠时,苯胺的消耗定额是:100/217=0.461t=461kg。
消耗定额的高低说明生产工艺水平的高低即操作技术水平的好坏。
1.4.2 影响产率的因素和提高产率的措施
1.4.2.1 影响产率的因素
物质制备实验的实际产量往往达不到理论值,这是因为有下列因素的影响。
①反应可逆 在一定条件下,化学反应建立了平衡,反应物不可能全部转化成产物。
②有副反应发生 有机反应比较复杂,在发生主反应的同时,一部分原料消耗在副反应中。
③反应条件不利 在制备反应中,若反应时间不足、温度控制不好或搅拌不够充分等都会引起实验产率降低。
④分离和纯化过程中造成的损失 有时制备反应所得粗产物的量较多,但却由于精制过程中操作失误,使产率大大降低了。
1.4.2.2 提高产率的措施
(1)破坏平衡 对于可逆反应,可采取增加一种反应物的用量或除去产物之一(如分去反应生成的水)的方法,以破坏平衡,使反应向正方向进行。究竟选择哪一种反应物过量,要根据反应的实际情况、反应的特点、各种原料的相对价格、在反应后是否容易除去以及对减少副反应是否有利等因素来决定。如乙酸异戊酯的制备中,主要原料是冰乙酸和异戊醇。相对来说,冰乙酸价格较低,不易发生副反应,在后处理时容易分离,所以选择冰乙酸过量。
(2)加催化剂 在许多制备反应中,如能选用适当的催化剂,就可加快反应速率,缩短反应时间,提高实验产率,增加经济效益。如乙酰水杨酸的制备中,加入少量浓硫酸,可破坏水杨酸分子内氢键,促使酰化反应在较低温度下顺利进行。
(3)严格控制反应条件 实验中若能严格地控制反应条件,就可有效地抑制副反应的发生,从而提高实验产率。如1-溴丁烷的制备中,加料顺序是先加硫酸,再加正丁醇,最后加溴化钠。如果加完硫酸后即加溴化钠,就会立刻产生大量溴化氢气体逸出,不仅影响实验产率,而且严重污染空气。在硫酸亚铁铵的制备中,若加热时间过长,温度过高,就会导致大量Fe(Ⅲ)杂质的生成。在乙烯的制备中若温度不快速升至160℃,则会增加副产物乙醚生成的机会。在乙酸异戊酯的制备中,如果分出水量未达到理论值就停止回流,则会因反应不完全而引起产率降低。
在某些制备反应中,充分的搅拌或振摇可促使多相体系中物质间的接触充分,也可使均相体系中分次加入的物质迅速而均匀地分散在溶液中,从而避免局部浓度过高或过热,以减少副反应的发生。如甲基橙的制备就需要在冰浴中边缓慢加试剂边充分搅拌,否则将难以使反应液始终保持低温环境,造成重氮盐的分解。
(4)细心精制粗产物 为避免和减少精制过程中不应有的损失,应在操作前认真检查仪器,如分液漏斗必须经过涂油试漏后方可使用,以免萃取时产品从旋塞处漏失。有些产品微溶于水,如果用饱和食盐水进行洗涤便可减少损失。分离过程中的各层液体在实验结束前暂时不要弃去,以备出现失误时进行补救。重结晶时,所用溶剂不能过量,可分批加入,以固体恰好溶解为宜。需要低温冷却时,最好使用冰水浴,并保证充分的冷却时间,以避免由于结晶析出不完全而导致的收率降低。过量的干燥剂会吸附产品造成损失,所以干燥剂的使用应适量,要在振摇下分批加入至液体澄清透明为止。一般加入干燥剂后需要放置30min左右,以确保干燥效果。有些实验所需时间较长,可将干燥静置这一步作为实验的暂停阶段。抽滤前,应将吸滤瓶洗涤干净,一旦透滤,可将滤液倒出,重新抽滤。热过滤时,要使漏斗夹套中的水保持沸腾,以避免结晶在滤纸上析出而影响收率。
总之,要在实验的全过程中,对各个环节考虑周全,细心操作。只有在每一步操作中都有效地保证收率,才能使实验最终有较高的收率。
1.4.3 氧化反应相关理论知识补充
