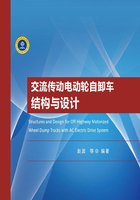
1.4.3 结构特点
(1)组成复杂,技术先进
为适应矿山生产运输要求,大型矿用自卸车普遍采用带废气涡轮增压的超大功率柴油机,传动系为电传动或液力机械传动,转向系为全液压动力转向,制动系多采用电制动和液压盘式制动,采用油气悬挂装置,全焊接高强度车架,倾斜式超大货箱,具有防落物和防翻滚结构的驾驶室,多级式液压举升液压缸等结构,比传统公路型汽车要复杂得多。
(2)车体庞大,外形超廓
矿用自卸车在有限的矿区范围内行驶,矿车的外形尺寸不像公路汽车那样受限制,为提高每车次的运输量,尽可能加大货箱容积,加宽加高整车外形尺寸,其外廓远远超过国家《公路工程技术标准》(JTGB 01—2003)和《道路车辆外廓尺寸、轴荷及质量限值》(GB 1589—2004)规定的道路行驶车辆车宽不得超过2.5m的上限值,不允许在公路上行驶。
(3)吨位巨大
为提高运输效率,降低运输成本,减少矿区的车流密度,对于不同开采规模的矿山,都力求采用尽可能大的吨位车型,以减少自卸车总数量。目前矿用自卸车的载重在20~360t之间,而且还在向大型化方向发展。
国内的大型矿山常采用100t以上的电动轮自卸车,西方各国使用较多的是100~300t的矿用自卸车,当前矿用自卸车的最大吨位已达到363t。
(4)动力强劲,爬坡能力强,车速不高
由于吨位巨大,道路又多坡,要求发动机必须具有高功率和高转矩,保证满载上坡的需要。由于非公路工况差,吨位巨大和道路多坡多弯道,出于安全性考虑,一般这类车型的最高车速在矿山上都限制在30~40km·h-1左右,最高车速也仅为50~55km·h-1左右。
重型矿用自卸车的发动机都属于工程机械类柴油发动机:一般额定转速在2000r·min-1左右,功率输出既要求功率巨大,又要求尽可能高的转矩,以适应整车车速不高、爬坡较多的使用特点。
(5)多重制动,安全可靠
矿区道路多弯、多坡,车辆满载吨位巨大,制动系统的可靠性和安全性必须优先保证。电动轮自卸车的制动系一般有以下多重制动方式:一是电阻制动;二是液压盘式制动;三是机械弹簧制动。在配备一个综合制动踏板的情况下,在制动踏板的最初行程中,首先是电阻制动投入工作,通常在车速降至5km·h-1左右时,液压盘式制动继而投入工作。当自卸车完全停止后,机械弹簧制动投入工作。
辅助的电力缓行制动时,电动轮电动机被调整为发电机运行状态,将车辆运行的机械能转变成电能,通过制动电阻栅,以热能的形式耗散在大气中,这时,电动轮电机产生的电动力矩阻碍车辆运行,从而起到减速制动的作用。
电阻制动能无摩擦地吸收自卸车动能,减缓车速,大大减少了液压盘式制动器的使用频率,使其寿命得以延长。
一般认为,自卸车的主制动器是液压盘式制动器,电阻制动是动力辅助制动,即无摩擦的缓行制动方式,机械弹簧只有在停车制动时才使用(紧急制动情况除外)。
主、辅制动系统结合后,一般常设有行车制动、停车制动、装载制动和紧急制动等多套制动系统,以保证矿用自卸车在任何行驶情况下都能安全、可靠地停车。
(6)常为两轴,超短轴距,后轮驱动
装卸场点一般面积窄小,道路多为临时性路面,地面多坑洼起伏,上下坡多,急转弯多,为保持自卸车机动灵活,一般采用两轴、超短轴距设计,力求缩短轴距与总长,车辆外形宽度和高度相对于长度的比例偏大。这种设计能够增强操纵稳定性,并使转弯直径最小,减少倒车次数。为轻量化和降低成本的考虑,多选择4×2后轮驱动型式。
