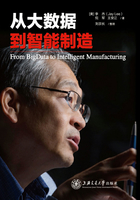
1.2 何谓智能制造的核心
制造系统的核心要素可以用5个M来表述,即材料(material)、装备(machine)、工艺(methods)、测量(measurement)和维护(maintenance),过去的三次工业革命都是围绕着这5个要素进行的技术升级。然而,无论是设备的精度和自动化水平提升,或是使用统计科学进行质量管理,或是状态监测带来的设备可用率改善,又或是精益制造体系带来的工艺和生产效率的进步等,这些活动依然是围绕着人的经验开展的,人依然是驾驭这5个要素的核心。生产系统在技术上无论如何进步,运行逻辑始终是:发生问题→人根据经验分析问题→人根据经验调整5个要素→解决问题→人积累经验。
而智能制造系统区别于传统制造系统最重要的要素在于第六个M,即建模(modeling),并且正是通过这第六个M来驱动其他5个要素,从而解决和避免制造系统的问题。因此智能制造系统运行的逻辑是:发生问题→模型(或在人的帮助下)分析问题→模型调整5个要素→解决问题→模型积累经验,并分析问题的根源→模型调整5个要素→避免问题。因此,一个制造系统是否能够被称为智能,主要判断其是否具备以下两个特征:
(1)是否能够学习人的经验,从而替代人来分析问题和形成决策。
(2)能否从新的问题中积累经验,从而避免问题的再次发生。
我们不难看出,无论是机器换人、物联网,或是互联网+,解决的只是5M要素的调整方式和途径,只是在执行端更加高效和自动化,并没有解决智能化的核心问题。
所以说,智能制造所要解决的核心问题是,如何对制造系统中的5M要素的活动进行建模,并通过模型(第六个M)驱动5M要素。智能制造所要解决的核心问题是知识的产生与传承过程。
从传统制造向智能制造转型的基础和内在动因是什么?
要回答这个问题,我们需要从制造业的竞争力和代表技术的发展进行分析。现代制造业的价值逻辑从20世纪70年代至今主要经历了4个阶段:以质量为核心、以流程改善为核心、以产品全生命周期为核心和以客户价值创造为核心。这个发展过程也是人们积累制造经验的过程,从解决“可见的问题”向解决“不可见的问题”延伸,同时在发现和解决新问题的过程中产生新的知识,并以不同的科技形式将其运用到5M要素中的过程。
第一阶段:在人的知识积累过程中提升质量和生产效率
从20世纪70年代至90年代,大到国家之间的制造业竞争,小到各个行业中企业间的竞争,无疑不围绕着“质量”这一核心展开。20世纪70年代,日本意识到其制造的产品在质量上与欧美存在着巨大差距,为了摆脱其产品在国际市场上无人问津的窘境,提出了以“全生产系统维护(TPM)”为核心的生产管理体系。TPM的核心思想可以用“三全”来概括:全效率、全系统和全员参与;目标可以用4个零来概括:零停机、零废品、零事故和零效率损失。实现方式主要包括3个方面的改善:提高工作技能、改进团队精神和改善工作环境。因此我们不难看出,在这个阶段,制造系统的进步主要依靠的并不是技术的升级,而是管理哲学和制度的创新,其核心是以组织为中心的实践与文化建设。然而不可否认的是,这一阶段的改革奠定了日本制造的精神内核,也使日本制造在短时间内险些使美国丧失世界第一制造大国的地位。受到日本制造冲击的美国和欧洲也纷纷效仿日本,建立了先进的生产管理制度,并完善了质量管理体系。这个阶段为制造系统的进步所带来的影响可以总结为:将解决生产过程中问题的经验,利用先进的管理制度和组织文化,转变成为人的知识。
第二阶段:利用数据对问题的发生过程进行建模,使知识积累的速度迅速提升
