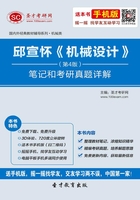
第3章 机械零件的疲劳强度
3.1 复习笔记
一、疲劳断裂特征
1.疲劳断裂过程
表面无缺陷的金属材料,其疲劳断裂过程分为两个阶段:
第一阶段是零件表面上应力较大处的材料发生剪切滑移,产生初始裂纹,形成疲劳源,疲劳源可以有一个或数个;
第二阶段是裂纹尖端在切应力下发生反复塑性变形,使裂纹扩展直至发生疲劳断裂。
2.疲劳断裂截面
疲劳断裂截面是由表面光滑的疲劳发展区和粗糙的脆性断裂区组成。
(1)零件在变应力下反复变形,裂纹周期地压紧和分开,使疲劳发展区呈光滑状态,在电子显微镜下放大观察,有以疲劳源为中心,间隔为0.1μm~1μm的同心疲劳纹。
(2)粗糙的脆性断裂区是由于剩余截面静应力强度不足造成的。
二、疲劳曲线和疲劳极限应力图
1.疲劳曲线
(1)疲劳极限
在循环特性下的变应力,经过N次循环后,材料不发生破坏的应力最大值称为疲劳极限σrN或τrN。
(2)疲劳曲线图形解析
表示循环次数N与疲劳极限间的关系曲线,称为疲劳曲线(σ-N或τ-N曲线)。典型的疲劳曲线如图3-1所示。

图3-1 疲劳曲线
①有限寿命区
a.当N<103(104)次时,疲劳极限较高,接近屈服极限,疲劳极限几乎与循环次数的变化无关,称为低周循环疲劳。
b.当N≥103(104)次时,称为高周循环疲劳,其中103(104)≤N<N0时,疲劳极限随循环次数的增加而降低。
②无限寿命区
N≥N0时,疲劳曲线为水平线,即疲劳极限不再随循环次数的增加而降低,称为无限寿命区。N0次循环时的疲劳极限记为:循环特性r时为σr,τr,对称循环时为σ-1、τ-1,脉动循环时为τ0、τ0。寿命N<103(104)次的零件,一般可按静应力强度计算,但在重要情况下,应按低周循环疲劳设计。
(3)疲劳曲线方程
①在有限寿命区103(104)≤N<N0范围内疲劳曲线方程式为

式中m为随材料和应力状态而定的指数;kN为寿命系数。
②疲劳曲线方程的有关问题
a.循环基数N0
材料性质不同,N0值也不同。
b.指数m
疲劳曲线的指数如图3-2所示。已知疲劳曲线方程对此式取对数得

m的平均值:对于钢,拉应力、弯曲应力和切应力时m=9,接触应力时m=6;对于青铜,弯曲应力时m=9,接触应力时m=8。
c.不同循环特性r时的疲劳曲线
不同r时的疲劳曲线具有相似的形状,但r愈大,σrN也愈大。

图3-2 疲劳曲线的指数m
2.疲劳极限应力图
简化疲劳极限应力图如图3-3所示,其具体方法是:考虑到塑性材料的最大应力不得超过屈服极限,故由屈服极限点S作135°斜线与AB连线的延长线交于E,得折线ABES,其上各点横坐标为极限平均应力σm,纵坐标为极限应力幅σa,因ES为屈服极限曲线,线上各点均为σs。

图3-3 塑性材料简化疲劳极限应力图
零件的工作应力(σm,σa)点处于折线以内时,其最大应力既不超过疲劳极限,也不超过屈服极限,故为疲劳和塑性安全区,在ABES以外为疲劳和塑性失效区。工作应力点距ABES折线愈远,安全程度愈高。
三、影响机械零件疲劳强度的主要因素
1.应力集中的影响
(1)应力集中对疲劳强度的影响
零件受载时,在几何形状突然变化处要产生应力集中,常用有效应力集中系数kσ、kr来考虑应力集中对疲劳强度的影响。

式中aσ,ar为考虑零件几何形状的理论应力集中系数;q为考虑材料对应力集中感受程度的敏感系数。
(2)降低应力集中的方法
在结构上,减缓零件几何尺寸的突然变化、增大过渡圆角半径、增加卸载结构等都可降低应力集中,提高疲劳强度。
(3)计算kr值
若缺少ar的数据而已知kσ时,可利用下式求kr值
kr=1+0.6(kσ-1)
若在同一截面上同时有几个应力集中源时,应采用最大有效应力集中系数进行计算。
2.尺寸的影响
零件尺寸的大小对疲劳强度的影响可以用尺寸系数εσ和εr来表示。当其他条件相同时,尺寸愈大,对零件疲劳强度的不良影响更加显著。若缺少ε数据时,可取εa=εr。
3.表面状态的影响
(1)表面状态系数βσ和βτ
零件加工表面质量对疲劳强度的影响用表面状态系数βσ和βτ来表示。

