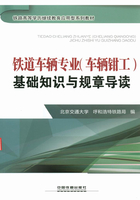
第二节 机械基础
一、机械连接
(一)螺纹连接
1.螺纹
(1)螺纹的形成
螺纹是指平面图形(如三角形、矩形、梯形等)在圆柱(或圆锥)表面上,沿着螺旋线上升所形成的具有规定牙型的连续凸起。凸起是指螺纹两侧面间的实体部分,又称为牙。在圆柱(或圆锥)外表面上所形成的螺纹称为外螺纹;在圆柱(或圆锥)内表面上所形成的螺纹称为内螺纹。
(2)普通螺纹的基本参数
①直径(图1-77)
大径(d、D)——指螺纹的最大直径,又叫作公称直径。
中径(d2、D2)——通过螺纹轴向剖面内牙型上沟槽和凸起宽度相等处的直径。
小径(d1、D1)——是指螺纹的最小直径。

图1-77 螺纹的大径、小径和中径
②线数(n)
线数是指螺纹螺旋线的数目。螺纹有单线和多线之分,沿一条螺旋线形成的螺纹称为单线螺纹,沿两条或两条以上螺旋线形成的螺纹称为多线螺纹,如图1-78所示。

图1-78 螺纹的线数、螺距及导程
③螺距(P)和导程(Pn)
螺距是指相邻两牙在中径线上对应两点间的轴向距离。
导程是指同一条螺旋线上的相邻两牙在中径线对应两点间的轴向距离。
螺纹导程=螺距×线数 即:Pn=P×n
④旋向
顺时针旋转时旋入的螺纹,称为右旋螺纹。逆时针旋转时旋入的螺纹,称为左旋螺纹。工程上常用右旋螺纹。
⑤升角(λ)
螺旋线的切线与垂直于螺纹轴线的平面间的夹角。
⑥牙型角(α)
螺纹轴向剖面内,螺纹牙型两侧边的夹角称为牙型斜角。
(3)螺纹的种类、特点及应用
按照用途的不同,螺纹可分为连接螺纹和传动螺纹两大类。连接螺纹有普通螺纹、管螺纹和圆锥螺纹。传动螺纹有梯形螺纹、锯齿形和矩形螺纹。
①普通螺纹牙型是等边三角形,内外螺纹旋合后留有径向间隙。普通螺纹按螺距大小又分为粗牙螺纹和细牙螺纹。细牙螺纹的螺距小,升角小,自锁性能好,强度高,但不耐磨,易滑扣。一般连接多用粗牙螺纹,细牙螺纹多用于细小零件、薄壁管件或受冲击、振动和变载荷的连接中,也用作微调机构的调整螺纹用。
②管螺纹
管螺纹螺纹牙型是等腰三角形,牙型角为55°。根据密封性,管螺纹又分为圆柱管螺纹和圆锥管螺纹。圆柱管螺纹的牙顶有较大的圆角,内外螺纹旋合后无径向间隙,保证连接的紧密性。适用于水、气、润滑和电气管路系统。圆锥管螺纹的螺纹分布在锥度为1:16的圆锥管壁上。内外螺纹旋合后,利用本身的变形就能保证连接的紧密性。适用于高温、高压或密封性要求高的管路系统。
③圆锥螺纹的牙型是等腰三角形,牙型角为60°,牙顶是平顶,多用于汽车、航空机械、机床的燃料、油、水、气的输送管路系统。
④矩形螺纹的牙型是矩形,牙型角为0°,传动效率较高,但牙根强度弱,磨损后难以修复。为便于加工,常制成10°的牙型角。
⑤梯形螺纹的牙型是等腰梯形,牙型角为30°,内外螺纹以锥面贴紧,不易松动。与矩形螺纹相比,传动效率略低,但工艺性好,牙根强度高,对中性好,是最常用的传动螺纹。
⑥锯齿形螺纹牙型是不等腰梯形,工作面的牙型角为3°,非工作面的牙型角为30°。内外螺纹旋合后,外径处无间隙,便于对中。这种螺纹具有矩形螺纹传动效率较高、梯形螺纹牙根强度高的特点,但中能用于单向受力的螺旋中。
2.螺纹连接
(1)螺栓连接
常见的普通螺栓连接如图1-79(a)所示。这种连接是被连接件上的通孔与螺栓杆间留有间隙,通孔的加工精度低,结构简单,装拆方便,使用时不受被连接件材料的限制,因此应用极广。图1-79(b)是铰制孔用螺栓连接,这种连接能精确固定被连接件的相对位置,并能承受横向载荷,但孔的加工精度要求较高。

图1-79 螺栓连接
(2)双头螺柱连接(图1-80)
双头螺柱连接适用于结构上不能采用螺栓连接的场合,例如被连接件之一太厚,不宜制成通孔或需要经常拆装时,往往采用双头螺柱连接。
(3)螺钉连接(图1-81)
螺钉连接是螺钉直接拧入被连接件的螺纹孔中,不用螺母,在结构上比双头螺柱连接简单,用途和双头螺柱连接相似,但多用于受力不大,又不需要经常拆装的场合。

