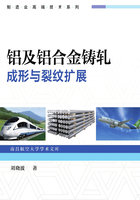
前言
随着世界经济和科学技术的发展,铝已成为仅次于钢铁的第二大金属。双辊铸轧技术具有生产工艺简单、生产周期短、生产成本低等优势而成为国内外铝工业中的一种主要生产方法。铝双辊超薄快速铸轧技术以其铸坯组织晶粒细化、较少的偏析、优良的力学性能以及高的生产率等特点而成为当今冶金科技的前沿技术之一。由于铸轧过程熔体流动和凝固传热更加复杂,铸坯质量的控制难度增加,铸轧工艺参数的可调范围减小,铸轧工艺参数的合理匹配已成为制约实现快速超薄铸轧,获得高质量铸坯的一个关键问题。高性能铝合金具有高的室温强度和良好的综合力学性能,已广泛应用于航空、国防、高铁等领域。由于高强铝合金在锻造变形过程中温度不均匀产生裂纹等缺陷,严重影响了铝合金的质量,因此,研究高强铝合金裂纹等缺陷的产生机理,确立抑制成形过程组织缺陷的调控方法,对于获得高质量铝合金具有重要的意义。
本书系统地研究分析了铝及铝合金铸轧成形与裂纹扩展规律及其影响因素。基于元胞自动机法(CA),采用LGK模型模拟了晶粒生长的动态演变,用基于正态分布的形核模型和KGT生长模型,对铝铸轧凝固过程中晶粒的生长及微观组织的形成进行了模拟,模拟结果有助于从理论角度解释微观组织中出现枝晶间偏析、点偏析及微观缩松等缺陷的形成原因。基于有限元法(FEM),建立了铝铸轧过程整体模型,分析了铸轧参数对铸轧过程的影响。基于损伤理论,研究了辊套疲劳寿命预估。基于有限差分法(FDM),建立了铸嘴的流动模型,分析了铸轧参数对铸嘴型腔熔体流动、出口速度及出口温度的影响。通过水模试验及铸轧过程试验验证了模拟的有效性。基于分子动力学法(MD),采用嵌入原子势法(EAM),模拟了铝裂纹扩展行为,从裂纹扩展图观察到裂纹扩展的变化情况:裂纹尖端钝化、子裂纹的产生、孔洞的生成及长大过程以及裂纹和孔洞的汇集;探讨加载速度和初始裂纹长度对体系裂纹扩展行为的影响;分析了孔洞大小、数量及分布对铝裂纹扩展行为的影响;模拟铝合金粗大第二相Al2Cu拉伸变形行为,发现Al2Cu非常脆,应变ε=0.086时应力达到峰值6.4GPa,在拉伸初期不易产生位错,从而弹性变形阶段较长;探讨温度和应变率对体系拉伸变形行为的影响;分析了孔洞数量及分布对Al2Cu拉伸变形行为的影响。基于均匀化方法,建立了铝合金细观结构的数学模型,对铝合金细观结构响应进行了分析;并分析了温度、孔洞数量对裂纹扩展的影响。对7050铝合金进行均匀化热处理,分析热变形参数对7050铝合金流变应力的影响;通过热变形参数对微观组织演化规律的影响,对高温塑性变形条件下的变形机制进行研究。
本书的内容为作者十余年来的研究成果,在研究过程中先后得到了国家自然科学基金项目(No:50564004)、教育部科学技术研究重点项目(No:02081)、江西省自然科学基金项目(No:0250020,2010GQC0803)及江西省教育厅科技落地计划科学前沿项目(No:KJLD12073)的资助。本书内容对研究铝及铝合金铸轧成形与裂纹扩展,从而获得高质量的铝及铝合金产品具有较强的指导作用。
感谢清华大学许庆彦教授、中南大学易幼平教授对本书内容的修改意见!感谢南昌航空大学学术文库专项基金资助!
由于时间仓促,且作者水平有限,书中错误和不当之处在所难免,在此诚恳地欢迎广大读者批评和指正。
刘晓波