与三轴底盘相比,两轴结构简单了许多,不仅降低了故障发生率,也提高了整车可靠性。而且,两轴底盘维修保养方便,转向机动灵敏、倒车方便。一般其单轴载荷远超过《道路车辆外廓尺寸、轴荷及质量限值》(GB 1589—2004)规定的单轴载荷不得超过12t的上限,不能在公路上行驶。
(7)全焊接高强度车架
车架一般由低合金、高强度厚钢板全焊接而成,关键受力部位多采用铸件或锻件以提高承载性能。采用承载式车架,横梁一般采用封闭型截面,以增强其弯曲、扭转强度和刚度;纵梁多采用变截面箱形结构,以保证等强度设计,这些特点保证了车架结构的坚固可靠和高强度性能[4]。
(8)前低后高的后卸式货箱
一般货箱由高强度、高耐磨性的低合金钢板全焊接制成,合金钢板的屈服极限一般为590~1034MPa,典型型式是采用铲斗型底板,前低后高,一般底板下倾角为9°~12°,尾部敞开无后栏板,这样的斜坡角可以保证即使是在上坡行车状态,矿石也不至于从车尾滚落。底板由高强度、高硬度、抗冲击的优质钢板焊接而成,板材最厚达到20mm左右,以适应非公路苛刻的运输工况和恶劣的装载方式,保证使用寿命可达8~10年。货箱前部,则向前伸出护板,以保护驾驶室及电控柜等不被电铲装卸的矿石撞击损坏。
在寒区使用的车型,为避免碎石土渣与底板冻结不能卸出,将发动机排气尾管接入货箱底板加强梁的空腔中,用以温热货箱底板,避免结冻。
(9)偏置式驾驶室,具有防落物和防翻滚结构
采用短头、狭小空间布置的双座非全宽驾驶室,偏置(一般是左侧置)在自卸车左前轮上方,位置在车架龙门梁的上部。
驾驶室一般是平板组装结构,对密封、隔音、隔热、减振等功能要求很高,采用模块化设计,视野宽,符合人机工程学,保证司机的操作舒适度。
此外,驾驶室要在矿石物料不慎坠落时,或者自卸车发生意外碰撞滚翻时,为司机提供“五侧安全保护”,保证司机的生命安全;或者驾驶室本身采用多支柱支撑结构,或在驾驶室外面的顶部和侧部配备独立的保护支撑装置,这些结构就是所谓的翻车保护结构(Roll-Over Protective Structures,ROPS)和落物保护结构(Falling Objects Protective Structures,FOPS)[5]、[6]。
(10)被动式油气悬架
大型矿用自卸车重吨位与短轴距的特点特别适宜安装筒式油气弹簧悬架,而传统的钢板弹簧易发生断裂,而且也没有合适的空间尺寸布置钢板弹簧。筒内顶部空间充满氮气(或氦气),作为弹性介质减缓车轮的跳动冲击,而筒内液压油,在内外筒伸缩过程中,环形空间变大或缩小,其油液经过节流孔往复进出,起到节流阻尼、减小伸缩弹跳频率的作用[7]。
通常前桥采取独立悬架,后桥使用非独立悬架。除减振、支撑和连接等功能外,前轮的油气悬挂缸还兼有转向主销的作用,外缸筒通常紧固在车架纵梁外侧,省去了传统的整体式前轴。
(11)全液压动力转向
由于整车质量大,前轴负荷也大,前轮的转向必须完全依靠液压动力。司机转动转向盘,目的在于轻松转动转向阀,控制高压油向液压转向液压缸的进入方向和流量,操动转向液压缸的活塞杆伸缩,经过转向杆系实现前轮转向。为保证转向安全可靠,不仅采用全液压转向,而且都配备紧急转向系统,当转向系统动力发生故障时,紧急转向系统能保证其还有一定的转向能力,将车停到一个比较安全的地方。
(12)双举式多级液压举升液压缸
常采用中部双举举升方式,即两只举升液压缸对称地安装在车架纵梁外侧,直接顶升货箱底板的纵梁,具有举升力量大、安全性能好的特点,常采用单作用的2级或3级伸缩式套筒液压缸结构,粗端在上,最细的一端朝下,这种倒置式的安装有利于将每级缸筒外侧粘附的泥沙、尘土向下推刮并脱离缸筒,提高了缸筒的清洁度,减少了沙粒的刮擦磨损。