图1-80 双头螺柱连接

图1-81 螺钉连接
(4)紧定螺钉连接(图1-82)
紧定螺钉连接是利用拧入零件螺纹孔中的螺钉末端顶住另一零件的表面或顶入相应的凹坑中,以固定两个零件的相对位置,并可传递不大的力或扭矩。螺钉除作为连接和紧定用外,还可作为调整零件位置,如机器、仪器的调节螺钉等。

图1-82 紧定螺钉连接
除上述四种基本螺纹连接形式外,还有一些特殊结构的连接(图1-83)。例如专门用于将机座或机架固定在地基上的地脚螺栓连接;装在机器或大型零、部件的顶盖或外壳上便于起吊用的吊环螺钉连接;用于工装设备中的T形槽螺钉连接等。

图1-83 特殊结构的螺纹连接
3.螺纹连接的预紧
在实用上,绝大多数螺纹连接在装配时都必须拧紧,使连接在承受工作载荷之前,预先受到力的作用。这个预加的作用力称为预紧力。
预紧的目的在于增强连接的可靠性和紧密性,防止受载后被连接件出现缝隙或发生相对运动。适当选用较大的预紧力对螺纹连接的可靠性以及连接件的疲劳强度都是有利的。特别像气缸盖、管路凸缘、齿轮箱轴承盖等紧密性要求较高的螺纹连接尤为必要。但过大的预紧力会导致整个连接的结构尺寸增大,也会使连接件在装配或偶然过载时被拉断。通常规定,拧紧后螺纹连接件的预紧应力不得超过其材料的屈服极限的80%。
对于重要的或有特殊要求的螺栓连接,则应根据载荷性质、连接刚度等具体工作条件确定适当的预紧力,并在装配图上注明数值,以便装配时加以严格控制。受变载荷的螺栓连接的预紧力应比受静载荷的要大些。
通常借助测力矩扳手或定力矩扳手控制预紧力的大小。
4.螺纹连接的防松
在冲击、振动或变载荷的作用下,螺纹连接会松脱。为了防止连接松脱,保证连接安全可靠,必须采取有效的防松措施。
防松的根本问题,在于防止螺旋副相对转动。防松的方法,按其工作原理可分为摩擦防松、机械防松和铆冲防松。
(1)摩擦防松
①对顶螺母:两螺母对顶拧紧后,使旋合螺纹间始终受到附加的压力和摩擦力的作用。工作载荷有变动时,该摩擦力仍然存在。因下螺母螺纹牙受力较小,其高度可小些,但为了防止装错,两螺母的高度取成相等为宜。结构简单,适用于平稳、低速和重载的连接。
②弹簧整圈:螺母拧紧后,靠垫圈压平而产生的弹性反力使旋合螺纹间压紧。同时垫圈斜口的尖端抵住螺母与被连接件的支承面也有防松作用。结构简单、防松方便。但由于垫圈的弹力不均,在冲击、振动的工作条件下,其防松效果较差,一般用于不甚重要的连接。
③自锁螺母:螺母一端制成非圆形收口或开缝后径向收口。当螺母拧紧后,收口胀开,利用收口的弹力使旋合螺纹压紧。结构简单,防松可靠,可多次装拆而不降低防松性能。适用于较重要的连接。
④开口销与槽形螺母:槽形螺母拧紧后将开口销穿入螺栓尾部孔和螺母的槽内。将开口销尾部掰开与螺母侧面贴紧。也可用普通螺母代替槽形螺母,但需拧紧螺母后再配钻销孔。适用于较大冲击振动的高速机械中的连接。
(2)机械防松
①止动垫圈:螺母拧紧后,将单耳或双耳止动垫圈分别向螺母和被连接件的侧面折弯贴紧,即可将螺母锁住。若两个螺栓需要双连锁紧时,可采用双连止动垫圈,使两个螺母相互制动。结构简单,使用方便,防松可靠。
②串联钢丝:用低碳钢丝穿入备螺钉头部的孔内,将各螺钉串联起来,使其相互制动。使用时必须注意钢丝的穿入方向;适用于螺钉组连接,防松可靠,但装拆不便。
(3)铆冲防松
①端铆:螺母拧紧后,把螺栓末端伸出部分铆死。防松可靠,但拆卸后连接件不能重复使用:适用于不需拆卸的特殊连接。
②冲点:螺母拧紧后,利用冲头在螺栓末端与螺母的旋回缝处打冲,利用冲点防松。防松可靠,但拆卸后连接件不能重复使用。适用于不需拆卸的特殊连接。
(二)键连接
键是一种标准零件,键主要用于轴和轴上零件(如带轮、齿轮等)的连接,起着传递扭矩的作用。键嵌入轴上的键槽中,再将带有键槽的齿轮装在轴上,当轴转动时,因为键的存在,齿轮就与轴同步转动,达到传递动力的目的。键的种类很多,常用的有普通平键、半圆键、楔键和切向键等。
1.平键连接
图1-84为普通平键连接的结构形式。键的两侧面是工作面,工作时,靠键同键槽侧面的挤压传递扭矩。键的上表面和轮毂上键槽的底面间则留有间隙。平键连接具有结构简单、装拆方便、对中性较好等优点,因而得到广泛应用。这种键连接不能承受轴向力,不能起到轴向固定的作用。
普通平键按形状分,有圆头(A型)、方头(B型)及单圆头(C型)三种。圆头平键放在轴上用键槽铣刀铣出的键槽中,键在键槽中轴向固定良好。缺点是键的头部侧面与轮毂上的键槽并不接触,因而键的圆头部分不能充分利用,而且轴上键槽端部的应力集中较大。方头平键是放在用锯片铣刀铣出的键槽中,因而避免了上述缺点,但对于尺寸大的键,宜用紧定螺钉压在轴上的键槽中,以防松动。单圆头平键则常用于轴端与毂类零件的连接。
普通平键用于静连接。当被连接的零件在工作过程中必须在轴上作轴向移动时,则须采用由导向平键或滑键组成的动连接。导向平键用螺钉固定在轴上的键槽中,轴上的传动零件则可沿键做轴向滑移。当零件滑移的距离较大时,因所需导键的长度过大,制造困难,故宜采用滑键。滑键固定在轮毂上,轴上零件带动滑键在轴上的键槽中作轴向滑移,因而轴上需铣出较长的键槽。如图1-85、图1-86所示。

