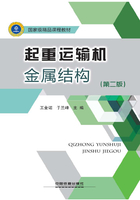
第五节 起重运输机金属结构设计计算方法
一、现代设计方法简介
用于起重机金属结构设计计算的现代设计方法主要有有限元法、优化设计、可靠性设计、疲劳设计、机械动态设计等。现代设计方法显著的特点是应用计算机这一先进手段,而计算手段的现代化又促进了设计计算理论的重大发展。
起重运输机械金属结构的设计计算不可避免地要涉及空间结构的超静定问题,加上计算工况甚多,应用手算方法实际上难以应付如此复杂的分析和繁重的计算工作量,传统的设计计算方法只能做出各种各样的简化和假定,计算结果与实际情况有较大的出入,不得不加大安全系数给予补偿。过去由于计算过于繁杂而不能解决的问题,现在借助于计算机已不是困难的事了。利用矩阵进行计算尤其便于计算机程序的设计,矩阵理论的发展与计算机在结构分析中的应用相得益彰。
应用计算机进行结构分析最具普遍意义的方法是有限元法。有限元法是把所要分析的弹性体假想地分割为有限个单元,各单元仅在节点处连接并传递内力,连接应满足变形协调条件,这个过程称为离散化。外载荷也以节点载荷的形式出现,把所有的外力向节点移置。这样将无限自由度的连续体的力学计算转变为有限单元节点参数的计算,以完成复杂结构的力学分析。在有限元法中,通常是以位移法来求解。有限元法的计算精度取决于单元的数量和形状,所以总可以达到所要求的精度。由于单元数量较多,只能用计算机求解数量庞大的线性联立方程组。
在现代设计理论和方法中,优化设计无疑占有重要地位。在结构设计的传统方法中,除最简单的构件设计外,都是首先凭借经验和判断,选择和确定结构方案,初选构件的截面尺寸,然后进行强度、刚度和稳定性的校核验算。对方案的修改或对为数不多的方案进行比较,同样是校核性的。由于计算工作量庞大,事实上只可能做少量的方案比较,结构设计的优劣过多地依赖于设计者的水平和经验,即使是优秀的设计者亦难达到很满意的设计。从被动地进行安全校核转变为主动地从各种可能的设计方案中寻求尽可能完善或是适宜的方案就是结构优化设计所追求的目标。自然,要把结构设计人员的精力从繁重的计算工作中解放出来,把主要精力转到优化方案的选择上去,只有借助计算机才能实现。
结构优化设计的理论和方法基本上可以归结为两大类:第一类是准则方法,它是从结构力学的原理出发,首先选定使结构达到最优的准则(例如满应力准则、能量准则等),而后根据这些准则寻求结构的最优解(即满应力设计、满应变能设计等);第二类是数学方法,它是从解极值问题的数学原理出发,运用数学规划和优选法等各种方法,求得一系列设计参数的最优解(例如重量最轻设计)。
结构优化设计问题,广义地说,应该把材料的用量、制造工艺和使用维修等各种因素综合起来考虑。尽管材料的用量最少(结构最轻)并不就等同于最经济或最优,但仍不失为对结构设计方案进行比较的一个重要指标。满应力设计与最轻设计并不一定是一回事,但是在不少情况下这两种设计的结果是相同的,或者是相当接近的,而满应力设计要比最轻设计简单得多,所以满应力设计是一种切实可行,同时又是人们比较熟悉、比较容易掌握的一种优化方法。通常采用应力比的方法逐次逼近满应力(比例满应力法)。它是先选定一个初始方案(各杆件的初始截面),计算在各种载荷组合下各杆件的最大内力和相应的最大应力,然后将它们与许用应力相比,其比值k<1即表示杆件原截面有富裕,k>1即表示杆件原截面不足。将各杆件的截面乘以对应的k值作为新截面重新计算应力,如此循环迭代直到ki→1即得到满应力设计方案。有时满应力设计会收敛到非最优点(超静定结构退化为静定结构)。为避免这种情况,通常采用齿行法。所谓齿行法是在满应力设计法中增加射线步,即从坐标原点出发,经过上一步比例满应力的设计点,沿此连线方向回到约束曲线(根据约束条件确定的可行域与不可行域的分界线)。在每一步比例满应力设计之后,加一步回到约束曲线的射线步,两种步法间隔地进行。每一次射线步后记录一次结构重量。当发现某一射线步后结构的重量大于上次的重量时,就取上次的设计点为最优点。
第二类优化设计方法中的数学规划法是在等式或不等式表示的限制(约束)条件下求多变量函数(目标函数)的极值问题。如果目标函数和约束方程是线性的,则寻求这类问题的最优解即为用线性规划进行结构的优化设计;如果目标函数或约束方程是非线性的,则为用非线性规划进行结构的优化设计。结构设计中的优化通常是有约束的,是约束最优化问题。非线性规划大致可分为三类:第一类是直接处理约束的方法,例如可行方向法、最速下降法、梯度投影法、减缩梯度法等;第二类方法是用线性规划法去逐次逼近非线性规划,如割平面法、逼近规划法等;第三类方法是将约束最优化问题化为一系列无约束最优化问题。除此之外,还有非常适宜于处理桁架、塔梁、梁和连续梁的动态规划以及几何规划、整数规划等。
在结构优化设计中利用计算机有很多可供选择的方法,分属于两条不同的途径:其一是充分利用计算机的能力,使之自动地进行探索;其二是利用人的直觉,以人机对话的方式指导计算机进行计算,即CAD(计算机辅助设计)。
结构的现代设计还有另一方面的重要内涵,即设计原理的革新。由计算机的应用引起的有限元法及优化设计等还只是手段和方法上的革新。归根到底,结构及其构件是否安全可靠(有足够的强度和稳定性)、是否满足使用要求(静刚度和动刚度)的判断依据更具有基础性的意义,这是设计原理所要解决的而不是用手段和方法可以代替的问题。
由于实际结构的载荷、材料的质量和制造质量都具有随机性,因此只有应用概率论才能更真实地描述和反映结构的有效性。所以当前结构设计原理的发展趋势是采用以概率论为基础的极限状态设计法。这在建筑钢结构设计领域内已成为最先进的结构设计方法。我国《钢结构设计规范》在1988年修订时,在静力强度和稳定计算中已经采用了这一设计原则,在疲劳计算中,由于疲劳极限状态的概念还不够确切,对有关因素研究得还不够,仍只能按传统的许用应力法进行计算。
在起重运输机械金属结构领域内,我国的GB/T 3811-2008《起重机设计规范》亦推荐采用以概率论为基础的极限状态设计法。极限状态计算法的基础是:在起重机使用条件下对金属结构的受载情况进行统计分析;对金属结构材料性能的均匀程度进行统计研究。在极限状态法中不采用安全系数的概念。
在结构疲劳计算中,根据断裂力学的观点,允许出现一定程度的裂纹,并保证在下次检查前能安全使用,据此进行的设计就是损伤容限设计。
基于概率论和应用统计的可靠性计算法能够评估起重机金属结构的使用寿命和可靠度,用这种方法设计的各类结构可达到期望的可靠度。
二、许用应力设计法
许用应力法的设计准则是:结构在组合载荷作用下所求得的构件或连接的计算应力σ不超过构件或连接的许用应力[σ]。
许用应力值[σ]以材料、零件、部件或连接的规定强度R(例如钢材屈服点、弹性稳定极限或疲劳强度计算中的各个极限应力)除以相应的安全系数n来确定。安全系数n等于强度系数γfi和高危险度系数γn的乘积(n=γfi·γn),一般情况下,当高危险度系数γn取为1时,安全系数n即为强度系数γfi。
许用应力法属于定值法,根据起重机使用经验确定的强度安全系数是许用应力法的基础。它采用统一的安全系数综合考虑材料、载荷等诸多因素。该方法应用简单方便,是目前起重机金属结构仍然采用的计算方法,但其安全系数取为定值是其不足之处。
许用应力法的设计流程为:
首先计算各指定载荷fi,必要时用适当的动力载荷系数Φi增大;然后根据载荷组合表进行组合,得出组合载荷。由此组合载荷
确定合成的载荷效应(内力、变形
,根据作用在构件或部件上的载荷效应(内力、变形)计算出应力
,并与由局部效应(内力、变形)引起的应力
相组合,得到合成设计应力
。最后将此应力
与许用应力[σ]相比较。许用应力设计法的典型流程图如图3-16所示。