从20世纪90年代开始,企业开始发现以关注生产现场为主的TPM模式所发挥出来的潜能越来越少,于是开始了向库存控制、生产计划管理、流程再造、成本管理、人才培养、供应链协同优化、设备资源和市场开发等整个生产系统的各个环节进行延伸。在这个阶段,以丰田(Toyota)为代表的日本企业主要采用了精益生产(lean manufacturing)技术体系,而以通用电器公司(GE)为代表的西方企业则主要采用6 sigma企业流程管理体系。两者的主要区别在于,精益生产仍然是以组织管理为中心的实践和流程优化为主要手段,而6 sigma则更多地使用分析与管理工具(如SPC、DMAIC、DFSS、QFD)。然而在大多数企业的实践中,两者并没有明确的界限,而是将两个体系中适合自己的部分加以应用。与以TPM为核心的管理方式相比,精益生产技术体系和6 sigma的进步主要体现在以下几点:① 从仅仅关注生产现场,延伸到整个产业链的各个要素;② 开始以客户为中心,以满足客户需求为导向,以为客户提供优质服务为目标;③生产系统中的大量数据被采集和分析,开始从以往的经验导向转变为数据和事实导向。在这个过程中,以美国汽车制造业为代表的企业开始意识到利用数据将生产过程中的问题和差异化进行建模的重要性,于是大量的先进统计工具和建模方法被引入设计和制造的过程中,美国制造的质量得以大幅提升。1990~2000年这个阶段对制造系统的影响是:大量的问题得以依靠数据被分析和保留下来,人获取知识的能力在许多分析工具的帮助下得以提升,同时知识以软件或嵌入式智能的形式得以分享、使用和传承。
第三阶段:制造的价值链向使用端延伸,利用预测分析技术发现隐性问题
进入2000年,企业的竞争焦点开始转移到产品的全生命周期管理与服务(PLM)方面,这标志着制造业的注意力从以往的以生产系统为核心,向以满足用户需求为导向的产品与服务转移。PLM是一种对所有与产品相关的数据、在整个生命周期内进行管理的技术,管理的核心对象是产品的数据。在企业内部,与PLM相关的主要软件工具包括客户关系管理系统(CRM)、计算机辅助设计(CAD)、产品数据管理系统(PDM)、计算机辅助工艺编制(CAPP)、制造执行系统(MES)、供应链管理系统(SCM)和企业资源计划系统(ERP)等,分别对需求分析、概念定义、产品设计、生产制造、产品销售、产品服务等环节的数据进行管理与分析,是企业实现全面信息化的过程。与此同时,以预诊与健康管理(PHM)为核心的预测分析技术被用于分析产品使用过程中的数据,通过对远程监控系统所采集的数据进行分析,实现对产品使用过程中的衰退和未知变异的透明化管理,通过及时避免产品故障为客户创造价值。代表产品包括小松机械(Komatsu)在2005年推出的康查士(KomtraxTM)系统、John Deere的精智农业管理系统(FarmSightTM),以及GE航空(GE Aviation)的On-wing SupportTM服务。这时的产品开始有了代表产品自身性能的“蛋黄”和代表以产品为载体的增值服务的“蛋白”区分,且“蛋白”所占的价值比重越来越大,各个公司都在思考如何以产品为载体为用户提供服务。商业模式也因此发生了转变,因为企业发现卖设备能够赚到的钱已经很少了,倒不如把设备租给用户从而赚取服务费用,于是就产生了产品的租赁体系和长期服务合同,其代表是GE所提出的“Power by the Hour(时间×能力)”的盈利模式,企业卖的不再是产品,而是为客户提供产品使用的能力。随着产品大量全生命周期数据的获取,尤其是产品使用过程中数据的收集,以及机器学习和仿真建模等先进分析技术的发展,使得人们能够从数据中获取以往不可见的知识,并利用这些知识去管理和解决以往不可见的问题。
更确切地讲,制造业的发展过程,其核心是制造哲学的进步过程,经历了标准化、合理化+规范化、自动化+集成化、网络化+信息化4个阶段,如图1-1所示。这背后的制造哲学可以概括为,以低成本生产高质量的产品;通过全流程改善降低浪费、次品和事故;通过产品全生命周期的数据管理,为用户提供所需要的能力和服务。在以上几个阶段的基础上,现在的制造系统正处在向智能化+客制化迈进的阶段,目标是实现在“无忧虑”的生产系统中,以低成本快速实现用户的客制化需求。而实现“无忧虑”的关键在于,对生产系统全过程中的5M要素,利用建模(modeling)进行透明化、深入和对称性的管理,实现从问题中产生数据,从数据中获取知识,再利用知识避免问题的闭环过程。

图1-1 制造业哲学的进步过程