图1-84 普通平键连接

图1-85 导向平键连接

图1-86 滑键连接(键槽已截短)
2.半圆键连接(图1-87)
半圆键形状如半圆。轴上键槽用尺寸与半圆键相同的半圆键槽铣刀铣出,因而键在槽中能绕其几何中心摆动以适应轮毂中键槽的斜度。半圆键工作时,靠其侧面来传递扭矩。这种键连接的优点是工艺性较好,装配方便,尤其适用于锥形轴与轮毂的连接。缺点是轴上键槽较深,对轴的强度削弱较大,故一般只用于轻载连接中。
3.切向键连接(图1-88)
由一对斜度为1:100的楔键组成。切向键的工作面是两键沿斜面拼合后相互平行的两个窄面,被连接的轴和轮毂上都开有键槽,装配时,把一对键分别从轮毂两端打入,拼合而成的切向键就沿轴的切线方向楔紧在轴与轮毂之间。工作时,靠工作面上的挤压力和轴与轮毂间的摩擦力来传递扭矩。用一个切向键时,只能单向传动;有反转要求时,必须用两个切向键,此时为了不致严重地削弱轴和轮毂的强度,两个键槽最好错开120°。由于切向键的键槽对轴的削弱较大,常用于直径大于100mm的轴上。例如用于大型带轮、大型飞轮,矿山用大型绞车的卷筒及齿轮等与轴的连接。
4.楔键连接
楔键分为普通楔键及钩头楔键,普通楔键又有圆头及方头两种形式(图1-89)。楔键的上下两面是工作面,键的上表面和与它相配合的轮毂键槽底面均具有1:100的斜度。装配时,圆头楔键要先放入键槽,然后打紧轮毂;方头及钩头楔键则在轮毂装到适当位置后才将键打紧,使它楔紧在轴和轮毂的键槽里。

图1-87 半圆键连接

图1-88 切向键连接

图1-89 楔键连接(b、c中已将键槽截短)
工作时,靠键的楔紧作用来传递扭矩,同时还可承受单向的轴向载荷,对轮毂起到单向定位作用。但在楔紧时破坏了轴与毂的对中性,故不宜用于对中要求严格或高速、精密传动的场合。由于楔键连接结构较平键连接简单,被连接零件在轴上的轴向固定不必采用附加零件,故通常在一些低速、轻载和对传动精度要求不高的连接中使用。
为了便于拆卸,楔键最好用于轴端;如用于轴的中部而又不能先装键时,则轴上键槽长度至少应为键长的两倍,以便于装配。使用带钩头的楔键时,拆卸较为方便,但如安放在轴端,则应注意加装安全罩。
5.(1)花键连接的特点及应用
花键连接(图1-90)(或多槽连接)由轴上和毂孔上的多个键齿和键槽组成。因而花键连接可以说是平键连接在数目上的发展。但是,由于结构形式和制造工艺的不同,与平键连接比较,花键连接在强度、工艺和使用方面有以下优点:
①因为在轴上与毂孔上直接而匀称地制出较多的齿和槽,故连接受力较为均匀;
②因槽较浅,齿根处应力集中较小,轴与毂的强度削弱较少;
③齿数较多,总接触面积较大,因而可承受较大的载荷;

