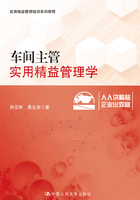
第2节 车间主管的角色
在大多数企业中,车间主管的主要职责是根据企业目标,制订生产计划,直接指挥、组织和监督现场员工,协调分配各类资源,保证完成上级下达的各项计划和指令。通常情况下,他们主要关心的事情便是具体工作任务的完成。而为了确保任务完成的顺畅性,他们必须从各个管理角度切入,全力以赴地推动企业精益经营活动的开展。总结来说,车间主管主要担当的角色有:
(1)任务分配者:将企业生产任务逐一分解,直至个人身上;
(2)事务组织者:把握当前资源使用情况,根据现时需求进行组织分配;
(3)问题发现者:在整个车间运作过程中关注工作状态,在第一时间发现车间运作、产品质量问题等,并组织处理;
(4)质量验收者:对产出质量进行定期验收;
(5)职业导师:培养员工的工作能力、精益知识和素养。
其中,任务分配者、事务组织者、质量验收者角色是我们已经认知到的,在本节中,我们将对其问题发现者和职业导师的角色定位进行重点阐述。
案例1 绝不隐藏问题
理念1 精益推行的主要场所
丰田曾提出了一个词汇——“现场”,按照意译,它是指亲自到现场了解实际情况。我们知道,任何生产现场中的问题都不会自动地展现出来。所以,如果车间主管要想发现车间生产情况,那么你必须了解精益推行的主要场所——车间里的真实情况。这意味着车间主管必须做到三件事:重视车间问题、深察车间问题和深度分析车间问题。
重视车间问题
作为精益生产之鼻祖,丰田早年的做法是非常值得称道的。他们赋予每位一线工人发现问题就“拉下安灯线”的权利,从而提醒车间主管和一线工人“当下出现了产品缺陷”。如果不及时解决这些问题,丰田会停止整条生产线的生产运作。
三菱汽车澳大利亚公司的成功也是得益于此。1983年,在剑桥集团举办的关于看板制度、质量控制与质量管理的研讨会上,三菱汽车澳大利亚公司总监格瑞姆·斯伯灵如此评论道:
“三菱自1980年开始接管了澳大利亚克莱斯勒公司。1977年和1978年,澳大利亚克莱斯勒的亏损接近5000万美元。而现在,一个众所周知的事实是,三菱汽车澳大利亚公司的运营状态是盈利,而且运作效率非常之高。我们认为,公司已经拥有澳大利亚汽车行业最高水平的生产效率,我们完全有能力生产出质量最佳的产品。
“同时,我也必须公正地说,在三菱接手之前,公司也尝试进行了一些改善运动,并取得了一定的成绩。但我们公司之所以能够持续繁荣,在很大程度上要归功于从日本公司那里学到的经验和教训。
“而三菱之所以能取得成就就是由于公司以最小的投入引入了一系统改进项目,如减少库存、改变工厂布局等。例如,以往设计工厂布局时,主要考虑如何去适应整幢大楼,但三菱却大胆地反其道而行之,让大楼在设计之初来匹配最优化的工厂布局。结果,流水线上的库存减少了80%,个人的绩效提高了30%。”
可见,发现车间里的问题对企业改善而言是一件至为重要的事情。不管多小的问题,企业都应将之视为企业整体系统的窗口,以明示的状态予以展现,就像我们在案例中所论述的那样——要让问题看得见,然后再彻底地予以解决。
深察车间问题
大野耐一曾说过:“我是彻底的现场主义者。因为我从年轻时起,就在生产第一现场中,不断磨炼长大的。后来我作为副社长,负责企业经营管理,就更不能离开生产第一现场了,因为现场是企业的主要情报来源。”他还说过:“与其每天坐在副社长办公室里冥思苦想,还不如到生产现场的各个角落去转转,直接获得第一手的生产信息,感受最直接的刺激。如果一直身处现场中,就能从那里获得满足。现场主义正符合我的个性。”
事实证明,现场主义不仅符合大野耐一的个性,也符合丰田公司的个性,更符合整个日本制造业甚至是全世界制造业的个性。这是因为,在现场中存在着最原始的资料和最真切的声音。这些来自最前线的信息会给车间管理人员带来最倾向于正确的问题评估与判断,从而做出最为可行的改善决策。
简言之,现场主义就是“行胜于言”,就是到鲜活的现场,俯下身去观察、触摸;而不是坐在一个人的办公室里空想,召开一些不着边际的会议,一个个地找员工沟通……如此远离现场,纸上谈兵,是极度不利于现场管理的。
保罗·肯尼迪在其著名的《大国的兴衰》一书中,曾有一句掷地有声的话:“现场主义是伟大的指导者。”中国人也曾经毫不客气地用一句极为形象的话来批评那些不坚持现场主义的人:“四体不勤,五谷不分。”由此足见,车间主管不仅要重视车间的精益改善,还要亲自深入车间里去实践。
深度分析车间问题
长期以来,日本企业都在身体力行着始于丰田、始于大野耐一的“现场主义”。而觊觎日本丰田公司管理经验的美国制造业,更是奉丰田现场主义为圭臬,竭尽全力地研究、仿效并执行。而中国企业对丰田现场主义也是始终怀有好感,但却始终不曾把握住现场主义实施之精髓。