图3-16 许用应力设计法的典型流程图
许用应力法中的许用值也包含了结构变形等其他广义许用控制值。
在许用应力设计法中,外载荷与内力一般为线性关系,当其呈非线性关系时,应特别注意需按具体情况作特殊的计算。
三、极限状态设计法
极限状态法的设计准则是:结构在含有分项载荷系数及高危险度系数在内的组合载荷作用下所求得的构件或连接的计算应力σ,不超过构件或连接的极限设计应力。
极限设计应力limσ以材料、零件、构件或连接的规定强度R(例如钢材屈服点、弹性稳定极限或疲劳强度计算中的各个极限应力)除以抗力系数γm来确定,或以其他广义的极限值作为可接受的极限状态控制值(如相对挠度极限值,结构振动频率参数的极限值等)。抗力系数γm反映了材料的强度变化和局部缺陷的(平均)统计结果。
采用极限状态设计法时,各项计算载荷在进行组合计算前应分别乘以各自对应的分项载荷系数γpi和高危险度系数γn后再进行组合与计算,在一般非高危险情况下,高危险度系数γn取为1。
极限状态法的设计流程为:
首先计算各指定载荷fi,必要时用适当的动力载荷系数Φi增大,同时乘以载荷组合中与该项载荷相对应的分项载荷系数γpi;然后根据载荷组合表进行组合,得出组合载荷Fj。在具有高度危险的特定情况下还需对组合载荷Fj乘以高危险度系数γn,得出设计载荷γnFj。再用此载荷确定设计载荷效应(内力、变形)Sk。根据作用在构件或部件上的载荷效应(内力、变形)计算出应力σ1l,并与由采用适当的载荷系数计算的局部效应(内力、变形)引起的其他应力σ2l相组合,得到合成设计应力σl,最后将此合成设计应力σl与极限应力limσ相比较。极限状态设计法的典型流程图如图3-17所示。