图1-90 外花键与内花键
④轴上零件与轴的对中性(这对高速及精密机器很重要);
⑤导向性较好(这对动连接很重要),可用研磨的方法提高加工精度及连接质量。
缺点是齿根仍有应力集中,有时需用专门设备加工,成本较高。
花键已标准化。它在机械制造中,特别是在飞机、汽车、拖拉机、机床制造业和农业机械中得到广泛的应用。
(2)花键连接的类型
花键连接按其齿形不同,分为矩形花键、渐开线花键和三角花键。
①矩形花键
按齿数和齿高的不同,齿形尺寸规定了四个尺寸系列,即轻系列、中系列、重系列及补充系列。轻系列的齿数最少,齿的高度也最低,因而承载能力也最小,多用于静连接或轻载连接。中系列的齿数较轻系列的多些,齿也高些,适用于中等载荷的静连接,或零件仅在空载下移动的动连接重系列的齿数最多齿也最高故常用于重载连接。
矩形花键可采用外径、齿侧和内径三种定心方式。其特点和应用见表1-7。
表1-7 矩形花键连接的定心方式及其特点和应用

②渐开线花键
渐开线花键可以用制造齿轮的方法来加工;工艺性较好,制造精度也较高,花键齿的齿根部强度高,应力集中小,易于对中,当传递的扭矩较大且轴径也大时,宜采用渐开线花键连接。
渐开线花键定心方式有:齿形定心、按与分度圆的同心圆柱面定心和外径定心。按渐开线齿形定心具有自动定心作用,有利于各齿均匀承载,一般应优先采用。渐开线花键按与分度圆的同心圆柱面定心适用于受径向载荷较小,又要求传动平稳的传动机构。采用此种定心方式时,花键的几何尺寸关系与按齿形定心时相同,定心的圆柱面应与花键分度圆柱同心。按外径定心只在特殊需要时才采用,如用于径向载荷较大,齿形配合又需选用动配合的传动机构。因为采用此种定心后,限制了花键自动定心的作用。加工花键的刀具需特殊制造。

图1-91 渐开线花键齿形定心

图1-92 渐开线花键按分度圆的同心圆柱面定心
③三角花键
三角花键的齿形为三角形,齿数较多,键齿较细,故对轴的强度削弱较小。三角花键只按齿侧定心,因而花键轴的内径及外径处都留有径向间隙。它适用于轻载和直径小的静连接,特别适用于薄壁零件的连接。

图1-93 渐开线花键按外径定心

图1-94 三角花键
(三)销连接
销主要用来固定零件之间的相对位置,也用于轴与毂的连接或其他零件的连接,并可传递不大的载荷。还可作为安全装置中的过载剪断元件。如图1-95~图1-97所示。

图1-95 定位销

图1-96 连接销

图1-97 安全销
销可分为圆柱销、圆锥销、槽销、开口销及特殊形状的销等,其中圆柱销及圆锥销均有国家标准。如图1-98~图1-100所示。

图1-98 圆柱销和圆锥销

图1-99 开尾圆锥销

图1-100 螺杆圆锥的应用
圆柱销靠过盈固定在孔中。这种销如经多次装拆就会破坏连接的可靠性和精确性;而圆锥销就无此缺点。
圆锥销具有1:100的锥度,使其有可靠的自锁性能。开尾圆锥销装入销孔后,把末端开口部分撑开,能保证销不致松脱。若被连接零件的锥孔未打通或为了装方便,也可用一端带有螺杆的螺杆圆锥销。
槽销是沿圆柱面的母线方向开有深度不同的凹槽的销(图1-101)。槽常有三条,用滚压或模锻方法制出。槽的主要形状有:沿销全长的平行直槽;沿销全长的楔形槽;一端有短楔槽、两端有短楔槽及中部有短凹槽等。
槽销压入销孔后,它的凹槽即产生收缩变形,故可借材料的弹性而固定在销孔中。安装槽销的孔不需精确加工,并且在同一孔中可装拆多次。槽销近来应用较为普遍,对于受振动载荷的连接也很适用。在很多场合下,槽销可代替键、螺栓、圆锥销来使用(图1-102)。
开口销(图1-103)是一种防松零件,常用A2、A3及10、15等低碳钢丝来制造。

图1-101 槽销

图1-102 槽销的应用

图1-103 开口销
销的类型可根据工作要求选定。用于连接的销,工作时,通常受挤压和剪切作用。其尺寸可根据连接的结构特点,按经验确定;定位销通常不受载荷或只受很小的载荷,其直径可按结构确定,数目不少于两个。销装入被连接件的销孔内的长度约为销的直径的1~2倍。
二、机械传动
(一)带传动
1.带传动的组成及工作原理
带传动一般是由主动轮1、传动带2和从动轮3组成(图1-104),传动带紧套在两轮上,使带和带轮之间的接触面产生正压力。当原动机驱动主动轮转动时,依靠带和带轮间的摩擦力的作用,带动从动轮一起转动,并传递动力。