铸铁对于加工后的表面状态很不敏感,故可取。
(2)改善表面状态的措施
①如淬火、渗氮、渗碳等热处理工艺,抛光、喷丸、滚压等冷作工艺。改善后的表面状态系数可能大于1,计算时取1。
②冷拉加工产生的残余拉应力,会降低疲劳强度。
③受到腐蚀的金属表面形成应力集中源,故腐蚀也会降低疲劳强度。
4.综合影响系数
应力集中、零件尺寸和表面状态都只对应力幅有影响,对平均应力没有明显影响。为此,可将这三个系数合并为一综合影响系数

零件的工作应力幅要乘以综合影响系数,或材料的极限应力幅要除以综合影响系数。
四、许用疲劳极限应力图
1.稳定变应力和非稳定变应力
(1)稳定变应力的定义
稳定变应力是指在每次循环中,平均应力σm、应力幅σa和周期都不随时间t变化的变应力,如图3-4(a)所示;图3-4(b)为其最大应力和累积循环次数的直方图。
(2)非稳定变应力的定义
非稳定变应力是指平均应力σm、应力幅σa和周期其中之一随时间变化的应力,其通常是由于载荷或工作转速变化所造成。作周期性规律变化的称为规律性非稳定变应力,随机变化的称为随机性非稳定变应力。

图3-4 稳定变应力及其直方图
2.许用疲劳极限应力图
如图3-5所示ABE是简化疲劳极限曲线,考虑了影响疲劳强度的综合影响系数(kσ)D或(kτ)D和寿命系数kN后,得到许用疲劳极限曲线AˊBˊEˊ。综合影响系数只对极限应力幅有影响,寿命系数对极限平均应力和极限应力幅均有影响。工作应力点C(σm,σn)必须落在OAˊBˊEˊSO区域(安全区)内。

图3-5 许用疲劳极限应力图
3.工作应力增长规律
(1)=常数,如转轴的弯曲应力;
(2)常数,如车辆振弹簧;
(3)σmin=常数,如气缸盖的螺栓联接。
五、稳定变应力时安全系数的计算
疲劳强度计算是采用安全系数法判断零件危险截面处的安全程度,其条件是:S≥[S]。由于计算是在零件的材料、结构和尺寸初步确定之后进行,所以具有验算性质。
1.r=常数时,单向应力状态时的安全系数
(1)简析
=常数
由上式可见,要使r=常数,比须保持不变。这时σa和σm应按同一比例增长。如图3-6所示为许用疲劳极限应力图,C(σm,σa)为工作点,连OC并延长与AˊEˊ交于
,因
=常数,所以工作应力沿射线OCˊ增长时,r=常数。

图3-6 r=常数时安全系数计算简图
OCˊ线与水平轴间夹角α为,根据求得的α角作射线与AˊE〞的交点即是求得Cˊ点,Cˊ点为应力增长规律的极限点。
计算安全系数时有图解法和解析法两种:
①图解法
此法是在按比例绘制的许用疲劳极限应力图上量取位于OAˊEOˊ区内代表Cˊ和C各应力的线段长来求:
a.r=常数时,疲劳强度的最大应力安全系数Sσ和应力幅安全系数Sσa;

b.r=常数,Sσ=Sσa,量取代表C1ˊ和C1各应力的线段求屈服强度安全系数。

②解析法
当工作点位于疲劳安全区时,可根据点Aˊ和Bˊ,求得AˊEˊ直线方程式和切应力。将和
的关系分别代入直线方程式和切应力方程式,得极限应力幅,最后按应力幅求安全系数。

对于塑性材料,当工作点位于塑性安全区,则应验算屈服强度安全系数。

采用解析法计算时,常不能判断工作点所在的区域,为安全计,疲劳强度和屈服强度安全系数都计算。
对于低塑性和脆性材料,因其疲劳极限应力图也为一直线,脆性材料不必验算屈服强度安全系数。
2.复合应力状态时的安全系数
(1)塑性材料
塑性材料零件在对称循环弯扭复合应力状态下,按第三强度理论计算时,可近似取,按第四强度理论计算时,可近似取
,复合安全系数为:

为防止塑性材料零件在复合应力下发生塑性变形,还要验算复合应力屈服强度安全系数(上式用于第三强度理论,下式用于第四强度理论)

式中
(2)低塑性和脆性材料

六、规律性非稳定变应力时机械零件的疲劳强度
1.疲劳损伤积累假说
(1)模型
如图3-7(a)所示为一零件的规律性非稳定变应力直方图,图中是当循环特性为r时各个循环的最大应力,N1、N2、…、Nn为与各应力相对应的积累循环次数。
为与各应力相对应的材料发生疲劳破坏时的极限循环次数,如图3-7(c)所示。