图3-17 极限状态设计法的典型流程图
四、起重机金属结构计算原则
在起重机金属结构设计计算中采用两种方法:许用应力设计法和极限状态设计法。
当结构在外载荷作用下产生了较大变形以至内力与载荷呈非线性关系时,宜采用极限状态设计法。但结构件及其连接的疲劳强度仍按许用应力设计法计算。
应验算在最不利载荷组合(表3-15~表3-19)下,起重机金属结构构件及连接的强度(含疲劳强度)、刚度和稳定性是否满足起重机设计规范的要求。
本书中的计算公式是按许用应力设计法给出的,若采用极限状态设计法,则应作如下变更:
(1)除疲劳强度外的所有计算强度和屈曲稳定性的公式,其左端的弯矩、扭矩、轴向力都应该将相应载荷乘以分项载荷系数γpi和高危险度系数γn后计算得出,右端的极限设计应力limσ则应该是用钢材屈服点σs或构件抗屈曲临界应力σcr除以抗力系数γm而得到,即:limσ=σs/γm或limσ=σcr/γm;
(2)在压弯构件稳定性计算式(见第五章)左侧的弯矩项中乘有增大系数时,其中的NE也应除以γm。
(3)若计算公式中出现有许用应力计算法的安全系数n时,则将此安全系数n用抗力系数γm代替。
五、材料的许用应力及结构强度计算
1.结构构件钢材的许用应力
(1)基本许用应力
基本许用应力即结构件钢材的拉伸、压缩和弯曲许用应力,对不同的载荷组合类别(组合A、组合B及组合C)规定相应的安全系数n,得到各载荷组合下的基本许用应力[σ]。
当σs/σb<0.7时,基本许用应力:

当σs/σb≥0.7时,基本许用应力:

式中 [σ]——钢材的基本许用应力(N/mm2),与载荷组合类别相对应;
n——与载荷组合类别相对应的强度安全系数;
σs——钢材的屈服点(N/mm2)。当钢材无明显的屈服点时,取σ0.2为σs(σ0.2为钢材标准拉力试验残余应变达0.2%时的试验应力);
σb——钢材的抗拉强度(N/mm2)。
钢材基本许用应力[σ]和安全系数n见表3-21。当σs/σb≥0.7时,以0.5σs+0.35σb代替表内的σs。
表3-21 强度安全系数n和钢材的基本许用应力[σ]

(2)剪切许用应力和端面承压许用应力
剪切许用应力和端面承压许用应力用基本许用应力[σ]按下面的公式分别确定:

[σcd]=1.4[σ] (3-34)
式中 [τ]——剪切许用应力(N/mm2);
[σcd]——承压许用应力(N/mm2)。
2.连接材料的许用应力
起重机常用的连接方法有:焊接连接、螺栓连接及销轴连接。
按规定要求采用焊条、焊丝、焊剂施焊时,焊缝的许用应力见第四章表4-3。
普通螺栓、销轴连接的许用应力见第四章表4-6。
3.按许用应力法计算结构的强度
许用应力法计算强度的表达式为
σmax≤[σ]i (3-35)
τmax≤[τ]i (3-36)
式中 σmax、τmax──在载荷组合B或载荷组合C作用下,结构中产生的最大应力;
[σ]i、[τ]i──结构材料的基本许用应力,见表3-21,i=A,B,C。
六、起重机金属结构刚度计算
轴心受力构件的刚度计算见第五章。
对起重机金属结构的刚度要求是为了保证起重机的正常使用。刚度要求一般分静态和动态两个方面。
计算刚度时载荷用标准值,即不考虑各类动载系数、分项载荷系数(采用极限状态法时)。
1.静态刚度
受弯构件的静态刚度以在规定的载荷作用于指定位置时,结构在某一位置处的静态弹性变形值来表征。静态刚度应满足下述要求:
f≤[f] (3-37)
式中 [f]──结构许用静位移,见表3-22;
f──额定载荷(对桥式类型起重机包括小车自重)位于规定位置时结构的静位移,起重机常用结构的静位移计算见表3-23。
弹性变形值按结构力学的方法计算。结构中遇到变截面构件则以相应的折算惯性矩代替,实腹式轴向受力构件的折算惯性矩计算见第八章,桁架结构的折算惯性矩计算见第九章。
2.动态刚度的计算
一般起重机金属结构可不校核动态刚度,当用户或设计本身对此有要求时则做动态特性校核。
动态刚度以满载情况下,钢丝绳绕组的下放悬吊长度相当于额定起升高度时,系统在垂直方向的最低阶固有频率(简称满载自振频率)来表征。动态刚度应满足下述要求:
fd≥[fd] (3-38)
式中 [fd]──满载自振频率许用值,见表3-22;
fd──满载自振频率(Hz)。
表3-22 起重机金属结构静态及动态刚度要求

续上表

表3-23 起重机常用结构的静位移

续上表

对桥式和臂架类起重机,fd简化计算方法如下:
对桥式类型起重机,当满载小车位于跨中,物品处于最低悬挂位置时在垂直方向的自振频率可按单自由度系统的简化公式计算:

式中 g──重力加速度(m/s2)
y1──结构在吊重悬挂点,起升载荷引起的静变位(m)[设计初,小车在跨中时可取y1=(1/800~1/700)L,小车在悬臂端时可取y1=l0/350,l0为有效悬臂端长(m)];
λ0──起升滑轮组在起升载荷作用下的静变位。λ0与起升高度H有关,设计开始时可取λ0=0.0029H(m);
β──系数,由下式计算:

其中 m1──金属结构的换算质量(kg),各种门式起重机金属结构的换算质量计算式列于表3-24;
m2──吊重的质量(kg)。
表3-24 各种门式起重机金属结构的换算质量

续上表

注:Pxc──起重小车的重量(N);
PG──桥架结构的重量(N);
g──重力加速度,g=9.81m/s2。
对门座起重机和轮式起重机垂直方向的满载自振频率可按下面近似公式计算:

式中 yL──额定起升载荷在臂架端部(或象鼻架端部)引起的垂直方向的静位移(m)[设计初,可取y1=(1/250~1/200)R,R为最大幅度];
λ0──不考虑支承结构的弹性时钢丝绳绕组在额定载荷悬挂处的静伸长(m),计算时必须计及从臂架端部滑轮至卷筒之间的绳长。
七、结构稳定性计算
对受压构件、受弯构件和压弯构件需校核其稳定性。
轴心受压构件的整体稳定性条件为
σmax≤φ[σ] (3-42)
受弯构件整体稳定性条件为
σmax≤φb[σ] (3-43)
受弯构件局部稳定性条件为
σr≤[σcr] (3-44)
式中 σmax──按载荷组合B计算的结构最大应力;
φ──轴心受压构件的稳定系数,见第五章;
φb──受弯构件侧向屈曲稳定系数,见第六章;
σr──按载荷组合B计算的板的复合应力;
[σ]──载荷组合B的强度许用应力,见表3-21;
[σcr]──板的局部稳定许用应力,见第六章。
偏心受压构件的整体稳定性计算见第五章。