图1-104 带传动示意图
2.带传动的特点
(1)带具有弹性,可缓解冲击和振动,传动平稳,无噪声。
(2)当机器过载时,带在带轮上打滑,对机器具有过载保护作用。
(3)结构简单,成本低,带损坏后容易更换,安装维护方便。
(4)结构不够紧凑,大功率的带传动尺寸往往很大,而且不能保证准确的传动比。
3.带传动的类型及应用
在带传动中,常用的有平形带传动、三角带传动、圆形带传动和同步齿形带传动等。
(1)平形带传动
平形带的横剖面扁平。工作时,带的环形内表面与轮缘接触,结构简单,带轮也容易制造,而且平形带比较薄,挠曲性能好,适用于在传动中心距较大、高速运转的传动。
常用的平形带有橡胶布带、缝合棉布带、棉织带和毛织带等数种。其中以橡胶布带应用最多。

图1-105 带传动的类型
(2)三角带
三角带的横剖面是梯形,带轮上也做出相应的轮槽。工作时,三角带只和轮槽的两个侧面接触。根据摩擦原理,在同样的张紧力下,三角带传动较平形带传动能产生更大的摩擦力;而且结构比较紧凑,允许的传动比也比较大,三角带已标准化并大量生产等优点,因此三角带传动的应用比平形带传动广泛得多。
标准三角胶带都制成无接头的环形,由伸张层1、强力层2、压缩层3和包布层4组成(图1-106)。三角胶带的结构主要有帘布结构和线绳结构两类。帘布结构三角胶带制造比较方便,一般用途的三角带主要采用帘布结构;线绳结构的三角带柔韧性好,抗弯强度高,适用转速较高、载荷不大、带轮直径较小的场合。
三角胶带剖面尺寸分为O、A、B、C、D、E、F七种型号。为了制造和测量方便,公称长度以内圆周长度表示。
除以上所述的三角胶带外,还有一种活络三角带(图1-107)。这种传动带是由多层挂胶帆布贴合,经硫化并冲成小片,逐节搭迭后用螺栓连接而成。活络三角带的长度,可以根据需要加长或缩短,应于中心距不能调整的传动。一般可以代替同型号的三角胶带,但在速度较高时,传动的平稳性较差,而且使用寿命也较短。
(3)多楔带
多楔带(图1-108)传动带兼有平形带和三角带的优点:柔性好,摩擦力大,能传递的功率高,并解决了多根三角带长短不一而使各带受力不均的问题。多楔带传动主要用于传递功率较大而结构要求紧凑的场合,带速可达40m/s。

图1-106 三角带的组成

图1-107 活络三角带

图1-108 多楔带
(二)链传动
1.链传动的组成及工作原理
链传动由主动轮1、链条2和从动轮3组成(图1-109),属于带有中间挠性件的啮合传动。链轮上制有特殊齿形的齿,依靠链轮轮齿与链节的啮合来传递运动和动力。

图1-109 链传动
2.链传动的特点
与带传动、齿轮传动相比,链传动具有下列特点:
(1)和齿轮传动比较,链传动较易安装,成本低廉,它可以在两轴中心结构较为紧凑相距较远的情况下传递运动和动力,而且能在低速、重载和高温条件下及尘土飞扬的不良环境中工作。
(2)和带传动比较,它能保证准确的平均传动比,传递功率较大,传递效率较高,一般可达0.95~0.97,且作用在轴和轴承上的力较小。链传动是属于带有中间挠性件的啮合传动。与带传动相比,链传动无弹性滑动和打滑现象,因而能保持准确的传动比(平均传动比),传动效率较高;又因链条不需要像带那样张得很紧,所以作用于轴上的径向压力较小。
(3)链条的铰链易磨损,使得节距变大,造成脱落现象。
3.链传动的应用
当两轴平行且同向回转,中心距较远,传递功率较大、平均传动比要求较准确时,可采用链传动。链传动多用于轻工机械、农业机械、石油化工机械、采矿、冶金、运输起重机械和机床、汽车、摩托车和自行车等机械传动上。
4.链条的种类
链条的种类很多,常用的是滚子链和齿形链。
(1)滚子链
滚子链也称套筒滚子链(图1-110),由外链板1、销轴2、内链板3、套筒4和滚子5组成。销轴与外链板、套筒与内链板分别采用过盈配合固定。而销轴与套筒、滚子与套筒之间则为间隙配合,这样当链节屈伸时,内链板与外链板之间就能相对转动。套筒、滚子与销轴之间也可以自由转动。当链条与链轮进入或脱离啮合时,滚子可在链轮上滚动,两者之间主要是滚动摩擦,从而减少了链条和链轮齿的磨损。
(2)齿形链
齿形链根据铰接的结构不同,可分圆销铰链式,轴瓦铰链式和滚柱铰链式三种。
圆销铰链式齿形链(图1-111)主要由套筒、齿形板报、销轴3与外链板4组成。销轴3与套筒1为间隙配合。这种铰链的承压面仅为宽度的一半,故比压大,易磨损,成本较高。但它比套筒滚子链传动平稳,传动速度高,且噪声小,因而齿形链又叫无声链。