工业上常以廉价的空气或纯氧作氧化剂,但由于其氧化能力较弱,一般要在高温、高压的条件下才能发生氧化反应;实验室中常用的氧化剂有KMnO4、Na2Cr2O7、HNO3等。这些氧化剂氧化能力强,可以氧化多种基团,属于通用型氧化剂。下面将根据氧化剂和氧化方法的不同对氧化反应进行讨论。
1.4.3.1 气相催化氧化反应
气相催化氧化属于多相催化氧化,要求催化剂活性高、选择性好、负荷高、并能长期保持催化活性。而对于流化床反应器所用的催化剂还要求有足够的机械强度,使催化剂在相对运动中不易被磨损或粉碎。
气相催化氧化反应使用的固体催化剂主要由催化活性组分、助催化剂和载体组成。催化活性组分一般是过渡金属及其氧化物,根据催化原理,这些物质对氧具有一定的化学吸附能力。常用的过渡金属催化剂有Ag、Pt、Pd等;常用的氧化物催化剂有V2O5、MoO3、BiO3、Fe2O3、WO3、Sb2O3、SeO2、TeO2和Cu2O等。以其中一种或数种氧化物复合使用。V2O5是最常用的氧化催化剂,纯V2O5的催化活性较小,还需要添加一些辅助成分,以提高催化活性组分的活性、选择性或稳定性等性能,这些辅助成分称为助催化剂。最常用的助催化剂是K2SO4,K2O、SO3、P2O5等氧化物也有助催化作用。在催化剂中,另外还采用硅胶、浮石、氧化铝、氧化钛、碳化硅等高熔点物质作为载体,以增加催化剂的催化活性组分的比表面积、空隙度、机械强度、热稳定性等,延长催化剂的寿命。
关于过渡金属氧化物的作用,人们有不同的看法。有一种观点持续时间较长,认为是传递氧的媒介物。即:
氧化态催化剂 + 原料还原态催化剂+氧化产物
还原态催化剂 + 氧(空气)氧化态催化剂
气-固相接触催化氧化反应是典型的气-固非均相催化反应,包括扩散、吸附、表面反应、脱附和反扩散五个步骤。由于反应需要的温度较高,又是强烈的放热反应,为抑制平行和连串副反应,提高气-固接触催化氧化反应的选择性,必须严格控制氧化反应的工艺条件。
不管是液相催化氧化还是气-固相接触催化氧化,都须特别注意安全,防止火灾、爆炸事故的发生!必须严格控制反应温度,严防物料泄漏,消除明火与静电!另外,当液相催化氧化反应超温超压须打开放空阀泄压时,泄压前须对生产现场紧急清场,除相关人员外,其他人员、车辆一律不许进入现场,并要确认无电焊、气焊、金属切割等产生火花的维修、加工作业!泄压过程中要密切注意反应釜的压力变化,控制好所泄物料流速!对于气-固相接触催化氧化,还必须特别注意被氧化物与空气的物料配比,配比必须控制在爆炸范围之外!如气态被氧化物与空气配比在爆炸范围之内,须将被氧化物相态改变为熔融态,氧化设备采用流化床或改用其他氧化方法。
1.4.3.2 化学试剂氧化
一般来说,把空气与氧以外的氧化剂总称为化学氧化剂,并把使用化学氧化剂的反应统称为“化学氧化”。在实际的生产中,为了提高氧化反应的选择性,常采用化学氧化法。
化学氧化剂大致分为以下几种类型:
①金属元素的高价化合物,例如KMnO4、MnO2、Mn2O3、Mn2(SO4)3、CrO3、Na2Cr2O7、PbO2、Ce(SO4)2、Ce(NO3)4、SnCl4、FeCl3和CuCl2等;
②非金属元素的高价化合物,例如HNO3、N2O4、NaNO3、NaNO2、H2SO4、SO3、NaClO、NaClO3和NaIO4等;
③其他无机富氧化合物,例如臭氧、双氧水、过氧化钠、过碳酸钠和过硼酸钠等;
④有机富氧化合物,例如有机过氧化氢物、有机过氧酸、硝基苯、间硝基苯磺酸、2,4-二硝基氯苯等;
⑤非金属元素,例如卤素和硫黄。