为了寻找问题,一些车间主管可能会下达指令,要求所有人员每天都去现场了解情况——这件事是很容易做到的。但是,如果人们欠缺分析与了解情况的技巧,那么这种实务工作却往往不会产生什么实际效果。
丰田技术中心总裁山品匡史曾如此说道:“并不是亲自到现场查看而已,而是要问:发生了什么?你看到了什么?情况如何?问题何在?在北美地区的丰田企业里,我们仍然只是做到亲自到现场查看而已。但问题是,你进行了真正深入的分析吗?你真的了解情况与问题吗?最根本的是我们必须根据实际信息来做决策。统计数字只能说明事实,我们需要知道更多。有时候我们被指责花了太多时间在所有分析工作上,有人会说:‘凭常识就可以判断,我知道问题出在哪里。’但是,只有收集资料和深入分析才能告诉你,你的常识到底正不正确。”
山品匡史的话告诉我们,要使制造异常现形于表面,车间主管必须亲临实地来验证现场问题;然后,再根据证实、证明过的信息与数据,结合各种技术的应用,来思考与分析问题的根源,由此提出的解决对策才是最有针对性、最有效的。
车间主管们必须谨记:企业管理的价值从何而来?从解决问题中来。在哪里解决问题?答案永远是车间现场!可以说,重视车间现场,这是车间主管在精益改善活动推行中的主要责任所在。
案例2 丰田的职业导师
理念2 培养精益素养
在现实工作中,很多车间主管将其自我工作内容为:每天只要负责给员工分配工作,而后监督工作落实,最终验收工作成果即可;对于员工在想什么、要做什么、能做什么基本不太关注。
然而,精益是一项比较复杂的事。如果员工在头脑上并未形成端正的精益观念,也未掌握有效的精益技能,那么车间的精益推行是难以为继的。海尔集团前总裁张瑞敏说过:“一些人做事有个大毛病,就是不认真,每天工作总是欠缺一点,天长日久,就落下落后的顽症。”这种状况是与精益化截然相反的状态。因为精益化要求人们不断提高自身价值,做事要精益求精。那么,如何才能使自己的个体价值逐步提高呢?这就要求人们具有精益素养,即精益知识和精益观念。
在刚开始推行精益时,员工们并不需要多么详尽的精益知识,而是首先培养精益的意识。大野耐一最初导入精益生产时,注重的也不是精益知识,而是精益意识。一个人是否具有精益意识,对精益活动开展的态度会截然不同。我们可能会表现为四种状态:
(1)推动者:愿意付诸努力,并积极尝试精益活动。
(2)追随者:通常是不计较名利或基于对推动者的信任,能够不折不扣地执行精益措施。
(3)观望者:受各种因素的影响(如先前的失败经验),对精益的举措或效果持怀疑态度,对精益活动持观望态度。
(4)抵制者:由于过于自尊或因个人利益等因素而对精益活动的开展持有敌意,在短时间内难以与之沟通合作。
每个人的内心深处都不喜欢别人对自己指手画脚。只有那些自己亲自选择的事情,人们才会真正地全力以赴去执行。所以,当我们推动精益活动时,一定要确认一个具有精益化素养——精益意识和精益知识,这样才会从真正意义上参与精益,推动精益化的实现。
当员工具有精益意识后,掌握精益知识的重要性就会凸显出来。那么,我们可以从哪里帮助员工获得精益知识呢?
在北美、欧洲和日本,有许多培训机构或场所可以学习到精益知识。许多精益企业本身也乐于与客户、供应商共同实施改善。例如,恩福集团曾举行过“三天改善”活动,期间曾有500多名外围公司的人员共同参与其中。并且,也有很多有关精益技术应用的书籍和资料,其内容论述得非常翔实。
由于大多数人并不熟悉精益概念,所以员工们可能需要很多时间去掌握,当然也就需要寻求一些外界帮助。这时,车间主管们可以邀请专家对产品价值流作出评价,并帮员工展开突破性改善和改善活动。比如,在产品开发中应用质量功能展开法、在生产车间引入精益技术时,我们都需要借助很多不同的技术。所以,我们要邀请一批掌握专门知识的专业人员来进行精益知识传授。
目前,世界上很多公司都在利用的咨询人员的来源就是早年奉行精益管理的日本人和他们的传承者,他们开创或传承了精益思想。从过去到现在,他们似乎具有为消除浪费而不懈努力的天性。比如大野耐一,他的一生都在指导精益改善运动,直到他去世。
然而无论是掌握精益知识还是养成精益精神,员工们都很难独自实现这两大目标。在此过程中,作为与员工距离最近的管理者、有着更丰富的精益推行经验的人——车间主管,还应发挥职业导师的职能,使员工始终坚持精益观念和原则,推进工作和企业运作向着精益化的方向发展。
事实上,每一位车间主管都应形成这样的认识:在精益车间管理中,对于员工,我的角色不仅仅是任务分配者、工作监督者、质量验收者、事务组织者等,我还应作为员工的职业导师,帮助员工获得丰富的精益知识,养成端正的精益素养。
【辅助阅读】
理光制造的精益素养养成计划