图1-110 套筒滚子链

图1-111 圆销铰链式齿形链
(三)齿轮传动
1.齿轮传动的组成及要作原理
齿轮传动由主动轮和从动轮组成,两齿轮的轴线相对位置不变,并各绕其自身的轴线而转动。如图1-112所示,当一对齿轮相互啮合而工作时,主动轮Ol的轮齿1、2、3…,通过啮合点法向力F的作用逐个地推动从动轮O2的轮齿1′、2′、3′,…,使从动轮转动,从而将主动轮的动力和运动传递给从动轮。
2.齿轮传动的特点及应用
齿轮传动与带传动和链传动等比较,有如下特点:
(1)能保证瞬时传动比恒定,平稳性较高,传递运动准确可靠。
(2)传递的功率和速度范围较大。齿轮传动传递的功率从几瓦至几万千瓦,圆周速度从很低到每秒100m以上。
(3)结构紧凑、可实现较大的传动比。在同样的使用条件下,齿轮传动所需的空间尺寸一般较小。

图1-112 齿轮传动组成
(4)传动效率高,工作可靠,使用寿命长。常用的机械传动中,以齿轮传动的效率为最高。如一级圆柱齿轮传动的效率可达99%。设计制造正确合理,使用维护良好的齿轮传动,工作可靠,寿命度达一、二十年,这也是其他机械传动所不能比拟的。
(5)齿轮传动的制造及安装精度要求高,价格较贵,且不宜用于传动距离过大的场合。齿轮传动是现代各类机械传动中应用最广泛最主要的一种传动。在工程机械、矿山机械、冶金机械以及各类机床中都应用着齿轮传动。齿轮传动所传递的功率从几瓦至几万千瓦,它的直径从不到1mm的仪表齿轮,到10m以上的重型齿轮,它的圆周速度从很低到每秒100m以上。大部分齿轮是用来传递旋转运动的,但也可以把旋转运动线往复运动,如齿轮齿条传动。
3.齿轮传动的基本要求
用来传递运动和动力的齿轮,其啮合传动是个比较复杂的过程。从传递运动和动力两方面来考虑,齿轮传动应满足以下两个基本要求:
(1)传动要平稳。要求齿轮在传动过程中,任何瞬时的传动比保持恒定不变。这样可以保持传动的平稳性,避免或减少传动中的噪声、冲击和振动。
(2)承载能力强。要求齿轮的尺寸小、重量轻,而承受载荷的能力大。也就是要求强度高,耐磨性好、寿命长。
4.齿轮传动的类型(图1-113)

图1-113 齿轮传动类型
齿轮传动的种类很多,可以按不同方法进行分类。
根据齿轮传动轴的相对位置,可将齿轮传动分为两大类,即平面齿轮传动(两轴平行)和空间齿轮传动(两轴不平行)。
按齿轮传动在工作时的圆周速度不同,可分低速(v<3m/s)、中速(v=3~15m/s)和高速(v>15m/s)三种。
按齿轮传动的工作条件不同,可分闭式齿轮传动和开式齿轮传动两种。在农业机械、建筑机械以及简易的机械设备中有一些齿轮传动没有防尘罩或机壳,齿轮完全暴露在外边,这叫开式齿轮传动。这种传动不仅外界杂物极易侵入,而且润滑不良,因此工作条件不好,轮齿也容易磨损,故只宜用于低速传动。当齿轮传动装有简单的防护罩,有时还把大齿轮部分地浸入油池中,则称为半开式齿轮传动。它的工作条件虽有改善,但仍不能做到严密防止外界杂物侵入,润滑条件也不算最好。而汽车、航空发机等所用的齿轮传动,都是装在经过精确加工而且封闭严密的箱体(机匣)内,这称为闭式齿轮传动(齿轮箱)。它与开式或半开式的相比,润滑及防护等条件最好,多用于重要的场合。
按齿形方向与轴的相对位置,可分直齿、斜齿和曲齿三种。
按轮齿的齿廓曲线不同,可分为渐开线齿轮,摆线齿轮和圆弧齿轮等几种。
按齿轮的啮合方式分,可分为外啮合齿轮传动、内啮合齿轮传动和齿条传动。
(四)蜗杆传动
1.蜗杆传动的组成(图1-114)
蜗杆传动是由蜗杆和蜗轮组成,用来传递空间互相垂直而不相交的两轴间的运动和动力。由于它具有传动比大而结构尺寸紧凑等优点,所以在各类机床、冶金、矿山及起重设备等的传动系统中,得到了广泛的应用。
2.蜗杆传动的类型
根据蜗杆形状的不同,蜗杆传动可以分为圆柱蜗杆传动、圆弧面蜗杆传动和锥蜗杆传动。
(1)圆柱蜗杆传动
圆柱蜗杆传动包括普通圆柱蜗杆传动和圆弧齿圆柱蜗杆传动两类。
①普通圆柱蜗杆传动
普通圆柱蜗杆传动又分为多种类型,但其中最常用的是阿基米德蜗杆传动。
阿基米德蜗杆,在垂直于其轴线的剖面上,齿廓曲线为阿基米德螺旋线;在通过其轴线的剖面上,齿廓为直线,犹如直齿齿条的齿廓;在螺旋线的法向剖面内,齿廓为曲线。至于蜗轮,在主剖面(通过蜗杆轴线并垂直于蜗杆的平面)上,其齿廓则为渐开线。在此剖面上,蜗杆与蜗轮的啮合关系可以看做是直齿齿条和齿轮的啮合关系。阿基米德圆柱蜗杆的缺点是难以进行磨削,因而精度不高。但它具有加工简便的优点,故在机械中应用最广。