图3-7 疲劳损伤积累图
(2)疲劳损伤积累假说
在每一次应力作用下,零件寿命就要受到微量的疲劳损伤,当疲劳损伤积累到一定程度达到疲劳寿命极限时便发生疲劳断裂。
(3)线性疲劳损伤积累
应力每循环一次造成零件一次寿命损伤,故其总寿命损伤率

零件达到疲劳寿命极限时,理论上总寿命损伤率为1,即。
(4)试验结果
总寿命损伤率约在0.7~2.2之间。表面有残余压应力的可能大于1,表面有残余拉应力的可能小于1。为计算方便,通常取1。
(5)小于疲劳极限σr的应力对疲劳寿命无影响
2.等效稳定变应力和寿命系数
(1)等效稳定变应力
非稳定变应力下零件的疲劳强度计算是先将非稳定变应力折算成单一的与其总寿命损伤率相等的等效稳定变应力σv。通常取等效应力σr等于非稳定变应力中作用时间最长的和(或)起主要作用的应力。
(2)寿命系数
如图3-7(b)所示,取σv=σ1。对应σv的是等效循环次数Nv和材料发生疲劳破坏时的极限循环次数Nˊv(如图3-7(c)所示)。


式中kN为等效循环次数时的寿命系数。
3.规律性非稳定变应力时安全系数的计算步骤
(1)取等效应力σv等于非稳定变应力中作用时间最长的和(或)起主要作用的应力σi,并取σv的应力幅σav和平均应力σmv相应地等于σi的应力幅σai和平均应力σmi;
(2)求等效循环次数Nv;
(3)求等效循环次数时的寿命系数kN和疲劳极限σrv;
(4)按等效应力计算疲劳强度安全系数;
(5)按最大非稳定变应力计算塑性材料屈服强度安全系数。
七、低周循环疲劳概述
低周循环疲劳是指零件在变应力达到屈服极限和循环次数低于103(104)时发生的疲劳损坏。与高周循环疲劳一样,低周循环疲劳也是由于反复塑性变形造成的。

图3-8 应变疲劳曲线(ε0-N曲线)
在低周循环下,疲劳极限与循环次数几乎无关,σ-N疲劳曲线已不适用。通过试验得知,绝大多数金属的塑性应变量εm与循环次数N间存在着明显关系,如图3-8所示的应变疲劳εp-N曲线,其方程式为

式中N为低周循环次数;εp为循环次数为N时的塑性应变量;b为与材料有关的常数,对于大多数材料,b=0.35~0.8(软钢0.591,30CrM0钢0.621,40CrNiM0钢0.556,硬铝0.590);C为常数,近似等于静拉伸断裂时的应变量。
八、疲劳裂纹寿命概述
材料表面和内部都不可避免有裂纹存在。断裂力学是在承认裂纹存在的前提下进行的疲劳强度计算,其判据是裂纹扩展到临界尺寸时发生疲劳断裂。疲劳裂纹的扩展速度da/dN可近似用以下关系表示


式中a为裂纹半长;N为循环次数;C为与材料有关的系数,如40钢C:3.1×10-11;n为指数(结构钢3~4,40钢为3);ΔK为应力强度因子幅度;a为几何效应因子,与零件的形状和尺寸、裂纹的形状、尺寸和部位,以及载荷等因素有关;Δσ为变应力的变化范围。(当σmin为压应力时,取σmin=0)。
应力强度因子幅度ΔK是控制裂纹扩展速度的主要参数。当ΔK小于界限应力强度因子幅度
时,裂纹便不扩展,所以要求无限寿命的零件,其计算判据为

在对称循环下,结构碳钢和低合金钢高强度钢

裂纹以一定速度扩展,由积分式可得裂纹半长由a1扩展到a2时的循环次数(寿命)。

式中N1为裂纹初始半长为a1时的循环次数;N2为裂纹半长扩展到a2时的循环次数。
当ΔK增大到等于材料的断裂韧度KIc时,裂纹达到临界尺寸ac,扩展速度急剧增大,发生裂纹失稳扩展断裂。裂纹临界尺寸ac可用式算出,在该式中令ΔK=KIc。
按da/dN=ΔK设计时,允许零件在有裂纹的情况下工作,但裂纹的最大允许长度和临界长度之间要有一定的安全系数。
对于高周循环疲劳,无裂纹寿命占总寿命的主要部分,裂纹寿命计算只是计算高周循环零件出现裂纹后的剩余寿命。对于低周循环疲劳,无裂纹寿命占总寿命很小部分,可忽略不计,裂纹出现后扩展阶段的寿命占总寿命的绝大部分,所以裂纹寿命就是低周循环零件的寿命。