各种化学氧化剂都有它们自己的特点。其中属于强氧化剂的有:KMnO4、MnO2、CrO3、Na2Cr2O7、HNO3,它们主要用于制备羧酸和醌类,但是在温和条件下也可用于制备醛和酮,以及在芳环上直接引入羟基。其他的化学氧化剂大部分属于温和氧化剂,而且局限于特定的应用范围。
化学试剂氧化法有其独特的优点,即低温反应,容易控制,操作简便,方法成熟。只要选择适宜的氧化剂就可以得到良好的产品。由于化学氧化剂的高度选择性,它不仅能用于芳酸和醌类的制备,还可用于芳醇、芳醛、芳酮和羟基化合物的制备,尤其是对于产量小、价格高的精细化工产品,化学试剂氧化法有着广泛的应用。
化学试剂氧化法的缺点是消耗较贵的化学氧化剂。虽然某些氧化剂的还原产物可以回收,但仍有废水处理问题;另外,化学试剂氧化大部分是分批操作,设备生产能力低,有时对设备腐蚀严重。由于以上缺点,以前曾用化学试剂氧化法制备某些中间体,例如苯甲酸、苯酐、蒽醌等,现在工业上都已改用催化氧化法。
各种化学氧化剂都有它们各自的特点,现扼要介绍如下。
(1)高锰酸钾 高锰酸钾亦名“灰锰氧”“PP粉”,是一种常见的强氧化剂,常温下为紫黑色片状晶体,易见光分解。在水中溶解度为6.38g/100mL(20℃)。
高锰酸钾在酸性、中性和碱性介质中都有氧化性。在不同的介质中,反应结果不一样。在强酸性水介质中,锰原子的价态则由+7价还原为+2价,氧化力太强,选择性差,只适用于制备个别非常稳定的化合物,而锰盐又难于回收,所以工业上很少使用酸性氧化法。
KMnO4在中性或碱性介质中进行氧化时,锰原子的价态由+7价还原为+4价,也有很强的氧化能力。此法氧化能力较酸性介质弱,但是选择性好,生成的羧酸以钾盐或钠盐的形式溶于水,产品的分离与精制简单,副产品二氧化锰的用途也广泛。
2KMnO4+H2O2MnO2↓+2KOH+3[O]
在这个过程中,平均1mol高锰酸根释放出1.5mol原子氧、1molKOH和1molMnO2。由于KOH的碱性,如果不能及时中和,则随着氧化的进行,介质的pH值会逐渐升高,导致KMnO4的氧化能力下降,使得氧化反应速率下降,或者氧化停留在中间体阶段。如果生成的KOH能引起副反应,可以向反应液中加入硫酸镁来抑制其碱性。
2KOH+MgSO4K2SO4+Mg(OH)2↓
例如,将3-甲基-4-硝基乙酰苯胺用高锰酸钾氧化制取2-硝基-5-乙酰氨基苯甲酸时,加入硫酸镁可避免乙酰氨基的水解。
硫酸镁的加入能起到稳定介质pH值的作用,能维持KMnO4的氧化能力。
KMnO4受热易分解,其分解释放[O]的速度较快,但[O]氧化有机物的速率往往较慢,多余的[O]易形成O2从体系中逸出,故使用KMnO4氧化时,要注意对其[O]释放速率的控制。通常控制反应温度在40~100℃,投料时以分批量加入固体形式KMnO4为宜,即向底物(即参与反应的有机物)中加入一批KMnO4,待其反应后再加入下一批KMnO4。反应结束后过量的KMnO4可以用亚硫酸氢钠还原掉。
(2)二氧化锰氧化剂 二氧化锰可以是天然软锰矿的矿粉(含MnO260%~70%),也可以是用高锰酸钾氧化时的副产物。二氧化锰一般可在各种不同浓度的硫酸中使用。在稀硫酸中氧化时,要用过量较多的二氧化锰。在浓硫酸中氧化时,只要稍过量的二氧化锰即可。其氧化反应式如下:
MnO2 + H2SO4[O]+ MnSO4 + H2O
二氧化锰是比较温和的氧化剂,可使芳环侧链上的甲基氧化为醛,可用于制备芳醛、醌类以及在芳环上引入羟基等。
反应实例如下:
(3)重铬酸钠(Na2Cr2O7)氧化剂 重铬酸钠容易潮解,但是它比重铬酸钾的价格便宜得多,在水中的溶解度大,故在工业中应用广泛。重铬酸钠通常是在各种浓度的硫酸中使用。其氧化反应方程如下:
Na2Cr2O7 + 4H2SO43[O]+ Cr2(SO4)3 + Na2SO4 + 4H2O
重铬酸钠主要用于将芳环侧链上的甲基氧化为羧基。例如由对硝基甲苯的氧化制对硝基苯甲酸等。
重铬酸钠在中性或碱性介质中是温和的氧化剂,可用于将—CH3、—CH2OH、—CH2Cl、—CHCHCH3等基团氧化成醛基。
目前由于重铬酸盐价格较贵,含铬废液的处理费用较高,因此已逐渐被其他氧化法所代替。
(4)硝酸氧化剂 硝酸也是一种强氧化剂,稀硝酸的氧化能力比浓硝酸更强。浓硝酸在低温时主要是硝化剂,而稀硝酸在较高温度下则是氧化剂。硝酸价格便宜,在条件允许的情况下,用硝酸作氧化剂是比较经济的。
用硝酸作氧化剂的优点是它在反应后生成氧化氮气体,反应液中无残渣,分离提纯氧化产品较为容易,工艺简单。其缺点是介质的腐蚀性很强,氧化反应较剧烈,反应的选择性不好,有废气的产生,而且除氧化反应外,还容易引起硝化和酯化等副反应。
硝酸常用来氧化芳环或杂环侧链成羧酸;氧化含有对碱敏感的基团的醇成相应的酮或羧酸;氧化活泼亚甲基成羰基;氧化氢醌成醌;氧化亚硝基化合物成硝基化合物等。例如:
分子中含有对碱敏感的基团(如卤素)时,由于不能选用碱性介质的高锰酸钾氧化,故要用硝酸氧化。如:
稀硝酸和浓硝酸对有机物进行氧化时,稀硝酸和浓硝酸分别被还原为NO和NO2气体,废气采用氢氧化钠水溶液吸收。
(5)过氧化物氧化剂 过氧化氢和有机过氧化物是一种特殊的氧化剂。在有机合成中,过氧化氢与氢氧化钠一起使用,主要用于生成有机过氧酸。如:
有机过氧化物作为氧化剂有以下两个特点。
第一个特点是,有利于在羰基与其邻位碳原子间插入一个氧原子,即使酮转变为酯,特别是将环酮氧化为内酯。
这种反应一般在酸性介质中进行,以乙酸、氯仿、二氯甲烷或醚为溶剂。如:
第二个特点是可将碳碳双键氧化成环氧化物。如:
有机物采用过氧化物或其他化学氧化剂进行氧化,要优先考虑用双氧水作氧化剂。氧化反应中,双氧水被还原为水,不会往反应体系中带入杂质,有利于目的产物的分离和纯度的提高,这是双氧水与其他化学氧化剂相比最显著的优点。双氧水贮存时必须注意贮存温度常温(不能过高),不能与可燃、易燃物质混合贮存。双氧水使用时必须注意在低温下使用,浓度不能过高,不能与重金属离子等微量杂质接触。防止火灾、爆炸事故的发生!
1.4.4 苯甲酸工业上的制备方法简介
工业上苯甲酸是在钴、锰等催化剂存在下用甲苯液相空气氧化法制得或由邻苯二甲酸酐水解脱羧制得。
液相空气氧化要用乙酸钴作催化剂,其用量约为100~150mg/kg,反应温度为150~170℃,压力为1MPa,生产流程如图1-4。

图1-4 甲苯液相空气氧化法制苯甲酸流程示意图
1—氧化反应器;2—汽提塔;3—精馏塔
甲苯、乙酸钴(2%水溶液)和空气连续地从氧化塔的底部进入。反应物的混合除了依靠空气的鼓泡外,还借助于氧化塔中下部反应液的外循环冷却。从塔上部流出的氧化产物中约含有苯甲酸35%。反应中未转化的甲苯由汽提塔回收,氧化的中间产物苯甲醇和苯甲醛可在汽提塔及精馏塔的顶部回收,与甲苯一样回入氧化塔再反应。精制是苯甲酸可由精馏塔的侧线出料收集。塔釜中残留的重组分主要是苯甲酸苄酯和焦油状产物,其中的钴盐可以再生使用。氧化尾气夹带的甲苯经冷却后再用活性炭吸附,吸附在活性炭上的甲苯可用水蒸气吹出回收,活性炭同时得到再生。氧化产物也有采用四个精馏塔进行分离的,分别回收甲苯、轻组分、苯甲醛和苯甲酸。此法制取苯甲酸按消耗甲苯计算的收率可达97%~98%,产品纯度可达99%以上。