图1-114 蜗杆传动组成
②圆弧齿圆柱蜗杆传动
圆弧齿圆柱蜗杆传动在主剖面上,蜗杆的齿廓为凹弧形,而与之相配的蜗轮的齿廓则为凸弧形。所以圆柱蜗杆传动是一种凹凸弧齿廓相啮合的传动,也是一种线接触的啮合传动。其主要特点为:效率高,一般可达90%以上;承载能力高,一般可较普通圆柱蜗杆传动高出50%~150%;体积小、重量轻、结构紧凑。这种传动广泛地应用到冶金、矿山、化工、建筑、起重等机械设备的减速机构中。
(2)圆弧面蜗杆传动(图1-115)
圆弧面蜗杆传动的特征是,所用蜗杆切制螺纹段的外形是以凹圆弧为母线所形成的旋转曲面,所以把这种蜗杆传动叫做圆弧旋转面蜗杆传动,简称圆弧面蜗杆传动。在这种传动的啮合带内,蜗轮的节圆位于蜗杆的节弧面上,亦即蜗杆的节弧沿蜗轮的节圆包着蜗轮。在主剖面内,蜗杆和蜗轮的轮齿都是直线齿廓。由于同时相啮合的齿对增多,而且轮齿的接触线与蜗杆齿运动的方向近似于垂直,这就大大改善了轮齿受力情况和润滑油膜形成的条件,因而承载能力约为阿基米德蜗杆传动的2~4倍,效率一般高达0.85~0.9;但它需要较高的制造和安装精度。
(3)锥蜗杆传动(图1-116)
锥蜗杆传动也是一种空间交错轴之间的传动,两轴交错角通常为90°。蜗杆是由在节锥上分布的等导程的螺旋所形成的,故称为锥蜗杆。而蜗轮在外观上就象一个螺旋圆锥齿轮,它是用与锥蜗杆一致的锥滚刀在普通滚齿机上加工而成的,故称为锥蜗轮。锥蜗杆传动的特点是:同时接触的点数较多,重迭系数大;传动比范围大(一般为10~360);承载能力和效率较高;侧隙便于控制和调整;能作离合器使用;可节约有色金属;制造安装简便,工艺性好。但由于结构上的原因,传动具有不对称性,因而正、反转时受力不同,承载能力和效率也不同。

图1-115 圆弧面蜗杆传动

图1-116 锥蜗杆传动
3.普通圆柱蜗杆传动的特点
(1)在蜗杆传动中,因蜗杆头数一般较少,所以能实现大的传动比。
(2)在蜗杆传动中,由于蜗杆齿是连续不断的螺旋齿,蜗轮齿和它是逐渐进入啮合及逐渐退出啮合的,同时啮合的齿对又较多,故冲击载荷小、传动平稳、噪声低。
(3)当蜗杆的螺旋线升角小于啮合面的当量摩擦角时,蜗杆传动便具有自锁性。
(4)蜗杆传动与螺旋齿轮传动一样,在啮合处有相对滑动。当滑动速度很大,工作条件不够良好时,就会产生较严重的摩擦与磨损,从而引起过分发热,使润滑情况恶化。因此摩擦损失较大,效率低。
三、摩擦基本知识
(一)摩擦概述
在正压力作用下,当相互接触的两个物体受切向外力的影响而发生相对滑动,或有相对滑动的趋势时,在接触表面上就会产生抵抗滑动的阻力,这一自然现象叫作摩擦,这时产生的阻力叫摩擦力。
摩擦是一种不可逆过程,其结果必然有能量损耗和摩擦表面物质的丧失或转移,即磨损。磨损会使零件的表面形状和尺寸遭到缓慢而连续的破坏,使机器的效率及可靠性逐渐降低,从而丧失原有的工作性能,最终还可能导零件的突然破坏。
(二)摩擦分类
摩擦可分两大类:一类是发生在物质内部,阻碍分子间相对运动的内摩擦;另一类是当相互接触的两个物体发生相对滑动或有相对滑动的趋势时,在接触表面上产生的阻碍相对滑动的外摩擦。仅有相对滑动趋势时的摩擦叫作静摩擦;相对滑动进行中的摩擦叫作动摩擦。动摩擦又分滑动摩擦与滚动摩擦。滚动摩擦的机理与规律完全不同于滑动摩擦。
根据摩擦面间存在润滑剂的情况,滑动摩擦又分干摩擦、边界摩擦(边界润滑)、混合摩擦(混合润滑)及流体摩擦(流体滑动)。混合摩擦及流体摩擦统称非流体摩擦。干摩擦是指表面间无任何润滑剂或保护膜的纯金属接触量的摩擦。在工程实际中,并不存在真正的干摩擦,因为任何零件的表面不仅会因氧化而形成氧化膜,而且多少也会被润滑油所湿润或受到“油污”。
1.干摩擦
两个无润滑物体之间的摩擦,主要是由两种因素所构成,一是摩擦面的实际接触区内出现的黏着;二是较硬表面上的不平度凸峰在较软表面上所起的犁刨作用。
影响摩擦系数的因素很多,除了摩擦副的配偶材料性质以外,主要还有表面膜与镀层、滑动速度、环境温度和表面粗糙度等。
摩擦副的配偶材料性质对摩擦系数的影响,主要取决于材料的互溶性。对于相同金属或互溶性的金属所组成的摩擦副,易发生相互黏着现象,故摩擦系数大。反之,则其值较小。
相对滑动速度对摩擦系数的影响,主要是由于摩擦表面温度升高将引起表面材料的机械性能发生变化。当相对滑动速度低于音速的十分之一(约30m/s)时,摩擦表面的性质和状态不致发生明显的改变,一般可不考虑它的影响。在高于这个速度时,摩擦系数将随速度的增大而降低,而且用导热性较差的材料(如合金钢)比用导热性较好的材料(如铜),摩擦系数要降低的更多。
周围介质温度对摩擦系数的影响。金属材料的摩擦副随着温度的升高,摩擦系数先是下降,在700~8000℃时降到一个最低点,然后又随温度的升高而增大。这种现象是由于温度升高,使得分子间的阻抗减少,因而形成前一阶段摩擦系数下降;当温度继续升高时,由于金属的硬度急剧下降,塑性加大,因而摩擦系数的机械分量增大,所以随着温度的继续升高,摩擦系数也迅速加大。
在干摩擦情况下,对于具有一般光洁度的表面,光洁度提高时则摩擦系数减小;但当光洁度提高到一定程度后,如再继续提高,则因实际接触面积的增大,表面间的分子吸力也增大,所以摩擦系数将随着表面粗糙度的增高而缓慢上升。
2.边界摩擦(边界润滑)
摩擦表面间,由于润滑油的存在而大大改变了摩擦的特性。当两个受“油污”的表面在重载作用下靠得非常紧(两表面间可能只有1μm、甚至只有一两个分子那样厚的油膜存在,以致有许多的不平度凸峰发生接触),而润滑油的体积性质(又叫黏性)还不能起作用时,其摩擦特性便主要取决于润滑油和金属表面的化学性质,这种能保护金属不致黏着的薄膜.叫作边界薄膜。这时两表面间形成的摩擦就叫边界摩擦。
在边界摩擦时的摩擦规律,基本上与干摩擦相同,只是摩擦系数小些,通常约在0.1左右。因为不能完全避免金属的直接接触,所以这时仍有磨损产生。
3.混合摩擦(混合润滑)
随着摩擦面间油膜厚度的增大,表面不平度凸峰直接接触的数量在缩小,而油膜承载的比重在增加。根据对粗糙面相互作用的研究表明,在混合摩擦(混合润滑)时,可用膜厚比λ来标志不平度与油膜各自分担载荷的情况:

式中 hmin——两粗糙面间的最小公称油膜厚度,μm;
σ——两粗糙面的综合不平度,μm:
其中σ1、σ2——分别为两表面不平度的均方根值,μm。
当λ<0.4时,为边界摩擦,载荷完全由不平度承担;当0.4≤λ≤3.0时为混合摩擦,随着λ值的增大,油膜承担载荷的比例也在增加;在λ=1时,不平度所承担的总载荷约为30%。
很显然,在混合摩擦时,因仍然有不平度凸峰的直接接触,所以不可避免地还有磨损存在,只是摩擦系数要比边界摩擦时小得多了。
4.液体摩擦(液体润滑)
正如以上所指出,当摩擦面间的油膜厚度大到足以将两个表面的不平度凸峰完全分开时,即形成了完全的液体摩擦。这时的油分子大都不受金属表面吸附作用的支配而自由移动,摩擦是在流体内部的分子之间进行,所以摩擦系数极小(油润滑时约为0.001~0.008),而且不会有磨损产生。